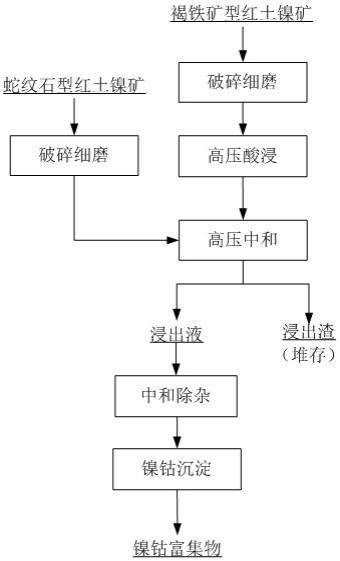
1.本技术涉及红土镍矿处理技术领域,具体而言,涉及一种红土镍矿两段加压提取镍钴的系统及工艺。
背景技术:
2.红土镍矿中的镍占地球上陆基镍储量的70%左右,是提取金属镍的主要矿源。根据化学成分的不同,一般分为两种类型:一种是硅镁镍矿(蛇纹石矿型),镍、硅、镁含量高,铁、钴含量低。另一种是褐铁矿类型,铁、钴含量较高,镁含量低,其所含的镍储量占到红土矿资源的70%,因而其开发利用备受关注。
3.湿法处理红土镍矿中,对蛇纹石矿主要有常压酸浸、加压
‑
常压联合等工艺,其镍钴浸出率随酸矿比呈正比升高,同时,铁的浸出率也升高,辅助材料消耗增大,由于其镍钴回收率相对较低,当国际镍市场价格不景气时,其经济效益会受到很大的影响。对褐铁矿处理的工艺主要有高压酸浸法(hpal),如古巴moa bay厂、柯拉湾厂、murrinmurrin厂、瑞木厂等,其镍钴浸出率可达>95%。加压浸出工艺具有镍、钴回收率高,铁浸出率低,选择性强的特点。近年来,国际上进行的红土镍矿开发项目,较多采用了高压酸浸的湿法工艺,如中冶瑞木项目,在建的有力勤、华友、格林美等公司在印尼的项目都采用高压酸浸工艺。
4.目前已建成或在建的高压酸浸法处理褐铁矿型红土镍矿,无一例外都采用高压酸浸处理褐铁矿
‑
常压中和处理蛇纹石矿的联合工艺,简称高压酸浸
‑
常压中和,其典型工艺流程见图1。高压酸浸处理褐铁矿,在高温高酸下实现对镍钴的选择性浸出,杂质铁铝大部分存在于渣中,可以获得较高的镍钴浸出率,反应结束后矿浆经闪蒸降温,加入蛇纹石矿浆中和褐铁矿矿浆中的残酸,同时尽可能浸出蛇纹石中的镍,镍浸出率一般为40~60%左右。该方法可以少量浸出蛇纹石中的镍,提高了红土镍矿的资源利用率,同时用蛇纹石矿中和残酸,有利于降低后续中和除杂工序中和剂的使用量,具有一定优势,因此获得了较大应用。如现有技术cn107250394a中也公开了类似技术,其采用了高压处理褐铁矿
‑
常压处理腐泥土矿的联合工艺。
5.针对高压酸浸
‑
常压中和工艺,有几点值得进一步改进:一方面,高压酸浸矿浆冷却往往要采用3级闪蒸3级预热,余热利用率不高,造成了能源的浪费;另一方面,蛇纹石矿浆用于浸出后常压中和,由于反应是在常压条件下进行,浸出的铁无法生产赤铁矿沉淀而释放出酸,使得镍的浸出率很低,仅为50
‑
60%左右,造成了资源的浪费;另外,常压中和无法有效去除铝,导致后期中和除杂时,需要消耗大量的碱等中和剂以去除。
6.现有技术中,专利cn101001964a中公开采用了常压酸浸处理褐铁矿
‑
高压中和处理腐泥土矿的联合工艺,其公开了在120
‑
160℃范围、高于大气压力的条件下处理酸浸液和腐泥土矿;其存在镍、钴浸取率不高的问题,而且中和除杂时,需要消耗大量的碱等中和剂以去除铝、铁等,成本较高。
7.金川集团公开的专利cn104789766a中,采用常压处理腐泥土矿
‑
加压浸出褐铁矿的联合工艺;其存在酸耗高的问题,而且在后期的中和除杂时,也需要消耗大量的碱等中和
剂以去除铝、铁等,成本较高。
8.本技术人早期公开的专利cn103614571a中,采用了常压浸出褐铁矿
‑
加压浸出蛇纹石矿的联合工艺,通过降低加压浸出段温度和压力的方式,以达到降低投资、能耗和生产成本的目的;但其存在镍、钴浸取率不高的问题,而且在中和除杂时也需要消耗大量的碱等中和剂以去除铝、铁等。
9.因此,研究如何充分利用高压酸浸过程的矿浆余热,降低能耗,同时提高镍、钴的浸出率具有重大意义。
10.基于此思考,本发明提出采用“高压酸浸
‑
