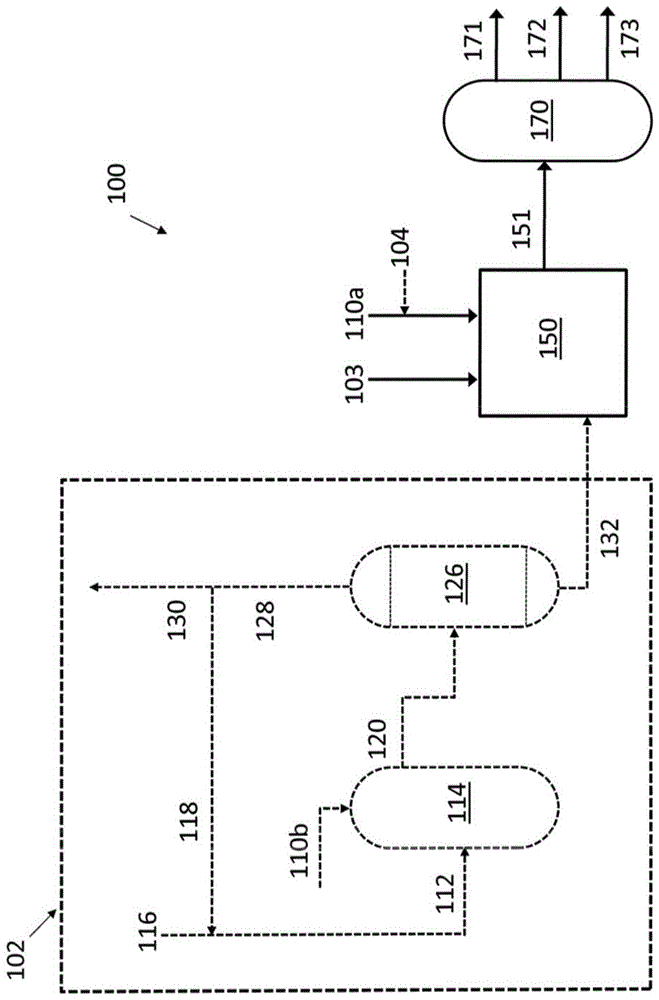
本发明涉及用于生产柴油和航空燃油的中间馏分以及相关调合组分的集成炼油工艺。
背景技术:
:中间馏分,包含用于住宅、商业和工业建筑的运输燃料和加热油,约占全球精炼产品的30%。全球对中间馏分的需求相对于其他任何石油精炼产品一直稳定提升并且持续高速增长。在美国,中间馏分是全国货物运输的主要燃料来源,因此对国家经济基础设施的发展至关重要。尽管汽油作为主要的乘用车燃料在美国占据主导地位,但柴油燃料一直是石油市场近期增长的主要驱动力。在2007年至2009年经济衰退之前,美国对柴油的需求每年增长2%以上,而对汽油的需求每年增长1.2%。当前,柴油有望再次发挥支撑经济扩张和发展的主要能源作用。2007年推出的柴油精炼技术的进步导致清洁、超低硫(即<10ppmw)柴油的生产。与2000年代初期的排放量相比,这些进步还使重型卡车应用中的颗粒物和氮氧化物的排放量减少了98%以上。此外,该技术导致开发和推出了比以前车型更清洁、更安静的高性能柴油汽车、卡车和suv,进一步增加了对柴油的需求。新燃油经济性要求的引入使柴油燃料能够在美国的运输市场中发挥更大的作用。为了满足消费者对柴油燃料不断增长的需求,零售商增加了供应量。实际上,现在美国一半以上的燃料零售加油站都提供柴油燃料。在不久的将来,炼油厂可能会被迫投资用于提高中间馏分比例收率的转化工艺,或者寻找替代工艺来生产满足预期需求所需的中间馏分。随着对中间馏分的需求不断增加,许多新炼油厂选择加氢裂化而非流化催化裂化(fcc)作为将原料转化为柴油燃料的主要工艺。这是因为与fcc工艺相比,加氢裂化工艺产生更高的柴油收率和更优异的柴油质量。此外,许多炼油厂正在利用加氢处理和焦化等重尾(heavyend)技术将短烃残渣或长烃残渣转化为运输燃料。fcc装置产生大量的高硫、低十六烷值的芳烃馏分油,例如轻循环油(lco)。根据现代柴油质量规范,该lco需要深度加氢处理、加氢、加氢裂化或其任意组合,以生产符合监管标准的柴油和汽油调合组分。目前有许多高压加氢处理装置专门设计用于将fcc工艺中产生的lco改质(upgrade)为符合当前标准的柴油燃料。除了降低硫含量外,这些高压加氢处理装置还显著提高了所得产物流的十六烷值,例如提高了20至30个百分点。此外,用于生产高质量合成柴油燃料的替代方法是增加fcc裂化的程度(severity)以最大限度地提高来自fcc单元的汽油范围内低分子量烯烃产物的产量,并使这些烯烃低聚。由汽油生产中间馏分调合组分在现有技术中是众所周知的。例如,wo2012/076758公开了一种通过碳数为5至7的烯烃的二聚和/或低聚由汽油燃料组分馏分生产中间馏分燃料组分的方法。低聚反应产生的产物由一种或多种原子或原子团的重复连接基团组成。用于烯烃低聚的催化剂包括酸催化剂如沸石、非沸石酸催化剂、镍催化剂和过渡金属催化剂。低聚反应通常在高于200℃的温度和高于50bar的压力下进行。在wo2012/076758公开的方法中,中间馏分烃通过直链脂肪族c9-c16烃的低聚/聚合和分馏来生产,其中直链脂肪族c9-c16烃对应于约为165℃至290℃的正常沸点。氟离子亲和力用作衡量路易斯酸强度的合适量度。christie等,j.fluorinechem.,101(2000)151-153,通过引用并入本文,其提出了使用pf-标度来指示路易斯酸的强度。低碳数烯烃的烷基化以生产烷基化汽油调合组分在现有技术中也是众所周知的。世界各地的炼油厂都安装了许多烷基化单元。最常见和广泛使用的烷基化过程使用液体酸,例如hf或h2so4。