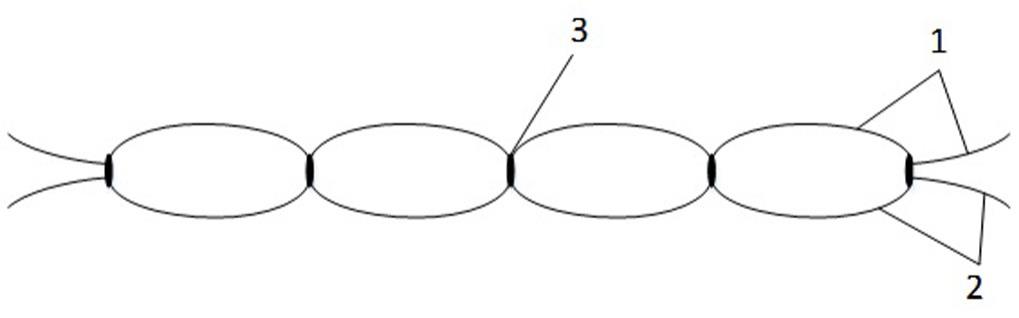
1.本发明涉及纺织技术领域,主要涉及一种长绒棉石墨烯锦纶包双芯混纺纱线及其制备方法。
背景技术:
2.牛仔服装自20世纪六七十年代才开始在我国流行,而牛仔布始终伴随着牛仔服装的发展而发展,牛仔布的发展至今也有上百年历史,牛仔布经历了百年风雨的洗礼后,长盛不衰,且市场越来越大,因为牛仔面料与服装老少皆宜穿著,有很强的通用性,所以它长期成为国内外服装消费者所青睐的时装之一,提到牛仔给人们的感觉就是两个概念“耐磨”、“难洗”。
3.现如今的牛仔布,为了增加穿着的舒适性,通常会以氨纶包芯纱作为纬纱织入牛仔布,这种纱线制作出来的牛仔面料穿着在身上时伸缩自如,并且舒适比较合体。但氨纶包芯纱的强力相对较低,反复拉伸之后容易断裂失去弹性,降低牛仔面料穿着舒适度,且其耐磨性能也不如无弹力牛仔面料。与其它类型的弹力纱线相比,包芯纱的强力相对较低。一般情况下,包芯纱强力只相当于同规的外包纤维单独成纱时的80%~90%。包芯纱首先断裂的是外包纤维,外包纤维所形成的强力即包芯纱的强力。氨纶丝是一根低强高伸的长丝,氨纶丝在包芯纱内无助于纱线的强力。
4.因此,现有技术还有待于改进和发展。
技术实现要素:
5.鉴于上述现有技术的不足,本发明的目的在于提供一种长绒棉石墨烯锦纶包双芯混纺纱线及其制备方法,旨在解决用于弹力牛仔布的现有氨纶包芯纱的强度有待提升的问题。
6.本发明的技术方案如下:一种长绒棉石墨烯锦纶包双芯混纺纱线的制备方法,其中,包括以下步骤:原料选配:按照重量百分比计,选择石墨烯锦纶30
‑
50%、长绒棉50%
‑
70%;清梳联:将部分长绒棉经过清梳联制成棉网,再用棉网包裹石墨烯锦纶经过清梳联制成第一生条;将剩余长绒棉经过清梳联制成第二生条;并条;粗纱;细纱:以涤纶长丝与氨纶丝作为芯纱,以长绒棉石墨烯锦纶的混纺粗纱为外包纱,经细纱工序制成长绒棉石墨烯锦纶包双芯混纺纱线;络筒。
7.所述的长绒棉石墨烯锦纶包双芯混纺纱线的制备方法,其中,所述用棉网包裹石墨烯锦纶经过清梳联制成第一生条的过程中,清花打手的速度为750
‑
810 r/min,清梳的湿度控制在70%
‑
75%左右,清梳的梳理的速度范围380
‑
410 r/min,清梳的梳理隔距范围是四
点隔离11、10、10、9,控制道夫和剥棉罗拉的张力在1.04
‑
1.09。
8.所述的长绒棉石墨烯锦纶包双芯混纺纱线的制备方法,其中,所述用棉网包裹石墨烯锦纶经过清梳联制成第一生条的过程中,取消清梳的落杂点。
9.所述的长绒棉石墨烯锦纶包双芯混纺纱线的制备方法,其中,所述清梳联工序中,部分长绒棉的用量占所有长绒棉重量的25
‑
35%,剩余长绒棉占所有长绒棉重量的65
‑
75%。
10.所述的长绒棉石墨烯锦纶包双芯混纺纱线的制备方法,其中,所述并条工序中,采用三道并合,罗拉的中心距为(40~42)*(44~48)mm;所述三道并合的过程,包括以下步骤:预并:将对第一生条进行预并合得到预并条,采用1.5
‑
