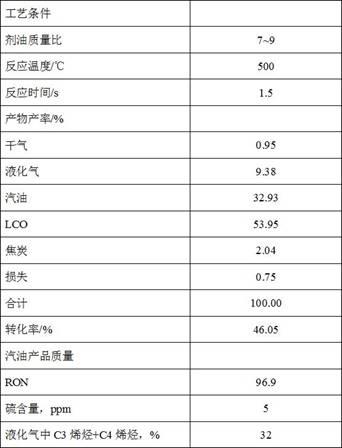
1.本发明涉及一种催化裂化方法,具体地说涉及一种富产高辛烷值汽油的催化裂化方法,本发明还涉及一种加氢裂化-催化裂化组合工艺,所述组合工艺能够高效处理催化裂化柴油。
背景技术:
2.流化催化裂化是以减压蜡油、焦化蜡油、常压渣油等为原料,在裂化催化剂存在下,主要生成汽油、柴油、液化气等产品。根据催化裂化的操作条件、催化剂、目的产物分布的不同,催化裂化的操作状态可以有多种。目前炼厂常用的催化裂化操作,以减压蜡油、焦化蜡油、常压渣油、减压渣油为原料,以稀土y型沸石、稀土氢y型沸石、稀土超稳y 型沸石或超稳y型沸石为催化剂的活性组分,在温度470~515℃、表压为 0.07~0.2兆帕、催化剂与原料烃的重量比为3~6的条件下反应,主要生产汽油和柴油。
3.近几年来,我国成品油消费结构发生巨大变化,消费柴汽比不断降低,导致催化裂化柴油(lco)的加工路线产生改变。lco在我国柴油调和组分中占比较高,具有芳烃含量高、十六烷值低以及硫、氮含量高等特点,性质相对较差,成为炼厂主要的低附加值油品。
4.目前,对催化裂化柴油二次加工仍以加氢方式为主,通过对催化柴油中杂质脱除、芳烃饱和以及开环转化等方式生产柴油调和组分或高辛烷值汽油、轻芳烃等,将催化柴油转化为高附加值汽油调和组分和清洁柴油,成为炼厂生产清洁油品、降低柴汽比的有效途径。
5.催化裂化柴油的芳烃含量较高,可达70%~85%,其中双环及双环以上芳烃含量占总芳烃含量的60%~70%。如何高效合理地将催化柴油中富含的低附加值芳烃加氢转化为高价值产品,成为催化柴油改质的难点所在。
6.以脱硫为主要目的的催化柴油加氢精制技术是以催化柴油或催化柴油与直馏柴油、焦化柴油混合油为原料,在常规柴油加氢精制反应条件下脱除原料中硫、氮等杂质,生产清洁柴油产品。该方法可以实现催化柴油深度脱硫,但十六烷值提升幅度有限,其中的高芳烃组分也未能得到充分利用。传统加氢裂化技术虽然可以将催化柴油裂化为汽油馏分和高十六烷值柴油馏分,但氢耗量大,成本高,不具有市场竞争优势。最大量提高催化柴油十六烷值的加氢改质技术,在柴油馏分收率较高(一般在95%以上)条件下,可有效提高催化柴油十六烷值,十六烷值增幅可达8~15个单位,但对于十六烷值极低(一般20以下)的催化裂化柴油等劣质柴油馏分原料来说,仍无法满足柴油调和组分的质量要求。中压加氢改质技术是在中压条件下,催化柴油适度裂化(柴油收率约为80wt%),兼顾实现脱硫、脱氮、十六烷值提升,但该过程对原料要求苛刻。
7.催化柴油加氢转化技术是近年来应用较为广泛的技术,通过控制有限饱和及深度的加氢裂化,将催化裂化柴油中双环、三环芳烃组分选择性裂化为单环芳烃,以生产汽油馏分为主要目标,尽量减少柴油产量,生产高辛烷值汽油调和组分或是优质的芳烃等高价值产品。但为了多获得生产汽油馏分的目标,反应选择性变差,氢耗上升,能耗较高,液体产品
收率下降,价值较低的小分子烷烃产量较高,高成本的氢气较多转移到了低价值的小分子饱和烷烃分子中和辛烷值相对较低的汽油馏分直链烷烃中。