高压中和”的系统及方法处理红土镍矿的工艺路线,采用高压高温处理褐铁矿,浸出后矿浆先不进行闪蒸,而是通过管道直接进入高压中和单元,与加入的蛇纹石矿浆协同进行高压中和,利用褐铁矿高压酸浸余热在稍低温度和压力下中和残留的硫酸以及使新生成的铁以赤铁矿形式沉淀释放出酸,同时实现蛇纹石的强化浸出,而伴随着蛇纹石的强化浸出,其又可以促使al
3
的进一步水解,降低中和液中杂质al的浓度。在该工艺及系统中,一段高压酸浸保证褐铁矿的充分浸出,二段利用一段高压酸浸矿浆的余热浸出蛇纹石,同时实现降低残酸、降低杂质铝的目标,可极大提高蛇纹石型红土镍矿的浸出率。
技术实现要素:
11.为了克服现有技术的上述缺点,本技术的目的在于提供一种红土镍矿两段加压提取镍钴的系统及工艺,通过高压酸浸
‑
高压中和的新思路,实现高压酸浸矿浆余热的充分利用和蛇纹石矿镍钴的高效浸出,降低了能耗和辅助材料的消耗,实现了红土镍矿中镍钴的高效提取。
12.第一方面,本技术提供了一种红土镍矿两段加压提取镍钴的系统,包括:高压酸浸装置,以用于对褐铁矿型红土镍矿进行高温高压酸浸,所述高压酸浸装置具有褐铁矿型红土镍矿矿浆入口、硫酸入口和浸后矿浆出口;高压中和单元,以用于对高压酸浸后的矿浆进行高温高压中和处理,所述高压中和单元具有高压酸浸矿浆入口、蛇纹石型红土镍矿矿浆入口、高压中和后液出口和高压中和底流出口;中和除杂单元,以用于对高压中和处理后的矿浆进行中和除杂处理,所述中和除杂单元具有高压中和后液入口、中和剂入口、中和除杂后液出口和中和除杂底流出口;镍钴沉淀单元,以用于对中和除杂后液进行沉淀处理,所述镍钴沉淀单元具有中和除杂后液入口、沉淀剂入口、沉淀后液出口和镍钴富集物出口;其中,高压酸浸装置的浸后矿浆出口与高压中和装置的高压酸浸矿浆入口之间通过管道直接相连。
13.根据本技术处理红土镍矿的系统,通过将高压酸浸装置处理后的矿浆,经管道直接输送至高压中和单元,与加入的蛇纹石矿浆协同进行高压中和;此系统可充分利用褐铁矿高压酸浸处理后的余热,以实现提高蛇纹石的强化浸出、促进al
3
的进一步水解,达到提高镍、钴浸出率,降低碱等辅材消耗的效果。
14.在一种可能的实现方式中,本技术的高压酸浸装置为卧式或立式高压釜。
15.在一种可能的实现方式中,本技术的高压中和单元包括依次相连的高压中和装
置、闪蒸装置和浓密装置,所述高压中和装置为卧式或立式高压釜。
16.在一种可能的实现方式中,本技术的中和除杂单元包括依次相连的中和除杂装置和浓密装置。
17.在一种可能的实现方式中,本技术的镍钴沉淀单元包括依次相连的镍钴沉淀装置、浓密装置和压滤装置。
18.在一种可能的实现方式中,本技术用于连接高压酸浸装置的浸后矿浆出口与高压中和装置的高压酸浸矿浆入口的管道为保温管道,管道外壁还进一步附有加热单元;所述加热单元的加热方式选自电阻丝加热、电磁加热、红外加热中的任一种,其目的是为了保证可充分利用高压酸浸的余热,提高镍、钴浸出率,降低碱等辅材的消耗。
19.在一种可能的实现方式中,高压中和装置还进一步设有加热单元,以在需要时,可对矿浆进行加热处理。
20.第二方面,本技术提供了一种红土镍矿两段加压提取镍钴的工艺,包括以下步骤:步骤一、高压酸浸:在高压酸浸装置中加入褐铁矿型红土镍矿和硫酸溶液,控制二者的液固比、酸矿比和反应条件,完成高压酸浸,得到浸出矿浆;步骤二、高压中和:步骤一中所述浸出矿浆经管道直接进入高压中和单元,向高压中和单元中加入蛇纹石型红土镍矿矿浆,进行高压中和,反应结束后进行液固分离,得到浸出液;步骤三、中和除杂:向步骤二所述的浸出液中添加中和剂,脱除浸出液中的铁、铝杂质,反应结束后进行液固分离,得到除杂后液;步骤四、镍钴沉淀:向步骤三所述的除杂后液中加入沉淀剂,使镍、钴沉淀,反应结束后进行液固分离、洗涤,得到镍钴富集物和沉淀后液。
