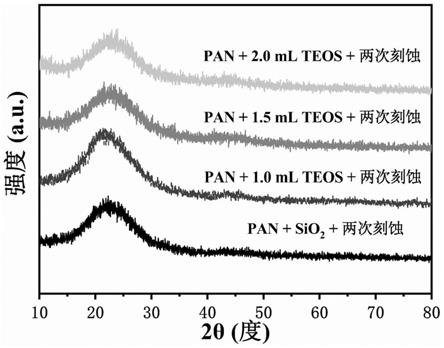
1.本发明涉及一种碳纤维的制备方法,尤其涉及一种同时具有大比表面积和微孔的碳纤维的制备方法,属于多孔碳材料制备技术领域。
背景技术:
2.多孔碳材料因其独特的性能而备受关注,它们拥有高表面积、大孔体积和独特的孔径分布的特点,具有很大的应用潜力[chem.rev.,2015,115,5159]。另外,根据国际纯粹与应用化学联合会(iupac)的定义,多孔材料可根据孔径大小分为三类:微孔(孔径小于2nm)、介孔(孔径在2至50nm)和大孔(孔径大于50nm)。然而,具有宽孔径分布的活性碳具有许多局限性,例如低电导率、低传质和低结构稳定性的缺点,阻碍了在催化和电化学方面的应用。为了克服这些缺点,人们尝试通过各种方法来制备具有窄孔径分布、高比表面积和高电导率的高质量多孔碳材料。然后通过将多孔碳与其它材料进行复合,可得到许多特殊功能性材料,实现增强的性能,并应用于多种领域。
[0003]
制备多孔碳材料的方法主要包括硬模板法、软模板法和混合模板法。在硬模板法中,通过引入硬模板,然后经过后续刻蚀处理的方法,从而制备出多孔碳材料。liang等将富氮芳族聚合物和胶体二氧化硅分别用作前体和模板,然后通过氨活化,得到比表面积为1280m2g
‑1的微/介孔碳材料[nat.commun.,2014,5,4973]。相对于硬模板而言,软模板法可以免去刻蚀等繁琐步骤,并通过其它各种策略创造多孔结构。在这些策略中,化学活化法(例如koh) 被认为是一种成熟的方法,用于制备具有非常大表面积且高度多孔的碳材料。xia等通过koh 活化的方法将碳材料进行退火活化,得到比表面积为1820.6m2g
‑1的多孔碳材料[nano energy, 2021,84,105877]。
[0004]
尽管制备碳材料的方法有很多种,但是静电纺丝作为一种经典制备碳材料的方法,可以用来制备出各种纳米或微米级直径的超细纤维碳材料,因而是制备碳材料的有利法宝。它可以通过调控静电纺丝的各个参数以及退火条件从而达到控制材料形貌及结构的特点,同时具有操作简单,制备方便且可大规模制备等优势。wang等利用静电纺丝和硬模板法制备了比表面积高达488m2/g、大孔尺寸的多孔碳纤维[acs nano,2018,12,3406]。cn106521715a(一种高比表面积微孔碳纤维的制备方法)公开了利用电纺酚醛树脂和聚乙烯醇的混合物制备出多孔碳纤维,但是它们的表面积不大。通过将硬模板法与软模板法相结合的软硬混合模板法,可以进一步扩展多孔碳纤维材料的制备,并提高其比表面积。但是,在产生的大量孔隙的同时,可能会导致其纳米结构的崩溃,这也是制备多孔碳纤维的难点。另外在硬模板法中,sio2在有机溶剂中溶解性较差,将严重影响电纺过程和多孔的形成。
[0005]
因此,在保持特定纳米结构同时开发超高比表面积的微孔碳材料仍然是一项艰巨的挑战。
技术实现要素:
[0006]
为了解决上述技术问题,本发明的目的在于提供一种在可以保持特定纳米结构的同时具有超高比表面积的微孔碳材料维的制备方法。
[0007]
为了实现上述目的,本发明的基于静电纺丝的碳纤维的制备方法,该制备方法包括以下步骤:
[0008]
将造孔剂加入到聚丙烯腈溶液中,制成前驱体混合溶液;
[0009]
向前驱体混合溶液中盐酸,形成均匀的溶液并进行静电纺丝,得到静电纺丝纤维样品;
[0010]
将电纺丝纤维样品进行预氧化处理和碳化处理,研磨形成粉末;
[0011]
将粉末浸泡于氢氧化钾溶液中,搅拌、清洗、抽滤、烘干;
[0012]
