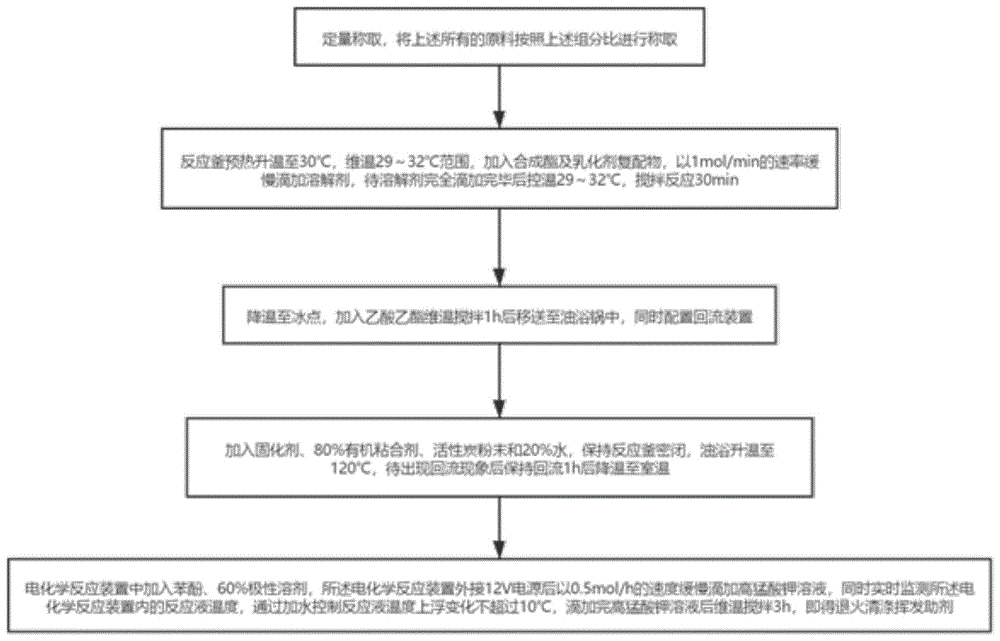
本发明涉及铝合金制油助剂的技术领域,尤其涉及一种铝合金带轧制油用退火清涤挥发助剂生产制备方法。
背景技术:
铝合金板带作为重要的有色金属加工材料,在金属带材中的用量仅低于钢铁。在铝合金轧制过程中,一般是将热轧生产的粗轧铝合金板经过若干道次的冷轧加工,压成更小厚度的铝合金薄板,直至小于0.2mm的铝箔。随着中国经济持续发展和工业转型升级,市场对铝合金板带产品的质量要求日益提高,铝合金板带加工过程中的工艺润滑作用对企业的生产效率、设备损耗以及板材产品质量起着关键的作用,越来越受到重视。
铝合金板带轧制油液主要分为热轧乳化液和冷轧轧制油,在热轧时,一般采用水包油型(o/w)乳化油进行冷却和润滑,冷轧轧制油一般是纯油性。具体到冷轧轧制油,良好的冷轧轧制油需具备无毒、低气味、低粘度、高闪点、低终馏点、窄馏分、黏温性能好、退火时不产生油斑、氧化安定性及表面光洁度良好等要求。原先在轧制油中,通常基础油占94%-95%左右,随着环保意识及冷轧技术的加强,铝合金板带冷轧向大压下量、低油耗、高速和高表面质量方向发展,对铝合金冷轧轧制油的挥发性能和退火清净性能有了更严格的要求。
现有铝合金带轧制油用退火清涤挥发助剂的挥发性能和退火清净性能不足,考虑到未来铝合金板带将向高性能的中厚板和更精密的铝箔方向发展,产品需要有更好的制成品表面质量,铝合金冷轧轧制油需要有更适宜的黏度、更低的芳烃和硫含量、更窄的馏分、更高的闪点和更低的油耗,研究一种新式铝合金带轧制油用退火清涤挥发助剂具有重要意义。
技术实现要素:
本部分的目的在于概述本发明的实施例的一些方面以及简要介绍一些较佳实施例。在本部分以及本申请的说明书摘要和发明名称中可能会做些简化或省略以避免使本部分、说明书摘要和发明名称的目的模糊,而这种简化或省略不能用于限制本发明的范围。
鉴于上述现有铝合金带轧制油用退火清涤挥发助剂存在的问题,提出了本发明。
因此,本发明解决的技术问题是:解决现有铝合金带轧制油用退火清涤挥发助剂挥发性能和退火清净性能不足的问题。
为解决上述技术问题,本发明提供如下技术方案:一种铝合金带轧制油用退火清涤挥发助剂生产制备方法,由下列重量份的原料组成:合成酯10~15份、乳化剂复配物5~7份、溶解剂1~2份、乙酸乙酯10~15份、固化剂5~7份、有机粘合剂3~5份、活性炭粉末5~10份、苯酚10~13份、浓度0.1mol/l的高猛酸钾溶液15~20份、极性溶剂5~8份,其余为纯水;
依据上述原料的制备方法为:
s1:定量称取,将上述所有的原料按照上述组分比进行称取;
s2:反应釜预热升温至30℃,维温29~32℃范围,加入合成酯及乳化剂复配物,以1mol/min的速率缓慢滴加溶解剂,待溶解剂完全滴加完毕后控温29~32℃,搅拌反应30min;
s3:降温至冰点,加入乙酸乙酯维温搅拌1h后移送至油浴锅中,同时配置回流装置;
s4:加入固化剂、80%有机粘合剂、活性炭粉末和20%水,保持反应釜密闭,油浴升温至120℃,待出现回流现象后保持回流1h后降温至室温;
s5:电化学反应装置中加入苯酚、60%极性溶剂,所述电化学反应装置外接12v电源后以0.5mol/h的速度缓慢滴加高猛酸钾溶液,同时实时监测所述电化学反应装置内的反应液温度,通过加水控制反应液温度上浮变化不超过10℃,滴加完高猛酸钾溶液后维温搅拌3h,即得退火清涤挥发助剂。
