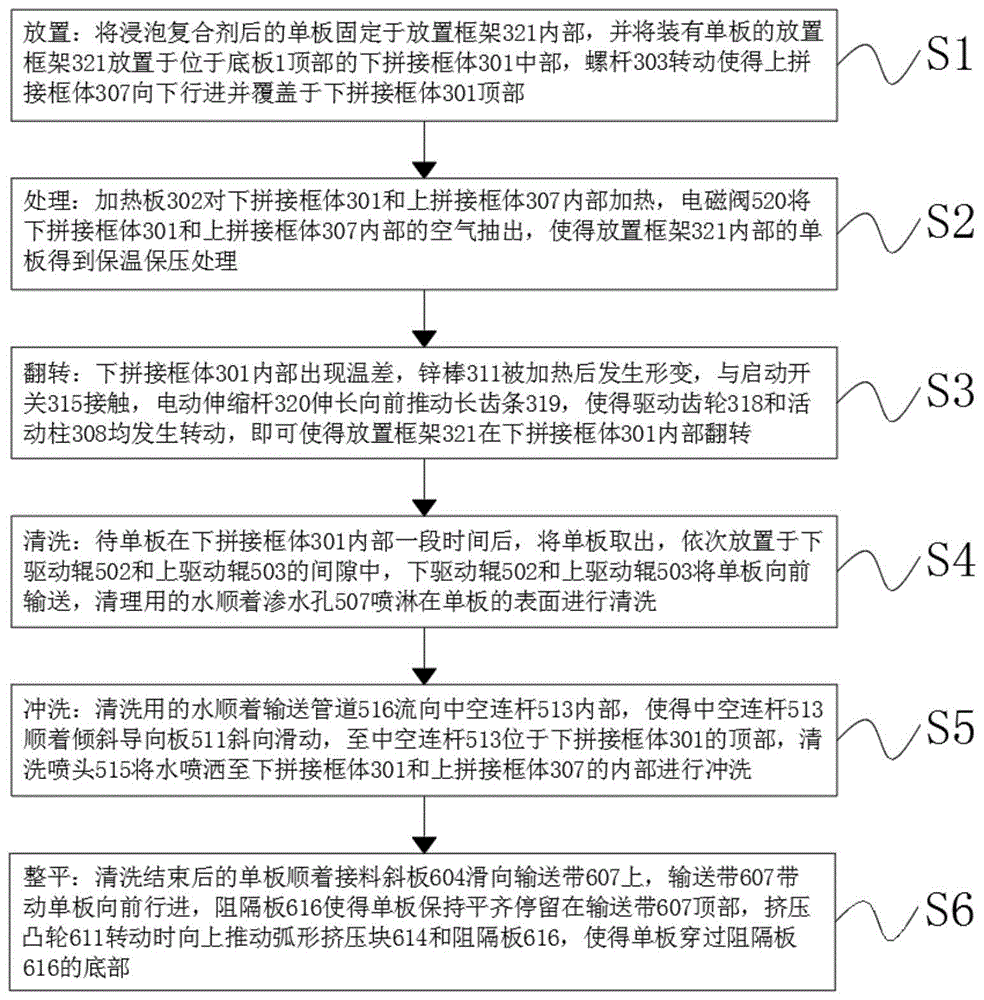
本发明涉及胶合板制备技术领域,具体为一种胶合板的制备方法。
背景技术:
胶合板是家具常用材料之一,为人造板三大板之一,亦可供飞机、船舶、火车、汽车、建筑和包装箱等作用材,胶合板是由木段旋切成单板或由木方刨切成薄木,再用胶粘剂胶合而成的三层或多层的板状材料,通常用奇数层单板,并使相邻层单板的纤维方向互相垂直胶合而成,通常其表板和内层板对称地配置在中心层或板芯的两侧,胶合板所使用的单板在胶合前需要浸泡复合剂,来提高单板的韧性和抗压能力;
但是目前胶合板所使用的单板浸泡复合剂后直接冲洗胶合,复合剂并未充分扩散至单板的内部,导致制备的胶合板抗压能力弱,进而使得胶合板质量差影响其正常使用,所以本发明提供了一种胶合板的制备方法,来满足人们的需求。
技术实现要素:
本发明提供一种胶合板的制备方法,可以有效解决上述背景技术中提出的胶合板所使用的单板浸泡复合剂后直接冲洗胶合,复合剂并未充分扩散至单板的内部,导致制备的胶合板抗压能力弱,进而使得胶合板质量差影响其正常使用的问题。
为实现上述目的,本发明提供如下技术方案:一种胶合板的制备方法,包括如下步骤:
s1:放置:将浸泡复合剂后的单板固定于放置框架内部,并将装有单板的放置框架放置于位于底板顶部的下拼接框体中部,螺杆转动使得上拼接框体向下行进并覆盖于下拼接框体顶部;
s2:处理:加热板对下拼接框体和上拼接框体内部加热,电磁阀将下拼接框体和上拼接框体内部的空气抽出,使得放置框架内部的单板得到保温保压处理;
s3:翻转:下拼接框体内部出现温差,锌棒被加热后发生形变,与启动开关接触,电动伸缩杆伸长向前推动长齿条,使得驱动齿轮和活动柱均发生转动,即可使得放置框架在下拼接框体内部翻转;
s4:清洗:待单板在下拼接框体内部一段时间后,将单板取出,依次放置于下驱动辊和上驱动辊的间隙中,下驱动辊和上驱动辊将单板向前输送,清理用的水顺着渗水孔喷淋在单板的表面进行清洗;
s5:冲洗:清洗用的水顺着输送管道流向中空连杆内部,使得中空连杆顺着倾斜导向板斜向滑动,至中空连杆位于下拼接框体的顶部,清洗喷头将水喷洒至下拼接框体和上拼接框体的内部进行冲洗;
s6:整平:清洗结束后的单板顺着接料斜板滑向输送带上,输送带带动单板向前行进,阻隔板使得单板保持平齐停留在输送带顶部,挤压凸轮转动时向上推动弧形挤压块和阻隔板,使得单板穿过阻隔板的底部。
与现有技术相比,本发明的有益效果:本发明结构科学合理,使用安全方便:
1.设置有单板预处理机构,利用驱动电机带动螺杆转动,使得活动架和上拼接框体可以进行升降,上拼接框体和下拼接框体相互拼接形成一个密封框,起到了一个密封罐的作用,且拆卸组合方便,使得放置框架内部被复合剂浸泡过后的单板处于密封环境下,并利用加热板对密封框内部进行加热,同时利用调压阀和连接气道将密封框内部的空气抽入气压罐内部,进而提高密封框内部的压强,使得单板在密封框内部位于高温高压的环境下,可以促进浸泡的复合剂分子向单板的内部扩散,提高单板表面纤维的韧性,有效增强单板抗断裂能力,在将单板胶合拼接前对单板进行处理,提高了胶合板的品质和使用寿命。
2.加热板从下方对下拼接框体和上拼接框体拼接成的密封框进行加热,使得密封框上下温度不一致,导致单板的顶部和底部受热不均匀,锌棒在密封框内被加热,由于热胀冷缩原理,使得锌棒发生形变向前延伸,且锌的热胀系数高,对温差表现的更加精确,而位于活动柱上方和下方的两个锌棒距离加热板的距离不同,即受到的加热程度不同,使得锌棒的延伸距离不同,待密封框内部上下温差达到一定程度后,位于下方的锌棒延伸并与启动开关相接触,启动电动电动伸缩杆,利用长齿条和驱动齿轮相互啮合,使得驱动齿轮和活动柱转动,进而驱动放置框架和单板在密封框内部转动,可以及时根据密封框内部实际的温差来使得放置框架旋转,无须机械性频繁的驱动放置框架转动,使得单板可以在密封框内部得到充分的加热,避免单板旋转次数过多受热效果降低。
