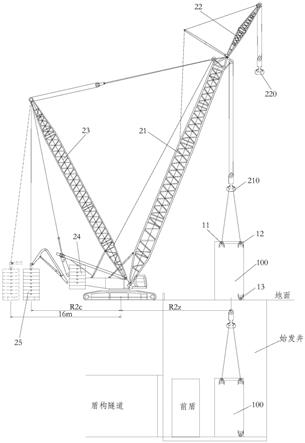
1.本发明涉及一种大直径盾构机中盾整体的下井组装工艺。
背景技术:
2.随着地下空间的开发,盾构技术已经广泛应用于软土层的地铁、隧道、市政管道等工程领域。盾构机的下井吊装是盾构施工中重要的一个环节,盾构机所具有的超大、超重的特点使其下井成为盾构施工中最大的一个危险因素。盾构机主要由刀盘、主驱动、前盾、中盾、尾盾、连接桥、拼装机、7节后配套拖车等部件组成。例如,直径为8~9m的盾构机尺寸大,重量重,因此盾构机需要分件吊装,前盾分为下半块、驱动部件和上半块,中盾和盾尾均沿圆周方向分成一个底部块、左侧块和右侧块。中盾又分中盾前体和中盾后体,中盾前体与中盾后体之间设有铰接密封和紧急气囊,因此铰接密封和紧急气囊不是整圈式,而是在圆周上也为三段式。
3.中盾组装时,首先在地面分别把中盾前后体的底部块、左侧块和右侧块一一对应地拼装好成两个独立的中盾前、后体,并在中盾后体的底部圆周上安装对应三段式的铰接密封和紧急气囊;其次,在地面安装台上把两个独立的中盾前后体拼装成中盾整体后,把中盾整体纵向分解为中盾底部块、左侧块和右侧块;然后,将中盾底部块、中盾左侧块和中盾右侧块分别吊装下井,在井下钢套筒基座上拼装成中盾整体,最后,将各段铰接密封和紧急气囊在中盾前体的三个硫化窗口内进行硫化连接成整圈,在用螺栓把盖板固定在硫化窗口上。
4.上述中盾组装时的缺点如下:
5.1、分段式铰接密封需要中盾在井下安装后,在盾壳的硫化窗口内进行硫化(高温熔化)连接成整圈,增加安装及硫化工序;
6.2、由于硫化窗口内有橡胶材质的铰接密封和紧急气囊,不能用电焊固定三块窗口盖板,只能采用螺栓固定盖板,使盖板与硫化窗口之间存在缝隙,容易出现往盾体外漏油脂或泥水侵入铰接密封腔中,给地下盾构施工带来隐患风险;
7.3、铰接密封为唇形密封圈,因此硫化连接处容易产生错位而形成为薄弱处,不能承受很大的摩擦力和拉力;
8.4、分段式紧急气囊不能采用硫化工艺等连接,在硫化窗口始终存在接头隔断,不能形成整环贯通的气腔,在紧急情况下充气后易存在泄漏处,使紧急气囊失效。
技术实现要素:
9.本发明的目的在于克服现有技术的缺陷而提供一种大直径盾构机中盾整体的下井组装工艺,它不仅能安装整圈式铰接密封和紧急气囊,有效保障了铰接密封和紧急气囊的功能,还能安全可靠地将中盾整体准确地吊入始发井下的设定位置。
10.本发明的目的是这样实现的:一种大直径盾构机中盾整体的下井组装工艺,适用的中盾整体的外径d=8~9m,高度h=4~4.5m,重量g=268~270t;所述下井组装工艺采用
400t履带起重机吊装,该起重机上的主臂长为36m,主钩的载荷为400t,副臂长为9m,副钩的载荷为200t,超起桅杆臂长为30m,车身配重20t,转台配重110t,超起平衡重230t,超起平衡重半径为12~16m。
11.本发明的下井组装工艺按照以下流程进行:中盾分块地面组装、中盾整体翻转为水平状态、中盾铰接密封安装、中盾整体翻转为垂直状态和中盾整体吊装下井;
12.进行中盾分块地面组装流程时,是将102t重的中盾底部块、11t重的中盾h纵梁、85t重的中盾左侧块和70t重的中盾右侧块组装成中盾整体,采用400t履带起重机的标准工况且主钩单独吊装,按照以下步骤进行:
13.步骤一,在所述中盾底部块的两端环向法兰面的前后部各自通过螺栓安装一个拼装吊耳;在所述中盾左侧块的外表面上和中盾右侧块的外表面上各自均布地焊接四个拼装吊耳;
14.步骤二,先将起重机安装在始发井口一旁的中盾拼装场地上,并在拼装场地上固定好基座,接着将起重机的主钩半径调整到13m,并在起重机的主钩用四根钢丝绳和四个卸扣一一对应地挂在所述中盾底部块的四个拼装吊耳上,再将中盾底部块吊装到在基座上,然后将中盾底部块上的四个拼装吊耳拆除;
