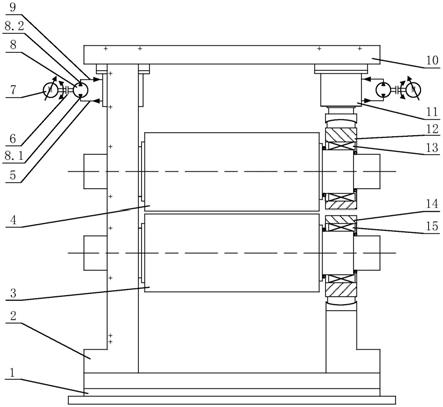
锂电池极片轧机泵控agc液压系统和装置
技术领域
1.本实用新型涉及一种极片辊压成型设备技术领域,特别涉及一种锂电池极片轧机泵控agc液压系统和装置。
背景技术:
2.锂电池作为新能源汽车三大核心零部件之一,不仅占据整车40%左右的成本,且其性能直接决定了整车的安全性和续航里程。从整车角度,要求锂电池具有长寿命、高能量密度、支持快速充电、低成本、大负载、适应恶劣环境工况等技术特点。锂电池的制造成型包含多步工序,其中正负极片辊压成型是其中关键工序之一,对电池的最终性能影响很大。正负极片辊压成型目的在于增加正负极材料的压实密度,合适的压实密度可增大电池的放电容量、减小内阻、减小极化损失、延长电池的循环寿命。
3.目前,锂电池极片辊压成型通常采用极片轧机设备,电池极片的轧制是轧辊与电池极片之间产生摩擦力,把电池极片拉进旋转的轧辊之间,电池极片受压变形的过程。极片辊压成型厚度一致性是衡量锂电池稳定性的重要指标,极片厚度精度通常要求达到
±
0.5微米,这对极片轧机液压辊缝厚度自动控制(简称液压agc)提出了很高的要求。
4.液压agc是一种通过控制进入agc油缸的油液量实现厚度在线自动调节的技术,这种方式结构简单,灵敏度高,能够满足很严格的厚度精度要求,可实现恒压力、恒辊缝轧制。传递的力和功率大的液压伺服控制系统的引入使得极片轧机能够实现压力和辊缝的在线实时调节,轧制单双层交替涂布的极片时,单层部分也能得到比较好的轧制效果,使得轧制极片的质量大大提高。
5.传统液压agc采用电液伺服阀控缸技术,阀控agc由液压油源、管路系统、伺服阀、液压缸、传感器和控制系统组成。虽然阀控agc具有良好的控制性能,但由于系统构型复杂,导致设备集成度低、装机成本高,加之液压油源的恒压运转与管路、阀口的节流损失,导致系统能源的浪费;又由于伺服阀抗污染能力差,对油液清洁度等级要求高(nas3
‑
5),系统需要设置精密的过滤装置,提高装机成本。为保障系统可靠运行,对设备维护提出了苛刻的要求。
技术实现要素:
6.本实用新型要解决的技术问题是克服现有技术的不足而提供一种锂电池极片轧机泵控agc液压系统和装置,能够实现极片恒压力、恒辊缝的高精度轧制,而且降低了系统的装机、运行及维护成本,提高了功重比和可靠性。
7.为解决上述技术问题,本实用新型所采取的技术方案是:
8.一种锂电池极片轧机泵控agc液压系统,包括控制器、伺服电机、双排量泵、阀块、过滤器、蓄能器、二位三通换向阀、溢流阀、单向阀、压力传感器、流量传感器和位移传感器;所述阀块中开设有高压孔道和低压孔道;所述伺服电机的输出轴通过联轴器与双排量泵的输入轴相连,双排量泵的油口面和agc缸的油口面均与阀块的壁面贴合安装,双排量泵的第
一油口通过低压孔道与agc缸的有杆腔相连,双排量泵的第二油口通过高压孔道和与agc缸的无杆腔相连,双排量泵的泄油口通过过滤器与低压孔道连接,双排量泵的小排量控制口和大排量控制口通过二位三通换向阀与高压孔道连接,并且二位三通换向阀与控制器相连;所述蓄能器与低压孔道相连;所述溢流阀的进油口与高压孔道相连,出油口与低压孔道相连;所述单向阀的出油口与高压孔道相连,进油口与低压孔道相连;所述压力传感器和流量传感器设置在高压孔道上,所述位移传感器安装在agc缸上;所述压力传感器、流量传感器和位移传感器均与控制器相连,控制器经伺服驱动器与伺服电机相连,对伺服电机进行闭环控制。
