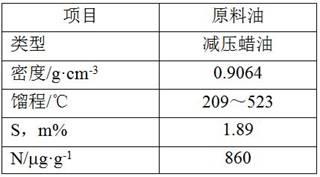
1.本发明涉及一种加氢裂化装置引氢的方法,具体地说涉及一种催化剂床层温度超温或者飞温后引氢的方法。
背景技术:
2.加氢裂化工艺是在临氢、高温、高压条件和催化剂的作用下,使重馏分油(vgo、cgo、dao)加氢脱硫、加氢脱氮、多环芳烃加氢饱和及开环裂化,转化为轻油和中间馏分油等目的产品的过程。其使用的催化剂在加氢领域比较特殊,除了含有加氢金属组分以外,还含有硅铝载体,且随着其结果或者硅铝比的差异,催化剂本身具有酸性功能,即裂化功能。
3.由于酸性功能的存在,加氢裂化装置在生产运行过程中的风险较高,最常见且最危险的就是超温或者飞温情况的出现。造成上述问题出现的原因很多,如原料性质变化,加热炉出口温度波动,循环氢量降低或者循环氢压缩机停机、冷氢量减少等。在工业实际生产中一般来说,加氢裂化(或加氢改质)类装置难免会遇到以上的问题,一旦问题出现,轻者需要进行工艺条件的调整或者计划停工,此时催化剂床层温度也会存在一定程度的波动,重者需要进行紧急停工处理,此时催化剂床层温度一般均会高于正常生产温度较多。紧急停工是为了保护催化剂或者其它设备的安全等在严重事态下进行的停工手段,一般的采用紧急卸压手段将装置内含有的氢气分子在短时间内大量排出,切断关键反应物之一的氢气,既能降低事故持续发生的几率,又可以最大限度的保护催化剂等关键单元。
4.对于紧急停工的介绍,可参考如下内容:为满足特殊紧急情况的要求,高压加氢装置的反应系统都设有7bar/min和21bar/min的紧急卸压系统。
5.一般的,造成装置紧急停工卸压的原因有:(1)循环氢压缩机停运。循环氢压缩机如果停运,反应系统就失去了从催化剂床层上携带出反应热的能力,反应系统需要紧急卸压处理,以有效的抑制氢气和油继续在反应器内高温条件下反应并放热。
6.(2)催化剂床层温度过高或者超温。若任何一点反应温度超过正常状态28℃或温度超过反应器设计允许的操作温度,装置必须立即启动21bar/min进行紧急卸压放空。
7.(3)设备泄漏或者火灾等意外情况发生。
8.特别需要注意的是,无论采取哪种紧急卸压系统,都应严格掌握一旦开启后,均要将压力一卸到底的原则(即降到0.5mpa以下)。
9.在装置紧急卸压之后,一般采用氮气置换系统后微正压保存的方式等待装置再次开工。
10.在上述超温或者飞温的条件下,由于产生的意外情况不同,一旦装置采取紧急泄压后,由于反应系统内载热体的大量流失。反应器催化剂床层温度会不可控制的上升,其具体的上升程度也不尽相同,但无论上升程度如何,系统内残余的油品在高温、失氢的状态下势必会生成烯烃,此类烯烃在未来开工引氢的过程中一定要加以调整及控制、不然极易造
成催化剂床层的二次超温。
11.cn102443426a介绍了一种加氢裂化工艺的开工活化方法,催化剂硫化效果好,具有更突出的反应效果。中国专利cn103769243a介绍了加氢催化剂的器外预硫化方法,可以提高器外预硫化催化剂的持硫率,并提高催化剂使用性能。但二者未解决在催化剂卸压后引氢时存在的床层温度超高的风险。
12.cn103773436a和cn102443412a介绍了器外预硫化二类活性中心加氢催化剂的开工方法,可以在不影响二类活性中心加氢催化剂使用性能的前提下,更好的利用起催化剂的自身特点,简化开工工艺,降低装置能耗或者有利于催化剂形成更多的二类加氢活性中心,有利于提高催化剂的使用性能,但其核心仍然未提及续开工时引氢温度对于床层飞温风险的影响。
13.cn201610365747.6公开了一种加氢裂化开工方法,具有开工、切换原料及进入稳定生产状态所需时间短,避免开工过程中钝化剂的消耗及注氨过程存在的潜在危险,不仅节约了能耗,而且减少了钝化剂对环境的污染和对人体的危害。对于卸压后引氢的问题仍未提及或者解决。
