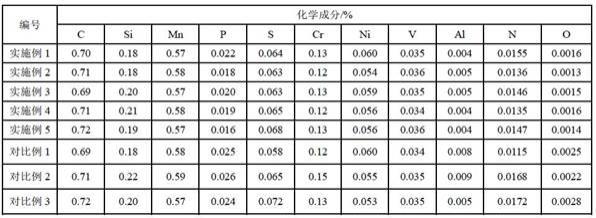
1.本发明涉及钢铁材料制造技术领域,具体是一种发动机连杆用钢及其生产方法。
背景技术:
2.随着汽车工业的飞速发展,发动机零部件设计与制造过程的高质量、高效率、低成本、低能耗已成为提高产品竞争力的唯一途径。传统、落后加工技术的生产模式已难以适应市场的变化,加工技术的变革成为必然的发展趋势及发展方向。许多新工艺打破常规,以构思新颖、效益显著为特点应运而生,满足了现代企业的要求。连杆裂解技术就是20世纪年代出现的一种先进的连杆加工新技术,与传统加工技术相比,该技术因具有大幅度提高产品质量、提高生产率、降低生产成本等突出优点而备受业界关注。
3.连杆作为发动机的重要零部件,在工作过程中承受着很高的周期性冲击力、惯性力和弯曲力。连杆的制造质量直接影响到发动机的性能和可靠性,这就要求连杆应具有高的强度、韧性和耐疲劳性能,以及很高的加工精度。其胀断特性决定了其需要较为严格的窄成分控制、合理的各项力学性能匹配,并采取微合金化方式控制晶粒度,生产难度大。
4.国内很多厂家在生产高碳、含硫、含氮、微合金发动机连杆用钢时,lf精炼炉采用高碱度渣料,这种高碱度渣系对钢中的s含量影响较大,尤其是s的收得率会受到较大影响,不容易稳定s窄范围控制。而钢中的n经过rh真空处理后处于较低水平,后期需要补加大量含氮合金或包芯线,开大底吹搅拌帮助合金融化,温降较大,且易造成钢水二次氧化。
5.中国发明专利申请号为200910062748.3,公开了低碳高硫易切削钢的生产工艺方法,其中精炼炉造低碱度渣,精炼渣的组成和重量比例为:cao 40
‑
50%,sio
2 15
‑
30%,al2o
3 20
‑
35%,mgo 5
‑
15%;精炼后期钢中除s以外的化学成分进入要求范围后,向精炼炉内喂s线,并保持钢包底吹氩的强度,s的回收率为75
‑
85%;钢中各元素的化学成分达到所需要求,温度达到1580
‑
1600℃后,向精炼炉中喂ca线或ca
‑
si线,软吹时间8
‑
15min,方可起坑调包上连铸平台。该专利中精炼渣采用低碱度,s成分易于控制,s的收得率高,但没有进行真空处理,钢水纯净度低,且不利于夹杂物控制。
6.中国发明专利申请号为200910063354.x,公开了一种含氮、硫非调质钢的生产方法,公开了精炼炉中精炼渣采用碱度为1.5
‑
3.0的中碱度的精炼渣,精炼渣的百分含量为:cao 40
‑
50%,sio
2 15
‑
20%,al2o
3 20
‑
25%,mgo 5
‑
10%,其它为不可避免的氧化物杂质。该专利提供的工艺路线简单,钢中增氮容易,节约合金;s成分易于控制,s的收得率高。但没有进行真空处理,钢水纯净度低,且不利于夹杂物控制,且精炼过程通过底吹氮气控制n,导致n的收得率不稳定,风险大。
7.《现 代 冶 金》中公开了一篇“c70s6by非调质钢中硫的窄成分控制技术”论文,该论文中阐述了c70s6by非调质钢转炉运用高碳和顶渣技术进行渣洗脱硫的方法,lf通过调整渣系以及后续控制软吹时间的工艺措施,准确实现了c70s6by钢中硫的窄成分控制。但该论文采用转炉炉后造预熔精炼渣,精炼炉前期碱度偏高,降低了渣子流动性,渣量大,且rh真空处理后喂入大量含氮、硫包芯线,操作繁琐、处理周期长,不利于大批量生产。
8.鉴于目前高碳、含硫、含氮、微合金发动机连杆用钢存在的上述不足,研发一种发动机连杆用钢及其生产方法是本技术领域亟待解决的技术问题。
技术实现要素:
9.本发明的目的就是为了解决了钢中s、n含量波动大的问题,提供一种发动机连杆用钢及其制备方法,本发明通过lf炉造低碱度渣,可以精准控制钢中的s含量;rh炉处理全程采用氮气驱动,可以保证整个rh真空处理过程,钢中n含量不会降低,从而精准控制钢中n含量;生产的钢中有合适的组织及夹杂物形态,具备良好的综合性能。
10.本发明是通过以下技术方案来实现的:本发明的一种发动机连杆用钢,其化学组分及其质量百分比为:c 0.69