9.进一步的,还包括快换接头和压力继电器,所述快换接头和压力继电器均设置在低压孔道上,并且压力继电器与控制器相连。
10.进一步的,还包括温度传感器;所述温度传感器设置在低压孔道上,并且温度传感器与控制器相连。
11.进一步的,还包括二位二通换向阀、第一阻尼螺钉、第二阻尼螺钉;所述二位二通换向阀跨接在高压孔道与低压孔道之间,第一阻尼螺钉安装在二位二通换向阀与低压孔道之间,第二阻尼螺钉安装在二位二通换向阀与高压孔道之间;所述控制器与二位二通换向阀相连。
12.一种锂电池极片轧机agc装置,包括底座、安装在底座上的机架以及两个agc缸,机架为左右对称结构,其顶部连接有横梁;在机架的内腔里左右对称安装着两个上轴承座和两个下轴承座,上轴承座为活动轴承座,下轴承座为固定轴承座;上轧辊通过上轴承配合安装在上轴承座中,下轧辊通过下轴承配合安装在下轴承座中;在每个上轴承座上面的横梁上均安装有与上轴承座连接的、为上轴承座提供下压动力的agc缸;agc缸的底座安装在横梁上,agc缸的缸杆安装在相应上轴承座上;两个agc缸的外侧均设置有一套任一上述的锂电池极片轧机泵控agc液压系统。
13.一种锂电池极片轧机泵控agc液压系统压力闭环控制方法为:上位机通过总线形式将agc压力指令给定到控制器中,同时控制器接收压力传感器反馈压力,通过实时对比两种压力,pid控制器闭环控制程序输出期望转速信号至伺服驱动器,由伺服驱动器控制伺服电机带动双排量泵旋转,当无杆腔压力超过给定压力时,控制器发出负转速指令,双排量泵的第二油口从无杆腔吸油减压;当无杆腔压力低于给定压力时,控制器发出正转速指令,双排量泵的第二油口向无杆腔注油增压,从而实现系统压力的高精度控制。
14.进一步的,系统采用压力前馈补偿控制器、流量非线性补偿控制器和泄漏补偿控制器,压力前馈补偿控制器通过对设定压力进行轨迹规划,计算伺服电机转速补偿值;流量非线性补偿控制器通过接收压力、流量和转速信号,计算流量非线性补偿值;泄漏补偿控制器通过接收压力和流量信号,计算泄漏补偿值,所述所有补偿值与pid控制器输出转速信号共同作用在伺服驱动器内,使系统压力响应速度更快,控制精度更高。
15.一种锂电池极片轧机泵控agc液压系统位置闭环控制方法为:上位机通过总线形式将agc位置指令给定到控制器中,同时控制器接收位移传感器反馈位置,通过实时对比两种位置,pid控制器闭环控制程序输出期望转速信号至伺服驱动器,由伺服驱动器控制伺服电机带动双排量泵旋转,当agc缸杠杆的实际位置大于给定位置时,控制器发出负转速指令,双排量泵的第二油口从无杆腔吸油,减小缸杆的伸出量;当agc缸杠杆的实际位置小于
给定位置时,控制器发出正转速指令,双排量泵的第二油口向无杆腔注油,增加缸杆的伸出量,从而实现缸杆位置的高精度控制。
16.进一步的,系统采用位置前馈补偿控制器、流量非线性补偿控制器和流量死区补偿控制器,位置前馈补偿控制器通过对设定位置进行轨迹规划,计算伺服电机转速补偿值;流量非线性补偿控制器通过接收压力、流量和转速信号,计算流量非线性补偿值;流量死区补偿控制器通过接收压力、流量和转速信号,计算流量死区补偿值,所述所有补偿值与pid控制器输出转速信号共同作用在伺服驱动器内,使系统位置响应速度更快,控制精度更高。
17.采用上述技术方案所产生的有益效果在于:
