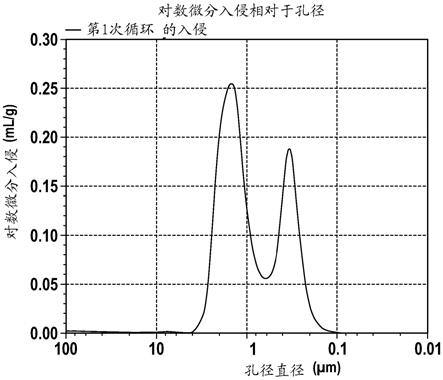
用于制造超导部件的基于铌锡化合物的粉末
1.本发明涉及用于制造超导部件的基于铌锡化合物的粉末,所述铌锡化合物特别是nb
x
sn
y
,其中1≤x≤6并且1≤y≤5,其中该粉末的特征在于高孔隙率,涉及其制造方法以及这种粉末用于制造超导部件的用途。
2.超导体是指在低于特定温度(所谓的转变温度)时其电阻降至零的材料。在超导状态下,材料的内部保持没有电场和磁场,并且无损耗地传输电流。超导体尤其用于产生强的、恒定的磁场或用于制造低损耗变压器,在相同的功率下,它们具有比传统变压器更小的尺寸和质量并因此尤其在移动操作中具有优势。
3.超导体可分为不同的类别如金属超导体、陶瓷超导体和高温超导体。最迟自发现铌锡 (nb3sn) 的转变温度为 18.05 k 以来,铌及其合金已成为用于制造超导体的材料的焦点。因此,由铌制成的超导腔谐振器例如用于粒子加速器(包括在汉堡 desy 或日内瓦cern的 xfel 和 flash)。
4.作为超导部件,超导线材特别令人感兴趣,它们尤其用于制造超导线圈。对于强超导线圈而言,通常需要具有仅几微米厚的导电丝/细丝的千米长的线材,这需要复杂的制造方法。
5.为了制造这种线材,特别是基于铌锡合金的,尤其使用所谓的青铜法,其中使用cu
‑
sn合金作为起始材料。
6.如,ep 0 048 313 描述了基于青铜
‑
nb3sn的超导线材,其可用于高磁场的情况下,并且其特征在于青铜
‑
nb3sn线材中的立方相和具有稳定的在很大程度上防止了四方相的形成和/或减少了四方变形(1
‑
c/a)的合金成分, 所述合金成分来自下组:li be mg sc y u ti zr hf v ta mo re fe ru ni pd zn al ga in tl si ge sb,重量百分比范围为 0.01 至 7,基于线材中 nb 的比例计,和/或 0.05 至 10,基于线材中青铜的比例计。
7.替代地,可以通过所谓的pit(粉末套管)法制造基于铌锡合金的超导线材,在该方法中,将粉末状含锡起始化合物引入到铌管中,然后拉制成线材。在最后一步中,通过热处理在含铌管壳与填入的含锡粉末之间形成超导nb3sn边界层。在此,关于含锡起始化合物,相组成、化学纯度和粒度(其不允许大于成品细丝的直径)是决定性的。
8.t. wong 等人以nbsn2为例,描述了一种pit工艺和含锡起始化合物的制造(t. wong 等人,“ti and ta additions to nb3sn by the powder in tube process”, ieee transactions on applied superconductivity, vol. 11, no. 1 (2001), 3584
‑
3587)。在此,在该方法中不利的是,为使铌与锡令人满意地反应生成 nbsn2,需要一个由研磨和长达48小时的热处理组成的多级工艺。此外,一般性教导是氧含量应尽可能低。
9.us 7,459,030描述了一种通过pit工艺制造超导nb3sn线材的方法,其中使用钽锡合金粉末作为起始化合物。为了制造它,使用了 k2nbf7和k2taf7,它们在与锡反应之前被还原为各自的铌金属和钽金属。然而,所描述的方法的缺点是对于使用这些铌金属和钽金属有一些限制。如,只能使用最大氧含量小于 3000 ppm 和最大氢含量小于 100 ppm 的那些金属。超过所述氧含量导致成品线材的品质下降。在氢值高于 100 ppm 的情况下,在进行该工艺时会出现安全技术问题,因为在温度处理时氢会逸出。此外,所述方法的缺点是,目
