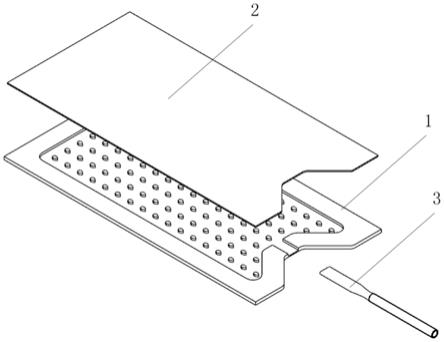
1.本发明涉及电子设备热管理技术领域。
背景技术:
2.随着微电子技术的迅猛发展,电子器件尤其是消费电子产品逐渐朝高热流密度、轻薄化方向发展,狭小空间内小型电子元件热量的高效疏导已成为一个亟需解决的挑战。超薄相变传热装置(厚度小于2mm)作为一种高效的二维两相传热器件,利用工质的气液相变潜热,可将电子元件的局部热点的热量迅速传导并扩散至面积较大的冷凝面上,从而具有热阻低、均温性好等优点,目前已在狭小空间内高功率元件散热中得到广泛应用。
3.超薄相变传热装置的工作原理与普通热管相同,热端蒸发的气态工质在压差作用下输运到冷端,冷凝成液态工质后通过毛细芯抽吸至热源,完成一个工质循环。要保证热管正常工作,毛细芯能提供的最大毛细力(
△
p
c
)
max
必须能克服以下三个阻力之和:液态工质从蒸发段到冷凝段的流动阻力
△
p
l
,液态工质从冷凝段返回蒸发段的流动阻力
△
p
v
,热管工作方位决定的重力压力
△
p
g
。即必须满足以下条件
4.(
△
p
c
)
max
≥
△
p
l
△
p
v
△
p
g
5.随着相变传热装置厚度的不断降低,蒸汽腔空间不断被压缩导致气态工质流速迅速增加,将带来两个后果,一是液态气流动压降
△
p
v
上升,二是由于气液逆向运动导致的气液界面剪切力增大,间接造成液态工质回流阻力
△
p
l
增大。常规相变传热装置毛细芯一般为单一尺度结构,存在毛细力与渗透率(表征液体流动阻力)难以兼顾的问题。同时,为了结构强度考虑需在蒸发腔内部设置圆形加强筋,从未带来为气液两相工质的流动带来负面影响。因此,超薄相变传热装置特殊的尺寸特性对相变传热装置毛细性和整体构型的设计优化提出了新的要求。
技术实现要素:
6.本发明提供一种超薄相变传热装置,通过加强筋与毛细芯的改良,纾解了超薄相变传热装置毛细力不足以及超薄空间下气液界面剪切力过高的难题,提高了超薄平板的毛细极限与携带极限,强化了超薄相变传热装置的传热性能。
7.本发明提出的一种超薄相变传热装置,包括底板、盖板、充液管和工质;所述底板、盖板和充液管焊接成型后通过充液管冲入定量工质,工质在底板和盖板形成的空腔中循环流动;所述底板为长方体结构,一侧加工出凹腔、阵列加强筋和充液管预留槽;所述加强筋为翼型结构,前半部分迎着气态工质来流方向使用圆形结构,后半部分使用抛物线结构;所述盖板为长方体结构,一侧加工出毛细芯和加强筋基座,毛细芯为槽道结构,加强筋基座与加强筋平面尺寸相同。
8.进一步的,所述槽道根据加强筋基座形状做适应性绕流设计。
9.进一步的,所述槽道使用界面化学氧化法改性,在槽道外表面上覆盖纳米球
‑
纳米棒
‑
纳米花三层复合纳米结构。
10.进一步的,所述超薄相变传热装置厚度为0.5至1.5mm。
11.本发明与现有技术相比,具有以下优点:
12.本发明的超薄相变传热装置采用翼型加强筋和经过纳米结构修饰的绕流槽道毛细芯,在不影响超薄相变传热装置结构强度的前提下可减小气态工质输运速度和压降,降低气液界面阻力,提高毛细芯毛细力,强化了超薄相变传热装置的传热性能。
附图说明
13.图1为本发明装置的爆炸视图。
14.图2为本发明装置的剖视图。
15.图3为本发明装置底板的三维视图。
16.图4为图3中a的局部放大图。
17.图5为本发明装置盖板的三维视图。
18.图6为图5中b的局部放大图
19.图7为本发明装置绕流槽道毛细芯改良示意图。
20.图8为本发明装置纳米结构修饰绕流槽道毛细芯改良示意图。
21.图9为超薄相变传热装置工作状态应力云图,其中(a)为圆形加强筋,(b)为翼型加强筋。
