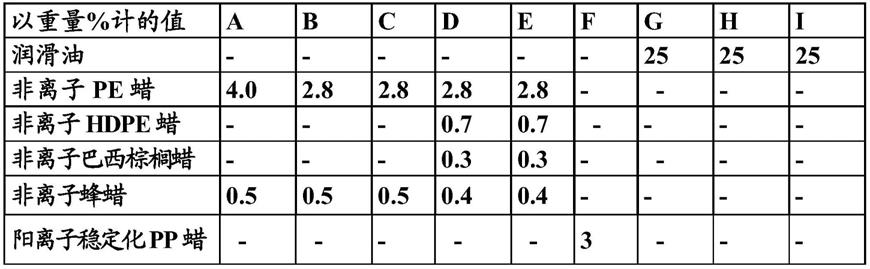
预处理冷成型用金属基材的简化方法和用于该目的的反应性润滑剂
1.本发明涉及一种预处理冷成型用金属基材的简化方法,一种相应反应性润滑剂和一种已经由该方法预处理的金属基材及其用途。
2.冷成型在低于待成型的成型体的再结晶温度的温度下,通常在至多约450℃的温度下进行。加热可能仅通过成型过程中作用于涂敷的金属成型体坯件(blank)和工具之间的摩擦力以及由于材料流动的内摩擦力发生,但任选也通过预热待成型的成型体而发生。
3.然而,待成型的成型体的温度通常最初是环境温度,即约10
‑
32℃。然而,若事先将待成型的成型体加热至例如在650
‑
850℃,850
‑
1250℃或650
‑
1250℃范围内的温度,则该成型方法称为亚热成型(semihot forming)或锻造(forging)。此外,升至高压通常在冷成型过程中发生,例如在钢的情况下在200mpa至1gpa范围内并且有时甚至高达2gpa。
4.作为待成型的成型体,主要使用带材、板材、嵌条、线材、线束、具有复杂形状的成型部件、轴套、型材如中空或实心型材、管材、圆坯、圆盘、棒材、撑条或圆柱。该成型体原则上可以由任何金属材料构成。该成型体通常基本由钢构成。
5.冷成型操作首要的是包括拉伸(拉伸成型)、旋压、压薄(ironing,成型至最终尺寸)和/或深拉、螺纹滚压和/或打线(thread striking)、压制如冷流成型(加压成型)和/或冷锻(cold upset forging)。
6.尽管通常将非反应性成型油用于金属成型体在非常低形变程度以及相应地轻力下的冷成型,但在更高形变程度的情况下通常在成型体和工具之间使用至少一个涂层作为分隔层,以避免成型体和工具冷焊在一起。在后一情形中,通常对成型体提供至少一个润滑剂涂层或润滑剂组合物,以降低成型体表面和成型工具之间的摩擦阻力。
7.作为分隔层,通常在锌盐存在下在磷酸溶液中施用高度结晶涂层;该涂层在盛行的温度下不会熔融,化学和物理连接于金属基材(例如通过化学吸附)并且由于在成型过程中在工具和基材之间起分隔作用而防止冷焊。
8.用于该分隔层上的润滑剂组合物可以是各种各样的。该润滑剂层优选使用包含皂、油和/或有机聚合物和/或共聚物的润滑剂组合物产生。
9.(水基)润滑剂组合物具有碱性ph,而施用该分隔层的传统浴具有酸性ph。为了延长浴寿命,绝对必要的是在两次处理操作之间进行漂洗并且任选地,借助合适中和剂除去过量酸。这导致可以按如下构成的常规工艺顺序:
10.1)清洁(和漂洗),
11.2)酸洗(和漂洗),
12.3)活化,
13.4)用磷酸锌转化处理,
14.5)漂洗/中和,
15.6)润滑,
16.7)任选地,干燥。
17.在步骤1中例如可能源自新的钢基材生产的所有类型残渣借助强碱性清洁剂在非
常高的温度下除去。
18.步骤2包括表面的酸洗,这包括除垢和除锈。取决于所用酸的类型,温度可以在环境温度至60℃的范围内。
19.一种经典的磷化方法通常要求活化以适应磷酸盐晶体的尺寸。该步骤3优选使用水基晶种溶液在室温至55℃下进行。
20.然后在步骤4中借助酸性水基磷酸锌溶液进行转化处理。随后的步骤5包括漂洗步骤以及随后的任选中和。
21.步骤6是润滑。取决于该润滑剂,这可以在水基聚合物存在下在55
‑
60℃下进行,在水基皂存在下在70
‑
85℃下进行或者在水基载盐晶体存在下在超过70℃下进行。
22.在最后步骤7中,任选进行强制干燥。在水基润滑剂的情况下,这有时是必要的,因为被处理的待成型体在一些情况下被紧密包裹,例如线束,以避免水基残渣。
23.寻找理想的工艺效率驱使冷成型工业朝向要求更少处理步骤的新技术发展。
24.步骤3和4的简化描述于wo 2015/055756 a1中。在这里由于在步骤4中使用不含磷酸盐的转化涂层而可以省略步骤3。因为步骤4中的浴组合物也比在锌磷化的情况下要简单,该方法具有更少的控制参数,这使得操作更简单。
25.现有技术中已经尝试在一个处理操作中施用转化层(步骤4)和润滑剂层(步骤6)。因此,de 2102295 b2描述了一种反应性润滑油,在这种情况下在表面上形成含铁的磷酸盐层。然而,该组合物包含小于20重量%的水;因此它具有含油主相并且因此不能称为水基。