标化合物含有高含量的未反应的锡,并且成品线芯还含有含钽化合物,这会对线材的超导性能产生不利影响。此外,在还原起始化合物k2nbf7和k2taf7时形成难溶的金属氟化物,例如 mgf
2 或 caf2,它们不能完全分离。此外,该工艺链中的所有含氟化合物都具有很强的毒性。
10.m. lopez等人描述了通过机械合金化和低温退火合成纳米金属间 nb3sn(m. lopez等人,“synthesis of nano intermetallic nb3sn by mechanical alloying and annealing at low temperature”, journal of alloys and compounds 612 (2014), 215
‑
220)。然而,所述方法的缺点是杂质通过研磨被引入到产物中。
11.a. godeke 等人给出了关于用于制造铌锡超导体的传统 pit方法的综述(a. godeke 等人,“state of the art powder
‑
in
‑
tube niobium
‑
tin superconductors”, cryogenics 48 (2008), 308
‑
316)。
12.所有在现有技术中已知的用于从nb3sn制造超导线材或从元素制造其制造所需的铌锡前体粉末例如nbsn2的方法的缺点是,为使铌与锡完全反应,锡必须通过固体扩散到达铌颗粒的内部中。该工艺非常耗时,并且由于 nbsn
2 在高于 840℃ 的温度下分解,因此也不能通过引入能量来加速。nbsn2的制造在实践中特别困难。该反应的已知放热性质通常导致在 800 至 1200℃ 的常见工艺条件下超过 840℃ 的 nbsn
2 分解温度。
13.此外,在现有技术中已知的铌
‑
锡粉末仅能困难地研磨,这导致从所用的含有钢或硬质合金的研磨介质中引入杂质,例如铁、钴、镍、硅、钨或碳,并在线材制造中产生劣质产品。
14.用于制造铌
‑
锡粉末的已知方法的另一个缺点是使用毒性很强的含卤素的化合物,例如 k2nbf7或nbcl5。这些用作前体用于用合适的还原剂还原成铌金属,所述铌金属在进一步的步骤中与锡反应生成铌
‑
锡目标化合物。
15.此外,用于制造铌
‑
锡粉末的已知方法的缺点在于,由于将氧引入元素铌和锡中,显著比例的氧被转移到目标化合物。因此,例如根据us 7,459,030的方法限于使用氧含量最大为3000ppm的铌和钽金属粉末和氧含量最大为2000ppm的锡。
16.因此,本发明的目的是提供合适的用于制造超导部件、特别是超导线材的起始化合物,其能够缩短耗时的固相扩散步骤并具有改进的研磨特性,及其制造方法,该方法此外不需要还原含卤素的原料。
17.令人惊讶地已发现,所述目的通过具有附聚物的粉末得以实现,所述附聚物具有特定的孔隙率。
18.因此,本发明的第一个主题是用于制造超导部件的粉末,其包含nb
x
sn
y
,其中1≤x≤6并且1≤y≤5,其中所述粉末具有尺寸为d90值小于400μm、优选220至400μm的三维附聚物,借助于激光衍射来确定,所述附聚物由平均粒径为小于15μm、优选小于8μm、特别优选0.1μm至5μm的初级颗粒组成,借助于扫描电子显微镜来确定,并且所述附聚物具有孔,所述孔的90%或更多具有0.1至20μm、优选0.2至15μm、特别优选0.3至10μm的直径,借助于水银孔隙率测定法来确定。
19.在本发明的一个优选的实施方式中,所述附聚物具有d50值为100至300μm、优选150至220μm的粒度分布,借助于激光衍射来确定。
20.d90值或 d50值是说明粉末中粒度小于或等于所给出的尺寸的附聚物的百分比的
值。
21.在一个优选的实施方式中,nb
x
sn
