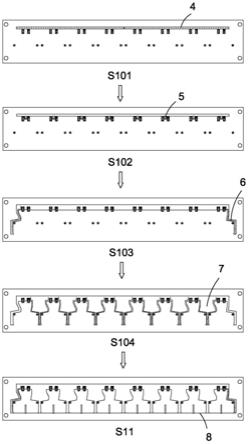
1.本发明涉及线路板加工技术领域,具体涉及一种高频线路板的制作工艺。
背景技术:
2.线路板是电子元器件电连接的提供者。它的发展已有100多年的历史了;它的设计主要是版图设计;采用线路板的主要优点是大大减少布线和装配的差错,提高了自动化水平和生产劳动率。线路板从单层发展到双面板、多层板,未来线路板生产制造技术发展趋势是在性能上向高频、高密度、高精度、细孔径、细导线、小间距、高可靠、多层化、高速传输、轻量、薄型方向发展。
3.部分高频线路板会布置金手指,如内存条等插接式结构,在制作过程中,通常先对基板进行整板电镀,再利用铣刀加工出分隔槽。传统的成型工艺,通常利用铣刀沿着高频电路板的外形或轮廓直接一次加工出分隔槽,如图1~3所示,加工完成后,金手指位置顶端会出现多切的现象,导致出现不良边9,而且在会出现掉油现象,掉油位置10分布在分隔槽的边缘。出现不良边9的原因主要是:在cnc自动加工进程中,由于铣刀从基板一侧沿另一侧直接加工,加工后的金手指位置一侧无支撑,导致金手指位置受力不均,从而出现多切现象。出现掉油的原因主要是:由于高频线路板通常使用玻纤pp作为压合材料,在铣刀切槽过程中,少量玻璃纤维细丝翘起,导致槽两侧的油墨脱落。
技术实现要素:
4.针对以上问题,本发明提供一种高频线路板的制作工艺,能够解决在成型过程中出现的不良边问题以及掉油问题。
5.为实现上述目的,本发明通过以下技术方案来解决:一种高频线路板的制作工艺,包括以下步骤:s1发料:准备基板,在基板上设计出多个并排的高频线路板区域,每个高频线路板区域内均设计有两个金手指位置;s2整板电镀:对基板进行电镀,基板上下两端面分别形成第一铜镀层、第二铜镀层;s3钻孔:对基板进行钻孔,形成通孔;s4镀通孔:对通孔进行电镀,使通孔内壁镀上第三铜镀层;s5干膜:对基板进行压干膜,经过曝光、显影后,非线路区域裸露出铜镀层,线路区域表面覆盖一层干膜;s6蚀刻:利用蚀刻液将裸露的铜镀层蚀刻掉,并除去干膜;s7防焊:在非线路区域印刷一层防焊油墨,固化后形成防焊膜;s8文字:在防焊膜上印刷上设定的文字或图案;s9锡铜镍:在线路区域的金手指位置镀上一层锡铜镍镀层;s10成型:
s101一次成型:利用铣刀在所有金手指位置上侧加工出顶边内槽;s102二次成型:利用铣刀在每两个金手指位置之间加工出金手指内槽;s103三次成型:利用铣刀在首末两个高频线路板区域的边缘加工出侧边内槽;s104四次成型:利用铣刀在每两个高频线路板区域之间加工出板间内槽;s11加工v形槽:在基板上切割出v形槽。
6.具体的,在步骤s10成型过程中,所述铣刀的转速为35~45krpm,行进速度为4~6mm/sec。
7.具体的,经过步骤s3钻孔后,还需要对通孔进行等离子去胶渣处理,除去通孔内壁的钻孔残胶。
8.具体的,所述步骤s4镀通孔过程中,对通孔进行两次电镀,第一次电镀厚度为0.2mil,第二次电镀厚度为0.4mil,所形成的第三铜镀层厚度为0.6mil。
9.具体的,第一次电镀后,需要对通孔进行检测,若通孔内产生铜瘤,则利用装有三氯化铁稀溶液的高压水枪对通孔进行冲洗,除去铜瘤后再进行第二次电镀。
10.具体的,所述三氯化铁稀溶液中三氯化铁的浓度低于0.2mol/l。
11.具体的,在完成步骤s9锡铜镍后,在板面上贴上一层离型膜,再进行后续步骤s10成型,完成步骤s10成型后再去除离型膜,所述离型膜的厚度为0.1~0.5mm。
