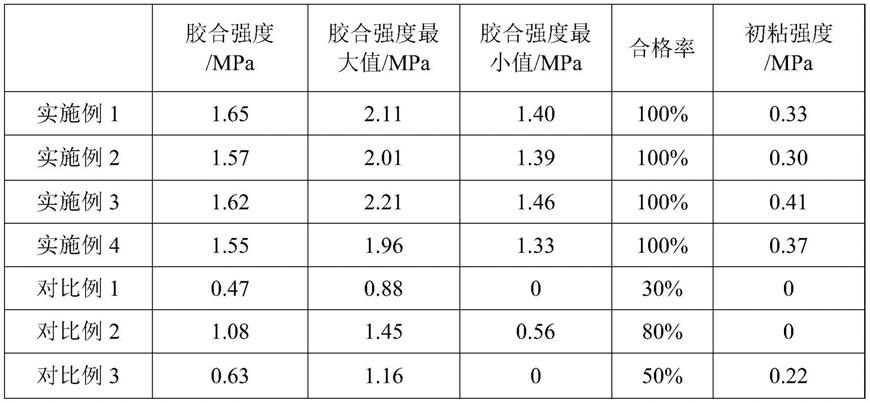
1.本发明属于木材粘合剂领域,具体涉及一种用于实木复合人造板的粘合剂组合物。
背景技术:
2.人造板是以木材或其他非木材植物为原料,经一定机械加工分离成各种单元材料,经施加胶粘剂后,重组热压而制成的板材或模压制品。我国是人造板生产大国,2018年人造板总产量为2.99亿立方米,比2017年增长1.4%左右,中国人造板产品产量占全球人造板总产量的50%-60%。2018年,我国胶合板产量为1.7898亿立方米,同比增长4.1%。过去10年我国胶合板类产品产量年均增速达到17.5%,仍是人造板中增幅最快的板种。实木复合地板年平均产量为1600万平方米,约22万立方米。
3.我国木材工业胶黏剂消耗量超过整个胶黏剂总量的90%,最主要品种为脲醛树脂胶黏剂uf(含改性),其次是酚醛树脂胶黏剂,另外三聚氰胺胶和异氰酸酯胶也有部分使用。三醛胶在生产和使用时会释放对人体有害的游离苯酚、甲醛等物质,尤其是在室内装修和家具板材中,因为甲醛并不完全缩聚,固化树脂因水解或者分解释放出游离甲醛,逐步向四周散发而造成室内环境污染,甲醛持续释放时间可达10-15年。我国于2017年对“室内装饰装修材料人造板及其制品中甲醛释放限量”强制性国家标准《gb/t18580》进行了修改,甲醛限量要求更加严格。家用实木复合地板与生活相关,无醛人造板是未来发展的趋势。
4.异氰酸酯属于非醛类粘合剂,目前已经在定向刨花板、刨花板、纤维板及集成材等方面得到广泛应用,但是限于技术及设备原因还未在胶合板中广泛应用,只是作为固化剂配合其他组分进行使用。使用异氰酸酯粘合剂最显著的优点就是无甲醛,制品中甲醛释放量与原木的甲醛释放量检测值基本一致;异氰酸酯板材另外一个优势就是耐水性好,可以制备耐水性实木复合板,达到i类板材耐沸水煮的要求。
5.专利cn103740324b公开了一种人造板用胶粘剂,以及它的制备方法和应用。所述人造板用胶粘剂的原料包括:分散介质、蛋白类物质、碱性化合物和交联增强剂;所述交联增强剂为单宁—乙二醛树脂。发明提供的人造板用胶粘剂不含甲醛,主要原料来源于可再生物质,是一种环保型人造板用胶粘剂;彻底解决了使用胶粘剂时甲醛污染的问题,又同时保证了胶粘剂的耐水性和胶合强度等实用性。发明中胶黏剂虽然改善了热压时间长的问题,但制胶工艺复杂,胶液呈现较强碱性,板坯初粘差,制的板材不能达到i类板要求。
6.专利cn105295740b公开了一种无醛的液态胶粘剂及人造板加工方法,该液态胶粘剂由无机材料的氯化镁水溶液和氧化镁粉末,按照1:1比例混合调配而成;所述氯化镁水溶液是由氯化镁粉末或卤片与水,按照1:1~1:3比例制备而成,且氯化镁粉末或卤片的纯度为45%~99%。胶液无初粘性,无法满足后期修补翻板工作,制备的胶合板性能也无法达到i类板要求。
7.专利cn105885773a公开了一种人造板用生物质无醛胶粘剂及其制备方法,发明中以豆粉为主要粘合剂,经过系列改性过程制备无醛粘合剂,制板无甲醛释放。但制胶工艺复
杂,生产时板坯边部易干胶,初粘变差,且制品耐水性差,容易发霉。
8.专利cn101524857a公开了一种异氰酸酯喷涂制备胶合板的方法,具有成本低,热压时间短,单板含水率要求低等优势。但是喷涂过长会造成环境污染,对人体造成伤害;异氰酸酯固化后粘附设备表面,对设备也会造成损害;组坯后的板材无初粘性,无法进行表板修复工作,对热压过程也造成很多不便。