将烘干后的粉末与氢氧化钾混合,进行退火处理,清洗、抽滤、烘干,得到碳纤维。
[0013]
本发明的基于静电纺丝的碳纤维的制备方法通过硬模板(四乙氧基硅烷)与软模板(koh 活化)相结合的软硬混合模板法,可以获得高比表面积且孔径分布更小的碳纤维,另外碳纤维可以很好保持其结构,不会塌陷。
[0014]
本发明的基于静电纺丝的碳纤维的制备方法包括制备前驱体混合溶液的步骤。
[0015]
在本发明的一具体实施方式中,聚丙烯腈溶液为聚丙烯腈与n,n
‑
二甲基甲酰胺的混合溶液;其中,聚丙烯腈溶液中聚丙烯腈与n,n
‑
二甲基甲酰胺的混合比例为(0.5
‑
1.5)g:20ml。
[0016]
在本发明的一具体实施方式中,采用的造孔剂为四乙氧基硅烷;其中,聚丙烯腈溶液中聚丙烯腈与造孔剂的混合比例为(0.5
‑
1.5)g:(1
‑
2)ml。
[0017]
本发明的基于静电纺丝的碳纤维的制备方法包括制备静电纺丝纤维样品的步骤。
[0018]
在本发明的一具体实施方式中,采用的盐酸的浓度质量分数为37%的浓盐酸;其中,聚丙烯腈溶液中聚丙烯腈与盐酸的混合比例为(0.5
‑
1.5)g:(5
‑
20)μl。
[0019]
在本发明的一具体实施方式中,静电纺丝的工艺条件为:
[0020]
喷丝头和铝箔收集器的距离为18
‑
25cm,正电压数值为25kv以内(优选20kv
‑
25kv),注射器的推速为0.05mm/min
‑
0.2mm/min。
[0021]
本发明的基于静电纺丝的碳纤维的制备方法包括制备粉末的步骤。
[0022]
在本发明的一具体实施方式中,预氧化处理为:
[0023]
空气氛围、预氧化温度为250℃
‑
300℃、预氧化时间为60min
‑
180min。
[0024]
在本发明的一具体实施方式中,碳化处理为:
[0025]
氩气氛围,碳化处理的温度为700℃
‑
900℃、碳化处理的时间为60min
‑
120min。
[0026]
在本发明的一具体实施方式中,将所述粉末浸泡于氢氧化钾溶液时,氢氧化钾溶液浓度为3摩尔/升
‑
6摩尔/升,搅拌时间为12h
‑
36h,烘干所用的温度为60℃
‑
180℃。
[0027]
在本发明的一具体实施方式中,将烘干后的粉末与氢氧化钾混合时,烘干后的粉末与氢氧化钾的混合质量比例为0.5
‑
2:0.5
‑
2;
[0028]
退火处理是在氩气氛围中700℃
‑
900℃下退火120min
‑
240min。
[0029]
本发明还提供了一种碳纤维,该碳纤维是通过本发明的基于静电纺丝的碳纤维的制备方法制备得到的;其中,该碳纤维的比表面积至少为2530.5m
2 g
‑1,最小孔径分布为1.7nm左右。
[0030]
本发明的碳纤维可以用于电催化、锂离子电池、锂硫电池中。
[0031]
本发明的基于静电纺丝的碳纤维的制备方法通过两步刻蚀法,使得制备的碳纤维同时具有较大比表面积和微孔。具体涉及以静电纺丝作为制备手段,利用四乙氧基硅烷作为造孔剂, koh作为刻蚀剂,通过软硬混合模板法制备出bet比表面积高达2530.5m
2 g
‑1,最小孔径分布在1.7nm左右微孔碳纤维。该材料的制备为未来供了更为广阔的应用前景,应用领域包括电催化、锂离子电池和锂硫电池等能源转换方面。
[0032]
本发明的基于静电纺丝的碳纤维的制备方法,利用sio2前驱体四乙氧基硅烷(teos) 作为造孔剂,成功避免了sio2固体难溶于有机溶剂n,n
‑
二甲基甲酰胺的问题,制备了介孔碳纤维。然后经过koh二次刻蚀步骤得到bet比表面积高达2530.5m
2 g