15.步骤三,将起重机的主钩半径保持在13m,接着起重机的主钩用两根钢丝绳捆绑在中盾h纵梁上,再并将中盾h纵梁吊到所述中盾底部块上,然后将中盾h形纵梁与中盾底部块连接;
16.步骤四,先将起重机的主钩半径调整到16m,接着起重机的主钩用四根钢丝绳和四个卸扣一一对应地挂在中盾右侧块上的四个拼装吊耳上,将中盾右侧块吊装到所述中盾底部块上,然后将中盾右侧块分别与中盾底部块和中盾h纵梁连接;
17.步骤五,将起重机的主钩半径调整到15m,接着起重机的主钩用四根钢丝绳和四个卸扣一一对应地挂在中盾左侧块上的四个拼装吊耳上,将中盾左侧块吊装到所述中盾底部块上,然后将中盾左侧块分别与中盾底部块、中盾h纵梁和中盾右侧块连接,形成中盾整体;中盾整体包括中盾前体和中盾后体,位于中盾后体前部的铰接环插置在位于中盾前体后部的铰接腔内,安装在铰接腔内的铰接油缸与铰接环铰接;
18.步骤六,先在中盾前体的前顶部外表面以对称于盾构机的垂直中心线的方式焊接一对第一吊耳,在中盾后体的后顶部外表面上以对称于盾构机的垂直中心线的方式焊接一对第二吊耳,在中盾后体的后底部外表面上以对称于盾构机的垂直中心线的方式焊接一对第三吊耳,一对第三吊耳与一对第二吊耳处于同一个立面,再割除中盾左侧块上的四个拼装吊耳和中盾右侧块上的四个拼装吊耳;
19.进行中盾整体翻身为水平状态流程时,采用400t履带起重机带超起工况且主、副臂带钩复合吊装,按照以下步骤进行:
20.步骤一,先按起重机的吊装负载率要小于80%的规范要求,求得中盾整体吊装总载荷为268~270
÷
0.8=335~337.5t,从起重机的载荷表查得大于并接近335~337.5t的主钩加副钩总载荷为340t,并对应主钩半径r1z=12m,主钩载荷为400t,副钩半径r1f=15.7m,副钩载荷为200t,并得到中盾整体的重心吊装半径为(12 15.7)
÷
2=13.85m;
21.步骤二,先在起重机的超起桅杆上挂好230t的超起平衡重,并将超起平衡重半径调整到r1c=12m,且使超起平衡重的底部离地0.2米以下,再将主钩半径调整到rz=12m,副
钩半径调整到rf=15.7m,起重机的主钩用四根钢丝绳一一对应地挂在一对第一吊耳和一对第二吊耳上,起重机的副钩用两根钢丝绳一一对应地挂在一对第三吊耳上,起重机的主钩和副钩缓缓起升,使中盾整体底部离地20cm后静置5分钟,再协调操作副钩起升、主钩下降,使中盾整体在空中逆时针翻转90
°
达到水平状态,然后起重机的主钩和副钩同时缓慢下降,将中盾整体以水平状态放在地面上;
22.进行中盾铰接密封安装流程时,采用400t履带起重机的标准工况且主钩单独吊装,按照以下步骤进行:
23.步骤一,先拆除230t的超起平衡重,接着将起重机的副钩与一对第三吊耳脱钩,同时将主钩与一对第一吊耳脱钩挂到一对第三吊耳上,再通过中盾前体内的铰接油缸将中盾后体顶升,然后拆除铰接油缸与中盾后体的连接,最后起重机的主钩将中盾后体拔出中盾前体并将中盾后体放在地面上;
24.步骤二,在中盾后体的铰接环的外表面上的三道拼接纵缝和中盾前体的铰接腔的内壁面上的三道拼装纵缝各自进行水密焊,并打磨光滑,再在中盾后体的铰接环上安装两道整圈式铰接密封和一道整圈式紧急气囊;
25.步骤三,起重机的主钩将中盾后体重新吊起并插装到中盾前体的铰接腔中,再将铰接油缸与中盾后体连接;
26.进行中盾整体翻转为垂直状态流程时,采用400t履带起重机带超起工况且主、副臂带钩复合吊装,先在起重机上挂好230t的超起平衡重,并将超起平衡重半径调整到r1c=12m,且使超起平衡重的底部离地0.2米以下,再将主钩半径调整到r1z=12m,副钩半径调整到r1f=15.7m,起重机的主钩与一对第三吊耳脱钩并挂在一对第一吊耳上,副钩与一对第三吊耳挂钩,主钩和副钩同时缓缓起升,使中盾整体的底部离地20cm后静置5分钟,再协调操作主钩上升、副钩下降,使中盾整体在空中顺时针翻转90