14.cn103059961a和cn103059969a公开了一种加氢裂化催化剂的开工钝化方法。在催化剂钝化阶段往精制段引入高氮石脑油,通过其加氢生成的氨气作为钝化剂对裂化剂进行钝化,从而达到无需使用钝化剂的目的。虽然可以起到对裂化催化剂钝化杀掉初活性的作用,但是需要额外的引入其他液体组分,且仍然利用氨气对催化剂进行钝化,其钝化的机理是均匀钝化,但不适用于卸压后引氢的条件。
15.cn102921441a介绍了一种磷化钨催化剂的制备方法,其在制备过程中通入氮气流对催化剂进行钝化,虽然在一定程度上可以起到钝化的效果,但是惰性气体的钝化效果很差,是无法应用于加氢裂化过程的,更不要说引氢过程了。
16.cn104593051a和cn104593050a公开了一种硫化型加氢催化剂的开工方法,利用加入的化学物质生成的油膜对硫化型催化剂的放热过程进行钝化,虽然可以彻底的解决硫化过程硫集中释放的热量控制问题,但是无法应用于加氢裂化领域,其生成的油膜在加氢裂化时会反应或者分解,无法起到抑制床层飞温的作用。
17.cn104342200a公开了一种重整生成油选择性加氢的方法,其核心在于利用一些“毒物”对催化剂中的活性金属进行钝化,虽然效果显著,但并不适用于加氢裂化过程对于分子筛的处理以及温度平衡的过程。
技术实现要素:
18.针对现有技术存在的不足,本发明提供一种加氢裂化装置紧急停工后的引氢方法。该方法解决了装置温度波动意外停工后引氢时存在的风险问题,稳定了在续开工过程中加氢裂化催化剂活性的恢复过程,从而在不影响催化剂活性的基础上,缩短了续开工过程的时间。
19.本发明中所述的紧急停工过程通常是指,加氢裂化装置在正常生产过程中出现意外情况导致加氢裂化催化剂床层温度超过正常生产28℃以上后,启动紧急卸压手段释放反应系统内氢气到底(一般低于0.5mpa)后,引入氮气保持系统压力为4~5mpa。
20.本发明的一种加氢裂化装置紧急停工后的引氢方法,包括以下内容:
(1)调整加氢精制反应器入口温度为50~250℃,以一次通过方式(不开循环氢压缩机)向系统内引入氢气,引氢速率为1000~30000nm3/h,同时以一定速率排出系统内存留气相,保持系统压力不上升的前提下对反应系统进行氢气置换;(2)在步骤(1)引氢和排放系统存留氢气的过程中,加氢精制和加氢裂化催化剂床层保持恒温(温度不上升)1~10小时;(3)将加氢精制反应器入口温度提高5~30℃,但不超过250℃,恒温,继续对反应系统进行氢气置换;(4)重复步骤(3)0~3次,优选0~1次;(5)当系统内氮气纯度低于10%时,启动循环氢压缩机,进行后续的升温以及升压操作。
21.进一步,视加氢裂化装置紧急停工时的超温程度以及当前催化剂床层情况(使用的催化剂活性差异),优选设定2~3个恒温阶段。当系统内氮气纯度低于10%时启动循环氢压缩机,进行后续的升温以及升压等常规操作。
22.上述方法中,所述超过正常生产28℃是目前工业中普遍认同的超温标准,其参照物为正常生产时的平稳温度,当催化剂床层温度超过此限制值后,会启动紧急卸压程序,以最快的速度排出系统内的反应物之一——氢气。在此过程中,视意外情况的不同以及催化剂酸性的差异,催化剂床层温度会维持不变或者持续升高,且此过程已经不在可控范围内,其温度波动将一直持续到系统内氢气释放干净为止。加氢裂化装置紧急停工后,反应系统内气体主要为氮气,同时含有少量氢气。此时反应系统的压力一般为4~5mpa,氢分压为0.5mpa以下。
23.上述方法中,所述的加氢裂化装置含有预处理催化剂以及裂化催化剂。加氢裂化预处理催化剂也为本领域常规的加氢裂化预处理催化剂,包括载体和所负载的加氢金属。以催化剂的重量为基准,加氢裂化预处理催化剂通常包括元素周期表中第
ⅵ
b族金属组分,如钨和/或钼以氧化物计为10%~35%,优选为15%~30%;第
ⅷ
