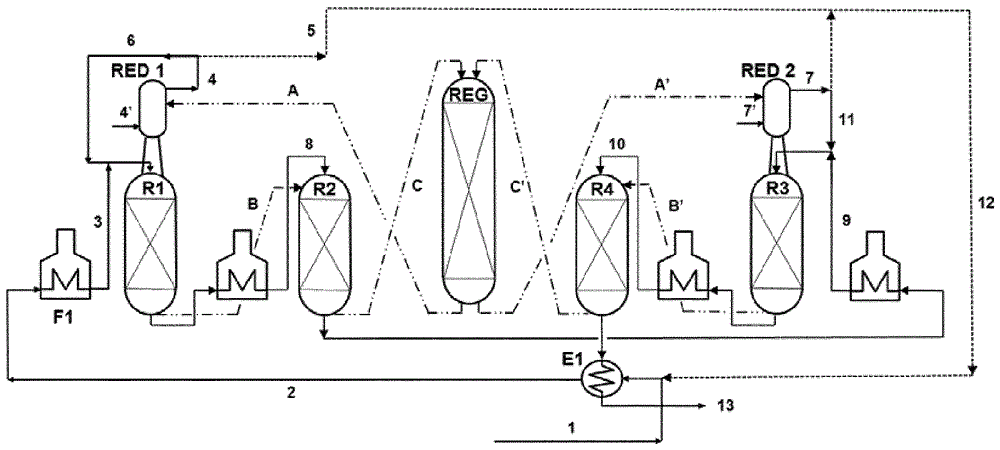
本发明涉及烃转化领域,更具体而言,涉及催化重整领域。本发明的主题是采用至少两个反应区、两个还原区和一个再生区,且将来自所述还原区的流出物至少部分地在每个反应区的顶部再循环的方法。现有技术石脑油类型的烃馏分的重整(或催化重整)在精炼领域是众所周知的。该反应可以由这些烃馏分生产具有高辛烷值的燃料的基料和/或用于石化工业的芳族馏分,同时为炼油厂提供其他操作所需的氢气。催化重整方法包括使包含链烷烃化合物和环烷烃的烃馏分与氢气和重整催化剂,例如铂催化剂接触,并且将链烷烃化合物和环烷烃转化为芳族化合物并伴随产生氢气。由于重整方法中涉及的反应是吸热的,因此建议加热从一个反应器中取出的流出物,然后将其送至下一个反应器。随着时间的推移,由于焦炭在重整催化剂的活性位点上的沉积,重整催化剂变得失活。因此,为了维持重整单元的可接受的生产率,必须将催化剂再生以除去沉积物并因此恢复催化剂的活性。存在各种类型的重整方法:“非再生”、“半再生”和“连续”重整。连续催化重整或ccr方法包括在反应器中进行反应,在所述反应器中催化剂从顶部连续地向下流动,并且再生在附加反应器中连续进行,将催化剂再循环到主反应器,从而不中断反应。在后续的说明书中将只讨论这种类型的催化重整。重整将并行发生的多种类型的反应汇集到一起,特别是平衡异构化反应、脱氢反应和脱氢环化反应。这些反应在低h2含量的条件下产生芳环。事实上,根据串联反应器中的进展,主反应并不相同。例如,环烷烃的脱氢是非常迅速的,主要在第一反应器中发生。异构化反应较慢,在所有反应器中更逐步地发生,而环烷烃的裂化主要在最后一个反应器中发生。无论进行何种反应,所使用的催化剂必须能够提供所需的所有反应,同时保持良好的活性,良好的选择性和良好的稳定性。此外,重整反应产生氢气(h2),而裂化副反应消耗氢气。因此,在不控制h2含量的情况下,副反应会导致碳数大于或等于5的化合物(c5 ),更特别是芳族化合物的收率降低。典型地,所述副反应是裂化或烷基化。通过低h2含量最小化这些反应。因此,氢气含量在芳族化合物的最终收率中起着重要作用。然而,氢气在反应器中焦炭的形成中也起着关键作用。因此,焦炭的形成不但取决于h2浓度,还取决于总环烷烃的含量、温度、压力和循环时间。由于第一反应区中的环烷烃的含量较高,因此焦炭主要在该第一区中形成。在包括具有4个反应器的单个反应区的方法中,在反应器1和反应器2中结焦的催化剂逐渐移动到反应器3和反应器4中,从而导致4个反应器中的催化剂显著失活,因此导致芳族化合物的收率降低。因此,在重整方法中加入氢气来限制焦炭的形成,从而防止催化剂过早失活导致的过短的循环时间和因此过分频繁的再生。这就是为什么在常规配置中,在沉降器之后将一部分氢气经由压缩机和再循环环路在第一反应区的入口和第二反应区的出口之间在所述方法中循环,从而使催化剂有足够的氢气供应以限制焦炭含量。文献fr2946660描述了如上所述的重整方法的配置,其中将催化剂再生区出口处的还原流出物再循环至反应区的最后反应器中。这样的方法可以减少最后反应器中焦炭的形成并平衡整个方法中的反应,但也导致可以产生芳族化合物的脱氢环化的减少、增加焦炭的形成并加速不希望的脱氢环化反应。文献fr2961215涉及汽油的再生式催化重整方法,该方法衍生自前述方法,特别是在第一反应器顶部的入口处将来自催化剂还原区的流出物的至少一部分再循环。该方法可以改善重整产物的产量(更好的c5 收率)和氢气平衡。不幸的是,在这种类型的方法中,焦炭含量在所有反应器中都受到管理,因此难以限制和控制总氢气供应。因此,裂化反应仍然是显著的,进而不利地影响转化率并因此不利地影响芳族化合物的收率。此外,该方法使用压缩机来将氢气循环到各种反应器中,其成本相当可观,占单元成本的20%-40%。