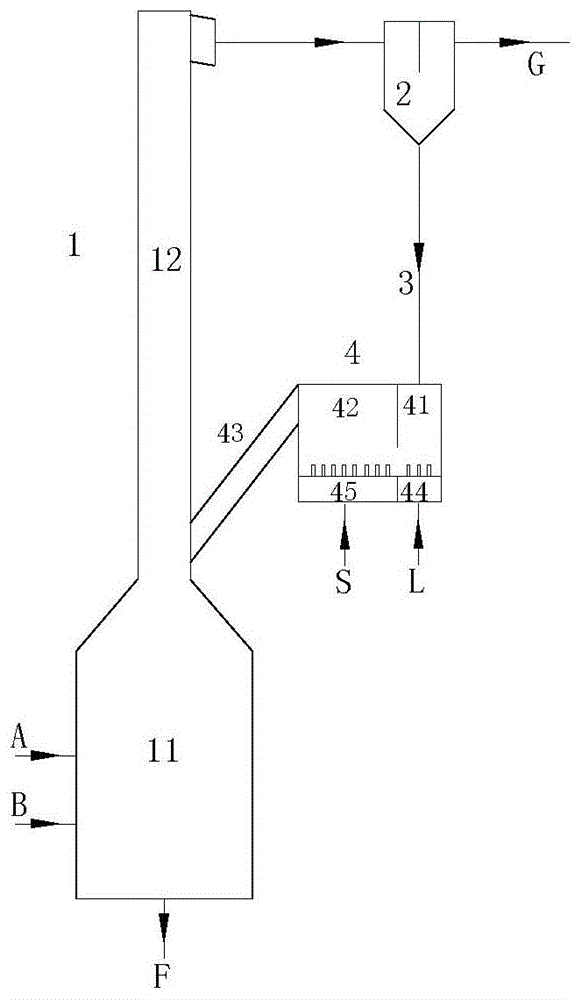
本发明涉及燃料气化技术领域,具体地,涉及一种循环流化床部分气化装置以及一种循环流化床部分气化方法。
背景技术:
煤炭气化技术是洁净煤技术的重要组成部分,是高效、洁净利用煤炭的主要途径之一,已成为众多现代能源和化工系统的核心技术。煤部分气化技术充分利用了煤的不同组分的不同反应特性,实现煤炭分级利用,将煤中易于气化的部分进行气化提取作为高附加值煤气,部分气化后的剩余物-焦炭用作冶金、机械与化工的重要原料或燃料。
煤部分气化技术的目标产品是高附加值煤气及半焦产品,且煤气中不含焦油。目前,煤部分气化的关键问题在于解决煤气中含有焦油的问题。脱除方法主要包括生物脱除法、物理脱除法和化学脱除法。其中,化学脱除法是在一定温度和特定气氛下通过化学反应将焦油转化为小分子气体化合物,可充分将焦油转化为有效气,主要包含热裂解脱除法、部分氧化脱除法、催化重整脱除法等。一般而言,热裂解脱除法的有效脱除温度需要大于1250℃,气体的停留时间大于0.5s。在实际应用过程中,对设备材质和保温效果的要求都比较苛刻,同时热裂解过程中易于生成积碳。部分氧化脱除法在实际应用中不单独使用,需要通过第二气化剂来实现,会影响煤气热值。催化重整脱除法是煤焦油在催化剂作用下将焦油催化转化为有用气体组分的方法。常见的催化剂有碱金属和其他金属基催化剂、非金属氧化物催化剂和木炭与生物质焦等。
技术实现要素:
本发明的目的在于至少部分地克服现有技术的缺陷,提供一种新的循环流化床部分气化装置以及循环流化床部分气化方法。
本发明的目的还在于提供一种循环流化床部分气化装置以及循环流化床部分气化方法,能够在温和反应条件下生产高附加值煤气及半焦产品。
本发明的目的还在于提供一种循环流化床部分气化装置以及循环流化床部分气化方法,有效降低煤气中的焦油含量。
本发明的目的还在于提供一种循环流化床部分气化装置以及循环流化床部分气化方法,能够简化系统工艺,并降低运行成本。
为达到上述目的或目的之一,本发明的技术解决方案如下:
一种循环流化床部分气化装置,所述循环流化床部分气化装置包括气化炉炉膛、气固分离器和返料器,其中,气化炉炉膛与气固分离器相连通,气固分离器与返料器相连通,返料器与气化炉炉膛相连通,所述气化炉炉膛上设有燃料入口、第一气化剂入口、炉膛顶部出口、固体产品出口和返料口,所述气固分离器设置有气体产品出口,
所述气化炉炉膛具有变径结构。
根据本发明的一个优选实施例,所述气化炉炉膛包括位于下部的鼓泡区和位于上部的输送区,并且鼓泡区的最大炉膛横截面积大于输送区的最大炉膛横截面积。
根据本发明的一个优选实施例,鼓泡区的最大炉膛横截面积是输送区的最大炉膛横截面积的1.2-4倍。
根据本发明的一个优选实施例,鼓泡区的最大炉膛横截面积是输送区的最大炉膛横截面积的1.4-1.6倍。
根据本发明的一个优选实施例,所述返料器被配置为使得从气固分离器分离的循环物料能够在返料器内发生反应。
根据本发明的一个优选实施例,所述返料器包括第二气化剂入口,用于向返料器内供应第二气化剂。
根据本发明的一个优选实施例,所述返料器包括第二气化剂布风装置,所述第二气化剂入口设置在第二气化剂布风装置上。
根据本发明的一个优选实施例,所述返料器包括进料室、反应室和返料管,进料室的入口与气固分离器的循环物料出口相连通,进料室和反应室的下端彼此连通,返料管的入口和反应室的出口相连通,返料管的出口与气化炉炉膛的返料口相连通。
根据本发明的一个优选实施例,所述第二气化剂布风装置设置在反应室的下方。
根据本发明的一个优选实施例,所述返料器包括第二气化剂入口,用于向返料器内供应第二气化剂,所述第二气化剂入口设置在反应室的下部。
