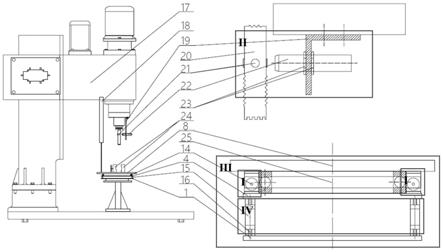
1.本发明专利涉及一种微钻标定系统与方法,尤其适用于多层薄层状岩石、坚硬土、多层材料的一种随钻力学性质测试的微钻标定系统与方法。
背景技术:
2.微钻试验装置是钻探行业研究岩石可钻性、进行室内模拟钻进的一种小型钻机模拟平台,主要通过台式钻机改造而成,或专门制作的可调速、调扭矩、控制给进速度的小型模拟装置。一般是把岩块卡夹在一个带有给进压力的底座上,钻头安装在扭矩或转速可调的动力头上,主要检测不同钻头、钻孔直径、钻速、冲洗液流量、冲洗液性质的钻进效率、碎岩的工作状态,用于确定最优的工艺参数、冲洗液改性配方、岩石的可钻性等级等指标。由于基于钻进参数和碎岩效率设计,钻进过程中较少进行扭矩、转速、进尺速度、泵压、振动等与样品物理力学性质关系的分析,现有的装备有的对中不准、给进控制不精细,缺少测量部件安装条件,也不具备进行精细测试条件。因此,着手于一种新的方法:在钻进过程中,实时获得钻进参数(钻压,钻速,转速,扭矩,轴向位移,冲洗液量等),为今后通过钻进参数建立获取被测样品物性或力学参数和特征的技术方法奠定基础。
技术实现要素:
3.针对现有技术的不足之处,本发明提供一种结构简单,使用方便的随钻力学性质测试的微钻标定系统与方法
4.为实现上述技术目的,本发明的一种随钻力学性质测试的微钻标定系统,匹配微钻实验机使用,微钻实验机的钻头设置在微钻实验机横梁底部,微钻实验机的微钻实验机横梁回转轴线由上到下设有进尺传感器和转速监测系统,转速监测系统设置在微钻实验机的钻头上,转速监测系统的正下方设有摆放在微钻实验机的平台上的三层圆盘组合结构,三层圆盘组合结构包括钻压监测系统和扭矩监测系统;
5.所述的速监测系统包括固定架,多个永磁磁铁,接近开关和紧固螺母;其中多个永磁磁铁为偶数个,对称设置在所述微钻实验机的钻头上,所述接近开关通过固定架水平设置在永磁磁铁一侧,固定架与接近开关连接处设有紧固螺母;
6.所述三层圆盘组合结构包括由下至上设置的第一层铁制圆形底盘,第二层铁制圆形底盘和第三层铁制圆形底盘,第一层底盘固定在微钻实验机上,第一层底盘的盘面上等间距设有四个m22型号通孔,所述第二层底盘圆盘边有四个沿两条相互垂直的直径对称分布的m12型号螺纹孔,周边沿直径分布两对m5螺纹孔,第二层底盘上表面设有环凹槽;第三层圆盘圆盘上部设有两条沿着直径方向、互相垂直的t型凹槽,t型凹槽内滑动设有四支搭配所述岩样夹持器,所述岩样夹持器可沿所述t型槽移动,从而用以夹持住任何规格试验岩样;第三层圆盘下部内测设有圆环凹槽,第二层底盘上表面的环凹槽与第三层圆盘下部的圆环凹槽之间设有推力球轴承,周边沿直径分布两对m5螺纹孔;
7.所述扭矩监测系统设置在第二层铁制圆形底盘和第三层铁制圆形底盘之间,扭矩
监测系统包括围绕三层圆盘组合结构(iii)设置的多个扭矩监测器,所述扭矩监测器包括微型压力传感器、第一角钢和第二角钢,其中第一角钢和第二角钢相对设置,其中第一角钢与第三层铁制圆形底盘连接,第二角钢与第二层铁制圆形底盘连接,微型压力传感器设置在第二角钢上并与第一角钢之间,微型压力传感器固定子啊第二角钢上并与第一角钢接触,第一角钢通过m5螺纹孔固定在第三层圆盘下部,所述第二角钢通过m5螺纹孔固定在第二层圆盘上;
8.所述钻压监测系统包括多个设置在第一层铁制圆形底盘和第二层铁制圆形底盘之间的压力传感器,所述压力传感器的底部通过m12螺纹孔分别与第一层圆盘的m12螺纹孔匹配连接,压力传感器的顶部通过螺纹孔分别与第二层圆盘的m12螺纹孔匹配连接。