8.将lco先进行加氢精制,再作为fcc装置进料,生产高辛烷值汽油或调和组分,是经常采用的技术路线。us5944982a公开了fcc工艺和加氢工艺的组合工艺,其中fcc工艺采用的是双提升管工艺,重质原料经过fcc装置第一提升管反应后,分离出相对较轻的组分和较重的组分,较轻组分(重石脑油和lco)经过加氢处理后,加氢产物回炼到第二提升管进行裂化反应。us5152883a公开了一种lco、回炼油以及澄清油经过加氢再回炼到fcc装置生产高辛烷值汽油的方法。该方法为重油经过fcc装置后,将fcc产物中lco、回炼油以及澄清油进行分离,经加氢装置处理后,再将大于221℃以上的馏分分离出来,然后回炼到fcc装置来生产高辛烷值汽油。cn101760239a公布了一种催化裂化柴油的利用方法。该方法先将催化裂化柴油分离成小于230℃的组分、沸点在230-310℃之间的组分和大于310℃的组分,然后对沸点在230-310℃之间的组分和大于310℃的组分分别在不同的加氢深度下进行加氢,再把两种加氢产物进分馏塔分离出富含单环芳烃的柴油,然后与之前小于230℃的组分混合送至催化裂化,从而生产芳烃或高辛烷值汽油。cn103805247a公开了一种加工劣质柴油的组合工艺方法。该方法将劣质柴油首先进行加氢改质反应;反应流出物分离所得液体进行芳烃抽提;芳烃组分送至催化裂化生产高辛烷值汽油,链烷烃及饱和烃调和到柴油馏分中。cn106753551a公开了一种利用催化裂化柴油生产高辛烷值汽油的方法,包括以下步骤:将催化裂化柴油加氢精制后分离为小于280℃的馏分和大于280℃的馏分,将大于280℃的馏分进行芳烃抽提,得到富含芳烃的抽出油和富含烷烃的抽余油;将所述小于280℃的馏分及所述富含烷烃的抽余油进行催化裂化得到富含芳烃的高辛烷值汽油;所述富含芳烃的抽出油进行芳烃利用。
9.综上所述,现有技术中在裂化催化剂存在下以生成汽油、低碳烯烃等产品为目标的催化裂化工艺主要以减压蜡油、焦化蜡油、常压渣油、加氢精制柴油等为原料。将催化裂化柴油进行选择性加氢饱和,然后再返回催化裂化装置进行裂化反应,生成汽油和液化气,最大化降低柴汽比是普遍应用的技术。虽然经过加氢精制后的催化裂化柴油可裂化性能大幅度提高,但是催化裂化柴油在加氢精制过程中,大量双环芳烃生成茚萘及四氢萘类等含有环烷环的芳烃类化合物,含有环烷环的芳烃类化合物是供氢剂类化合物,在催化裂化反应过程中会发生明显的供氢反应,一方面导致茚萘类及四氢萘类化合物脱氢转化成双环芳烃,导致反应转化率下降结焦量上升;另一方面,供氢剂对汽油的关键质量指标辛烷值和液化气产品中高价值的烯烃含量均有明显影响,为避免该问题,刘天波在《炼油技术与工程》第49卷第12期p34-39中介绍采用独立的催化裂化反应器加以解决,但仍不能从根本上解决问题,含有大量供氢剂的加氢柴油本身在催化裂化反应中,仍存在大量不利的氢转移反应,造成高辛烷值组份烯烃含量相对较低,低辛烷值组份直链烷烃含量相对较高,焦炭生成量偏高,需要外排一部分低价值的油浆。
技术实现要素:
10.针对现有的不足,本发明提供一种催化裂化方法,所述方法能够提高催化裂化汽油的收率及液化气中烯烃的含量;本发明还提供一种加氢裂化-催化裂化组合工艺,所述组合工艺能够高效处理催化裂化柴油,生成高收率的汽油和高烯烃含量的液化气产品。
11.本发明的第一个方面是提供一种催化裂化方法,包括如下内容:催化裂化原料进入催化裂化提升管反应器,与催化裂化催化剂接触进行裂化反应,催化裂化生成油进入分馏单元分离出液化气、汽油和催化裂化柴油;所述催化裂化原料中含有质量含量为20%-100%的加氢裂化柴油馏分,优选质量含量为50%-100%的加氢裂化柴油馏分,进一步优选所述催化裂化原料为加氢裂化柴油馏分,所述加氢裂化柴油馏分的十六烷值为22-55,优选为25-50,进一步优选为30-48,单环芳烃质量含量不低于18%,优选为20-60%,进一步优选为25-50%。