其他已知的工艺使用超强酸,其酸度等于或强于100%硫酸。另一种定义超强酸的方法是哈米特(hammet)酸度值至少为(-12)或更低的酸。为了进行对比,纯硫酸的哈米特酸度值为(-12)。其他提高中间馏分产量的工艺改进已被提出,包括降低fcc石脑油终沸点(endpoint)。由于对中间馏分产品的需求不断增长,石油精炼厂面临并由本公开解决的问题是如何有效且经济地选择性增加来自现有原料的中间馏分燃料组分的产量以满足该需求。技术实现要素:本公开的方法解决了如何选择性增加中间馏分燃料组分的产量的问题,在本公开的方法中,适合用作汽油调合组分的烃组合物被催化烷基化为中间馏分,所述中间馏分包括适合用作航空燃油和柴油燃油的组分。芳族化合物在催化剂存在下被原料流中已经存在的烯烃烷基化,产生包括柴油调合组分的中间馏分。在一个实施方式中,在催化剂存在下,使碳数为5至14的烯烃石脑油原料流与芳族化合物反应,产生烷基化芳族化合物,从而提高了相应燃料组分的沸点。原料可源自单元操作,例如fcc单元、延迟焦化单元、流化焦化单元、减粘裂化单元、常规热裂化单元、热解单元、流裂化单元或它们的组合.提质炼油厂原料的方法,该炼油厂原料包含源自单一烃裂化单元操作,该炼油厂原料是富含c5至c14烯烃和沸点为15℃至250℃的芳烃的复杂混合物,所述方法包括:a.将原料引入烷基化单元,所述原料包含适合用作汽油调合组分的芳族化合物和烯烃化合物,该烷基化单元中包含至少一种具有路易斯酸和/或布朗斯台德酸活性的催化剂,产生具有更高沸程的烷基化产物流;b.回收来自烷基化单元的烷基化产物流;和c.从烷基化产物流中分离中间馏分。如本文所用,术语“石脑油”和“汽油”是指沸点在约36℃至180℃范围内的烃类。石脑油是未加工的馏分,而汽油是最终产品。如本文所用,术语“中间馏分”是指在煤油和柴油范围内(通常在约140℃至370℃的范围内)沸腾的烃类。本文所用的术语“煤油”是指沸点范围为约140℃至240℃的烃类。如本文所用,术语“柴油”是指沸点范围为约180℃至370℃的烃类。附图说明下面将参考附图更详细地描述本公开的方法,其中:图1是根据本公开的集成的烷基化方法的简化方法流程图;图2a复现或表示由甲苯被1-辛烯烷基化产生的gs-ms反应产物的光谱图的相关部分;图2b是图2a的光谱图的放大区域,显示了甲苯被1-辛烯烷基化的gs-ms反应产物;图2c是c15h24的某些异构体的质谱图;图2d是c15h24的某些异构体的质谱图;图3是显示本公开的方法中柴油调合组分的产量和催化剂与油的重量比的关系的图;图4是显示本公开的方法中总液体产物的api比重和催化剂与油的比例的关系的图;和图5是显示原料的碳数和根据本发明的方法生产的所选产物的图。为清楚起见,简化的示意图和描述不包括炼油厂操作中通常使用的以及本领域普通技术人员众所周知的众多阀门、泵、温度传感器、电子控制器等。具体实施方式参考图1,其描述了本公开的方法的一个实施方式,其用于将含有碳数在5至14的芳烃和烯烃的烯烃重石脑油流催化转化为柴油沸点范围内的烷基化芳烃,来增加中间馏分产量。该集成的烷基化方法和用于实践该方法的系统通常称为100。原料流110a进入烷基化单元150,在烷基化单元150中,原料流110a与催化剂103接触一段时间,该时间足以通过离子成分完成芳族化合物的烷基化,该离子成分由混合原料流中存在的烯烃化合物的分解形成。烷基化产物流151被回收并通入分馏区170,在分馏区170,汽油和中间馏分被分离并分别作为产物流171和172回收,并且底部流173从分馏区170排出。分馏区170可包括分馏单元,例如闪蒸容器、分馏塔、气提、汽提、汽液分离器、蒸馏塔或这些单元的组合。