9.所述第一层底盘尺寸是直径365mm、厚度10mm的铁制圆盘;所述第二层底盘尺寸是直径356mm、厚度100mm的铁制圆盘,圆盘上部内有深度1mm、内径240mm、外径300mm的圆环凹槽;所述第三层圆盘尺寸是直径417mm、厚度22mm的铁制圆盘,圆盘下部内测有深度1mm、内径240mm、外径300mm的圆环凹槽。
10.在所述第一层圆形底盘和所述第二层圆形底盘之间安装四只所述压力传感器输出的压力值总和为钻进压力;
11.f
钻压
=f1 f2 f3 f412.式中,f1、f2、f3、f4分别是四只压力传感器的输出值,单位n;
13.所述钻压监测系统除监测上部钻进压力外,还用于支撑所述钻压监测系统上部结构,连结固定所述第一层圆形底盘和所述第二层圆形底盘。
14.所述扭矩监测系统是通过岩样夹持器和所述推力球轴承,将钻头施加在岩样上的扭矩测量转换为施加在两只微小型压力传感器上的压力测量;
15.m=f
×
s
16.式中,f表示施加在微型压力传感器上的压力值,单位n;s表示钻头到微型传感器的力臂大小,单位m;m表示扭矩,单位n
·
m。
17.所述第二层底盘内部圆环凹槽和所述第三层底盘内部圆环凹槽之间固定设有用以固定推力球轴承,防止轴承与所述底盘发生相对移动。
18.所述t形凹槽作为流水槽使用,所述第三层圆形底盘直径大于所述第一层圆形底盘和所述第二层底盘,可以让水通过流水槽直接落下,减小水对所述第三层底盘下面所有仪器的腐蚀。
19.一种于随钻力学性质测试的微钻标定系统的标定方法,其步骤如下:
20.a.利用水泥黄沙配比制备水泥砂浆十八只试样胚,养护72h以上后构成试验试样;包括三只用于测得单轴抗压强度的标准圆柱试样、三只用于巴西劈裂试验从而取得抗拉强度的标准圆饼试样、九只用于获得抗剪强度的标准方形试样以及三只用于使用上述随钻力学性质测试的微钻标定系统进行微钻试验的方形试样;
21.根据岩石力学试验规范,将上述三只标准圆柱试样贴上应变片,通过岩石伺服机进行三次单轴抗压试验,并对所获结果取平均值,获得该组水泥砂浆试样的单轴抗压强度以及杨氏模量和泊松比;将上述三只标准圆饼试样进行三次巴西劈裂试验,并对所获结果取平均值获得抗拉强度;将上述九只标准方形试样每三个一组,进行剪切角为50
°
、60
°
、70
°
的剪切强度试验,对所获结果取平均值,获得该组水泥砂浆试样的抗剪强度以及粘聚力和
内摩擦角;在获得该一组水泥砂浆的抗压、抗拉和抗剪等力学参数以及泊松比和杨氏模量等变形参数后,对剩余三只方形试样进行微钻实验;
22.b.将上述其中一只标准方形试样放于三层圆盘组合结构(ⅲ)的第三层铁制圆形底盘上,然后调整岩样夹持器在t型槽上滑动从而使试样固定在第三层铁制圆形底盘中央,完成试样安装;
23.c.完成式样安装后,开启微钻试验台液压控制开关,使钻头与式样上表面接触后关闭液压开关;开启微钻试验台电机开关控制钻头转速为一定值,将两只微型压力传感器、四只压力传感器和进尺传感器读数清零;再次打开液压控制开关开始钻进;微钻试验台上部钻头部分位置保持不动,由微钻试验台的下部液压结构带动三层圆盘组合结构(ⅲ)向上运动实现钻进;当钻头接触到试样后,四只压力传感器接收到钻进过程中的压力开始读数;钻头的转动带动推力球轴承的转动,将钻头受到的扭矩力通过第一角钢转化为施加在堆成设置在推力球轴承旁的两只微小型压力传感器上,开始进行扭矩力的检测;同时,进尺传感器开始记录时深曲线;接近开关开始接收钻头钻头接触试样后转速的变化;上述扭矩监测系统(ⅰ)、钻压监测系统(ⅳ)、转速监测系统(ⅱ)以及进尺传感器记录的时深信号均在同一个时间序列之下;