作为本发明所述的铝合金带轧制油用退火清涤挥发助剂生产制备方法的一种优选方案,其中:所述合成酯包括异构葵酸与异构辛酸以1:1.4或1:1.5或1:1.8进行复配混合。
作为本发明所述的铝合金带轧制油用退火清涤挥发助剂生产制备方法的一种优选方案,其中:所述乳化剂复配物包括聚乙二醇型非离子表面活性剂和阴离子表面活性剂以1:2进行复配混合。
作为本发明所述的铝合金带轧制油用退火清涤挥发助剂生产制备方法的一种优选方案,其中:所述非离子表面活性剂为由含有羟基的蓖麻油与环氧乙烷加成形成的聚氧乙烯酰胺,所述阴离子表面活性剂为十二烷基硫酸铵。
作为本发明所述的铝合金带轧制油用退火清涤挥发助剂生产制备方法的一种优选方案,其中:所述溶解剂为甲酸、乙腈、丙酮或丁酮中的一种或任意两种以1:1.5混合的混合物。
作为本发明所述的铝合金带轧制油用退火清涤挥发助剂生产制备方法的一种优选方案,其中:所述固化剂为山梨酸酯、山梨酰胺、硅酸钠和氟硼酸锌中的任意一种。
作为本发明所述的铝合金带轧制油用退火清涤挥发助剂生产制备方法的一种优选方案,其中:所述有机粘合剂包括10~35wt%有机树脂和65~90wt%有机溶剂。
作为本发明所述的铝合金带轧制油用退火清涤挥发助剂生产制备方法的一种优选方案,其中:所述有机树脂包括丙烯酸树脂、环氧丙烯酸树脂、达玛树脂中的一种或多种;所述有机溶剂包括松节油、pma、脱芳烃溶剂油、己二酸二甲酯中的两种或两种以上组合混合物。
作为本发明所述的铝合金带轧制油用退火清涤挥发助剂生产制备方法的一种优选方案,其中:所述极性溶剂为dpg、pg、dpma中的一种或几种的混合物。
作为本发明所述的铝合金带轧制油用退火清涤挥发助剂生产制备方法的一种优选方案,其中:还包括热熔性高温颗粒剂20~25份、成膜剂1~2份,反应釜中加入热熔性高温颗粒剂、成膜剂及20%有机粘合剂,在200℃下热熔后降至室温,加入所述退火清涤挥发助剂和40%极性溶剂,制作成分散目为确定目标目的分散网囊进行使用。
本发明的有益效果:本发明提供一种铝合金带轧制油用退火清涤挥发助剂生产制备方法,通过提供的原料和具体的工艺进行制备,其中,通过回流装置及电化学反应装置的引入进行挥发助剂的性能提升,从化合物本质上提高了挥发助剂的挥发性能,同时,电化学从苯酚中电离出羟基离子,在退火的过程中还可以综合其他反应剂进一步去除掉铝合金板带中的s元素,提升板材表面性能,本发明中同样给出一种使用该挥发助剂的方式,通过高温材料为主体制作网囊,将挥发助剂附着到网囊上,提升在油剂合成中的控制度及性能度。
附图说明
为了更清楚地说明本发明实施例的技术方案,下面将对实施例描述中所需要使用的附图作简单地介绍,显而易见地,下面描述中的附图仅仅是本发明的一些实施例,对于本领域普通技术人员来讲,在不付出创造性劳动性的前提下,还可以根据这些附图获得其它的附图。其中:
图1为本发明提供的制备方法流程图。
图2为本发明提供的网囊的大致生成图。
图3为本发明提供的网囊的局部方法图。
具体实施方式