在另一个实施方式中,氢气与烃原料流混合,优选混合至饱和水平,以提供富氢的液态烃原料流。原料流中氢气的存在增强了氢气转移反应并增加了催化剂的稳定性。氢与油的摩尔比在0.05:1至1:1的范围内,在优选实施方式中,氢与油的摩尔比为0.05:1至0.5:1。当氢气加入系统时,该方法既可以作为三相系统运行,即原料、过量氢气和固体催化剂;也可以是两相系统,其中所有存在的氢气均溶解在液态原料和催化剂中。系统是两相或是三相将取决于系统的操作压力和本领域技术范围内的其他反应条件。当系统中存在氢气时,它的作用是防止或最小化焦炭的形成,从而保持催化剂的活性。可以消耗氢气来氢化烯烃,但这种消耗将受限于系统中可用的氢气和热力学条件。由于溶解性,还会有氢损失。因此,氢气不会被大量消耗。在一些实施方式中,消耗的氢气的量为新鲜原料中h2的0.01至0.1wt%。如图1所示,过量摩尔量的氢气104与烷基化单元150上游的原料流110a混合。在两相系统中,增强烷基化反应中的氢转移所需的全部或大部分氢溶解在氢混合区中烷基化单元上游的液态原料中。在一个实施方式中,烷基化单元上游的氢分配容器接收氢气、新鲜原料和任选的已经通过烷基化反应器的再循环产物,并且液体在预定的压力和温度条件下是饱和的,以溶解至少大部分需要进入液态原料的氢气,产生合并的液体原料/溶解氢气流作为烷基化单元的原料。合并的液体原料/溶解氢流优选是氢饱和原料,也称为富氢原料。通过在烷基化单元上游在预定条件下闪蒸含有溶解氢的原料来消除或显著减少气体氢,产生含有溶解氢的液态烃原料的单一反应物相,所述溶解氢优选在烷基化单元150的普通操作条件的温度和压力下处于饱和水平。之后烷基化单元将作为两相系统运行,即,含有溶解氢的液态烃原料和一种以上的小粒径的固体多相催化剂。该任选的两相加氢实施方式采用氢分配容器102,其包括混合/分配区114,混合/分配区114在本文中也称为混合区,其具有至少一个用于接收液态烃原料流110b的入口和至少一个用于接收氢气流112的入口,或者,用于接收原料和氢气两者的组合入口,以及用于排放富氢原料和过量氢的组合流120的出口。闪蒸区126具有与排出组合流120的出口流体连通的入口、与混合/分配区114的一个以上氢气入口流体连通的气体出口128、以及用于排放富氢原料的出口(132)。在该实施方式中,富氢原料被送至烷基化单元150。在氢分配容器102的操作中,液态烃原料流110b在混合/分配区114中与氢气流112紧密混合以将预定量的氢气溶解在液体混合物中,产生富氢液态烃原料和过量氢气。进入的氢气流112包括新鲜氢气流116和来自闪蒸区126的再循环氢气流118。流120被输送到闪蒸区或闪蒸容器126中,在闪蒸区或闪蒸容器126中,未溶解的氢气和存在的任何其他气体(例如轻质原料馏分)被闪蒸出来并作为闪蒸流128移除。闪蒸区126可包括一个以上的闪蒸罐,这些闪蒸罐在合适的压力和温度条件下运行,以在液态烃溶液进入下游烷基化单元150时保持液态烃溶液中的氢气的预定浓度,该烷基化单元150在预定的温度和压力条件下运行。再循环氢气流128的一部分118被再循环并与新鲜氢气原料116混合。氢气流112中再循环氢气的量通常取决于与从闪蒸区126回收的过量未溶解氢气的量有关的许多因素。闪蒸气体的剩余部分作为排放流130从系统中排出。图1中描述的混合/分配区114可以是实现液体和气体必要的紧密混合的任何装置,使得氢气在预定条件下溶解在液态烃原料中,以根据反应机理实现所需的烷基化程度。在其他实施方式中,混合区可包括用于氢气和原料的组合入口。