‑
0.73%,si 0.15
‑
0.25%,mn 0.55
‑
0.60%,p≤0.045%,s 0.060
‑
0.070%,cr 0.10
‑
0.15%,ni 0.04
‑
0.08%,v 0.030
‑
0.040%,al≤0.010%,n 0.0120
‑
0.0160%,o≤0.0020%,其余为fe和不可避免的杂质;其生产工艺路线为:转炉冶炼
→
lf精炼炉精炼
→
rh真空炉精炼
→
连铸
→
轧制
→
缓冷。
11.优选地,本发明的化学组分及其质量百分比为:c 0.70%,si 0.18%,mn 0.57%,p 0.022%,s 0.064%,cr 0.13%,ni 0.060%,v 0.035%,al 0.004%,n 0.0155%,o 0.0016%,其余为fe和不可避免的杂质。
12.本发明的发动机连杆用钢性能参数为:rm 900
‑
1050mpa,rel≥550mpa,a≥10%,z≥20%,布氏硬度hb 280
‑
310。
13.本发明的一种发动机连杆用钢的生产方法,包括以下步骤:(1)转炉冶炼
①
冶炼终点时控制c 0.20
‑
0.40%,p≤0.025%,出钢温度t=1560
‑
1600℃,采用滑板挡渣;
②
出钢过程中向钢水中加入铝锭,每吨钢水铝锭的加入量为2.5
‑
3.0kg,其他元素按照化学成分要求进行配加;(2)lf精炼
①
精炼炉造低碱度渣,将碱度控制在1.2
‑
2.0,精炼渣的组成和重量百分比为cao 35
‑
45%,sio
2 25
‑
30%,al2o
3 10
‑
15%,mgo 5
‑
13%,其它为不可避免的氧化物杂质;
②
白渣保持时间≥15min,据钢水中s含量,加入硫化亚铁将s调至0.062
‑
0.068%,吊包至rh真空炉中;(3)rh真空炉精炼
①
rh真空处理全程采用氮气驱动,流量80
‑
100 nm3/h,极限真空度(小于67pa)保持时间≥10 min;
②
加入氮化硅铁1.2 kg/t,退到四级泵后,循环5
‑
10 min,控制n含量为0.0120
‑
0.0160 %,再加入覆盖剂,吊包至连铸;(4)连铸中包钢水过热度≤25 ℃,采用电磁搅拌和弱冷制度的连铸工艺,电磁搅拌电流为400a,频率为3.5 hz;结晶器冷却水量为150
‑
160 m3/h,二冷水比水量为0.8
‑
1.0 l/kg,200方连铸坯拉坯速度为1.2
‑
1.4 m/min,连铸坯矫直温度为950
‑
1000 ℃,铸坯切割后入坑缓
冷48 h,避开高温脆化区域,消除应力;(5)轧钢预热区温度≤850 ℃,加热区温度1140
‑
1190 ℃,均热区温度1130
‑
1180 ℃,总加热时间≥130 min;冷床保温罩开启角度30
°
,加快冷床步进速度,保证钢材剪切温度≥400 ℃;钢材及时入坑缓冷,保证φ50 mm及以上规格圆钢入坑温度≥400 ℃,φ50 mm以下规格圆钢入坑温度≥350 ℃,第一时间盖好缓冷盖,缓冷时间≥36 h方可起坑。
14.本发明的生产工艺设定的理由如下:本发明在转炉出钢时加入大量铝锭脱氧,是由于al是炼钢过程中最为经济有效的脱氧元素,脱氧效果好且耗时短,采用滑板挡渣可有效避免出钢过程下渣,造成钢水回磷。
15.在lf精炼炉造低碱度渣,是因为发动机连杆用钢要求钢中s含量在0.060
‑
0.070%,s含量范围窄,控制难度大。采用低碱度渣系,可以保持整个精炼过程s含量较为稳定,若s含量低于目标,则加入硫化亚铁进行增s。
16.本发明在rh真空处理全程采用氮气驱动,是因为发动机连杆用钢要求钢中n含量范围为0.0120
‑
0.0160%。n元素控制难度非常大,通过采用氮气驱动,退泵后循环一定时间,可以保证整个rh真空处理过程,钢中n含量不会降低,为成品n含量精准控制提供了保障。