为使本发明的上述目的、特征和优点能够更加明显易懂,下面结合说明书附图对本发明的具体实施方式做详细的说明,显然所描述的实施例是本发明的一部分实施例,而不是全部实施例。基于本发明中的实施例,本领域普通人员在没有做出创造性劳动前提下所获得的所有其他实施例,都应当属于本发明的保护的范围。
现有铝合金带轧制油用退火清涤挥发助剂的挥发性能和退火清净性能不足。
故此,本发明提供一种铝合金带轧制油用退火清涤挥发助剂生产制备方法,如下实施例。
实施例:
实施例1
一种铝合金带轧制油用退火清涤挥发助剂生产制备方法,由下列重量份的原料组成:合成酯10份、乳化剂复配物5份、溶解剂1份、乙酸乙酯10份、固化剂5份、有机粘合剂3份、活性炭粉末5份、苯酚10份、浓度0.1mol/l的高猛酸钾溶液15份、极性溶剂5份,其余为纯水;
依据上述原料的制备方法为:
s1:定量称取,将上述所有的原料按照上述组分比进行称取;
s2:反应釜预热升温至30℃,维温29~32℃范围,加入合成酯及乳化剂复配物,以1mol/min的速率缓慢滴加溶解剂,待溶解剂完全滴加完毕后控温29~32℃,搅拌反应30min;
s3:降温至冰点,加入乙酸乙酯维温搅拌1h后移送至油浴锅中,同时配置回流装置;
s4:加入固化剂、80%有机粘合剂、活性炭粉末和20%水,保持反应釜密闭,油浴升温至120℃,待出现回流现象后保持回流1h后降温至室温;
s5:电化学反应装置中加入苯酚、60%极性溶剂,电化学反应装置外接12v电源后以0.5mol/h的速度缓慢滴加高猛酸钾溶液,同时实时监测电化学反应装置内的反应液温度,通过加水控制反应液温度上浮变化不超过10℃,滴加完高猛酸钾溶液后维温搅拌3h,即得退火清涤挥发助剂。
其中,合成酯包括异构葵酸与异构辛酸以1:1.4进行复配混合。
其中,乳化剂复配物包括聚乙二醇型非离子表面活性剂和阴离子表面活性剂以1:2进行复配混合。非离子表面活性剂为由含有羟基的蓖麻油与环氧乙烷加成形成的聚氧乙烯酰胺,阴离子表面活性剂为十二烷基硫酸铵。
其中,溶解剂为甲酸、乙腈、丙酮或丁酮中的一种或任意两种以1:1.5混合的混合物。
其中,固化剂为山梨酸酯。
进一步的,有机粘合剂包括10~35wt%有机树脂和65~90wt%有机溶剂。有机树脂包括丙烯酸树脂、环氧丙烯酸树脂、达玛树脂中的一种或多种;有机溶剂包括松节油、pma、脱芳烃溶剂油、己二酸二甲酯中的两种或两种以上组合混合物。
其中,极性溶剂为dpg、pg、dpma中的一种或几种的混合物。
更进一步的,还包括热熔性高温颗粒剂20份、成膜剂1份,反应釜中加入热熔性高温颗粒剂、成膜剂及20%有机粘合剂,在200℃下热熔后降至室温,加入退火清涤挥发助剂和40%极性溶剂,制作成分散目为确定目标目的分散网囊进行使用。
实施例2
一种铝合金带轧制油用退火清涤挥发助剂生产制备方法,由下列重量份的原料组成:合成酯15份、乳化剂复配物7份、溶解剂2份、乙酸乙酯15份、固化剂7份、有机粘合剂5份、活性炭粉末10份、苯酚13份、浓度0.1mol/l的高猛酸钾溶液20份、极性溶剂8份,其余为纯水;
依据上述原料的制备方法为:
s1:定量称取,将上述所有的原料按照上述组分比进行称取;
s2:反应釜预热升温至30℃,维温29~32℃范围,加入合成酯及乳化剂复配物,以1mol/min的速率缓慢滴加溶解剂,待溶解剂完全滴加完毕后控温29~32℃,搅拌反应30min;
s3:降温至冰点,加入乙酸乙酯维温搅拌1h后移送至油浴锅中,同时配置回流装置;