‑1,最小孔径分布在1.7 nm左右的微孔碳纤维,为材料在未来的储能和能源转换领域奠定了良好基础。
附图说明
[0033]
图1为本发明基于不同体积四乙氧基硅烷电纺丝(实施例2、3和4中)和sio2电纺丝 (对比例3中)经过二次刻蚀后的x
‑
射线衍射图谱;四乙氧基硅烷的体积范围为1.0
‑
2.0ml; sio2质量为0.9g。
[0034]
图2为本发明制备对比例2、4和6的bet比表面积测试结果。
[0035]
图3为本发明制备对比例3、5和实施例2、3和4的bet比表面积测试结果。
[0036]
图4为本发明制备的多孔碳纤维的透射电镜俯视图:(a)是对比例3中制得的,(b)是实施例2中制得的,(c)是实施例3中制得的,(d)是实施例4中制得的。
[0037]
图5为本发明制备的多孔碳纤维的扫描电镜俯视图:(a)是实施例2中制得的(标尺为 500nm),(b)实施例3中制得的(标尺为500nm);(c)是实施例2中制得的(标尺为300nm), (d)实施例3中制得的(标尺为300nm)。
具体实施方式
[0038]
本发明为一种基于静电纺丝制备超高比表面积、微孔碳纤维的方法,所用到造孔剂化学结构式为:
[0039][0040]
与直接利用sio2纳米颗粒固体或纳米颗粒水溶液前驱体来制备多孔碳纳米纤维的办法相比,本发明利用sio2前驱体四乙氧基硅烷(teos)作为造孔剂,成功避免了sio2固体难溶于有机溶剂n,n
‑
二甲基甲酰胺,制备了介孔碳纤维。然后经过koh二次刻蚀步骤得到微孔尺寸的碳纤维;通过添加不同量的teos,确定了最适宜的量,得到其bet比表面积高达2530.5 m
2 g
‑1,孔径分布在1.7nm左右的微孔碳纤维,为材料在未来的储能和能源转换领域奠定了良好基础。
[0041]
上述一种基于静电纺丝制备超高比表面积、微孔碳纤维的方法,它包括以下步骤:(a) 将造孔剂加入pan(聚丙烯腈)溶液中混合配制成前驱体混合溶液,所述造孔剂为teos
(四乙氧基硅烷);(b)将上述前驱体混合溶液中加入一定体积的浓盐酸(质量分数为37%),直至形成均匀的溶液并进行静电纺丝;(c)将所述电纺丝纤维样品进行预氧化和碳化处理,并将退火得到的样品进行研磨,形成粉末;(d)将所述退火后的粉末浸泡于氢氧化钾溶液中,持续搅拌,然后清洗、抽滤、烘干;(e)将所述烘干后的粉末与氢氧化钾混合,混合均匀后,在管式炉中进行退火处理,然后清洗、抽滤、烘干即可。
[0042]
步骤(a)中,聚丙烯腈溶液为0.9g pan与20ml dmf(n,n
‑
二甲基甲酰胺)混合所得,所加造孔剂的体积为1.0ml
‑
2ml。步骤(b)中,所用质量37%的浓盐酸体积为10μl。所述静电纺丝的条件为喷丝头和铝箔收集器之间的距离调整为23cm,正电压数值为20kv以内,注射器的推速为0.05mm/min。步骤(c)中,所述电纺丝纤维的预氧化条件为空气氛围、退火温度为270℃、退火时间为120min;碳化条件为氩气氛围,退火温度为700
‑
900℃、退火时间为60
‑
120min。步骤(d)中,所述氢氧化钾溶液浓度为6摩尔/升,搅拌时间为24h,烘干所用的温度为60℃。步骤(e)中,所述烘干后的粉末与氢氧化钾的混合比例为1:1,退火条件为氩气氛围,退火温度为700℃
‑
900℃、退火时间为120min。
[0043]
实施例1
[0044]
本实施例提供一种化合物四乙氧基硅烷用于静电纺丝制备大比表面积、微孔碳纤维的方法,其结构式为:
[0045][0046]
实施例2
[0047]