最后,使用单一类型的催化剂不能适用于在整个方法中发生的不同反应。因此,已经开发了不使用压缩机并采用多个反应区的方法,以便为给定的反应区提供特定的催化剂,和因此能够根据反应区来调节和控制反应。文献ep2995379和文献ep2995380涉及将催化剂连续再生,特别是在不同的操作条件下、借助于彼此分开的再生区将催化剂连续再生的重整方法。在标准方式中,气态流出物依次地流入每个反应器,然后流入炉,然后进入下一个反应器(吸热反应),可移动的催化剂在每个反应器中靠重力下降,然后通过提升上升到下一个反应器的顶部。最后将该催化剂所含的氢气排放并送至再生器,在那里以受控的方式焚烧焦炭以恢复该催化剂的活性。该方法的特征在于连续再生器被划分为四个区域,催化剂靠重力穿过这些区域。前两个区域可以燃烧焦炭。控制温度和氧气分压以提供焦炭的定向和完全燃烧。在两个燃烧区之间额外供应空气和骤冷气体可以调节第二床入口处的温度和氧气浓度。在燃烧后,催化剂流入最后两个区域,在那里发生氧氯化反应(催化活性的恢复,特别是金属相的再分散)和煅烧反应。不同于燃烧气体的气体在这两个区域中循环(这次是以逆流方式),并且伴随氧氯化引入富含气态氯(由氯化剂分解产生)但贫氧的新的额外的气体供给。催化剂的这种双循环使得可以在两个反应区中管理不同的循环速率,从而在所述区域中采用不同的催化剂和焦炭水平进行操作。因此,能够采用针对第一反应器(其中主要发生上述前三个重整反应)优化的催化剂进行操作将具有很强的优势。出于限制副反应和从而促进主要的重整反应的目的,仍然必须控制h2含量以改善芳族化合物的收率,也为了限制焦炭的形成。通过避免使用压缩机来降低工厂和生产成本也很重要。此外,在不同的反应区中更好地分配h2可以降低能耗,从而降低方法的总成本。令人惊讶的是,本申请人的公司已开发出一种新的连续再生重整方法,其包括多个限定的反应区和两个催化剂还原区,其中在不同反应区的顶部处将还原流出物至少部分地再循环。然后可以通过使用还原氢气、通过再循环来限制第一反应区入口处的氢气注入,并因此省去了再循环压缩机。因此,降低了所述设备的能耗和运行成本。本申请人的公司还发现,在所述重整方法内使用中间再生器可以提高芳族化合物的收率,同时限制使催化剂失活的焦炭的形成。因此,根据一个实施方案,所述方法可以使用分区再生器,这使得可以在适于所述区域中发生的特定反应和焦化程度的操作条件下,借助于分区中间再生器使用适于反应区的催化剂。通过阅读下面给出的描述,将更好地理解本发明的其他特征和优点。本发明的主题本发明的主题涉及在400℃-700℃的温度、0.1-10mpa的压力和0.1-10h-1的每单位重量催化剂每小时处理的原料重量流量下催化重整烃原料的方法,所述烃原料包含每分子含5-12个碳原子的链烷烃、环烷烃和芳烃,在所述方法中:-所述烃原料(1)循环通过至少:a)在氢气的存在下的第一反应区,所述第一反应区包括至少两个串联的催化重整反应器(r1、r2),所述反应器包括在移动床中循环的第一催化剂;然后b)在氢气的存在下的第二反应区,从而获得反应流出物(13),所述第二反应区包括至少两个串联的催化重整反应器(r3、r4),所述反应器包括在移动床中循环的第二催化剂,所述第二催化剂与所述第一催化剂相同或不同;-所述第一催化剂和第二催化剂分别循环通过:i)所述第一反应区和所述第二反应区;然后ii)第一再生区和第二再生区(reg);然后iii)在氢气的存在下的第一还原区和第二还原区(red1和red2),然后在步骤i)中将所述第一催化剂和所述第二催化剂返回至所述第一反应区和所述第二反应区;在所述方法中,将在每个还原区(red1和red2)的出口处获得的还原流出物(4和7)至少部分地送至每个反应区的第一反应器(r1、r3)的顶部。