s4:加入固化剂、80%有机粘合剂、活性炭粉末和20%水,保持反应釜密闭,油浴升温至120℃,待出现回流现象后保持回流1h后降温至室温;
s5:电化学反应装置中加入苯酚、60%极性溶剂,电化学反应装置外接12v电源后以0.5mol/h的速度缓慢滴加高猛酸钾溶液,同时实时监测电化学反应装置内的反应液温度,通过加水控制反应液温度上浮变化不超过10℃,滴加完高猛酸钾溶液后维温搅拌3h,即得退火清涤挥发助剂。
其中,合成酯包括异构葵酸与异构辛酸以1:1.5进行复配混合。
其中,乳化剂复配物包括聚乙二醇型非离子表面活性剂和阴离子表面活性剂以1:2进行复配混合。非离子表面活性剂为由含有羟基的蓖麻油与环氧乙烷加成形成的聚氧乙烯酰胺,阴离子表面活性剂为十二烷基硫酸铵。
其中,溶解剂为甲酸、乙腈、丙酮或丁酮中的一种或任意两种以1:1.5混合的混合物。
其中,固化剂为山梨酰胺。
其中,有机粘合剂包括10~35wt%有机树脂和65~90wt%有机溶剂。有机树脂包括丙烯酸树脂、环氧丙烯酸树脂、达玛树脂中的一种或多种;有机溶剂包括松节油、pma、脱芳烃溶剂油、己二酸二甲酯中的两种或两种以上组合混合物。
进一步的,极性溶剂为dpg、pg、dpma中的一种或几种的混合物。
更进一步的,还包括热熔性高温颗粒剂25份、成膜剂2份,反应釜中加入热熔性高温颗粒剂、成膜剂及20%有机粘合剂,在200℃下热熔后降至室温,加入退火清涤挥发助剂和40%极性溶剂,制作成分散目为确定目标目的分散网囊进行使用。
实施例3
一种铝合金带轧制油用退火清涤挥发助剂生产制备方法,由下列重量份的原料组成:合成酯13份、乳化剂复配物6份、溶解剂1.5份、乙酸乙酯13份、固化剂6份、有机粘合剂4份、活性炭粉末8份、苯酚12份、浓度0.1mol/l的高猛酸钾溶液18份、极性溶剂7份,其余为纯水;
依据上述原料的制备方法为:
s1:定量称取,将上述所有的原料按照上述组分比进行称取;
s2:反应釜预热升温至30℃,维温29~32℃范围,加入合成酯及乳化剂复配物,以1mol/min的速率缓慢滴加溶解剂,待溶解剂完全滴加完毕后控温29~32℃,搅拌反应30min;
s3:降温至冰点,加入乙酸乙酯维温搅拌1h后移送至油浴锅中,同时配置回流装置;
s4:加入固化剂、80%有机粘合剂、活性炭粉末和20%水,保持反应釜密闭,油浴升温至120℃,待出现回流现象后保持回流1h后降温至室温;
s5:电化学反应装置中加入苯酚、60%极性溶剂,电化学反应装置外接12v电源后以0.5mol/h的速度缓慢滴加高猛酸钾溶液,同时实时监测电化学反应装置内的反应液温度,通过加水控制反应液温度上浮变化不超过10℃,滴加完高猛酸钾溶液后维温搅拌3h,即得退火清涤挥发助剂。
其中,合成酯包括异构葵酸与异构辛酸以1:1.8进行复配混合。
其中,乳化剂复配物包括聚乙二醇型非离子表面活性剂和阴离子表面活性剂以1:2进行复配混合。非离子表面活性剂为由含有羟基的蓖麻油与环氧乙烷加成形成的聚氧乙烯酰胺,阴离子表面活性剂为十二烷基硫酸铵。
其中,溶解剂为甲酸、乙腈、丙酮或丁酮中的一种或任意两种以1:1.5混合的混合物。
其中,固化剂为硅酸钠。