24.d.利用计算器采集检测数据,并记载跟踪步骤c的钻进全过程;当进尺传感器实时显示的位移读数与式样高度相等时说明此时试样被钻通,关闭微钻试验台开关,扭矩监测系统(ⅰ)所检测得到的扭矩值、钻压监测系统(ⅳ)所检测得到的钻压值、转速监测系统(ⅱ)所检测得到的转速值以及进尺传感器所检测到的时间位移曲线自动保存在计算机中,一次实验结束;
25.e.安装第二只方形试样,根据控制变量法,保持微钻试验台液压压力大小不变,改变钻头转速大小,重复步骤c和步骤d,获得了相同钻压不同转速下的钻进参数曲线,第二次试验结束;安装第三只方形试样,保持钻头转速大小不变,改变微钻试验台液压压力大小,重复步骤c和步骤d,获得了相同转速不同钻压下的钻进参数曲线;
26.f.重复步骤a~e,改变水泥黄沙配比,从而改变了水泥砂浆试样的物理力学参数大小,其中,十五只试样获得同一水泥黄沙配比下试样的物理力学参数,剩余三只方形试样进行微钻试验,进行第二组、第三组实验;
27.g.整理由步骤a得到的试样力学参数和变形参数数据,和由步骤b~e得到的钻压、转速、钻速和扭矩等随钻参数数据,利用数理统计以及机器学习的方法,建立试样物理力学参数数值和随钻参数之间的数值联系;
28.h.通过上述的内部岩性单一、均质无结构面的试样标定内部岩性多样、含有裂隙等结构面的非均匀的一般试样;根据进尺传感器(18)所检测到的时间位移曲线,利用上述检测到的钻压、转速、扭矩和钻速等随钻参数曲线的形状、变化规律、振幅大小、频率和趋势,刻画钻进历程,标定非均匀试样内部结构面、裂隙的大小和产状。
29.本发明的有益效果,
30.一、对在钻进参数能够达到实时监测、连续采集的效果,为后续实验数据处理、分析和研究提供了数据基础;采集的数据与传统钻探获得的随钻监测数据更精确;
31.二、所选的四只压力传感器、两只微小型压力传感器和进尺传感器可替换为精度更或者量程更大的传感器,满足不同实验的精度要求;在不进行实验时,可将上述传感器拆
卸下来进行保养,从而延长传感器的使用寿命;
32.三、设备操作简单,方便使用,具有良好的实用价值;。
33.四、现场传统的钻探试验和室内试验原理相同,历程相同,但现场传统的钻探试验由于设备体积大,钻进深度和钻进参数之间在时间上存在着严重的滞后性,无法匹配;在室内试验中,由于尺度较小(100mm
‑
200mm),时间与深度匹配较好,滞后性的问题可以忽略,并且所有的传感器都在同一时间序列下进行,能够精准的标定岩土随钻力学性质。
附图说明
34.图1为本发明的第一层铁制圆形底盘结构示意图;
35.图2为本发明的第二层铁制圆形底盘结构示意图;
36.图3为本发明的第三层铁制圆形底盘结构示意图;
37.图4为本发明的扭矩传感器系统组成示意图;
38.图5为本发明的扭矩传感器系统三维示意图
39.图6为本发明的压力传感器示意图;
40.图7为本发明的三层圆盘结构示意图;
41.图8为本发明的推力球轴承结构示意图;
42.图9为本发明的各类传感器安装在微钻实验机上示意图;
43.图10为本发明的试验钻压
‑
位移曲线对比图。
44.图中:1
‑
第一层铁制圆形底盘,2
‑
第一通孔,3
‑
第一m12螺纹孔,4
‑
第二层铁制圆形底盘,5
‑
第一m5螺纹孔,6
‑
第一凹槽,7
‑
第二m12螺纹孔,8
‑
第三层铁制圆形底盘,9
‑
第二凹槽,10
‑
第二m5螺纹孔,11
‑
t型凹槽,12
‑
第一3#角钢,13
‑
第二3#角钢,14
‑
微小型压力传感器,15
‑