3.设置有单板清洗机构,将高温高压处理后单板放置于下驱动辊和上驱动辊的间隙处,利用下驱动辊和上驱动辊转动即可将单板向前输送,下驱动辊和上驱动辊前部分会将单板表面残留的复合剂进行擦拭,待单板行进至防水罩下方,分流箱体和渗水孔将水喷淋至单板的表面,对单板进行清洗,且下驱动辊和上驱动辊的后部分会将清洗后的单板表面水分除去,保证清洗后的单板保持干燥,便于后续的加工,且使得水不会四处滴落导致工作环境脏乱。
4.单板清洗用的水会滴落至集水槽内部,并通过输送管道流向中空连杆内部,水在中空连杆内部积聚,水自身的重力会将中空连杆向下压,滑块和中空连杆会顺着倾斜导向板向下滑动,使得中空连杆和清洗喷头移动至下拼接框体上方,利用单板清洗后用的水可以对下拼接框体和上拼接框体内部进行清洗,去除受热时单板表面的复合剂滴落在下拼接框体或者被蒸发粘附在上拼接框体内壁形成的痕迹,使得下拼接框体和上拼接框体保持洁净,提高了对资源的利用率,使得整体加工过程更加体现出节能环保理念。
5.设置有单板收集整理机构,清理结束后的单板落在接料斜板上,缓冲块和缓冲弹簧起到了缓冲的作用,且接料斜板表面包裹有橡胶垫,有效的避免了单板落下时边角损坏,单板落在输送带上,阻隔板对单板进行阻隔,且输送带持续向前行进,单板同时受到阻力和向前的推动力,即可使得单板的边部完全与阻隔板贴合,保证单板保持平齐,输送轴持续转动时会带动主动齿轮转动,进而使得从动齿轮和挤压凸轮转动,挤压凸轮转动至上方时会挤压弧形挤压块,且弧形挤压块的底端呈平面状态,挤压凸轮与弧形挤压块底端接触,将弧形挤压块向上推动,使得阻隔板不再阻挡单板,单板可以顺着输送带平整的被输送至预定位置处。
综上所述,通过单板预处理机构和单板清洗机构相互配合,下拼接框体和上拼接框体拼接而成的密封框体内部的空气被抽入气压罐内部压缩储存,在对单板进行清洗时,电磁阀启动,将气压罐内部的空气通过输气管输送至上布气箱内部,压缩的空气会通过通管流向侧边布气箱,通过布气孔和排气孔同时向外排出并吹向单板,吹至未清洗的单板表面会去除其表面的杂质和灰尘,提高了清理效率,同时对下驱动辊和上驱动辊也起到了一定的清理作用,且气压罐内部压缩的空气由密封框体内部抽出,带有一定的温度,吹向单板时会对促进其表面残留的复合剂再次吸收,起到了二次处理的作用,而压缩空气吹向清洗后的单板表面时,对单板起到了烘干的作用,使得其表面保持干燥。
附图说明
附图用来提供对本发明的进一步理解,并且构成说明书的一部分,与本发明的实施例一起用于解释本发明,并不构成对本发明的限制。
在附图中:
图1是本发明的步骤流程图;
图2是本发明装置的结构示意图;
图3是本发明支撑架的安装结构示意图;
图4是本发明气压罐的安装结构示意图;
图5是本发明中空连杆的安装结构示意图;
图6是本发明调压阀的安装结构示意图;
图7是本发明单板预处理机构的结构示意图;
图8是本发明单板清洗机构的结构示意图;
图9是本发明防水罩的安装结构示意图;
图10是本发明单板收集整理机构的结构示意图;
图11是本发明缓冲块的安装结构示意图;
图中标号:1、底板;2、固定支架;
