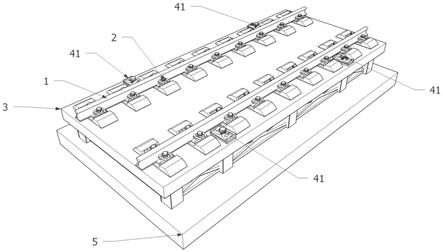
自调平装配式钢
‑
混凝土组合轨道结构
技术领域
1.本发明涉及轨道交通技术领域,特别地,涉及一种自调平装配式钢
‑
混凝土组合轨道结构。
背景技术:
2.我国高铁技术发展从无到有,由弱变强,历经了四个阶段,经过20多年的持续努力,我 国已经成为世界上高铁系统技术最全、创新能力最强、运营里程最长、运行速度最快、在建 规模最大的国家。截至2020年底,我国高速铁路运营里程已突破3.5万公里,根据《中长期 铁路网规划(2016年)》和《“十二五”综合交通运输体系规划》,今后我国仍将持续一定规模 的高速铁路建设,到2025年高速铁路规模将达到3.8万公里,远期将达到4.5万公里左右。 在2019年中共中央、国务院印发的《交通强度建设纲要》中,也对我国今后的轨道交通发展 提出了更高的要求,即要为人民提供“更安全可靠、更经济高效、更温馨舒适、更方便快捷、 更节能环保”的交通。高铁在全球其它国家也得到了空前发展,目前除已开通高铁的日本、 法国、德国、意大利、西班牙、比利时等国家外,还有10多个国家正在建设高铁,20多个国 家对高铁进行了规划,高速轨道交通系统已经成为世界多个优先发展计划。因此,开展高速 铁路建造技术研究是我国高铁“自主创新”、“走出去”、“持续引领世界高铁发展”的迫切需 要。
3.无砟轨道结构因其高平顺性、高稳定性、少维修等优点,已成为高速铁路的主要轨道结构型式,常用的结构组成为轨道板、充填层、混凝土底座或支承层。目前,高速铁路板式无砟轨道结构主要组成部件除了轨道板在工厂预制完成外,其它部分如底座板、填充层均采用现浇方式制作完成,并且轨道结构采用“逆作法”施工,即先浇筑混凝土底座或支承层,然后再在预制的轨道板和混凝土底座或支承层之间通过灌注填充形成充填层,以连接轨道板和混凝土底座或支承层,接着先进行轨道板的精调,然后再灌注板下调整层。该种竖向多层、纵向异构的带状结构体系,具有建造材料属性差别大、结构层次多、服役环境复杂等特征,在长期运营过程中存在以下问题:
①
传统的高速铁路轨道结构施工方法现场湿作业工作量大,导致轨道结构精度控制难度大、质量稳定性差和建造成本高等问题,且容易引起施工质量隐患,无法进行快速装配式智能化建造;
②
预制板式无砟轨道中混凝土底座、水泥乳化沥青砂浆层/自密实混凝土现场施工,工序较多影响施工效率,且水泥乳化沥青砂浆层耐久性较差;充填层可调整量小,适应下部支撑结构和环境能力弱,在大变形或特殊支撑基础上铺设较为困难;
③
由于轨道板、充填层、及底座板之间建造材料属性差别大、结构层次多,故而该多层轨道结构服役期间很难协同工作,容易发生界面损伤问题,且结构整体传力路径不明确,进而影响轨道结构服役期间的稳定性和使用寿命;
④
由于现有轨道结构的组成和施工方法,故而轨道结构养护、维修困难,更换困难,维修费用高。
4.综上所述,我国在无砟轨道结构方面取得了重要突破,为我国的高铁快速发展和“走出去”战略提供了保证,但是由于我国无砟轨道结构体系研发及营运时间短,传统轨道形式和施工方法难以满足高精度、少病害、节能环保、智能化的轨道结构建造要求,完全自主创新的轨道结构形式选择范围有限。因此,亟需基于安全服役的全寿命设计理念、智能建造和运维技术等,深入开展新型轨道结构及其建造技术研究,形成具有自主知识产权的新型装配式轨道结构及其智能建造成套技术。
技术实现要素:
5.本发明提供了一种自调平装配式钢
‑
混凝土组合轨道结构,以解决现有无砟轨道结构施工时现场湿作业工作量大、质量稳定性差;充填层可调整量小,适应下部支撑结构和环境能力弱;容易出现界面损伤,轨道结构服役期间的稳定性和使用寿命差;轨道板养护和维修困难、更换困难等技术问题。
6.本发明采用的技术方案如下:一种自调平装配式钢
‑
混凝土组合轨道结构,包括:现场浇筑成型于支撑基础上的底座板,底座板沿列车的运行方向延伸,底座板上设有沿其长度方向依次间隔设置且由工厂预制的预制钢
‑
混凝土轨道单元,其上支设有用于对列车进行导向支撑的钢轨;自调平装配式钢
‑
混凝土组合轨道结构还包括自调平扣锚系统,自调平扣锚系统的下端预埋于底座板中,自调平扣锚系统的上端穿设预制钢