22.图10为超薄相变传热装置气态工质流速图,其中(a)为圆形加强筋,(b)为翼型加强筋。
23.图11为超薄相变传热装置气态工质压力云图,其中(a)为圆形加强筋,(b)为翼型加强筋。
24.图中有:底板1、盖板2、充液管3、加强筋11、充液口12,槽道21和加强筋底座22。
具体实施方式
25.下面结合附图对发明进行进一步描述:
26.图1给出了本发明装置的爆炸视图,具体包括立包括底板1、盖板2、充液管3和工质。底板、盖板、充液管均使用紫铜材质。充液管采用外径2mm的铜管,一侧经机械压扁至0.6mm后与底板和盖板焊接。底板、盖板和充液管焊接成型后总厚度为1.2mm,再通过充液管注入定量工质。
27.图2给出了本发明装置的剖视图。焊接完成的底板1和盖板2成为一体,工质填充在盖板2的毛细性中。
28.图3给出了本发明装置底板的三维视图。底板1一侧加工出凹槽、加强筋11以及充液口12。底板长100mm,宽40mm,凹槽距边5mm,深度0.6mm。
29.图4给出了图3中a的局部放大图。加强筋11前段直径1mm,后段为二次曲线,加强筋整体呈阵列排列,间距4mm。充液口12和凹槽齐平,宽度3.3mm。
30.图5给出了本发明装置盖板的三维视图。盖板2为长方体结构,一侧加工出毛细芯21和加强筋基座22,毛细芯为槽道结构,距边4mm。盖板尺寸略小于底板,长宽分别为98mm和38mm。
31.图6给出了图3中b的局部放大图。槽道21高、宽、间距同为0.2mm,加强筋底座22高
0.2mm,截面尺寸与加强筋11相同。
32.图7给出了本发明装置绕流槽道毛细芯改良示意图。一般槽道结构为沿传热方向的竖直槽道,但对于具有加强筋的相变传热装置,加强筋结构会堵塞一部分的液体流动通道,如图7(a)所示,填充部分为下凹的槽道结构,中间的三股流道因为加强筋的存在变为死区,严重影响了相变传热装置内部工质的回流。可以设计出如图7(b)所示的绕流槽道结构,原先中间区域被堵塞的流道可以通过绕流的方式绕过加强筋,有效流通面积可增加50%。
33.图8给出了本发明装置纳米结构修饰绕流槽道毛细芯改良示意图。槽道毛细芯分别经过丙酮以及稀硫酸清洗后放入氧化剂(氢氧化钠浓度2.5mol/l,过硫酸铵浓度0.065mol/l)中反应10分钟,取出清洗后在260℃空气氛围中氧化6小时。sem照片显示,槽道表面基础上可生成了均一的多尺度氧化铜纳米结构,有效改善毛细性的润湿性能,提高毛细抽力。
34.图9给出了工质压力0.2mp的极限情况下超薄相变传热装置工作状态应力云图,其中(a)为圆形加强筋,(b)为翼型加强筋。圆形加强筋结构超薄相变传热装置内部的应力分布更为均为,最大应力12.7mp。翼型加强筋结构超薄相变传热装置内部最大应力13.2mp,比圆形加强筋结构稍大,同时应当注意到应力集中主要发生在翼型结构的尾部,尾部越尖,应力最大,因此从超薄相变传热装置的强度考虑,尾部尖角不易过小。考虑到紫铜的屈服强度为70mp,翼型加强筋结构可满足超薄相变传热装置的强度需求。
35.图10给出了超薄相变传热装置气态工质流线图,其中(a)为圆形加强筋,(b)为翼型加强筋。相变传热装置内部的速度最高值出现在加强筋两侧下游位置,翼型加强筋相变传热装置气态工质最高速度为2.17m/s,比圆形加强筋降低8%。工质最高流速的降低益于两个方面,一是工质的流通截面略微增加,二是工质的流型更为规整,流线更为舒展。
36.图11给出了超薄相变传热装置气态工质压力云图,其中(a)为圆形加强筋,(b)为翼型加强筋。圆形加强筋尾部出现了压力分布不均的情况,这将导致工质发生粘性损耗,增加流动压降。翼型加强筋则可以有效改善上述情况,最大压降可降低7.1%。
再多了解一些
本文用于企业家、创业者技术爱好者查询,结果仅供参考。