21.在一种可能的实现方式中,步骤一中,所述褐铁矿型红土镍矿的矿粉粒度小于0.074mm;优选地,粒度小于0.05mm;所述硫酸溶液初始酸度为100~300g/l;具体地,初始酸度为100 g/l、125 g/l、150 g/l、175 g/l、200 g/l、225 g/l、250 g/l、275 g/l或300 g/l等。
22.所述液固比为2:1~10:1ml/g;具体地,液固比为2:1、3:1、4:1、5:1、6:1、7:1、8:1、9:1或10:1等。
23.所述酸矿比为:300~390kg/t
‑
矿。
24.所述反应条件为:浸出温度200~270℃,压力为1.55~5.5mpa,浸出时间为0.5~3.0h,搅拌转速为200~600rpm。具体地,浸出温度为200℃、210℃、220℃、230℃、240℃、250℃、260℃或270℃等;压力为:1.55mpa,1.91mpa,2.32mpa,2.80mpa,3.34mpa,3.97mpa,4.69mpa,5.5mpa等;浸出时间为:0.5h、1h、1.5h、2h、2.5h或3h等;搅拌转速为200rpm、300rpm、400rpm、500rpm或600rpm等。
25.高压酸浸过程中,褐铁矿中的镍、钴、铁、铝、锰等金属氧化物或复合盐直接与硫酸反应转化成为金属离子进入溶液中,其化学反应通式可表示为:me2o
n
(s) 2nh
= 2me
n
nh2o其中me:ni、co、fe、al、mn等有价金属,n:金属化合价。
26.在高温高压条件下,浸出的fe
3
会发生强烈的水解,形成赤铁矿沉淀,并释放出等当量的酸。
27.2fe
3
3h2o(1) = fe2o3(s) 6h
本发明人同时发现,通过控制硫酸与褐铁矿的比例,在浸出温度200~270℃,压力为1.55~5.5mpa的条件下,优选地,酸矿比为:320~360kg/t
‑
矿,温度为230~260℃,压力为2.8~4.69mpa;随着矿浆酸度的降低,少部分al
3
会发生水解,形成草明矾或明矾沉淀并释放出酸。草明矾或明矾在高温高压下不溶于酸,沉淀进入到渣中,从而使溶液al
3
浓度降低。在高温下,会发生如下反应:6al
3
9so
42
‑
14h2o
ꢀ→ꢀ
2(h3o)al3(oh)6(so4)2(s) 10h
5so
42
‑
3al
3
2so
42
‑
m 6h2o = mal3(so4)2(oh)6(s) 6h
其中,m为na
、k
或nh
4
。
28.在一种可能的实现方式中,步骤二中,步骤一的矿浆经管道通过自流或者压力差进入高压中和单元中;所述管道为保温管道,管道的外壁还进一步附有加热单元;所述加热单元的加热方式选自电阻丝加热、电磁加热、红外加热中的任一种;所述蛇纹石型红土镍矿矿浆中,蛇纹石红土镍矿的矿粉粒度小于0.15mm;优选地,小于0.1mm。
29.其中,蛇纹石型红土镍矿的加入量为褐铁矿型红土镍矿的10~100%;具体地,加入量为10%、20%、30%、40%、50%、60%、70%、80%、90%或100%等。
30.高压中和的反应条件包括:反应温度190~250℃,压力为1.25~3.97mpa,浸出时间为0.5~3.0h,搅拌转速为200~600rpm。具体地,反应温度为190℃、200℃、210℃、220℃、230℃、240℃或250℃等;压力为:1.25mpa,1.55mpa,1.91mpa,2.32mpa,2.80mpa,3.34mpa,3.97mpa等;浸出时间为:0.5h、1h、1.5h、2h、2.5h或3h等;搅拌转速为200rpm、300rpm、400rpm、500rpm或600rpm等。优选的反应温度为200~230℃。