有效的单元操作包括一个以上的气液分配容器,该装置可包括喷射器、喷嘴或其他提供足够的速度的设备,以将氢气注入液态烃中并伴随湍流混合,从而促进氢饱和。在烷基化单元150中,将含有预定量的溶解氢(优选处于饱和水平)的富氢烃原料流132与催化剂103合并。原料流110a或110b源自任何合适的单元操作,其在炼油厂的电池范围内可方便并地获得。例如,原料流的来源可以是fcc装置、热裂化装置或其组合。合适的烯烃流来自以下类型的热裂化单元操作:延迟或流化焦化单元、减粘裂化单元、常规热裂化单元、热解单元、蒸汽裂化单元和不使用氢气的其他裂化工艺。对于本领域的普通技术人员来说显而易见的是,并非所有这些单元操作都可能在单个炼油厂内找到。在某些实施方式中,原料中的烯烃浓度可以在1wt%至60wt%的范围内。在优选的实施方式中,原料中烯烃浓度范围(wt%)为30-46、30-59、30-9、39-46、39-59、39-9、6-46、6-59或6-9wt%。在某些实施方式中,原料中的芳族浓度在1wt%至60wt%的范围内。在优选的实施方式中,原料中芳族的浓度范围(wt%)为13-19、13-16、13-37、10-19、10-16、10-37、25-19、25-16或25-37wt%。用于该方法的合适的催化剂是可溶性均相化合物或非均相化合物,选自:具有路易斯酸和/或布朗斯台德酸位点的树脂、非晶或结构化金属氧化物、金属氟化物、金属氯化物。基于本领域普通技术人员已知的或通过常规实验确定的特征,催化剂中的金属选自元素周期表iupac第4-12族。在某些实施方式中,用于该方法的合适的催化剂是非晶硅铝催化剂或沸石催化剂。沸石可以选自:afi-、ats-、beta-、con-、emt-、euo-、fau-、fer-、ifr-、itq-、mfi-、mor-、mse-、mtw-、mww-、nes-、nfi-、stf-、mcm-和zsm型沸石。优选的沸石包括fau-、mor-、beta-、mfi-和mcm型沸石。在一些实施方式中,强酸是优选的,例如具有高pf-值的那些,例如具有大于1.0的pf-值的那些。在优选的实施方式中,使用具有路易斯酸度和布朗斯台德酸度两者的多相催化剂。在烷基化单元中存在具有相似功能的催化剂的组合,即烷基化催化剂。在某些实施方式中,适用于本方法的催化剂包括christie等人公开的pf-值大于1的路易斯酸。这些酸包括sbf5、alf3、alfcl2、alf2cl、alcl3、teof4、inf3、gaf3、asf3、snf5、snf4、cis-io2f3、pf5、seof4、tef4、bf3、gef4、cif5、brf3、sif4、sef4、sof4、xeof4、tef6、pof3、xef4、sf4、cof2、pf3、hf、no2f和nof。在一些实施方式中,烷基化反应可在约25℃至小于250℃的温度下进行。在优选的实施方式中,烷基化反应在约25℃至90℃范围内的温度下进行。在某些实施方式中,烷基化反应在约1bar至30bar范围内的压力下进行。在所有实施方式中,烷基化产物流151具有比初始原料流110a或110b更高的沸点范围。如前所述,为了清楚起见,没有示出本领域技术人员已知的附加设备,例如泵、压缩机、分离容器等。实施例1:通过1-辛烯烷基化甲苯:在不同的催化剂与油和甲苯与1-辛烯的比例下,使用alcl3催化剂进行了六个反应。所有反应均在90℃的温度和大气压的条件下进行,保持4小时。表1总结了运行参数。表1参考图2a,得到的gc-ms色谱描绘了甲苯被1-辛烯烷基化的结果,其对应于表1的运行编号1。图2b描绘了烷基化产物的放大区域,并清楚地显示了八种不同结构的/立体异构体。