12.上述催化裂化方法中,所述加氢裂化柴油中链烷烃质量含量18-50%、优选20~45%,进一步优选25~40%。
13.上述催化裂化方法中,加氢裂化柴油的初馏点控制在165~250℃之间,优选为175~230℃之间,但因为蒸馏装置精度的问题,实际值与控制值会有所偏离。
14.上述催化裂化方法中,催化裂化原料中进一步含有渣油、蜡油、加氢精制柴油中的一种或几种。
15.上述催化裂化方法中,所述催化裂化反应条件如下:反应温度500-600℃、剂油重量比5-10、接触时间1.0s-4.0s、转化率控制40-90%。
16.上述催化裂化方法中,所述催化裂化反应采用的催化剂可以采用市售商品或者按照现有技术制备。所采用的催化裂化催化剂包括通常用于催化裂化的催化剂,如硅铝催化剂、硅镁催化剂、酸处理白土及x型、y型、zsm、beita等,优选采用开环能力更好的y型分子筛催化剂。
17.上述催化裂化方法中,所述加氢裂化柴油可以采用如下方法制备:加氢裂化原料油通过加氢预处理反应区、加氢裂化反应区进行反应,反应产物经过分离出液化气、汽油产品后获得加氢裂化柴油。
18.上述加氢裂化方法中,所述加氢裂化原料油具有如下性质:芳烃质量含量为60~95%,优选65~80%;其中双环以上芳烃质量含量40~65%,优选45~55%;所述加氢裂化原料可以来源于催化裂化柴油馏分、煤焦油柴油馏分、页岩油柴油馏分中的一种或几种,优选为催化裂化柴油馏分。
19.上述催化裂化方法中,所述的加氢预处理反应区、加氢裂化反应区可以设置在同一个加氢反应器内,也可以分别设置在两个以上的加氢反应器内,优选分别设置在两个加氢反应器内。
20.上述催化裂化方法中,所述的加氢预处理反应区装填加氢精制催化剂进行加氢脱硫、加氢脱氮或芳烃饱和等反应,所述加氢精制催化剂以vib族和/或第viii族金属为活性组分,以氧化铝或含硅氧化铝为载体。第vib族金属一般为mo和/或w,第viii族金属一般为co和/或ni。以催化剂的重量为基准,第vib族金属含量以氧化物计为8wt%~28wt%,第viii族金属含量以氧化物计为2wt%~15wt%。
21.上述催化裂化方法中,所述的加氢预处理反应区操作条件如下:反应温度300-420 ℃、反应压力5-13mpa、体积空速0.5-5.0h-1
、氢油体积比500-2000。
22.上述催化裂化方法中,所述的加氢裂化反应区装填加氢裂化催化剂进行加氢裂化反应,所述加氢裂化催化剂一般含有裂化组分和金属组分,所述裂化组分可使用y、beita等类型分子筛中的一种分子筛或几种,优选使用y分子筛,金属组分为vib族和/或第viii族金
属,加氢裂化催化剂中除上述金属组分、裂化组分外,还可以包括氧化铝、无定型硅铝等组分。
23.上述催化裂化方法中,所述的加氢裂化反应区操作条件如下:反应温度300-450℃、反应压力5.0mpa-13.0mpa、体积空速0.5-5.0h-1
、氢油体积比500-2000。
24.上述催化裂化方法中,所述加氢裂化反应区上部装填的加氢裂化催化剂以mo-ni为加氢活性金属组分、反应器下部装填的加氢裂化催化剂以mo-co为加氢活性金属组分,上下部两种加氢裂化催化剂体积比为1:1~5:1;进一步优选采用fd2g催化柴油生产高辛烷值汽油的加氢裂化工艺专用加氢裂化催化剂fc-70a、fc-70b或fc-24b催化剂(上述催化剂为中国石化催化剂有限公司生产)。