12.本发明的有益效果是:1.本发明的高频线路板的制作工艺,通过调整成型过程中铣刀的走刀流程,先所有金手指位置上侧加工出顶边内槽,然后在每两个金手指位置之间加工出金手指内槽,然后在首末两个高频线路板区域的边缘加工出侧边内槽,最后在每两个高频线路板区域之间加工出板间内槽,调整走刀流程后,相比常规的一刀切式的走刀方式,能够使金手指位置受力均匀,从而避免出现不良边的现象;2.在完成步骤s9锡铜镍后,通过在板面上贴上一层离型膜,再进行后续步骤s10成型,完成步骤s10成型后再去除离型膜,利用离型膜的覆膜作用,能够避免玻璃纤维翘起而出现的槽边缘掉油问题;3.经过步骤s3钻孔后,需要对通孔进行等离子去胶渣处理,除去通孔内壁的钻孔残胶,并且对通孔进行两次电镀,并且在第一次电镀完成后,需要对通孔进行检测,若通孔内产生铜瘤,则利用装有三氯化铁稀溶液的高压水枪对通孔进行冲洗,除去铜瘤后再进行第二次电镀,能够解决通孔内出现铜瘤的问题。
附图说明
13.图1为常规高频线路板的加工流程示意图。
14.图2为图1中b部分的放大图。
15.图3为常规高频线路板加工完成后的结构示意图。
16.图4为本发明的一种高频线路板的制作工艺的加工流程示意图。
17.图5为经过本发明的工艺制作得到的高频线路板的结构示意图。
18.图6为图5中a部分的放大图。
19.附图标记为:基板1、高频线路板区域2、金手指位置3、顶边内槽4、金手指内槽5、侧边内槽6、板间内槽7、v形槽8、不良边9、掉油位置10。
具体实施方式
20.下面结合实施例和附图对本发明作进一步详细的描述,但本发明的实施方式不限于此。
21.实施例1参照图4~6所示,一种高频线路板的制作工艺,包括以下步骤:s1发料:准备基板1,在基板1上设计出多个并排的高频线路板区域2,每个高频线路板区域2内均设计有两个金手指位置3;s2整板电镀:对基板1进行电镀,基板1上下两端面分别形成第一铜镀层、第二铜镀层;s3钻孔:对基板1进行钻孔,形成通孔,并利用等离子去胶渣机对通孔内壁进行等离子去胶渣处理,除去通孔内壁的钻孔残胶;s4镀通孔:对通孔进行两次电镀,第一次电镀厚度为0.2mil,然后对通孔进行检测,若通孔内产生铜瘤,则利用装有三氯化铁稀溶液的高压水枪对通孔进行冲洗,三氯化铁稀溶液中三氯化铁的浓度为0.1mol/l,除去铜瘤后再进行第二次电镀,第二次电镀厚度为0.4mil,使通孔内壁镀上厚度为0.6mil的第三铜镀层;s5干膜:对基板1进行压干膜,经过曝光、显影后,非线路区域裸露出铜镀层,线路区域表面覆盖一层干膜;s6蚀刻:利用蚀刻液将裸露的铜镀层蚀刻掉,并除去干膜;s7防焊:在非线路区域印刷一层防焊油墨,固化后形成防焊膜;s8文字:在防焊膜上印刷上设定的文字或图案;s9锡铜镍:在线路区域的金手指位置3镀上一层锡铜镍镀层,在板面上贴上一层厚度为0.5mm离型膜;s10成型:s101一次成型:设定铣刀的转速为40krpm,行进速度为5mm/sec,利用铣刀在所有金手指位置3上侧加工出顶边内槽4;s102二次成型:设定铣刀的转速为40krpm,行进速度为5mm/sec,利用铣刀在每两个金手指位置3之间加工出金手指内槽5;s103三次成型:设定铣刀的转速为40krpm,行进速度为5mm/sec,利用铣刀在首末两个高频线路板区域2的边缘加工出侧边内槽6;s104四次成型:设定铣刀的转速为40krpm,行进速度为5mm/sec,利用铣刀在每两个高频线路板区域2之间加工出板间内槽7,去除离型膜;s11加工v形槽:在基板1上切割出v形槽8。
22.s12检测:经检测金手指位置3的顶端良好,且顶边内槽4、金手指内槽5、侧边内槽6、板间内槽7的边缘均无掉油现象。
23.以上实施例仅表达了本发明的1种实施方式,其描述较为具体和详细,但并不能因此而理解为对本发明专利范围的限制。应当指出的是,对于本领域的普通技术人员来说,在不脱离本发明构思的前提下,还可以做出若干变形和改进,这些都属于本发明的保护范围。因此,本发明专利的保护范围应以所附权利要求为准。
再多了解一些
本文用于企业家、创业者技术爱好者查询,结果仅供参考。