18.(1)本实用新型省去庞大的液压站、复杂管路系统以及昂贵的伺服阀,降低了装机成本;采用伺服驱动节能技术,有效避免了传统阀控agc的溢流节流损失,降低了运行成本;还具有良好的抗污染能力,无需频繁更换系统滤芯,降低了维护成本;(2)泵控agc液压系统集成度高,方便在极片轧机机械本体安装,提高了功重比;有效避免复杂管路系统中油液跑冒滴漏以及油液杂质污染引起的伺服阀故障问题,提高了可靠性;(3)采用经典pid与压力前馈补偿、流量非线性补偿和泄漏补偿相结合的压力闭环控制,经典pid与位置前馈补偿、流量非线性补偿和流量死区补偿相结合的位置闭环控制,使系统响应速度更快,控制精度更高。
附图说明
19.图1是本实用新型锂电池极片轧机agc装置整体结构示意图;
20.图2是本实用新型液压原理图;
21.图3是本实用新型逻辑控制流程图;
22.图4是本实用新型压力闭环控制框图;
23.图5是本实用新型位置闭环控制框图;
24.图中:1
‑
底座,2
‑
机架,3
‑
下轧辊,4
‑
上轧辊,5
‑
低压孔道,6
‑
联轴器,7
‑
伺服电机,8
‑
双排量泵,8.1
‑
第一油口,8.2
‑
第二油口,8.3
‑
泄油口,8.4
‑
小排量控制口,8.5
‑
大排量控制口,9
‑
高压孔道,10
‑
横梁,11
‑
agc缸,12
‑
上轴承座,13
‑
上轴承,14
‑
下轴承座,15
‑
下轴承,16
‑
快换接头,17
‑
温度传感器,18
‑
压力继电器,19
‑
蓄能器,20
‑
过滤器,21
‑
二位三通换向阀,22
‑
阀块,23
‑
单向阀,24
‑
溢流阀,25
‑
压力传感器,26
‑
第一阻尼螺钉,27
‑
二位二通换向阀,28
‑
第二阻尼螺钉,29
‑
位移传感器,30
‑
流量传感器。
具体实施方式
25.上述说明仅是本实用新型技术方案的概述,为了能够更清楚了解本实用新型的技术手段,下面通过附图对本实用新型进行进一步阐述。
26.如图1所示,一种锂电池极片轧机agc装置,包括底座1、安装在底座上的机架2以及两个agc缸11,机架2分为左右两个,并通过横梁10联结在一起。在机架2的内腔里左右对称安装着两个上轴承座12和两个下轴承座14,上轴承座12为活动轴承座,下轴承座14为固定轴承座;上轧辊4通过上轴承13配合安装在上轴承座12中,下轧辊3通过下轴承15配合安装在下轴承座14中;在每个上轴承座12上面的横梁10上均安装有与上轴承座12连接的、为上轴承座12提供压下动力的agc缸11;agc缸11的底座安装在横梁10上,agc缸11的缸杆安装在
相应上轴承座12上;两个agc缸11的外侧均设置有一套上述的泵控agc液压系统。伺服电机7、双排量泵8和阀块22等均固定安装在agc缸11上。
27.如图2所示,一种锂电池极片轧机泵控agc液压系统,包括控制器、伺服电机7、双排量泵8、阀块22、过滤器20、蓄能器19、二位三通换向阀21、溢流阀24、单向阀23、压力传感器25、流量传感器30和位移传感器29;阀块22中开设有高压孔道9和低压孔道5;伺服电机7的输出轴通过联轴器6与双排量泵8的输入轴相连,双排量泵8的油口面和agc缸11的油口面均与阀块22的壁面贴合安装,双排量泵8的第一油口8.1通过低压孔道5与agc缸11的有杆腔相连,双排量泵8的第二油口8.2通过高压孔道9和与agc缸11的无杆腔相连,双排量泵8的泄油