17.本发明采用低过热度浇注,采用电磁搅拌和弱冷制度的连铸工艺,铸坯入坑缓冷36h以上,是由于本发明钢的c含量为0.69
‑
0.73%,高碳钢容易发生碳偏析,s、n含量均较高,铸坯在常规空冷过程中易产生裂纹,甚至发生严重开裂。
18.本发明控制铸坯加热温度在1130
‑
1190℃,总加热时间≥130min,是要保持足够高的加热温度,使c、si、mn、cr等元素充分溶解且均匀分布到高温奥氏体中,为获得均质化的钢材创造条件,又要防止高温奥氏体过分长大产生不良组织而恶化发明钢的性能。
19.本发明在钢材轧后入坑缓冷,是由于如果轧后冷却速度快,将形成贝氏体组织,大大缩小下游用户加工的工艺窗口,导致硬度超标,而且还会因热应力和组织应力叠加产生裂纹甚至断裂的风险。
20.本发明通过转炉出钢过程加入铝锭预脱氧,lf精炼炉全程造低碱度渣(1.2
‑
2.0);rh真空处理全程采用氮气驱动,流量80
‑
100 nm3/h,极限真空度(小于67 pa)保持时间≥10 min,加入含氮合金,退到四级泵后,循环5
‑
10 min,精准控制钢中s含量和n含量。连铸钢水过热度≤25 ℃,采用电磁搅拌和弱冷制度的连铸工艺,铸坯切割后入坑缓冷48 h,避开高温脆化区域,消除应力。轧钢预热区温度≤850 ℃,加热区温度1140
‑
1190 ℃,均热区温度1130
‑
1180 ℃,总加热时间≥130 min;冷床保温罩开启角度30
°
,加快冷床步进速度,保证钢材剪切温度≥400 ℃。钢材及时入坑缓冷,保证φ50 mm及以上规格圆钢入坑温度≥400 ℃,φ50 mm以下规格圆钢入坑温度≥350 ℃,第一时间盖好缓冷盖,缓冷时间≥36 h方可起坑。确保本发明钢有合适的组织及夹杂物形态,具备良好的综合性能。
附图说明
21.图1是本发明实施例1生产钢材中的硫化锰夹杂物的元素分析;图2是本发明实施例1生产钢材中的硫化锰夹杂物的形貌分析;图3是本发明实施例1生产钢材中的复合夹杂物的元素分析;图4是本发明实施例1生产钢材中的复合夹杂物的形貌分析;
图5是本发明实施例1生产的规格为φ55mm圆钢金相组织分析。
具体实施方式
22.下面结合实施例对本发明作进一步的详细说明,便于更清楚地了解本发明,但它们不对本发明构成限定。
23.实施例1本实施例的一种发动机连杆用钢,其化学组分及其质量百分比为:c 0.70%,si 0.18%,mn 0.57%,p 0.022%,s 0.064%,cr 0.13%,ni 0.060%,v 0.035%,al 0.004%,n 0.0155%,o 0.0016%,其余为fe和不可避免的杂质。
24.本实施例的一种发动机连杆用钢的生产方法,包括以下步骤:(1)转炉冶炼
①
冶炼终点时控制c 0.25 %,p 0.018 %,出钢温度t=1580 ℃,采用滑板挡渣;
②
出钢过程中向钢水中加入铝锭,每吨钢水铝锭的加入量为2.8 kg,其他元素按照化学成分要求进行配加;(2)lf精炼
①
精炼炉造低碱度渣,将碱度控制在1.5,精炼渣的组成和重量百分比为cao 42 %,sio
2 28 %,al2o312 %,mgo 9 %,其它为不可避免的氧化物杂质;
②
白渣保持时间15 min,据钢水中s含量,加入硫化亚铁将s调至0.064 %,吊包至rh真空炉中;(3)rh真空炉精炼
①
rh真空处理全程采用氮气驱动,流量90 nm3/h,极限真空度(小于67pa)保持时间12 min;
②
加入氮化硅铁1.2 kg/t,退到四级泵后,循环5 min,控制n含量为0.0155%,再加入覆盖剂,吊包至连铸;(4)连铸中包钢水过热度20 ℃,采用电磁搅拌和弱冷制度的连铸工艺,电磁搅拌电流为400a,频率为3.5 hz;结晶器冷却水量为155 m3/h,二冷水比水量为0.85 l/kg,200方连铸坯拉坯速度为1.2 m/min,连铸坯矫直温度为980 ℃,铸坯切割后入坑缓冷48 h,避开高温脆化区域,消除应力;(5)轧钢预热区温度750 ℃,加热区温度1160 ℃,均热区温度1150 ℃,总加热时间135 min;冷床保温罩开启角度30