31.在上述实现方式中,高压酸浸矿浆(褐铁矿矿浆)不经闪蒸,通过管道直接进入高压中和单元,与加入的蛇纹石矿浆协同进行高压中和,利用褐铁矿矿浆余热,进行高压中和,蛇纹石中的镍、钴、铁、铝、锰等金属氧化物或复合盐直接与褐铁矿矿浆中残留的硫酸反应转化成为金属离子进入溶液中,其化学反应通式可表示为:me2o
n
(s) 2nh
= 2me
n
nh2o其中me:ni、co、fe、al、mn等有价金属,n:金属化合价。
32.在高温高压条件下,浸出的fe
3
会发生强烈的水解,形成赤铁矿沉淀,并释放出等当量的酸。
33.2fe
3
3h2o(1) = fe2o3(s) 6h
al
3
也会大部分水解,形成草明矾或明矾沉淀并释放出酸。
34.6al
3
9so
42
‑
14h2o
ꢀ→ꢀ
2(h3o)al3(oh)6(so4)2(s) 10h
5so
42
‑
3al
3
2so
42
‑
m 6h2o = mal3(so4)2(oh)6(s) 6h
其中,m为na
、k
或nh
4
。
35.从热力学上,当高压釜温度为190℃以上、压力为1.25mpa以上时,尤其是温度为200℃以上、压力为1.55mpa以上时,就有利于上述反应的发生。al
3
水解受环境酸度和温度的影响,高酸度会抑制al
3
的水解,并增大明矾的溶解度,低酸度可促进al
3
的水解,降低明矾石的溶解度。所以在高压酸浸步骤中,al
3
会发生少部分水解,而在高压中和时,由于蛇纹石消耗了残酸,体系中的酸度大大降低,有利于al
3
的进一步水解,绝大部分的al
3
发生水
解反应。而铁、铝水解释放的酸又进一步促进了镍、钴氧化物或复合盐的浸出。
36.nio(s) 2h
= ni
2
h2o(1)coo(s) 2h
= co
2
h2o(1)即,与传统高压酸浸
‑
常压中和不同,本发明通过控制蛇纹石矿的加入量,以及充分利用褐铁矿的余热,保持反应温度190~250℃、压力1.25~3.97mpa的高温高压中和条件,可以使镍钴充分浸出,镍钴浸出率可达95%以上,同时两段的高温高压条件使铁、铝杂质充分水解,高压中和后液中铁铝杂质含量低,可大大降低后续中和除杂工序中碱等辅助材料的消耗,起到简化工序、降低成本的效果。
37.在一种可能的实现方式中,步骤三中,所述中和剂为氧化钙和/或碳酸钙;所述中和除杂的反应件为:ph值为3.8~4.5,反应温度为25~85℃,反应时间为0.5~3.0h。具体地,ph值为3.8、3.9、4.0、4.1、4.2、4.3、4.4或4.5等;反应温度为25℃、30℃、35℃、40℃、45℃、50℃、55℃、60℃、65℃、70℃、75℃、80℃或85℃;反应时间为0.5h、1h、1.5h、2h、2.5h或3h等。
38.在上述实现方式中,中和除铁铝时,加入的中和剂在溶液体系可分解出oh
‑
或者co
32
‑
,与浸出液中的残酸中和生成水,体系oh
‑
变多,oh
‑
与fe
3
、al
3
浓度之积达到金属离子对应氢氧化物的溶度积后,便会沉淀析出,发生如下反应:fe
3
3oh
‑
=fe(oh)3↓
al
3
3oh
‑
=al(oh)3↓
。
39.在一种可能的实现方式中,步骤四中,所述沉淀剂为氢氧化钠、碳酸钠、氧化镁中的一种或多种;所述中和除杂的反应条件为:ph值为7.0~8.5,反应温度为25~85℃,反应时间0.5~3.0h。具体地,ph值为7.0、7.2、7.5、8.0、8.2或8.5等;反应温度为25℃、30℃、35℃、40℃、45℃、50℃、55℃、60℃、65℃、70℃、75℃、80℃或85℃;反应时间为0.5h、1h、1.5h、2h、2.5h或3h等。
40.上述实现方式中,镍钴沉淀原理和中和除杂原理类似,通过加入沉淀剂调节体系ph值,使ni
2
、co
2
生成氢氧化物沉淀析出,发生如下反应:ni
2
2oh
‑
=ni(oh)2↓
co
2
2oh
‑