族金属如镍和/或钴以氧化物计为1%~7%,优选为1.5%~6%。载体为无机耐熔氧化物,一般选自氧化铝、无定型硅铝、二氧化硅、氧化钛等。其中常规加氢裂化预处理催化剂可以选择现有的各种商业催化剂,例如抚顺石油化工研究院(fripp)研制开发的3936、3996、ff-16、ff-26、ff-36、uds-6等加氢精制催化剂;也可以根据需要按本领域的常识进行制备。
24.所述的加氢裂化催化剂按重量含量计含有10%~30%,优选为15%~25%活性金属氧化物,和45%以上,优选50%~70%的分子筛;活性金属包括wo、mo、co、ni中的一种或几种。所述分子筛包括但不限于y型或usy分子筛。加氢裂化催化剂包括加氢活性金属、分子筛组分和氧化铝载体。加氢裂化催化剂可以选择现有的各种商业催化剂,例如抚顺石油化工研究院(fripp)研制开发的fc-24、fc-46、fc-52等加氢裂化催化剂;也可以根据需要按本领域的常识制备加氢裂化催化剂。
25.上述方法中,所述的紧急卸压手段为本领域常规知识,一般视装置操作压力的不同分为7bar/min和/或21bar/min,为加氢领域技术人员所熟知的技术内容。所述的氢气以及氮气及其二者的浓度要求满足常规知识的认识即可,无特殊限制。
26.上述方法中,所述的根据超温温度,分为四个阶段,分别为超温后催化剂床层高点温度低于400℃,400~600℃,600~800℃,高于800℃。超温过程出现的温度不同,系统内残存的烯烃类型以及含量有所区别,所以对其控制过程既要保证续引氢过程的平稳,又要尽量
的减少停工时间,本专利的适用性才能更好的体现。高点温度越高,所对应的引氢时反应器入口温度越低。原则上可控制在80~250℃,优选100~200℃。
27.上述方法中,根据划分的超温温度,引入氢气后,系统内排出存留气相的速率也存在差异,对应的高点温度(高点温度即加氢裂化装置超温后催化剂床层热点温度)越低,所排出气相以及引入氢气的的速率越低,一般可维持在1000~30000nm3/h,优选5000~20000nm3/h。系统内残留气相的排出方式不做限制,可以利用装置现有流程的放空系统排放,必要时可根据采用启动紧急放空手段来排除系统内的反应热量(残留油品中烯烃反应释放的热量即通过引氢及排放气相的一次通过流通方式进行排出)。
28.上述方法中,根据划分的超温温度,引入氢气后,系统内由于残存烯烃浓度及类型的差异,其反应温度以及释放的热量也有所区别,对应的高点温度越低,其反应过程释放的热量越少,故对于本方法引氢过程的风险越低,所以对应的恒温阶段可适当减少,一般的可根据实际情况设定0~5个升温后的恒温阶段,优选1~4个恒温阶段。
29.本发明所述的氮气纯度低于10%时启动循环氢压缩机,此处为体积分数。在此条件下,循环气分子量变化幅度很小,不会对循环氢量造成影响,启动循环氢压缩机更加安全可靠,可以在实现平稳引氢的同时最大限度的降低对于关键设备的损耗。气体采样口可以设在在加氢裂化反应器出口处。
30.本发明中,步骤(5)中所述的后续升温以及升压等操作为本领域技术人员熟知的内容,此时不再累述。
31.本申请在对加氢裂化装置超温停工后的问题进行了深入研究后发现,加氢裂化装置在裂化剂超温后,在缺氢气氛和超高的床层温度下,加氢裂化催化剂有可能发挥了催化裂化催化剂的功能,并表现出较高的热裂解活性,原料油在此条件下发生深度裂解反应,生成较多的烯烃并在裂化催化剂床层中积累和沉积。虽然经历了紧急泄压,但系统中仍然存有较多的烯烃。而在加氢裂化装置再次引氢开工的过程中,按照常规开工方法,直接升温引氢不管温度如何,系统内的气相是不流通的,系统内生成的烯烃与引入的较高含量的氢气发生剧烈的加氢反应,释放出较高的热量,此时循环氢压缩机并未投入使用,因此导致裂化催化剂床层再次超温,而对加氢裂化催化剂造成再次损害。该问题的提出,并非本领域的常规技术问题,而是本申请发明人针对现有技术进行深入剖析而提出的。针对停工后的加氢裂化装置再次引氢开工,发明人提出了上述的技术方案。首先在维持较低的精制反应器入口温度的情况下,以一次通过方式,边往系统引入新氢,边排放系统存量气相,对系统气体进行逐步的置换;针对裂化催化剂超温过程中不同的热点温度,逐渐提高精制反应器的入口温度,并进行恒温置换;直至系统内氮气含量降至10v%以下,方才启动循环氢压缩机,并进行后续的升温及升压操作。