1.7倍的后区牵伸工艺;混一并:采用5根第一生条的预并条与2根第二生条一起并合;末并:将混一并出来的条子再次并合。
11.所述的长绒棉石墨烯锦纶包双芯混纺纱线的制备方法,其中,所述粗纱工序中,捻系数为90
‑
95,后区隔距为60
‑
66 mm,后区牵伸倍数1.2
‑
1.25倍,粗纱的定量为7.0~8.5克/10米。
12.所述的长绒棉石墨烯锦纶包双芯混纺纱线的制备方法,其中,所述细纱工序中,钳口隔距3.5mm,皮辊选用邵氏硬度70度的胶辊,后区隔距38~42mm,后区牵伸倍数1.15
‑
1.22倍。
13.所述的长绒棉石墨烯锦纶包双芯混纺纱线的制备方法,其中,在细纱工序前,对涤纶长丝与氨纶丝进行预处理,所述预处理过程包括以下步骤:根据成纱的弹性要求,先把氨纶丝1牵伸到所需的牵伸倍数,再与涤纶长丝并在一起经过5~7公斤高压空气加上网点,使涤纶长丝和氨纶丝锁紧在一起。
14.所述的长绒棉石墨烯锦纶包双芯混纺纱线的制备方法,其中,所述络筒工序中,采用水雾捻或者机械搓捻的接头形式,络筒速度900
‑
1100m/min;在络筒工序后还包括以下步骤:蒸纱定型:经过70
‑
90℃,15
‑
25分钟的高温定型。
15.一种长绒棉石墨烯锦纶包双芯混纺纱线,其中,包括外包纱和芯纱;外包纱按照重量百分比计,由石墨烯锦纶30
‑
50%、长绒棉50%
‑
70%组成;芯纱由涤纶长丝和氨纶丝组成,采用如上所述的长绒棉石墨烯锦纶包双芯混纺纱线的制备方法制备得到。
16.有益效果:本发明中,为了提高氨纶包芯纱的强力和耐磨性能,同时保证纱线的舒适度,在本发明技术方案中选用长绒棉、石墨烯锦纶的组合作为外包纱,这样可以集长绒棉的高单纤维强力与石墨烯锦纶的高强一起,使生产出来的纱线强度极高,能很好的满足牛仔面料用纱高强的需求。
附图说明
17.图1为本发明中对涤纶长丝与氨纶丝进行预处理后的结构示意图。
18.标号说明:1、氨纶丝;2、涤纶长丝;3、网点。
具体实施方式
19.本发明提供一种长绒棉石墨烯锦纶包双芯混纺纱线及其制备方法,为使本发明的
目的、技术方案及效果更加清楚、明确,以下对本发明进一步详细说明。应当理解,此处所描述的具体实施例仅仅用以解释本发明,并不用于限定本发明。
20.在本发明中,除非另有明确的规定和限定,第一特征在第二特征之“上”或之“下”可以包括第一和第二特征直接接触,也可以包括第一和第二特征不是直接接触而是通过它们之间的另外的特征接触。而且,第一特征在第二特征“之上”、“上方”和“上面”包括第一特征在第二特征正上方和斜上方,或仅仅表示第一特征水平高度高于第二特征。第一特征在第二特征“之下”、“下方”和“下面”包括第一特征在第二特征正下方和斜下方,或仅仅表示第一特征水平高度小于第二特征。
21.下文的公开提供了许多不同的实施方式或例子用来实现本发明的不同结构。为了简化本发明的公开,下文中对特定例子的部件和设置进行描述。当然,它们仅仅为示例,并且目的不在于限制本发明。此外,本发明可以在不同例子中重复参考数字和/或参考字母,这种重复是为了简化和清楚的目的,其本身不指示所讨论各种实施方式和/或设置之间的关系。此外,本发明提供了的各种特定的工艺和材料的例子,但是本领域普通技术人员可以意识到其他工艺的应用和/或其他材料的使用。
