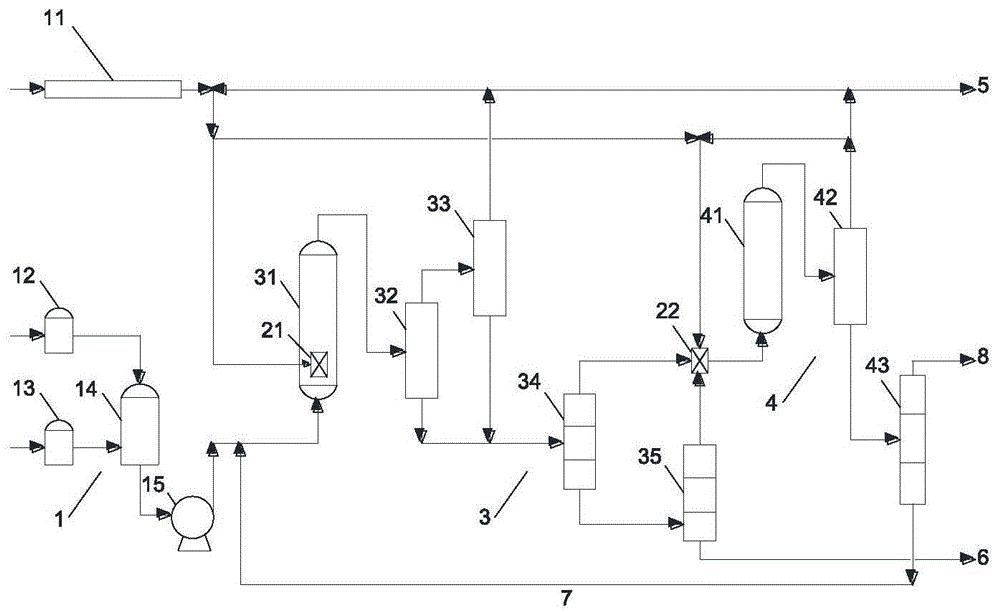
本实用新型涉及煤直接液化的技术领域,具体而言,涉及一种煤直接液化的乳化床强化反应系统。
背景技术:
煤直接液化技术早在19世纪即已开始研究。1914年德国化学家柏吉斯研究氢压下煤的液化,同年与比尔维勒共同取得此项试验的专利权。1926年,德国法本公司研究出高效加氢催化剂,用柏吉斯法建成一座由褐煤高压加氢液化制取液体燃料的工厂。第二次世界大战前,德国由煤及低温干馏煤焦油生产液体燃料,1938年已达到年产1.5mt的水平,第二次世界大战后期,总生产能力达到4mt;1935年英国卜内门化学工业公司在英国比灵赫姆也建起一座由煤及煤焦油生产液体燃料的加氢厂,年产150kt。此外,日本、法国、加拿大及美国也建过一些实验厂。战后,由于石油价格下降,煤液化产品经济上无法与天然石油竞争,遂相继倒闭,甚至实验装置也都停止试验。至60年代初,特别是1973年石油大幅度提价后,煤直接液化工作又受到重视,并开发了一批新的加工过程,如美国的溶剂精炼煤法、埃克森供氢溶剂法、氢煤法等。
axens北美有限公司在煤直接液化技术开发和示范方面具有悠久历史,起源于上世纪60年代。煤直接液化技术的开发基于工业氢-油工艺,并证明了乳化床反应器技术具有显著的通用性。包括氢-油工艺、ctsl(二级催化液化法)和煤/油混合加工工艺在内的这些技术,处于当今世界上煤液化技术的领先的地位。
但是,在使用乳化床反应器对煤进行直接液化的反应过程中,由于氢气无法与煤浆充分反应,从而导致反应效率降低。
技术实现要素:
鉴于此,本实用新型提出了一种煤直接液化的乳化床强化反应系统,旨在解决现有技术中氢气无法与煤浆充分反应,导致的煤直接液化过程中反应效率低下的问题。
本实用新型提出了一种煤直接液化的乳化床强化反应系统,包括:
进料单元,用以制备煤浆,并对煤浆和氢气进行输送;
乳化床液化单元,其与所述进料单元连接,作为所述煤浆与氢气进行液化反应的场所,并对所述液化反应产物进行分离和蒸馏;
乳化床加氢单元,其与所述乳化床液化单元连接,用以对所述轻质馏分和所述馏出油进行催化加氢反应;
微界面发生器,分别设置在所述乳化床液化单元和所述乳化床加氢单元之前,用以将煤直接液化过程中的气体的压力能和/或液体的动能转变为气泡表面能,使氢气破碎成直径为微米级别的微气泡。
进一步地,上述煤直接液化的乳化床强化反应系统中,所述微界面发生器选自气动式微界面发生器、液动式微界面发生器以及气液联动式微界面发生器中的一种或几种。
进一步地,上述煤直接液化的乳化床强化反应系统中,所述微界面发生器包括:第一微界面发生器和第二微界面发生器;其中,所述第一微界面发生器设置在所述乳化床液化单元内,所述第二微界面发生器与设置在所述乳化床液化单元与所述乳化床加氢单元之间。
进一步地,上述煤直接液化的乳化床强化反应系统中,所述微米级别的微气泡为直径大于等于1μm、小于1mm的微气泡。
进一步地,上述煤直接液化的乳化床强化反应系统中,所述乳化床液化单元,包括:内部设置有所述第一微界面发生器的第一乳化床反应器、分离器以及蒸馏塔。
进一步地,上述煤直接液化的乳化床强化反应系统中,所述乳化床加氢单元,包括:与所述第二微界面发生器相连的第二乳化床反应器、气液分离器以及产品分馏塔。
进一步地,上述煤直接液化的乳化床强化反应系统中,所述进料单元包括:用于制备和输送煤浆的浆体输送单元与用于输送氢气的气体输送单元。
