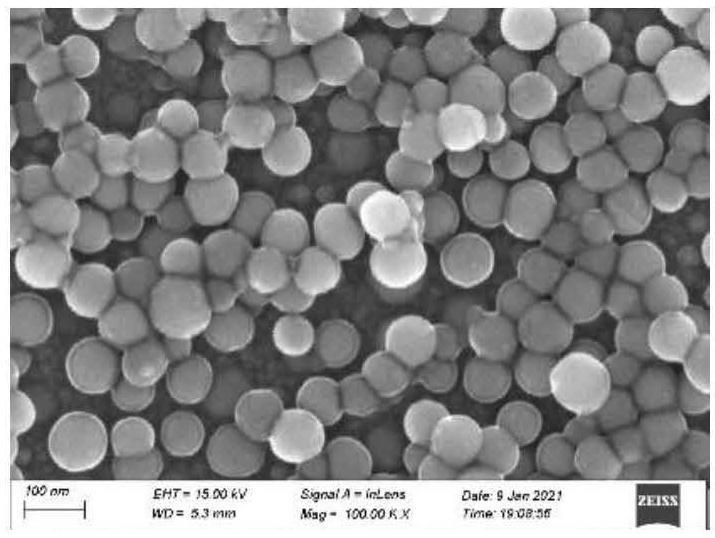
一种gh4738镍基高温合金的热加工工艺
技术领域
1.本发明涉及镍基合金热加工技术领域。具体地说是一种gh4738镍基高温合金的热加工工艺。
背景技术:
2.涡轮盘是燃气轮机和航空发动机上重要部件,其性能的好坏直接影响着燃气轮机和航空发动机的产品质量。在之前,涡轮盘的材料从研发到投产一直为gh4169,但发现该合金在高温服役时变形导致不能正常使用,经反复研究思考发现,亚稳态γ
′
相的溶解温度较低,使得该合金不能在超过650℃正常服役。在这样的形势下,研究者对gh4864、gh4738等合金进行了研究。早在1952年special metal公司采用真空冶炼法成功研制出以γ
′
相沉淀硬化为硬化手段的高温合金,并在20世纪60年代制成800℃以下的涡轮盘将其用在波音727等发动机上,而我国在1973年开始研发并少量生产。但gh4738镍基高温合金由于其合金含量高、塑性差、可变形温度区间较小,变形组织中容易出现混晶和粗晶现象、变形过程中试件开裂等问题。由于gh4738镍基高温合金在变形过程中易于出现混晶的现象,导致性能下降。为了保证组织的均匀性,工厂在出货前通常会将锻件表层切削掉,造成材料浪费的同时提高了生产成本。企业生产时为了保证组织均一性能稳定,常会将材料晶粒粗大的表层(通常为5~10mm)车掉,造成了材料的浪费。同时高温合金材料的组织和性能的不稳定性会导致涡轮盘的蠕变松弛、腐蚀磨损和高温疲劳,这影响了涡轮盘的使用寿命。因此,寻求合适的热处理工艺以及确定合理的热处理工艺参数来改善gh4738组织不均匀,同时减少切削量对企业的生产有很大的意义。
技术实现要素:
3.为此,本发明所要解决的技术问题在于提供一种gh4738镍基高温合金的热加工工艺,以解决当前gh4738镍基高温合金的变形组织中容易出现混晶和粗晶等现象以及变形过程中试件开裂等问题;以使gh4738镍基高温合金具有腐蚀磨损速率低、硬度高的特点,提高最终合金盘锻件整体硬度和高温冲蚀性能,同时也提高锻件的成材率,以满足涡轮盘使用寿命要求的。
4.为解决上述技术问题,本发明提供如下技术方案:
5.一种gh4738镍基高温合金的热加工工艺,包括如下步骤:
6.步骤a:以gh4738镍基高温合金为原料,对其依次采用真空感应熔炼vim和真空自耗重熔var工艺进行冶炼,得到真空自耗锭;步骤b:将所述真空自耗锭进行均匀化处理及开坯锻造处理,得到gh4738合金棒材坯料;步骤c:将所述gh4738合金棒材坯料放入燃气炉内随炉升温,保温后利用锻锤进行平砧镦粗,得到gh4738合金盘锻件;步骤d:将所述gh4738合金盘锻件依次进行固溶处理、稳定化处理和二次时效处理,即得到得到晶粒尺寸均匀,高温冲蚀性能优异的gh4738镍基高温合金。
7.本发明的技术方案取得了如下有益的技术效果:
8.(1)本发明的热加工工艺可以避免gh4738镍基高温合金变形组织中现混晶和粗晶等现象,并避免变形过程中出现试件开裂等问题。采用本发明的热加工工艺可以使制备得到的gh4738镍基高温合金组织均匀,具有硬度高、高温冲蚀性能好的优点,可满足涡轮盘使用寿命的要求,其中gh4738镍基高温合金的硬度可达44hrc,在冲蚀时磨料温度750℃、靶材温度750℃、磨料总量2kg、冲蚀速度88m/s、冲蚀角度90
°
以及冲蚀时间为20s的条件下,gh4738镍基高温合金的冲蚀速率为0.053
‑
0.058cm3/kg。本发明的热处理加工工艺还可以避免因gh4738镍基高温合金在变形过程中出现混晶现象而在出货前需要切削锻件表层而造成的材料浪费,有效降低了生产成本,提高了锻件的成材率。
9.(2)本发明的热加工工艺可使gh4738镍基高温合金的锻前晶粒尺寸控制在较小范围内,且在镦粗后的锻件中晶粒分布较均匀,从而使其具有较高的晶界面积,为合金变形过程中的元素扩散提供高速通道;通过控制变形温度可以使棒坯中的碳化物更好地发挥钉扎作用,从而阻止晶粒的长大;通过控制锻前升温速率、变形量等工艺参数,使锻件的晶粒尺寸较小,同时具有较高的硬度;另外,本发明通过选择特定的固溶处理、稳定性处理和二次时效处理的温度、时间及冷却方式,使gh4738镍基高温合金在经热处理后,第二相γ'的含量增多,并控制其晶粒尺寸不再长大或者控制其尺寸长大幅度在可接受范围内,同时使合金组织中的γ'相分布更均匀;另外,本发明的固溶处理温度有利于晶内粒状m
23
c6碳化物的形核,而稳定化处理温度则更有利于片状碳化物在粒状碳化物的基础上进一步形核并长大,并最终使得m
23
c6碳化物完全析出,从而达到强化合金组织的晶界和基体的作用。
附图说明
10.图1a本发明gh4738合金棒坯的微观组织om图;
11.图1b本发明gh4738合金棒坯的微观组织sem图;
12.图2本发明中所用高温冲蚀设备示意图;
13.图3a本发明gh4738合金较低变形温度锻件的显微组织om图(1120℃);
14.图3b本发明gh4738合金较低变形温度锻件的显微组织om图(1140℃);
15.图3c本发明gh4738合金较低变形温度锻件的显微组织sem图(1120℃);
16.图3d本发明gh4738合金较低变形温度锻件的显微组织sem图(1140℃);
17.图3e本发明gh4738合金较低变形温度锻件的γ'相粒径分布图(1120℃);
18.图3f本发明gh4738合金较低变形温度锻件的γ'相粒径分布图(1140℃);
19.图4a本发明gh4738合金较高变形温度锻件的显微组织om图(1160℃);
20.图4b本发明gh4738合金较高变形温度锻件的显微组织om图(1180℃);
21.图4c本发明gh4738合金较高变形温度锻件的显微组织sem图(1160℃);
22.图4d本发明gh4738合金较高变形温度锻件的显微组织sem图(1180℃);
23.图4e本发明gh4738合金较高变形温度锻件的γ'相粒径分布图(1160℃);
24.图4f本发明gh4738合金较高变形温度锻件的γ'相粒径分布图(1180℃);
25.图5本发明中不同变形温度的平均晶粒尺寸和硬度的对比图(改良热处理前);
26.图6a本发明gh4738合金不同变形程度锻件的显微组织om图(58%);
27.图6b本发明gh4738合金不同变形程度锻件的显微组织om图(65%);
28.图6c本发明gh4738合金不同变形程度锻件的显微组织om图(70%);
29.图6d本发明gh4738合金不同变形程度锻件的显微组织sem图(58%);
30.图6e本发明gh4738合金不同变形程度锻件的显微组织sem图(65%);
31.图6f本发明gh4738合金不同变形程度锻件的显微组织sem图(70%);
32.图6g本发明gh4738合金不同变形程度锻件的γ'相粒径分布图(58%);
33.图6h本发明gh4738合金不同变形程度锻件的γ'相粒径分布图(65%);
34.图6i本发明gh4738合金不同变形程度锻件的γ'相粒径分布图(70%);
35.图7本发明中不同变形程度(变形量58%
‑
70%)的平均晶粒尺寸和硬度的对比图;
36.图8a本发明阶梯升温下gh4738合金不同变形量锻件的显微组织om图(62%);
37.图8b本发明阶梯升温下gh4738合金不同变形量锻件的显微组织om图(68%);
38.图8c本发明阶梯升温下gh4738合金不同变形量锻件的显微组织sem图(62%);
39.图8d本发明阶梯升温下gh4738合金不同变形量锻件的显微组织sem图(68%);
40.图8e本发明阶梯升温下gh4738合金不同变形量锻件的γ'相粒径分布图(62%);
41.图8f本发明阶梯升温下gh4738合金不同变形量锻件的γ'相粒径分布图(68%);
42.图9a本发明阶梯升温下gh4738合金不同变形量锻件的显微组织om图(72%);
43.图9b本发明阶梯升温下gh4738合金不同变形量锻件的显微组织om图(80%);
44.图9c本发明阶梯升温下gh4738合金不同变形量锻件的显微组织sem图(72%);
45.图9d本发明阶梯升温下gh4738合金不同变形量锻件的显微组织sem图(80%);
46.图9e本发明阶梯升温下gh4738合金不同变形量锻件的γ'相粒径分布图(72%);
47.图9f本发明阶梯升温下gh4738合金不同变形量锻件的γ'相粒径分布图(80%);
48.图10本发明不同变形程度(变形量62%
‑
80%)的平均晶粒尺寸和硬度的对比图;
49.图11a本发明不同变形温度gh4738合金锻件亚固溶热处理后金相图om图(1120℃);
50.图11b本发明不同变形温度gh4738合金锻件亚固溶热处理后金相图om图(1140℃);
51.图11c本发明不同变形温度gh4738合金锻件亚固溶热处理后金相图om图(1160℃);
52.图11d本发明不同变形温度gh4738合金锻件亚固溶热处理后金相图om图(1180℃);
53.图12a本发明不同变形量gh4738合金锻件亚固溶热处理后金相图om图(58%);
54.图12b本发明不同变形量gh4738合金锻件亚固溶热处理后金相图om图(65%);
55.图12c本发明不同变形量gh4738合金锻件亚固溶热处理后金相图om图(70%);
56.图13本发明gh4738合金锻件亚固溶热处理后sem图(变形量58%);
57.图14a本发明gh4738合金较低变形温度锻件热处理后的显微组织om图(1120℃);
58.图14b本发明gh4738合金较低变形温度锻件热处理后的显微组织om图(1140℃);
59.图14c本发明gh4738合金较低变形温度锻件热处理后的显微组织sem图(1120℃);
60.图14d本发明gh4738合金较低变形温度锻件热处理后的显微组织sem图(1140℃);
61.图14e本发明gh4738合金较低变形温度锻件热处理后的γ'相粒径分布图(1120℃);
62.图14f本发明gh4738合金较低变形温度锻件热处理后的γ'相粒径分布图(1140
℃);
63.图15a本发明gh4738合金较高变形温度锻件热处理后的显微组织om图(1160℃);
64.图15b本发明gh4738合金较高变形温度锻件热处理后的显微组织om图(1180℃);
65.图15c本发明gh4738合金较高变形温度锻件热处理后的显微组织sem图(1160℃);
66.图15d本发明gh4738合金较高变形温度锻件热处理后的显微组织sem图(1180℃);
67.图15e本发明gh4738合金较高变形温度锻件热处理后的γ'相粒径分布图(1160℃);
68.图15f本发明gh4738合金较高变形温度锻件热处理后的γ'相粒径分布图(1180℃);
69.图16本发明不同变形温度的锻件平均晶粒尺寸和硬度的对比图(改良热处理后);
70.图17a本发明gh4738合金不同变形程度锻件热处理后的显微组织om图(58%);
71.图17b本发明gh4738合金不同变形程度锻件热处理后的显微组织om图(65%);
72.图17c本发明gh4738合金不同变形程度锻件热处理后的显微组织om图(70%);
73.图17d本发明gh4738合金不同变形程度锻件热处理后的显微组织sem图(58%);