9.因此,需要一种粘合剂配方体系,能够满足粘合剂适用期要求,同时保证组坯后具有较好的初粘性,同时制板满足无醛环保要求,耐水等级达到i类板要求。
技术实现要素:
10.本发明目的在于提供一种异氰酸酯基无醛粘合剂组合物,该粘合剂能够满足目前api(水性乳液 异氰酸酯)体系对粘合剂适用期要求,同时铺装后板坯,冷压后具有较好的初粘性,能够满足后生产工艺要求。所述异氰酸酯基无醛粘合剂用于制造实木复合人造板,板材性能达到i类板耐水要求,合格率高,制品甲醛释放量达到无醛板标准。
11.为实现以上发明目的,本发明采用以下技术方案:
12.一种用于实木复合人造板的粘合剂组合物,所述组合物包含以下组分:
13.改性异氰酸酯
ꢀꢀꢀꢀꢀ
100质量份;
14.粉体填料
ꢀꢀꢀꢀꢀꢀꢀꢀꢀ
20-100质量份,优选30-60质量份;
15.防腐剂
ꢀꢀꢀꢀꢀꢀꢀꢀꢀꢀꢀ
0.1-2质量份,优选0.5-1质量份;
16.其中,所述改性异氰酸酯为铌酸盐改性的异氰酸酯。
17.本发明中,所述改性异氰酸酯的制备方法包含以下步骤:
18.(1)将铌酸盐进行烘干处理;
19.(2)将铌酸盐混入溶剂后加到异氰酸酯中,混合吸附异氰酸酯中的-nco基团后脱除溶剂,得到改性异氰酸酯粘合剂。
20.本发明中,步骤(1)所述铌酸盐选自铌酸锌、铌酸镁、铌酸钠、铌酸钾、铌酸锶、铌酸锂和铌酸铅中的一种或多种,优选铌酸锌。铌原子序数41,属周期系
ⅴ
b族,铌元素可以以多价态形式存在。-nco基团属于强极性基团,在50-90℃下,nbo
3-可以对-nco基团产生吸附作用,起到抑制-nco基团降低其活性的作用,在室温下减少-nco与水的反应,降低胶液粘度上升速度。热压过程,在高温及水蒸气作用下,体系能量提高,铌酸根与-nco解除吸附,-nco与水及木材发生反应,不影响其胶合强度;同时热压过程中,铌酸盐还能够催化大分子纤维素降解产生小分子羟基物质,增强胶合强度。
21.本发明中,步骤(1)铌酸盐用量为异氰酸酯量的1wt%-20wt%,优选5wt%-10wt%。
22.本发明中,步骤(1)所述铌酸盐处理温度120-130℃。
23.本发明中,步骤(1)处理后铌酸盐含水率低于0.1%,以铌酸盐总质量计。
24.本发明中,步骤(2)所述异氰酸酯选自脂肪族异氰酸酯和/或芳香族异氰酸酯,优选芳香族异氰酸酯,更优选多亚甲基多苯基异氰酸酯(pmdi,聚合mdi)。
25.本发明中,步骤(2)所述溶剂为乙酸乙酯。
26.本发明中,步骤(2)脱除溶剂后所述改性异氰酸酯中乙酸乙酯含量≤100ppm。
27.本发明中,步骤(2)所述改性异氰酸酯粘度为300-1000cp。
28.本发明中,步骤(2)所述铌酸盐混入溶剂后滴加到异氰酸酯中。
29.本发明中,步骤(2)所述滴加过程中升温,升至50-90℃,优选70-80℃。
30.本发明中,步骤(2)所述混合后保持时间为2-4h。
31.本发明中,所述粉体填料为糊精、面粉、淀粉、豆粉、硅藻土、石膏粉、果壳粉、滑石粉和碳酸钙中的一种或多种,优选糊精和其他任一种或多种粉体填料,更优选糊精和面粉;优选的,所述糊精与面粉的质量比为1:1-1:2。使用填料的目的主要在于提高胶液的固体含量,控制涂胶过程水分的引入量,从而使热压排气段顺利进行;同时一些植物性淀粉蛋白粉体可以提高胶液的初始粘结性,使得铺装后的实木复合板在冷压后具有较好的粘结,方便后加工工序进行。