3、单板预处理机构;301、下拼接框体;302、加热板;303、螺杆;304、驱动电机;305、定位杆;306、活动架;307、上拼接框体;308、活动柱;309、卡槽;310、固定架;311、锌棒;312、活动板;313、挤压弹簧;314、下挤压柱;315、启动开关;316、上挤压柱;317、弧形槽;318、驱动齿轮;319、长齿条;320、电动伸缩杆;321、放置框架;322、顶盖;323、侧板;324、卡块;
4、安装架;
5、单板清洗机构;501、安装横板;502、下驱动辊;503、上驱动辊;504、限位板;505、防水罩;506、分流箱体;507、渗水孔;508、储水箱体;509、进水管;510、集水槽;511、倾斜导向板;512、滑块;513、中空连杆;514、复位弹簧;515、清洗喷头;516、输送管道;517、调压阀;518、连接气道;519、气压罐;520、电磁阀;521、输气管;522、上布气箱;523、布气孔;524、通管;525、侧边布气箱;526、排气孔;527、排水管;
6、单板收集整理机构;601、固定座;602、缓冲弹簧;603、缓冲块;604、接料斜板;605、支撑架;606、输送轴;607、输送带;608、输送电机;609、主动齿轮;610、从动齿轮;611、挤压凸轮;612、竖直导向板;613、升降块;614、弧形挤压块;615、横杆;616、阻隔板。
具体实施方式
以下结合附图对本发明的优选实施例进行说明,应当理解,此处所描述的优选实施例仅用于说明和解释本发明,并不用于限定本发明。
实施例:如图1-11所示,本发明提供一种技术方案,一种胶合板的制备方法,包括如下步骤:
s1:放置:将浸泡复合剂后的单板固定于放置框架321内部,并将装有单板的放置框架321放置于位于底板1顶部的下拼接框体301中部,螺杆303转动使得上拼接框体307向下行进并覆盖于下拼接框体301顶部;
s2:处理:加热板302对下拼接框体301和上拼接框体307内部加热,电磁阀520将下拼接框体301和上拼接框体307内部的空气抽出,使得放置框架321内部的单板得到保温保压处理;
s3:翻转:下拼接框体301内部出现温差,锌棒311被加热后发生形变,与启动开关315接触,电动伸缩杆320伸长向前推动长齿条319,使得驱动齿轮318和活动柱308均发生转动,即可使得放置框架321在下拼接框体301内部翻转;
s4:清洗:待单板在下拼接框体301内部一段时间后,将单板取出,依次放置于下驱动辊502和上驱动辊503的间隙中,下驱动辊502和上驱动辊503将单板向前输送,清理用的水顺着渗水孔507喷淋在单板的表面进行清洗;
s5:冲洗:清洗用的水顺着输送管道516流向中空连杆513内部,使得中空连杆513顺着倾斜导向板511斜向滑动,至中空连杆513位于下拼接框体301的顶部,清洗喷头515将水喷洒至下拼接框体301和上拼接框体307的内部进行冲洗;
s6:整平:清洗结束后的单板顺着接料斜板604滑向输送带607上,输送带607带动单板向前行进,阻隔板616使得单板保持平齐停留在输送带607顶部,挤压凸轮611转动时向上推动弧形挤压块614和阻隔板616,使得单板穿过阻隔板616的底部;
底板1顶部的两端对称固定安装有固定支架2,底板1的顶端中部安装有单板预处理机构3,下拼接框体301和上拼接框体307拼接成一个密封框体,对浸泡过复合剂的单板进行保温保压处理,促进复合剂向单板内部扩散,且根据温差造成的锌棒311形变来间接控制放置框架321,保证单板受热更加均匀;