定义和缩写明确指出的是,贯穿本说明书,表述“……和……之间”和“包括在……和……之间”应理解为包括所提及的限值。在本专利申请中,术语“包括”与“含有”和“包含”同义(表示相同的事物),是包容性或开放性的,并且不排除其他未陈述的要素。应当理解的是,术语“包括”包括排他性的封闭术语“由……组成”。附图说明图1表示本发明方法中使用的催化重整单元的总体视图,其包括用于催化剂的中间再生的区域和两个反应区,所述两个反应区本身由两个串联的反应器(r1、r2和r3、r4)和还原区(red1和red2)组成,其中将还原流出物的至少一部分送至每个反应区的第一反应器(r1、r3)的顶部。根据一个实施方案,将在每个还原区(red1和red2)的出口处经由管线4和管线7获得的还原流出物经由管线6和管线11至少部分地送至每个反应区的第一反应器(r1、r3)的顶部,并且经由管线5和管线12至少部分地与经由管线1的新鲜烃原料混合。发明详述在本发明的含义内,所呈现的不同实施方案可以单独使用或彼此组合使用,对组合没有任何限制。下文的详细描述是结合图1给出的。本发明涉及在400℃-700℃的温度、0.1-10mpa的压力和0.1-10h-1的每单位重量催化剂每小时处理的原料重量流量下催化重整烃原料的方法,所述烃原料包含每分子含5-12个碳原子的链烷烃、环烷烃和芳烃,在所述方法中:-所述烃原料(1)循环通过至少:a)在氢气的存在下的第一反应区,所述第一反应区包括至少两个串联的催化重整反应器(r1、r2),所述反应器包括在移动床中循环的第一催化剂;然后b)在氢气的存在下的第二反应区,从而获得反应流出物(13),所述第二反应区包括至少两个串联的催化重整反应器(r3、r4),所述反应器包括在移动床中循环的第二催化剂,所述第二催化剂与所述第一催化剂相同或不同;-所述第一催化剂和第二催化剂分别循环通过:i)所述第一反应区和所述第二反应区;然后ii)第一再生区和第二再生区(reg);然后iii)在氢气的存在下的第一还原区(和第二还原区(red1和red2),然后在步骤i)中将所述第一催化剂和所述第二催化剂返回至所述第一反应区和所述第二反应区;在所述方法中,将在每个还原区(red1和red2)的出口处获得的还原流出物(4和7)至少部分地送至每个反应区的第一反应器(r1、r3)的顶部。根据本发明的方法涉及在400℃-700℃的温度、0.1-10mpa的压力和0.1-10h-1的每单位重量催化剂每小时处理的原料重量流量下重整每分子含5-12个碳原子的链烷烃、环烷烃和芳烃原料。优选地,所述烃原料是石脑油馏分。烃原料的循环烃原料1循环通过至少两个反应区,每个反应区包括至少两个催化重整反应器,对于第一反应区分别表示为r1、r2,对于第二反应区分别表示为r3、r4,在图1中所述反应器以“并排”配置的方式呈现。将所述反应器串联放置。在本发明的上下文中,所述方法可以包括多于两个反应段,每个反应段使用具有相同或不同组成的催化剂进行操作。不同的反应区可以垂直堆叠的形式布置在同一个反应器中,或分别并排布置在至少第一反应器和至少第二反应器中,如图1所示。烃原料1流过流出物/原料换热器e1,然后经由管线2流过预热炉f1,然后经由管线3引入第一反应区的第一反应器r1中,所述第一反应器至少包含第一催化剂和氢气。随后,所述原料经由管线8流过第一反应区的第二反应器r2,然后经由管线9和10流过第二反应区的反应器r3和r4,从而经由管线13获得反应流出物。将反应流出物在最后一个反应区的最后一个反应器r4的出口处回收,在流出物/原料换热器e1中冷却并在出口13处回收。反应流出物13经过处理(图1中未示出)以一方面分离出氢气和裂化产物(优选为具有小于或等于4的碳数的化合物),另一方面分离出包含具有大于或等于5的碳数的化合物的重整产物。