26.润滑剂的典型施用在冷成型工业由开放式操作浴进行。油基体系导致更高的voc污染(voc=挥发性有机化合物),因为在该处理过程中并非不显著量的油可能汽化。此外,油基体系在职业卫生方面出现问题,因为它们易燃并且在>150℃的闪点下必须分类为危险品。水基,即乳化体系另一方面通常由于大于35重量%的水含量而没有火灾荷载(fire load)方面的问题。同样,voc污染更低,因为该体系的最大温度由水的沸点限制。
27.因此,本发明的目的首先是要提供一种用于冷成型的水基预处理方法,其中要求尽可能少的处理步骤。
28.正如惊人地发现的那样,可以将转化处理步骤(步骤4)和润滑步骤(步骤6)合并成一个步骤并且因此省略其间的中和(步骤5):
29.1)清洁(和漂洗),
30.2)酸洗(和漂洗),和
31.3)转化处理和润滑的合并。
32.为了在水基处理操作中组合施用高度结晶转化层和润滑剂层,不得不克服一些困难。因此,润滑剂大多具有强碱性ph,而酸性侵蚀对于转化层的沉积至关重要。
33.其次,本发明的目的是要提供一种用于冷成型的预处理方法,其中在步骤3中施用的合并的转化和润滑剂层具有如此高的层重以及还有对金属基材如此强的附着力以至于甚至在成型操作之后它仍以足够量存在,即在成型操作过程中它不会以使得工具与工件的有效分隔和摩擦系数的有效降低不再出现的程度除去。
34.为了确保在步骤3中施用的合并的转化和润滑剂层在成型操作之后仍以足够量存在,在本发明的情形中已经发现所述合并层需要像纯结晶性,例如基于草酸盐的转化层一样与金属基材的表面既是化学结合的,即以晶体和表面之间的化学键形式,又是物理结合
的,即通过吸附,而不是正如对于可以得到的非反应性润滑剂的情况那样是纯物理的。
35.上述目的已经由一种预处理冷成型用金属基材的本发明方法实现,其中待成型的金属基材依次(successively):
36.1)优选机械或化学清洁和随后漂洗,
37.2)优选酸洗和随后漂洗,
38.3)与包含如下组分的水基酸性反应性润滑剂接触:
39.a)草酸,
40.b)至少一种包含硝基胍和/或至少一种铁(iii)源的促进剂,和
41.c)至少一种成膜剂、至少一种蜡和/或至少一种乳化的润滑油,以及
42.4)任选干燥,其中该至少一种成膜剂选自乙烯、丙烯、苯乙烯、(甲基)丙烯酸、(甲基)丙烯酸酯、乙烯基胺、乙烯基甲酰胺、乙烯基吡咯烷酮、乙烯基己内酰胺、乙酸乙烯酯、乙烯基咪唑和/或环氧化物的均聚物和共聚物及其盐以及还有聚氨酯、聚酰胺、聚乙烯亚胺、聚胺及其盐,
43.其中该至少一种蜡选自非离子蜡和阳离子稳定化蜡,以及
44.其中该至少一种乳化的润滑油选自合成油、矿物油、植物油和动物油。
45.由于在冷成型工业中润滑剂的施用总是在浸渍浴中进行,出于安全原因通常要求该类润滑剂组合物不易燃,即具有>150℃的闪点,并且因此大大避免挥发性有机化合物(voc)。
46.因此,步骤3中的水基合并处理操作有利的是基本没有voc,即没有向步骤3中的反应性润滑剂中加入voc如挥发性油。
47.定义:
48.当在本发明上下文中说明待成型的金属基材“依次”进行所示处理步骤时,这并不排除在所示处理步骤之前、之间和/或之后进行一个或多个其他处理步骤,即例如其他漂洗步骤的可能性。然而,在优选实施方案中不进行在冷成型之前进行的其他处理步骤。
49.对本发明目的而言,“水基”是指相应组合物,尤其是酸性反应性润滑剂包含大于35重量%的水。
[0050]“反应性润滑剂”对本发明的目的而言是一种与金属基材反应并且因此在该基材上形成合并的转化和润滑剂层的润滑剂。
[0051]
对本发明目的而言,“草酸”也包括草酸的单重或双重脱质子形式。
[0052]
对本发明目的而言,“铁(iii)源”优选是水溶性铁(ii)盐如硝酸铁(iii)。然而,与适合产生铁(iii)离子的氧化物组合的水溶性铁(ii)盐也可以作为铁(iii)源。
[0053]“成膜剂”对本发明目的而言是其中单个聚合物链物理交联并且具有粘弹性能的均聚物或共聚物。