25.上述催化裂化方法中,所述加氢裂化反应区优选的操作条件如下:反应压力6.0-10.0mpa;反应温度370-400℃;体积空速1.0-2.0;氢油体积比700-1500。
26.本发明的第二个方面是提供一种加氢裂化-催化裂化组合工艺,包括如下步骤:(1)加氢裂化原料油通过加氢预处理反应区、加氢裂化反应区进行反应,反应产物经过分离得到液化气、汽油馏分、加氢裂化柴油馏分,所述加氢裂化柴油馏分的十六烷值为22-55,优选为25-50,进一步优选为30-48,单环芳烃质量含量不低于18%,优选为20-60%,进一步优选为25-50%;(2)含有20wt%-100wt%步骤(1)获得的加氢裂化柴油馏分的催化裂化原料进入催化裂化反应器,优选含有70wt%-100wt%步骤(1)获得的加氢裂化柴油馏分的催化裂化原料进入催化裂化反应器,与催化裂化催化剂接触进行反应,催化裂化生成油进入分馏单元分离出液化气、汽油和催化裂化柴油。
27.上述组合工艺中,所述加氢裂化原料油具有如下性质:芳烃质量含量60~95%,优选65~80%,十六烷值一般为30以下,优选20以下;其中双环以上芳烃质量含量40~65%,优选45~55%。所述加氢裂化原料可以来源于催化裂化柴油馏分、煤焦油柴油馏分、页岩油柴油馏分等含有芳烃含量较多的原料中的一种或几种。通过加氢裂化,将柴油馏分十六烷值提升8以上,优选提升10以上,通常为10~20。
28.上述组合工艺中,步骤(1)通过温度、压力等条件的控制,使反应后加氢裂化柴油馏分中具有较高的单环芳烃,同时具有适宜的十六烷值。一般情况下,控制相对低的压力和相对高的反应温度,有利于获得上述结果。
29.上述组合工艺中,步骤(1)中所述的加氢预处理反应区、加氢裂化反应区可以设置在同一个加氢反应器内,也可以分别设置在两个以上的加氢反应器内,优选分别设置在两个加氢反应器内。
30.上述组合工艺中,步骤(1)中所述的加氢预处理反应区装填加氢精制催化剂进行加氢脱硫、加氢脱氮或芳烃部分饱和等反应,所述加氢精制催化剂以vib族和/或第viii族金属为活性组分,以氧化铝或含硅氧化铝为载体。第vib族金属一般为mo和/或w,第viii族金属一般为co和/或ni。以催化剂的重量为基准,第vib族金属含量以氧化物计为8wt%~28wt%,第viii族金属含量以氧化物计为2wt%~15wt%。
31.上述组合工艺中,步骤(1)中所述的加氢预处理反应区操作条件如下:反应温度300-420 ℃、反应压力5-13mpa、体积空速0.5-3.0h-1
、氢油体积比500-2000。
32.上述组合工艺中,步骤(1)中所述的加氢裂化反应区装填加氢裂化催化剂进行加
氢裂化反应,所述加氢裂化催化剂一般含有裂化组分和金属组分,所述裂化组分可使用y、beita等类型分子筛中的一种分子筛或几种,优选使用y分子筛,金属组分为vib族和/或第viii族金属,加氢裂化催化剂中除上述金属组分、裂化组分外,还可以包括氧化铝、无定型硅铝等组分。
33.上述组合工艺中,步骤(1)中所述的加氢裂化反应区操作条件如下:反应温度300-450℃、反应压力5.0mpa-13.0mpa、体积空速0.5-3.0h-1