单板预处理机构3包括下拼接框体301、加热板302、螺杆303、驱动电机304、定位杆305、活动架306、上拼接框体307、活动柱308、卡槽309、固定架310、锌棒311、活动板312、挤压弹簧313、下挤压柱314、启动开关315、上挤压柱316、弧形槽317、驱动齿轮318、长齿条319、电动伸缩杆320、放置框架321、顶盖322、侧板323和卡块324;
底板1的顶端中部固定安装有下拼接框体301,下拼接框体301的底端内部嵌入安装有加热板302,两个固定支架2的顶端均固定安装有驱动电机304,两个驱动电机304的输出轴均固定安装有螺杆303,底板1顶部的两端位于两个螺杆303的一侧分别固定安装有定位杆305,螺杆303和定位杆305的中部均活动安装有活动架306,四个活动架306的底端之间固定安装有上拼接框体307,下拼接框体301的顶部的两端对称转动安装有活动柱308,活动柱308的顶部对称开设有卡槽309,活动柱308一端的顶部和底部对称固定安装有固定架310,固定架310的中部固定安装有锌棒311,活动架306和螺杆303之间通过螺纹连接,上拼接框体307的底部开设有半圆形槽,半圆形槽直径与活动柱308的直径相同,驱动齿轮318底部的啮齿与长齿条319相啮合,放置框架321的边部与下拼接框体301的内壁之间留有空隙,利用驱动电机304带动螺杆303转动,使得活动架306和上拼接框体307可以进行升降,上拼接框体307和下拼接框体301相互拼接形成一个密封框,起到了一个密封罐的作用,使得放置框架321内部被复合剂浸泡过后的单板处于密封环境下,并利用加热板302对密封框内部进行加热,同时利用调压阀517和连接气道518将密封框内部的空气抽入气压罐519内部,进而提高密封框内部的压强,使得单板在密封框内部位于高温高压的环境下,可以促进浸泡的复合剂分子向单板的内部扩散,提高单板表面纤维的韧性,有效增强单板抗断裂能力,在将单板胶合拼接前对单板进行处理,提高了胶合板的品质和使用寿命;
活动柱308的一端活动套接有活动板312,活动板312的一端固定连接有挤压弹簧313,活动板312的底部固定安装有下挤压柱314,下挤压柱314的一端固定安装有启动开关315,上拼接框体307底部的两端对称活动安装有上挤压柱316,下拼接框体301和上拼接框体307两端的内壁位于下挤压柱314和上挤压柱316一侧位置处均开设有弧形槽317,启动开关315的端部与弧形槽317的侧边相平齐,上挤压柱316的端部延伸出弧形槽317的侧边,上挤压柱316一端的两侧设置有倾斜角,上挤压柱316另一端的端面与活动板312的侧面位于同一水平面,启动开关315的信号输出端与电动伸缩杆320的信号输入端相连接,活动柱308的一端固定连接有驱动齿轮318,下拼接框体301底部的一端位于驱动齿轮318下方位置处活动安装有长齿条319,长齿条319的底端固定连接有电动伸缩杆320,下拼接框体301的中部放置有放置框架321,放置框架321的顶部通过螺栓固定安装有顶盖322,放置框架321的两边部对称固定安装有侧板323,侧板323的一端与卡槽309对应位置处对称固定连接有卡块324,卡块324嵌入卡槽309的内部,卡块324的高度小于卡槽309的深度,使的卡块324不会阻隔活动柱308转动,加热板302从下方对下拼接框体301和上拼接框体307拼接成的密封框进行加热,使得密封框上下温度不一致,导致单板的顶部和底部受热不均匀,锌棒311在密封框内被加热,由于热胀冷缩原理,使得锌棒311发生形变向前延伸,而位于活动柱308上方和下方的两个锌棒311距离加热板302的距离不同,即受到的加热程度不同,使得锌棒311的延伸距离不同,待密封框内部上下温差达到一定程度后,位于下方的锌棒311延伸并与启动开关315相接触,启动电动电动伸缩杆320,利用长齿条319和驱动齿轮318相互啮合,使得驱动齿轮318和活动柱308转动,进而驱动放置框架321和单板在密封框内部转动,可以及时根据密封框内部实际的温差来使得放置框架321旋转,无须机械性频繁的驱动放置框架321转动,使得单板可以在密封框内部得到充分的加热,避免单板旋转次数过多受热效果降低;