根据本发明的一个优选实施例,在进料室的下方设置有流化风布风装置,并且在所述流化风布风装置上设置有流化风入口,用于向进料室内供应流化风。
根据本发明的一个优选实施例,所述返料管包括附加第二气化剂入口,用于向返料管内供应附加第二气化剂。
根据本发明的一个优选实施例,所述返料管包括附加第二气化剂布风装置,所述附加第二气化剂入口设置在附加第二气化剂布风装置上。
根据本发明的一个优选实施例,所述反应室的与水平面平行的截面的横截面积大于或等于所述进料室的与水平面平行的截面的横截面积。
根据本发明的一个优选实施例,气化炉炉膛的返料口位于输送区,和/或燃料入口和第一气化剂入口位于鼓泡区。
根据本发明的一个优选实施例,所述固体产品出口设置在鼓泡区上。
根据本发明的一个优选实施例,所述鼓泡区具有变径结构,并且鼓泡区的下部的横截面积小于鼓泡区的中部的横截面积。
根据本发明的一个优选实施例,在所述鼓泡区和输送区之间设置有喉口段,所述喉口段的最小横截面积小于输送区的最大横截面积。
根据本发明的一个优选实施例,所述喉口段的最小横截面积与输送区的最大横截面积的比值为0.7-0.95。
根据本发明的一个优选实施例,所述附加第二气化剂布风装置设置在返料管的底部。
根据本发明的一个优选实施例,所述喉口段和/或输送区上设置有配风口,用于供应配风。
根据本发明的一个优选实施例,所述配风为含氧气体。
根据本发明的一个优选实施例,在所述返料器上设置有次级固体产品出口,用于排出次级固体产品。
根据本发明的一个优选实施例,所述返料器包括附加燃料入口,用于向返料器内供应附加燃料。
根据本发明的一个优选实施例,所述附加燃料入口设置在反应室上。
根据本发明的一个优选实施例,所述反应室还设置有气体出口,所述气体出口与气化炉炉膛的上部相连通。
根据本发明的一个优选实施例,所述循环流化床部分气化装置还包括二级回料阀,设置在气化炉炉膛和返料管之间,所述二级回料阀的进口与返料管的出口连通,所述二级回料阀的出口与气化炉炉膛连通。
根据本发明的一个优选实施例,所述循环流化床部分气化装置还包括立管,设置在气固分离器和返料器之间。
根据本发明的另一个方面,提供了一种循环流化床部分气化方法,采用如前述实施例中任一项所述的循环流化床部分气化装置,所述循环流化床部分气化方法包括:
a)将燃料与第一气化剂通入气化炉炉膛,发生部分气化反应,反应生成的部分固体产品从固体产品出口离开循环流化床炉膛,反应生成的气体携带部分固体物料进入气固分离装置,分离后的气体产品离开循环流化床;
b)使从气固分离器分离的循环物料通入返料器;
c)将返料器内的物料返回气化炉炉膛。
根据本发明的一个优选实施例,步骤b)包括:将第二气化剂通入返料器,与被气固分离装置分离并进入返料器的循环物料发生反应。
根据本发明的一个优选实施例,所述循环流化床部分气化方法还包括:
向返料器的返料管内供应附加第二气化剂。
根据本发明的一个优选实施例,所述循环流化床部分气化方法还包括:
使配风从配风口进入气化炉炉膛。
根据本发明的一个优选实施例,所述循环流化床部分气化方法还包括:
通过返料器上的次级固体产品出口排出次级固体产品。
根据本发明的一个优选实施例,第一气化剂中所含氧量与给入气化炉炉膛的燃料完全燃烧所需的氧量的比值为0.08-0.3。
根据本发明的一个优选实施例,所述第二气化剂为氧气或空气,或上述二者的混合物,或上述二者中的至少一者与水蒸气的混合物。
根据本发明的一个优选实施例,鼓泡区的流化速度为1m/s-2.5m/s,并且输送区的流化速度大于2.5m/s。
根据本发明的一个优选实施例,鼓泡区的温度为500-900℃,并且输送区的温度850-1300℃。
根据本发明的一个优选实施例,将返料器内生成的部分气体产物通过平衡管返回气化炉炉膛的上部;以及将返料器内生成的其它产物通过返料管返回气化炉炉膛。