y
化合物是选自nb3sn、nb6sn5、nbsn2及其混合物的化合物。
22.令人惊奇地已经表明,在根据本发明的粉末中的铌固体内,所需的扩散路径由于小的初级粒度而明显减少,并且由于该特别的孔结构,锡可以在反应时非常容易地到达附聚物的内部中,由此可以使该制造工艺显著加速。此外,令人惊讶地已发现,通常进行粉末制造的温度或反应时间可以明显降低/减少。因此,例如,在本发明范围内可以在低于 800℃ 的温度下在少于 6 小时和甚至少于 4 小时内制造仅在最高 840℃ 的温度下稳定的 nbsn2。对于nb3sn,在 1050℃ 的温度下获得少于 6 小时的时间窗口,或者在 950℃ 的温度下获得少于 8 小时的时间窗口。
23.对于制造超导体已经证实特别有利的是使用纯相的粉末,以避免任何外来相影响超导性能。令人惊讶地已发现,根据本发明的粉末的特征还在于高纯度,这尤其表现在,其仅具有小比例的不同于各自的目标化合物的化合物相。因此,在一个优选的实施方式中,根据本发明的粉末的特征在于,化合物nb3sn或nb6sn5或nbsn2所占比例在每种情况下大于90%、优选大于94%、特别优选大于97%,基于所有检测到的结晶相计并且通过根据本发明的粉末的x射线衍射图的rietveld解析来确定。
24.在另一个优选的实施方式中,根据本发明的粉末的特征在于粉末中金属锡的比例小于3%、优选小于0.5%,基于所有检测到的结晶相计并且通过根据本发明的粉末的x射线衍射图的rietveld解析来确定。在一个特别优选的实施方式中,根据本发明的粉末基本上不含金属锡。在本上下文中,“基本上不含”应理解为是指在 x 射线衍射图中无法检测到金属锡的比例。
25.氧的存在会导致损害超导体的性能。在此,令人惊讶地已表明,与现有技术相比,尽管孔隙率增加,但根据本发明的粉末的氧含量没有增加。因此,一个实施方式优选,其中该粉末的氧含量小于1.8重量%、优选0.35至1.5重量%,特别是0.5至1.2重量%,基于粉末的总重量计。
26.根据本发明的粉末优选具有0.5至5 m2/g、优选1至3 m2/g的bet比表面积。在此,bet比表面积可以根据astm d3663来测定。
27.对于通过pit方法制造超导线材而言已经证实有利的是,使用具有特别细的粒度的粉末。因此,所使用的粉末大都在引入到管中之前被研磨。在此,令人惊讶地已表明,根据本发明的粉末表现出改进的研磨特性,由此可以实现更小的粒度,或者替代地,可以采用更温和的研磨方法。在一个优选的实施方式中,根据本发明的粉末在研磨附聚物后具有d99值为小于15μm、优选小于8μm、特别优选1μm至6μm的粒度,借助于激光衍射来确定。在另一个优选的实施方式中,根据本发明的粉末在研磨附聚物后具有小于10μm、优选小于7μm、特别优选小于0.5μm至5μm的d90值,在每种情况下借助于激光衍射来确定。
28.对于用增材制造法例如 lbm(激光束熔化)、ebm(电子束熔化)和/或 lc(激光熔覆)制造超导部件而言已经证实有利的是,使用具有特别的球形颗粒形状的粉末。在此,令人惊奇地已表明,根据本发明的粉末可以通过已知方法非常容易地雾化成具有球形颗粒的粉末,例如用eiga方法(电极感应熔炼气体雾化)。因此,在一个优选的实施方式中,根据本发明的粉末的所有粉末颗粒的至少95%在雾化后具有0.7至1、特别优选0.8至1的费雷特
径,其中费雷特径在以本发明范围内被定义为颗粒的最小直径除以最大直径,可以通过评价sem图像来确定。
29.根据本发明的粉末的特征尤其在于它的高纯度。因此,一个实施方式优选,其中所有金属元素在粉末中的比例为小于 500 ppm、优选小于 300 ppm、特别优选 1 ppm 至 150 ppm,在每种情况下基于粉末的总重量计。金属元素特别是通过研磨工艺引入的那些元素。在本发明范围内,ppm数据在每种情况下基于质量比例计。