74.图17e本发明gh4738合金不同变形程度锻件热处理后的显微组织sem图(65%);
75.图17f本发明gh4738合金不同变形程度锻件热处理后的显微组织sem图(70%);
76.图17g本发明gh4738合金不同变形程度锻件热处理后的γ'相粒径分布图(58%);
77.图17h本发明gh4738合金不同变形程度锻件热处理后的γ'相粒径分布图(65%);
78.图17i本发明gh4738合金不同变形程度锻件热处理后的γ'相粒径分布图(70%);
79.图18本发明不同变形量锻件热处理后的平均晶粒尺寸和硬度的对比图;
80.图19a本发明阶梯升温gh4738合金不同变形量锻件热处理后的om图(62%);
81.图19b本发明阶梯升温gh4738合金不同变形量锻件热处理后的om图(68%);
82.图19c本发明阶梯升温gh4738合金不同变形量锻件热处理后的sem图(62%);
83.图19d本发明阶梯升温gh4738合金不同变形量锻件热处理后的sem图(68%);
84.图19e本发明阶梯升温gh4738合金不同变形量锻件热处理后γ'相粒径分布图(62%);
85.图19f本发明阶梯升温gh4738合金不同变形量锻件热处理后γ'相粒径分布图(68%);
86.图20a本发明阶梯升温gh4738合金不同变形量锻件热处理后的om图(72%);
87.图20b本发明阶梯升温gh4738合金不同变形量锻件热处理后的om图(80%);
88.图20c本发明阶梯升温gh4738合金不同变形量锻件热处理后的sem图(72%);
89.图20d本发明阶梯升温gh4738合金不同变形量锻件热处理后的sem图(80%);
90.图20e本发明阶梯升温gh4738合金不同变形量锻件热处理后γ'相粒径分布图(72%);
91.图20f本发明阶梯升温gh4738合金不同变形量锻件热处理后γ'相粒径分布图(80%);
92.图21本发明不同变形量(62%
‑
80%)锻件热处理后的平均晶粒尺寸和硬度的对比图;
93.图22a本发明阶梯升温下变形温度1140℃、变形量80%的gh4738合金锻件ebsd图;
94.图22b本发明阶梯升温下变形温度1140℃、变形量80%gh4738热处理件ebsd图;
95.图22c本发明gh4738合金不同状态下具有不同位向差晶界的分布规律;
96.图22d本发明gh4738合金不同状态下<2
°
和2
°
~5
°
不同位向差晶界的分布规律;
97.图23a本发明中沿图22a中直线段方向取向角度分布(a1);
98.图23b本发明中沿图22a中直线段方向取向角度分布(a2);
99.图23c本发明中沿图22a中直线段方向取向角度分布(b1);
100.图23d本发明中沿图22a中直线段方向取向角度分布(c1);
101.图24a本发明中沿图22b中直线段方向取向角度分布(a1);
102.图24b本发明中沿图22b中直线段方向取向角度分布(a2);
103.图24c本发明中沿图22b中直线段方向取向角度分布(b1);
104.图24d本发明中沿图22b中直线段方向取向角度分布(b2);
105.图25a本发明中沿图22b中直线段方向取向角度分布(c1);
106.图25b本发明中沿图22b中直线段方向取向角度分布(c2);
107.图25c本发明中沿图22b中直线段方向取向角度分布(c3);
108.图25d本发明中沿图22b中直线段方向取向角度分布(c4);
109.图26a本发明变形温度为1140℃、变形量为80%、阶梯升温下gh4738合金锻件的ebsd图(晶粒间的取向差角图,>15
°
,5
°
~15
°
以及2
°
~5
°
);其中,标记3为31.6
°
<110>结构的σ27a孪晶界和35.4
°
<210>结构的σ27b孪晶界;
110.图26b本发明变形温度为1140℃、变形量为80%、阶梯升温下gh4738合金锻件的ebsd图(σ3,σ9,σ27孪晶界);其中,标记1为60
°
<111>取向的初生σ3孪晶界,标记2为高阶次的28.9
°
<101>结构的σ9孪晶界;
111.图26c本发明变形温度为1140℃、变形量为80%、阶梯升温下gh4738合金锻件的ebsd图(晶粒间的位错密度图);
112.图26d本发明变形温度为1140℃、变形量为80%、阶梯升温下gh4738合金锻件的ebsd图(再结晶晶粒的分布);其中,标记1为60
°
<111>取向的初生σ3孪晶界,标记2为高阶次的28.9
°
<101>结构的σ9孪晶界;
113.图27a本发明变形温度为1140℃、变形量为80%、阶梯升温下gh4738合金锻件热处理后的ebsd图(晶粒间的取向差角图,>15
°
,5
°
~15
°
以及2
°
~5
°
);其中,标记3为31.6
°
<110>结构的σ27a孪晶界和35.4
°
<210>结构的σ27b孪晶界;
114.图27b本发明变形温度为1140℃、变形量为80%、阶梯升温下gh4738合金锻件热处理后的ebsd图(σ3,σ9,σ27孪晶界);其中,标记1为60
°
<111>取向的初生σ3孪晶界,标记2为高阶次的28.9
°
<101>结构的σ9孪晶界,标记3为31.6
°
<110>结构的σ27a孪晶界和35.4
°
<210>结构的σ27b孪晶界;
115.图27c本发明变形温度为1140℃、变形量为80%、阶梯升温下gh4738合金锻件热处理后的ebsd图(晶粒间的位错密度图);
116.图27d本发明变形温度为1140℃、变形量为80%、阶梯升温下gh4738合金锻件热处理后的ebsd图(再结晶晶粒的分布);其中,标记1为60
°
<111>取向的初生σ3孪晶界,标记2为高阶次的28.9
°
<101>结构的σ9孪晶界;
117.图28a本发明中位错与γ'相的弱耦合切割关系示意图;其中,标记4为未被切割过
的γ'相或第二条位错切割后再次恢复的γ'相,标记5为第一条位错切割过γ'相后产生的apb;
118.图28b本发明中位错与γ'相的强耦合切割关系示意图;其中,标记4为未被切割过的γ'相或第二条位错切割后再次恢复的γ'相,标记5为第一条位错切割过γ'相后产生的apb;
119.图29本发明中gh4738合金锻件的tem图;
120.图30a本发明中gh4738合金棒坯中的γ'相;
121.图30b本发明中gh4738合金锻件中的γ'相
122.图30c本发明中gh4738合金亚固溶热处理件中的γ'相
123.图30d本发明中gh4738合金“改良”热处理件中的γ'相
124.图31a本发明中gh4738合金亚固溶热处理件中的晶界碳化物;
125.图31b本发明中gh4738合金“改良”热处理件中的晶界碳化物;
126.图32本发明中gh4738合金热处理件的晶内碳化物tem照片;
127.图33a本发明gh4738合金热处理件中晶界碳化物的tem
‑
mapping图(tem
‑
haadf图);
128.图33b本发明gh4738合金热处理件中晶界碳化物的tem
‑
mapping图(ni元素);
129.图33c本发明gh4738合金热处理件中晶界碳化物的tem
‑
mapping图(cr元素);
130.图33d本发明gh4738合金热处理件中晶界碳化物的tem
‑
mapping图(ti元素);
131.图34a本发明gh4738热处理件的高温冲蚀形貌(阶梯升温下变形量62%);
132.图34b本发明gh4738热处理件的高温冲蚀形貌(阶梯升温下变形量68%);
133.图34c本发明gh4738热处理件的高温冲蚀形貌(阶梯升温下变形量72%);
134.图34d本发明gh4738热处理件的高温冲蚀形貌(阶梯升温下变形量80%);
135.图35本发明gh4738热处理件高温冲蚀速率和硬度的关系。
具体实施方式
136.1.一种gh4738镍基高温合金的热加工工艺
137.gh4738镍基高温合金的热加工工艺包括如下步骤:
138.步骤a:以gh4738镍基高温合金为原料,对其依次采用真空感应熔炼vim和真空自耗重熔var工艺进行冶炼,得到真空自耗锭。
139.步骤b:将所述真空自耗锭进行均匀化处理及开坯锻造处理,得到gh4738合金棒材坯料;均匀化处理温度为1180℃,均匀化处理时间为12小时;开坯锻造的始锻温度为1160℃。
140.步骤c:将所述gh4738合金棒材坯料放入燃气炉内随炉升温至1140℃,保温15min后利用锻锤进行平砧镦粗,得到gh4738合金盘锻件,gh4738合金盘锻件的变形量控制在80%;升温时,采用阶梯升温的方式进行升温;阶梯升温的方法如下:先将所述gh4738合金棒材坯料升温至800℃后保温30min,随后所述gh4738合金棒材坯料每升高50℃保温10min,直至升温至变形温度后再保温15min,整个阶梯升温过程中的升温速率均为30℃/min。
141.步骤d:将所述gh4738合金锻件依次进行固溶处理、稳定化处理和二次时效处理,即得到gh4738镍基高温合金。固溶处理的方法为:将所述gh4738合金盘锻件加热到960℃,
保温7min,然后采用水冷wc的方式将所述gh4738合金盘锻件冷却至20℃,水冷wc的冷却速率为750℃/min;稳定化处理方法为:将经固溶处理后的所述gh4738合金盘锻件加热到845℃,保温15min,然后采用空冷ac的方式将所述gh4738合金盘锻件冷却至20℃,空冷ac的冷却速率为15℃/min;二次时效处理方法为:将经二次时效处理后的所述gh4738合金盘锻件加热到760℃,保温30min,然后采用空冷ac的方式将所述gh4738合金盘锻件冷却至20℃,空冷ac的冷却速率为15℃/min。
142.在本实施例中,固溶处理时,冷却速度过快容易导致锻件内应力过大而出现开裂现象,因此要选择合适的冷却方式。由于不同的介质传热能力不同,空冷最慢(15℃/min)、盐水冷最快(2000℃/min),油冷(200℃/min)比水冷(750℃/min)慢。本实例选用水冷是因为冷却速度相对较快时,晶粒尺寸小、二次相来不及长大,有利于提高强度、硬度,对锻件的性能有利。同时本实施例通过控制锻件的变形量,及协同其它加工技术手段,使得在750℃/min的水冷下冷却至20℃时既不会导致锻件开裂,又具有较高的强度和硬度。
143.2.gh4738镍基高温合金材料制备及检测
144.2.1gh4738镍基高温合金材料的制备
145.本实施例中所使用的gh4738合金是高合金化程度的镍基变形高温合金,使用真空感应熔炼(vim)和真空自耗重熔(var)工艺制备而成,经过均匀化处理和开坯锻造制得得高合金含量的镍基变形高温合金棒材。图1a
‑
b为锻态gh4738合金的棒坯微观组织,由图1a可知,锻态合金的晶粒较为粗大且分布不均匀,其平均晶粒尺寸约为42μm。由图1b得知,锻造态合金主要由γ奥氏体基体和晶内弥散分布的γ'相构成。表2
‑
1为gh4738镍基高温合金的标称化学成分。
146.表2
‑
1 gh4738镍基高温合金的名义化学成分表(mass%)
[0147][0148]
2.2锻造工艺
[0149]
gh4738镍基高温合金在变形过程中易于出现混晶的现象,导致性能下降。为了保证组织的均匀性,工厂在出货前通常会将锻件表层切削掉,造成材料浪费的同时提高了生产成本。gh4738镍基高温合金的热加工工艺对该合金的锻件组织和性能有较大的影响。查阅相关资料,gh4738镍基高温合金的变形温度确定在1120℃
