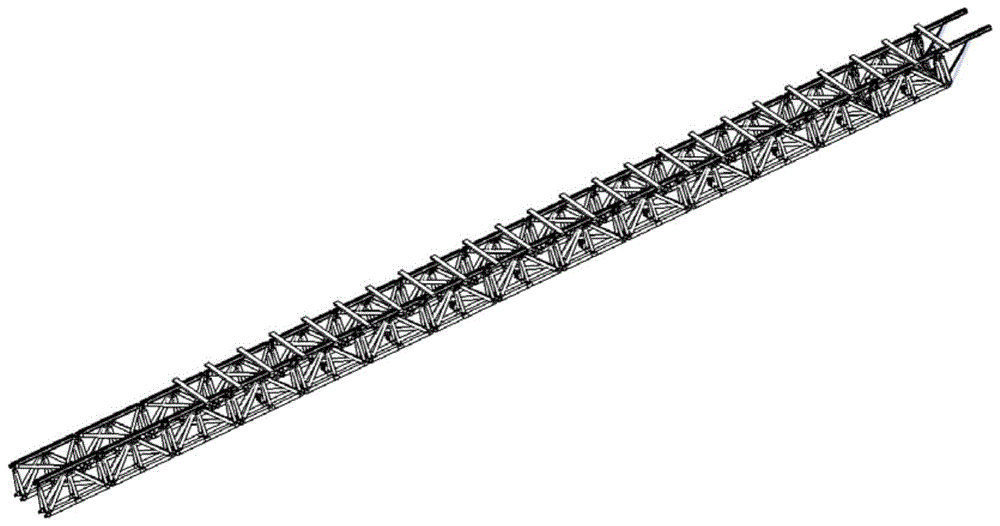
本发明属于桥梁工程技术领域,具体为一种大跨度纤维增强复合材料抢修梁架设方 法。
背景技术
对于大跨度纤维增强复合材料抢修梁来说(例如92m大跨度抢修桥梁),架设时具 有较多的要求:一是无法采用全机械化作业,需要采用人工辅助机械架设;二是作业场 地仅为70米,不到全桥长度的80%;三是架设时间有限制,对于92m大跨度抢修桥梁 架设时间不能超过8小时。同时大跨度纤维增强复合材料抢修梁还具有如下特点:(1) 抢修梁跨度大,高度高,架设器具要求高,人工架设作业难度大,必然需要人工辅助机 械架设,8小时的架设时间需要合理安排;(2)单跨主梁重量轻,可分可结,一方面有 利于人工分解架设,另一方面整体性差,架设稳定性差,也不利于快速化架设;(3)下 部弦杆为复合材料结构,不利于下部滚轮推送,因此需要对下部输送装置进行设计;(4) 张弦尺寸长,重量大,占据空间高达5米,安装与张紧难度大。
目前常用的应急救援桥梁架设方案主要有导梁悬臂推送法、悬挂式架设方法、跨骑 式架设方法。
导梁悬臂推送法常规方法是在主梁(例如装配式公路钢桥和重型桁架桥)的端部固 定较为轻便的导梁,将主梁和导梁同时平推至沟壑对岸,继续平推将主梁推送到预定位 置,见图1。通常,在架设时需要长度略小于主梁的导梁,导梁拼接时间较短,但是, 由于架设大跨桥梁时需要较大平衡力或平衡力臂,对场地与车辆要求均较高,因此,该 方法一般用于小跨度军用桥梁,如国内常见的84式机械化桥等,难以应用于大跨度应 急桥梁架设工程中。
悬挂式架设方法,是将导梁固定于主梁顶部,升高导梁,将导梁推送于沟壑两端后, 再将主梁利用悬挂于导梁底部的方式推送到沟壑对岸,见图2。悬挂式架设方法需要两 岸有可靠锚固点,在军用桥梁上应用较少,如我国73式轻便钢桥,其承载能力小,且 还需要到对岸进行锚固作业,因此应用范围狭窄。
跨骑式架设方法,是先将导梁固定于主梁内部(例如中国重型支援桥和瑞典FB48 快速桥)利用主梁的重量控制导梁不倾翻,将导梁推送至沟壑对岸,再利用导梁控制主 梁不倾翻,将主梁推送至沟壑对岸,见图3。跨骑式架设方法成了大跨度应急救援桥的 主要选择。
随着技术的发展,轻型的、高强度的纤维增强复合材料得到了广泛的应用,特别是 由于纤维增强复合材料质量轻、拆装方便,特别适用于应急救援桥梁工程中,纤维增强 复合材料之间也需要金属连接件进行连接。纤维增强复合材料的主梁和导梁之间的连接 也仅仅能在与主梁的金属连接件和导梁之间进行,因此也给跨骑式架设方法带来新的不 便。导梁与主梁之间需要导轨及小轮,小轮间距过大,导梁与主梁刚度不一致会影响推 送平顺性;导梁到位后需要将导梁支撑于地面,高度过大,与下部横联干涉;需要配套 机械化架设装备。此外,当导梁行进至接近主梁端部时,导梁的压力仅仅存在于仅有的 几个连接件上,极易造成连接件损坏,导致无法顺利架设。
技术实现要素:
为了达到上述目的,本发明提供了一种大跨度纤维增强复合材料抢修梁架设方法。