‑
混凝土轨道单元后伸出,以用于将底座板和预制钢
‑
混凝土轨道单元连接成可拆卸式的整体结构,并用于对自调平装配式钢
‑
混凝土组合轨道结构进行调平。
7.进一步地,预制钢
‑
混凝土轨道单元包括轨道板和预制装配式钢结构、及用于对钢轨进行安装和支撑的承轨台;预制装配式钢结构沿底座板的长度方向布设,轨道板支撑于预制装配式钢结构上,且与预制装配式钢结构预制成整体;自调平扣锚系统的下端预埋于底座板内,自调平扣锚系统的上端依次穿设预制装配式钢结构和轨道板后伸出,以用于将底座板、预制装配式钢结构、及轨道板连接成可拆卸式的整体结构,并将预制装配式钢结构支撑于底座板上;承轨台沿轨道板的长度方向依次间隔设置于轨道板的上表面上,钢轨支撑于承轨台上,并通过连接于承轨台的第一扣件组固定。
8.进一步地,预制装配式钢结构为钢桁架,钢桁架包括多根竖直间隔设置的节点立柱、连接于相邻两根节点立柱之间的连接栏、及用于连接钢桁架和轨道板的第一栓钉;轨道板支设于钢桁架的顶端,且通过第一栓钉与钢桁架连接成整体。
9.进一步地,预制装配式钢结构为工字钢结构,工字钢结构包括沿底座板的宽度方向平行间隔设置的两条支撑钢带、沿支撑钢带的长度方向依次间隔连接于支撑钢带上的节点立柱、连接于两条支撑钢带之间的第一横隔板、及用于连接支撑钢带和轨道板的第二栓钉;支撑钢带沿底座板的长度方向延伸;轨道板支设于两条支撑钢带的顶端,且通过第二栓钉与对应设置的支撑钢带连接成整体。
10.进一步地,预制装配式钢结构为钢箱结构,钢箱结构包括沿底座板的宽度方向平行间隔设置的两条支撑钢箱、沿支撑钢箱的长度方向依次间隔连接于支撑钢箱内的节点立柱、及用于连接支撑钢箱和轨道板的第三栓钉;支撑钢箱沿底座板的长度方向延伸;轨道板支设于两条支撑钢箱的顶端,且通过第三栓钉与对应设置的支撑钢箱连接成整体。
11.进一步地,自调平扣锚系统对应各节点立柱设置,包括预埋于底座板内的集成系统底座、栓锚调平锚杆、及螺纹连接于栓锚调平锚杆外圆上的第一调节螺圈和第二扣件;栓锚调平锚杆的下端与集成系统底座固定,栓锚调平锚杆的上端依次穿设对应设置的节点立柱和轨道板后伸出;第一调节螺圈位于预制装配式钢结构和底座板之间,且预制装配式钢结构支撑于第一调节螺圈上;第二扣件通过栓锚调平锚杆压紧固定于轨道板的上表面上。
12.进一步地,自调平扣锚系统包括对应每个节点立柱设置的栓锚系统和自调平系统;栓锚系统包括固定设置于对应设置的节点立柱内的栓锚系统底座、栓锚螺旋锚杆、及螺纹连接于栓锚螺旋锚杆外圆上的第三扣件,栓锚螺旋锚杆的下端与栓锚系统底座固定,栓锚螺旋锚杆的上端依次穿设节点立柱和轨道板后伸出,第三扣件通过栓锚螺旋锚杆压紧固定于轨道板的上表面上;自调平系统包括预埋于底座板内的自调平系统底座、自调平螺杆、及螺纹连接于自调平螺杆外圆上的第二调节螺圈,自调平螺杆的下端与自调平系统底座固定,自调平螺杆的上端向上伸入对应设置的节点立柱内,第二调节螺圈位于预制装配式钢结构和底座板之间,且预制装配式钢结构支撑于第二调节螺圈上。
13.进一步地,自调平扣锚系统包括对应不同的节点立柱设置的栓锚系统和自调平系统;栓锚系统包括固定设置于对应设置的节点立柱内的栓锚系统底座、栓锚螺旋锚杆、及螺纹连接于栓锚螺旋锚杆外圆上的第三扣件,栓锚螺旋锚杆的下端与栓锚系统底座固定,栓锚螺旋锚杆的上端依次穿设节点立柱和轨道板后伸出,第三扣件通过栓锚螺旋锚杆压紧固定于轨道板的上表面上;自调平系统包括预埋于底座板内的自调平系统底座、自调平螺杆、及螺纹连接于自调平螺杆外圆上的第二调节螺圈,自调平螺杆的下端与自调平系统底座固定,自调平螺杆的上端向上伸入对应设置的节点立柱内,第二调节螺圈位于预制装配式钢结构和底座板之间,且预制装配式钢结构支撑于第二调节螺圈上。
14.进一步地,自调平扣锚系统包括用于调节的调平螺栓、及用于调平的调平填充层;调平螺栓穿设支撑钢带或支撑钢箱的底部后,旋入底座板内;调平填充层用于调平轨道结构时现场浇筑充填于支撑钢带或支撑钢箱与底座板之间,以用于调平轨道结构。