=co(oh)2↓
。
41.在一种可能的实现方式中,本技术的褐铁矿型红土镍矿为高铁矿石,铁含量为35~50wt%,镍含量为0.6~2.0wt%;具体地,铁含量为35wt%、38wt%、40wt%、42wt%、45wt%、48wt%或50wt%等,镍含量为0.6wt%、0.8wt%、1.0wt%、1.2wt%、1.4wt%、1.6wt%、1.8wt%或2.0wt%等。本技术的蛇纹石型红土镍矿为高镁矿石,氧化镁含量一般大于20wt%,镍含量为0.6~2.0wt%;具体地,镍含量为0.6wt%、0.8wt%、1.0wt%、1.2wt%、1.4wt%、1.6wt%、1.8wt%或2.0wt%等。
42.第三方面,本技术提供前述红土镍矿两段加压提取镍钴的系统及工艺在红土镍矿湿法提取镍钴中的应用。
43.与已有技术相比,本发明具有如下有益效果:本技术提供的系统,通过将高压酸浸装置处理后的矿浆,经管道、尤其是保温管道直接输送至高压中和单元,与加入的蛇纹石矿浆协同进行高压中和;此系统可充分利用褐铁矿高压酸浸处理后的余热,以实现提高蛇纹石的强化浸出、促进al
3
的进一步水解,达到提高镍、钴浸出率,降低碱等辅材消耗的效果。
44.本技术提供的方法充分利用了高压酸浸矿浆余热,降低了生产过程能耗,利用褐
铁矿浸出后残余硫酸在高温高压下继续浸出蛇纹石矿,实现了高压酸浸矿浆余热的高效利用。巧妙地利用了反应发生的条件,采用高压酸浸矿浆余热所能保持的高温高压反应条件,强化浸出蛇纹石矿,同时铁铝水解沉淀释放出的酸进一步浸出镍钴,实现了蛇纹石矿镍钴的高效浸出,蛇纹石矿镍钴浸出率由传统的40~60%提升至85%以上,大大提高了镍资源的利用率。另外,两段高温高压条件,使浸出液中的铁、铝充分发生水解沉淀反应,水解沉淀释放的新酸用来浸出蛇纹石矿,大大提高了硫酸的利用率,降低了酸耗。同时,浸出液中铁、铝含量较传统高压酸浸工艺明显降低,降低了后续中和用碱量,大大简化了后续中和除杂工序,降低了辅助材料消耗。
45.本技术的系统及方法对矿石品位无特殊要求,原料适应性广,可高效联合处理褐铁矿型和蛇纹石型红土镍矿。
附图说明
46.为了更清楚地说明本技术实施例的技术方案,下面将对本技术实施例中所需要使用的附图作简单地介绍,应当理解,以下附图仅示出了本技术的某些实施例,因此不应被看作是对范围的限定,对于本领域普通技术人员来讲,在不付出创造性劳动的前提下,还可以根据这些附图获得其他相关的附图。
47.图1为现有技术的典型工艺流程图;图2为本发明红土镍矿两段加压提取镍钴的系统结构示意图图3为本发明实施例1提供的工艺流程图。
具体实施方式
48.为使本技术实施例的目的、技术方案和优点更加清楚,下面将对本技术实施例中的技术方案进行清楚、完整地描述。实施例中未注明具体条件者,按照常规条件或制造商建议的条件进行。所用试剂或仪器未注明生产厂商者,均为可以通过市售购买获得的常规产品。
49.参见图2,所示为本发明实施例提供的一种红土镍矿两段加压提取镍钴系统的结构示意图。
50.由图2可知,所述红土镍矿两段加压提取镍钴的系统包括高压酸浸装置100,以用于对褐铁矿型红土镍矿进行高温高压酸浸,所述高压酸浸装置100具有褐铁矿型红土镍矿矿浆入口101、硫酸入口102和浸后矿浆出口103;高压中和单元200,以用于对高压酸浸后的矿浆进行高温高压中和处理,所述高压中和单元具有高压酸浸矿浆入口201、蛇纹石型红土镍矿矿浆入口202、高压中和后液出口203和高压中和底流出口204;中和除杂单元300,以用于对高压中和处理后的矿浆进行中和除杂处理,所述中和除杂单元300具有高压中和后液入口301、中和剂入口302、中和除杂后液出口303和中和除杂底流出口304;镍钴沉淀单元400,以用于对中和除杂后液进行沉淀处理,所述镍钴沉淀单元400具有中和除杂后液入口401、沉淀剂入口402、沉淀后液出口403和镍钴富集物出口404;其中,高压酸浸装置100的浸后矿浆出口103与高压中和单元200的高压酸浸矿浆