[0054]“(甲基)丙烯酸”对本发明目的而言是甲基丙烯酸和/或丙烯酸,而“(甲基)丙烯酸酯”相应地是甲基丙烯酸酯和/或丙烯酸酯。
[0055]
对本发明的目的而言,“蜡”应理解为一种在20℃下可捏合,是脆硬性固体,具有粗到细晶体结构,就颜色而言是半透明到不透明但不是玻璃质的,在40℃以上熔融而不分解,在略高于熔点下是流动液体(低粘度),具有强烈温度依赖性稠度和溶解度并且可在温和压力下抛光的材料。若不满足上述性能中的不止一种,则该材料相应地不是蜡。该蜡对本发明
目的而言优选借助非离子性和/或阳离子性物质在水溶液中乳化。
[0056]
对本发明目的而言,“非离子蜡”尤其也可以是在酸性介质中由非离子基团或者非离子性物质如表面活性剂,更优选非离子性物质,尤其是非离子表面活性剂稳定化的蜡,从而使该蜡以蜡乳液形式存在。
[0057]“阳离子稳定化蜡”对本发明目的而言是一种在酸介质中由阳离子基团或阳离子性物质如表面活性剂,更优选阳离子性物质,尤其是阳离子表面活性剂稳定化的蜡,从而使该蜡以蜡乳液形式存在。
[0058]“合并的转化和润滑剂层”对本发明目的而言首先是在其自身中组合了转化层和润滑剂层的性能的化学均相层。然而,它也可以是在相互之上或者在相互邻近处具有化学非均相区域,即具有转化层的区域和具有润滑剂层的区域的涂层。
[0059]
当在本发明上下文中就重量浓度(g/l或重量%)使用表述“作为x计算”—其中x在每种情况下是具体所示的特定化合物时,这具有下列含义:当使用替换化合物(不是x)时,它应当以如对x那样在考虑其分子量下由在每种情况下具体所示重量浓度(g/l或重量%)计算的摩尔浓度使用。
[0060]
待成型金属基材例如可以是带材(对本领域熟练技术人员而言也已知为“卷材”)、板材、任选预拉伸的线材、线束、具有复杂形状的成型部件、轴套、型材如中空或实心型材、管材、圆坯、圆盘、棒材、撑条、圆柱、嵌条、坯件或半成品。对本领域熟练技术人员而言,嵌条是圆盘或者一段线材、线束或撑条。
[0061]
待成型金属基材原则上可以由任何金属材料构成。它优选主要,即在大于50mol%的程度上由选自铁、钢、铝、铝合金、铜、铜合金、镁、镁合金、钛和钛合金的金属或金属合金构成。待成型金属基材更优选由铁材料如钢、合金钢或不锈钢构成。
[0062]
在优选在本发明方法中进行的步骤1中,首先机械或化学清洁金属基材。化学清洁优选通过在70
‑
90℃下浸入水基碱性清洁浴中10
‑
30分钟而进行,而机械清洁优选借助干或湿除垢或颗粒喷砂进行。
[0063]
随后漂洗金属基材。漂洗优选借助去离子水或自来水进行。
[0064]
然后在在同样优选进行的步骤2中酸洗金属基材。酸洗优选通过在高达约70℃下浸入水基酸性酸洗浴中数秒至30分钟而进行。酸洗通常在任选被抑制的盐酸、硫酸或磷酸中进行。它可以在一个浴中进行,但也可以在浴级联中进行。
[0065]
然后漂洗金属基材。漂洗在这里优选借助去离子水或自来水进行。
[0066]
作为组分a),本发明方法的步骤3中的反应性润滑剂优选包含2
‑
500g/l,特别优选5
‑
100g/l,非常特别优选10
‑
50g/l草酸,在每种情况下作为二水合草酸计算。
[0067]
草酸优选以更便宜和更少吸湿的二水合草酸加入反应性润滑剂中。
[0068]
步骤3中的反应性润滑剂包含至少一种包含硝基胍和/或至少一种铁(iii)源的促进剂作为组分b)。这里的硝基胍含量优选在0.01
‑
20g/l,特别优选0.5
‑
10g/l,非常特别优选1.0
‑
5g/l范围内,而铁(iii)的含量作为硝酸铁(iii)计算优选在0.0004
‑
2g/l,特别优选0.04
‑
2g/l,非常特别优选0.4
‑
2g/l范围内。
[0069]
因此,在优选实施方案中,反应性润滑剂包含:
[0070]
a)2
‑
500g/l,优选10
‑
50g/l草酸,在每种情况下作为二水合草酸计算,和
[0071]
b)0.01
‑
20g/l,优选1.0
‑
5g/l硝基胍和/或0.0004
‑
2g/l,优选0.4
‑
2g/l铁(iii),
[0072]
作为硝酸铁(iii)计算,加上组分c)。