异构体的经验化学式为c15h24,其中确认了在甲苯环上具有不同结构或立体异构体的烷基。这些色谱清楚地表明实现了1-辛烯对甲苯的烷基化。图2a显示了甲苯和1-辛烯在相对较短的保留时间(即5-6分钟)洗脱,而更重的烷基化产物在更长的保留时间(即10-10.6分钟)洗脱。图2c显示了图2b中由正方形标识的峰的质谱。质谱示出了与甲基化苯物种(m/z105)一致的特征。图2d显示了图2b中由三角形标识的峰的质谱。质谱示出了与二甲基化苯物种(m/z119)一致的特征。为了对比,在1-辛烯对甲苯的烷基化中使用usy-5作为催化剂,并且以使用alcl3时类似的方式进行烷基化。usy-5是一种y型沸石,其二氧化硅与氧化铝的摩尔比为5。在使用usy-5作为催化剂的任何运行中都没有明显的反应。实施例2:使用未经任何预处理的fcc石脑油原料进行芳烃烷基化运行。fcc石脑油的性质列于表2中。原料流的组成成分为17.7wt%,沸点高于180℃。表2以下反应组使用了四种不同的催化剂。第一种催化剂是alcl3,如上面讨论的,其为已知的路易斯酸催化剂。第二种催化剂是zeo1,一种不含活性相金属的沸石系催化剂,设计用于在高温和低压下裂解重油。第三种催化剂是zeo2e,一种挤出物形式的沸石系催化剂,含有ni和mo作为活性相金属,设计用于加氢裂化工艺。第四种催化剂是zeo2p,一种粉末形式的沸石系催化剂,含有ni和mo作为活性相金属,设计用于加氢裂化工艺。zeo2e和zeo2p都具有负载在催化剂上的4wt%氧化镍和16wt%氧化钼。此外,zeo1、zeo2e和zeo2p沸石包含sio2和al2o3,其中一部分al2o3被tio2和zro2取代,即它们的骨架被改性。通过改变催化剂与油的重量比,对每种催化剂进行了一系列反应。表3总结了反应条件的矩阵。催化剂的质量已标准化为沸石含量。表3运行编号催化剂催化剂类型c/o比例,g/kg1-6alcl3粉末6.7-65.77-12*zeo1粉末2.0-19.713-17*zeo2e挤出物6.5-52.418无催化剂-19-24*zeo2e挤出物6.7-65.7gc-ms分析表明,使用alcl3催化剂可成功地将fcc石脑油原料烷基化。石脑油向柴油调合组分的转化率随着催化剂与油比例的增加而增加。图3示出了催化剂-油的比例与柴油产量的关系。例如,使用alcl3作为催化剂且催化剂与油的比例为65.7g/kg时,观察到柴油产量增加了22v%。该值代表了与原料相比,在柴油范围内沸腾的组分量的增加。由于烷基化作用增加了分子量,因此总液体产物的api比重下降。图4示出了液体产物的api比重随催化剂-油比例的变化。如表2所示,原料流的api比重为54.3°。当alcl3催化剂-油比例为52.3时,api比重下降至43.6°,造成了api比重10.7°的下降。根据该数据,在所指定的恒定反应条件下,alcl3看上去是最活跃的催化剂。上述结果表明,芳烃被存在于裂化石脑油中的烯烃烷基化,使烃的沸点从石脑油范围转移到中间馏分范围。在石脑油范围内沸腾的烃被转化为在中间馏分范围内沸腾的烃,其用作柴油调合组分。参考图5,其示出了使用alcl3和zeo2e作为催化剂运行时的碳数相对丰度,催化剂与油的比例分别为65.7和52.4,并且两个催化剂的碳数均发生增加。从该数据看来,alcl3在所指定的恒定反应条件下是最活跃的催化剂。本发明的方法和系统已在上述和附图中进行了描述,对于本领域普通技术人员来说,修改是显而易见的,并且本发明的保护范围将参照权利要求书确定。当前第1页12
再多了解一些
本文用于企业家、创业者技术爱好者查询,结果仅供参考。