‑
1180℃之间;该合金的变形程度确定为50%
‑
80%。
[0150]
2.2.1变形温度工艺方案
[0151]
为了探究变形温度对gh4738镍基高温合金组织和性能的影响规律,选取了4组φ45
×
50mm的高温合金棒材坯料试样,热变形方案如表2
‑
2所示。试验时将棒坯放入燃气炉内,分别随炉升温至1120℃、1140℃、1160℃和1180℃并在炉内保温15min,分别取出进行镦粗试验,4组试样的变形量均为70%,最后从4组锻饼的同一位置上取10mm
×
10mm
×
10mm的正方体试样进行热处理试验,采用的热处理工艺为1020℃
×
4h/wc 845℃
×
4h/ac 760℃
×
16h/ac。观察、统计、分析gh4738镍基高温合金锻饼在变形前后以及锻饼在热处理前后的显微组织与材料性能在不同变形温度变化下的演变规律。
[0152]
表2
‑
2变形温度工艺方案
[0153][0154]
2.2.2变形程度工艺方案
[0155]
为了探究不同变形程度对gh4738镍基高温合金组织和性能的影响规律,由文献可知,高温合金变形程度范围在50%
‑
80%,因此设置了三种变形量,分别为58%、65%、70%,如表2
‑
3所示。将3组φ45
×
50mm的高温合金棒材坯料放置于燃气炉内随炉升温至变形温度1160℃,保温10min进行镦粗。在锻饼上取位置相同且尺寸均为10mm
×
10mm
×
10mm的3组试样进行热处理。热处理工艺为960℃
×
7min/oc 845℃
×
15min/ac 760℃
×
30min/ac。观察、统计、分析gh4738镍基高温合金锻饼在变形前后以及锻饼在热处理前后的显微组织与材料性能在不同变形程度变化下的演变规律,确定出最佳的变形程度。
[0156]
表2
‑
3变形程度工艺方案
[0157][0158]
2.3热处理工艺
[0159]
通常高温合金锻件热变形后的综合力学性能尚未达到最佳状态,将锻件进一步热处理后会提高锻件的性能。锻件的综合力学性能不仅与晶粒尺寸有关,而且与第二相的尺寸,形状,含量和分布有关。为了使锻件获得更加均匀的组织和更优异的力学性能,需对锻件进行适当的热处理。热处理工艺对gh4738镍基高温合金的组织和性能非常重要,通过合适的热处理工艺,能够充分发挥材料的潜力。
[0160]
通过查阅国内外相关资料,gh4738镍基高温合金常用的热处理制度有两种分别为:亚固溶热处理制度和过固溶热处理制度。其中亚固溶热处理制度包括:固溶处理:将锻件加热到(996
‑
1038)℃,保温4h
±
0.5h,水冷或油冷;稳定化处理:将锻件加热到845℃,保温4h
±
0.5h,空冷;时效处理:将锻件加热到760℃,保温16h
±
1h,空冷。过固溶热处理制度包括:固溶处理:将锻件加热到(1038
‑
1079)℃,保温1h
‑
4h,空冷;稳定化处理:将锻件加热到845℃,保温4h
±
0.5h,空冷;时效处理:将锻件加热到760℃,保温16h
±
1h,空冷。
[0161]
2.3.1固溶处理工艺方案
[0162]
表2
‑
4固溶温度处理工艺方案
[0163][0164]
为研究gh4738镍基高温合金最佳固溶处理时间以及冷却方式,选取最佳变形温度和变形程度的三组10mm
×
10mm
×
10mm的锻件试样。三组试样在960℃分别固溶处理4h、1h和
7min,然后均油冷至室温。将去除油渍的三组试样845℃保温4h后空冷至室温。最后将三组试样在760℃时效处理16h,空冷至室温。测试并分析3组试样的显微组织和硬度的变化,确定最佳的固溶时间。
[0165]
同样选择与上述相同变形温度、变形程度的锻件,固溶温度和固溶时间不变,将冷却方式设置为水冷、油冷和空冷三种方式,并将三组试件进行与上述相同的稳定化处理和二次时效。选择出最佳的固溶处理冷却方式。
[0166]
2.3.2稳定化处理及时效处理工艺方案
[0167]
在最优的变形温度和变形程度下的锻件,通过最优的固溶处理方式,按照对应1:1:4的时间比例,初步制定了稳定化处理的时间和时效处理的时间。整个流程均选取最佳的工艺参数,观察并分析最优工艺参数下锻件性能提升的原因。
[0168]
2.4冲蚀磨损试验
[0169]
为研究不同热加工工艺下的gh4738镍基高温合金冲蚀磨损性能,选取不同热加工工艺下磨损试样尺寸为50mm
×
50mm
×
10mm的gh4738镍基高温合金,采用如图2所示的冲蚀磨损试验机,进行冲蚀磨损试验。通过观察该合金的微观组织结构及冲蚀磨损后的表面形貌,结合该合金的冲蚀速度以及冲蚀磨损特征机理分析材料的抗冲蚀磨损性能。
[0170][0171][0172]
其中,冲蚀速度可以定量的表征该合金在不同工艺下的磨损速度,进而说明该合金在某种冲蚀条件的抗冲蚀磨损性能。通过冲蚀前后称重,对比材料不同的重量,用冲蚀磨损量代表冲蚀粒子对材料表面的影响,这被定义为冲蚀速度。根据公式(2
‑
1)、(2
‑
2)计算冲蚀速度。冲蚀磨损工艺参数如下,测试环境为室温,测试压力为5kg/cm2,冲蚀粒子速度为88m/s,冲蚀角度为90
°
,测试时间为600s,冲蚀粒子质量为2kg。
[0173]
2.5试验表征方法
[0174]
2.5.1金相组织观察
[0175]
对不同热加工工艺下的gh4738镍基高温合金进行金相组织观察分析。在金相观察分析前需要将该合金切割成10mm
×
10mm
×
10mm的试样,接着将高温合金试样进行磨光、电解抛光以及金相腐蚀。电解抛光可以去除试样表面的划痕,使得金相更加清晰,抛光溶液为20%hcl 80%ch3oh,电压20~25v,时间7~10s,金相腐蚀剂为3gcucl2 20mlhcl 30mlc2h5oh。本实施例采用蔡司光学显微镜,将腐蚀后的试样在50、100、200、500、1000倍数下观察和分析。
[0176]
2.5.2sem/ebsd分析
[0177]
为了观察不同热加工工艺下的gh4738镍基高温合金γ
′
相的形貌、尺寸和分布,需要将gh4738镍基高温合金切割成10mm
×
10mm
×
10mm的试样,后将高温合金试样进行磨光、电解抛光以及电解腐蚀。电解抛光溶液为20%hcl 80%ch3oh,电压18~20v,时间5~10s。
电解腐蚀溶液为170mlh3po4 10mlh2so4 15gcr2o3,电压3~5v,时间5~10s。将电解腐蚀后的试样放置于扫描电镜上进行微观组织观察和能谱分析。扫描电子显微镜(sem)测试试样需经过电解抛光和电解腐蚀,电子背散射衍射(ebsd)测试试样需经过电解抛光。
[0178]
2.5.3硬度检测
[0179]
硬度测试采用rh
‑
150a型洛氏硬度计,其通过将硬钢球或金刚石锥压入或撞击样品表面,并通过测量金属的局部塑性变形来反映金属硬度的测试。同一个试件反复进行5组试验并记录试验数据,将数据中最大值和最小值去掉后求取平均值,即为所测的硬度值。本实施例的硬度值均为洛氏硬度,单位为hrc。
[0180]
2.5.4tem分析
[0181]
将需要进行透射电子显微镜(tem)测试的gh4738镍基高温合金样品,使用线切割机将其剪切为8mm
×
8mm
×
2mm的方形薄片,用金相砂纸将方形薄片抛磨至65μm以下,然后使用双喷减薄仪进行剪薄处理,在(
‑
40℃)
‑
(
‑
35℃),50v电压,40ma
‑
45ma的电流环境中制得透射电镜薄片试样,其中电解液采用10%hclo4 90%c2h5oh的混合溶液,后用透射电镜对薄片试样进行微观组织观察和分析。
[0182]
2.5.5平均晶粒尺寸统计
[0183]
需要统计平均晶粒尺寸的gh4738合金试样,经化学腐蚀后显现出晶界,使用金相显微镜采集试样的晶界分布照片,通过image j软件测量照片中晶粒的直径,每个晶粒取三个不同角度且较为典型的位置测量,三组数据取平均值即为每个晶粒的测量值。根据astm等级表结合晶粒的测量值,对图片中的晶粒进行分类并计算每一等级所占的百分比,对同一等级的晶粒取平均值。每个等级晶粒的平均值与其所占百分比的乘积之和为该种材料的平均晶粒尺寸。
[0184]
2.5.6γ
′
相含量统计
[0185]
需要统计γ
′
相含量的gh4738合金试样,经电化学腐蚀后显现出γ
′
相,使用扫描电镜采集试样的γ
′
相分布照片,通过image pro plus软件统计图片中最亮的γ
′
相所占图片像素面积的百分比,即为γ
′
相的含量。每组试验统计三次并取平均值。
[0186]
3.gh4738合金在不同变形工艺参数下组织和性能的演变规律
[0187]
3.1引言
[0188]
对于变形高温合金来说,使锻件得到均匀分布的晶粒尺寸和弥散分布的γ
′
相是其获得优良综合力学性能的保障。经过变形所制备的合金锻件的微观组织是否均匀取决于合理的变形工艺参数。gh4738合金的γ
′
相含量较高(体积分数约为23.5%),在变形过程中较难控制锻件的组织均匀性。另外,合金的变形过程的终锻温度一般都会被限定在γ
′
相完全回溶到基体的温度线以下。若能够掌握γ
′
相在变形过程中的溶解及析出行为,则对控制gh4738合金变形后的晶粒尺寸、γ
′
相尺寸及其分布均具有很重要的意义。综上所述,需对gh4738合金在变形过程中的晶粒细化和γ
′
相在变形过程中的溶解及析出行为规律进行研究。
[0189]
随着加热温度的不断升高,该合金中的γ
′
相的体积分数呈下降趋势。当加热温度升高到一定温度时,γ
′
相将会完全溶解到合金基体中,此时材料将呈现出单一γ相。通常行业内研究者认为高温合金在高温下的静态溶解过程与该合金中各种元素的扩散行为有着非常紧密的关系。与此同时,合金中的第二相在高温下的溶解与析出行为也是高温合金
研究中的一个重要的相变过程。此外,第二相对合金变形过程中的晶粒细化有着很重要的影响。热加工过程中,γ
′
相与合金中位错的交互作用是影响γ
′
相在基体中分布规律以及再结晶行为的主要因素。有学者表明,γ
′
相可以阻碍晶界迁移,并对材料的动态再结晶有促进作用,从而对晶粒的细化有利。另有学者表明,在热变形过程中,位错与γ
′
相的交互作用可以促进γ
′
相的溶解。变形完成后,随着锻件温度的降低,溶质原子会在晶界处和缺陷位置析出,因此γ
′
相会在γ基体中重新分布。虽然目前已有研究人员对热加工过程中晶粒细化和γ
′
相中的演变规律进行研究,但大多数是基于热模拟机上的试验,由于试验条件过于理想化,以致其与实际的生产加工之间存在着一定的差距。
[0190]
因此,本实施例对gh4738合金棒坯进行不同变形温度和不同变形程度的热变形试验,较为系统性的研究了该合金变形后晶粒细化行为和γ
′
相的析出规律。并分析了变形后该合金的强化机理。本实施例研究为gh4738合金棒坯的变形工艺参数的制定提供一定的试验基础和理论依据。
[0191]
3.2变形温度对gh4738合金组织和性能的影响
[0192]
为了探究在自由锻工艺下,gh4738合金锻造涡轮盘的热加工工艺。制定了在同一变形量下,不同变形温度的热加工工艺方案,如表3
‑
1所示。在分析实际结果后,可以将试验结果分为两个部分,分别为较高变形温度(1150℃以下)和较低变形温度(1150℃以上),四组锻饼均未出现变形裂纹。