22.为了提高氨纶包芯纱的强力和耐磨性能,同时保证纱线的舒适度,在本发明技术方案中选用长绒棉、石墨烯锦纶的组合作为外包纱,这样可以集长绒棉的高单纤维强力与石墨烯锦纶的高强一起,使生产出来的纱线强度极高,能很好的满足牛仔面料用纱高强的需求。而且,采用石墨烯锦纶,不仅可以利用锦纶纤维的高强力高耐磨的特性,还可以使纱线具有石墨烯的抗菌性能。采用长绒棉结合吸湿性较好的锦纶,还能提高包芯纱吸湿性能,还可以解决牛仔面料厚重带来的闷湿,进一步提高牛仔面料的穿着舒适度。
23.但是,由于单一的石墨烯锦纶韧性很大在纺过程中很容易产生静电,很难单独生产,因此,采用传统的包芯纱制备工艺并不能顺利生产。在本发明方案中除了利用长绒棉的高强力以外,更重要的是将长绒棉与石墨烯锦纶组合使其能顺利用于纱线生产中。本发明技术方案中,针对长绒棉与石墨烯锦纶组合,还提供了一种长绒棉石墨烯锦纶包双芯混纺纱线的制备方法,通过对纺纱工艺的改进使得纱线能顺利生产。
24.具体地,长绒棉石墨烯锦纶包双芯混纺纱线的制备方法,包括以下步骤:(1)原料选配:按照重量百分比计,选择石墨烯锦纶30
‑
50%、长绒棉50%
‑
70%。
25.(2)清梳联:将部分长绒棉经过清梳联制成棉网,再用棉网包裹石墨烯锦纶经过清梳联制成第一生条;将剩余长绒棉经过清梳联制成第二生条。
26.其中,部分长绒棉的用量占所有长绒棉重量的25
‑
35%,剩余长绒棉占所有长绒棉重量的65
‑
75%。
27.由于单一的石墨烯锦纶韧性很大,单一的纤维梳理的难度有点大,纤维之间很容易纠接在一起梳理不开,很难单独生产,另外石墨烯锦纶价格昂贵,因此,在本发明中先采用部分长绒棉梳理成棉网,再与石墨烯锦纶混合后再进行清梳联,一是可以保证石墨烯锦纶能顺利生产,二是可以使石墨烯锦纶与长绒棉均匀混合,保证最终成品强度均匀,三是用棉网包裹石墨烯锦纶可以大大减少石墨烯锦纶的损耗,降低生产成本,四是制成第一生条的清梳工序中可以把落杂点取消进一步降低生产成本。
28.在本发明实施例方案中,为了使石墨烯锦纶能顺利生产,对所述用棉网包裹石墨烯锦纶经过清梳联制成第一生条的过程进行了优化改进,具体如下:
由于石墨烯锦纶与长绒棉的纤维长度都比较长,清梳工艺采用的原则为柔性梳理,不能过度分梳造成纤维梳断的情况。清花打手的速度比单一的纺棉要低10%左右,现有纺棉的清花打手的速度为870r/min,而本发明方案中清花打手的速度为750
‑
810 r/min。
29.由于石墨烯绵纶的回潮率比较低,且,石墨烯锦纶很膨松,在纺过程中很容易产生静电,为了消除静电使生产顺利进行,清梳联过程中的湿度要比一般情况下纺棉的湿度高20%左右,清梳的湿度控制在70%
‑
75%左右。如果空调系统没办法满足高湿度要求的情况下,可以采用喷雾加湿的办法,保证湿度满足生产要求。