15.进一步地,自调平扣锚系统包括固定于支撑钢箱底部的调平垫板、垂直连接调平垫板且分设于支撑钢箱两侧的靴套、用于调节的调平螺栓、用于将支撑钢箱与自调平扣锚系统相连的插销、及用于调平的调平填充层;调平螺栓穿设调平垫板后,旋入底座板内;插销穿设支撑钢箱后,其两端再分别插入对应侧的靴套;调平填充层用于调平轨道结构时现场浇筑充填于调平垫板与底座板之间,以用于调平轨道结构。
16.本发明具有以下有益效果:从设计理念上,相比现有技术中混凝土底座和轨道板通过充填于两者之间的充填层而连接成多层复合或者叠合结构,构建本发明的自调平装配式钢
‑
混凝土组合轨道结构时,底座板和预制钢
‑
混凝土轨道单元两者通过预埋的自调平扣锚系统连接固定成整体结构,整体结构协调工作性能稳定,整体传力路径清晰、明确,进而轨道结构服役期间稳定性好、使用寿命长,能长期保持轨道结构品质,实现了多层复合/叠合结构到整体协同工作的转变。
17.从建造技术上,相比现有技术中的充填层现浇成型,本发明的自调平装配式钢
‑
混凝土组合轨道结构中,由于取消了充填层,不仅相互作用的界面减少,而且现场湿作业工作量相对减少很多,材料浪费少、质量稳定性好、建造成本较低,且不易引起施工质量隐患,
钢
‑
混凝土组合轨道单元标准化设计、工厂化生产、智能化安装,实现了充填层现浇成型到预制装配智能化建造的转变。
18.从平顺控制上,相比现有技术中通过现场施工浇筑充填层来控制轨道结构的整体平顺性,本发明的自调平装配式钢
‑
混凝土组合轨道结构结构中,通过自调平扣锚系统即可调节对预制钢
‑
混凝土轨道单元的平顺性,进而根据安装环境自适应调节轨道结构整体的平顺性,而自调平扣锚系统的调节操作简单,精度控制容易,并预制钢
‑
混凝土轨道单元和自调平扣锚系统均可由工厂预制,制作精度高,且还可以根据底座板的实际浇筑情形,适应性调节预制钢
‑
混凝土轨道单元以弥补底座板的浇筑缺陷;另一方面,本发明的自调平系统可根据运营环境和支撑结构变形进行阶段性调节,可调整量大,进而适应下部支撑结构和环境能力强,特别适应于在大跨度桥梁等大变形支撑结构上铺设,而且结构自重轻、刚度大,可有效改善下部支撑结构受力状态。
19.从养护维修上,本发明的预制钢
‑
混凝土组合结构轨道单元和底座板两者通过自调平扣锚系统连接固定成可拆卸式的整体结构,该整体结构相比现有结构的界面减少,实际运营过程中病害较少,而且整体结构连接固定简单、容易拆装维护,故而本发明的预制钢
‑
混凝土组合结构轨道单元养护、维修简单,更换简单,维修费用低,维修所需周期短,工人的劳动强度低。
20.除了上面所描述的目的、特征和优点之外,本发明还有其它的目的、特征和优点。下面将参照图,对本发明作进一步详细的说明。
附图说明
21.构成本技术的一部分的附图用来提供对本发明的进一步理解,本发明的示意性实施例及其说明用于解释本发明,并不构成对本发明的不当限定。在附图中:图1是本发明优选实施例的自调平装配式钢
‑
混凝土组合轨道结构第一实施例三维结构示意图;图2是图1中钢桁架的三维结构示意图;图3是图1中自调平扣锚系统第一实施例的三维分解示意图;图4是图1中钢桁架的另一三维结构示意图;图5是图1中自调平扣锚系统第二实施例的三维分解示意图;图6是图1中自调平装配式钢
‑
混凝土组合轨道结构构建于路基上的三维结构示意图;图7是图1中自调平装配式钢
‑
混凝土组合轨道结构构建于桥梁上的三维结构示意图;图8是图1中自调平装配式钢
‑
混凝土组合轨道结构构建于隧道上的三维结构示意图;图9是本发明优选实施例的自调平装配式钢
‑
混凝土组合轨道结构第二实施例三维结构示意图;图10是图9中工字钢结构的三维结构示意图;图11是本发明优选实施例的自调平装配式钢
‑
混凝土组合轨道结构第三实施例三维结构示意图;
图12是图11中钢箱结构的三维结构示意图;图13是本发明优选实施例的自调平装配式钢
‑
混凝土组合轨道结构第四实施例三维结构示意图;图14是图13的三维分解结构示意图;图15是本发明优选实施例的自调平装配式钢
‑
混凝土组合轨道结构第五实施例三维结构示意图;图16是图15的三维分解结构示意图。
22.图例说明1、钢轨;2、第一扣件组;3、预制钢
‑