[0193]
表3
‑
1锻前加热工艺实际结果
[0194][0195]
图3a
‑
f为gh4738合金在不同变形温度下的变形组织。这两组试样对应的是较低变形温度(低于1150℃)的锻件。当变形温度为1120℃时,晶粒分布均匀细小,没有出现混晶,平均晶粒尺寸为14μm。γ'相呈球形分布于γ基体中,γ'相的平均直径约为40.42nm,体积分数约为15%。由第二相的粒径分布来看,大多数的γ'相分布于35
‑
50nm的范围内,小部分分布于35nm以下和50nm以上的范围内。当变形温度为1140℃时,晶粒分布较为均匀,再结晶较为充分。但较大晶粒与较小晶粒的差距略大于1120℃,其平均晶粒尺寸为17μm,γ'相同样呈球形分布于γ基体中,γ'相的平均直径约为40.47nm,体积分数约为16%。根据第二相的粒径分布来看,大多数的γ'相分布同样是分布于35
‑
50nm的范围内,但γ'相在该范围内各个区间的分布有一些差距。就目前的研究结果表明,γ'相粒径分布的差距对材料性能影响优先级均在细晶强化和γ'相体积分数之后。通过对比图3a和图3b的晶界碳化物可以得出,变形温度为1120℃时,碳化物多以较大尺寸的块状形式分布于晶界上;变形温度为1140℃时,晶界上的块状碳化物含量较少,并可以观察到更小尺寸的碳化物在晶界上析出,同时也可以观察到大晶粒周围晶界上的碳化物较少。结合两组锻件的晶粒尺寸分析可得,较大尺寸的块状碳化物可以对再结晶晶粒的生长起到钉扎作用。
[0196]
图4a
‑
f为gh4738合金在不同变形温度下的变形组织。这两组试样对应的是较高变形温度(高于1150℃)的锻件。当变形温度为1160℃时,晶粒分布均匀较为细小,且没有出现
混晶,平均晶粒尺寸为23μm。γ'相呈球形分布于γ基体中,γ'相的平均直径约为42.97nm,体积分数约为15.5%。由第二相的粒径分布来看,大多数的γ'相分布于35
‑
50nm的范围内,小部分分布于35nm以下和50nm以上的范围内。当变形温度为1180℃时,晶粒分布较为均匀,再结晶比较充分。但较大晶粒与较小晶粒的差距略大于1160℃,其平均晶粒尺寸为30μm,γ'相同样呈球形分布于γ基体中,γ'相的平均直径约为48.32nm,体积分数约为16%。根据第二相的粒径分布来看,大多数的γ'相分布同样是分布于40
‑
60nm的范围内,但γ'相在该范围内各个区间的分布仍有一些差距。经分析较高变形温度的两组试验,同样可以得出细晶强化和γ'相体积分数对材料力学性能影响较大。通过对比图4a和图4b的晶界碳化物可以得出,变形温度为1160℃时,观察到一个大尺寸的碳化物分布于晶界上,查阅相关文献可知这种大尺寸的碳化物为初生的mc碳化物,很难观察到小尺寸的碳化物在晶界析出;变形温度为1180℃时,晶界上的未观察到任何大块的碳化物,并且小尺寸的碳化物在晶界上析出的数量也很少。结合两组锻件的晶粒尺寸分析可得,较高变形温度的锻件由于失去块状碳化物的钉扎作用,锻件的晶粒尺寸会随变形温度的升高逐渐以更大速率长大。由于两组锻件变形量均比较大,晶粒虽有所长大,但尺寸分布仍较为均匀。
[0197]
图5为不同的变形温度锻件的平均硬度和γ'相的对比。其中变形温度为1120℃锻件的硬度为37hrc,变形温度为1140℃锻件的硬度为35hrc,变形温度为1160℃锻件的硬度为34hrc,变形温度为1180℃锻件的硬度为33.5hrc。结合上文的晶粒变化可得,两组较高变形温度的锻件,随着变形温度的升高,硬度呈持续下降趋势,这与锻件晶粒尺寸逐渐变大同样有直接关系。随变形温度升高而引起晶粒尺寸的进一步变大最终导致的硬度有较大幅度的下降,对于较高的变形温度的锻件来说,主要是变形温度已经超过碳化物溶解到基体的温度(1150℃),大部分晶界失去碳化物的钉扎作用,从而导致晶粒较大幅度的长大。随着晶粒尺寸长大速率的升高,在力学性能上则表现为材料硬度持续的较大速率的下降。
[0198]
3.3变形程度对gh4738合金组织和性能的影响
[0199]
为了探究在自由锻工艺下,gh4738合金锻造涡轮盘的热加工工艺。制定了在同一变形温度下,不同变形量的热加工工艺方案,实际变形参数如表3
‑
2所示。在分析实际结果后,三组试验结果的变形量均未达到预期的数值,但三组大变形量试样的参数仍然有一定的变形量梯度,三组锻饼同样未出现变形裂纹。
[0200]
表3
‑
2变形量工艺实际结果
[0201][0202]
图6a
‑
i为gh4738合金在不同变形程度下的变形组织。这三组试样均为大变形量(高于50%)的锻件,但由于变形温度(1160℃)已超过碳化物的完全回溶温度(1150℃),因此三组锻件的晶粒尺寸会较大。当变形量为58%时,晶粒分布均匀但较为粗大,没有出现混晶,平均晶粒尺寸为30μm。γ'相呈球形分布于γ基体中,γ'相的平均直径约为41.34nm,体积分数约为15%。由第二相的粒径分布来看,大多数的γ'相分布于35
‑
50nm的范围内,小部分分布于35nm以下和50nm以上的范围内。当变形量为65%时,晶粒分布较为均匀,再结晶较为充分,但晶粒依然较为粗大。65%变形量晶粒较58%变形量的差距较小,其平均晶粒尺寸
为28μm,γ'相同样呈球形分布于γ基体中,γ'相的平均直径约为42.06nm,体积分数约为16%。根据第二相的粒径分布来看,大多数的γ'相分布同样是分布于35
‑
50nm的范围内,但γ'相在该范围内各个区间的分布有一些差距。当变形量为70%时,晶粒分布依然较为均匀,再结晶较为充分,晶粒较前两者的有明显的减小趋势。70%变形量平均晶粒尺寸为25μm,γ'相同样呈球形分布于γ基体中,γ'相的平均直径约为42.29nm,体积分数约为16.5%。根据第二相的粒径分布来看,大多数的γ'相分布同样是分布于35
‑
50nm的范围内,但γ'相在该范围内各个区间的分布有一些差距。通过对比图6a、图6b和图6c的晶界碳化物可以得出,在三种变形量锻件的晶界上均未观察到大颗粒的块状碳化物,但可以观察到有细小的碳化物在晶界析出。结合两组锻件的晶粒尺寸分析可得,失去块状碳化物对晶界的钉扎作用,即使变形量进一步增大,也不能阻止晶粒的长大。
[0203]
图7为不同的变形程度锻件的平均硬度和γ'相的对比。其中变形量为58%的锻件的硬度为31hrc,变形量为65%的锻件的硬度为32hrc,变形量为70%的锻件的硬度为33.5hrc。结合上文的晶粒变化可得,三组较高变形温度不同变形量的锻件,随着变形量的增加,硬度呈上升趋势,这与锻件晶粒尺寸逐渐变小有直接关系,但三组试样的硬度均处于较低的水平。随变形量的增加而引起晶粒尺寸的减小最终使得硬度升高,对于较高变形温度的锻件来说,依旧无法弥补失去碳化物钉扎晶界所导致的在锻前晶粒过分长大带来的缺陷。因此,锻前晶粒的过分长大对材料硬度下降的优先级要高于再结晶后的细晶强化作用,前两者又高于锻件的沉淀强化作用,因为此时第二相的含量较低。主要是变形温度逐渐接近碳化物溶解到基体的温度(1150℃),部分晶界失去碳化物的钉扎作用,从而导致晶粒长大,在力学性能上则表现为硬度下降。
[0204]
3.4阶梯升温下变形程度对gh4738合金组织和性能的影响
[0205]
为了探究在自由锻工艺下,gh4738合金锻造涡轮盘的热加工工艺。制定了在同一变形温度下,不同变形量的热加工工艺方案,实际变形参数如表3
‑
3所示。在分析实际结果后,四组锻饼同样未出现变形裂纹,并对阶梯升温的加热工艺进行了研究。阶梯升温的方法如下:先将所述gh4738合金棒材坯料升温至800℃后保温30min,随后所述gh4738合金棒材坯料每升高50℃保温10min,直至升温至变形温度后再保温15min,整个阶梯升温过程中的升温速率均为30℃/min。
[0206]
表3
‑
3变形量工艺实际结果
[0207][0208][0209]
图8a
‑
f为gh4738合金在阶梯升温下不同变形量的变形组织。这两组试样对应的是较低变形温度(低于1150℃)的锻件。当变形量为62%时,晶粒分布均匀细小,没有出现混晶,平均晶粒尺寸为23μm。γ'相呈球形分布于γ基体中,γ'相的平均直径约为56nm,体积分数约为15%。由第二相的粒径分布来看,大多数的γ'相分布于45
‑
65nm的范围内,小部分分布于45nm以下和65nm以上的范围内。当变形量为68%时,晶粒分布较为均匀,再结晶较为
充分。但较大晶粒与较小晶粒的差距略大于变形量为62%,其平均晶粒尺寸为20μm,γ'相同样呈球形分布于γ基体中,γ'相的平均直径约为53.46nm,体积分数约为16%。根据第二相的粒径分布来看,大多数的γ'相分布同样是分布于45
‑
65nm的范围内,但γ'相在该范围内各个区间的分布有一些差距。通过对比图8a和图8b的晶界碳化物可以得出,两种变形量锻件均由两种尺寸的晶粒,其中较大尺寸的晶粒被更小的尺寸晶粒包围,说明在70%变形量以下锻件的再结晶基本完成;同时也可以观察到变形量为68%的锻件中γ'相的分布相对前者更加均匀。造成这种现象的主要原因是随着晶粒的细化,晶界面积增加,其为合金变形过程中的元素扩散提供高速通道。
[0210]
图9a
‑
f为gh4738合金在阶梯升温下不同变形量的变形组织。这两组试样对应的是较低变形温度(低于1150℃)的锻件。当变形量为72%时,晶粒分布均匀细小,没有出现混晶,平均晶粒尺寸为18μm。γ'相呈球形分布于γ基体中,γ'相的平均直径约为53.48nm,体积分数约为15%。由第二相的粒径分布来看,大多数的γ'相分布于45
‑
65nm的范围内,小部分分布于45nm以下和65nm以上的范围内。当变形量为80%时,晶粒分布较为均匀,再结晶较为充分。但较大晶粒与较小晶粒的差距略大于变形量为72%时,其平均晶粒尺寸为15μm,γ'相同样呈球形分布于γ基体中,γ'相的平均直径约为47.70nm,体积分数约为16%。根据第二相的粒径分布来看,大多数的γ'相分布同样是分布于40
‑
60nm的范围内,但γ'相在该范围内各个区间的分布有一些差距。变形量为70%以上的两组试样晶粒尺寸相比70%以下的锻件更加细小且晶粒较为均匀,同时两种变形量的γ'相的分布均较为弥散。随着变形量的增加锻件中γ'相的尺寸却逐渐降低,但γ'相的析出量并未大幅度的增加。同样说明了更高的晶界面积对变形过程中的溶质原子扩散有促进作用,基体中均匀分布的溶质原子为γ'相的弥散分布奠定基础。
[0211]
图10为不同的变形量锻件的平均硬度和γ'相的对比。其中变形量为62%锻件的硬度为36.5hrc,变形量为68%锻件的硬度为38.5hrc,变形量为72%锻件的硬度为40hrc,变形量为80%锻件的硬度为41hrc。结合上文的晶粒变化可得,四组较低变形温度的锻件,随着变形量的增加,硬度呈上升趋势,这与锻件晶粒尺寸逐渐变小有直接关系。由于相对较低的变形温度(1140℃)和合适的锻前加热工艺,变形前处于变形温度下的棒坯具有适中的变形抗力,保证在变形过程中不会产生变形裂纹;此时棒坯的晶粒也不会过度长大,同时大变形量能够使锻件完全进行再结晶,保证了变形后锻件得到细小且均匀的晶粒,从而使材料具有较高的强度。由于此时锻件中第二相未完全析出,对材料强度的影响较小,需要通过热处理来进一步使材料得到强化。
[0212]
3.5本实施例小结
[0213]