压力传感器,16
‑
压力传感器m12螺纹孔,17
‑
微钻实验机横梁,18
‑
进尺传感器,19
‑
固定架,20
‑
取芯钻头,21
‑
永磁磁铁,22
‑
接近开关,23
‑
紧固螺母,24
‑
岩样夹持器,25
‑
推力球轴承。
ⅰ‑
扭矩监测系统,
ⅱ‑
转速监测系统,
ⅲ‑
三层圆盘组合结构,
ⅳ‑
钻压监测系统。
具体实施方式
45.下面将结合本发明实施例中的附图对本发明实施例中的技术方案进行说明:
46.如图9所示,本发明的一种随钻力学性质测试的微钻标定系统,匹配微钻实验机使用,微钻实验机的钻头20设置在微钻实验机横梁17底部,微钻实验机的微钻实验机横梁17回转轴线由上到下设有进尺传感器18和转速监测系统ⅱ,转速监测系统ⅱ设置在微钻实验机的钻头20上,转速监测系统ⅱ的正下方设有摆放在微钻实验机的平台上的三层圆盘组合结构ⅲ,三层圆盘组合结构ⅲ包括钻压监测系统ⅳ和扭矩监测系统ⅰ;
47.所述的速监测系统ⅱ包括固定架19,多个永磁磁铁21,接近开关22和紧固螺母23;其中多个永磁磁铁21为偶数个,对称设置在所述微钻实验机的钻头20上,所述接近开关22通过固定架19水平设置在永磁磁铁21一侧,固定架19与接近开关22连接处设有紧固螺母23;
48.如图1、图2、图3和图7所示,所述三层圆盘组合结构ⅲ包括由下至上设置的第一层铁制圆形底盘1,第二层铁制圆形底盘4和第三层铁制圆形底盘8,第一层底盘1固定在微钻实验机上,第一层底盘1的盘面上等间距设有四个m22型号通孔2,所述第二层底盘4圆盘边
有四个沿两条相互垂直的直径对称分布的m12型号螺纹孔7,周边沿直径分布两对m5螺纹孔5,第二层底盘4上表面设有环凹槽6;第三层圆盘8圆盘上部设有两条沿着直径方向、互相垂直的t型凹槽11,t型凹槽11内滑动设有四支搭配所述岩样夹持器24,所述岩样夹持器24可沿所述t型槽11移动,从而用以夹持住任何规格试验岩样;第三层圆盘8下部内测设有圆环凹槽9,第二层底盘4上表面的环凹槽6与第三层圆盘8下部的圆环凹槽9之间设有推力球轴承25,如图8所示,周边沿直径分布两对m5螺纹孔10;所述扭矩监测系统i是通过岩样夹持器24和所述推力球轴承25,将钻头施加在岩样上的扭矩测量转换为施加在两只微小型压力传感器14上的压力测量;
49.m=f
×
s
50.式中,f表示施加在微型压力传感器上的压力值,单位n;s表示钻头到微型传感器的力臂大小,单位m;m表示扭矩,单位n
·
m。
51.第一层底盘1尺寸是直径365mm、厚度10mm的铁制圆盘;所述第二层底盘4尺寸是直径356mm、厚度100mm的铁制圆盘,圆盘上部内有深度1mm、内径240mm、外径300mm的圆环凹槽6;所述第三层圆盘8尺寸是直径417mm、厚度22mm的铁制圆盘,圆盘下部内测有深度1mm、内径240mm、外径300mm的圆环凹槽9。在所述第一层圆形底盘1和所述第二层圆形底盘4之间安装四只所述压力传感器15输出的压力值总和为钻进压力;
52.f
钻压
=f1 f2 f3 f453.式中,f1、f2、f3、f4分别是四只压力传感器的输出值,单位n;
54.所述钻压监测系统iv除监测上部钻进压力外,还用于支撑所述钻压监测系统iv上部结构,连结固定所述第一层圆形底盘1和所述第二层圆形底盘4。
55.第二层底盘4内部圆环凹槽6和所述第三层底盘内部圆环凹槽9之间固定设有用以固定推力球轴承25,防止轴承与所述底盘发生相对移动。
56.所述t形凹槽11作为流水槽使用,所述第三层圆形底盘8直径大于所述第一层圆形底盘1和所述第二层底盘4,可以让水通过流水槽直接落下,减小水对所述第三层底盘8下面所有仪器的腐蚀。