32.与现有技术相,本发明具有以下有益效果:1、针对现有加氢裂化装置运行中出现的超温紧急停工后引氢的安全问题,本发明进行了极大的创新,在保证设备安全的前提下,开创了动态气流携热的独特理念。对于意外停工后的引氢过程做了改动及创新,避免了催化剂床层出现二次超温,一定程度上延长了运行周期。本发明为了解决现有超温后引氢过程的安全性问题,将加氢裂化催化剂床层温度的升高与引氢温度,恒温时间、恒温阶段以及动态流动量进行了关联,在保证过程安全的前提下,减少了续开工过程的时间,其控制参数的合理匹配也是保证催化剂活性稳定的关键手
段。在不影响催化剂活性的基础上完成紧急事故后的续开工过程,降低了后续运转过程中的种种隐患,不仅可以大量的节约人力、物力,同时也提高了加氢裂化装置催化剂运行的稳定性,既降低了操作风险,又可以实现最快速度恢复开工过程的目的。
33.2、在工艺过程中,本发明方法可直接应用于加氢裂化装置的事故过程中,避免额外的投资以及改造工作,稳定了催化剂活性,最大限度的利用装置的现有流程对“事故”裂化催化剂进行后续保护,达到了资源合理利用的目的,同时具有节省能源、工艺流程简单、操作便利、环保低碳等优点。
34.3、本发明方法仅通过工艺参数以及气相动态流动做出了改变,其方法的原则出发点也是对于关键动设备的保护,恢复过程充分,工艺条件适宜,安全性极佳,不会对装置的任何部位产生不利的影响,使得后续生产的过程更精细化及标准化,降低了企业装置操作波动以及操作风险。
具体实施方式
35.下面结合实施例及比较例来进一步说明本发明一种加氢裂化装置停工后的引氢方法的作用及效果。下述实施例及比较例中采用原料油的性质见表1,其中所提及的活性均转化为相同时期以及转化深度下的反应温度,使用的催化剂主要物化性质见表2,实施例及比较例中均含有加氢裂化预处理(加氢精制)过程,没有特殊提及时,所述的超温过程均指加氢裂化段。
36.表1 原料油主要性质表2 催化剂主要性质
实施例1当加氢裂化装置生产过程中出现了意外事故,导致催化剂床层温度升高,被迫采取了紧急卸压手段,该过程中催化剂床层温度最高升至395℃。压力一卸到底后引入氮气保持系统压力为4.3mpa,此后缓慢降低催化剂床层温度,至精制段入口温度为200℃时,向系统内充入氢气,引入速率为5000nm3/h,此时利用放空系统向外排放系统气相,排放速率为5000nm3/h,同时保证在该条件下恒温8小时,待系统内氮气纯度达到9.1%时,启动循环氢压缩机,进行后续的升温升压及原料引入和参数调整等工作。
37.实施例2当加氢裂化装置生产过程中出现了意外事故,导致催化剂床层温度升高,被迫采取了紧急卸压手段,该过程中催化剂床层温度最高升至528℃。压力一卸到底后引入氮气保持系统压力为4.5mpa,此后缓慢降低催化剂床层温度,至精制段入口温度为180℃时,向系统内充入氢气,引入速率为8000nm3/h,此时利用放空系统向外排放系统气相,排放速率为8000nm3/h,同时保证在该条件下恒温8小时,继续提高精制段入口温度至200℃,恒温4小时,待系统内氮气纯度达到9.8%时,启动循环氢压缩机,进行后续的升温升压及原料引入和参数调整等工作。
38.实施例3当加氢裂化装置生产过程中出现了意外事故,导致催化剂床层温度升高,被迫采取了紧急卸压手段,该过程中催化剂床层温度最高升至778℃。压力一卸到底后引入氮气保持系统压力为4.7mpa,此后缓慢降低催化剂床层温度,至精制段入口温度为150℃时,向系统内充入氢气,引入速率为13000nm3/h,此时利用放空系统向外排放系统气相,排放速率为14000nm3/h,同时保证在该条件下恒温8小时,继续提高精制段入口温度至180℃,恒温4小时,继续提高精制段入口温度至200℃,恒温4小时,待系统内氮气纯度达到8.8%时,启动循环氢压缩机,进行后续的升温升压及原料引入和参数调整等工作。