烃原料、反应流出物以及在移动床中循环的第一催化剂和第二催化剂的流动沿向下的方向并流发生。优选地,所述移动床是“径向”型的。催化剂类型在根据本发明的方法的上下文中使用的一种或多种催化剂包含活性相和载体。活性相所述活性相包含至少一种来自元素周期表第viii族的金属、任选一种或多种助催化剂金属、至少一种掺杂剂和/或至少一种卤素。-所述来自元素周期表第viii族的金属优选是铂。相对于催化剂的总重量,所述金属的含量为0.02重量%-2重量%,优选0.05重量%-1.5重量%,更优选0.1重量%-0.8重量%。-所述助催化剂金属选自来自元素周期表第viii族的金属,例如铼和铱。相对于催化剂的总重量,每种助催化剂金属的含量为0.02重量%-10重量%,优选0.05重量%-5重量%,更优选0.1重量%-2重量%。-所述掺杂剂选自镓、锗、铟、锡、锑、铊、铅、铋、钛、铬、锰、钼、钨、铑、锌和磷。优选地,在根据本发明的方法的上下文中使用多种掺杂剂。相对于催化剂的总重量,每种掺杂剂的含量可以为0.01重量%-2重量%,优选0.01重量%-1重量%,更优选0.01重量%-0.7重量%。-所述卤素优选是氯。相对于催化剂的总重量,卤素含量为0.1重量%-15重量%,优选为相对于催化剂的总重量的0.2重量%-5重量%。当所述催化剂包含单一卤素(其为氯)时,相对于催化剂的总重量,氯含量为0.5-2重量%。载体在根据本发明的方法的上下文中使用的催化剂的多孔载体基于氧化铝。催化剂中使用的多孔载体的一种或多种氧化铝可以具有任何类型并且可以通过本领域技术人员已知的不同方法合成。多孔载体以直径为1-3mm、优选1.5-2mm的珠粒的形式提供,这些值是非限制性的。通过本领域技术人员公知的任何方法将多孔载体成型可以在所有组分已经沉积在所述多孔载体上之前或之后进行。制备在根据本发明的方法的上下文中使用的催化剂可以通过本领域技术人员公知的任何技术制备,例如通过干法浸渍或者通过液相或气相沉积。第viii族的金属可以通过常规技术沉积,特别是从铂前体或包含铂盐或铂的化合物的水溶液或有机溶液中浸渍。一种或多种掺杂剂和/或一种或多种助催化剂金属也可以通过常规技术从前体化合物,例如所述金属的有机金属化合物、掺杂剂金属的磷基化合物、卤化物、硝酸盐、硫酸盐、乙酸盐、酒石酸盐、柠檬酸盐、碳酸盐或草酸盐和胺型配合物开始沉积。根据一个实施方案,卤素可以通过氧氯化处理添加到催化剂中。在使用之前,在氢气下处理催化剂并使用基于硫的前体处理催化剂以获得具有活性和选择性的金属相。这种在氢气下进行处理的程序,也称为在氢气下的还原,包括将催化剂保持在100-600℃、优选200-580℃的温度下的纯氢气或经稀释的氢气物流中30分钟至6小时。这种还原可以在煅烧之后立即进行,也可以稍后由用户进行。用户也可以直接还原经干燥的产物。在还原之后进行使用基于硫的前体进行处理的程序。通过本领域技术人员公知的任何方法进行采用硫的处理(也称为硫化)。催化剂的循环催化剂经由每个反应区的管线b和管线b'在不同反应器中的移动床中循环。不同反应区的催化剂可以相同或不同。在所述第一催化剂与所述第二催化剂相同的情况下,所述第一中间再生区和所述第二中间再生区仅形成同一个公共中间再生区。相对于第一催化剂的总重量,在第一反应区的出口处产生的焦炭水平为3重量%-7重量%,优选4重量%-6重量%。相对于第二催化剂的总重量,在第二反应区的出口处产生的焦炭水平为3重量%-7重量%,优选4重量%-6重量%。在所述第一催化剂与所述第二催化剂不同的情况下,所述第一中间再生区和所述第二中间再生区仅形成同一个分区中间再生区。待处理的原料1、还原流出物6和11以及分别在反应器r2、r3和r4的入口处的不同的中间流出物8、9和10基本上径向地穿过催化剂。每个反应区可包括一个或多个移动催化剂床。