57.如图4和图5所示,所述扭矩监测系统i设置在第二层铁制圆形底盘4和第三层铁制圆形底盘8之间,扭矩监测系统i包括围绕三层圆盘组合结构iii设置的多个扭矩监测器,所述扭矩监测器包括微型压力传感器14、第一角钢12和第二角钢13,其中第一角钢12和第二角钢13相对设置,其中第一角钢12与第三层铁制圆形底盘8连接,第二角钢13与第二层铁制圆形底盘4连接,微型压力传感器14设置在第二角钢13上并与第一角钢12之间,微型压力传感器14固定子啊第二角钢13上并与第一角钢12接触,第一角钢12通过m5螺纹孔10固定在第三层圆盘8下部,所述第二角钢13通过m5螺纹孔5固定在第二层圆盘4上;
58.所述钻压监测系统ⅳ包括多个设置在第一层铁制圆形底盘1和第二层铁制圆形底盘4之间的压力传感器15,所述压力传感器15的底部通过m12螺纹孔16分别与第一层圆盘1的m12螺纹孔3匹配连接,压力传感器15的顶部通过螺纹孔16分别与第二层圆盘4的m12螺纹孔7匹配连接。
59.一种使随钻力学性质测试的微钻标定系统的标定方法,其步骤如下:
60.a.利用水泥黄沙配比制备水泥砂浆十八只试样胚,养护72h以上后构成试验试样;包括三只用于测得单轴抗压强度的标准圆柱试样、三只用于巴西劈裂试验从而取得抗拉强
度的标准圆饼试样、九只用于获得抗剪强度的标准方形试样以及三只用于使用上述随钻力学性质测试的微钻标定系统进行微钻试验的方形试样;
61.根据岩石力学试验规范,将上述三只标准圆柱试样贴上应变片,通过岩石伺服机进行三次单轴抗压试验,并对所获结果取平均值,获得该组水泥砂浆试样的单轴抗压强度以及杨氏模量和泊松比;将上述三只标准圆饼试样进行三次巴西劈裂试验,并对所获结果取平均值获得抗拉强度;将上述九只标准方形试样每三个一组,进行剪切角为50
°
、60
°
、70
°
的剪切强度试验,对所获结果取平均值,获得该组水泥砂浆试样的抗剪强度以及粘聚力和内摩擦角;在获得该一组水泥砂浆的抗压、抗拉和抗剪等力学参数以及泊松比和杨氏模量等变形参数后,对剩余三只方形试样进行微钻实验;
62.b.将上述其中一只标准方形试样放于三层圆盘组合结构ⅲ的第三层铁制圆形底盘8上,然后调整岩样夹持器24在t型槽11上滑动从而使试样固定在第三层铁制圆形底盘8中央,完成试样安装;
63.c.完成式样安装后,开启微钻试验台液压控制开关,使钻头20与式样上表面接触后关闭液压开关;开启微钻试验台电机开关控制钻头转速为一定值,将两只微型压力传感器14、四只压力传感器15和进尺传感器18读数清零;再次打开液压控制开关开始钻进;微钻试验台上部钻头部分位置保持不动,由微钻试验台的下部液压结构带动三层圆盘组合结构ⅲ向上运动实现钻进;当钻头20接触到试样后,四只压力传感器15接收到钻进过程中的压力开始读数;钻头20的转动带动推力球轴承25的转动,将钻头20受到的扭矩力通过第一角钢12转化为施加在堆成设置在推力球轴承25旁的两只微小型压力传感器14上,开始进行扭矩力的检测;同时,进尺传感器18开始记录时深曲线;接近开关22开始接收钻头20钻头接触试样后转速的变化;上述扭矩监测系统ⅰ、钻压监测系统ⅳ、转速监测系统ⅱ以及进尺传感器18记录的时深信号均在同一个时间序列之下;
64.d.利用计算器采集检测数据,并记载跟踪步骤c的钻进全过程;当进尺传感器18实时显示的位移读数与式样高度相等时说明此时试样被钻通,关闭微钻试验台开关,扭矩监测系统ⅰ所检测得到的扭矩值、钻压监测系统ⅳ所检测得到的钻压值、转速监测系统ⅱ所检测得到的转速值以及进尺传感器18所检测到的时间位移曲线自动保存在计算机中,一次实验结束;