混凝土轨道单元;301、承轨台;302、轨道板; 303、钢桁架;3031、第一栓钉;3032、上弦杆;3033、下弦杆;3034、腹杆;3035、节点立柱;3036、填充柱;304、工字钢结构;3041、第二栓钉;3042、上翼缘板;3043、下翼缘板;3044、第一腹板;3045、加劲肋;3046、第一横隔板;305、钢箱结构;3051、第三栓钉;3052、顶板;3053、底板;3054、第二腹板;3055、第二横隔板;4、自调平扣锚系统;401、第二扣件;402、栓锚调平锚杆;403、第一调节螺圈;404、集成系统底座;41、栓锚系统;411、第三扣件;412、栓锚螺旋锚杆;413、栓锚系统底座;42、自调平系统;421、自调平螺杆;422、第二调节螺圈;423、自调平系统底座;424、靴套;425、插销;426、调平螺栓;427、调平垫板;428、调平填充层;5、底座板;6、路基;7、箱梁;8、支座;9、桥墩;10、隧道。
具体实施方式
23.以下结合附图对本发明的实施例进行详细说明,但是本发明可以由下述所限定和覆盖的多种不同方式实施。
24.参照图1、图9、图11,本发明的优选实施例提供了一种自调平装配式钢
‑
混凝土组合轨道结构,包括:现场浇筑成型于支撑基础上的底座板5,底座板5沿列车的运行方向延伸,底座板5上设有沿其长度方向依次间隔设置且由工厂预制的预制钢
‑
混凝土轨道单元3,其上支设有用于对列车进行导向支撑的钢轨1。自调平装配式钢
‑
混凝土组合轨道结构还包括自调平扣锚系统4,自调平扣锚系统4的下端预埋于底座板5中,自调平扣锚系统4的上端穿设预制钢
‑
混凝土轨道单元3后伸出,以用于将底座板5和预制钢
‑
混凝土轨道单元3连接成可拆卸式的整体结构,并对自调平装配式钢
‑
混凝土组合轨道结构进行调平。
25.构建本发明的自调平装配式钢
‑
混凝土组合轨道结构前,首先在工厂预制出预制钢
‑
混凝土轨道单元3的各组成结构,并将各组成结构装配连接形成预制钢
‑
混凝土轨道单元3,同时构建出自调平扣锚系统4;构建本发明的自调平装配式钢
‑
混凝土组合轨道结构时,首先在支撑基础上现场浇筑出沿列车运行方向延伸的底座板5,且浇筑底座板5时,将构建的自调平扣锚系统4的固定端预埋于底座板5内,且使自调平扣锚系统4的连接端向上伸出底座板5;接着再依次将预制钢
‑
混凝土轨道单元3沿底座板5的长度方向依次间隔铺设于底座板5上、将钢轨1铺设并固定于预制钢
‑
混凝土轨道单元3上,并使自调平扣锚系统4的连接端穿设预制钢
‑
混凝土轨道单元3后向上伸出;最后再拧紧自调平扣锚系统4,即可通过自调平扣锚系统4将底座板5和预制钢
‑
混凝土轨道单元3连接固定成可拆卸式的整体结构。
26.从设计理念上,相比现有技术中混凝土底座和轨道板通过充填于两者之间的充填层而连接成多层复合或者叠合结构,构建本发明的自调平装配式钢
‑
混凝土组合轨道结构
时,底座板5和预制钢
‑
混凝土轨道单元3两者通过预埋的自调平扣锚系统4连接固定成整体结构,整体结构协调工作性能稳定,整体传力路径清晰、明确,进而轨道结构服役期间稳定性好、使用寿命长,能长期保持轨道结构品质,实现了多层复合/叠合结构到整体协同工作的转变。
27.从建造技术上,相比现有技术中的充填层现浇成型,本发明的自调平装配式钢
‑
混凝土组合轨道结构中,由于取消了充填层,不仅相互作用的界面减少,而且现场湿作业工作量相对减少很多,材料浪费少、轨道单元精度控制难度小、质量稳定性好、建造成本较低,且不易引起施工质量隐患,钢
‑
混凝土组合轨道单元标准化设计、工厂化生产、智能化安装,实现了充填层现浇成型到预制装配智能化建造的转变。
28.从平顺控制上,相比现有技术中通过现场施工浇筑充填层来控制轨道结构的整体平顺性,本发明的自调平装配式钢
‑
混凝土组合轨道结构结构中,通过自调平扣锚系统4即可调节对预制钢
‑
混凝土轨道单元3的平顺性,进而根据安装环境自适应调节轨道结构整体的平顺性,而自调平扣锚系统4的调节操作简单,精度控制容易,并预制钢
‑
混凝土轨道单元3和自调平扣锚系统4均可由工厂预制,制作精度高,且还可以根据底座板5的实际浇筑情形,调节预制钢
‑
混凝土轨道单元3以弥补底座板5的浇筑缺陷;另一方面,本发明的自调平系统可根据运营环境和支撑结构变形进行阶段性调节,可调整量大,进而适应下部支撑结构和环境能力强,特别适应于在大跨度桥梁等大变形支撑结构上铺设,而且结构自重轻、刚度大,可有效改善下部支撑结构受力状态。