在经由管线c和管线c'离开每个反应区的最后一个反应器后,催化剂进入再生区reg,该再生区包括依次且按以下顺序循环的所述第一催化剂和所述第二催化剂:-沉积在催化剂上的焦炭的燃烧段(i);-可以使微晶再分散的氧氯化段(ii);和-将催化剂的氧化物还原的煅烧段。燃烧段每个燃烧段包括环形空间,该环形空间由两个气体可渗透但催化剂不可渗透的筛网界定,催化剂在所述环形空间中靠重力循环。优选地,所述环形空间被催化剂不可渗透的分离构件划分成多个部分;优选地,所述分离构件也是气密性的。所述部分能够分别包含具有不同组成的催化剂。所述筛网选自本领域技术人员公知的任何构件,例如网格或穿孔板。氧氯化段每个氧氯化段通过催化剂不可渗透的分离构件将腔室的区域分隔成隔室获得;优选地,所述分离构件也是气密性的。优选地,氧氯化段与煅烧段通过混合段隔开,所述混合段被构造成进行氧氯化气体与煅烧气体的混合。煅烧段每个煅烧段通过催化剂不可渗透的分离构件将腔室的区域分隔成隔室获得;优选地,所述分离构件也是气密性的。所述催化剂在中间再生区内靠重力循环。在不同的反应区使用不同的催化剂的情况下,所述再生区同时且分别处理至少两种在移动床中循环的重整催化剂,这些催化剂能够根据转化的进程进行特定的催化反应。因此,所述再生区使得可以共同处理至少两种类型的具有不同组成的催化剂,所述催化剂特别适于进行具有低辛烷值的石脑油馏分的催化重整中涉及的反应。优选地,当第一反应区的催化剂与第二反应区的催化剂不同时,中间再生器被分区;例如,可以使用如专利ep2995379中所述的分区再生器。因此,在针对每个反应区的每种类型催化剂特定的条件下处理催化剂,其中催化剂的流量、气体流量或气体组成可能不同,或者例如第一反应区的第一反应器的酸度可以被降低,因为该条件对于环烷烃的脱氢不是必需的,并且第一反应区的温度也可以被降低,因为环烷烃的脱氢可以在较低的温度下进行,从而限制了第一反应区的焦炭含量。术语“组成”应理解为是指构成催化剂的要素,即载体和活性金属相。为了能够在同一个中间再生器reg内再生每个反应区的催化剂,第一反应区产生的焦炭水平与第二反应区产生的焦炭水平相等。因此,再生器reg可以根据焦炭的目标水平来设计比例。因此调节再生器reg的循环时间、压力、温度和入口处的氢气量以观察所述目标。在中间再生区中循环以进行再生后,催化剂经由管线a和管线a'进入还原区red1和还原区red2,从而在富含氢气的气体(经由管线4'和管线7')的存在下在所述还原区中被还原。经还原的催化剂离开还原区以在第一反应器(r1或r3)的顶部处进入其反应区。管线4'和管线7'源自高压再接触罐(图1中未表示)或源自本领域技术人员公知的氢气纯化。管线4'和管线7'具有大于90摩尔%的氢气含量。对应于管线3和管线6的混合物的进入r1的物流的h2/hc之比为0.10-0.40,这足以控制第一反应区中焦炭的含量。对应于管线9和管线11的混合物的进入r3的流的h2/hc之比为1.30-1.80,优选1.40-1.70。随着停留时间的增加,重整反应释放氢气,从而可以减缓焦炭的形成。除了在第一反应区中引入和原位产生的氢气之外,第二反应区还进料有产生自来自还原区red2的还原流出物的低流量氢气。还原段red1和还原段red2产生被称为还原流出物并分别表示为4和7的还原气体。将这些还原流出物4和7至少部分地送至每个反应区的第一反应器的顶部,即分别经由管线6送至r1,经由管线11送至r3。优选地,将所述还原流出物4和7至少部分地送至每个反应区的第一反应器(r1、r3)的顶部,并且经由管线5和管线12至少部分地与新鲜烃原料1混合。这些含有水和氯的流出物的再循环可以实现氯化化合物和水在第一反应区的催化剂上的再吸收,并因此可以减少方法中的氯和水的消耗。