65.e.安装第二只方形试样,根据控制变量法,保持微钻试验台液压压力大小不变,改变钻头转速大小,重复步骤c和步骤d,获得了相同钻压不同转速下的钻进参数曲线,第二次试验结束;安装第三只方形试样,保持钻头转速大小不变,改变微钻试验台液压压力大小,重复步骤c和步骤d,获得了相同转速不同钻压下的钻进参数曲线;
66.f.重复步骤a~e,改变水泥黄沙配比,从而改变了水泥砂浆试样的物理力学参数大小,其中,十五只试样获得同一水泥黄沙配比下试样的物理力学参数,剩余三只方形试样进行微钻试验,进行第二组、第三组实验;
67.g.整理由步骤a得到的试样力学参数和变形参数数据,和由步骤b~e得到的钻压、转速、钻速和扭矩等随钻参数数据,利用数理统计以及机器学习的方法,建立试样物理力学参数数值和随钻参数之间的数值联系;
68.h.通过上述的内部岩性单一、均质无结构面的试样标定内部岩性多样、含有裂隙等结构面的非均匀的一般试样;根据进尺传感器(18)所检测到的时间位移曲线,利用上述
检测到的钻压、转速、扭矩和钻速等随钻参数曲线的形状、变化规律、振幅大小、频率和趋势,刻画钻进历程,标定非均匀试样内部结构面、裂隙的大小和产状。
69.实施例一、
70.如图1、图2、图3、图6所示,第一层圆形底盘1为直径365mm,厚度10mm的铁质圆盘;在底盘1内部钻出4个直径为m22的通孔3,,目的是为了固定在微钻实验机上。在靠近圆盘边界处,在相互垂直的两条直径上钻出四个m12的螺纹孔2,其直径大小与压力传感器15上通孔16大小一致,用于固定住压力传感器15。最下部第一层铁制圆盘1厚度不宜太厚,也不能太薄,厚度过大,会占用更多的实验空间,使实验难以展开;厚度过小没有足够的强度支撑上部零件的重量和钻压之和,影响钻机整体稳定性,因此综合考虑选取厚度为10mm;第二层铁制底盘5为直径365mm,厚度10mm的铁质圆盘,底盘上面内部铣出一个内径240mm,外径300mm,深度1mm的圆环凹槽6,圆环直径大小与上部推力球轴承25相对应,其目的一是为了固定推力轴承25,二是能够限制推力轴承25的水平方向移动,保证实验的平稳;在第二层底盘4边界处钻有四个m12的螺纹孔7,目的是固定压力传感器15;在外侧沿一条直径还有四个m5的螺纹孔4,两只为一组,用于固定3#角钢12;第三层铁制底盘7为一个直径417mm,厚度21.7mm的铁质圆盘8,在上面有两条沿着直径方向、互相垂直的t型凹槽11,第三层底盘底部铣出一个圆环凹槽9,大小与推力球轴承25相对应,并将第三层底盘对应放置于轴承上;并沿一条直径钻出两组m5螺纹孔10,用于固定3#角钢14;第一层底盘1,第二层底盘4直径均比第三层底盘8小,目的是在实验钻进过程中,冲洗液能够沿着原有底盘边缘落下,从而不会浸湿推力球轴承25和各类传感器,减小推力轴承因生锈造成的摩擦影响实验结果,也保护了传感器,延长使用寿命,能够重复实验;图6就是安装完成的三层圆盘结构ⅲ;