29.从养护维修上,本发明的预制钢
‑
混凝土组合结构单元和底座板5两者通过自调平扣锚系统4连接固定成可拆卸式的整体结构,该整体结构相比现有结构的界面减少,实际运营过程中病害较少,而且整体结构连接固定简单、容易拆装维护,故而本发明的预制钢
‑
混凝土组合结构轨道单元养护、维修简单,更换简单,维修费用低,维修所需周期短,工人的劳动强度低。
30.可选地,如图2、图9和图11所示,预制钢
‑
混凝土轨道单元3包括预制混凝土轨道板302和预制装配式钢结构,且两者通过预制装配式钢结构内的栓钉连接组成整体结构,预制钢
‑
混凝土轨道单元3还包括用于对钢轨1进行安装和支撑的承轨台301。预制装配式钢结构沿底座板5的长度方向布设,轨道板302支撑于预制装配式钢结构上,且与预制装配式钢结构预制成整体。自调平扣锚系统4的下端预埋于底座板5内,自调平扣锚系统4的上端依次穿设预制装配式钢结构和轨道板302后伸出,以用于将底座板5、预制装配式钢结构、及轨道板302连接成可拆卸式的整体结构。承轨台301沿轨道板302的长度方向依次间隔设置于轨道板302的上表面上,钢轨1支撑于承轨台301上,并通过连接于承轨台301的第一扣件组2固定。本可选方案中,预制钢
‑
混凝土轨道单元3包括在工厂预制成型为一体的轨道板302和预制装配式钢结构,相比于全浇筑式的轨道板结构,本发明的预制钢
‑
混凝土轨道单元3的结构自重小,可节省材料,经济性好,且便于后期与底座板5的装配。
31.本可选方案中,轨道板302和承轨台301由工厂预制成型,加工简单,制作精度高。第一扣件组2的数量为两组,两组第一扣件组2分设于钢轨1的两侧;每组第一扣件组2包括用于扣紧钢轨的螺旋道钉和平垫圈、用于防止螺旋道钉安装后转动的弹条、用于扣紧钢轨下端边缘的绝缘块、用于顶抵钢轨1和承轨台301内凹槽的轨距挡板、轨下垫板、铁垫板、铁垫板下弹性垫板、铁垫板下调高垫板和预埋套管,螺旋道钉穿设轨下垫板、铁垫板、铁垫板
下弹性垫板、铁垫板下调高垫板后拧入对应的承轨台301的预埋套管内,通过绝缘块与弹条扣紧钢轨;第一扣件为市场上常用的扣件。
32.本可选方案中,预制装配式钢结构的第一实施例,如图2所示,预制装配式钢结构为钢桁架303,钢桁架303包括多根竖直间隔设置的节点立柱3035、连接于相邻两根节点立柱3035之间的连接栏、及用于连接钢桁架303和轨道板302的第一栓钉3031。轨道板302支设于钢桁架303的顶端,且通过第一栓钉3031与钢桁架303连接成整体。本可选方案的具体实施例中,如图2所示,多根节点立柱3035沿预制装配式钢结构的长度方向呈两列布设,每列包括依次间隔设置的多根节点立柱3035;连接栏包括连接相邻两根节点立柱3035的上弦杆3032、平行上弦杆3032设置且连接相邻两根节点立柱3035的下弦杆3033、及倾斜布设且两端分别连接相邻两根节点立柱3035的多根腹杆3034;第一栓钉3031的上端预埋于上方的轨道板302内,第一栓钉3031的下端穿设对应的上弦杆3032后与上弦杆3032螺纹连接,以实现预制装配式钢结构与对应的轨道板302可拆卸式连接固定,本发明的预制钢
‑
混凝土轨道单元3结构简单、容易制备,且整体连接、拆卸操作简单,整体结构稳定,可靠性强。
33.本可选方案中,预制装配式钢结构的第二实施例,如图10所示,预制装配式钢结构为工字钢结构304,工字钢结构304包括沿底座板5的宽度方向平行间隔设置的两条支撑钢带、沿支撑钢带的长度方向依次间隔连接于支撑钢带上的节点立柱(图未示)、连接于两条支撑钢带之间的第一横隔板3046、及用于连接支撑钢带和轨道板302的第二栓钉3041。支撑钢带沿底座板5的长度方向延伸。轨道板302支设于两条支撑钢带的顶端,且通过第二栓钉3041与对应设置的支撑钢带连接成整体。本可选方案中,如图10所示,各支撑钢带包括沿底座板5的长度方向延伸的上翼缘板3042、与上翼缘板3042平行间隔布设的下翼缘板3043、垂直连接于上翼缘板3042和下翼缘板3043之间的第一腹板3044、及连接上翼缘板3042、下翼缘板3043、及第一腹板3044的多块加劲肋3045;第一横隔板3046的两端分别垂直连接两条支撑钢带的两块第一腹板3044;第二栓钉3041的上端预埋于上方的轨道板302内,第二栓钉3041的下端穿设对应的上翼缘板3042后与上翼缘板3042螺纹连接,以实现预制装配式钢结构与对应的轨道板302可拆卸式连接固定,本发明的预制钢