底板1的一侧固定安装有安装架4,安装架4的顶部固定安装有单板清洗机构5,下驱动辊502和上驱动辊503在喷淋清洗单板的过程中将其向前输送,且起到了擦拭清理的作用,清洗用的水流至中空连杆513内部可以对下拼接框体301和上拼接框体307进行清洗;
单板清洗机构5包括安装横板501、下驱动辊502、上驱动辊503、限位板504、防水罩505、分流箱体506、渗水孔507、储水箱体508、进水管509、集水槽510、倾斜导向板511、滑块512、中空连杆513、复位弹簧514、清洗喷头515、输送管道516、调压阀517、连接气道518、气压罐519、电磁阀520、输气管521、上布气箱522、布气孔523、通管524、侧边布气箱525、排气孔526和排水管527;
安装架4顶部的两端均对称固定安装有安装横板501,两个安装横板501之间等距转动安装有下驱动辊502,另两个安装横板501之间等距转动安装有上驱动辊503,下驱动辊502和上驱动辊503之间的边部固定安装有限位板504,位于上驱动辊503上方位置处的安装横板501顶端的中部固定安装有防水罩505,防水罩505内部的顶端等距固定安装有分流箱体506,分流箱体506的底部开设有渗水孔507,防水罩505的顶部固定安装有储水箱体508,储水箱体508的顶部固定连接有进水管509,位于下驱动辊502下方位置处的安装横板501的底端固定安装有集水槽510,安装架4的中部靠近底板1的一端对称固定安装有倾斜导向板511,倾斜导向板511的内部嵌入滑动安装有滑块512,两个滑块512之间固定连接有中空连杆513,滑块512的一端高度连接有复位弹簧514,中空连杆513的顶部和底部均等距固定安装有清洗喷头515,中空连杆513的一端等距固定连接有输送管道516,输送管道516的一端延伸至集水槽510的内部,下驱动辊502位于上驱动辊503的正下方,下驱动辊502和上驱动辊503之间留有间隙,下驱动辊502和上驱动辊503的表面均粘结有清理毛垫,储水箱体508的底端与分流箱体506相连接,中空连杆513内部的顶端固定安装有液位传感器,清洗喷头515和液位传感器均与外界控制阀相连接,将高温高压处理后单板放置于下驱动辊502和上驱动辊503的间隙处,利用下驱动辊502和上驱动辊503转动即可将单板向前输送,下驱动辊502和上驱动辊503前部分会将单板表面残留的复合剂进行擦拭,待单板行进至防水罩505下方,分流箱体506和渗水孔507将水喷淋至单板的表面,对单板进行清洗,且下驱动辊502和上驱动辊503的后部分会将清洗后的单板表面水分除去,保证清洗后的单板保持干燥,便于后续的加工,且使得水不会四处滴落导致工作环境脏乱,单板清洗用的水会滴落至集水槽510内部,并通过输送管道516流向中空连杆513内部,水在中空连杆513内部积聚,水自身的重力会将中空连杆513向下压,滑块512和中空连杆513会顺着倾斜导向板511向下滑动,使得中空连杆513和清洗喷头515移动至下拼接框体301上方,利用单板清洗后用的水可以对下拼接框体301和上拼接框体307内部进行清洗,去除受热时单板表面的复合剂滴落在下拼接框体301或者被蒸发粘附在上拼接框体307内壁形成的痕迹,使得下拼接框体301和上拼接框体307保持洁净,提高了对资源的利用率,使得整体加工过程更加体现出节能环保理念;