(1)在直接升温的热加工工艺下,大变形量的gh4738合金锻件,随着变形温度的增加,锻件的晶粒尺寸逐渐增大,硬度逐渐降低。当变形温度超过1150℃时,锻件的晶粒尺寸会有较大幅度的长大。主要是因为当锻前加热温度超过1150℃时,棒坯中的碳化物已经全部回溶到基体中,晶界失去碳化物的钉扎作用则会快速长大。因此在相同的变形量下,低于1150℃的两组锻件的组织较为理想。
[0214]
(2)在直接升温的热加工工艺下,较高变形温度的gh4738合金锻件,随着变形量的增加,晶粒尺寸逐渐变小,硬度也逐渐增加。但由于变形温度较高,失去碳化物对晶界的钉扎作用,不同变形量的锻件的晶粒尺寸均较大,且整体硬度表现较低。当gh4738合金的变形
温度高于1150℃时,变形温度对材料硬度的影响程度比变形程度更高。
[0215]
(3)在阶梯升温的热加工工艺下,较低变形温度的gh4738合金锻件,随着变形量的增加,晶粒尺寸逐渐变小,硬度也逐渐增加。由于变形温度低于1150℃,锻前加热阶段的升温速率较慢,因此锻件的晶粒尺寸明显减小,硬度也有较大幅度的升高。由于锻前棒坯的晶粒并未过渡长大以及碳化物对晶粒的钉扎作用,因此锻件整体硬度表现较高。
[0216]
(4)针对自由锻条件下的gh4738镍基高温合金变形工艺来说,锻前的升温速率具有最高的优先级,其次是变形温度,最后是变形程度。较缓的锻前升温速率、较低的变形温度以及较大的变形量,可以得到使用性能良好的gh4738合金锻件。
[0217]
4.热处理工艺对gh4738合金锻件组织和性能的影响规律
[0218]
4.1引言
[0219]
gh4738合金属于γ
′
相沉淀硬化型镍基高温合金,通常需要经过热处理使得材料中的γ
′
相得以充分析出,从而使材料达到使用要求。对于gh4738合金来说,其对应美国的waspaloy高温合金。经查阅美国航空局的相关标准可知,waspaloy高温合金有两种热处理工艺,一种是亚固溶热处理方案,另一种是过固溶热处理方案。亚固溶方案具体参数为:1020℃/4h/ac 845℃/4h/ac 760℃/16h/ac;过固溶方案具体参数为:1080℃/4h/ac 845℃/24h/ac 760℃/16h/ac。目前亚固溶热处理方案在国内也经常被应用于涡轮盘的生产中,而过固溶方案通常被应用于烟气轮机叶片的生产中。对于gh4738镍基高温合金来说,合金的晶粒尺寸、γ
′
相以及碳化物都会对其硬度、强度、塑性和韧性等力学性能均有影响。γ
′
相的含量决定了合金的强度,材料的抗拉强度和屈服强度都会随着γ
′
相含量的增加而得到提高,随之而来的塑性也会相应的降低。产品的需求和γ
′
相的溶解温度是热变形工艺和热处理工艺方案制定的重要依据。因此,若要通过选择合理的热加工工艺和热处理工艺,获得良好的组织,进而提高合金使得使用性能,因而需要掌握析出相的析出规律。高温合金中第二相的含量的变化和调整,对显微组织、组织稳定性以及最终性能都具有重要的影响。在日常的生产过程中,不同批次的高温合金中的γ
′
相和碳化物的含量并不相同,并且它们的析出量、析出温度和溶解温度也会发生相应的变化。因此,需要根据合金元素含量和组织特征以及热变形工艺来制定合理的热处理方案。
[0220]
4.2gh4738合金锻件热处理工艺的制定
[0221]
为了探究在自由锻工艺下,gh4738镍基合金锻造涡轮盘的热处理工艺。首先使用了行业内制造涡轮盘锻件经常使用的亚固溶热处理方案,其主要参数为1020℃/4h/ac 845℃/4h/ac 760℃/16h/ac。通过分析亚固溶热处理方案下锻件的晶粒和γ
′
相的变化,来进一步制定合适自由锻涡轮盘锻件的热处理方案,用以得到最佳的使用性能。
[0222]
图11a
‑
d为较大变形量(62.5%)不同变形温度锻件在亚固溶热处理下的组织。图11a和图11b两组对应较低变形温度(低于1150℃)的锻件热处理后的组织。当变形温度为1120℃时在热处理后,晶粒分布均匀,但较热处理前已经长大,平均晶粒尺寸为71μm,其硬度值为34.5hrc。当变形温度为1140℃时在热处理后,晶粒分布均匀,晶粒同样发生长大,平均晶粒尺寸为78μm,其硬度值为33hrc。热处理后两组锻件的晶粒尺寸均发生长大且差距较小,因此较热处理前硬度会有一定程度的下降。图11c和图11d两组对应较高变形温度(高于1150℃)的锻件热处理后的组织。当变形温度为1160℃时在热处理后,晶粒分布均匀,但较热处理前已经长大,平均晶粒尺寸为84μm,其硬度值为31.5hrc。当变形温度为1140℃时在
热处理后,晶粒分布均匀,晶粒同样发生长大,平均晶粒尺寸为98μm,其硬度值为30.5hrc。热处理后两组锻件的晶粒尺寸均发生长大但幅度较小,因此较热处理前硬度仅有小幅度的下降。综合对比四组试样,经热处理后晶粒尺寸比较接近但均已长大,相应的硬度也会下降。由本实施例第3部分内容可知,锻件的晶粒尺寸对硬度有很大的影响,而热处理后的晶粒长大是不可逆的,若需要高强度的锻件产品,则需要保证热处理后锻件的晶粒基本上不发生变化。
[0223]
图12a
‑
c为较高变形温度(1160℃)不同变形量(高于50%)锻件在亚固溶热处理下的组织。图12a、图12b和图12c为三组对应58%、65%、70%变形量的锻件热处理后的组织。当变形量为58%的锻件在热处理后,晶粒分布均匀,但较热处理前已经长大,平均晶粒尺寸为101μm,其硬度值为30.5hrc。当变形量为65%的锻件在热处理后,晶粒分布均匀,晶粒同样发生长大,平均晶粒尺寸为90μm,其硬度值为31.5hrc。当变形量为70%的锻件在热处理后,晶粒分布均匀,但较热处理前已经长大,平均晶粒尺寸为86μm,其硬度值为32.5hrc。热处理后两组锻件的晶粒尺寸均发生长大且差距较小,因此较热处理前硬度会有一定程度的下降。综合对比四组试样,经热处理后晶粒尺寸比较接近但均已长大,相应的硬度也会下降。
[0224]
由图13所示,选取变形温度为1160℃变形量为58%的锻件观察其热处理前后的第二相变化。可以看出热处理前后的γ'相在形态上均为球形。热处理前后γ'相在γ基体上的分布大致相同,但热处理后的γ'相分布更加均匀。热处理后γ'相的体积分数较热处理前有一定的程度的增加,并且此时γ'相接近于完全析出。热处理后的γ'相尺寸有明显的长大。此外,热处理前后的硬度变化不大。在镍基高温合金中γ'相的析出总量与合金中al ti元素的总含量有关。对于已选定的镍基高温合金来说,合金中al ti元素的总含量是确定的,且γ'相在热处理后基本全部析出,此时γ'相的大小和γ'相的数量呈负相关。γ'相长大的原因是奥斯特瓦尔德熟化的影响。γ'相粒径增大的同时两个γ'相之间的间距会变大,此时γ'相对位错的阻碍作用就会相应的减弱。对于已选定的镍基高温合金来说,γ'相粒径越大,γ'相对位错的阻碍作用减弱的效果就越明显。结合热处理前后锻件硬度的变化,分析可得亚固溶热处理方案并不适合上文中的高变形温度下的大变形量锻件。由本实施例第3部分可知,锻件的晶粒尺寸对硬度有很大的影响,而热处理后的晶粒长大是不可逆的,若需要高强度的锻件产品,则需要保证热处理后锻件的晶粒基本上不发生变化。并且锻件中的γ'相从粒径和分布上都是较为合理的,但此时的γ'相并未完全析出。综合分析,亚固溶热处理后的锻件较热处理前硬度有较为明显的下降,造成下降的主要因素是晶粒较大幅度的长大,次要因素是γ'相粒径的长大。
[0225]
为得到较高使用强度的锻件,需要制定一个合适上述锻件的“改良”热处理方案。“改良”热处理方案是在亚固溶热处理方案的基础上经过一系列的改进与测试来确定。首先根据gh4738镍基高温合金的ttt曲线,可以得出相转变温度为960℃。并且在现有的4小时固溶保温条件下,亚固溶温度越接近1040℃时,晶粒长大的可能性越大,因此我们选择960℃的固溶温度为最佳。在固溶时间上,接近1040℃的固溶温度下,保温时间越长晶粒长大的可能性越大。因此,我们需要减少保温时间来尽量降低固溶过程中晶粒尺寸的长大。在固溶过程中γ'相的调整方面,加快固溶处理的冷却速度,可以有效的减缓γ'相奥斯特瓦尔德熟化的进行。从而得到大量小尺寸的γ'相,这对材料的沉淀强化十分有利。但也要注意随着
冷却速率的增加,在淬火时存在开裂的风险。由于稳定化处理温度为mc碳化物向m
23
c6碳化物转化的最适宜温度,因此对于稳定化处理方案的改良,只改变保温时间,稳定化处理温度保持不变。稳定化处理过程中尝试使用水冷来代替空冷,以至于晶界处析出大量m
23
c6碳化物,此时虽可以小幅度的提升材料强度,但会导致晶界脆化,因此稳定化处理的冷却方式以空冷为宜。时效处理温度γ'相稳定析出的最佳温度,因此对于时效处理方案的改良,只改变保温时间,时效处理温度保持不变。时效过程中冷却方式若改变为水冷,则会增加淬火开裂的风险,因此时效处理的冷却方式依然以空冷为宜。热处理方案改良如下表4
‑
1所示。在热处理过程中:空冷ac的冷却速率为15℃/min,盐水冷bc的冷却速率为2000℃/min,水冷wc的冷却速率为750℃/min,油冷oc的冷却速率为200℃/min;固溶处理、稳定化处理以及时效处理后均冷却至20℃。
[0226]
通过对表4
‑
1中几组热处理方案进行试验,选取变形温度为1160℃变形量为58%的锻件结果如下,原变形件的硬度为33hrc,经方案1热处理后锻件的硬度为35hrc,经方案2热处理后的锻件的硬度为35.5hrc,经方案3热处理后的锻件硬度为38hrc,经方案4热处理后的锻件的硬度为38.5hrc。综合以上结果,热处理方案3、方案4的效果均较好,但综合考虑热处理过程中节能方面的因素,则方案4更为合适。
[0227]
表4
‑
1不同固溶保温时间的热处理方案
[0228][0229]
通过上述热处理方案的试验,可以得出随着固溶冷却速率的增加,材料的强度会随之增强。为探究不同固溶冷却速率对材料硬度的影响,在方案4的基础上设置了另外三种固溶冷却方式,分别为:盐水冷(bc)、油冷(oc)、空冷(ac)。试样为阶梯升温下变形温度为1140℃变形量为80%的锻件,具体参数如下表4
‑
2所示。阶梯升温的方法同“3.4”。
[0230]
表4
‑
2不同固溶冷却方式的热处理方案
[0231][0232]
通过对表4
‑
2中几组热处理方案进行试验,选取阶梯升温下变形温度为1160℃变形量为58%的锻件结果如下,原变形件的硬度为36hrc,经方案4热处理后锻件的硬度为42hrc,经方案5热处理后的锻件的硬度为44hrc,经方案6热处理后的锻件硬度为40hrc,经方案7热处理后的锻件的硬度为38.5hrc。综合以上结果,在同一固溶温度和时间下,随着冷却速率的增加,硬度值会有显著的提升,同时淬火应力也会不断增加,并且存在开裂的风险。
[0233]
4.3热处理对gh4738镍基高温合金锻件组织和性能的影响
[0234]
4.3.1热处理对不同变形温度gh4738镍基高温合金锻件组织和性能的影响
[0235]
图14a
‑
f为gh4738镍基高温合金在不同变形温度下锻件热处理后的组织。这两组
试样对应的是较低变形温度(低于1150℃)的锻件。当变形温度为1120℃时锻件经热处理后,晶粒较热处理前几乎没有变化,平均晶粒尺寸约为15μm。γ'相呈球形分布于γ基体中,γ'相的平均直径约为70.33nm,体积分数约为23.5%。由第二相的粒径分布来看,大多数的γ'相分布于55