30.因为石墨烯锦纶是化纤,且部分长绒棉已经经过一次清梳联处理,因此,石墨烯锦纶和处理过的长绒棉含杂量很少,长度整齐度很好,若梳理速度过高会造成纤维梳断,降低纱线强力。为了降低对纤维的损伤,对于清梳的梳理工艺的选择也要特别注意,要尽可能的降低锡林的梳理速度,大约比一般纺棉的梳理速度低15%左右,一般纺棉的梳理速度是470r/min,本发明中清梳的梳理的速度范围380
‑
410 r/min;放大梳理隔距,梳理隔距比纺棉的梳理隔距放大1
‑
2丝(1丝=1/1000英吋),一般纺棉的梳理隔距是四点隔距9、8、8、7,本发明中清梳的梳理隔距范围是四点隔离11、10、10、9。另外,可以加大道夫和剥棉罗拉的张力,张力范围控制在1.04
‑
1.09,让棉网能够顺利转移。优选地,可以取消清梳的落杂点,进一步降低成本。
31.其中,道夫和剥棉罗拉的张力,主要是通过控制道夫的表面速度和剥棉罗拉的表面速度之比,使其速度比在1.04
‑
1.09范围之内。
32.在步骤(2)中,长绒棉的清梳联过程均采用一般纺棉工艺进行,在此不赘述。
33.(3)并条:采用三道并合,罗拉的中心距为(40~42)*(44~48)mm;其中,所述三道并合的过程,包括以下步骤:预并:对第一生条进行预并合得到预并条,采用1.5
‑
1.7倍的后区牵伸工艺;混一并:采用5根第一生条的预并条与2根第二生条一起并合;末并:将混一并出来的条子再次并合,保证混合的均匀度。
34.由于纤维长度较长,整齐度较好,因此,本发明方案中并条工序采用大的罗拉隔离,罗拉的中心距(40~42)*(44~48)mm。
35.为了进一步的合使纤维伸直平行,预并条的后牵伸倍数偏大掌握,采用1.5
‑
1.7倍的后区牵伸工艺,提高纤维的伸直平行度。
36.并条工序为了保让各种纤维的充分混合,并条工序采用三道并合:先经过预并,将6
‑
7根的梳棉生条进行预并合,优选为采用7根梳棉生条进行预并合,可以提高石墨烯与长绒棉的混合均匀度;再混一并,混一并采用5根长绒棉和石墨烯的预并条与2根纯的长绒棉的条子一起并合,达到达求的混纺比;末并。优选地,预并条工序的梳棉生条是由一条清梳生产线上不同的梳棉机台制成,采用不同梳棉机台制备的棉条进行搭配并条可以进一步提高混合的均匀度。
37.(4)粗纱:捻系数为90
‑
95,后区隔距为60
‑
66 mm,后区牵伸倍数1.2
‑
1.25倍,粗纱的定量为7.0~8.5克/10米。
38.在粗纱工序中,粗纱的捻系数尽量加大,做到90
‑
95,采用加大的捻系数的原因是为了保证成纱的条干指标,保证粗纱表面的粗糙程度,纺纱张力尽可能的减少,防止意外伸长,造成成纱细节,保证粗纱的牵伸顺利进行。用大的后区隔距和较小的后区牵伸倍数是为
了提高纤维的伸直平行度,保证成纱条干,保证粗纱成形良好。粗纱的定量偏重控制,一是为了提高产量,另外一个的原因是为了在后工序达伸的过程中,须条的宽度较宽,有利于包覆效果。通过对粗纱工序的以上改进,能做到质、量合一的完美结合。
39.(5)细纱:以涤纶长丝与氨纶丝作为芯纱,以长绒棉石墨烯锦纶的混纺粗纱为外包纱,经细纱工序制成长绒棉石墨烯锦纶包双芯混纺纱线。细纱工序中,钳口隔距3.5mm,皮辊选用邵氏硬度70度的胶辊,后区隔距38~42mm,后区牵伸倍数1.15