下拼接框体301底部的一端固定安装有调压阀517,调压阀517的一端固定连接有连接气道518,连接气道518的一端固定安装有气压罐519,气压罐519中部的一端固定安装有电磁阀520,电磁阀520的一端固定连接有输气管521,安装架4的顶部固定安装有上布气箱522,上布气箱522底部的两端对称开设有布气孔523,上布气箱522的底端对称固定连接有通管524,通管524的底端固定连接有侧边布气箱525,侧边布气箱525中部的两端对称开设有排气孔526,下拼接框体301底部的一端固定连接有排水管527,输气管521的一端与上布气箱522相连接,布气孔523和排气孔526均对称分布于防水罩505的两侧,布气孔523位于上驱动辊503的正上方,排气孔526与下驱动辊502和上驱动辊503之间间隙位于同一水平面,在对单板进行清洗时,电磁阀520启动,将气压罐519内部的空气通过输气管521输送至上布气箱522内部,压缩的空气会通过通管524流向侧边布气箱525,通过布气孔523和排气孔526同时向外排出并吹向单板,吹至未清洗的单板表面会去除其表面的杂质和灰尘,提高了清理效率,同时对下驱动辊502和上驱动辊503也起到了一定的清理作用,且气压罐519内部压缩的空气由密封框体内部抽出,带有一定的温度,吹向单板时会对促进其表面残留的复合剂再次吸收,起到了二次处理的作用,而压缩空气吹向清洗后的单板表面时,对单板起到了烘干的作用,使得其表面保持干燥;
安装架4的底部固定安装有单板收集整理机构6,利用输送带607向前的推动力和阻隔板616的阻隔,使得单板保持平齐,挤压凸轮611间歇的向上推动阻隔板616,即可使得平齐的单板正常向前行进;
单板收集整理机构6包括固定座601、缓冲弹簧602、缓冲块603、接料斜板604、支撑架605、输送轴606、输送带607、输送电机608、主动齿轮609、从动齿轮610、挤压凸轮611、竖直导向板612、升降块613、弧形挤压块614、横杆615和阻隔板616;
安装架4中部的一端内侧对称固定安装有固定座601,固定座601的内部固定安装有缓冲弹簧602,缓冲弹簧602的顶部固定连接有缓冲块603,缓冲块603的顶端固定安装有接料斜板604,安装架4底部的一端固定安装有支撑架605,支撑架605的顶部对称固定安装有输送轴606,输送轴606的表面套接有输送带607,缓冲块603的底部嵌入滑动安装于固定座601的内部,接料斜板604的表面包裹粘结有橡胶垫,接料斜板604与水平面之间的夹角为45度,接料斜板604的底部延伸至输送带607一端的上方位置处,一个输送轴606的一端固定安装有输送电机608,另一个输送轴606的两端均固定连接有主动齿轮609,支撑架605的两边部位于主动齿轮609一侧位置处均转动安装有从动齿轮610,从动齿轮610中部的一端固定连接有挤压凸轮611,支撑架605的顶部与从动齿轮610对应位置处固定安装有竖直导向板612,竖直导向板612的中部嵌入滑动安装有升降块613,升降块613的一端固定连接有弧形挤压块614,两个升降块613之间固定连接有横杆615,横杆615的底端固定安装有阻隔板616,主动齿轮609和从动齿轮610之间相互啮合,主动齿轮609和从动齿轮610之间的齿数比为1比2,