‑
80nm的范围内,小部分分布于55nm以下和80nm以上的范围内。当变形温度为1140℃的锻件经热处理后,晶粒较热处理前几乎没有变化,其平均晶粒尺寸为17μm,γ'相同样呈球形分布于γ基体中,γ'相的平均直径约为70nm,体积分数约为23%。根据第二相的粒径分布来看,大多数的γ'相主要分布于60
‑
80nm的范围内。对比上述两组,平均晶粒尺寸较为接近,但1140℃锻件中存在较大的晶粒。γ'相的平均粒径非常接近,但其粒径分布有所不同。两组的γ'相粒径均发生长大,且分布较为弥散。
[0236]
图15a
‑
f为gh4738镍基高温合金在不同变形温度下锻件热处理后的组织。这两组试样对应的是较高变形温度(高于1150℃)的锻件。当变形温度为1160℃时锻件经热处理后,晶粒较热处理前几乎没有变化,平均晶粒尺寸约为23μm。γ'相呈球形分布于γ基体中,γ'相的平均直径约为72.34nm,体积分数约为23.2%。由第二相的粒径分布来看,大多数的γ'相分布于60
‑
90nm的范围内,小部分分布于60nm以下和90nm以上的范围内。当变形温度为1180℃的锻件经热处理后,晶粒较热处理前几乎没有变化,其平均晶粒尺寸为29μm,γ'相同样呈球形分布于γ基体中,γ'相的平均直径约为72.18nm,体积分数约为23%。根据第二相的粒径分布来看,大多数的γ'相分布于65
‑
85nm的范围内。分析该两组数据可得,变形温度为1180℃的锻件γ'相粒径分布更偏向于大尺寸,并且其γ'相分布更加均匀。
[0237]
图16为不同的变形温度锻件的平均硬度和平均晶粒尺寸的对比。其中变形温度为1120℃锻件在热处理后的硬度为38hrc,变形温度为1140℃锻件在热处理后的硬度为36hrc,变形温度为1160℃锻件在热处理后的硬度为34hrc,变形温度为1180℃锻件在热处理后的硬度为33hrc。结合上文的晶粒变化可得,四组不同变形温度的锻件在热处理后,随着变形温度的升高,硬度呈下降趋势,因为四组锻件晶粒尺寸几乎没有变化。但热处理后的锻件较热处理前硬度有较大幅度的提高,这是因为γ'相析出量增加导致的。综合分析,使用“改良”热处理方案处理后的锻件,热处理前后锻件的晶粒尺寸并没有变化,锻件中γ'相析出量增加、分布更加均匀,γ'相已接近完全析出。在γ'相析出较为充分、分布较为均匀的情况下,小尺寸的γ'相可以提高材料的强度。但此时,两组锻件热处理后的硬度并不高,也说明了细晶强化对gh4738镍基高温合金硬度的影响也是材料的强化的一个重要因素。
[0238]
4.3.2热处理对不同变形程度gh4738镍基高温合金锻件组织和性能的影响
[0239]
图17a
‑
i为gh4738镍基高温合金在不同变形程度锻件热处理后的组织。当变形量为58%的锻件经热处理后,晶粒尺寸基本上没有变化,平均晶粒尺寸约为31μm。γ'相呈球形分布于γ基体中,γ'相的平均直径约为82.5nm,体积分数约为23.5%。由第二相的粒径分布来看,大多数的γ'相分布于70
‑
100nm的范围内,小部分分布于70nm以下和100nm以上的范围内。
[0240]
当变形量为65%时,晶粒分布较为均匀,再结晶较为充分,但晶粒依然较为粗大。65%变形量晶粒较58%变形量的差距较小,其平均晶粒尺寸为31μm,γ'相同样呈球形分布于γ基体中,γ'相的平均直径约为79.74nm,体积分数约为23%。根据第二相的粒径分布来看,大多数的γ'相分布同样是分布于70
‑
100nm的范围内,但γ'相在该范围内各个区间的分布有一些差距。当变形量为70%时,晶粒分布依然较为均匀,再结晶较为充分,晶粒较前
两者的有明显的减小趋势。70%变形量平均晶粒尺寸为27μm,γ'相同样呈球形分布于γ基体中,γ'相的平均直径约为69.81nm,体积分数约为23.7%。根据第二相的粒径分布来看,大多数的γ'相分布同样是分布于50
‑
90nm的范围内。通过对比图17a、图17b和图17c的晶界碳化物可以得出,在三种变形量锻件的晶界上均未观察到大颗粒的块状碳化物,但可以观察到有细小的碳化物在晶界析出。结合两组锻件的晶粒尺寸分析可得,失去块状碳化物对晶界的钉扎作用,即使变形量进一步增大,也不能阻止晶粒的长大。
[0241]
图18为不同的变形程度锻件的硬度和平均晶粒尺寸的对比。其中变形量为58%的锻件的硬度为36hrc,变形量为65%的锻件的硬度为36.5hrc,变形量为70%的锻件的硬度为38hrc。结合上文的晶粒变化可得,三组较高变形温度不同变形量的锻件,随着变形量的增加,硬度呈上升趋势,这与锻件晶粒尺寸逐渐变小有关,但三组试样的硬度均处于较低水平。随变形量的增加而引起晶粒尺寸的减小使得硬度升高,对于较高变形温度锻件来说,依旧无法弥补失去碳化物钉扎晶界所导致的在锻前晶粒过分长大带来的缺陷。因此,锻前晶粒的过分长大对材料硬度下降的优先级要高于再结晶后的细晶强化作用,前两者又高于锻件的沉淀强化作用。变形温度逐渐接近碳化物溶解到基体的温度(1150℃),部分晶界失去碳化物的钉扎作用,从而导致晶粒长大,在力学性能上则表现为硬度下降。
[0242]
4.4热处理对阶梯升温下不同变形程度gh4738镍基高温合金锻件组织和性能的影响
[0243]
图19a
‑
f为gh4738镍基高温合金在较低变形温度下不同变形量的热处理组织。这两组试样对应的是较低变形温度(低于1150℃)的锻件。当变形量为62%的锻件经热处理后,晶粒尺寸几乎没有变化,平均晶粒尺寸为25μm。γ'相呈球形分布于γ基体中,γ'相的平均直径约为77.29nm,体积分数约为24%。由第二相的粒径分布来看,大多数的γ'相分布于60
‑
95nm的范围内,小部分分布于95nm以上的范围内。
[0244]
当变形量为68%的锻件经热处理后,晶粒并没有变化。其平均晶粒尺寸为21μm,γ'相同样呈球形分布于γ基体中,γ'相的平均直径约为79.49nm,体积分数约为23%。根据第二相的粒径分布来看,大多数的γ'相分布同样是分布于60
‑
100nm的范围内,但γ'相在该范围内各个区间的分布有一些差距。
[0245]
图20a
‑
f为gh4738镍基高温合金在较低变形温度下不同变形量的热处理组织。这两组试样对应的是较低变形温度(低于1150℃)的锻件。当变形量为72%的锻件经热处理后,晶粒尺寸几乎没有变化,平均晶粒尺寸为16μm。γ'相呈球形分布于γ基体中,γ'相的平均直径约为69.93nm,体积分数约为23.5%。由第二相的粒径分布来看,大多数的γ'相分布于55
‑
85nm的范围内,小部分分布于85nm以上的范围内。当变形量为80%的锻件经热处理后,晶粒并没有变化。其平均晶粒尺寸为14μm,γ'相同样呈球形分布于γ基体中,γ'相的平均直径约为69.69nm,体积分数约为24%。根据第二相的粒径分布来看,大多数的γ'相分布同样是分布于60
‑
85nm的范围内,但两者的γ'相在该范围内各个区间的分布有一些差距。变形量为80%的锻件经热处理后的γ'相分布更均匀一些。
[0246]
图21为不同的变形量锻件热处理后的平均硬度和γ'相的对比。其中变形量62%锻件热处理后的硬度为38.5hrc,变形量68%锻件热处理后的硬度为40hrc,变形量72%锻件热处理后的硬度为42hrc,变形量80%锻件热处理后的硬度为44hrc。结合上文的晶粒变化可得,四组阶梯升温的不同变形量的锻件,随着变形量的增加,硬度呈上升趋势,这与锻
件晶粒尺寸逐渐变小有直接关系。但热处理后四组试样的硬度均处于较高的水平,其中热处理后γ'相的沉淀强化也起到重要作用。
[0247]
4.5本实施例小结
[0248]
(1)gh4738镍基高温合金锻件经过亚固溶热处理后,晶粒均发生明显的长大,长大后的晶粒尺寸同样较为接近,并且热处理后锻件硬度差值较小,整体表现较差均低于热处理前的锻件。
[0249]
(2)在直接升温的热加工工艺下,不同热加工工艺下的gh4738镍基高温合金锻件经热处理后,晶粒尺寸较锻件几乎没有变化。热处理后的γ'相得到了充分的析出,分布也较为均匀,但γ'相的粒径有所增大。热处理后材料的硬度在锻件的基础上得到了进一步的提高,整体硬度表现较好。因此材料γ'相沉淀强化可以在一定程度上弥补晶粒长大导致的硬度下降,使得最终硬度呈上升趋势。
[0250]
(3)在阶梯升温的热加工工艺下,较低变形温度的gh4738镍基高温合金锻件经热处理后,晶粒尺寸基本没有长大。热处理后的γ'相同样得到了较为充分的析出,分布同样较为均匀,但γ'相的尺寸也有一定程度的长大。锻件热处理后的硬度得到了一定程度的提高,整体硬度表现优良。细晶强化和沉淀强化的双重作用使得最优的热加工工艺的锻件硬度达到最高值。
[0251]
(4)针对自由锻条件下的gh4738镍基高温合金变形工艺来说,锻前的升温速率具有最高的优先级,其次是变形温度,最后是变形程度。较缓的锻前升温速率、较低的变形温度以及较大的变形量,可以得到使用性能良好的gh4738镍基高温合金锻件。
[0252]
5.gh4738锻件热加工过程中再结晶分析及沉淀相的强化机理
[0253]
5.1引言
[0254]
gh4738镍基高温合金是一种沉淀硬化型高温合金,主要被应用于燃气轮机的涡轮盘和叶片等关键的转动部件。为满足近些年来对发动机和燃气轮机热端关键部件的日益增加的要求,在合金中加入大量的固溶强化型的元素(如:cr、co、mo等元素)和第二相沉淀强化元素(al元素和ti元素)。在gh4738镍基高温合金的热加工过程中通常伴随着晶界迁移和动态再结晶等微观组织的转变过程。再结晶晶粒将以原始晶界弓弯的形式形核并通过晶界迁移过程逐渐长大,该过程中能够有效的消除变形晶粒内的位错亚结构。合金中析出相在热加工过程中的演变同样对锻件的性能有较大的影响。另一方面,飞机发动机吸入的砂砾经过燃烧室加热后,会冲击到涡轮盘及叶片上,严重影响飞机发动机的服役寿命,给全球的航空工业造成了严重的损失。提升飞机发动机涡轮盘的抗冲蚀能力,对于飞机发动机的服役时间的延长至关重要。目前国内外的研究人员在gh4738镍基高温合金热变形过程中对于热加工的温度和时间的修正和优化,再结晶形式研究,但所优化和修正的热加工工艺并不适用于现有的热加工工艺,并且缺乏相应的组织验证。此外,该合金在现有的变形机制下再结晶晶粒形核机制以及变形晶粒亚结构的影响仍然缺少进一步的研究。本实施例以gh4738镍基高温合金锻件为研究基础,研究了合金在热加工过程中的组织演变规律。通过微观组织的研究,进一步优化gh4738镍基高温合金的热加工工艺,分析该合金在变形过程中的组织演变以及晶粒内部亚结构演变的规律,进而确定了合金在现有工艺下的再结晶机制,及其抗高温冲蚀性能。
[0255]
5.2gh4738镍基高温合金热加工过程再结晶机制和孪晶界演变规律
[0256]
5.2.1热加工工艺对合金再结晶规律影响
[0257]
本实施例试验采用阶梯升温下变形温度为1140℃变形量为80%的自由锻锻件为试验材料。当棒坯被加热到1140℃时,γ'相已经完全溶解到基体中,大部分的初生的碳化物也已经回溶到基体,此时γ'相和碳化物对晶界的钉扎作用已经大幅度的降低,因而晶界会有一定幅度的长大,同时降低了锻件的变形抗力,更有利于成形。目前,国内外学者对判定合金变形组织中晶粒是否为再结晶晶粒均采用累计取向角的方式。累计取向角是通过分析沿某一直线累计取向角的差值,来判断某一区域位错密度或亚结构的数量。