其中,有机粘合剂包括10~35wt%有机树脂和65~90wt%有机溶剂。有机树脂包括丙烯酸树脂、环氧丙烯酸树脂、达玛树脂中的一种或多种;有机溶剂包括松节油、pma、脱芳烃溶剂油、己二酸二甲酯中的两种或两种以上组合混合物。
进一步的,极性溶剂为dpg、pg、dpma中的一种或几种的混合物。
更进一步的,还包括热熔性高温颗粒剂23份、成膜剂1.5份,反应釜中加入热熔性高温颗粒剂、成膜剂及20%有机粘合剂,在200℃下热熔后降至室温,加入退火清涤挥发助剂和40%极性溶剂,制作成分散目为确定目标目的分散网囊进行使用。
实施例4
一种铝合金带轧制油用退火清涤挥发助剂生产制备方法,由下列重量份的原料组成:合成酯14份、乳化剂复配物5.5份、溶解剂1.8份、乙酸乙酯12份、固化剂5.8份、有机粘合剂4.2份、活性炭粉末6份、苯酚11份、浓度0.1mol/l的高猛酸钾溶液19份、极性溶剂6份,其余为纯水;
依据上述原料的制备方法为:
s1:定量称取,将上述所有的原料按照上述组分比进行称取;
s2:反应釜预热升温至30℃,维温29~32℃范围,加入合成酯及乳化剂复配物,以1mol/min的速率缓慢滴加溶解剂,待溶解剂完全滴加完毕后控温29~32℃,搅拌反应30min;
s3:降温至冰点,加入乙酸乙酯维温搅拌1h后移送至油浴锅中,同时配置回流装置;
s4:加入固化剂、80%有机粘合剂、活性炭粉末和20%水,保持反应釜密闭,油浴升温至120℃,待出现回流现象后保持回流1h后降温至室温;
s5:电化学反应装置中加入苯酚、60%极性溶剂,电化学反应装置外接12v电源后以0.5mol/h的速度缓慢滴加高猛酸钾溶液,同时实时监测电化学反应装置内的反应液温度,通过加水控制反应液温度上浮变化不超过10℃,滴加完高猛酸钾溶液后维温搅拌3h,即得退火清涤挥发助剂。
其中,合成酯包括异构葵酸与异构辛酸以1:1.4进行复配混合。
其中,乳化剂复配物包括聚乙二醇型非离子表面活性剂和阴离子表面活性剂以1:2进行复配混合。非离子表面活性剂为由含有羟基的蓖麻油与环氧乙烷加成形成的聚氧乙烯酰胺,阴离子表面活性剂为十二烷基硫酸铵。
其中,溶解剂为甲酸、乙腈、丙酮或丁酮中的一种或任意两种以1:1.5混合的混合物。
其中,固化剂为氟硼酸锌。
其中,有机粘合剂包括10~35wt%有机树脂和65~90wt%有机溶剂。有机树脂包括丙烯酸树脂、环氧丙烯酸树脂、达玛树脂中的一种或多种;有机溶剂包括松节油、pma、脱芳烃溶剂油、己二酸二甲酯中的两种或两种以上组合混合物。
进一步的,极性溶剂为dpg、pg、dpma中的一种或几种的混合物。
更进一步的,还包括热熔性高温颗粒剂21份、成膜剂1.8份,反应釜中加入热熔性高温颗粒剂、成膜剂及20%有机粘合剂,在200℃下热熔后降至室温,加入退火清涤挥发助剂和40%极性溶剂,制作成分散目为确定目标目的分散网囊进行使用。
实施例5
一种铝合金带轧制油用退火清涤挥发助剂生产制备方法,由下列重量份的原料组成:合成酯11份、乳化剂复配物5.2份、溶解剂1.2份、乙酸乙酯12份、固化剂6.5份、有机粘合剂3.5份、活性炭粉末9份、苯酚11份、浓度0.1mol/l的高猛酸钾溶液18份、极性溶剂7份,其余为纯水;
依据上述原料的制备方法为:
s1:定量称取,将上述所有的原料按照上述组分比进行称取;