使得从动齿轮610和挤压凸轮611转动一圈所需要的时间为主动齿轮609的两倍,确保对单板的阻隔时间足够长,避免单板还未平齐即向前行进,挤压凸轮611和弧形挤压块614之间位于同一竖直平面上,竖直导向板612的底端设置有放置块,升降块613的底端与竖直导向板612的顶端相贴合,阻隔板616的两侧面均固定粘结有防护垫,阻隔板616的底端与输送带607的表面之间留有间隙,清理结束后的单板落在接料斜板604上,缓冲块603和缓冲弹簧602起到了缓冲的作用,且接料斜板604表面包裹有橡胶垫,有效的避免了单板落下时边角损坏,单板落在输送带607上,阻隔板616对单板进行阻隔,且输送带607持续向前行进,单板同时受到阻力和向前的推动力,即可使得单板的边部完全与阻隔板616贴合,保证单板保持平齐,输送轴606持续转动时会带动主动齿轮609转动,进而使得从动齿轮610和挤压凸轮611转动,挤压凸轮611转动至上方时会挤压弧形挤压块614,且弧形挤压块614的底端呈平面状态,挤压凸轮611与弧形挤压块614底端接触,将弧形挤压块614向上推动,使得阻隔板616不再阻挡单板,单板可以顺着输送带607平整的被输送至预定位置处。
本发明的工作原理及使用流程:在使用一种胶合板的制备方法过程中,首先,将浸泡过复合剂的单板放置于放置框架321的内部,利用螺栓将顶盖322固定于放置框架321的顶部,接着将放置框架321放置于下拼接框体301的顶部,且卡块324嵌入卡槽309的内部,驱动电机304启动,带动螺杆303转动,使得活动架306和上拼接框体307顺着螺杆303和定位杆305向下移动,至上拼接框体307覆盖于下拼接框体301的顶部,上拼接框体307和下拼接框体301之间形成一个密封框体,放置框架321和单板被包裹于密封框体内部,加热板302从下方对密封框体进行加热,使得密封框体内部温度上升到一定程度,同时调压阀517启动,将密封框体内部的空气抽向气压罐519的内部压缩储存,提高密封框体内部的压强;
单板在密封框体内部受到保温保压处理,可以促进浸泡的复合剂向单板内部扩散,而密封框体内部受热不均匀,位于活动柱308上方和下方的两个锌棒311均受到不同程度的加热,两个锌棒311会发生不同程度的形变,位于活动柱308下方的锌棒311形变长度更长,会与启动开关315接触,启动开关315启动电动伸缩杆320,电动伸缩杆320向前推动长齿条319,使得驱动齿轮318和活动柱308转动,而卡块324卡接于卡槽309内部,即放置框架321会随着活动柱308一起转动,使得放置框架321在密封框体内部翻转,顶盖322朝向下方,且锌棒311会随着活动柱308一起转动,形变更长的锌棒311转动时会挤压上挤压柱316,上挤压柱316向外挤压活动板312,挤压弹簧313被压缩,启动开关315随着活动板312向一侧移动,两个锌棒311位置交换后,所处环境的温度不同,调转至上方的锌棒311向内收缩,上挤压柱316不再挤压活动板312,挤压弹簧313伸长,使得启动开关315恢复原位,位于下方的锌棒311伸长,一段时间后,锌棒311与启动开关315接触,使得放置框架321再次转动,保证单板在密封框体内部可以根据所受加热情况来翻转,确保单板受热均匀;