而且,在第二反应区的第一反应器r3的顶部处,还原流出物7可以经由管线11在反应器入口处与部分转化的原料直接混合,或者经由管线12重新引导至流出物/原料换热器,以提高第一反应区的第一反应器(r1)的h2/hc之比。对应于管线4和管线7的还原流出物的氢气含量远低于对应于管线4'和管线7'的引入的气体(其氢气含量为80摩尔%-87摩尔%)。离开还原段red1和还原段red2的还原流出物4和还原流出物7是除了原位形成的氢气之外的唯一氢气来源。所述还原流出物4和还原流出物7具有0.47-0.57mpa的压力和450℃-520℃的温度。相对于所述还原流出物4和还原流出物7的总体积,所述还原流出物4和还原流出物7的氢气含量为90体积%-99.9体积%。相对于所述还原流出物4和还原流出物7的总体积,所述流出物的氯含量为20-50体积ppm。相对于所述还原流出物4和还原流出物7的总体积,所述流出物的水含量为50-100体积ppm。每个反应区的第一反应器(即分别为r1和r3)的入口处的压力为0.45-0.6mpa,优选0.46-0.58mpa。以下实施例举例说明本发明,但不限制其范围。实施例在后续的实施例中使用的石脑油原料具有以下性质:表1链烷烃(重量%)56.4环烷烃(重量%)30.5芳族化合物(重量%)13.1密度(kg/m3)0.7428平均沸点(℃)116.3表1-石脑油原料的特性。在后续的实施例中使用的催化剂是包含负载在氯化氧化铝基料上的0.25%铂和0.3%锡的催化剂。参照方法包括按常规次序的4个绝热反应器,不具有中间催化剂再生,标准h2/hc之比为2。使用相同的原料和相同的催化剂模拟其他三种方法:-情况1(不根据本发明):在第一反应区入口处具有低h2/hc之比的重整方法,不具有用于催化剂中间再生的区域。-情况2(根据本发明):在第一反应区入口处具有低h2/hc之比的重整方法,具有催化剂的中间再生并额外供应氢气。-情况3(根据本发明):具有比其他两种情况略高的h2/hc之比的重整方法,具有催化剂的中间再生并额外供应氢气。不同方法的结果在下表2中给出。h2、c4-化合物和c5 化合物的收率以及总芳族化合物的收率和所需的c5 辛烷值以相对于注入的新鲜烃原料的总重量流量的重量百分数表示。反应区1和反应区2的出口处的焦炭百分数相对于催化剂的重量表示。参照情况1(不根据本发明)情况2(根据本发明)情况3(根据本发明)反应器r1压力(mpa)0.380.380.380.38第一反应器(r1、r3)入口处的平均温度(℃)530530530530第一反应区入口处的h2/hc(摩尔/摩尔)20.20.20.4在第二反应区入口处添加的额外的h2/hc(摩尔/摩尔)nana0.20.4反应区的数量1122在反应器之后的催化剂再生r4r4r2和r4r2和r4反应区1的催化剂的停留时间(天)5322反应区2的催化剂的停留时间(天)nana88结果h2收率(重量%)3.633.303.843.86c4-化合物收率(重量%)7.9810.058.728.70c5 收率(重量%)88.3986.6587.4487.44总芳族化合物收率(重量%)72.0168.8274.3474.07所需的c5 辛烷值102.72102.36104.68104.51反应区1的出口处的焦炭(重量%)5.1011.484.805.20反应区2的出口处的焦炭(重量%)nana5.314.7表2-计算结果。根据结果表,发现相对于参照,总芳族化合物的收率提高了2个百分点。还注意到当h2/hc之比降低时(参照和情况1),并且尽管反应区中的催化剂的停留时间缩短,但反应区出口处的焦炭含量高,同时芳族化合物收率下降了3.2个百分点。总之,中间再生可以提高总芳族化合物的收率,同时显著地限制焦炭的形成并同时保持低h2/hc之比。当前第1页12
再多了解一些
本文用于企业家、创业者技术爱好者查询,结果仅供参考。