、氢油体积比500-2000。
34.上述组合工艺中,步骤(1)中所述加氢裂化反应区上部装填的加氢裂化催化剂以mo-ni为加氢活性金属组分、反应器下部装填的加氢裂化催化剂以mo-co为加氢活性金属组分,上下部两种加氢裂化催化剂体积比为1:1~5:1。
35.上述组合工艺中,步骤(1)中所述加氢裂化反应区优选的操作条件如下:反应压力6.0-10.0mpa;反应温度370-400℃;体积空速1.0-2.0;氢油体积比700-1500。
36.上述组合工艺中,所述加氢裂化柴油中链烷烃质量含量18-50%、优选20~45%,进一步优选25~40%。
37.上述组合工艺中,步骤(2)中步骤(1)获得的加氢裂化柴油单独或者同其它物料混合后进入催化裂化提升管反应器,所述其它原料为渣油、蜡油、加氢精制柴油中的一种或几种。
38.上述组合工艺中,步骤(2)中步骤(1)获得的加氢裂化柴油进入催化裂化提升管反应器,与催化裂化催化剂接触进行裂化反应,催化裂化生成油进入分馏单元分离出液化气、汽油和催化裂化柴油。
39.上述组合工艺中,步骤(2)中所述催化裂化柴油可以部分或全循环回步骤(1)的加氢预处理反应区及加氢裂化反应区。
40.上述组合工艺中,步骤(2)中所述催化裂化反应条件如下:反应温度500-600℃、剂油重量比5-10、接触时间1.0s-4.0s、转化率控制40-90%。
41.上述组合工艺中,步骤(2)所述催化裂化反应采用的催化剂可以采用市售商品或者按照现有技术制备。所采用的催化裂化催化剂包括通常用于催化裂化的催化剂,如硅铝催化剂、硅镁催化剂、酸处理白土及x型、y型、zsm、beita等,优选采用开环能力更好的y型分子筛催化剂。
42.上述组合工艺中,步骤(2)中催化裂化反应器可以设置为单提升管催化裂化反应器,也可以设置为多提升管催化裂化反应器,优选为双提升管催化裂化反应器,进一步优选双提升管催化裂化反应器分别加工含有加氢裂化柴油的原料和其它不含有加氢裂化柴油的重质原料,例如蜡油、渣油中的一种。
43.上述组合工艺中,所述加氢裂化使用含有y分子筛的加氢裂化催化剂;所述催化裂化使用含有y分子筛的催化裂化催化剂。
44.上述组合工艺中,所述加氢裂化转化率控制在10%~60%,优选20%~50%;催化裂化转化率控制在20%~90%,优选30%~70%。
45.本技术通过大量研究发现,以双环及以上芳烃为主要组成的催化裂化柴油等劣质柴油,在保持单环芳烃含量较高的同时,大幅度提高十六烷值后,对催化裂化反应特别有利,主要表现为催化裂化汽油的收率增加、辛烷值提升、液化气中高价值的烯烃含量增加等。柴油十六烷值是表征柴油燃料在柴油机中的易燃性指标,与在催化裂化装置中的裂化
性能为不同的原理,但通过优化十六烷值和单环芳烃等指标,使催化裂化性能获得显著提升。其原理可能在于,通过提高十六烷值,改变了分子结构,避免了供氢剂结构类物质过多对催化裂化反应过程的影响。
46.本发明采用催化柴油加氢裂化 催化裂化联合加工方案设计,催化柴油原料首先进入催化柴油加氢裂化装置定向改变分子结构(柴油馏分中保留较多单环芳烃,同时大幅度提高十六烷值),未转化油作为催化裂化装置进料,实现在催化裂化单元的可控、深度转化,减少非目标的氢转移副反应,多产高质量汽油和富含烯烃液化气高价值产品,根据全厂供氢及催化加工负荷情况,可灵活调整催化柴油加氢裂化装置转化深度,控制未转化油产量和氢气用量,进而提高生产灵活性。