‑
1.22倍。
40.在所述细纱工序中,在保证粗纱顺利牵伸的前提下,细纱工序选用较小的钳口隔距3.5mm,以减小棉结疵点,改善细纱的条干均匀度。对皮辊的要求较多,不能太软也不能太硬,选用邵氏硬度70度的胶辊。合理的使用钢丝圈型号,以减少成纱毛羽,加强设备维护。为了保证牵伸部件的良好运作,采用较大的后区隔距38~42mm和较小的后区牵伸倍数1.15~1.22倍,以进一步改善成纱条干。
41.为了进一步提高氨纶包芯纱的强度并达到防止滑弹的目的,在本发明中还提供一种优选的实施例方案,在细纱工序前,对涤纶长丝与氨纶丝进行预处理。所述预处理过程包括以下步骤:根据成纱的弹性要求,先把氨纶丝1牵伸到所需的牵伸倍数(如2.5倍、2.8倍、3.0倍、3.2倍、3.5倍、3.8倍、4.0倍等等),再与涤纶长丝2并在一起经过5
‑
7公斤高压空气加上网点3,使涤纶长丝2和氨纶丝1锁紧在一起。
42.经过预处理后的涤纶长丝2和氨纶丝1的结构如图1所示,网点3使纶长丝2和氨纶丝1锁紧在一起,起到固定氨纶丝1的作用,达到提高氨纶包芯纱的强度并达到防止滑弹的目的。
43.网点3是指氨纶丝与涤纶长丝之间形成一个交联点。
44.(6)络筒:采用水雾捻或者机械搓捻的接头形式,络筒速度900
‑
1100m/min。
45.为了保证络筒接头,络筒工序时采用水雾捻或者机械搓捻的接头形式。络筒速度偏低控制,防止纱线挂毛,导致布面起横。
46.(7)蒸纱定型:纺好的筒子纱,经过70
‑
90℃,15
‑
25分钟的高温定型。
47.蒸纱定型是一个优选的工序,蒸纱定型是可以固捻,以利于后工序织造。
48.本发明所提供的长绒棉石墨烯锦纶包双芯混纺纱线的制备方法,采用传统的纺法设备,通过改进工艺和原料配合,使含长绒棉、锦纶、石墨烯、氨纶、涤纶5种组分的材料组合成纱线,可用于牛仔服饰,在传统弹力牛仔的基础上,增加了抗菌、耐磨、高强的功能。
49.本发明中还提供一种采用如上所述的制备方法制备得到的长绒棉石墨烯锦纶包双芯混纺纱线,包括外包纱和芯纱;外包纱按照重量百分比计,由石墨烯锦纶30
‑
50%、长绒棉50%
‑
70%组成;芯纱由涤纶长丝和氨纶丝组成。
50.其中,氨纶丝的d数可以为20d
‑
105d,涤纶长丝的d数可以为50d
‑
150d,长绒棉石墨烯锦纶包双芯混纺纱线的纱支范围可以为4
‑
26s。所述石墨烯锦纶的规格可以为1.3
‑
1.5d*36
‑
40mm,此规格的纤维韧性比较大。
51.所述长绒棉石墨烯锦纶包双芯混纺纱线,具有以下优点:(1)高强:这种纱线集长绒棉高单纤维强力与石墨烯锦纶的高强一起,生产出来的纱线强度极高,能很好的满足牛仔用纱高强的需求。
52.(2)耐磨:由于石墨烯锦纶极强的耐磨性能,使得采用石墨烯锦纶作为外包纱的纱线也具有极强的耐磨性能。
53.(3)抗菌:由于石墨烯具有抗菌的特性,使得采用石墨烯锦纶作为外包纱的纱线也具有抗菌性能。