口8.3通过过滤器20与低压孔道5连接,双排量泵8的小排量控制口8.4和大排量控制口8.5通过二位三通换向阀21与高压孔道9连接,并且二位三通换向阀21与控制器相连;蓄能器19与低压孔道5相连;溢流阀24的进油口与高压孔道9相连,出油口与低压孔道5相连;单向阀23的出油口与高压孔道9相连,进油口与低压孔道5相连;压力传感器25和流量传感器30设置在高压孔道9上,位移传感器29安装在agc缸11上;压力传感器25、流量传感器30和位移传感器29均与控制器相连,控制器经伺服驱动器与伺服电机7相连,对伺服电机7进行闭环控制。
28.本实用新型采用伺服电机7带动双排量泵8直接驱动控制agc缸11的一体化容积控制方案,依据电池极片轧制成型质量设定agc缸11的压力值或位置值,控制器接收到压力/位置指令向伺服驱动器发出转速信号,伺服驱动器进而控制伺服电机7驱动双排量泵8旋转建压,双排量泵8的第一油口8.1从agc缸11的有杆腔吸油,第二油口8.2向agc缸11的无杆腔压油,agc缸能够实现压力和位置的在线实时调节,实现极片恒压力、恒辊缝的高精度轧制,轧制单双层交替涂布的极片时,单层部分也能得到比较好的轧制效果,双排量泵8内泄漏油液依次通过泄油口8.3、过滤器20和低压孔道5储存在蓄能器19中,过滤器20用于过滤系统油液的杂质,保证油液的清洁度;二位三通换向阀21用于控制高压孔道9的油液与小排量控制口8.4和大排量控制口8.5的通断,当二位三通换向阀21断电时,高压孔道9与小排量控制口8.4连通,与大排量控制口8.5断开,此时双排量泵8处于小排量工作模式,双排量泵8输出的油液量减少,agc缸11处于微量调整模式;当二位三通换向阀21通电时,高压孔道9与小排量控制口8.4断开,与大排量控制口8.5连通,此时双排量泵8处于大排量工作模式,双排量泵8输出的油液量增加,agc缸11处于快速动作模式;压力传感器25用于监测高压孔道9的压力,流量传感器用于监测输入到agc缸11的流量,位移传感器29用于监测agc缸11的缸杆位置,并实时反馈到控制器中,当高压孔道9的压力超过安全设定值时,溢流阀24通过低压孔道5将多余的油液溢流到蓄能器19中,使高压孔道9的压力稳定在安全范围内;蓄能器19作为系统的补油单元通过低压孔道5与单向阀23向系统的高压孔道9补充油液,用于补偿系统工作过程中产生的内外泄漏。
29.泵控agc液压系统还包括快换接头16和压力继电器18,快换接头16和压力继电器18均设置在低压孔道5上,并且压力继电器18与控制器相连。当压力继电器18监测到低压孔道5的压力低于最低允许值时,系统发出报警,设备停机,此时需通过快换接头16向蓄能器19补油。
30.泵控agc液压系统还包括温度传感器17;温度传感器17设置在低压孔道5上,并且温度传感器17与控制器相连。当温度传感器17监测到系统低压孔道5的油液温度过高时,系
统发出报警,设备停机,此时需让设备静置一段时间,直至油液温度冷却到允许工作范围内。
31.泵控agc液压系统还包括二位二通换向阀27、第一阻尼螺钉26、第二阻尼螺钉28;二位二通换向阀27跨接在高压孔道9与低压孔道5之间,第一阻尼螺钉26安装在二位二通换向阀27与低压孔道5之间,第二阻尼螺钉28安装在二位二通换向阀27与高压孔道9之间;控制器与二位二通换向阀27相连。当设备准备停机或遇到紧急情况需要急停卸荷时,二位二通换向阀27得电,高低压孔道5、9连通,系统卸荷,弯辊缸将上轧辊4抬升归位,第一阻尼螺钉26、第二阻尼螺钉28用于防止卸荷时产生过大的冲击振动。