[0073]
反应性润滑剂优选包含至少一种包含至少一种铁(iii)源的促进剂作为组分b)。铁(iii)源的存在具有的优点是形成相对细的层,即具有相对小晶体(直径:大约3
‑
5μm)的层,其中层形成更快速进行,因而要求更短的气体时间(gas time,更少的气体放出、更少的材料和化学品损失)。特别合适的铁(iii)源是硝酸铁(iii),这是因为其特别好的溶解性、其易得性及其良好的促进效果。
[0074]
当步骤3中反应性润滑剂的组分c)包含至少一种选自乙烯、丙烯、苯乙烯、(甲基)丙烯酸、(甲基)丙烯酸酯、乙烯基胺、乙烯基甲酰胺、乙烯基吡咯烷酮、乙烯基己内酰胺、乙酸乙烯酯、乙烯基咪唑和/或环氧化物的均聚物和共聚物及其盐以及还有聚氨酯、聚酰胺、聚乙烯亚胺、聚胺及其盐的成膜剂时,这些成膜剂在反应性润滑剂中的总含量优选在0.01
‑
100g/l,特别优选0.5
‑
30g/l,非常特别优选1
‑
20g/l范围内。
[0075]
当组分c)包含至少一种选自非离子蜡和阳离子稳定化蜡的蜡时,这些蜡在反应性润滑剂中的总含量优选在0.1
‑
300g/l,特别优选0.1
‑
150g/l,非常特别优选5
‑
70g/l范围内。
[0076]
当组分c)包含至少一种乳化的润滑油时,乳化的润滑油的总含量优选在1
‑
50重量%,特别优选10
‑
40重量%,非常特别优选20
‑
30重量%范围内,作为纯油计算并且基于整个反应性润滑剂。
[0077]
在第一优选实施方案中,步骤3中该反应性润滑剂的组分c)包含至少一种选自乙烯、丙烯、苯乙烯、(甲基)丙烯酸、(甲基)丙烯酸酯、乙烯基胺、乙烯基甲酰胺、乙烯基吡咯烷酮、乙烯基己内酰胺、乙酸乙烯酯、乙烯基咪唑和/或环氧化物的均聚物和共聚物及其盐以及还有聚氨酯、聚酰胺、聚乙烯亚胺、聚胺及其盐的成膜剂。上述成膜剂的存在具有的优点是所得润滑薄膜锚固在基材上并且因此具有更大硬度和稳定性。此外,得到更均匀的层。
[0078]
在第一特别优选实施方案中,组分c)仅包含至少一种选自乙烯、丙烯、(甲基)丙烯酸、(甲基)丙烯酸酯、乙烯基胺、乙烯基甲酰胺、乙烯基吡咯烷酮、乙烯基己内酰胺、乙酸乙烯酯、乙烯基咪唑和/或环氧化物的均聚物和共聚物及其盐以及还有聚乙烯亚胺、聚胺及其盐,尤其选自乙烯基吡咯烷酮的均聚物和共聚物的成膜剂,但不包含其他成膜剂。上述成膜剂,尤其是乙烯基吡咯烷酮的均聚物和共聚物具有的优点是对酸特别稳定,这导致步骤3中的水基酸性反应性润滑剂在冷成型方法中通常出现的温度下,甚至在0.15
‑
1.5范围内的非常低ph下具有特别低的发生相分离以及发生质子化和失稳的倾向并且当仅包含这些成膜剂中的至少一种时具有高盐含量。该至少一种成膜剂的重均分子量,尤其是在聚乙烯基吡咯烷酮(例如可以以k 17p得到,德国basf)的情况下,更优选在1000
‑
700,000g/mol,特别优选3000
‑
300,000g/mol,非常特别优选4000
‑
47500g/mol范围内。
[0079]
在第二特别优选实施方案中,组分c)包含至少一种选自聚乙烯
‑
聚丙烯共聚物,聚乙烯和聚丙烯均聚物,尤其是聚乙烯均聚物,以及乙烯基胺
‑
乙烯基甲酰胺共聚物的成膜剂。例如可以以9030(basf,德国)得到的乙烯基胺
‑
乙烯基甲酰胺共聚物在这里是非常特别有用的。
[0080]
在第二优选实施方案中,在步骤3中该反应性润滑剂的组分c)包含至少一种选自非离子蜡和阳离子稳定化蜡的蜡。上述蜡的存在具有的优点是它仅在熔融状态下,即在成
型过程中形成润滑薄膜。这里优选在每种情况下在酸介质中由至少一种非离子表面活性剂稳定化的非离子蜡,同时优选在每种情况下在酸介质中由至少一种阳离子表面活性剂稳定化的阳离子稳定化蜡。因此,步骤3中的反应性润滑剂优选含有至少一种非离子或阳离子表面活性剂。这也适用于下列特别优选的实施方案。
[0081]
在第一特别优选实施方案中,组分c)仅包含至少一种选自非离子蜡和阳离子稳定化蜡,尤其选自阳离子稳定化蜡的蜡,但不包含其他蜡。上述蜡,尤其是阳离子稳定化蜡具有的优点是对酸特别稳定,这导致步骤3中的水基酸性反应性润滑剂在冷成型方法中通常出现的温度下,甚至在0.15