[0258]
当变形温度较高时,合金中γ'相完全溶解,大量的再结晶晶粒通过原始晶界弓弯的形式形核。再结晶晶粒首先在位错密度较高的三叉晶界处形核并长大,随着晶粒内的位错密度不断增大,则会促进非连续再结晶晶粒的形核。由图22a可知,合金锻件的平均尺寸较小且较为均匀,说明较大的变形量能促进锻件再结晶的进行。此时碳化物会抑制原始晶界的迁移,并且再结晶晶粒的形核率会有显著增加,因此在该变形工艺下合金的再结晶机制主要为非连续动态再结晶(ddrx)。
[0259]
图22c中可以看出gh4738镍基高温合金锻件和热处理件中不同位相差晶界的分布规律基本一致,均呈现出小角度晶界和大角度晶界含量接近,并且中角度晶界的含量占比很小的特征。图22d给出了gh4738镍基高温合金小角度晶界中<2
°
和2
°‑5°
的不同位相差分布规律。由图可以看出,在锻件和热处理件中<2
°
的小角度晶界的占比很高,且均在80%以上。高占比的<2
°
晶界表明合金中含有一定量的位错亚结构和亚晶界。合金在平砧镦粗变形过程中,大量位错在运动时遇到晶界的阻碍,会导致位错的缠结和堆叠,进而形成合金中的亚结构。在低层错能的金属中,完整位错通常会分解为能量更低的不全位错,因而更容易形成孪晶结构。
[0260]
图23a
‑
d为取向角沿图22a中直线分布图。通过分析图中变形晶粒的累计取向角可得,gh4738镍基高温合金锻件中变形晶粒的累计取向角最大值仅为5.8
°
。结合图26d综合分析,合金坯料在锻前加热到变形温度时,合金中的第二相已经全部回溶到基体中,含量较少的初生的碳化物也有大部分回溶到基体中,以至于在变形过程中几乎没有析出相钉扎晶界。此时的再结晶晶粒通过原始晶界弓弯的方式形核,其主要的形核机制为非连续动态再结晶机制。在变形过程中,mc碳化物会回溶到基体中,并锻件冷却过程中会在再结晶晶界和孪晶界上分散析出粒状m
23
c6碳化物,其对再结晶晶界和孪晶界有钉扎作用。
[0261]
图24a
‑
d为取向角沿图22b中直线分布图。经分析图中变形晶粒的累计取向角可得,gh4738镍基高温合金热处理中变形晶粒的累计取向角最大值仅为5.7
°
。该值与锻件变形晶粒的累计取向角最大值基本一致。这也说明本研究使用的热处理制度并未使合金中的再结晶晶粒和孪晶发生变化。因为960℃的亚固溶温度尚未达到m
23
c6碳化物的回溶温度,因此晶界中的残留初始mc和粒状m
23
c6碳化物仍能钉扎晶界,所以在热处理后gh4738镍基高温合金保持了锻件中的再结晶晶粒和亚结构不变,并未出现晶粒长大的现象,这也为合金进一步的强化奠定了基础。
[0262]
图25a
‑
d为取向角沿图22b中直线分布图。通过分析图25a中的变形晶粒的累计取向角可得,曲线中段出现陡峰,说明直线段穿过了再结晶晶界。分析图25c中变形晶粒的累计取向角可得,最大累计取向角仅为1.2
°
,说明该处存在再结晶晶界。结合图27a
‑
d分析可得,再结晶晶界处的位错强度明显高于其它区域,同时该晶界上的碳化物也较多,其对位错
的运动有阻碍作用。变形过程中小角度晶界的形成,进一步增大了合金的晶界面积,从而使合金拥有更高的强度。由于碳化物的钉扎作用,热处理后取向差角<2
°
的再结晶晶粒并未长大,这也与其采用的热处理方案有关。
[0263]
5.2.2热加工工艺对合金孪晶界演变影响
[0264]
有研究表明,由于镍基高温合金层错能较低,变形过程中较容易诱发孪晶的生成。孪晶的产生会降低再结晶晶粒的晶界能,因此,位于再结晶晶粒中具有孪晶取向的晶界对动态再结晶有促进作用。本实施例通过分析gh4738镍基高温合金热变形过程中60
°
<111>取向的初生σ3孪晶界(图26a
‑
d和图27a
‑
d中标记1所示)、高阶次的28.9
°
<101>结构的σ9孪晶界、31.6
°
<110>结构的σ27a孪晶界和35.4
°
<210>结构的σ27b孪晶界(σ9:图26a
‑
d和图27a
‑
d中标记2所示,σ27a和σ27b:图27a
‑
d中标记3所示)。依据“重合位置点阵”规则,2个相互作用的σ3孪晶界能够生成1个σ9孪晶界(即σ3 σ3=σ9),1个σ3孪晶界与1个σ9孪晶界作用可能生成1个σ3孪晶界(即σ3 σ9=σ3)也可能生成1个σ27孪晶界(即σ3 σ9=σ27),两个相邻的孪晶作用可能在三岔晶界出形成更高阶次的孪晶界。孪晶多生成于三岔晶界处且多分布在晶内,孪晶的生成可以降低三岔晶界的自由能,且比两个相邻的晶粒取向差改变所降低的晶界自由能要多,因此,孪晶在低层错能的镍基高温合金中更容易形成。
[0265]
此外,较高的变形温度会对孪晶界的生成起到促进作用。由zener原理可知,当晶界与强化相相互作用时,强化相对晶界的钉扎作用与晶界的界面能呈正相关。gh4738镍基高温合金中强化相包括γ'相和碳化物两种。在镍基合金中,共格孪晶界的界面能较低仅为0.03j
·
m
‑2,通常的大角度晶界的晶界能为0.69j
·
m
‑2。因此,孪晶界的形成过程中受强化相的钉扎作用较小。
[0266]
图26a
‑
d所示,锻件的变形晶粒中存在着较多的位错亚结构以及亚晶界,较小尺寸的再结晶晶粒中基本不存在孪晶界,而较大尺寸的再结晶晶粒中容易出现孪晶界,说明在再结晶晶粒长大的同时也伴随着孪晶界的产生。锻件中的孪晶界多分布在三岔晶界处,该处孪晶界的形成能够降低体系的界面能。合金锻件中的孪晶界以初生的σ3孪晶界为主,同时还存在少量高阶的σ9孪晶界,几乎不存在高阶的σ27孪晶界。孪晶界的产生最直接的表现是增大了晶界面积,其对合金会有一定的强化作用。
[0267]
图27a
‑
d给出了gh4738镍基高温合金热处理件的ebsd图。通过与图26a
‑
d对比分析可得,热处理后的合金中,仍以初生的σ3孪晶界为主,高阶的σ9孪晶界含量有所增加,同时也出现了高阶的σ27孪晶界。其中初生的σ3孪晶界一部分分布在晶粒内部,一部分分布在晶界上,而高阶的σ9孪晶界和σ27孪晶界则全部分布在晶界上。经热处理后合金中的孪晶界有一定程度的减少,因为部分孪晶界会在热处理过程中转变为大角度晶界。
[0268]
5.3gh4738镍基高温合金析出相的演变规律
[0269]
gh4738镍基高温合金中的析出相主要包括:γ'相、mc碳化物以及m
23
c6碳化物。
[0270]
5.3.1合金中γ'相的演变规律
[0271]
γ'相是一种面心立方有序结构相,γ'相和γ基体的相容性保证了γ'相可以存在于γ基体中。该种合金中的γ'相的含量约为23%,同时γ'相析出强化也是合金的主要强化方式。合金性能的高低主要受合金中γ'相的含量、分布、大小、形态的影响。本实施例的第3部分和第4部分中分别提到gh4738镍基高温合金锻件中γ'相的含量约为15%,合金
热处理件中γ'相的含量约为22%,且γ'相对合金强化影响的优先级分别为含量>大小>分布>形态。
[0272]
γ'相和位错存在两种耦合切割关系,一种为强耦合切割关系,另一种为弱耦合切割关系。在gh4720li高温合金中强耦合切割关系和弱耦合切割关系的过渡点为在γ'相粒径为40nm时,γ'相粒径小于40nm时表现为弱耦合切割;γ'相粒径大于40nm时表现为强耦合位错切割。在弱耦合切割关系中,临界剪切应力的估计值为τ
c
,结果如下:
[0273][0274]
其中,γ
apb
为位错切割γ'相形成的反相畴界能,b为位错的柏氏矢量,r为γ'相的粒子半径,f为γ'相的体积分数,t为位错的线张量。在强耦合关系中,临界剪切应力的估计值为τ
c
,结果如下:
[0275][0276]
其中,g为基体的剪切模量,w为常数。如图28a
‑
b所示,其为弱耦合切割关系与强耦合切割关系的示意图,其示意了成对位错切割γ'相的两种形式。图28a示意了成对位错分别切割不同的γ'相,图28b示意了成对位错分别切割同一个γ'相,其中标记5为第一条位错切割过γ'相后产生的apb,标记4为的为未被切割过的γ'相或第二条位错切割后再次恢复的γ'相。这里的反相畴界属于高能的反相畴界,第二条位错切过需要很高的能量,因此这两种小尺寸γ'相对材料的强度贡献较大。
[0277]
有研究表明,在位错弱耦合切割时,临界剪切力τ
c
与γ'相半径为正相关,即随着γ'相的增加τ
c
不断增加;在位错强耦合切割时,临界剪切力τ
c
与γ'相半径为负相关,即随着γ'相的增加τ
c
不断减少。位错弱耦合切割与位错强耦合关系的分界点:当γ'相的粒径等于切割γ'相的位错对的间距时,用公式表示为:
[0278][0279]
其中d为γ'相的粒径,f为γ'相对位错的钉扎力,γ
apb
为反向畴界能。将两种位错对γ'相的切割关系与γ'相粒径的关系用公式分别可以表示,位错对弱耦合切割时:
[0280][0281]
此时,位错对的间距较大,大于γ
′
相的直径,位错对与γ
′
相表现为弱耦合切割关系;位错对强耦合切割时:
[0282][0283]
此时,γ
′
相的直径较大,大于位错对的间距,位错对与γ
′
相表现为强耦合切割关系。gasson等人在对gh4720li合金中的研究发现,对于给定的d而言,τ
c
的有效值总是两种耦合切割关系中的较低值,因为位错的移动更倾向于通过两种位错切割机制中抗滑移性能最小的。在任意给定的情况下,都会有一个d值,可以优化流动应力和硬度,使其达到最优的性能。
[0284]
在gh4720li合金的强化研究中,最优的沉淀强化状态下γ'相的最佳粒径为40nm。
同时γ'相的粒径在30
‑
100nm的范围内依然有较好的强化效果,该范围内临界剪切应力值为峰值的70%
‑
100%;在20
‑
30nm以及100nm
‑
200nm的范围内会有强化效果一般,此时临界剪切应力值的范围为峰值的50%
‑
70%;当粒径大于200nm时强化效果较差,此时临界剪切应力值的范围为峰值的50%以下。gh4738镍基高温合金的γ'相与gh4720li合金中的γ'相从成分和形态上均较为接近,仅γ'相含量有一些差别,因此上述粒径与临界剪切应力对gh4738镍基高温合金也将适用。由图29可知,在gh4738镍基高温合金中的位错间距约为40nm。又因为当第一条位错切入γ'相同时第二条位错刚好切出该γ'相时强化效果最佳。因此进一步确定了γ'相的最佳粒径为40nm。
[0285]
图30a
‑
d给出了合金在不同状态下γ'相的sem图。通过分析图30a合金棒坯中γ'相的存在形式可知,棒坯中的γ'相尺寸约为200nm,γ'相在γ基体中分布较为均匀,γ'相含量约为22%,形状呈近似团絮状。图30b中合金锻件中的γ'相的尺寸约为48nm,分布上γ'相在γ基体中有一定程度的偏聚,γ'相含量约为15%,形状呈近似球形。图30c为亚固溶热处理制度下的热处理件,其中γ'相的尺寸约为120nm,γ'相在γ基体中分布较为均匀,γ'相含量约为23%,形状呈近似球形。图30d为“改良”热处理制度下的热处理件,其中γ'相的尺寸约为70nm,γ'相在γ基体中分布较为均匀,γ'相含量约为22%,形状同样呈近似球形。
[0286]