47.相比现有加氢精制 催化裂化联合加工方案设置,本发明加氢裂化 催化裂化联合单元操作中,加氢裂化单元对于催化柴油可裂解性能的改善效果更为明显,经催化柴油加氢裂化装置加工后的未转化油在催化裂化单元裂化难度相比经加氢精制单元加氢后的加氢催化柴油显著下降,相同催化裂化条件下转化率更高,低价值的油浆和焦炭产量更低,本发明方案基本不产生外排油浆(最先进的现有技术也需外排油浆2%以上),焦炭产量也是最先进现有技术的50%左右。也就是说,本发明方案可以大大提高催化裂化单元的单程转化率,减少未转化油的循环量,相当于提高了装置的处理能量。而相比于加氢精制装置对于催化柴油无转化功能,催化柴油加氢裂化装置也可以裂化一部分催化柴油,这样在本发明工艺中催化柴油的裂化转化由加氢和催化两套单元共同承担,使得在催化柴油转化深度相比加氢精制 催化裂化联合加工方案更高,转化效率大幅增加,而转化效率的增加带来明显的益处就是本发明方案催化柴油单位转化率氢耗相比现有技术显著降低。
48.此外,传统的催化柴油加氢裂化技术为了保障汽油产品辛烷值,需要控制反应压力,通常在中低压下操作更为合适,而本发明由于两套装置的联合使用,催化裂化汽油高辛烷值的特点,使得催化柴油加氢裂化单元可以在更高的操作压力下转化,然后通过加氢汽油与催化汽油的调和来满足汽油产品辛烷值大于90的要求,同时,由于催化柴油加氢裂化压力的提高进一步改善了未转化油质量,使得其裂解性能更好。相比于常规加氢精制过程,催化柴油加氢裂化过程相同条件下脱硫效果更好,使得催化裂化进料硫含量更低,也使得本发明生产的汽油硫含量更低。
49.本发明采用催柴加氢裂化 催化裂化联合加工方案设计,催化柴油的裂化转化任务由两个单元共同分担,加工催化柴油时,具有氢耗低、转化深度高、生产方案灵活性大和汽油产品质量好的优点,当采用单独加工方式时,可生产硫含量小于10ppm,辛烷值大于90的高辛烷值、国六汽油调和组分。同时,加氢单元得到的汽油和催化裂化单元得到的汽油虽然宏观上都具有高辛烷值特点,但组成不完全相同,特别是烯烃和异构烷烃的含量不同,可以对全厂汽油进行综合调节。
50.具体实施方式
51.下面结合实施例及比较例进一步说明本发明方法的作用和效果,但以下实施例不构成对本发明方法的限制,本发明上下文中%如无具体说明均为质量百分数。
52.本发明实施例及比较例中原料油及加氢裂化柴油烃类组成分析(芳烃、双环以上
芳烃等)均采用中间馏分烃类组成的测定质谱法(nb/sh/t 0606-2019)测定,十六烷值测定采用标准号gbt386-2010方法测定,所述液化气中的c3烯烃、c4烯烃采用液化石油气组成的测定气相色谱法(nb/sh/t 0230-2019)方法测定。
53.本发明实施例及比较例中,所述的质谱组成以链烷烃、环烷烃、芳烃的质量含量为100%计,所述的化学氢耗为反应消耗氢气质量除以反应原料质量*100%,所述的转化率为(1-未转化柴油质量除以柴油原料质量)*100%(每套装置的转化率以其进料量为基准,两套装置总转化率以加氢裂化装置总进料量为基准,如果有循环进料总进料量包括循环进料),所述的加氢单元单位催化柴油转化率氢耗为化学氢耗除以加氢单元转化率,所述单环芳烃质量含量、双环及以上芳烃含量均以芳烃的总质量计,所述的液化气中c3烯烃 c4烯烃的质量含量指的是催化裂化反应生成的液化气。