°
达到直立状态,并保持中盾整体的底部始终距离地面20cm,然后将副钩与一对第三吊耳脱钩;
27.进行中盾整体吊装下井流程时,采用400t履带起重机带超起工况且主钩单独吊装,按照以下步骤进行:
28.步骤一,先拆除中盾整体内10根共20吨重的推进油缸,使中盾整体的重量减到248~250t,接着按起重机的吊装负载率要小于80%的规范要求,求得中盾整体吊装总载荷为248~250
÷
0.8=310~337.5t,从起重机的载荷表查得大于并接近310~337.5t的主钩载荷为315.6t,对应的主钩半径r2z=16m;
29.步骤二,分多次协调操作主臂变幅和超起平衡重变幅,使主钩半径调整到r2z=16m,并将超起平衡重半径调整到r2c=13m,在操作超起平衡重变幅的过程中要确保超起平衡重的底部距离地面不大于20cm;再缓慢操作起重机的转台,将中盾整体转到位于始发井口的正上方,再缓慢下降中盾整体至始发井下的钢套筒基座上,待中盾整体固定牢靠后再松钩,然后将拆除的10根推进油缸安装到中盾整体内,中盾整体吊装下井完成。
30.上述的大直径中盾整体的下井组装工艺,其中,进行中盾整体吊装下井流程的步骤二时,在中盾整体的两侧各系一条引导绳,由专人牵引,防止中盾整体在下井过程中发生旋转和磕碰。
31.本发明的大直径盾构机中盾整体的下井组装工艺,具有以下特点:
32.1、先将中盾的三个分块在地面上组装成中盾整体,接着将中盾整体翻转为水平状
态放置于地面上,再将中盾前体和中盾后体拆分,并安装整圈式铰接密封和紧急气囊,然后将中盾前体和后体组合成中盾整体,最后将中盾整体翻身为垂直状态后吊入始发井,这样就能安装整圈式铰接密封和紧急气囊,省去了硫化连接分段式铰接密封和紧急气囊的工序,有效保障了铰接密封和紧急气囊的功能。
33.2、在将中盾整体翻转为水平状态、将中盾整体翻身为垂直状态以及将中盾整体吊装入井时都采用400t履带起重机的超起工况吊装,整个过程安全可靠,使中盾整体准确地吊入始发井下的设定位置,实现超大吨位的中盾整体的入井组装。
附图说明
34.图1是本发明在进行中盾分块地面组装流程的步骤二时的状态图;
35.图2是本发明在进行中盾分块地面组装流程的步骤四时的状态图;
36.图3是本发明在进行中盾分块地面组装流程的步骤五时的状态图;
37.图4是本发明在进行中盾分块地面组装流程的步骤六时的结构图;
38.图5是图4中的a
‑
a向视图;
39.图6是本发明在进行中盾整体翻转为水平状态流程的步骤二时的状态图;
40.图6a是图6中的b向视图;
41.图7是本发明在进行中盾整体翻转为水平状态流程的步骤二时的状态图;
42.图8是本发明在进行中盾铰接密封安装流程的步骤一时的状态图;
43.图9是本发明在进行中盾铰接密封安装流程的步骤一时的状态图;
44.图10是本发明在进行中盾整体吊装下井流程的步骤二时的状态图。
具体实施方式
45.下面将结合附图对本发明作进一步说明。
46.请参阅图1至图10,本发明的大直径盾构机中盾整体的下井组装工艺,适用的中盾整体的外径d=8~9m,高度h=4~4.5m,重量g=268~270t;
47.本发明的大直径盾构机中盾整体的下井组装工艺采用400t履带起重机200吊装,该起重机200上的主臂21长为36m,主钩220的载荷为400t,副臂22长为9m,副钩220的载荷为200t,超起桅杆臂23长为30m,车身配重为20t,转台配重24为110t,超起平衡重25为230t,超起平衡重半径为12~16m;
48.本发明的大直径盾构机中盾整体的下井组装工艺,按照以下流程进行:中盾分块地面组装、中盾整体翻转为水平状态、中盾铰接密封安装、中盾整体翻转为垂直状态和中盾整体吊装下井;
