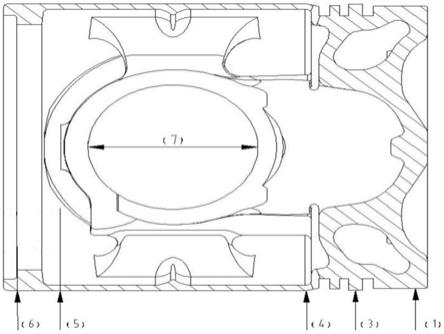
1.本发明专利属于整体式活塞加工制造领域,涉及一种柴油机整体式活塞进行整体硬化处理的方法,特别涉及到基于多次时效处理和离子氮化相结合的方式对中高速柴油机整体式球墨铸铁活塞进行整体硬化处理,并且氮化后变形可控,不需要再精加工。
背景技术:
2.活塞是柴油机的关键零部件之一,其直接接触燃烧室,工作的时候承受高温、高压、冲击和气体腐蚀,工作条件十分恶劣,对其疲劳寿命、抗磨损性能要求很高。
3.某型号中高速柴油机整体式活塞采用球墨铸铁浇铸而成,然而相比钢制活塞,球墨铸铁活塞的疲劳强度和抗磨损性较差,同时其采用斜环槽设计,无法采用感应淬火技术对其环槽进行硬化处理。为了提高整体强度以及环槽部位的抗磨损性能,这就要求我们寻找一种合适的表面硬化方法对活塞进行整体表面强化。
4.传统的整体式表面硬化方式例如电镀、渗碳和氮化,其中因结合力和抗冲击性能原因,电镀工艺不适用于需要承受高周期性载荷的中高速柴油机铸铁活塞,而渗碳工艺则完全不适用于铸铁件的硬化。相对于整体式球墨铸铁活塞,氮化处理是一种较为合适的整体式表面处理方法,但是中高速柴油机活塞的加工尺寸要求很高,例如环槽和裙部型线,而球墨铸铁活塞在氮化处理后的,受机加工应力释放、组织应力、热应力的综合作用,往往变形量较大,为了纠正尺寸,不得不在硬化后的表面上再次加工,其机加工难度很大,对刀具要求很高。
技术实现要素:
5.本发明的目的在于一种柴油机整体式活塞进行整体硬化处理的方法,以寻求合适的去应力工艺和氮化处理工艺,来对球墨铸铁活塞进行表面硬化处理,并抑制其变形量,达到氮化后不再进行车削加工的目的。
6.为实现上述目的,本发明采用以下技术方案:
7.一种柴油机整体式活塞进行整体硬化处理的方法,所述整体式活塞采用球墨铸铁浇注而成,所述方法包括以下步骤:
8.a)回火:当整体式活塞采用qt700材料时,铸造后进行珠光体化正火,再使用井式炉进行575
‑
585℃保温3
‑
5h的回火处理,以消除正火处理冷却后产生的热应力和组织应力;当整体式活塞采用qt450材料时,铸造后进行铁素体化退火,退火后再使用井式炉加热至745
‑
755℃保温2
‑
4h,炉冷至450
‑
550℃出炉空冷,不进行再回火;
9.b)第一次时效:在经步骤a)处理后的铸造件进行粗加工后,使用井式炉升温进行565
‑
575℃保温5
‑
7h的时效处理,然后降温出炉,其中,升温速率≤180℃/h,炉冷降温至180℃以下出炉;
10.c)第二次时效:在经步骤b)处理后的铸造件进行半精加工后,使用气氛保护炉升温进行565
‑
575℃保温5
‑
7h的时效处理,然后降温出炉,其中,升温速率≤180℃/h,炉冷降
温至180℃以下出炉;
11.d)精加工:对经步骤c)第二次时效处理后的铸造件进行最终尺寸的精加工,并且在精加工时预留0.01
‑
0.02mm的变形余量;
12.e)氮化处理:对步骤d)精加工后的铸造件进行辉光离子氮化处理,处理时控制升温速率≤60℃/h,并且控制保温温度450
‑
550℃,氮化处理结束时炉冷至≤100℃出炉。
13.根据本发明的方法,优选地,步骤a)中,当整体式活塞采用qt700材料时,铸造后进行珠光体化正火,再使用井式炉进行578
‑
582℃保温3.5
‑
4.5h的回火处理,以消除正火处理冷却后产生的热应力和组织应力;当整体式活塞采用qt450材料时,铸造后进行铁素体化退火,退火后再使用井式炉加热至7485
‑
752℃保温2.5
‑
3.5h,炉冷至480
‑