实现上述目的的技术方案如下:
一种大跨度纤维增强复合材料抢修梁架设方法,包括以下步骤:
步骤(1):利用纤维增强复合材料和连接件拼装主梁;
步骤(2):在主梁的横梁上安装用于对导梁限位的限位框,限位框内侧安装多个用 于滑动导梁的滚轮;
步骤(3):利用纤维增强复合材料和连接件拼装导梁,边拼接导梁边将导梁推送至 主梁内部;
步骤(4):安装主梁的桥面板和水平联系杆;
步骤(5):将主梁临时锚固于待架设的沟壑一端的地面,保持主梁不动;将导梁向 前整体推送,使导梁后段和主梁前段形成一段重合段,将导梁和主梁临时固接,在导梁 和主梁重合段前端利用千斤顶将导梁顶升;
步骤(6):向前推送主梁至前端导梁落地,继续向前推送主梁至主梁端部至预设位 置,用千斤顶顶起主梁,拆卸导梁,取出千斤顶使主梁落地。
进一步的,所述步骤(1)利用纤维增强复合材料和连接件拼装主梁具体位:在地 面利用纤维增强复合材料和连接件拼装一对主梁,并在一对主梁之间安装用于连接主梁 的中间横梁,形成大跨度纤维增强复合材料主梁。
进一步的,步骤(3)中的导梁的长度为主梁长度的70-80%,导梁的纵截面为倒置 的梯形。
进一步的,所述限位框纵截面的形状为与导梁的纵截面形状相配合的倒置的梯形;
限位框框上与导梁腰的位置相匹配的区域设置一对上限位轮和一对下限位轮,限位 框的底部设置横梁滚轮,用于推动导梁在限位框内滑动。
进一步的,所述重合段的长度为导梁长度的15-20%。
进一步的,步骤(5)中,在导梁和主梁重合段的前端和后端,使用U型箍将导梁 锁死在主梁上。
进一步的,步骤(1)中拼装主梁时,将处于折叠状态的张弦机构平行安装到主梁下 弦底部,和主梁一起进行推送;在步骤(6)主梁落地后,远程控制张弦机构使其处于 菱形展开状态,使得张弦张紧。
与现有技术相比,本发明的有益效果如下:
本发明提供的大跨度纤维增强复合材料抢修梁架设方法,通过将导梁内嵌于两片主 梁之间,从主梁内部推送导梁,导梁快到对岸时,将主梁与导梁固结,整体推送过去无 需拼接超过主梁的导梁,大大节约了场地,同时整个架设过程导梁和主梁连接部位足够 多,避免局部受力过大,保证了架设的安全性。
本发明提供的大跨度纤维增强复合材料抢修梁架设方法,通过设置带有上下限位轮 的限位框,且在横梁上设置横梁辊轮,使得导梁沿主梁的推送更加快捷方便,提高了工 作效率。
附图说明
图1为导梁悬臂推送法的工艺图,其中a为推送起始阶段,b为推送至快到预设位 置阶段。
图2为悬挂式架设方法的工艺图,其中a为推送起始阶段,b为推送至快到预设位 置阶段。
图3为跨骑式架设方法的工艺图,其中a为推送起始阶段,b为推送至快到预设位 置阶段。
图4为大跨度纤维增强复合材料的主梁基本结构图。
图5为在中间横梁的限位框内侧安装多个用于滑动导梁的滚轮示意图。
图6为边拼接导梁边将导梁推送至主梁内部示意图。
图7为安装大跨度纤维增强复合材料的主梁的桥面板和水平联系杆示意图。
图8为将导梁向前整体推送示意图。
图9为在导梁和主梁重合段前端利用千斤顶将导梁顶升示意图。