合金棒坯中γ'相的平均尺寸已超过200nm,临界剪切应力较低,其γ'相沉淀强化的效果是最差的。经变形后的锻件中的γ'相的平均尺寸约为48nm,临界剪切应力很高,但γ'相未完全析出,其γ'相沉淀强化的效果较好,但并未达到峰值。经亚固溶热处理制度后的热处理件中γ'相的平均尺寸约为120nm,临界剪切应力居中,其γ'相沉淀强化的效果较为一般。经“改良”热处理制度后的热处理件中γ'相的平均尺寸约为70nm,临界剪切应力较高,相较于锻件其γ'相析出较为完全,其γ'相沉淀强化的效果很好。
[0287]
在热加工过程中,棒坯中的粗大γ'相经过热变形过程中的回溶与析出得到了接近最佳尺寸的γ'相,后经过“改良”热处理使得γ'相得以充分析出,同时γ'相粒径有一定程度的长大。整个热加工过程中,合金中γ'相沉淀效果不断增强,再结合变形后合金的细晶强化作用,使得合金最终的性能较棒坯有很大程度的提高。
[0288]
5.3.2合金中碳化物的演变规律
[0289]
gh4738镍基高温合金中的碳化物主要含有mc和m
23
c6两种。mc碳化物的形态呈粗大的不规则立方体形态,m
23
c6碳化物更倾向于以不连续的粒状形态在晶界析出,也可以观察到片状的m
23
c6碳化物。有研究者发现大量连续成膜的晶界碳化物对合金的塑性有不利影响,并且采取了将合金的碳含量大幅度降低的措施。也有研究者发现在一些镍基高温合金中,当碳含量低于0.03%时,合金的塑性和蠕变性能将剧烈下降。mc碳化物可以分为初生和次生两种,初生的mc碳化物是在合金凝固的过程中形成的,其多分布于晶界和晶内,且尺寸较大;次生mc碳化物是在合金初溶温度以下,在合金的热加工的冷却过程中、热处理和长期服役的过程中,在合金的γ基体中析出。
[0290]
初生的mc碳化物由于尺寸较大、析出温度以及溶解温度均较高,所以在合金的热加工过程初生碳化物可以稳定的存在于基体中。而次生的mc碳化物在高温下的稳定性较差,一方面其在高温下会回溶到基体中;另一方面,其会与γ基体反应生成m
23
c6碳化物和γ'相。温度是影响合金中mc碳化物分解的重要因素。m
23
c6碳化物同样分为初生和次生两
种,初生的m
23
c6碳化物是在合金凝固过程中1300℃以下形成;次生m
23
c6碳化物的分成两种,一种是由mc转化为来,另一种是γ基体中固溶的剩余碳直接析出。
[0291]
碳化物作为gh4738镍基高温合金继γ'相之后的又一种析出强化相,大尺寸的晶界碳化物有钉扎晶界的作用,晶内碳化物则可以在一定程度上强化基体。由于合金热变形时的变形温度较高,合金中仅能观察到少量的块状的初生mc碳化物。在亚固溶热处理工艺下的热处理件,晶界析出大量且近似连续的m
23
c6碳化物,此时的晶界碳化物会显著的降低合金的塑性。图22a和图25a中的再结晶晶界和孪晶界上均存在间隔分布的粒状m
23
c6碳化物,热处理件较锻件中的晶界碳化物的含量基本接近,说明“改良”热处理并未引起晶界碳化物的大量析出,同时也没有使现有的晶界碳化物溶于基体。利用场发射扫描电镜观察了“改良”热处理件中的两种晶界碳化物,如图31a
‑
b所示。
[0292]
通过对比两种热处理方案的热处理件发现“改良”热处理件中的碳化物析出明显较少,说明另有一部分的碳化物在晶内析出。对图32中碳化物的对比分析可得,晶粒内弥散分布着大量小尺寸碳化物,该种碳化物分为两种形态,一种是形态呈薄片状的碳化物;另一种是尺寸更小的粒状碳化物。经分析图33a
‑
d的tem
‑
mapping照片可得,两种晶内碳化物均为m
23
c6碳化物。通过对图32的进一步观察可以发现,大多数的薄片状的碳化物均是以粒状碳化物为基础进一步长大而成的。在图33a
‑
d中还可以观察到,该种碳化物并未和γ'相有明显的关联,所以该种碳化物更倾向于在γ'相之间的“空隙”中形核并长大。
[0293]
结合上文中对“改良”热处理件中晶界碳化物含量基本不变的描述,可以得出以下结论:两种形态的晶内碳化物是可以在基体中稳定的。“改良”热处理工艺下的热处理件中的碳元素绝大多部分在晶内碳化物中,仅有少部分存在于晶界碳化物中。晶内碳化物在γ'相的“间隙”中形核并长大。粒状碳化物首先形核,片状的碳化物在粒状碳化物的基础上进一步形核并长大。在晶界上的初生的mc碳化物和次生的粒状m
23
c6碳化物,起到强化晶界的作用,晶内的两种形态的m
23
c6碳化物,则起到强化基体的作用。上述所有的碳化物共同作用使得合金可以在γ'相沉淀强化的基础上得到进一步的强化。在960℃的固溶处理温度有利于晶内粒状m
23
c6碳化物的形核,而845℃的稳定化处理温度下,则更有利于片状碳化物在粒状碳化物的基础上进一步形核并长大,并最终使得m
23
c6碳化物完全析出。
[0294]
5.4不同热加工工艺下gh4738镍基高温合金的高温冲蚀性能规律
[0295]
gh4738镍基高温合金被广泛的使用在烟气轮机中。烟气轮机工作时的高温烟气中含有大量高温的烟尘颗粒,同样会对烟气轮机的涡轮盘及叶片造成损伤。因此,掌握该种材料的高温冲蚀性能规律,对于材料服役寿命的预测及涡轮盘叶片有效防止过早损伤有很大的意义。作为航空发动机、燃气轮机和烟气轮机常用的涡轮盘材料,研究该种材料的热加工工艺对合金的高温冲蚀性能的影响是非常重要的。本实施例中通过对gh4738镍基高温合金在不同热加工工艺下的变形试验,探究其组合变化和力学性能的演变规律。
[0296]
hutchings等人对冲蚀磨损的定义为,靶材表面因高速运动的颗粒冲击而被去除的现象。bitter等人认为靶材因为高速运动的物体撞击而造成表面破坏的现象叫做冲蚀。材料的冲蚀磨损性能有很多的影响因素,包括磨料的大小、形状和成分,靶材的温度,冲蚀角度,冲蚀速度。其中靶材方面的影响因素还包括靶材的微观组织和力学性能。
[0297]
由于gh4738镍基高温合金是航空发动机涡轮盘的应用越来越广泛,研究热加工工艺对gh4738镍基高温合金冲蚀磨损性能的影响尤为重要。同时进一步分析梯度加热工艺下
不同热加工工艺对材料高温冲蚀磨损性能的影响。本实施例中高温冲蚀的试验条件为,冲蚀时磨料的温度为750℃,靶材的温度为750℃,磨料的总量为2kg,冲蚀速度为88m/s,冲蚀角度为90
°
,冲蚀时间为20s。
[0298]
影响高温冲蚀速率的因素包括:靶材的硬度、磨料与靶材的接触时间、靶材吸收磨料的能量值等。有研究表明,在高温合金的冲蚀过程中,当冲蚀角度为90
°
时,磨料与靶材的接触时间相比其它冲蚀角度较短,同时吸收能力值反而会较高。
[0299]
图34a
‑
d中给出了不同工艺下的高温冲蚀形貌,图中可以观察到较多的凿坑,以及少量的切削,且以冲击变形机制为主。图35为不同工艺下合金试样的高温冲蚀速率与合金的硬度关系,经对比后发现几组试样的高温冲蚀速率数值较为接近,且合金的高温冲蚀速率与合金的硬度呈负相关。
[0300]
gh4738镍基高温合金的强化主要分为晶界强化和晶内强化。由于碳化物的钉扎作用在高温下合金的晶界强化受影响较小,但对于γ'相沉淀强化来说,由于高温下位错运动加剧,使得位错与γ'相的作用形式发生改变,其中一部分由原来的位错切割γ'相变为微孪晶以及位错攀移绕过两种机制,导致γ'相沉淀强化效果减弱。gh4738镍基高温合金中,由于基体中除少量的mc碳化物和晶界m
23
c6碳化物之外,再没有其它微米级的析出相,因此相较其它高温合金在高温下阻碍位错运动的能力将进一步下降。
[0301]
5.5本实施例小结
[0302]
(1)gh4738镍基高温合金在γ单相区镦粗时的热变形锻件的再结晶机制为非连续动态再结晶。变形后的锻件中包含大量的亚结构和孪晶界,且再结晶晶界处的位错密度很高。经热处理后锻件中依以亚结构和孪晶界为主,但孪晶界的数量有所减少,再结晶晶界处的位错密度同样有一定程度的减少。
[0303]
(2)gh4738镍基高温合金在热加工过程中γ'相的演变过程包括以下几个方面:在形态上,由棒坯中的棉絮状转变为锻件中的球形,热处理后仍为球形。在尺寸上,棒坯中存在平均粒径为220nm的大尺寸γ'相,转变为锻件中平均粒径为48nm的小尺寸γ'相,热处理后长大为平均粒径为70nm的γ'相。在分布上,棒坯的γ'相分布较为均匀,锻件中的γ'相出现团聚现象,热处理后γ'相则较为均匀。在含量上,棒坯中的γ'相基本全部析出,锻件的γ'相含量仅为15%,热处理后则再次析出完全。粒径在40
‑
100nm范围内完全析出且分布均匀的球状γ'相对合金的强化效果较好。
[0304]
(3)gh4738镍基高温合金在热变形后锻件的再结晶晶界处析出少量的呈断续排布的粒状m
23
c6碳化物,热处理后粒状碳化物稳定存在且析出量基本不变,但晶粒内析出片状的m
23
c6碳化物,其在一定程度上强化了基体。
[0305]
(4)不同工艺下的gh4738镍基高温合金热加工件,在750℃的高温冲蚀条件下,冲蚀速率相差不大,冲蚀形貌主要表现为凿坑和少量的切削,所以主要以冲击变形机制为主。由于在高温下,部分位错切割小尺寸γ'相机制的改变,使得高温下的晶内的强度有一定程度的下降但塑性有所提高,但晶界强化机制对抗高温冲蚀效果表现较好。当γ'相含量接近或相同时,晶界强化在抵抗高温冲蚀的过程中占主导地位。
[0306]
综上,本实施例以开坯后的gh4738镍基高温合金棒状坯料作为初始材料,对其在不同热加工工艺下的变形行为进行了研究,分析了坯料在合金热变形过程中晶粒的细化机制,第二相及碳化物的析出规律,确定了合金在热变形过程中的再结晶形式,总结了热处理
方案对和合金组织和力学性能的影响,以及不同变形量的热处理件抗高温冲蚀性能的差异。得到了主要结论如下:
[0307]
(1)gh4738镍基高温合金棒坯热变形试验结果表明:在直接升温的加热条件下,变形温度与锻件的晶粒尺寸呈正相关,变形温度与锻件的硬度呈负相关;无论在直接升温还是阶梯升温的加热条件下,变形量与锻件的晶粒尺寸均呈负相关,变形量与锻件的硬度均呈正相关,且阶梯升温的锻件较直接升温的锻件硬度更高。同时上述不同锻件的γ'相各项特征均较为接近。热变形工艺对锻件硬度的影响主要取决于锻件的晶粒尺寸,热变形工艺对锻件晶粒尺寸的影响包括:锻前的升温方式、变形量和变形温度。
[0308]
(2)gh4738镍基高温合金锻件热处理试验结果表明:使用亚固溶热处理方案的锻件在热处理后,晶粒尺寸发生一定程度的长大,以致锻件在热处理后硬度的降低。采用“改良”热处理方案的锻件,在晶粒尺寸基本不变的基础上,γ'相得到完全析出,且分布较为均匀,虽然γ'相的粒径有所长大,但仍在强化效果较好的范围内。本实施例中不同状态的锻件在热处理后硬度均得到提升,且呈现出不同的硬度梯度。
[0309]
(3)gh4738镍基高温合金锻件晶粒的再结晶方式为非连续动态再结晶,锻件组织中包含大量的亚结构和孪晶界,且再结晶晶界处的位错密度很高,经热处理后锻件中仍以亚结构和孪晶界为主。粒径在40
‑
100nm范围内完全析出且分布均匀的球状γ'相对合金有较好的强化作用。锻件的晶界处析出了少量的呈断续排布的粒状m
23
c6碳化物,热处理后粒状碳化物稳定存在且析出量基本不变,但晶粒内析出片状的m
23
c6碳化物,其在一定程度上强化了基体。
[0310]
(4)阶梯升温下不同变形量的锻件的高温冲蚀速率相差不大,冲蚀形貌主要表现为凿坑和少量的切削,主要以冲击变形机制为主。当锻件中γ'相含量接近或相同时,晶界强化在抵抗高温冲蚀的过程中占主导地位。在γ'相含量不同时,除晶界强化机制的影响之外,γ'相含量较高的合金,抗高温冲蚀能力更好。
再多了解一些
本文用于企业家、创业者技术爱好者查询,结果仅供参考。