32.如图3所示,本实用新型泵控agc系统的逻辑控制方法为:设备启机后先进行初始化,其次检测系统是否有卸荷与报警指令,若有卸荷指令,则触发卸荷子程序,二位二通换向阀27打开,系统卸荷,伺服电机7处于待机模式;若有报警指令,则触发开环子程序,伺服电机7处于待机模式,若无卸荷与报警指令,则系统开始温度与压力自检,当检测的温度过低时,则触发开环加热程序,直至温度达到系统正常工作温度,当检测的温度过高或检测的压力在设备正常运行范围外时,则触发开环子程序,伺服电机7处于待机模式,若系统温度、压力自检正常,则设备可以开始正常工作,系统进行控制模式的选择,当系统工作在压力控制模式时,给定压力指令,系统调用压力闭环控制子程序,控制伺服电机7的转速,使系统压力快速响应到给定压力,并使其稳定在所需精度范围内,当系统工作在位置控制模式时,给定位置指令,系统调用位置闭环控制子程序,控制伺服电机7的转速,使agc缸11的缸杆快速响应到给定位置,并使其稳定在所需精度范围内。
33.如图4所示,本实用新型泵控agc系统的压力闭环控制过程为:上位机通过总线形式将agc压力指令给定到控制器中,同时控制器接收压力传感器25反馈压力,通过实时对比两种压力,pid控制器闭环控制程序输出期望转速信号至伺服驱动器,由伺服驱动器控制伺服电机7带动双排量泵8旋转,当无杆腔压力超过给定压力时,控制器发出负转速指令,双排量泵8的第二油口8.2从无杆腔吸油减压;当无杆腔压力低于给定压力时,控制器发出正转速指令,双排量泵8的第二油口8.2向无杆腔注油增压,从而实现系统压力的高精度控制,同时系统采用压力前馈补偿控制器、流量非线性补偿控制器和泄漏补偿控制器,压力前馈补偿控制器通过对设定压力进行轨迹规划,计算伺服电机7转速补偿值;流量非线性补偿控制器通过接收压力、流量和转速信号,计算流量非线性补偿值;泄漏补偿控制器通过接收压力和流量信号,计算泄漏补偿值,所述所有补偿值与pid控制器输出转速信号共同作用在伺服驱动器内,使系统压力响应速度更快,控制精度更高。
34.如图5所示,本实用新型泵控agc系统的位置闭环控制过程为:上位机通过总线形式将agc位置指令给定到控制器中,同时控制器接收位移传感器29反馈位置,通过实时对比两种位置,pid控制器闭环控制程序输出期望转速信号至伺服驱动器,由伺服驱动器控制伺服电机7带动双排量泵8旋转,当agc缸11杠杆的实际位置大于给定位置时,控制器发出负转速指令,双排量泵8的第二油口8.2从无杆腔吸油,减小缸杆的伸出量;当agc缸11杠杆的实际位置小于给定位置时,控制器发出正转速指令,双排量泵8的第二油口8.2向无杆腔注油,增加缸杆的伸出量,从而实现缸杆位置的高精度控制,同时系统采用位置前馈补偿控制器、流量非线性补偿控制器和流量死区补偿控制器,位置前馈补偿控制器通过对设定位置进行轨迹规划,计算伺服电机7转速补偿值;流量非线性补偿控制器通过接收压力、流量和转速
信号,计算流量非线性补偿值;流量死区补偿控制器通过接收压力、流量和转速信号,计算流量死区补偿值,所述所有补偿值与pid控制器输出转速信号共同作用在伺服驱动器内,使系统位置响应速度更快,控制精度更高。
再多了解一些
本文用于企业家、创业者技术爱好者查询,结果仅供参考。