本实施例提供基于静电纺丝制备多孔碳纤维的过程,具体步骤如下:首先,将0.9g pan 加入到20ml的有机溶剂dmf中,并不断搅拌,直至彻底溶解,然后在不断搅拌下向其中加入1ml的teos溶剂,随后加入10μl的浓盐酸,并不断搅拌,直至溶液均匀。然后利用配好的上述溶液进行静电纺丝,用5ml医用注射器吸取若干量配制好的电纺液,再安装上静电纺丝专用的23号针头上。将注射器小心安装到静电纺丝的推动泵上,然后用干净的铝箔纸包住收集器上的转筒,以做接收纺丝的用途。将喷丝头和铝箔收集器之间的距离调整为23cm。打开静电纺丝的正负电压,调整相应的参数,使得正压在20kv,并使得收集器的转筒收集喷丝头喷射的电纺丝。将收集到的纺丝在60℃的电热恒温鼓风干燥箱中干燥12h。
[0048]
随后干燥后的电纺丝纤维进行预氧化,条件为空气氛围、退火温度为270℃、退火时间为120min;紧接着进行碳化,条件为氩气氛围,退火温度为800℃、退火时间为120min。将退火得到的碳纤维浸泡于6m koh溶液中进行刻蚀,除去造孔剂,随后清洗至中性,并烘干。将烘干后的样品与koh按照1:1的质量比进行混合均匀,放至磁舟中,在ar气氛下进行退火刻蚀,退火温度为700℃、退火时间为120min,随后清洗至中性,并烘干。
[0049]
实施例3
[0050]
本实施例提供基于静电纺丝制备多孔碳纤维的过程,具体步骤如下:首先,将0.9g pan 加入到20ml的有机溶剂dmf中,并不断搅拌,直至彻底溶解,然后在不断搅拌下向其中加入1.5ml的teos溶剂,随后加入10μl的浓盐酸,并不断搅拌,直至溶液均匀。然后利用配好
的上述溶液进行静电纺丝,用5ml医用注射器吸取若干量配制好的电纺液,再安装上静电纺丝专用的23号针头上。将注射器小心安装到静电纺丝的推动泵上,然后用干净的铝箔纸包住收集器上的转筒,以做接收纺丝的用途。将喷丝头和铝箔收集器之间的距离调整为23 cm。打开静电纺丝的正负电压,调整相应的参数,使得正压在20kv,并使得收集器的转筒收集喷丝头喷射的电纺丝。将收集到的纺丝在60℃的电热恒温鼓风干燥箱中干燥12h。
[0051]
随后干燥后的电纺丝纤维进行预氧化,条件为空气氛围、退火温度为270℃、退火时间为120min;紧接着进行碳化,条件为氩气氛围,退火温度为800℃、退火时间为120min。将退火得到的碳纤维浸泡于6m koh溶液中进行刻蚀,除去造孔剂,随后清洗至中性,并烘干。将烘干后的样品与koh按照1:1的质量比进行混合均匀,放至磁舟中,在ar气氛下进行退火刻蚀,退火温度为700℃、退火时间为120min,随后清洗至中性,并烘干。
[0052]
实施例4
[0053]
本实施例提供基于静电纺丝制备多孔碳纤维的过程,具体步骤如下:首先,将0.9g pan 加入到20ml的有机溶剂dmf中,并不断搅拌,直至彻底溶解,然后在不断搅拌下向其中加入2.0ml的teos溶剂,随后加入10μl的浓盐酸,并不断搅拌,直至溶液均匀。然后利用配好的上述溶液进行静电纺丝,用5ml医用注射器吸取若干量配制好的电纺液,再安装上静电纺丝专用的23号针头上。将注射器小心安装到静电纺丝的推动泵上,然后用干净的铝箔纸包住收集器上的转筒,以做接收纺丝的用途。将喷丝头和铝箔收集器之间的距离调整为23 cm。打开静电纺丝的正负电压,调整相应的参数,使得正压在20kv,并使得收集器的转筒收集喷丝头喷射的电纺丝。将收集到的纺丝在60℃的电热恒温鼓风干燥箱中干燥12h。
[0054]