‑
1.5范围内的非常低ph下具有特别低的发生相分离以及发生质子化和失稳的倾向并且当仅包含这些蜡中的至少一种时具有高盐含量。聚丙烯蜡的水分散体(例如aquacer 1041,byk,德国)和/或w
ü
konil o
‑
33a(s
ü
ddeutsche emulsions
‑
chemie gmbh,德国)以及还有褐煤蜡(例如licowax kst,clariant,德国)在这里是特别有用的。
[0082]
在第二特别优选实施方案中,组分c)包含至少一种优选选自非离子蜂蜡、非离子聚乙烯蜡、非离子hdpe蜡和褐煤蜡,特别优选选自非离子蜂蜡(例如aquacer 561,byk,德国)、非离子聚乙烯蜡和非离子hdpe蜡(例如aquacer 517,德国byk)的非离子蜡。这里“hdpe”是高密度聚乙烯,其由于相对未支化的聚合物链而具有高密度,优选在0.94
‑
0.97g/cm3范围内。
[0083]
至少一种蜡优选包含至少3种,更优选至少5种具有不同熔点的蜡。由于涵盖由其得到的优选至少50℃,更优选至少65℃的更大熔点范围,这些蜡在每种情况下在不同成型温度下熔融和润滑,结果优化了在不同成型要求下的润滑性能。在成型过程中的高应力通常导致更高温度,而低应力伴随着更低温度。此外,局部不同的应力以及因此温度也可能出现在待成型部件上。
[0084]
在第三优选实施方案中,步骤3中反应性润滑剂的组分c)包含至少一种选自乙烯、丙烯、苯乙烯、(甲基)丙烯酸、(甲基)丙烯酸酯、乙烯基胺、乙烯基甲酰胺、乙烯基吡咯烷酮、乙烯基己内酰胺、乙酸乙烯酯、乙烯基咪唑和/或环氧化物的均聚物和共聚物及其盐以及还有聚氨酯、聚酰胺、聚乙烯亚胺、聚胺及其盐的成膜剂,以及还有至少一种选自非离子蜡和阳离子稳定化蜡的蜡。以此方式得到均匀且非常好地附着并且也最佳地润滑的层。这里优选在酸介质中在每种情况下由至少一种非离子表面活性剂稳定化的非离子蜡,同时优选在酸介质中在每种情况下由至少一种阳离子表面活性剂稳定化的阳离子稳定化蜡。因此,步骤3中的反应性润滑剂优选包含至少一种非离子或阳离子表面活性剂。这也适用于下面的特别优选实施方案。
[0085]
在第一特别优选实施方案中,组分c)仅包含至少一种选自乙烯、丙烯、(甲基)丙烯酸、(甲基)丙烯酸酯、乙烯基胺、乙烯基甲酰胺、乙烯基吡咯烷酮、乙烯基己内酰胺、乙酸乙烯酯、乙烯基咪唑和/或环氧化物的均聚物和共聚物及其盐以及聚乙烯亚胺、聚胺及其盐,尤其选自乙烯基吡咯烷酮的均聚物和共聚物的成膜剂,并且还仅包含至少一种选自非离子蜡和阳离子稳定化蜡,尤其选自阳离子稳定化蜡的蜡,但不包含其他成膜剂且不包含其他蜡。上述成膜剂和蜡具有的优点是对酸特别稳定,这导致步骤3中的水基酸性反应性润滑剂在冷成型方法中通常出现的温度下,甚至在0.15
‑
1.5范围内的非常低ph下具有特别低的发生相分离以及发生质子化和失稳的倾向并且当仅包含这些成膜剂和蜡时具有高盐含量。还已发现至少3种,优选至少5种具有不同熔点的蜡的上述组合在这里是有利的。
[0086]
在第二特别优选实施方案中,组分c)包含至少一种选自聚乙烯
‑
聚丙烯共聚物,聚乙烯和聚丙烯均聚物,尤其是聚乙烯均聚物,以及乙烯基胺
‑
乙烯基甲酰胺共聚物,优选选自乙烯基胺
‑
乙烯基甲酰胺共聚物的成膜剂,以及还有至少一种选自非离子蜂蜡、非离子聚乙烯蜡和非离子hdpe蜡的蜡。还已发现至少3种,优选至少5种具有不同熔点的蜡的上述组合在这里是有利的。
[0087]
在第四优选实施方案中,步骤3中反应性润滑剂的组分c)包含至少一种乳化的润滑油。
[0088]
至少一种乳化的润滑油优选选自合成油、矿物油和植物油,更优选合成油和矿物油。一种合适的矿物油例如是shell gravex 913(荷兰shell)。
[0089]
至少一种乳化的润滑油优选具有在20
‑
1000mpas,尤其是50
‑
800mpas,特别优选100
‑
600mpas范围内的粘度。例如环烷脂族基础油具有上述范围内的粘度。
[0090]
特别适合乳化至少一种润滑油的乳化剂是非离子表面活性剂,更优选脂肪醇烷氧基化物,非常特别优选脂肪醇乙氧基化物如zosolat 1008/85(chemetall,德国)。总乳化剂含量优选在0.01