54.本发明实施例及比较例中,所采用的ff-36加氢精制催化剂、fc-70a加氢裂化催化剂、fc-70b加氢裂化催化剂、fc-32加氢裂化催化剂、ricc-1催化裂化催化剂、dfc-1加氢裂化催化剂催化剂生产厂家均为中国石化催化剂有限公司。
55.实施例1催化柴油原料油经管线与经管线引入的氢气进入加氢精制反应器反应,加氢精制反应生成油经管线进入加氢裂化反应器进行裂化反应,加氢裂化反应器反应生成油经管线进入高压分离器进行气、液分离,分离得到的氢气经管线循环回加氢精制反应器,液相经管线进入低压分离器,分离出轻烃组分经管线排出,剩余组分经管线进入分馏塔分馏,分馏得到的液化气和汽油组分分别经管线抽出,加氢柴油经管线进入催化裂化反应器提升管反应,催化裂化生成油经管线进入催化裂化产品分馏塔,分离出液化气和汽油产品分别经管线抽出,柴油部分经管线抽出,部分经管线循环回加氢精制反应器。
56.加氢精制催化剂采用工业牌号催化剂ff-36催化剂,裂化催化剂fc-70a和fc-70b催化剂级配使用,fc-70a/fc-70b级配比例3:1;催化裂化催化剂使用工业牌号ricc-1催化剂。
57.表1为原料油性质,表2为加氢裂化柴油性质,表3、表4为加氢段和催化段操作条件及反应结果,表5为加氢单元与催化单元合计催化柴油转化率、混合汽油产品辛烷值。
58.表1
表2表3
表4表5
实施例2催化柴油原料油与氢气混合进入加氢精制反应器反应,精制反应生成油进入加氢裂化反应器反应,裂化反应生成油进入高压分离器,分离得到的氢气循环回精制反应器,液相流入低压分离器,低压分离器分离得到的低分气排出;液相进入催化裂化提升管反应器;催化裂化生成油进入催化裂化产品分馏塔,分馏得到的液化气和汽油产品抽出,柴油部分抽出;部分循环回加氢精制反应器。
59.加氢精制催化剂采用工业牌号催化剂ff-36催化剂,裂化催化剂采用fc-70a和fc-70b催化剂级配使用,fc-70a/fc-70b级配比例3:1;催化裂化催化剂使用工业牌号dfc-1催化剂。
60.表6为原料油性质,表7为加氢裂化柴油性质,表8、表9为加氢段和催化段操作条件及反应结果,表10为加氢单元与催化单元合计催化柴油转化率、混合汽油产品辛烷值。
61.表6表7
表8表9
表10实施例3催化裂化柴油原料油与氢气混合进入加氢精制反应器反应,反应生成油进入加氢裂化反应器反应,裂化反应生成油进入高压分离器进行气液分离,分离得到的氢气循环回加氢精制反应器入口,分离得到的液相进入低压分离器,分离得到的气相经管线外排,液相经进入加氢产物分馏塔,分馏得到的液化气和汽油分别经过管线抽出,加氢柴油进入fdfcc装置双提升管中的一个提升管反应,反应生成油进入催化裂化单元分馏塔;另一股蜡油进料进入fdfcc装置双提升管中另外一个提升管反应,反应生成油进入催化裂化单元分馏塔。在分馏塔内完成产品分离,液化气、汽油由管线抽出;柴油部分由管线抽出;部分循环回加氢精制反应器管线。
62.加氢精制催化剂采用工业牌号催化剂ff-36催化剂,裂化催化剂采用fc-70a和fc-70b催化剂级配使用,fc-70a/fc-70b级配比例1:1;加氢柴油进料提升管内催化剂使用工业牌号dfc-1催化剂、蜡油进料提升管内使用工业牌号ricc-1催化剂。
63.表11为原料油性质,表12为加氢裂化柴油性质,表13、表14为加氢段和催化段操作条件及反应结果,表15为加氢单元与催化单元合计催化柴油转化率、混合汽油产品辛烷值。