图10为在导梁和主梁重合段的前端和后端锁死导梁示意图。
图11为继续向前推送主梁至主梁端部至预设位置示意图。
图12为重型导梁结构示意图。
图13为轻型导梁结构示意图。
图14为成桥状态结构示意图。
附图标记说明:
1-上限位轮,2-限位框,3-横梁,4-下限位轮,5-横梁辊轮,6-导梁,7-桥面板,8- 水平联系杆,9-千斤顶,10-垫块,11-前端U型箍,12-后端U型箍,13-主梁,14-张弦 机构。
具体实施方式
下面以92m大跨度纤维增强复合材料抢修梁为例,说明本发明大跨度纤维增强复合 材料抢修梁架设方法,包括以下步骤:
(1)在地面利用纤维增强复合材料和连接件拼装一对主梁13,并在一对主梁13之 间安装用于连接主梁13的中间横梁3,形成大跨度纤维增强复合材料的主梁基本结构, 主梁13底部设置有多个用于滚动主梁的滚轮,见图4;
(2)在中间横梁3上安装用于对导梁限位的限位框2,限位框2内侧安装多个用于 滑动导梁的滚轮,包括上限位轮1、下限位轮4和横梁辊轮5,见图5;单个轮子采用直 径D55mm-D100mm轴承,两个轮径采用D300mm,轮宽用100mm;
(3)在地面上利用纤维增强复合材料和连接件拼装导,6,边拼接导梁边将导梁6推 送至主梁13内部,见图6;导梁6的长度为72米;
(4)安装大跨度纤维增强复合材料的主梁13的桥面板7和水平联系杆8,见图7;
(5)将主梁13临时锚固于待架设的沟壑一端的附近地面,保持主梁13不动;将导 梁6向前整体推送60米,使导梁6和主梁13重合段长度为10米,见图8;推送可采用 绞盘或人工推送,初始推送力大小约为0.25吨,最终推送力大小约为2.4T吨;在导梁 6和主梁13重合段前端利用千斤顶9将导梁顶升,抬起导梁20cm,同时在前端横梁3 与导梁6之间塞入垫块10,见图9,然后将导梁6和主梁13重合段的前端和后端锁死 导梁6,见图10;
(6)向前推送主梁13至前端导梁6落地,继续向前推送主梁13使主梁前端边桥节 落至对岸预定位置,见图11,用千斤顶顶起主梁13,拆卸导梁6,取出千斤顶9使主梁 13落地。
下面再以图12和图13两种导梁结构计算导梁受力情况。导梁结构设计:主要是大 悬臂下根部控制断面内力状态、悬臂换简支的内力状态转换,主梁13与导梁6简支状 态下不断前移的内力状态。在以上多种结构状态下的最不利内力进行导梁构型与构件设 计。
图12为一种重型导梁(上宽为1.4M,下宽0.5M,高2.4M),该导梁使用的材料属性 参数见下表。
图13为一种轻型导梁(上宽为0.9M,下宽0.5M,高1.2M),该导梁使用的材料属性 参数见下表。
以上所述实施例仅表达了本发明的几种实施方式,其描述较为具体和详细,但并不 能因此而理解为对发明专利范围的限制。应当指出的是,对于本领域的普通技术人员来 说,在不脱离本发明构思的前提下,还可以做出若干变形和改进,这些都属于本发明的 保护范围。因此,本发明专利的保护范围应以所附权利要求为准。
本文用于企业家、创业者技术爱好者查询,结果仅供参考。