30.对于制造具有可接受性能的超导部件而言必不可少的是,所使用的粉末的化学纯度高,并且外来物质仅以受控形式作为掺杂剂引入。在工艺中无意中引入的物质,特别是金属杂质和含氟化合物应最小化。在此,这些杂质的主要来源之一是来自所使用的铌
‑
和锡金属粉末的污染。在一个优选的实施方式中,根据本发明的粉末的氟含量小于15ppm、优选小于5ppm。在另一个优选的实施方式中,根据本发明的粉末具有共计小于0.8重量%、优选小于0.5重量%、特别优选小于0.25重量%的除钽之外的意外金属杂质的含量,在每种情况下基于粉末的总重量计。
31.在一个优选的实施方式中,根据本发明的粉末此外包含掺杂剂,与所述的在工艺中无意中引入的物质相反,如由现有技术已知的那样,掺杂剂以给定的方式添加到根据本发明的粉末中。其中令人惊讶地已发现,对掺杂剂没有提出任何特别的要求,而是相反可以使用本领域技术人员已知的常规掺杂剂。
32.现有技术中描述的用于制造基于nb3sn的超导线材的一些方法从钽锡合金或从作为前体粉末的基于钽和铌的金属间锡合金出发。然而,这具有的缺点是,钽的残留物保留在以后的nb3sn线材细丝的芯中,由此尤其提高制造成本并且损害产品的超导性能。这里可提到的另一个缺点特别是,成品线材细丝中超导 nb3sn 边界层的厚度减小,这对最大载流能力具有预期的负面影响。在一个优选的实施方式中,根据本发明的粉末因此基本上不含钽和钽化合物。在一个特别优选的实施方式中,在根据本发明的粉末中钽及其化合物的比例小于1重量%、优选小于0.5重量%、特别优选小于0.1重量%,在每种情况下基于粉末的总重量计。
33.根据本发明的粉末的特征在于它的在小的初级粒度下的高孔隙率,借助于特定的制造方法实现的性能。因此,本发明的另一主题是用于制造根据本发明的粉末的方法,该方法允许精确地实现所述性能的组合。根据本发明的方法的特征在于,根据本发明的粉末是通过铌金属粉末与锡金属粉末的反应来制造的,其中所述铌金属粉末是通过用蒸气状还原剂还原铌氧化物得到的。令人惊奇地已发现,以这种方式获得了由于初级粒度、孔隙率和化学纯度的有利组合而特别适用于制造超导线材的粉末。例如在wo 00/67936中描述了在蒸气状还原剂存在下还原铌氧化物的合适方法。
34.为了有效地进行该方法,已经证实有利的是,在组合的方法步骤中进行铌金属粉末的制备和反应。因此,根据本发明的方法的一个实施方式优选,其中原位制备铌金属粉末。这可以特别通过在热处理中在锡金属粉末的存在下使铌氧化物与蒸气状还原剂反应来实现。
35.令人惊讶地已表明,以这种方式可以获得具有所需孔隙率的结构。这是特别出乎意料的,因为本领域技术人员在用镁还原 nbsn
‑
混合氧化物和
‑
氢氧化物时不会预期多孔 nbsn 产物。
36.铌氧化物优选为选自nb2o5、nbo2、nbo及其混合物中的一种。
37.令人惊讶地已表明,通过合适选择起始化合物,可以实现对于制造超导线材而言有利的粉末孔隙率。因此,一个实施方式优选,其中所述铌金属粉末具有三维附聚物,所述三维附聚物具有d90值小于 400μm、优选 200 至 350μm 的尺寸,借助于激光衍射来确定,所述附聚物由平均粒径小于 10μm、优选小于 4μm、特别优选 0.1μm 至 2μm 的初级颗粒形成,借助于扫描电子显微镜来确定,并且所述附聚物具有尺寸为0.1至20μm、优选0.2至15μm、特别优选0.2至5μm的孔,借助于水银孔隙率测定法来确定。