49.进行中盾分块地面组装流程时,是将102t重的中盾底部块101、11t重的中盾h纵梁102、85t重的中盾左侧块103和70t重的中盾右侧块104组装成中盾整体100,采用400t履带起重机200的标准工况且主钩单独吊装,按照以下步骤进行:
50.步骤一,在中盾底部块101的两端环向法兰面的前后部各自通过螺栓安装一个拼装吊耳;在中盾左侧块103的外表面上和中盾右侧块104的外表面上各自均布地焊接四个拼装吊耳;
51.步骤二,先将起重机200安装在始发井口一旁的中盾拼装场地上,并在拼装场地上
固定好基座300,接着将起重机的主钩210半径调整到13m,并在起重机的主钩210用四根钢丝绳和四个55t的卸扣一一对应地挂在中盾底部块101的四个拼装吊耳上,再将中盾底部块101吊装到在基座300上(见图1),然后将中盾底部块101上的四个拼装吊耳拆除;
52.步骤三,将起重机的主钩210半径保持在13m,接着起重机的主钩210用两根钢丝绳捆绑在中盾h纵梁102上,再并将中盾h纵梁102吊到中盾底部块101上,然后将中盾h形纵梁102与中盾底部块101连接;
53.步骤四,先将起重机的主钩210半径调整到16m,接着起重机的主钩210用四根钢丝绳和四个55t的卸扣一一对应地挂在中盾右侧块104上的四个拼装吊耳上,将中盾右侧块104吊装到中盾底部块101上,然后将中盾右侧块104分别与中盾底部块101和中盾h纵梁102连接(见图2);
54.步骤五,将起重机的主钩201半径调整到15m,接着起重机的主钩210用四根φ72mm
×
8m的钢丝绳和四个55t的卸扣一一对应地挂在中盾左侧块103上的四个拼装吊耳上,将中盾左侧块103吊装到中盾底部块101上,然后将中盾左侧块103分别与中盾底部块101、中盾h纵梁102和中盾右侧块104连接,形成中盾整体100(见图3);中盾整体100包括中盾前体100a和中盾后体100b,位于中盾后体100b前部的铰接环插置在位于中盾前体100a后部的铰接腔内,安装在铰接腔内的铰接油缸与铰接环铰接;
55.步骤六,在中盾前体100a的前顶部外表面以对称于盾构机的垂直中心线的方式焊接一对载荷为100t第一吊耳11,在中盾后体100b的后顶部外表面上以对称于盾构机的垂直中心线的方式焊接一对载荷为150t第二吊耳12,一对第一吊耳11之间的水平间距和一对第二吊耳12之间的水平间距均为4.1m,一对第一吊耳11与一对第二吊耳12的垂直间距为2.75m;在中盾后体100b的后底部外表面上以对称于盾构机的垂直中心线的方式焊接一对载荷为150t的第三吊耳13,该一对第三吊耳13之间的水平间距为5.26m,一对第三吊耳13与一对第二吊耳12处于同一个立面(见图4和图5),并割除中盾左侧块103上的四个拼装吊耳和中盾右侧块104上的四个拼装吊耳;
56.进行中盾整体翻身为水平状态流程时,采用400t履带起重机带超起工况且主、副臂带钩复合吊装,按照以下步骤进行:
57.步骤一,先按起重机的吊装负载率要小于80%的规范要求,求得中盾整体吊装总载荷为268~270
÷
0.8=335~337.5t,从起重机的载荷表查得大于并接近335~337.5t的主钩加副钩总载荷为340t,并对应主钩半径r1z=12m,主钩载荷为400t,副钩半径r1f=15.7m,副钩载荷为200t,并得到中盾整体的重心吊装半径r1=(12 15.7)
÷
2=13.85m;
58.步骤二,先在起重机的超起桅杆上挂好230t的超起平衡重25,并将超起桅杆半径调整到r1c=12m,且使超起平衡重25的底部离地0.2米以下,再将主钩半径调整到r1z=12m,副钩半径调整到r1f=15.7m,起重机的主钩210用四根φ96mm
×
12m钢丝绳和四个85t的卸扣一一对应地挂在一对第一吊耳11和一对第二吊耳12上,起重机的副钩220用两根φ96mm
×