进一步地,上述煤直接液化的乳化床强化反应系统中,所述分离器包括:与所述第一乳化床反应器相连的高温分离器和与所述高温分离器相连的低温分离器。
进一步地,上述煤直接液化的乳化床强化反应系统中,所述蒸馏塔包括:与所述分离器相连的常压蒸馏塔和与所述常压蒸馏塔相连的减压蒸馏塔
本实用新型的有益效果在于,本实用新型提供的煤直接液化的乳化床强化反应系统,通过将微界面发生器分别设置在所述液化反应单元和所述液化反应单元与所述催化加氢单元之间。所述微界面发生器分在所述液化反应、催化加氢反应之前将所述氢气在所述微界面发生器中破碎成直径为大于等于1μm、小于1mm的微气泡,以增大反应过程中所述氢气与相对应的反应物之间的相界传质面积,同时减小液膜厚度,降低传质阻力,提高反应相之间的传质效率,进而解决现有技术中由于氢气无法与煤浆充分反应,导致的煤直接液化过程中反应效率低下的问题。同时,本实用新型中可以根据不同原料组成、不同的产品要求或不同的催化剂,而灵活地进行预设操作条件的范围调整,以确保反应的充分有效进行,进而保证反应速率,达到了强化反应的目的。
尤其是,所述液化反应单元设置有,高温分离塔、低温分离器、常压蒸馏塔和减压蒸馏塔,可对液化反应的产物进行分离和蒸馏,生成轻质馏分、馏出油和氢气同时将废弃和固体残渣排除系统,从而提高系统的反应效率,增大资源的利用效率。
附图说明
通过阅读下文优选实施方式的详细描述,各种其他的优点和益处对于本领域普通技术人员将变得清楚明了。附图仅用于示出优选实施方式的目的,而并不认为是对本实用新型的限制。而且在整个附图中,用相同的参考符号表示相同的部件。在附图中:
图1为本实用新型实施例的煤直接液化的乳化床强化反应系统的结构图。
具体实施方式
为了使本实用新型的目的和优点更加清楚明白,下面结合实施例对本实用新型作进一步描述;应当理解,此处所描述的具体实施例仅仅用于解释本实用新型,并不用于限定本实用新型。
下面参照附图来描述本实用新型的优选实施方式。本领域技术人员应当理解的是,这些实施方式仅仅用于解释本实用新型的技术原理,并非在限制本实用新型的保护范围。
需要说明的是,在本实用新型的描述中,术语“上”、“下”、“左”、“右”、“内”、“外”等指示的方向或位置关系的术语是基于附图所示的方向或位置关系,这仅仅是为了便于描述,而不是指示或暗示所述装置或元件必须具有特定的方位、以特定的方位构造和操作,因此不能理解为对本实用新型的限制。
此外,还需要说明的是,在本实用新型的描述中,除非另有明确的规定和限定,术语“安装”、“相连”、“连接”应做广义理解,例如,可以是固定连接,也可以是可拆卸连接,或一体地连接;可以是机械连接,也可以是电连接;可以是直接相连,也可以通过中间媒介间接相连,可以是两个元件内部的连通。对于本领域技术人员而言,可根据具体情况理解上述术语在本实用新型中的具体含义。
参阅图1所示,为本实用新型实施例提供的煤直接液化的乳化床强化反应系统,其包括:进料单元1、乳化床液化单元3、微界面发生器、乳化床加氢单元4;其中,进料单元1,用以制备煤浆,并对煤浆和氢气进行输送;所述乳化床液化单元3用以将所述煤浆和氢气进行液化反应,将液化反应产物进行分离和精馏得到馏出油和轻质馏分,所述乳化床液化单元3分别与进料单元1和第二微界面发生器22的进口端连接。第二微界面发生器22进口端还与进料单元1连接,出口端与乳化床加氢单元4连接,用以接收液化反应产物中的轻质馏分、馏出油、氢气以及进料单元1输送的氢气,并将氢气破碎成直径大于等于1μm、小于1mm的微米级气泡,破碎完成后将微米级气泡与轻质馏分和馏出油混合形成气液乳化物,并运输所述气液乳化物至乳化床加氢单元4。乳化床加氢单元4,用以气液乳化物进行催化加氢反应,并对其产物进行分离和精馏,最终生成供氢性溶剂和产品油。