38.使用具有双峰孔径分布的铌金属粉末已经证实是特别有利的。因此,一个实施方式优选,其中铌金属粉末具有双峰孔径分布、优选具有0.9至20μm、特别优选1至10μm的最大值,和0.1至0.9μm、优选0.2至0.8μm的最大值,借助于水银孔隙率测定法来确定。不受特定理论的束缚,认为孔径的双峰分布能够改进锡通过孔进入到附聚物内部中。
39.令人惊讶地已表明,如现有技术中所述,对于制造根据本发明的粉末而言,限制铌金属粉末的氧含量不是必需的。然而,已经证实有利的是氧含量不要太高。因此,在一个优选实施方式中,用于制造根据本发明的粉末的铌金属粉末具有小于2.2重量%、优选0.35至1.9重量%、特别优选0.4至1.6重量%的氧含量,在每种情况下基于铌金属粉末的总重量计。此外,也不需要将这些铌金属粉末的氢含量限制在小于 100 ppm。因此,在根据本发明的方法中还可以使用氢含量大于100ppm,甚至110至400ppm的铌金属粉末。因此一个实施方式优选,其中用于制造根据本发明的粉末的铌金属粉末具有110至400ppm的氢含量,基于铌金属粉末的总重量计。
40.为了防止形成不希望的和部分难溶的卤化镁和卤化钙,例如mgf2和caf2、优选具有尽可能低的氟和氯含量的铌金属粉末。因此,通过铌氧化物的金属热蒸气还原制造的铌金属粉末优于通过含氟化合物(例如 k2nbf7)的还原或在含卤化物的盐熔体中电化学还原制造的铌金属粉末。在一个优选的实施方式中,所使用的铌金属粉末含有在每种情况下小于15ppm、优选在每种情况下小于10ppm、特别优选在每种情况下小于2ppm的氟和氯,基于铌金属的总重量计。
41.为了确保根据本发明的粉末所必需的化学纯度,一个优选的实施方式是使用所有金属元素的总和小于800ppm、优选小于500ppm的铌金属粉末。
42.已发现碱土金属化合物作为蒸气状还原剂特别有利。在一个优选的实施方式中,蒸气状还原剂是镁蒸气。已经表明,以这种方式可以实现铌氧化物粉末颗粒的良好润湿。特别是作为还原剂的镁具有以下优点:在转化为mgo之后它可以被简单有效地除去,由此避免了对产品的不必要的污染。
43.所需的目标化合物可以通过根据本发明的方法在比迄今在现有技术中已知的更低的温度下和更短的时间内来制造。因此,根据本发明的方法的一个实施方式优选,其中金属铌粉与金属锡的反应在300至1100℃、优选600至1050℃、特别优选650至790℃的反应温度下进行。在此,反应时间优选小于8小时、优选0.5至7小时、特别优选1至4小时。
44.如已经描述的,可以将掺杂剂加入到粉末中,由此可以调整粉末的性能。令人惊讶地已发现,在该方法开始时引入所述掺杂剂是有利的。因此,一个实施方式优选,其中用于制造铌金属粉末的铌氧化物另外具有掺杂剂。对于所使用的掺杂剂,没有提出任何特别的要求。相反,令人惊讶地已发现,可以使用本领域技术人员已知的所有常规掺杂剂。
45.根据本发明的粉末特别适用于制造超导部件。因此,本发明的另一主题是根据本发明的粉末用于制造超导部件,特别是用于制造超导线材的用途。在此,超导部件优选通过粉末冶金工艺或增材制造法或pit法来制造。超导线材的制造优选借助于pit法来进行。
46.本发明的另一主题是根据本发明的粉末在增材制造法中的用途。增材制造法可以是例如lbm(激光束熔化)、ebm(电子束熔化)和/或lc(激光熔覆)。
47.参考以下实施例更详细地解释本发明,其中这些实施例不应以任何方式被理解为对本发明构思的限制。
48.实施例:类似于wo 00/67936 a1中描述的制造方法,通过nbo2与镁蒸气的反应获得铌金属粉末。所得铌金属粉末的氧含量为8500ppm,氢含量为230ppm,氟含量为2ppm,金属杂质总共为310ppm,具有d50值为205μm且d90值为290μm的附聚物尺寸。初级颗粒的平均尺寸为 0.6