32.糊精通常分为三类:白糊精、黄糊精和英国胶或称“不列颠胶”。糊精是以淀粉为原料经烘烤氧化或加酸分解而生成的部分降解的低聚物。降解时,部分1,4-苷键断裂,生成许多短分子链,并发生1,6连接,产生许多支链。随降解条件和降解程度不同可产生不同品种。白糊精是在200℃左右用稀硝酸处理玉米淀粉的产品,它的色泽洁白。黄糊精是在180℃左右用盐酸水解淀粉而成,色泽呈黄褐色。现阶段使用的api粘合剂及豆胶,主要问题是单板铺装冷压后板坯初粘性差,对后续工序造成很大影响,降低生产效率,尤其在单板低含水率的情况下更加明显。使用糊精可以提高胶液的初粘性,尤其是和面粉复配使用时,效果更加明显。组合物中的改性异氰酸酯和糊精及面粉的组合物存在协同作用,铌酸改性pmdi活性降低,减少体系粘度的提升速度,提高胶液的适用期;少量的pmdi和填料中的-oh反应,可以适当提高胶液对板材的吸附性能,使板坯初粘性得到提高。使用本发明所述复合填料可以改善胶液对实木类薄板的粘结性能,冷压后的板坯初粘性好,可以按照脲醛胶工艺进行后续操作,节省大量时间。
33.本发明的另一目的在于提供一种加工实木复合人造板的方法。
34.一种加工实木复合人造板的方法,采用所述的粘合剂组合物,包含以下步骤:
35.s1:将粉体填料加入水混合,冷却后加入改性异氰酸酯和防腐剂,得到含水的粘合剂组合物;优选的,所述s1中,水的用量为100-300质量份,优选150-250质量份,以改性异氰酸酯100质量份计;
36.s2:将粘合剂组合物通过辊涂、刮刀涂布、帘式涂布或喷洒中的任一种或多种方式施加于实木复合板单元表面;
37.s3:经组坯、陈放、冷压、修补、热压和裁切工艺制得实木复合人造板。
38.本发明的又一目的在于提供一种实木复合人造板。
39.一种实木复合人造板,采用所述的粘合剂组合物或采用所述的加工方法制备,所述实木复合人造板包含木质人造单板、复合地板、竹地板、强化地板、细木工板、集成材和胶合板中的一种或多种。
40.与现有技术相比,本发明的积极效果在于:
41.(1)本发明的异氰酸酯基粘合剂胶液初粘性得到提高,单板低含水率在5%以下时,涂胶后4小时板坯冷压,初粘性依然可以满足后续生产要求,远超豆胶及市场其他无醛胶的初粘性;
42.(2)胶液适用期得到提高,适用期从1h可以延长至4h,满足长时间生产的要求;
43.(3)生产的板材胶合耐水解、强度高,经水处理后,胶合强度仍能大于1.55mpa(标
准要求为0.7mpa),耐水等级达到i类板要求,且所制板满足无醛环保要求。
具体实施方式
44.下面结合实施例进一步说明本发明的实施方案,但是本发明不限于所列出的实施例,还应包括在本发明所要求的权利范围内其它任何公知的改变。
45.多亚甲基多苯基异氰酸酯(pmdi):官能度2.7,25℃粘度为180-250cp,-nco含量30.5wt%-32wt%,万华化学集团股份有限公司;
46.桉木单板:厚度2.2mm,含水率3wt%-5wt%,幅面40cm*40cm,鲁丽胶合板厂;
47.面粉:白色粉末,普通级,水分≤8%,灰分≤0.7%,烟台台华面粉厂;