具体而言,所述进料单元1包括:氢气进料管道11、煤前处理装置12、催化剂制备装置13、煤浆制备装置14和煤浆泵15。其中所述氢气进料管道11一端外接氢气源另一端分别与乳化床液化单元3、微界面发生器和乳化床加氢单元4连接,用以氢气的运输;所述煤前置处理器与所述煤浆制备装置14入口端连接,用以原料煤粉的制备;所述催化剂制备装置13与所述煤浆制备装置14入口端连接,用以将催化剂原料制备成超细颗粒的催化剂粉末;所述煤浆制备装置14出口端与煤浆泵15入口连接,用以接收原料煤粉和催化剂粉末,并向煤浆制备装置14中注入供氢性溶剂,将原料煤粉、催化剂粉末和供氢性溶剂混合形成煤浆;所述煤浆泵15出口端与所述乳化床液化单元3连接,用以将煤浆制备装置14所制备的煤浆输送至乳化床液化单元3,进行液化反应。
当系统运行时,液化原料煤经过煤前处理装置12干燥粉碎后制成一定粒度的煤粉。催化剂原料经过催化剂制备装置13制成超细颗粒的催化剂。煤粉和催化剂在煤浆制备装置14与供氢性溶剂混合制成煤浆,煤浆制备完成后进入乳化床液化单元3,与此同时,氢气输送管道将氢气输送至乳化床液化单元3。
具体而言,所述微界面发生器通过将气体的压力能和/或液体的动能转变为气泡表面能并传递给氢气气泡,使氢气破碎成直径为微米级别的微米级气泡。同时,所述微界面发生器根据能量输入方式或气液比分为气动式微界面发生器、液动式微界面发生器或气液联动式微界面发生器;其中,气动式微界面发生器采用气体驱动,输入气量远大于液体量;液动式微界面发生器采用液体驱动,输入气量一般小于液体量;气液联动式微界面发生器采用气液同时驱动,输入气量接近于液体量。本实施例中,所述微界面发生器包括:第一微界面发生器21和第二微界面发生器22;其中,所述第一微界面发生器21设置在所述乳化床液化单元3内,所述第二微界面发生器22与设置在所述乳化床液化单元与所述乳化床加氢单元之间,同时所述第一微界面发生器21、所述第二微界面发生器22均选自气动式微界面发生器、液动式微界面发生器和气液联动式微界面发生器中的一种或几种。
具体而言,所述乳化床液化单元3包括:第一乳化床反应器31、高温分离器32、低温分离器33、常压精馏塔34和减压精馏塔35;其中,所述第一微界面发生器21位于所述第一乳化床反应器31内部,其与氢气进料管道11连接,用以将氢气破碎成直径大于等于1μm小于1mm的微米级气泡,并将微米级气泡输送至第一乳化床反应器31内部;所述第一乳化床反应器31进口端分别与煤浆泵15和乳化床加氢单元4连接,出口端与所述高温分离器32入口连接,用以接收煤浆和氢气微米级气泡,并作为煤浆和氢气微米级气泡液化反应的反应腔室;所述高温分离器32出口端分别与低温分离器33和常压精馏塔34的入口端连接,用以将液化反应产物进行气液分离,得到气相产物进入低温分离器33,液相产物进入常压精馏塔34;所述低温分离塔出口端分别与氢气进料管道11和常压精馏塔34连接,用以接收所述高温分离器32中分离出来的气相产物,并对气相产物进一步进行气液分离,所产生的气相产物进入氢气进料管道11与氢气混合循环使用,废气5部分排除系统,所产生的液相产物进入常压分馏塔;所述常压分馏塔出口端分别与第二微界面分离器和减压精馏塔35连接,用以将高温分离器32和低温分离器33所生成的液相产物进行分馏,得到轻质馏分进入第二微界面发生器22,塔底物料进入减压精馏塔35;所述减压精馏塔35出口端与第二微界面发生器22入口端连接,用以将常压精馏塔34生成的塔底物料进行沥青和固体的脱出,得到馏出油进入第二微界面发生器22,液化残渣6排除系统。