‑
混凝土轨道单元3结构简单、容易制备,且整体连接、拆卸操作简单,整体结构稳定,可靠性强。
34.本可选方案中,预制装配式钢结构的第三实施例,如图12所示,预制装配式钢结构为钢箱结构305,钢箱结构305包括沿底座板5的宽度方向平行间隔设置的两条支撑钢箱、沿支撑钢箱的长度方向依次间隔连接于支撑钢箱内的节点立柱(图未示)、及用于连接支撑钢箱和轨道板302的第三栓钉3051。支撑钢箱沿底座板5的长度方向延伸。轨道板302支设于两条支撑钢箱的顶端,且通过第三栓钉3051与对应设置的支撑钢箱连接成整体。本可选方案中,如图12所示,各支撑钢箱包括沿底座板5的长度方向延伸的顶板3052、与顶板3052平行间隔布设的底板3053、及垂直连接顶板3052和底板3053的两块第二腹板3054;第二横隔板3055垂直连接于相邻两块第二腹板3054之间;顶板3052的数量为两块,两块第二腹板3054分别连接对应设置的一块顶板3052;第三栓钉3051的上端预埋于上方的轨道板302内,第三栓钉3051的下端穿设对应的顶板3052后与顶板3052螺纹连接,以实现预制装配式钢结构与对应的轨道板302可拆卸式连接固定,本发明的预制钢
‑
混凝土轨道单元3结构简单、容易制备,且整体连接、拆卸操作简单,整体结构稳定,可靠性强。
35.可选地,预制装配式钢结构的上述第一、第二、及第三实施例中,预制装配式钢结
构均连接有自调平扣锚系统4,而自调平扣锚系统4又具有自调平扣锚系统4的第一具体实施例、自调平扣锚系统4的第二具体实施例、及自调平扣锚系统4的第三具体实施例等三个不同的实施例。优选地,如图3所示,预制装配式钢结构的上述第一、第二、及第三实施例中,预制装配式钢结构还包括填充于节点立柱3035内的填充柱3036。自调平扣锚系统4穿设填充柱3036设置。填充柱3036为采用聚氨酯类、环氧类、环氧改性聚氨酯、聚氨酯改性环氧类材料中的至少一种制备形成的柔性填充柱,用于使自调平扣锚系统4与对应的节点立柱间形成柔性连接,减振缓冲,防止自调平扣锚系统4与节点立柱间钢性碰撞,进而提高自调平扣锚系统4和预制装配式钢结构的使用寿命和服役安全性。
36.本可选方案中,自调平扣锚系统4的第一具体实施例,如图2和图3所示,自调平扣锚系统4对应各节点立柱3035设置,包括预埋于底座板5内的集成系统底座404、栓锚调平锚杆402、及螺纹连接于栓锚调平锚杆402外圆上的第一调节螺圈403和第二扣件401。栓锚调平锚杆402的下端与集成系统底座404固定,栓锚调平锚杆402的上端依次穿设对应设置的节点立柱3035和轨道板302后伸出。第一调节螺圈403位于预制装配式钢结构和底座板5之间,且预制装配式钢结构支撑于第一调节螺圈403上。第二扣件401通过栓锚调平锚杆402压紧固定于轨道板302的上表面上。本可选方案的具体实施例中,第二扣件401为市场上常用的扣件。本发明的自调平扣锚系统4的第一具体实施例中,通过栓锚调平锚杆402和第二扣件401将底座板5、预制装配式钢结构、及对应的轨道板302三者连接固定成可拆卸式的整体结构,三者连接操作简单,结构稳定、可靠;另一方面,通过调节第一调节螺圈403相对栓锚调平锚杆402的位置,调节预制钢
‑
混凝土轨道单元3的高度,进而调节组合轨道的整体高度及平顺性,调节操作简单、容易实施,环境适应性强。优选地,还可采用穿设于栓锚调平锚杆402外圆上的垫片代替第一调节螺圈403,使预制装配式钢结构支撑于垫片上,并通过增减不同厚度的垫片进而适应性调节组合轨道整体的高度和平顺性,调节操作简单、容易实施,环境适应性强。