随后干燥后的电纺丝纤维进行预氧化,条件为空气氛围、退火温度为270℃、退火时间为120min;紧接着进行碳化,条件为氩气氛围,退火温度为800℃、退火时间为120min。将退火得到的碳纤维浸泡于6m koh溶液中进行刻蚀,除去造孔剂,随后清洗至中性,并烘干。将烘干后的样品与koh按照1:1的质量比进行混合均匀,放至磁舟中,在ar气氛下进行退火刻蚀,退火温度为700℃、退火时间为120min,随后清洗至中性,并烘干。
[0055]
对比例1
[0056]
本对比例提供一种化合物二氧化硅用于静电纺丝制备多孔碳纤维,其结构式为:
[0057][0058]
对比例2
[0059]
本对比例提供一种对比的多孔碳纤维的过程制备过程,具体步骤如下:首先,将0.9g pan 加入到20ml的有机溶剂dmf中,并不断搅拌,直至彻底溶解,然后在不断搅拌下向其中加入0.9g商用sio2粉末,并不断搅拌,直至溶液均匀。然后利用配好的上述溶液进行静电纺丝,用5ml医用注射器吸取若干量配制好的电纺液,再安装上静电纺丝专用的23号针头
23号针头上。将注射器小心安装到静电纺丝的推动泵上,然后用干净的铝箔纸包住收集器上的转筒,以做接收纺丝的用途。将喷丝头和铝箔收集器之间的距离调整为23cm。打开静电纺丝的正负电压,调整相应的参数,使得正压在20kv,并使得收集器的转筒收集喷丝头喷射的电纺丝。将收集到的纺丝在60℃的电热恒温鼓风干燥箱中干燥12h。
[0070]
随后干燥后的电纺丝纤维进行预氧化,条件为空气氛围、退火温度为270℃、退火时间为120min;紧接着进行碳化,条件为氩气氛围,退火温度为800℃、退火时间为120min。将退火得到的碳纤维浸泡于6m koh溶液中进行刻蚀,除去造孔剂,随后清洗至中性,并烘干。将烘干后的样品与koh按照1:1的质量比进行混合均匀,放至磁舟中,在ar气氛下进行退火刻蚀,退火温度为700℃、退火时间为120min,随后清洗至中性,并烘干。
[0071]
对比例6
[0072]
本实施例提供基于静电纺丝制备多孔碳纤维的过程,具体步骤如下:首先,将0.9g pan 加入到20ml的有机溶剂dmf中,并不断搅拌,直至彻底溶解,然后在不断搅拌下向其中加入1.5ml的teos溶剂,随后加入10μl的浓盐酸,并不断搅拌,直至溶液均匀。然后利用配好的上述溶液进行静电纺丝,用5ml医用注射器吸取若干量配制好的电纺液,再安装上静电纺丝专用的23号针头上。将注射器小心安装到静电纺丝的推动泵上,然后用干净的铝箔纸包住收集器上的转筒,以做接收纺丝的用途。将喷丝头和铝箔收集器之间的距离调整为23 cm。打开静电纺丝的正负电压,调整相应的参数,使得正压在20kv,并使得收集器的转筒收集喷丝头喷射的电纺丝。将收集到的纺丝在60℃的电热恒温鼓风干燥箱中干燥12h。
[0073]
随后干燥后的电纺丝纤维进行预氧化,条件为空气氛围、退火温度为270℃、退火时间为120min;紧接着进行碳化,条件为氩气氛围,退火温度为800℃、退火时间为120min。将退火得到的碳纤维浸泡于6m koh溶液中进行刻蚀,除去造孔剂,随后清洗至中性,并烘干。
[0074]
比较实验例1
[0075]
本例提供一种多孔碳纤维的制备方法。参照文献(adv.energy mater.,2016,7,1601943)。分别将1.0g pan和pmma(聚甲基丙烯酸甲酯)溶于10ml dmf溶液中,并在60℃条件下搅拌2h,然后将这两种溶液以相同重量比例混合,搅拌3h,将得到的聚合物混合溶液在电纺单喷头(直径:0.1mm)、施加电压为18kv、流量为10μl min