48.白糊精:白色粉末,水分≤8%,纯度≥90%,济南浩然化工科技有限公司;
49.铌酸锌:白色粉末,800-1000目,纯度≥99%,广州市德力化工有限公司;
50.铌酸镁:白色粉末,800-1000目,纯度≥99%,广州市德力化工有限公司;
51.丙酸钙:白色粉末,800-1000目,有效物质含量≥99.5%,济南豪邦化工有限公司;
52.钛白粉:白色粉末,800-1000目,二氧化钛含量≥95%,廊坊奇彩颜料有限公司;
53.豆胶:胶合板用,豆粉:固化剂=1:2,宁波中科朝露新材料有限公司。
54.高速分散机,上海普申化工机械有限公司,型号eds1000;
55.热压机,苏州新协力企业发展有限公司,型号by602x2/2;
56.推台锯,青岛金三木木工机械有限公司,型号mj6128gy;
57.水浴锅,常州智博瑞仪器制造有限公司,型号hh-4;
58.粘度计,brookfield有限公司,型号dv2tlvkj0;
59.万能试验机,高铁检测仪器(东莞)有限公司,型号ai-7000m。
60.实施例1
61.改性异氰酸酯制备包括以下步骤:
62.(1)将铌酸锌进行烘干处理;烘干温度120℃,烘干时间为4小时,含水率为0.07%;
63.(2)将10g(1质量份)铌酸锌混入10g乙酸乙酯后滴加到1000g(100质量份)异氰酸酯中,滴加过程中升温,50℃下保持4h后脱除溶剂,得到改性异氰酸酯粘合剂,测试其粘度为300cp,乙酸乙酯含量为75ppm。
64.实木复合人造板制备过程包括以下步骤:
65.s1:将100g(10质量份)的白糊精和100g(10质量份)的面粉填料加入75℃的1500g(150质量份)水混合30min,冷却后加入改性异氰酸酯1000g(100质量份)和5g(0.5质量份)丙酸钙防腐剂,得到含水的粘合剂组合物;
66.s2:将粘合剂组合物在35℃烘箱陈放4h后进行制板,按照涂胶量单面160g/m2称取组合物,利用刮板均匀涂抹至桉木单板表面;
67.s3:经组坯、陈放、冷压、修补、热压和裁切工艺制得实木复合人造板;其中陈放时间为4h,冷压面压力为0.7mpa,冷压时间30min,热压温度110℃,热压压力0.8mpa,热压时间15min。
68.实施例2
69.改性异氰酸酯制备包括以下步骤:
70.(1)将铌酸锌进行烘干处理;烘干温度120℃,烘干时间为4小时,含水率为0.06%;
71.(2)将200g(20质量份)铌酸锌混入200g乙酸乙酯后滴加到1000g(100质量份)异氰酸酯中,滴加过程中升温,90℃下保持2h后脱除溶剂,得到改性异氰酸酯粘合剂,测试其粘度为1000cp,乙酸乙酯含量为85ppm。
72.实木复合人造板制备过程包括以下步骤:
73.s1:将150g(15质量份)的白糊精和150g(15质量份)的面粉填料加入75℃的1500g(150质量份)水混合30min,冷却后加入改性异氰酸酯1000g(100质量份)和5g(0.5质量份)丙酸钙防腐剂,得到含水的粘合剂组合物;
74.s2:将粘合剂组合物在35℃烘箱陈放4h后进行制板,按照涂胶量单面160g/m2称取组合物,利用刮板均匀涂抹至桉木单板表面;
75.s3:经组坯、陈放、冷压、修补、热压和裁切工艺制得实木复合人造板;其中陈放时间为4h,冷压面压力为0.7mpa,冷压时间30min,热压温度110℃,热压压力0.8mpa,热压时间15min。