520℃出炉空冷,不进行再回火。
14.根据本发明的方法,优选地,步骤b)中,在经步骤a)处理后的铸造件进行粗加工后,使用井式炉升温进行568
‑
572℃保温5.5
‑
6.5h的时效处理,然后降温出炉。在一种实施方式中,步骤b)中,升温速率为120
‑
180℃/h,比如140、150或160℃/h。
15.根据本发明的方法,优选地,步骤c)中,使用气氛保护炉升温进行568
‑
572℃保温5.5
‑
6.5h的时效处理,然后降温出炉。在一种实施方式中,步骤c)中,升温速率为120
‑
180℃/h,比如140、150或160℃/h。
16.在本发明的步骤d中,为纠正第二次时效处理后的变形,做最终尺寸的精加工,因为渗氮导致的组织变化是不可避免的,需预留0.01
‑
0.02mm的变形余量,比如外径预留0.01
‑
0.02mm或0.015mm的胀大量。
17.根据本发明的方法,优选地,步骤e)中,进行氮化处理时,使用顶柱工装,支撑活塞内腔,并将活塞头部朝上、止口端朝下悬空将活塞摆放在炉内,以降低因活塞头部质量较大的原因对裙部造成的压应力,减少裙部变形。
18.根据本发明的方法,优选地,步骤e)中,光离子氮化处理,处理时控制升温速率为50
‑
60℃/h,并且控制保温温度500
‑
550℃。本领域技术人员可以理解,氮化时间和其余氮化参数可以依照氮化层硬度和深度调整确定。
19.在本发明的一种实施方式中,步骤a)中,当整体式活塞采用qt700材料时,铸造后进行珠光体化正火,再使用井式炉进行580℃保温4h的回火处理,以消除正火处理冷却后产生的热应力和组织应力;当整体式活塞采用qt450材料时,铸造后进行铁素体化退火,退火后再使用井式炉加热至750℃保温3h,炉冷至500℃出炉空冷,不进行再回火;
20.步骤b)中,在经步骤a)处理后的铸造件进行粗加工后,使用井式炉升温进行570℃保温6h的时效处理,然后降温出炉;
21.步骤c)中,在经步骤b)处理后的铸造件进行半精加工后,使用气氛保护炉升温进行570℃保温6h的时效处理,然后降温出炉;
22.步骤d)中,对经步骤c)第二次时效处理后的铸造件进行最终尺寸的精加工,并且在精加工时预留0.01
‑
0.02mm的变形余量;
23.步骤e)中,对步骤d)精加工后的铸造件进行辉光离子氮化处理,处理时控制升温速率55℃/h,并且控制保温温度500℃。
24.本发明还提供了根据上述方法制得的整体式活塞。
25.本发明综合采用了降低加工应力的多种措施,降低氮化处理后的本体变形,保证
尺寸可控,不需进行后续机加工,大大降低了加工成本,提高了产品一次性合格率。
26.本发明不仅适用于柴油机整体式球墨铸铁活塞,同样适合应用于所有需要表面氮化处理且对变形量要求较高的球墨铸铁件。
附图说明
27.图1为实施例1
‑
3的活塞剖面检测位置示意图。
具体实施方式
28.下面结合实施例和附图,对本发明予以进一步的说明,但本发明不限于所列出的实施例,还应包括在本发明申请所附权利要求书定义的技术方案的等效改进和变形。
29.实施例1
30.某a型号整体球铁活塞,成品缸径185mm,销孔浮空设计,材料qt700,毛坯正火处理后为珠光体基体组织,以此毛坯进行加工,分别经过回火(步骤a)
→
粗车
→
第一次时效(步骤b)
→
半精车
→
第二次时效(步骤c)
→
精车(外径预留0.02mm胀大量,步骤d)
→
氮化工序(步骤e)。
31.其中,步骤a)中,使用井式炉进行578℃保温4.5h的回火处理,以消除正火处理冷却后产生的热应力和组织应力;