‑
10重量%,特别优选0.1
‑
8重量%,非常特别优选1
‑
5重量%范围内。
[0091]
本发明方法的步骤3中的反应性润滑剂除了组分a)、b)和c)外可以包含至少一种增稠剂d)、至少一种消泡剂e)、至少一种颜料f)、至少一种酸稳定表面活性剂g)和/或至少一种缓蚀剂h),这在特定应用中是有利的。
[0092]
特别有利的增稠剂d)是基于多糖,聚硅氧烷,聚乙烯基酰胺,即聚丙烯酰胺或聚乙二醇的增稠剂。增稠剂d)的总含量优选在至多100g/l,更优选至多10g/l范围内。
[0093]
特别有利的消泡剂e)是基于聚合物的不含聚硅氧烷的消泡剂如byk
‑
1711(byk,德国)或基于3d聚硅氧烷的消泡剂如foam ban ms
‑
550(m
ü
nzing,德国)。消泡剂e)的总含量优选在至多25g/l,更优选至多10g/l的范围内。金属基材上的腐蚀侵蚀(corrosive attack)导致气体放出,这特别是在至少一种酸稳定表面活性剂g)存在下可能导致沉积在基材上的稳定泡沫,但是这可以通过使用消泡剂降低或者甚至防止。
[0094]
特别有利的颜料f)是六角氮化硼、石墨和硫化钼。这些特别有效地促进该冷成型方法。颜料f)的总含量优选在至多500g/l,更优选至多50g/l的范围内。
[0095]
特别有利的酸稳定表面活性剂g)是脂肪醇烷氧基化物,非常特别优选脂肪醇乙氧基化物,如zosolat 1008/85(chemetall,德国)。酸稳定表面活性剂g)的总含量优选在0.01
‑
10重量%,特别优选0.1
‑
8重量%,非常特别优选1
‑
5重量%范围内。
[0096]
乳化的润滑油与缓蚀剂组合存在具有的优点是显著提高了金属基材的耐腐蚀性,结果相应地成型的部件可以储存更长时间。
[0097]
特别有利的缓蚀剂h)是壬基苯氧基乙酸(npa,德国basf)、琥珀酸单酯(l 12,德国basf)和咪唑啉衍生物(amine o,德国basf)。缓蚀剂h)的总含量优选在至多10重量%,更优选0.1
‑
5重量%,特别优选0.1
‑
3重量%范围内。
[0098]
步骤3中反应性润滑剂的ph优选小于2.0,更优选在0.15
‑
1.5范围内。这具有的优点是增强了腐蚀侵蚀并且因此增强了层形成。当与金属基材接触时,反应性润滑剂的温度优选在60
‑
95℃,特别优选75
‑
90℃,非常特别优选80
‑
85℃范围内。
[0099]
若在上述范围内,尤其是在非常特别优选的范围内选择温度,则得到的合并的转
化和润滑剂层特别均匀并且具有优异的附着力。
[0100]
已经发现步骤3中所用反应性润滑剂对热特别稳定。因此,润滑剂甚至在85℃的温度下数小时或甚至数天之后保持均相,即不发生c)至少一种成膜剂、至少一种蜡和/或至少一种乳化的润滑油的附聚和沉淀。
[0101]
金属基材与反应性润滑剂的接触优选将基材浸入润滑剂中或者通过将润滑剂倾注于基材上进行。接触时间,即处理时间优选在1
‑
40分钟,特别优选5
‑
30分钟,非常特别优选8
‑
20分钟范围内。
[0102]
在浸渍浴中形成的任何残渣(sludge)正如在磷化浴的情况下那样可以通过简单过滤在回收浴下除去。
[0103]
有利的是由于金属基材与反应性润滑剂在步骤3中接触而不在金属基材上沉积磷酸盐层,因为在随后热处理相应地敏感的组件,例如螺杆硬化和回火的情况下,发生δ
‑
铁素体的磷诱发形成并且这可能对材料性能具有不利影响。因此,反应性润滑剂优选基本不含磷酸盐,即不向其中加入磷酸盐。
[0104]
在本发明方法的步骤3之后,不应漂洗金属基材,因为否则的话存在洗掉已经在步骤3中施用的至少一种成膜剂、至少一种蜡和/或至少一种乳化的润滑油的危险。
[0105]
最后,金属基材可以在任选步骤4中干燥,然后进行冷成型方法。在水基润滑剂的情况下干燥通常可能是必要的,以在紧密包装被处理的待成型体,例如线束时避免水基残渣。本领域熟练技术人员在这里称为“强制干燥”。在步骤4中,干燥优选借助热空气在100
‑