12m钢丝绳和两个85t的卸扣一一对应地挂在一对第三吊耳13上(见图6和图6a),起重机的主钩210和副钩220缓缓起升,使中盾整体100底部离地20cm后静置5分钟,试吊检查吊机刹车、吊索具及地基承载力,再协调操作副钩220起升、主钩210下降,使中盾整体100在空中逆时针翻转90
°
达到水平状态,然后起重机的主钩210和副钩220同时缓慢下降,将中盾整体100以水平状态放在地面上(见图7);
59.进行中盾铰接密封安装流程时,采用400t履带起重机的标准工况且主钩单独吊装,按照以下步骤进行:
60.步骤一,先拆除230t的超起平衡重25,接着将起重机的副钩220与一对第三吊耳13脱钩,同时将主钩210与一对第一吊耳11脱钩挂到一对第三吊耳13上,再通过中盾前体100a内的铰接油缸将中盾后体100b顶升(见图8),然后拆除铰接油缸与中盾后体100b的连接,最后起重机的主钩210将中盾后体100b拔出中盾前体100并将中盾后体100b放在地面上(见图9);
61.步骤二,在中盾后体100b的铰接环的外表面上的三道拼接纵缝和中盾前体100a的铰接腔的内壁面上的三道拼装纵缝各自进行水密焊,并打磨光滑,再在中盾后体100b的铰接环上安装两道整圈式铰接密封和一道整圈式紧急气囊;
62.步骤三,起重机的主钩210将中盾后体100b重新吊起并插装到中盾前体100a的铰接腔中,再将铰接油缸与中盾后体100b连接;
63.进行中盾整体翻转为垂直状态流程时,采用400t履带起重机带超起工况且主、副臂带钩复合吊装,先在起重机上挂好230t的超起平衡重25,并将超起平衡重半径调整到r1c=12m,且使超起平衡重25的底部离地0.2米以下,再将主钩半径调整到r1z=12m,副钩半径调整到r1f=15.7m,起重机的主钩210与一对第三吊耳13脱钩并挂在一对第一吊耳11上,副钩220与一对第三吊耳13挂钩,主钩210和副钩220同时缓缓起升,使中盾整体100的底部离地20cm后静置5分钟,试吊检查吊机刹车、吊索具及地基承载力,再协调操作主钩210上升、副钩220下降,使中盾整体100在空中顺时针翻转90
°
达到直立状态,并保持中盾整体100的底部始终距离地面20cm,然后将副钩220与一对第三吊耳13脱钩,中盾整体离地翻身完成;
64.进行中盾整体吊装下井流程时,采用400t履带起重机带超起工况且主钩单独吊装,按照以下步骤进行:
65.步骤一,由于中盾整体的重量为268~270t,为了适应400t履带起重机的工况,先拆除中盾整体内10根共20吨重的推进油缸,使中盾整体的重量减到248~250t,接着按起重机的吊装负载率要小于80%的规范要求,求得中盾整体吊装总载荷为248~250
÷
0.8=310~337.5t,从起重机的载荷表查得大于并接近310~337.5t的主钩载荷为315.6t,对应的主钩半径r2z=16m;
66.步骤二,分多次协调操作主臂21变幅和超起平衡重25变幅,使主钩半径调整到r2z=16m,并将超起平衡重半径调整到r2c=13m,在操作超起平衡重25变幅的过程中要确保超起平衡重25的底部距离地面不大于20cm;再缓慢操作起重机200的转台,将中盾整体100转到位于始发井口的正上方,在中盾整体100的两侧各系一条引导绳,由专人牵引,防止中盾整体100在下井过程中发生旋转和磕碰,再缓慢下降中盾整体100至始发井下的钢套筒基座上(见图10),待中盾整体100固定牢靠后再松钩,然后将拆除的10根推进油缸安装到中盾整体内,中盾整体吊装下井完成。
67.以上实施例仅供说明本发明之用,而非对本发明的限制,有关技术领域的技术人员,在不脱离本发明的精神和范围的情况下,还可以作出各种变换或变型,因此所有等同的技术方案也应该属于本发明的范畴,应由各权利要求所限定。
再多了解一些
本文用于企业家、创业者技术爱好者查询,结果仅供参考。