54.(4)防滑弹:由于涤纶长丝和氨纶丝经过包覆机赋予了一定的网点,即使在后续的加工过程中仍会保持这一特性,使涤纶长丝和氨纶丝锁紧在一起。即使反复拉伸之后也不容易断裂失去弹性,同时涤纶长丝还可以提高氨纶丝在包芯纱内的强力。
55.以下通过具体实施例对本发明做进一步说明。
56.实施例1:(1)原料选配:按照重量百分比计,外包纱选择石墨烯锦纶40%、长绒棉60%;涤纶长丝选用75d;氨纶丝采用40d。
57.(2)清梳联:将占所有长绒棉重量的30%的长绒棉经过清梳联制成棉网,长绒棉的清梳联过程均采用一般纺棉工艺进行。
58.用棉网包裹石墨烯锦纶经过清梳联制成第一生条:清花打手的速度为760r/min,清梳的湿度控制在70%
‑
75%左右,清梳的梳理的速度范围380r/min,梳理隔距是四点隔距9、8、8、7,加大道夫和剥棉罗拉的张力,张力控制在1.05。
59.将剩余长绒棉经过清梳联制成第二生条,长绒棉的清梳联过程均采用一般纺棉工艺进行。
60.(3)并条:采用三道并合,罗拉的中心距为40*46mm;其中,三道并合包括:预并:对7根第一生条进行预并合得到预并条,采用1.5倍的后区牵伸工艺;混一并:采用5根长棉棉和石墨烯的预并条与2根纯的长绒棉的条子一起并合;末并:将混一并出来的条子再次并合。
61.(4)粗纱:捻系数为90,后区隔距为62,后区牵伸倍数1.2倍,粗纱的定量为7.5克/10米。
62.(5)细纱:先把氨纶丝牵伸至3.0倍,再与涤纶长丝并在一起经过高压空气(5公斤压力)加上网点,使涤纶长丝和氨纶丝锁紧在一起。
63.采用涤纶长丝与氨纶丝作为芯纱,经过细纱工序与长绒棉石墨烯锦纶的混纺粗纱纺成长绒棉石墨烯锦纶包双芯混纺纱线,钳口隔距3.5mm,皮辊选用邵氏硬度70度的胶辊,后区隔距38mm,后区牵伸倍数1.20倍。
64.(6)络筒:采用机械搓捻的接头形式,络筒速度为900 m/min。
65.(7)蒸纱定型:纺好的筒子纱,经过80℃,20分钟的高温定型。
66.对制备得到的长绒棉石墨烯锦纶包双芯混纺纱进行性能测试,结果如表1所示。以下检测依据fz/t 12010
‑
2011标准进行检测。
67.以涤纶长丝75d&氨纶丝40d为芯,以棉纤维为外包纤维的同样支数的包芯纱,其强力为570cn,比这个品种的强力要低15%~20%左右。
68.表1测试项目测试数据
实际号数(tex)43.2重量偏差0.3重量不匀率%0.80回潮率%5.7断裂强力(cn)672.0强力不匀率%9.5断裂伸长率%7.7断裂强度(cn/tex)16.2捻度(t/10cm)75.8捻度不匀率%1.1条干cv.50细节(
‑
30%)(个/km)160.1细节(
‑
40%)(个/km)2.5细节(
‑
50%)(个/km)0.0粗节( 35%)(个/km)142.0粗节( 50%)(个/km)15.8粗节( 70%)(个/km)1.5粗节( 100%)(个/km)0.0棉结( 140%)(个/km)123.8棉结( 200%)(个/km)15.8棉结( 280%)(个/km)2.9毛羽指数(3mm)4.28实施例2:长绒棉/石墨稀(1)原料选配:按照重量百分比计,外包纱选择石墨烯锦纶40%、长绒棉60%;涤纶长丝选用75d;氨纶丝采用70d。