根据本发明的一个优选实施例,第二气化剂中的氧气占第一气化剂、第二气化剂和配风中所含氧气总量的5%-25%。
根据本发明的一个优选实施例,所述循环流化床部分气化方法还包括:向返料器供应附加燃料。
根据本发明的一个优选实施例,进入返料器的反应室的第二气化剂与进入返料器的返料管的附加第二气化剂的组成不同。
根据本发明的一个优选实施例,反应室内的流化速度为0.4~2.5m/s。
根据本发明的一个优选实施例,反应室内的流化速度为0.4~1m/s。
根据本发明的一个优选实施例,控制反应室内的温度高于气化炉炉膛内的返料口以下的最高温度,并比燃料中灰在弱还原性气氛状态下的软化温度低50-150℃。
根据本发明的循环流化床部分气化装置以及循环流化床部分气化方法,在炉膛鼓泡区,燃料与第一气化剂在较低的气化剂氧当量比(气化剂中氧气量与燃料完全燃烧所需氧气量的比值)和反应温度条件下发生部分气化反应,生成大量半焦和含有焦油气的煤气,由于鼓泡区流化速度较低,较大颗粒的气化半焦不会被携带到炉膛上部,而是作为产品半焦从炉膛底部的固体产品出口(粗焦排渣口)排出;含有焦油气的煤气携带小颗粒半焦上升进入炉膛输送区;同时,1200℃-1300℃的高温气体及大量高温固体从返料器进入输送区,由于高温固体粒径小,在输送区的横截面积缩小的情况下,输送区的流化速度高,因此绝大部分高温固体直接被携带向上运动,在此过程中,一方面,高温气体及大量高温固体带入炉膛的热量使炉膛温度升高,使煤气中的焦油裂解,另一方面,来自鼓泡区的小颗粒半焦和来自返料器的半焦作为催化剂,对焦油进行催化重整,从而有效地降低了最终煤气中的焦油含量。
因此,本发明的循环流化床部分气化装置以及循环流化床部分气化方法能够在温和反应条件下生产高附加值煤气及半焦产品,可以有效降低煤气中的焦油含量,并且能够简化系统工艺,降低运行成本。
另外,在本发明中,第二气化剂通入返料器的反应室,反应室内只有循环半焦及从进料室进入反应室的少量的流化风,几乎没有有效气,从而避免了第二气化剂对有效气,尤其是ch4的消耗,在保证送入炉膛输送区的热量的同时,有效提高最终煤气的热值。
附图说明
图1为根据本发明的实施例一的循环流化床部分气化装置的示意图;
图2为根据本发明的实施例二的循环流化床部分气化装置的示意图;以及
图3为根据本发明的实施例三的循环流化床部分气化装置的示意图。
具体实施方式
下面结合附图详细描述本发明的示例性的实施例,其中相同或相似的标号表示相同或相似的元件。另外,在下面的详细描述中,为便于解释,阐述了许多具体的细节以提供对本披露实施例的全面理解。然而明显地,一个或多个实施例在没有这些具体细节的情况下也可以被实施。在其他情况下,公知的结构和装置以图示的方式体现以简化附图。
在催化重整脱除法中,将半焦作为催化剂的优势明显,其原料来源广泛,价格低廉,且失活后直接进入气化炉气化不用考虑活化和再生,越来越受到关注。有利地,采用两段床气化技术对燃料进行部分气化,将部分气化过程中产生的半焦作为催化剂,或进一步添加催化剂,对部分气化过程中产生的焦油进行催化重整,以降低煤气中焦油含量。然而,半焦作为催化剂的部分气化技术的成功应用较难,关键在于焦油脱除不理想,煤气中焦油含量过高,工艺复杂,需要额外添加催化剂,增加运行成本。
根据本发明的总体构思,提供了一种循环流化床部分气化装置,所述循环流化床部分气化装置包括气化炉炉膛、气固分离器和返料器,其中,气化炉炉膛与气固分离器相连通,气固分离器与返料器相连通,返料器与气化炉炉膛相连通,所述气化炉炉膛上设有燃料入口、第一气化剂入口、炉膛顶部出口、固体产品出口和返料口,所述气固分离器设置有气体产品出口,所述气化炉炉膛具有变径结构。
实施例一