氢气进入第一微界面发生器21,破碎成微米级气泡后进第一乳化床反应器31,与进入第一乳化床反应器31的煤浆进行液化反应,第一乳化床反应器31生成的液化反应产物进入高温分离器32进行气液分离,高温分离器32分离得到的气相产物进入低温分离器33进一步气液分离,低温分离器33得到的气相产物与氢气混合循环使用,废气5部分被排出系统。高温分离器32和低温分离器33的液相产物进入常压精馏塔34分离出轻质馏分,常压精馏塔34塔底物料进入减压精馏塔35进行沥青和固体的脱除,减压精馏塔35塔底物料即为液化残渣6,并将液化残渣6排出系统。为了保证残渣能在一定温度下顺利排除,一般控制残渣中的固体含量为50-55wt%。常压精馏塔34和减压精馏塔35生成的轻质馏分、馏出油与氢气混合进入第二微界面发生器22内部。
具体而言,所述乳化床加氢单元4包括:第二乳化床反应器41、气液分离器42以及产品分馏塔43。其中所述第二乳化床反应器41入口端与所述第二微界面发生器22出口端连接,其出口端与所述气液分离器42入口端连接,用以接收第二微界面发生器22生成的气液乳化物,并作为所述气液乳化物的催化加氢反应腔室;所述气液分离器42出口端分别与所述产品分馏塔43和氢气进料管道11连接,用以对催化加氢产物进行气液分离,得到的气相产物与氢气混合循环使用,废弃部分排除系统,得到的液相产物进入产品分馏塔43;所述产品分馏塔43还与所述第一乳化床反应器31连接,用以对气液分离器42生产的液相产物进行分馏,得到产品油8和循环溶剂7,所述循环溶剂7循环至第一乳化床反应器31进行二次液化反应。
第二微界面发生器22将氢气破碎成微米级气泡并使得微米级气泡与所述轻质馏分和馏出油混合形成气液乳化物,将所述气液乳化物输送至第二乳化床反应器41内部,第二乳化床反应器41进行以提高气液乳化物供氢性能为目的催化加氢,第二乳化床反应器41出口物料进入气液分离器42进行气液分离,气液分离器42生成的气相产物与氢气混合循环使用,废气5部分被排出系统。气液分离器42生成的液相物料进入产品分馏塔43,分馏出产品油8和循环溶剂7。其中循环溶剂7循环至第一乳化床反应器31进行二次液化反应,产品油8全部为汽油、柴油馏分。
本实施例中的煤直接液化的乳化床强化反应系统,通过在第一乳化床反应器31内部设置第一微界面发生器21和第二乳化床反应器41入口端设置第二微界面发生器22,使得在液化反应和催化加氢反应之前氢气在相应微界面发生器中破碎成直径为微米级别的微米级气泡,有效地增大了反应过程中所述氢气与煤浆等反应物之间的相界传质面积,提高了反应相之间的传质效率,进而解决了现有技术中氢气无法与煤浆充分反应,导致的煤直接液化过程中反应效率低下的问题。
下面结合具体实施例对本实用新型所述系统的具体方法与效果作进一步说明。
一种煤直接液化的乳化床强化反应方法,包括:
将原料煤制备成一种煤浆,并将煤浆送入第一乳化床反应器,与此同时,将氢气通入第一微界面发生器;
所述第一微界面发生器将所述氢气破碎成微米尺度的微米级气泡,并将微米级气泡输送至第一乳化床反应器内部与所述煤浆进行液化反应;