入口201之间通过管道104直接相连。
51.根据本发明的系统,下面结合实施例对本发明的提取工艺及其效果进行具体说明。
52.以下实施例及对比例中使用的为国外某红土镍矿,其主要元素含量见下表1。褐铁矿型红土镍矿镍、钴含量分别为1.01%和0.076%,铁含量较高为47.84%,镁含量为0.17%,除此之外还含有一定数量的铝、硅、铬以及少量的锰、锌等。蛇纹石型红土镍矿主要的元素为硅、镁、铁和镍,其中镍、钴含量分别为1.55%和0.066%,镁的含量为11.05%,硅的含量为16.72%,铁的含量为16.38%。
53.表1红土镍矿主要成分表
元素nicocuznmnmgcaalfesicr褐铁矿型1.010.076/0.270.480.170.0254.1647.841.751.93蛇纹石型1.550.0660.010.0230.3711.051.061.9516.3816.720.67
图3为本技术的工艺流程图,具体相关工艺参数可参见下述实施例。
54.实施例11
‑
1、高压酸浸褐铁矿型红土镍矿经破碎细磨后,取矿粉粒度为100%过0.074mm的上述褐铁矿100g,控制高压酸浸反应条件如下:加入硫酸溶液(初始硫酸浓度115g/l),控制液固比2:1,酸矿比:330kg
·
硫酸/t
·
矿,温度为250℃,压力为3.97mpa,搅拌转速为500rpm,时间1h。取少量矿浆液固分离、洗涤、烘干后送分析。
55.结果分析:渣含镍0.025%,渣含钴<0.005%,渣含铝1.89%,镍浸出率98.58%。
[0056]1‑
2、高压中和高压酸浸矿浆经管道进入高压中和单元,加入经矿粉细磨后,粒度为100%过0.15mm的蛇纹石矿浆进行高压中和反应。控制高压中和反应条件如下:蛇纹石型红土镍矿加入量为褐铁矿型红土镍矿的25wt%,蛇纹石矿矿浆浓度为35wt%,反应温度为230℃,压力为2.80mpa,搅拌转速为500rpm,反应时间1h。反应结束后矿浆液固分离、洗涤、烘干后送分析。
[0057]
结果分析:渣含镍0.06%,渣含钴<0.005%,该段镍浸出率为92.96%,两段镍总浸出率95.81%。浸出液成分如下表1
‑
1。
[0058]
表1
‑
1高压中和浸出液主要成分含量表元素fenicoal含量/(g/l)0.683.090.190.53可见,镍矿中的铁、铝已大部分水解沉淀,较少存在溶液中,实现了镍钴和铁铝的选择性浸出分离。
[0059]1‑
3、中和除杂取上述浸出液,使用生石灰乳液作为中和剂,进行中和除杂。控制中和除杂反应条件如下:温度为75℃,反应时间为2h,石灰乳浓度为20%,终点ph值为4.2,其中,氧化钙消耗:3.06kg
·
氧化钙/m3·
液;反应结束,液固分离。
[0060]
结果分析:渣量为5.4kg
·
渣/m3·
液,液计除铁率达99.03%,铝沉淀率为95.22%。
[0061]1‑
4、镍钴沉淀
取上述中和除杂后液,使用氢氧化钠作为沉淀剂,进行镍钴沉淀。控制镍钴沉淀反应条件如下:温度为70℃,反应时间为3h,终点ph值为7.8。反应结束,液固分离。
[0062]
结果分析:液计镍沉淀率为96.63%,钴沉淀率为95.86%。得到的镍钴富集物(氢氧化镍钴中间产品)成分见下表1
‑
2表1
‑
2镍钴富集物主要成分表元素caconimgcrmncuznfeal含量/wt%0.153.9240.851.460.01935.250.100.730.0760.24可见,镍钴富集物中镍含量为40.85%,钴含量为3.92%,可用于进一步精炼制备电池级硫酸镍和电池级硫酸钴。