37.本可选方案中,自调平扣锚系统4的第二具体实施例,图未示,自调平扣锚系统4包括对应每个节点立柱设置的栓锚系统41和自调平系统42,即每个节点立柱内均设有栓锚系统41和自调平系统42。栓锚系统41包括固定设置于对应设置的节点立柱内的栓锚系统底座413、栓锚螺旋锚杆412、及螺纹连接于栓锚螺旋锚杆412外圆上的第三扣件411,栓锚螺旋锚杆412的下端与栓锚系统底座413固定,栓锚螺旋锚杆412的上端依次穿设节点立柱和轨道板302后伸出,第三扣件411通过栓锚螺旋锚杆412压紧固定于轨道板302的上表面上。自调平系统42包括预埋于底座板5内的自调平系统底座423、自调平螺杆421、及螺纹连接于自调平螺杆421外圆上的第二调节螺圈422,自调平螺杆421的下端与自调平系统底座423固定,自调平螺杆421的上端向上伸入对应设置的节点立柱内,第二调节螺圈422位于预制装配式钢结构和底座板5之间,且预制装配式钢结构支撑于第二调节螺圈422上。本可选方案的具体实施例中,第三扣件411为市场上常用的扣件。本发明的自调平扣锚系统4的第二具体实施例中,通过自调平系统底座423及自调平螺杆421将底座板5和预制装配式钢结构连接成整体,还通过栓锚系统底座413、栓锚螺旋锚杆412、及第三扣件411将预制装配式钢结构和对应的轨道板302连接成可拆卸式的整体结构,进而通过栓锚系统41和自调平系统42将底座板5和预制钢
‑
混凝土轨道单元3两者连接固定成可拆卸式的整体结构,连接操作简单,结构稳定、可靠;另一方面,通过调节第二调节螺圈422相对自调平螺杆421的位置,调节预制
钢
‑
混凝土轨道单元3的高度,进而调节组合轨道的整体高度及平顺性,调节操作简单、容易实施,环境适应性强。优选地,还可采用穿设于自调平螺杆421外圆上的垫片代替第二调节螺圈422,使预制装配式钢结构支撑于垫片上,并通过增减不同厚度的垫片进而适应性调节组合轨道整体的高度和平顺性,调节操作简单、容易实施,环境适应性强。
38.本可选方案中,自调平扣锚系统4的第三具体实施例,如图4和图5所示,自调平扣锚系统4包括对应不同的节点立柱设置的栓锚系统41和自调平系统42,即预制钢
‑
混凝土轨道单元3的多根节点立柱中,部分设有栓锚系统41,其余部分设有自调平系统42。栓锚系统41包括固定设置于对应设置的节点立柱内的栓锚系统底座413、栓锚螺旋锚杆412、及螺纹连接于栓锚螺旋锚杆412外圆上的第三扣件411,栓锚螺旋锚杆412的下端与栓锚系统底座413固定,栓锚螺旋锚杆412的上端依次穿设节点立柱和轨道板302后伸出,第三扣件411通过栓锚螺旋锚杆412压紧固定于轨道板302的上表面上。自调平系统42包括预埋于底座板5内的自调平系统底座423、自调平螺杆421、及螺纹连接于自调平螺杆421外圆上的第二调节螺圈422,自调平螺杆421的下端与自调平系统底座423固定,自调平螺杆421的上端向上伸入对应设置的节点立柱内,第二调节螺圈422位于预制装配式钢结构和底座板5之间,且预制装配式钢结构支撑于第二调节螺圈422上。本可选方案的具体实施例中,第三扣件411为市场上常用的扣件。本发明的自调平扣锚系统4的第三具体实施例中,通过设置于部分节点立柱中的自调平系统底座423及自调平螺杆421将底座板5和预制装配式钢结构连接成整体,还通过设置于另一部分节点立柱中的栓锚系统底座413、栓锚螺旋锚杆412、及第三扣件411将预制装配式钢结构和对应的轨道板302连接成可拆卸式的整体结构,进而通过栓锚系统41和自调平系统42将底座板5和预制钢
‑
混凝土轨道单元3两者连接固定成可拆卸式的整体结构,连接操作简单,结构稳定、可靠;另一方面,通过调节第二调节螺圈422相对自调平螺杆421的位置,调节预制钢
‑
混凝土轨道单元3的高度,进而调节组合轨道的整体高度及平顺性,调节操作简单、容易实施,环境适应性强。优选地,还可采用穿设于自调平螺杆421外圆上的垫片代替第二调节螺圈422,使预制装配式钢结构支撑于垫片上,并通过增减不同厚度的垫片进而适应性调节组合轨道整体的高度和平顺性,调节操作简单、容易实施,环境适应性强。