s2:反应釜预热升温至30℃,维温29~32℃范围,加入合成酯及乳化剂复配物,以1mol/min的速率缓慢滴加溶解剂,待溶解剂完全滴加完毕后控温29~32℃,搅拌反应30min;
s3:降温至冰点,加入乙酸乙酯维温搅拌1h后移送至油浴锅中,同时配置回流装置;
s4:加入固化剂、80%有机粘合剂、活性炭粉末和20%水,保持反应釜密闭,油浴升温至120℃,待出现回流现象后保持回流1h后降温至室温;
s5:电化学反应装置中加入苯酚、60%极性溶剂,电化学反应装置外接12v电源后以0.5mol/h的速度缓慢滴加高猛酸钾溶液,同时实时监测电化学反应装置内的反应液温度,通过加水控制反应液温度上浮变化不超过10℃,滴加完高猛酸钾溶液后维温搅拌3h,即得退火清涤挥发助剂。
其中,合成酯包括异构葵酸与异构辛酸以1:1.8进行复配混合。
其中,乳化剂复配物包括聚乙二醇型非离子表面活性剂和阴离子表面活性剂以1:2进行复配混合。非离子表面活性剂为由含有羟基的蓖麻油与环氧乙烷加成形成的聚氧乙烯酰胺,阴离子表面活性剂为十二烷基硫酸铵。
其中,溶解剂为甲酸、乙腈、丙酮或丁酮中的一种或任意两种以1:1.5混合的混合物。
其中,固化剂为山梨酸酯。
其中,有机粘合剂包括10~35wt%有机树脂和65~90wt%有机溶剂。有机树脂包括丙烯酸树脂、环氧丙烯酸树脂、达玛树脂中的一种或多种;有机溶剂包括松节油、pma、脱芳烃溶剂油、己二酸二甲酯中的两种或两种以上组合混合物。
进一步的,极性溶剂为dpg、pg、dpma中的一种或几种的混合物。
更进一步的,还包括热熔性高温颗粒剂23份、成膜剂1.7份,反应釜中加入热熔性高温颗粒剂、成膜剂及20%有机粘合剂,在200℃下热熔后降至室温,加入所述退火清涤挥发助剂和40%极性溶剂,制作成分散目为确定目标目的分散网囊进行使用。
实施例6
一种铝合金带轧制油用退火清涤挥发助剂生产制备方法,由下列重量份的原料组成:合成酯14份、乳化剂复配物6.2份、溶解剂1.3份、乙酸乙酯15份、固化剂7份、有机粘合剂3份、活性炭粉末6份、苯酚12份、浓度0.1mol/l的高猛酸钾溶液17份、极性溶剂5份,其余为纯水;
依据上述原料的制备方法为:
s1:定量称取,将上述所有的原料按照上述组分比进行称取;
s2:反应釜预热升温至30℃,维温29~32℃范围,加入合成酯及乳化剂复配物,以1mol/min的速率缓慢滴加溶解剂,待溶解剂完全滴加完毕后控温29~32℃,搅拌反应30min;
s3:降温至冰点,加入乙酸乙酯维温搅拌1h后移送至油浴锅中,同时配置回流装置;
s4:加入固化剂、80%有机粘合剂、活性炭粉末和20%水,保持反应釜密闭,油浴升温至120℃,待出现回流现象后保持回流1h后降温至室温;
s5:电化学反应装置中加入苯酚、60%极性溶剂,电化学反应装置外接12v电源后以0.5mol/h的速度缓慢滴加高猛酸钾溶液,同时实时监测电化学反应装置内的反应液温度,通过加水控制反应液温度上浮变化不超过10℃,滴加完高猛酸钾溶液后维温搅拌3h,即得退火清涤挥发助剂。
合成酯包括异构葵酸与异构辛酸以1:1.8进行复配混合。
乳化剂复配物包括聚乙二醇型非离子表面活性剂和阴离子表面活性剂以1:2进行复配混合。非离子表面活性剂为由含有羟基的蓖麻油与环氧乙烷加成形成的聚氧乙烯酰胺,阴离子表面活性剂为十二烷基硫酸铵。