69.(2)清梳联:将占所有长绒棉重量的30%的长绒棉经过清梳联制成棉网,长绒棉的清梳联过程均采用一般纺棉工艺进行。
70.用棉网包裹石墨烯锦纶经过清梳联制成第一生条:清花打手的速度为780r/min,清梳的湿度控制在70%
‑
75%左右,清梳的梳理的速度范围400r/min,梳理隔距是四点隔距9、8、8、7,加大道夫和剥棉罗拉的张力,张力控制在1.07。
71.将剩余长绒棉经过清梳联制成第二生条,长绒棉的清梳联过程均采用一般纺棉工艺进行。
72.(3)并条:采用三道并合,罗拉的中心距为42*48mm;其中,三道并合包括:预并:对6根第一生条进行预并合得到预并条,采用1.5
‑
1.7倍的后区牵伸工艺;混一并:采用5根长棉棉和石墨烯的预并条与2根纯的长绒棉的条子一起并合;末并:将混一并出来的条子再次并合,保证混合的均匀度。
73.(4)粗纱:捻系数为93,后区隔距为64mm,后区牵伸倍数1.25倍,粗纱的定量为8.5
克/10米。
74.(5)细纱:先把氨纶丝牵伸至3.5倍,再与涤纶长丝并在一起经过高压空气(6公斤压力)加上网点,使涤纶长丝和氨纶丝锁紧在一起。
75.采用涤纶长丝与氨纶丝作为芯纱,经过细纱工序与长绒棉石墨烯锦纶的混纺粗纱纺成长绒棉石墨烯锦纶包双芯混纺纱线,钳口隔距3.5mm,皮辊选用邵氏硬度70度的胶辊,后区隔距42mm,后区牵伸倍数1.22倍。
76.(6)络筒:采用机械搓捻的接头形式,络筒速度为1000m/min。
77.(7)蒸纱定型:纺好的筒子纱,经过90℃,15分钟的高温定型。
78.对制备得到的长绒棉石墨烯锦纶包双芯混纺纱进行性能测试,结果如表2所示。以下检测依据fz/t 12010
‑
2011标准进行检测。
79.以涤纶长丝75d&氨纶丝70d为芯,以棉纤维为外包纤维的同样支数的包芯纱,其强力为1024cn, 比这个品种的强力要低10%~15%左右。
80.表2测试项目测试数据实际号数(tex)74.6重量偏差
‑
0.7重量不匀率%0.92回潮率%5.8断裂强力(cn)1205.3强力不匀率%7.9断裂伸长率.0断裂强度(cn/tex)16.5捻度(t/10cm)56.1捻度不匀率%0.6条干cv%9.90细节(
‑
30%)(个/km)22.0细节(
‑
40%)(个/km)0.0细节(
‑
50%)(个/km)0.0粗节( 35%)(个/km)21.0粗节( 50%)(个/km)1.0粗节( 70%)(个/km)0.0粗节( 100%)(个/km)0.0棉结( 140%)(个/km)16.5棉结( 200%)(个/km)1.7棉结( 280%)(个/km)0.0毛羽指数(3mm)9.28应当理解的是,本发明的应用不限于上述的举例,对本领域普通技术人员来说,可以根据上述说明加以改进或变换,所有这些改进和变换都应属于本发明所附权利要求的保护范围。
再多了解一些
本文用于企业家、创业者技术爱好者查询,结果仅供参考。