[0063]
实施例2与实施例1不同的是,本实施例高压中和采用的温度为190℃,压力为1.25mpa,其他步骤与实施例1相同。
[0064]
结果分析:高压中和反应后,渣含镍为0.08%,渣含钴<0.005%,该段镍浸出率为85.13%,两段镍总浸出率为93.36%。浸出液成分如下表2。
[0065]
表2高压中和浸出液主要成分含量表元素fenicoal含量/(g/l)2.483.370.222.63在中和除杂步骤中,控制终点ph值为4.2时,氧化钙消耗:4.71kg
·
氧化钙/m3·
液,渣量为23.78kg
·
渣/m3·
液。
[0066]
实施例3高压酸浸步骤中,与实施例1不同的是,温度控制为225℃,压力为2.55mpa,其他步骤与实施例1相同。
[0067]
结果分析:高压酸浸后,渣含镍0.09%,渣含钴<0.005%,镍浸出率为95.25%。
[0068]
高压中和步骤中,与实施例1不同的是,采用的温度为200℃,压力为1.55mpa,其他步骤与实施例1相同。
[0069]
结果分析:高压中和后,渣含镍0.12%,渣含钴<0.005%,该段镍浸出率为88.25%,两段镍总浸出率为90.64%。浸出液含铁0.52g/l,含铝0.63g/l。
[0070]
在中和除杂步骤中,控制终点ph值4.2时,氧化钙消耗:3.35kg
·
氧化钙/m3·
液,渣量为5.82kg
·
渣/m3·
液实施例4高压酸浸步骤中,与实施例1不同的是,温度控制为200℃,压力为1.55mpa,其他步骤与实施例1相同。
[0071]
结果分析:高压酸浸后,渣含镍0.10%,渣含钴<0.005%,镍浸出率92.33%。
[0072]
高压中和步骤中,与实施例1不同的是,采用的温度为190℃,压力为1.25mpa,其他步骤与实施例1相同。
[0073]
结果分析:高压中和后,渣含镍0.15%,渣含钴<0.005%,该段镍浸出率为85.39%,两段镍总浸出率89.64%。浸出液含铁1.10g/l,含铝1.28g/l。
[0074]
在中和除杂步骤中,控制终点ph值4.2时,氧化钙消耗:4.28kg
·
氧化钙/m3·
液,渣量为16.25kg
·
渣/m3·
液。
[0075]
实施例5高压酸浸步骤中,与实施例1不同的是,温度控制为270℃,压力为5.5mpa,其他步骤与实施例1相同。
[0076]
结果分析:高压酸浸后,渣含镍0.011%,渣含钴<0.005%,镍浸出率为99.11%。
[0077]
高压中和步骤中,与实施例1不同的是,采用的温度为250℃,压力为3.97mpa,其他步骤与实施例1相同。
[0078]
结果分析:高压中和后,渣含镍0.026%,渣含钴<0.005%,该段镍浸出率为95.69%,两段镍总浸出率98.02%。浸出液含铁0.38g/l,含铝0.23g/l。
[0079]
在中和除杂步骤中,控制终点ph值4.2时,氧化钙消耗:2.82kg
·
氧化钙/m3·
液,渣量为4.67kg
·
渣/m3·
液。
[0080]
实施例7与实施例1不同的是,本实施例高压中和采用的温度为180℃,压力为1.0mpa,其他步骤与实施例1相同。
[0081]
结果分析:高压中和反应后,渣含镍为0.12%,渣含钴0.008%,该段镍浸出率为84.64%,两段镍总浸出率为87.95%。浸出液成分如下表3。
[0082]
表3高压中和浸出液主要成分含量表元素fenicoal含量/(g/l)2.673.260.192.86在中和除杂步骤中,控制终点ph值为4.2时,氧化钙消耗:5.67kg
·
氧化钙/m3·
液,渣量为28.13kg
·
渣/m3·
液。
[0083]