280℃下进行,这导致润滑剂层的更快速和更均匀干燥并且使水残留物最小化。在步骤4中,干燥是指借助辅助剂如热空气或烘箱的干燥,而不是来自步骤3的仍然热/温的金属基材在空气中的干燥。
[0106]
本发明方法原则上适合所有可能的冷成型方法,尤其是用于:
[0107]
‑
例如焊接或无缝管、中空型材、实心型材、线材或棒材的拉伸(拉伸成型),例如在线材拉伸或管材拉伸中,
[0108]
‑
旋压,
[0109]
‑
例如带材或板材的压薄(成型至最终尺寸)和/或深拉,得到特别深拉的成型体,或者中空体的压薄(成型至最终尺寸)和/或深拉,得到更大变形的中空体,
[0110]
‑
例如螺母或螺栓坯料的螺纹滚压和/或打线,
[0111]
‑
例如中空体、实心体的压制如冷流成型(加压成型),
[0112]
‑
挤出,以及
[0113]
‑
例如线材段的冷锻,形成连接元件如螺母或螺栓坯料。
[0114]
在成型之后,已经通过本发明方法处理的金属基材可以容易地清洁,即合并的转化和润滑剂层可以借助碱性清洁剂、酸或酸洗液除去,正如也在用上覆聚合物润滑剂磷化的情况下使用的那样。
[0115]
本发明还提供了一种用于金属基材冷成型的水基酸性反应性润滑剂,包含:
[0116]
a)草酸,
[0117]
b)至少一种包含硝基胍和/或至少一种铁(iii)源的促进剂,和
[0118]
c)至少一种成膜剂、至少一种蜡和/或至少一种乳化的润滑油,其中至少一种成膜剂选自乙烯、丙烯、苯乙烯、(甲基)丙烯酸、(甲基)丙烯酸酯、乙烯基胺、乙烯基甲酰胺、乙烯
基吡咯烷酮、乙烯基己内酰胺、乙酸乙烯酯、乙烯基咪唑和/或环氧化物的均聚物和共聚物及其盐以及还有聚氨酯、聚酰胺、聚乙烯亚胺、聚胺及其盐,
[0119]
其中至少一种蜡选自非离子蜡和阳离子稳定化蜡,以及
[0120]
其中至少一种乳化的润滑油选自合成油、矿物油、植物油和动物油。
[0121]
本发明的该反应性润滑剂的有利实施方案已经在上面对本发明方法说明。
[0122]
本发明还涉及一种浓缩物,可以通过稀释,尤其是用水稀释并任选借助ph改性物质设定ph而由该浓缩物得到本发明的反应性润滑剂。
[0123]
此外,本发明涉及一种可以通过本发明的上述方法得到的预处理金属基材。
[0124]
可以以此方式得到的金属基材具有合并的转化和润滑剂层,后者具有的层重由重量分离方法测定作为润滑剂层计算在0.3
‑
15g/m2,优选0.3
‑
10g/m2范围内并且作为分隔/转化层计算在0.3
‑
30g/m2,优选1.5
‑
15g/m2范围内。
[0125]
在本发明的研究中已经惊人地发现该合并层可以分开且单独调节。因此,本发明方法的步骤3中更长的处理时间给出更厚的分隔/转化层,即作为分隔/转化层计算更高的层重,同时更高浓度的成膜剂/蜡/乳化的润滑油,即本发明反应性润滑剂的组分c),导致更厚的润滑剂层,即作为润滑剂层计算更高的层重。以此方式可以生产适应冷成型操作的相应条件的合并转化和润滑剂层。
[0126]
作为所得高层重和物理化学附着力的结果,该合并的转化和润滑剂层在传统冷成型方法中“保持完好”。因此,当该线材已经在拉床上在包括在4个步骤中直径总减小为至少40%,优选至少50%,特别优选至少55%的单一操作中经受成型模拟时,至少10%,优选至少15%,特别优选至少20%,非常特别优选至少23%的总层重(作为润滑剂层计算和作为分隔/转化层计算合起来)保留在预处理且预拉伸的高碳线材上。这里以%计的总减小以[(初始直径:最终直径)
–
1]
×
100计算。以此方式可以实现该成型基材的暂时令人满意的防腐。
[0127]
最后,本发明提供了可以由本发明方法得到的预处理金属基材在冷成型方法中的用途,例如用于生产管材、线材、连接元件、型材、密封部件或齿轮箱部件。
[0128]
本发明在下面通过工作实施例和对比例说明,这些工作实施例不应被认为构成限制。
实施例
[0129]
配制包含表1所列成分以及水的酸性反应性润滑剂a
‑
i。
[0130]
表1:
[0131]
[0132][0133]
表1(续):
[0134][0135]
*)未测定
[0136]
在搅拌的同时将反应性润滑剂a
‑