将液化反应产物在分离器中进行气液分离,其中的液相部分通过精馏塔形成轻质馏分和馏出油,将所述轻质馏分和馏出油进行混合后与氢气一同送至所述第二微界面发生器内部;
所述第二微界面发生器将所述氢气破碎成微米尺度的微米级气泡,并将微米级气泡与所述轻质馏分和馏出油的混合物进行气液混合形成气液乳化物,并将乳化物送至第二乳化床反应器内部,进行催化加氢反应;
将催化加氢产物通过分馏塔分离出产品油和其它供氢性溶剂。
本实施例中,液化反应的反应温度为400-450℃,压力为2-14mpa,气液比为100-2000,空速为0.7-1.2h-1。
本实施例中,催化加氢反应的反应温度为330-380℃,压力为5-12mpa,气液比为250-700,空速为0.5-2.0h-1。
可以理解的是,可以根据不同原料组成、不同的产品要求或不同的催化剂,而灵活地进行预设操作条件的范围调整,以确保反应的充分有效进行,进而保证反应速率,达到了强化反应的目的。同时,本实施例中不具体限定催化剂的种类,其可以为铁系催化剂、钼系催化剂、镍系催化剂、钴系催化剂以及钨系催化剂中的一种或几种组合,只要能够确保强化反应顺利进行即可。
为了进一步验证本实用新型所提供的加工方法,结合实施例和对比例进一步说明本实用新型的有益效果。
下面是使用本实用新型的优选实施例,对一种强化煤在三种不同反应条件下进行直接液化的液化结果。
实施例一:
反应器温度:第一乳化床反应器400℃,第二乳化床反应器330℃。
反应压力:第一乳化床反应器2mpa,第二乳化床反应器5mpa。
气液比:第一乳化床反应器100,第二乳化床反应器250。
空速:第一乳化床反应器0.7h-1,第二乳化床反应器0.5h-1。
煤浆浓度:40/50(干煤/溶剂,质量比)。
催化剂添加量:液化催化济:1.0wt%(铁/干煤)。
硫添加量:s/fe=2(摩尔比)。
本实施例中,煤的转化率为82.43%,产品中含有油产量为52.23%,氢耗为8.59%。
实施例二:
反应器温度:第一乳化床反应器420℃,第二乳化床反应器350℃。
反应压力:第一乳化床反应器8mpa,第二乳化床反应器8mpa。
气液比:第一乳化床反应器1000,第二乳化床反应器500。
空速:第一乳化床反应器1.0h-1,第二乳化床反应器1.3h-1。
煤浆浓度:40/50(干煤/溶剂,质量比)。
催化剂添加量:液化催化济:1.0wt%(铁/干煤)。
硫添加量:s/fe=2(摩尔比)。
本实施例中,煤的转化率为83.39%,产品中含有油产量为58.28%,氢耗为7.10%。
实施例三:
反应器温度:第一乳化床反应器450℃,第二乳化床反应器380℃。
反应压力:第一乳化床反应器14mpa,第二乳化床反应器12mpa。
气液比:第一乳化床反应器2000,第二乳化床反应器700。
空速:第一乳化床反应器1.2h-1,第二乳化床反应器2.0h-1。
煤浆浓度:40/50(干煤/溶剂,质量比)。
催化剂添加量:液化催化济:1.0wt%(铁/干煤)。
硫添加量:s/fe=2(摩尔比)。
本实施例中,煤的转化率为90.33%,产品中含有油产量为62.96%,氢耗为6.76%。
显然,本领域的技术人员可以对本实用新型进行各种改动和变型而不脱离本实用新型的精神和范围。倘若本实用新型的这些修改和变型属于本实用新型权利要求及其等同技术的范围之内,则本实用新型也意图包含这些改动和变型在内。
本文用于企业家、创业者技术爱好者查询,结果仅供参考。