从以上实施例的结果中可看出,采用高压酸浸
‑
高压中和两段加压工艺进行提取镍钴,大大提高了蛇纹石矿中镍钴浸出率,而且降低了后续中和用碱量和渣量。其中,高压中和步骤中,在温度为250℃、压力为3.97mpa时,蛇纹石矿中镍钴浸出率最高,中和用碱量最少;而在温度为180℃、压力为1.0mpa时,蛇纹石矿中镍钴浸出率较低,中和用碱量较多。
[0084]
对比例1与实施例1不同的是,高压酸浸矿浆冷却后,在常压中加入蛇纹石矿进行中和反应。反应温度为90℃,时间为4h。
[0085]
结果分析:渣含镍0.19%,渣含钴0.008%,该段镍浸出率为55.55%,两段镍总浸出率82.63%,浸出液成分如下表4。
[0086]
表4高压中和浸出液主要成分含量表元素fenicoal含量/(g/l)1.323.620.246.53取上述浸出液进行中和除杂,反应条件与实施例1相同,其中,氧化钙消耗:8.70kg
·
氧化钙/m3·
液。反应结束,液固分离。渣量为17.68
·
渣/m3·
液。铁铝沉淀率在95%左右。
[0087]
从结果可以看出,传统高压酸浸
‑
常压中和工艺,不仅常压中和反应耗时长,而且,蛇纹石矿中镍浸出率低,只有55.55%,另外,浸出液铁铝含量较高,中和除杂中氧化钙用量和渣量大大增加。
[0088]
对比例2
与实施例1不同的是,针对褐铁矿的酸浸是在常压下进行的,其中浸出温度为95℃,反应时间为6h;结果分析:渣含镍0.24%,渣含钴0.007%,镍浸出率86.05%。
[0089]
与实施例1不同的是,二段加入蛇纹石型红土镍矿高压浸出步骤中,反应温度为150℃,压力为0.48mpa。结果分析:渣含镍0.21%,渣含钴0.016%,该段镍浸出率87.50%,两段镍总浸出率87.03%,浸出液成分如下表5。
[0090]
表5高压中和浸出液主要成分含量表元素fenicoal含量/(g/l)5.324.410.184.24取上述浸出液进行中和除杂,反应条件与实施例1相同,其中,氧化钙消耗:6.04kg氧化钙/m3·
液。反应结束,液固分离。渣量为37.18kg
·
渣/m3·
液。铁铝沉淀率在95%左右。
[0091]
从结果可以看出,常压酸浸
‑
高压中和工艺中,其存在镍钴浸出率不高,浸出液含铁铝高,后续中和除杂渣量大,镍钴损失率高的问题。
[0092]
对比例3与对比例2不同的是,针对蛇纹石矿的酸浸是在常压下进行的,其中浸出温度为为110℃,反应时间为8min;结果分析:渣含镍0.22%,渣含钴0.008%,镍浸出率84.46%。
[0093]
与对比例2不同的是,二段高压浸出步骤中,加入了褐铁矿,反应温度为220℃,压力为2.32mpa。结果分析:渣含镍0.19%,渣含钴0.008%,该段镍浸出率89.30%,两段镍总浸出率86.04%,浸出液成分如下表6。
[0094]
表6高压中和浸出液主要成分含量表元素fenicoalmg含量/(g/l)1.834.270.292.8612.01取上述浸出液进行中和除杂,反应条件与实施例1相同,其中,氧化钙消耗:5.82kg
·
氧化钙/m3·
液。反应结束,液固分离。渣量为28.94kg
·
渣/m3·
液。铁铝沉淀率在95%左右。
[0095]
从结果可以看出,在上述的常压酸浸蛇纹石矿
‑
高压中和褐铁矿工艺中,其存在镍钴浸出率不高,浸出液含铁铝高,后续中和除杂渣量大,滤液含镁高可能存在设备结垢严重的问题。
[0096]
以上所述仅为本技术的实施例而已,并不用于限制本技术的保护范围,对于本领域的技术人员来说,本技术可以有各种更改和变化。凡在本技术的精神和原则之内,所作的任何修改、等同替换、改进等,均应包含在本技术的保护范围之内。
再多了解一些
本文用于企业家、创业者技术爱好者查询,结果仅供参考。