71.如图4所示,扭矩监测系统ⅰ结构包括两只相对3#角钢12、13和一只微小型压力传感器14,采用间接法来测量扭矩,岩样夹持器24将试样紧固,让试样到位于圆盘中间,从而让试样到两端微型压力传感器14的距离相等;在钻进过程时,通过固定在第三层底盘8下部的推力球轴承25,这样转动产生的扭矩就转换为施加在微小型压力传感器14上的压力,最后通过得到的压力值乘以力臂长度从而计算出扭矩大小,完成扭矩测量;转速监测系统ⅱ结构包括固定架19,永磁磁铁21,接近开关22和紧固螺母23,永磁磁铁21按实验转速大小和实验对转速精度的要求对称设置2n个吸附在钻杆上,其中n≥2,接近开关22用固定架19和紧固螺母23设置在所述微钻实验机横梁17底部,当钻杆转动时,接近开关22接收到磁铁21传来的脉冲信号,以此来得出转速大小;进尺传感器18固定在钻机横梁17上,进尺传感器18探头顶部抵在第三层底盘8上,当微钻实验机工作时,底盘带动探头向上移动从而产生信号输出,测得位移量;钻压监测系统ⅳ包括四只压力传感器15,每只压力传感器15顶部与底部各有一个m12的通孔16,通过螺丝对称固定在所述第一层底盘1和第二层底盘5之间,既可以使压力传感器受力均匀,又可固定岩样底座。
72.以下给出本发明的具体实施例。
73.在某个实施例中,基于微钻精细测试的岩土随钻力学性质测试的标定系统和方法如下:
74.利用微钻实验机多参数测试随钻监测装置,调整整套底盘结构使其水平,并使钻头中心与第三层底盘圆心对齐。将自制规格为70.7
×
70.7
×
70.7mm,强度为m10的试样放置在第三层铁制底盘上,并用岩样夹持器固定试样;根据微钻实验机的性能选择并安装钻速、
转速、扭矩和钻压监测系统,安装过程中需注意进尺传感器与地面垂直,压力传感器要对称放置;根据水泥砂浆试块的强度选择并安装微小型压力传感器,需确保两只微小型压力传感器对称放置并与地面平行,安装在第三层底盘之下的角钢需同时接触到微小型压力传感器。将各个传感器以半桥方式连接到数据采集器上,数据采集器与计算机相连,在计算机上对各类传感器平衡并清零;先打开冲洗液开关,后打开微钻实验机开关,开始钻进;当计算机上显示位移值即钻进深度等于试块高度70.7mm时停止钻进并保存数据;一次试验结束。
75.分析钻进曲线,以位移
‑
钻压曲线为例,如图9所示,左侧是由水泥黄沙比为1:4.02配制而成的水泥砂浆试样,右侧是由两种不同配比组合制作而成的试样,上部水泥沙子配比为1:4.02,下部为纯水泥;通过岩石力学试验得知,上部试样的单轴抗压强度为12.7mpa,下部试样的单轴抗压强度为30.4mpa,从钻进曲线可以看出,对于配比相同且单一均匀的水泥砂浆试样,在控制转速、钻速和钻压不变的情况下,获得的钻压值是一固定值;得到的其他钻进参数也为一固定值,因此通过大量的试验数据,利用数理统计方法和机器学习的方法,可以得到试样物理力学参数和钻进参数之间的数值关系;
76.图9右侧,由于制作过程的人为因素,上下两种试样之间的界面并不是水平的,而是一个斜截面。经过测量,斜截面最高处距顶面30mm,最低处距顶面35mm。通过钻取所得到的位移钻压曲线分析出,在钻进0
‑
10mm处,由于钻头刚接触到试样,会产生剧烈的震动,则表现出钻进压力突然增大,之后又迅速减小至平稳状态;在10mm
‑
30mm这一段曲线,钻进平稳,钻压在45n上下波动,在30m处,钻压开始上升,到35mm处钻压上升到最高处并开始趋于平稳,曲线30mm
‑
35mm之间的宽度刚好与岩心斜截面最低至最高点的距离对应,则可标定出连界面的产状;从35mm到70mm,钻压在250n上下波动。从实验可以看出,位移时间曲线与钻样取得的岩心有着很好的对应关系,即时深匹配度较好;通过分析钻进参数曲线的形状、频率、振幅以及趋势就可以得到例如结构面的产状或是地层的接触关系;结合这两条曲线,则可以在钻进过程中就可以快速得出试样的物理力学参数以及内部结构关系,图10即为最终生成的试验钻压
‑
位移曲线对比图。
再多了解一些
本文用于企业家、创业者技术爱好者查询,结果仅供参考。