e各自加热至不同温度并在相应温度下维持数小时。直到85℃的温度润滑剂都保持均相,即没有发生所包含蜡和成膜剂的附聚和沉淀。这对于润滑剂d来说在大于14小时之后并且在润滑剂e的情况下甚至在大于5天之后情况并非如此。然而,发现润滑剂f额外热稳定。在这种情况下,甚至在95℃的温度下大于5天之后也不发生附聚和沉淀。
[0137]
在80
‑
85℃下将各种钢基材各自浸入反应性润滑剂8
‑
10分钟。通过加入消泡剂(润滑剂b
‑
f与润滑剂a和g
‑
i相比)能够显著降低泡沫产生。沉积层的层重在将温热基材在空气中干燥之后对润滑剂b和e
‑
i借助重量分离测定。
[0138]
该重量分离方法按如下进行:
[0139]
1)计算预处理金属基材的表面积并称重后者。
[0140]
2)在溶剂二甲苯中除去该润滑剂层。
[0141]
3)再次称重该金属基材。
[0142]
4)在包含三乙胺/edta的10
‑
20%浓度氢氧化钠溶液中除去该分隔/转化层。
[0143]
5)再次称重该金属基材。
[0144]
1)和3)之间的重量差除以表面积得到作为润滑剂层计算的层重,而3)和5)之间的重量差除以表面积为作为分隔/转化层计算的层重。
[0145]
表2和表3说明以此方式测定的作为润滑剂层(sg(s))计算和作为分隔/转化层(sg(k))计算的层重,在每种情况下以g/m2计并且作为n=3的平均值(n.d.=未测定)。
[0146]
表2:
[0147][0148]
表3:
[0149][0150]
*)冷轧钢板;**)热轧钢板
[0151]
在所有情况下,可以以此方式证实合并的转化和润滑剂层的沉积。用润滑剂e预处理的线束的表面的扫描电镜照片额外显示出由草酸盐晶体构成的均匀封闭层。
[0152]
所有合并的转化和润滑剂层牢固附着在基材表面并且确保良好的暂时防腐。
[0153]
用如上所述的反应性润滑剂e预处理st1375/1570品级的高碳线材(voestalpine,austria)。然后在拉床上将该线材的直径在4个步骤中由10.9mm减小至7.0mm(见表4)。这里使用三个不同的拉伸速度:20m/s,40m/s和60m/s。在所有拉伸速度下,成型成功进行。在拉伸线材上没有出现缺陷如划伤。测量的拉伸力在每种情况下与传统聚合物润滑剂相当。表面温度升高小于110℃。
[0154]
表4:
[0155][0156]
以g/m2计的层重量如上所述借助重量分离在整个成型操作之前和之后测定。所得结果示于表5中(n的平均值=4)。
[0157]
表5:
[0158]
成型sg(s)sg(k)之前3.211.4之后0.43.0
[0159]
因此,在成型之前,总层重为约15g/m2,其中在成型之后仍保留约3.5g/m2。也就是
说,该层保留约25%。
[0160]
因此,尽管在最后成型阶段过程中观察到合并的转化和润滑剂层明显变薄,但没有发生基材表面的明显暴露。
[0161]
用如上所述的反应性润滑剂f预处理st1375/1570品级的高碳线材(voestalpine,austria)。然后在拉床上将该线材的直径在4个步骤中(试验i和试验ii)由11mm减小至6.7mm或者在2个步骤中(试验iii)由11mm减小至7.4mm(见表6)。这里使用三个不同的拉伸速度,即30m/s(试验i),60m/s(试验ii)和40m/s(试验iii),每个成型阶段线材直径减小20%(试验i和试验ii)或35%。在所有情况下,成型成功进行。在拉伸线材上没有出现缺陷如划伤。测量的拉伸力在每种情况下与传统聚合物润滑剂相当。表面温度升高小于110℃。
[0162]
表6:
[0163][0164][0165]
以g/m2计的层重量如上所述借助重量分离在整个成型操作之后测定。所得结果总结于表7中(sg(g)=总层重)。
[0166]
表7:
[0167]
试验sg(s)sg(k)sg(g)i3.23.87.0ii.3.45.28.6iii2.73.66.3
[0168]
因此,在每种情况下,合并的转化和润滑剂层以使得其他成型阶段,即直径减小可能已经进行的厚度保留在该基材上。
再多了解一些
本文用于企业家、创业者技术爱好者查询,结果仅供参考。