32.步骤b)中,在经步骤a)处理后的铸造件进行粗加工后,使用井式炉升温进行572℃保温5.5h的时效处理,然后降温出炉;
33.步骤c)中,在经步骤b)处理后的铸造件进行半精加工后,使用气氛保护炉升温进行568℃保温6.5h的时效处理,然后降温出炉;
34.步骤d)中,对经步骤c)第二次时效处理后的铸造件进行最终尺寸的精加工,并且在精加工时外径预留0.02mm的胀大量;
35.步骤e)中,对步骤d)精加工后的铸造件进行辉光离子氮化处理,处理时控制升温速率50℃/h,并且控制保温温度500℃。
36.最终检测结果如下表,扣除预留变形量之后,各部位尺寸与标准尺寸差距在
‑
0.01~0.02(mm)之间,满足允许的公差要求。检测位置示意图如图1。
[0037][0038]
注:“/”表示未检出变化值,下同。
[0039]
实施例2
[0040]
某b型号整体球铁活塞,成品缸径230mm,销孔浮空设计,材料qt700,毛坯正火处理后为珠光体基体组织,以此毛坯进行加工,分别经过回火(步骤a)
→
粗车
→
第一次时效(步骤b)
→
半精车
→
第二次时效(步骤c)
→
精车(外径预留0.02mm胀大量,步骤d)
→
氮化工序(步骤e)。
[0041]
其中,步骤a)中,使用井式炉进行582℃保温3.5h的回火处理,以消除正火处理冷却后产生的热应力和组织应力;
[0042]
步骤b)中,在经步骤a)处理后的铸造件进行粗加工后,使用井式炉升温进行568℃保温6.5h的时效处理,然后降温出炉;
[0043]
步骤c)中,在经步骤b)处理后的铸造件进行半精加工后,使用气氛保护炉升温进行572℃保温5.5h的时效处理,然后降温出炉;
[0044]
步骤d)中,对经步骤c)第二次时效处理后的铸造件进行最终尺寸的精加工,并且在精加工时外径预留0.02mm的胀大量;
[0045]
步骤e)中,对步骤d)精加工后的铸造件进行辉光离子氮化处理,处理时控制升温速率60℃/h,并且控制保温温度500℃。
[0046]
最终检测结果如下表,扣除预留变形量之后,各部位尺寸与标准尺寸差距在
‑
0.01~0.02(mm)之间,满足允许的公差要求。检测位置示意图如图1。
[0047][0048]
实施例3
[0049]
某c型号整体球铁活塞,成品缸径160mm,材料qt450,毛坯退火处理后为铁素体基体组织,以此毛坯进行加工,分别经过步骤a
→
粗车
→
第一次时效(步骤b)
→
半精车
→
第二次时效(步骤c)
→
精车(外径预留0.01mm胀大量,步骤d)
→
氮化工序(步骤e)。
[0050]
其中,步骤a)中,对退火后的铁素体使用井式炉加热至750℃保温3h,炉冷至500℃出炉空冷,不进行再回火;
[0051]
步骤b)中,在经步骤a)处理后的铸造件进行粗加工后,使用井式炉升温进行570℃保温6h的时效处理,然后降温出炉;
[0052]
步骤c)中,在经步骤b)处理后的铸造件进行半精加工后,使用气氛保护炉升温进行570℃保温6h的时效处理,然后降温出炉;
[0053]
步骤d)中,对经步骤c)第二次时效处理后的铸造件进行最终尺寸的精加工,并且在精加工时外径预留0.01mm的胀大量;
[0054]
步骤e)中,对步骤d)精加工后的铸造件进行辉光离子氮化处理,处理时控制升温速率55℃/h,并且控制保温温度550℃。
[0055]
最终检测结果如下表,扣除预留变形量之后,各部位尺寸与标准尺寸差距在
‑
0.01~0.01(mm)之间,满足允许的公差要求。检测位置示意图如图1。
[0056]
再多了解一些
本文用于企业家、创业者技术爱好者查询,结果仅供参考。