39.实施例4当加氢裂化装置生产过程中出现了意外事故,导致催化剂床层温度升高,被迫采取了紧急卸压手段,该过程中催化剂床层温度最高升至915℃。压力一卸到底后引入氮气保持系统压力为4.9mpa,此后缓慢降低催化剂床层温度,至精制段入口温度为120℃时,向系统内
充入氢气,引入速率为17000nm3/h,此时利用放空系统向外排放系统气相,排放速率为19000nm3/h,同时保证在该条件下恒温8小时,继续提高精制段入口温度至150℃,恒温4小时,继续提高精制段入口温度至180℃,恒温4小时,继续提高精制段入口温度至200℃,恒温4小时,待系统内氮气纯度达到9.2%时,启动循环氢压缩机,进行后续的升温升压及原料引入和参数调整等工作。
40.比较例1加氢裂化装置未出现任何问题,正常生产状态下的工作条件。
41.比较例2当加氢裂化装置生产过程中出现了意外事故,导致催化剂床层温度升高,被迫采取了紧急卸压手段,该过程中催化剂床层温度最高升至895℃。压力一卸到底后引入氮气保持系统压力为4.9mpa,此时精制段入口温度为190℃,向系统内充入氢气,引入速率为13000nm3/h,催化剂床层再度出现超温情况,高点温度达到了508℃,此后降低精制段入口温度为100℃,再进行后续的升温升压及原料引入和参数调整等工作。
42.比较例3当加氢裂化装置生产过程中出现了意外事故,导致催化剂床层温度升高,被迫采取了紧急卸压手段,该过程中催化剂床层温度最高升至971℃。压力一卸到底后引入氮气保持系统压力为5mpa,此后缓慢降低催化剂床层温度,至精制段入口温度为120℃时,向系统内充入氢气,引入速率为16000nm3/h,此时利用放空系统向外排放系统气相,排放速率为18000nm3/h,同时保证在该条件下恒温8小时,继续提高精制段入口温度至150℃,恒温4小时,继续提高精制段入口温度至180℃,恒温4小时,继续提高精制段入口温度至200℃,恒温4小时,待系统内氮气纯度达到62.2%时,启动循环氢压缩机,由于分子量波动导致压缩机停机,修复后再次进行后续的升温升压及原料引入和参数调整等工作。
43.比较例4当加氢裂化装置生产过程中出现了意外事故,导致催化剂床层温度升高,被迫采取了紧急卸压手段,该过程中催化剂床层温度最高升至695℃。压力一卸到底后引入氮气保持系统压力为4.8mpa,此时精制段入口温度为100℃,将氮气压力释放至0.5mpa以下后,向系统内充入氢气,引入速率为13000nm3/h,系统压力升至3.0mpa后,启动循环氢压缩机,逐步提高反应温度并等待系统满足升压要求。而后进行后续的升温升压及原料引入和参数调整等工作。
44.将上述实施例与比较例的效果进行对比,结果见表3。
45.表3*活性为该裂化催化剂达到相同转化深度条件下的反应温度,如不发生超温事故,那么比较例1的温度应为正常数值。
46.以上的实施例及比较例可以看出,该方法的最大特点是,在超温或者飞温意外发生后,后续引氢过程进行了合理的调整,避免了催化剂的二度受损,针对难以预估的意外停工,尤其是对于催化剂长周期运行要求以及设备安全维护较高的的企业而言,利用现有的流程进行引氢工艺技术的优化及改良,由此可以彻底的解决意外发生后的后续平稳开工工作,极大的增强了装置的可操作性、灵活性以及安全性,使得催化剂在后续运转过程中可以最大限度的降低意外发生所造成的影响,对催化剂的活性以及设备的安全进行了合理的保护,节约投资,在人力、物力上都有很大的优势,是一种经济效益显著的“亡羊补牢”式发明方法。
再多了解一些
本文用于企业家、创业者技术爱好者查询,结果仅供参考。