76.实施例3
77.改性异氰酸酯制备包括以下步骤:
78.(1)将铌酸镁进行烘干处理;烘干温度130℃,烘干时间为4小时,含水率为0.03%;
79.(2)将50g(5质量份)铌酸镁混入50g乙酸乙酯后滴加到1000g(100质量份)异氰酸酯中,滴加过程中升温,70℃下保持2h后脱除溶剂,得到改性异氰酸酯粘合剂,测试其粘度为472cp,乙酸乙酯含量为80ppm。
80.实木复合人造板制备过程包括以下步骤:
81.s1:将500g(50质量份)的白糊精和500g(50质量份)的面粉填料加入75℃的2500g(250质量份)水混合30min,冷却后加入改性异氰酸酯1000g(100质量份)和10g(1质量份)丙酸钙防腐剂,得到含水的粘合剂组合物;
82.s2:将粘合剂组合物在35℃烘箱陈放4h后进行制板,按照涂胶量单面160g/m2称取组合物,利用刮板均匀涂抹至桉木单板表面;
83.s3:经组坯、陈放、冷压、修补、热压和裁切工艺制得实木复合人造板;其中陈放时间为4h,冷压面压力为0.7mpa,冷压时间30min,热压温度110℃,热压压力0.8mpa,热压时间15min。
84.实施例4
85.改性异氰酸酯制备包括以下步骤:
86.(1)将铌酸镁进行烘干处理;烘干温度120℃,烘干时间为4小时,含水率为0.04%;
87.(2)将200g(20质量份)铌酸镁混入200g乙酸乙酯后滴加到1000g(100质量份)异氰酸酯中,滴加过程中升温,80℃下保持4h后脱除溶剂,得到改性异氰酸酯粘合剂,测试其粘度为972cp,乙酸乙酯含量为90ppm。
88.实木复合人造板制备过程包括以下步骤:
89.s1:将200g(50质量份)的白糊精和400g(50质量份)的面粉填料加入75℃的2500g(250质量份)水混合30min,冷却后加入改性异氰酸酯1000g(100质量份)和10g(1质量份)丙酸钙防腐剂,得到含水的粘合剂组合物;
90.s2:将粘合剂组合物在35℃烘箱陈放4h后进行制板,按照涂胶量单面160g/m2称取组合物,利用刮板均匀涂抹至桉木单板表面;
91.s3:经组坯、陈放、冷压、修补、热压和裁切工艺制得实木复合人造板;其中陈放时间为4h,冷压面压力为0.7mpa,冷压时间30min,热压温度110℃,热压压力0.8mpa,热压时间15min。
92.对比例1
93.用亚硫酸氢钠处理异氰酸酯:
94.s1:按质量比5:4:1称取水1000g、大豆蛋白粉800g和氢氧化钠200g,在90℃下搅拌并分多次加入大豆蛋白粉,降解2小时得到大豆蛋白降解液,出料保存。然后,在20℃下向异氰酸酯中逐滴滴加亚硫酸氢钠溶液,并通氮气进行保护,异氰酸酯与溶液的质量分别为190g、810g,保持3小时后得到亚硫酸氢钠处理的异氰酸酯。将处理后的异氰酸酯1000g、改性豆胶2000g、500g面粉混合均匀,得到胶液。
95.s2:将粘合剂组合物在35℃烘箱陈放4h后进行制板,按照涂胶量单面160g/m2称取组合物,利用刮板均匀涂抹至桉木单板表面;
96.s3:经组坯、陈放、冷压、修补、热压和裁切工艺制得实木复合人造板;其中陈放时间为4h,冷压面压力为0.7mpa,冷压时间30min,热压温度110℃,热压压力0.8mpa,热压时间15min。