64.表11表12表13
表14
表15实施例4采用实施例1工艺流程,与实施例1不同之处在于催化裂化分馏塔柴油全部循环回精制反应器。实施例4加氢精制催化剂与实施例1相同\加氢裂化催化剂使用常规加氢裂化催化剂fc-32,催化裂化催化剂使用工业牌号dfc-1催化剂。
65.表16为原料油性质,表17为加氢裂化柴油性质,表18、表19为加氢段和催化段段操作条件及反应结果,表20为加氢单元与催化单元合计催化柴油转化率、混合汽油产品辛烷值。
66.表16
表17表18
表19
表20实施例5催化柴油原料油经管线与经管线引入的氢气进入加氢精制反应器反应,加氢精制反应生成油经管线进入加氢裂化反应器进行裂化反应,加氢裂化反应器反应生成油经管线进入高压分离器进行气、液分离,分离得到的氢气经管线循环氢回加氢精制反应器,液相经管线进入低压分离器,分离出轻烃组分经管线排出,剩余组分经管线进入分馏塔分馏,分馏得到的液化气和汽油组分分别经管线抽出,加氢柴油经管线进入催化裂化反应器提升管反应,催化裂化生成油经管线进入催化裂化产品分馏塔,分离出液化气和汽油产品分别经管线抽出,柴油部分经管线抽出,部分经管线循环回加氢精制反应器。
67.加氢精制催化剂采用工业牌号催化剂ff-36催化剂,裂化剂fc-70a和fc-70b催化
剂级配使用,fc-70a/fc-70b级配比例3:1;催化裂化催化剂使用工业牌号ricc-1催化剂。
68.表21为原料油性质,表22为加氢裂化柴油性质,表23、表24为加氢段和催化段操作条件及反应结果,表25为加氢单元与催化单元合计催化柴油转化率、混合汽油产品辛烷值。
69.表21表22表23
表24表25
实施例6催化裂化柴油原料油与氢气混合进入加氢精制反应器反应,反应生成油进入加氢裂化反应器反应,裂化反应生成油进入高压分离器进行气液分离,分离得到的氢气循环回加氢精制反应器入口,分离得到的液相进入低压分离器,分离得到的气相经管线外排,液相经进入加氢产物分馏塔,分馏得到的液化气和汽油分别经过管线抽出,加氢柴油与蜡油原料一起进入fcc装置反应,反应生成油进入催化裂化单元分馏塔。在分馏塔内完成产品分离,液化气、汽油由管线抽出;柴油部分由管线抽出。
70.加氢精制催化剂采用工业牌号催化剂ff-36催化剂,裂化催化剂采用fc-70a和fc-70b催化剂级配使用,fc-70a/fc-70b级配比例1:1;催化裂化催化剂使用工业牌号ricc-1催化剂。
71.表26为原料油性质,表27为加氢裂化柴油性质,表28、表29为加氢段和催化段操作条件及反应结果,表30为加氢单元与催化单元合计催化柴油转化率、混合汽油产品辛烷值。
72.表26表27
表28表29
表30比较例1采用常规的加氢精制-催化裂化工艺,加氢精制催化剂及催化裂化催化剂与实施例1采用催化剂相同。
73.表31为反应原料、表32为加氢精制生成油性制,表33、表34为加氢精制和催化裂化反应器工艺条件及反应结果。
74.表31
表32表33
表34本发明工艺可实现较低氢耗下催化柴油的深度裂化转化,同时,汽油产品具有硫含量
低、辛烷值高的特点。相同氢气消耗下,催化柴油裂化转化深度相比现有技术提高5%以上,单位转化率氢耗降低0.005以上,以催化柴油处理量100万吨/年,催化柴油转化率60%计算,年节约氢气使用费用4200万。
再多了解一些
本文用于企业家、创业者技术爱好者查询,结果仅供参考。