溶解剂为甲酸、乙腈、丙酮或丁酮中的一种或任意两种以1:1.5混合的混合物。
固化剂为硅酸钠。
有机粘合剂包括10~35wt%有机树脂和65~90wt%有机溶剂。有机树脂包括丙烯酸树脂、环氧丙烯酸树脂、达玛树脂中的一种或多种;有机溶剂包括松节油、pma、脱芳烃溶剂油、己二酸二甲酯中的两种或两种以上组合混合物。
极性溶剂为dpg、pg、dpma中的一种或几种的混合物。
还包括热熔性高温颗粒剂22份、成膜剂1份,反应釜中加入热熔性高温颗粒剂、成膜剂及20%有机粘合剂,在200℃下热熔后降至室温,加入退火清涤挥发助剂和40%极性溶剂,制作成分散目为确定目标目的分散网囊进行使用。
对比例:
本发明在对比例中选用一种制备轧制油的方法,如下:以重量份数计,由以下组分组成:
油性剂:牛油20份、三羟甲基丙烷油酸酯5份;
腐蚀抑制剂:石油磺酸钠5份、脂肪酸酰胺1份、环烷酸钠4份;
乳化剂:辛基酚聚氧乙烯醚1份、脂肪醇聚氧乙烯醚羧酸1.5份;
调整剂:2-(氨基乙氧基)乙醇1.5份、二环己胺1.5份;
极压抗磨剂:sln-1112份
消泡剂:有机硅氧烷共聚物消泡剂0.1份;
基础油:精制矿物油57.4份;
额外加入挥发助剂:如上述实施例1~6,对比样中选用加入现有常见的挥发助剂及不加挥发助剂;
制备:将精制矿物油加入至带有搅拌的反应釜中,升温至40℃,开启搅拌,将油性剂、腐蚀抑制剂、乳化剂、调整剂、极压抗磨剂、消泡剂依次加入,保持恒温搅拌90分钟,至澄清透明,冷却至室温,配置成轧制油。
将上述轧制油用于同一款铝合金板带的制作中,试验结果如下表1所示:
表1:对比例中不同情况的性能表
其中,挥发效率=每分钟耗油/总耗油;由上表可知,本发明在退火清涤总时间及挥发效率上远胜于现有技术的挥发助剂,对成型的板材的表面平滑度也由于化合物官能团的附带祛除了硫元素变得更为平整,油耗上只体现在耗油速率较快,但是由于挥发反应更为迅速,总体的耗油量反而有所下降。
本发明还额外提供一种使用该挥发剂的方法:反应釜中加入热熔性高温颗粒剂、成膜剂及20%有机粘合剂,在200℃下热熔后降至室温,加入退火清涤挥发助剂和40%极性溶剂,制作成分散目为确定目标目的分散网囊进行使用。
通过以下方法进行在油剂合成中的控制度及性能度,如下表2所示:
表2:试剂使用规则表
同步表1中的轧制油制作工艺,当需要控制挥发效率时,采用上述表2中的具体参数在制备完成挥发助剂后进行使用。
本发明提供一种铝合金带轧制油用退火清涤挥发助剂生产制备方法,通过提供的原料和具体的工艺进行制备,其中,通过回流装置及电化学反应装置的引入进行挥发助剂的性能提升,从化合物本质上提高了挥发助剂的挥发性能,同时,电化学从苯酚中电离出羟基离子,在退火的过程中还可以综合其他反应剂进一步去除掉铝合金板带中的s元素,提升板材表面性能,本发明中同样给出一种使用该挥发助剂的方式,通过高温材料为主体制作网囊,将挥发助剂附着到网囊上,提升在油剂合成中的控制度及性能度。
应说明的是,以上实施例仅用以说明本发明的技术方案而非限制,尽管参照较佳实施例对本发明进行了详细说明,本领域的普通技术人员应当理解,可以对本发明的技术方案进行修改或者等同替换,而不脱离本发明技术方案的精神和范围,其均应涵盖在本发明的权利要求范围当中。
本文用于企业家、创业者技术爱好者查询,结果仅供参考。