97.对比例2
98.本对比例中改性异氰酸酯制备方法同实施例1,但填料不同,实木复合人造板制备过程包括以下步骤:
99.s1:将300g钛白粉加入到1500g(150质量份)水混合30min,冷却后加入改性异氰酸酯1000g(100质量份)和5g(0.5质量份)丙酸钙防腐剂,得到含水的粘合剂组合物;
100.s2:将粘合剂组合物在35℃烘箱陈放4h后进行制板,按照涂胶量单面160g/m2称取组合物,利用刮板均匀涂抹至桉木单板表面;
101.s3:经组坯、陈放、冷压、修补、热压和裁切工艺制得实木复合人造板;其中陈放时间为4h,冷压面压力为0.7mpa,冷压时间30min,热压温度110℃,热压压力0.8mpa,热压时间15min。
102.对比例3
103.对比例3中直接使用pmdi进行组合物制备,具体方法如下:
104.s1:将150g(15质量份)的白糊精和150g(15质量份)的面粉填料加入75℃1500g(150质量份)水混合30min,冷却后加入pmdi 1000g(100质量份)和5g(0.5质量份)丙酸钙防腐剂,得到含水的粘合剂组合物;
105.s2:将粘合剂组合物在35℃烘箱陈放4h后进行制板,按照涂胶量单面160g/m2称取组合物,利用刮板均匀涂抹至桉木单板表面;
106.s3:经组坯、陈放、冷压、修补、热压和裁切工艺制得实木复合人造板;其中陈放时间为4h,冷压面压力为0.7mpa,冷压时间30min,热压温度110℃,热压压力0.8mpa,热压时间15min。
107.将得到的板材样品根据国标《gbt 17657-2013人造板及饰面人造板理化性能试验方法》进行样品制备。样品按照i类板材测试方法进行胶合强度测试,即将样品浸入沸水中煮4h,然后在60℃的鼓风干燥箱内干燥16h,取出后再用沸水煮4h,随后在低于30℃冷水中处理1h得到试样,利用万能试验机进行胶合强度测试。样品条直接使用万能试验机进行性
能测试。性能测试结果如表1所示。实施例中所制板满足无醛环保要求,耐水等级达到i类板要求。
108.表1板材性能测试
[0109][0110]
实施例1-4使用本发明所述组合物进行胶合板生产,采用改性异氰酸酯作为固化剂,配制胶液后在35℃烘箱陈放4h后进行制板;异氰酸酯与水反应少,体系粘度增长较慢,制板性能较高,满足国标要求,沸水煮后胶合强度可达1.50mpa以上。对比例1采用现有异氰酸酯豆胶技术进行胶合板生产,同等工艺下,制板的初粘性很差,无初粘强度;胶液生产过程有大量的so2放出,严重影响现场环境;制板后板材也不能耐沸水煮,无法达到i类板要求。对比例2中未使用本发明所述的填料组合物,采用钛白粉作为填料,同等工艺下板坯陈放4h后基本散坯,无初粘强度,难以满足生产要求。对比例3中未使用改性异氰酸酯,配胶陈放过程异氰酸酯与水反应造成胶液体系粘度迅速增加,胶液流动性变差,胶合强度大幅降低。
[0111]
以上实施例仅用以本发明的优选实施方式进行描述,而非对本发明保护范围的限制,尽管参照较佳实施例对本发明作了详细说明,本领域的普通技术人员应当理解,对本发明的技术方案进行修改或者等同替换作出的各种变型和改进,均应落入本发明的权利要求书确定的保护范围内。
再多了解一些
本文用于企业家、创业者技术爱好者查询,结果仅供参考。