39.本可选方案中,自调平扣锚系统4的第四具体实施例,如图13和图14所示,自调平扣锚系统4包括用于调节的调平螺栓426、及用于调平的调平填充层428;调平螺栓426穿设支撑钢带或支撑钢箱的底部后,旋入底座板5内;调平填充层428用于调平轨道结构时现场浇筑充填于支撑钢带或支撑钢箱与底座板5之间,以用于调平轨道结构。本可选方案的具体实施例中,支撑钢箱的底板3053较宽且支撑钢带的下翼缘板3043较宽,调平螺栓426的数量为多个,多个调平螺栓426沿支撑钢箱或支撑钢带的长度方向依次间隔布设,且分设于支撑钢箱或支撑钢带主体结构的两侧。调节操作时,首先根据需要调节的量相应拧动对应位置处的调平螺栓426,使组合轨道顶面平顺性达到要求,然后再在支撑钢带或支撑钢箱的底部现场浇筑混凝土,以形成调平填充层428,从而完成组合轨道顶面平顺性的调节操作,调节操作简单、环境适应性强。
40.本可选方案中,自调平扣锚系统4的第五具体实施例,如图15和图16所示,自调平扣锚系统4包括固定于支撑钢箱底部的调平垫板427、垂直连接调平垫板427且分设于支撑钢箱两侧的靴套424、用于调节的调平螺栓426、用于将支撑钢箱与自调平扣锚系统4相连的
插销425、及用于调平的调平填充层428;调平螺栓426穿设调平垫板427后,旋入底座板5内;插销425穿设支撑钢箱后,其两端再分别插入对应侧的靴套424;调平填充层428用于调平轨道结构时现场浇筑充填于调平垫板427与底座板5之间,以用于调平轨道结构。调节操作时,首先取下插销425,使支撑钢箱与自调平扣锚系统4分离,然后再根据需要调节的量相应拧动对应位置处的调平螺栓426,使组合轨道顶面平顺性达到要求,接着再在支撑钢箱的底部现场浇筑混凝土,以形成调平填充层428,然后再将预制钢
‑
混凝土轨道单元3向下装入靴套424之间的位置,最后在相应位置处插入插销425,从而完成组合轨道顶面平顺性的调节操作,调节操作简单、环境适应性强。
41.可选地,如图6
‑
图8所示,底座板5用于支撑预制钢
‑
混凝土轨道单元3,并用于在浇筑形成过程中通过对其高度和平顺性的精确控制,进而精确控制自调平装配式钢
‑
混凝土组合轨道结构的高度和平顺性。本可选方案中,如底座板5现场浇筑形成于铁路的路基6上,如图6所示,或者底座板5现场浇筑形成于桥墩9上支座8的箱梁7上,如图7所示,或者底座板5现场浇筑形成于隧道10的基础上,如图8所示,底座板5的可设置范围广,适应性强。底座板5用于支撑预制钢
‑
混凝土轨道单元3,并用于在浇筑形成过程中通过对其高度和平顺性的精确控制,进而精确控制自调平装配式钢
‑
混凝土组合轨道结构的高度和平顺性。实际施工时,采用进口摊铺机施工,并用机器视觉测量控制基层标高,同时加强沉降观测,以所观测得到的数据分析、预测路基稳定情况,为减少标高及厚度控制的误差,可采用每8m~10m一个断面,每个断面上依次间隔设置多个点测量;施工中标高测点较多时,标高比较和厚度计算工作量大,可采用电子计算机进行,将底座板的设置高程、各测点的实测标高以制成数据文件,通过编制的数据处理程序计算各测点标高与设计高程的差值,各测点处的厚度,各段落的厚度平均值、均方差、代表值,以此指导下一次的调整和控制。
42.或者,根据装配式轨道底座板位形高精确建造要求,综合考虑施工实效、可实施性及底座板精度可达性,研究装配式轨道底座板智能化建造装备技术,可包括如下技术模块:1)底座板混凝土浇筑技术:通过固定式和移动式混凝土搅拌站技术优势和可行性比较研究,给出混凝土原材料供给系统、原料拌和浇筑系统的构成模式,提出底座板混凝土浇筑工艺流程的实现技术及装备;2)智能化空间位形精密控制技术:通过比选融合惯性导航系统、全球定位导航系统(gps、北斗)、视觉测量系统、三维激光扫描系统等,给出适用于装配式轨道结构底座板位形精密测量与智能控制技术;3)塑形定型技术:通过底座板塑形成型技术、空间位形挤压调整技术、顶面刨磨平整技术的可行性,给出相应的施工技术及装备,形成具有自适应性的智能化底座板塑形定型技术;4)智能控制系统:通过集成底座板混凝土浇筑技术、智能化空间位形精密控制技术、塑形定型技术,给出装配式轨道底座板智能化建造装备技术的中央控制系统,实现底座板建造全过程的感知识别、精确测量、智能决策、反馈调整,满足底座板空间位形精确定型要求。
43.以上所述仅为本发明的优选实施例而已,并不用于限制本发明,对于本领域的技术人员来说,本发明可以有各种更改和变化。凡在本发明的精神和原则之内,所作的任何修改、等同替换、改进等,均应包含在本发明的保护范围之内。
再多了解一些
本文用于企业家、创业者技术爱好者查询,结果仅供参考。