ꢀµ
m,附聚物的孔径分布是双峰的,最大值在0.5 和 3
ꢀµ
m处(见图 6)。该铌金属粉末随后在不同的条件下与氧含量为6800ppm的锡金属粉末反应,并对所得产物进行分析。
49.在对比实验1和2中使用的粉末是使用氧含量为2900ppm且氢含量为10ppm的常规无孔铌金属粉末。这些对比粉末的 d90值为 95
ꢀµ
m(见图 8)。
50.对于对比实验 3 和 4,通过在由 kcl/kf 组成的盐熔体中在 850℃ 下用液态钠还原 k2nbf7来制造铌金属粉末并随后通过洗涤去除所有盐。如此制造的铌金属粉末含有不规则成形的颗粒,没有 d90值为 29μm 的孔,这些颗粒没有烧结成附聚物。铌金属粉末的氧含量为2.4重量%,氢含量为150ppm,氟含量为2500ppm,金属杂质总共为10200ppm,其中主要杂质为镍和铁。
51.在所有对比实验中,铌金属粉末随后在不同的条件下与氧含量为 6800 ppm 的锡金属粉末反应,并对所得产物进行分析。
52.在所有实验中,所使用的锡金属粉末的粒度均小于 150
ꢀµ
m。
53.结果总结在表1中,其中孔径和粒度的数据在每种情况下与附聚物有关。粒度在每种情况下借助于激光衍射来确定(mastersizer s,分散在水和daxad11中,5分钟超声处理)。孔的尺寸借助于水银孔隙率测定法来确定 (micromeritics公司; autopore iv)并且与孔径分布的最大值的位置有关。氧含量借助于载气热萃取(leco tch600)来确定。金属杂质的痕量分析用以下分析仪器 pq 9000 (analytik jena) 或 ultima 2 (horiba) 借助于icp
‑
oes 进行。所有以重量%给出的数据在每种情况下基于粉末的总重量计。
54.x 射线衍射在粉末状样品上用 malvern
‑
panalytical 公司的仪器(带半导体检测器的 x’pert
‑
mpd,带 40 kv/40 ma 的 x 射线管 cu lff,ni 过滤器)进行。
55.在用h2so4洗涤并干燥后,分析实施例3的粉末。
56.对比例的粉末没有形成附聚物并且在分析中显示出不均匀的相组成。此外,对比实验3和4的粉末的特征在于1300至1800ppm的非常高的氟含量和总共6500至9000ppm的金属杂质,因此不适合制造超导部件,特别是线材。
57.随后在无氧气气氛中研磨得自实施例1的粉末,由此得到d90值为2.6μm且d99值为3.7μm的粒度分布。研磨后的氧含量为 1.14重量%,所有合计的金属杂质在研磨工艺前后之差为 140 ppm。
58.在本发明范围内令人惊讶地已发现,与预期相反,根据本发明的粉末的孔隙率的
增加没有导致氧含量的增加,即使在该粉末经受进一步的研磨步骤时也是如此。
59.此外,根据本发明的实施例表明,在目标化合物中没能检测到未反应的锡。
60.图1至3示出了根据本发明的粉末的sem图像,其中图1示出了根据实施例1获得的nbsn2,图2示出了根据实施例2获得的nb3sn,图3示出了根据实施例3获得的nb3sn。在所有图像上可以清楚地看到,根据本发明的粉末具有在常规粉末的情况下未观察到的孔隙率,如图 4 和 5中所示,它们示出了对比例 1 和 2 的sem图像。
61.图6示出了用于制造根据本发明的粉末的铌金属粉末的孔径分布的测量结果,其中可以容易地看到孔径的双峰分布。
62.图7示出了根据实施例1的根据本发明的粉末的孔径分布的测量结果,其中最大值在约3μm的孔径处。
63.图8示出了用于制造对比例1和2的铌金属粉末的sem图像。
再多了解一些
本文用于企业家、创业者技术爱好者查询,结果仅供参考。