待单板在密封框体内部处理完成后,驱动电机304带动螺杆303转动,使得上拼接框体307上升,将放置框架321取出,拆卸顶盖322,将单板取出,把单板依次放置于下驱动辊502和上驱动辊503之间的间隙处,下驱动辊502和上驱动辊503同时转动,使得单板被向前输送,下驱动辊502和上驱动辊503输送单板时会对其表面进行预清理,擦拭单板的表面,待单板行进至防水罩505的下方,储水箱体508内部的水由分流箱体506和渗水孔507喷淋至单板的表面,对单板进行清洗,清洗用的水落在集水槽510内部,而单板继续向前行进,位于后半部分的下驱动辊502和上驱动辊503会去除单板表面残留的水分,单板随着下驱动辊502和上驱动辊503行进的同时,电磁阀520启动,将气压罐519内部的压缩空气输送至上布气箱522内部,并经过通管524流向侧边布气箱525,通过布气孔523和排气孔526同时吹向下驱动辊502和上驱动辊503中部的单板,在单板未被水清洗之前再次促进复合剂的吸收,且可以吹走其表面残留的杂质和灰尘,对下驱动辊502和上驱动辊503也起到了清理的作用,且一部分空气吹向清洗结束后的单板表面,对单板进行烘干,便于后续的加工;
集水槽510内部单板清理用的水会通过输送管道516被输送至中空连杆513的内部,中空连杆513内部的水持续增多,水自身的重力将中空连杆513向下压,滑块512在倾斜导向板511内部斜向下滑动,复位弹簧514被拉长,中空连杆513和清洗喷头515随着滑块512移动至中空连杆513位于下拼接框体301的顶部,位于中空连杆513顶部和底部的清洗喷头515分别对准下拼接框体301和上拼接框体307的内部,待水集聚到一定程度后,中空连杆513内部的液位传感器将信号传输至外界控制器,进而启动清洗喷头515,将中空连杆513内部的水喷洒向下拼接框体301和上拼接框体307的内部,单板表面浸泡的复合剂会滴落在下拼接框体301的底部,且加热后复合剂蒸发会粘附在上拼接框体307的内壁,利用单板清洗用的水对下拼接框体301和上拼接框体307的内部进行冲洗,提高了资源的利用率;
清洗结束后的单板会移动至下驱动辊502和上驱动辊503的端部,并向下掉落至接料斜板604的斜面上,单板落在接料斜板604上会向下挤压接料斜板604,缓冲弹簧602和缓冲块603起到了缓冲作用,且接料斜板604的表面包裹有橡胶垫,保证单板掉落时其边角不会损坏,单板顺着接料斜板604的斜面滑向输送带607的表面,输送电机608带动输送轴606和输送带607转动,输送带607带着单板向前行进,阻隔板616对单板起到了阻隔作用,使得单板不再行进,而输送带607持续给单板向前的推力,单板位置发生了偏移,保证单板的边部完全贴合阻隔板616,使得单板保持平齐,而主动齿轮609会随着输送轴606转动,主动齿轮609和从动齿轮610相互啮合,从动齿轮610和挤压凸轮611即会随着主动齿轮609转动,待挤压凸轮611转动至上方时,与弧形挤压块614的侧边的弧面相接触,将弧形挤压块614向上推动,横杆615和阻隔板616均向上行进,挤压凸轮611的顶端与弧形挤压块614底端的平面相接触,阻隔板616不再与单板接触,使得单板可以保持平齐状态向前移动,待单板穿过阻隔板616的底部,挤压凸轮611继续转动不再与弧形挤压块614接触,横杆615和阻隔板616受到重力影响,自动下落,升降块613始终在竖直导向板612内部竖直上下行进,保证阻隔板616的位置不会发生偏移。
最后应说明的是:以上所述仅为本发明的优选实例而已,并不用于限制本发明,尽管参照前述实施例对本发明进行了详细的说明,对于本领域的技术人员来说,其依然可以对前述各实施例所记载的技术方案进行修改,或者对其中部分技术特征进行等同替换。凡在本发明的精神和原则之内,所作的任何修改、等同替换、改进等,均应包含在本发明的保护范围之内。
本文用于企业家、创业者技术爱好者查询,结果仅供参考。