°
,轧制的φ55 mm规格圆钢剪切温度为480 ℃,入坑温度为420℃,第一时间盖好缓冷盖,缓冷40 h方可起坑。
25.实施例1作为本发明的最佳实施例,通过lf精炼炉造低碱度渣,精准控制钢中s含量。rh真空炉采用氮气驱动,退泵循环等方法,精准控制钢中n含量,大幅度降低了钢中夹杂物。连铸采用低过热度浇注,减少偏析。轧钢加热温度窄范围控制,轧制后入坑缓冷,确保组织均匀,避免了异常组织及裂纹的产生,提高了材料的切削性能及疲劳性能。
26.本实施例生产的钢性能参数为:rm 1002 mpa、1004 mpa,rel 590 mpa、592 mpa,a 12.0%、12.0%,z 24%、23.5%,布氏硬度hb 289、292、292,得到的热轧态组织形态为珠光体和
铁素体,夹杂物为硫化锰和复合夹杂物。
27.将本实施例生产的钢材中的硫化锰进行元素分析和形貌分析,参见附图1和图2。从图1可以看出,钢材中的夹杂物主要成分为硫化锰;从图2可以看出,硫化锰在钢中呈断续条状分布,夹杂物长度为10~75μm,少量的硫化锰呈纺锤状,有利于本发明钢切削加工性能的提高。再将本实施例钢材中的复合夹杂物进行元素分析和形貌分析,参见附图3和图4。从图3和图4可以看出,复合夹杂物是以氧化物夹杂为形核点,并由硫化物包裹形成。因它对氧化物夹杂有包裹作用,有利于材料疲劳性能的提高。此外,我们还将本实施例生产的规格为φ55mm的圆钢进行金相组织分析,参见图5,从图5可以看出,本实施例生产的钢的热轧态组织为珠光体+少量铁素体组织,该组织较利于连杆涨断加工。
28.实施例2参照本发明的实施例1,本发明还进行了另外四个实施例,同时还按照传统工艺进行了一个对比例,实施例1
‑
5和对比例1中的化学成分列表参见下表1,实施例1
‑
5和对比例1中的工艺参数列表参见下表2,分别采用表1中的化学成分和表2中的工艺参数制备得到的钢材性能测试结果参见下表3。
29.表1本发明各实施例和对比例的化学成分表2本发明各实施例和对比例的关键工艺参数表3本发明各实施例及对比例的性能、组织和夹杂物检测分析结果列表
说明:表3中力学性能和硬度为1050℃保温0.5小时的正火态性能。rm:900~1050mpa,rel:≥550mpa,a≥10%,z≥20%,布氏硬度hb:280~310。
30.从表1及表2可以看出,相对于传统模式即对比例1
‑
3,本发明实施例1
‑
5的成分控制范围窄,尤其是s和n含量极为稳定。本发明实施例1
‑
5的lf精炼采用低碱度炉渣,钢中s含量得以稳定控制,rh真空炉精炼通过采用流量为90 nm3/h左右的氮气驱动,确保钢中n波动范围在20ppm以内。而对比例1
‑
3,精炼炉采用高碱度炉渣,钢中的s含量波动大(0.058
‑
0.072%),而rh真空炉精炼未采用氮气驱动,钢中的n含量无法稳定控制,波动范围大(0.0115
‑
0.0172%)。
31.从表3可以看出,本发明实施例1
‑
5的热轧态组织均为珠光体+铁素体,没有异常组织,夹杂物主要为硫化锰 复合夹杂物。相对于传统模式,本发明钢的组织及夹杂物形态利于连杆涨断加工,具备较好的切削性能及疲劳性能。而对比例1
‑
3的热轧态组织均为珠光体+贝氏体+铁素体,夹杂物主要为硫化锰 氧化铝 球状氧化物,组织中存在贝氏体,会降低钢材的切削性能,夹杂物散乱无章,严重影响钢材的疲劳寿命。
32.连杆作为发动机的重要零部件,在工作过程中承受着很高的周期性冲击力、惯性力和弯曲力。连杆的制造质量直接影响到发动机的性能和可靠性,这就要求连杆应具有高的强度、韧性和耐疲劳性能,以及很高的加工精度。采用本发明生产的发动机连杆用钢工艺可靠性强,钢材质量稳定,适用于大批量生产,优势明显。
33.本发明的实施例仅为最佳例举,并非对技术方案的限定性实施。
再多了解一些
本文用于企业家、创业者技术爱好者查询,结果仅供参考。