‑1、喷丝头和收集器之间的距离为15cm的条件下进行纺丝。将收集到的纺丝先在270℃下稳定2h,然后在氩气氛围、 800℃下退火1h。在koh活化过程中,将400mg上述退火得到的纺丝分散在20ml的6 摩尔每升的koh水溶液中搅拌4h,然后在室温下静置20h。随后将溶液通过反复离心和多次洗涤步骤,并在60℃下干燥。最后在氩气氛围、800℃下退火1h,得到多孔碳纤维。通过bet比表面积测的比表面积和孔径分布结果见表1。
[0076]
比较实验例2
[0077]
本例提供一种多孔碳纤维的制备方法,参照文献(adv.mater.2012,24,2047)。将静电纺丝制备的聚吡咯纳米纤维与koh按照重量比3:1混合,并以3℃min
‑1加热速率加热到650℃,在氮气氛围下保持0.5h,将koh活化后的混合物用1mol l
‑1hcl溶液和去离子水洗涤至滤液变成中性,最后将样品在80℃烘箱中干燥过夜,得到多孔碳纤维。通过bet比表面积测的比表面积和孔径分布结果见表1。
[0078]
表1利用实施例2至4、对比例2至6测的比表面积和孔径分布结果
[0079][0080][0081]
本技术中通过软硬模板法制备高比表面积的微孔碳纤维(实施例3中),并与对比例2、 3、4、5和6中进行对比。结果表明,利用koh刻蚀处理可以轻松除去造孔剂,避免使用危险的氢氟酸处理(参见图1);利用四乙氧基硅烷作为造孔剂的硬模板法,可以显著提高碳纤维的比表面积和缩小孔径分布,也意味着它能更加均匀地分散在静电纺丝溶液中,从而使得具有更小的孔径分布(参见图2);利用四乙氧基硅烷作为造孔剂的硬模板法,再加上koh 活化的软模板法,可以显著提高材料的比表面积,并改善碳纤维中的孔径分布(参见图3);通过透射电镜测试进行对比,利用四乙氧基硅烷作为造孔剂的硬模板法,再加上koh活化的软模板法,能表明出明显的孔道结构,意味着四乙氧基硅烷适合用于静电纺丝来着制备多孔碳纤维(参见图4);通过扫描电镜测试进行对比,利用四乙氧基硅烷作为造孔剂的硬模板法,再加上koh活化的软模板法,经过两次刻蚀后,材料仍保持很好的结构完整性,同时可能观察到明显的孔道结构,这表明,利用四乙氧基硅烷作为造孔剂,经过一次刻蚀,后再利用软模板法的koh活化刻蚀,仍能保持碳纤维结构不塌,(参见图5)。基于以上原因,利用四乙氧基硅烷作为造孔剂的硬模板法,再加上koh活化的软模板法,可以显著提高碳纤维的比表面积和改善孔径分布(参见表1)。
[0082]
与比较实验例1和2相比,利用四乙氧基硅烷的硬模板和koh的软模板活化方法可以使得碳纤维材料获得更大比表面积和更小的孔径分布(参见表1)。可见基于本发明的一种基于静电纺丝制备超高比表面积、微孔碳纤维的方法,具有更大的比表面积和更小的孔径分布的优势,这将为材料在未来的储能和能源转换领域奠定良好基础;这是因为,利用四乙氧基硅烷作为造孔剂,相比于sio2而言,可以更好地溶解在静电纺丝的溶液中,不仅可以方便后续的电纺过程,而且通过提高四乙氧基硅烷的体积,可以提高孔的数量,从而使其拥
有更大的比表面积。另外再加上koh的软模板法活化过程,可以再进一步提高碳纤维的比表面积和缩小孔径分布,最终使得碳纤维保持完整的结构,同时具有更大的比表面积和微孔级别的孔径分布,其最大比表面积和最小的孔径分布分别为2530.5m
2 g
‑1和1.7nm,该材料的制备为后续在能源转换领域的应用打下了坚实的基础。
[0083]
上述实施例只为说明本发明的技术构思及特点,其目的在于让熟悉此项技术的人士能够了解本发明的内容并据以实施,并不能以此限制本发明的保护范围。凡根据本发明精神实质所作的等效变化或修饰,都应涵盖在本发明的保护范围之内。
再多了解一些
本文用于企业家、创业者技术爱好者查询,结果仅供参考。