图1为根据本发明的实施例一的循环流化床部分气化装置的示意图。如图1所示,循环流化床部分气化装置包括依次相连的气化炉炉膛1、气固分离装置2、立管3和返料器4。气化炉炉膛1具有燃料入口、第一气化剂入口、炉膛顶部出口、固体产品出口和返料口。在图1的实施例中,燃料入口设置在气化炉炉膛1的中下部,用于向气化炉炉膛1内供应燃料a,第一气化剂入口设置在气化炉炉膛1的侧部,用于向气化炉炉膛1内供应第一气化剂b,炉膛顶部出口设置在气化炉炉膛1的上部,固体产品出口可以设置在气化炉炉膛1底部。气固分离装置2可以是常规形式的分离装置,包括入口、气体产品出口和循环物料出口,气固分离装置2的入口与气化炉炉膛1的炉膛顶部出口连通,气体产品出口用于排出经气固分离装置2分离的气体产品,循环物料出口通常位于气固分离装置2的底部,用于排出经气固分离装置2分离的循环物料,该循环物料出口与返料器4的入口通过立管3相连通,也即立管3设置在气固分离器2和返料器4之间。返料器4的出口与气化炉炉膛1的返料口相连通。
根据本发明的发明构思,所述气化炉炉膛(1)具有变径结构。具体地,所述气化炉炉膛(1)自下而上分为鼓泡区(11)和输送区(12),并且鼓泡区(11)的最大炉膛横截面积大于输送区(12)的最大炉膛横截面积。在图1的实施例中,鼓泡区(11)和输送区(12)均为大致圆筒状,并且在鼓泡区(11)和输送区(12)存在过渡区,鼓泡区11的最大炉膛横截面积在过渡区逐渐过渡到输送区12的最大炉膛横截面积,鼓泡区11的最大炉膛横截面积a1是输送区12的最大炉膛横截面积a2的1.4倍,即a1=1.4a2。
根据具体应用,鼓泡区(11)的最大炉膛横截面积可以是输送区(12)的最大炉膛横截面积的1.2-4倍,优选地,鼓泡区(11)的最大炉膛横截面积是输送区(12)的最大炉膛横截面积的1.4-1.6倍。
进一步地,所述返料器4被配置为使得从气固分离器2分离的循环物料能够在返料器4内发生反应。具体地,所述返料器4包括第二气化剂入口,用于向返料器4内供应第二气化剂s。第二气化剂入口优选地设置在返料器4的底部。进一步地,所述返料器4包括第二气化剂布风装置45,所述第二气化剂入口设置在第二气化剂布风装置45上。通过为返料器4设置第二气化剂入口、第二气化剂布风装置45,可以向返料器4内供应第二气化剂,这样从气固分离器2分离的循环物料能够与第二气化剂在返料器4内发生反应,并且由于从气固分离器2分离的循环物料为碳含量相对较低的循环半焦,其软化温度较高,因此结焦温度较高,由此可以使返料器4内的反应在较高温度下进行,解决了炉膛底部温度受限导致气化性能低的问题。
根据本发明的发明构思,在炉膛鼓泡区,燃料与第一气化剂在较低的气化剂氧当量比(气化剂中氧气量与燃料完全燃烧所需氧气量的比值)和反应温度条件下发生部分气化反应,生成大量半焦和含有焦油气的煤气,由于鼓泡区流化速度较低,较大颗粒的气化半焦不会被携带到炉膛上部,而是作为产品半焦从炉膛底部的固体产品出口(粗焦排渣口)排出;含有焦油气的煤气携带小颗粒半焦上升进入炉膛输送区;同时,1200℃-1300℃的高温气体及大量高温固体从返料器进入输送区,由于高温固体粒径小,在输送区的横截面积缩小的情况下,输送区的流化速度高,因此绝大部分高温固体直接被携带向上运动,在此过程中,一方面,高温气体及大量高温固体带入炉膛的热量使炉膛温度升高,使煤气中的焦油裂解,另一方面,来自鼓泡区的小颗粒半焦和来自返料器的半焦作为催化剂,对焦油进行催化重整,从而有效地降低了最终煤气中的焦油含量。
因此,本发明的循环流化床部分气化装置能够在温和反应条件下生产高附加值煤气及半焦产品,可以有效降低煤气中的焦油含量,并且能够简化系统工艺,降低运行成本。
在图1所示的实施例中,返料器4包括进料室41、反应室42和返料管43,进料室41的入口与立管3的出口相连通,进料室41和反应室42的下端彼此连通,返料管43的入口和反应室42的出口相连通,返料管43的出口与气化炉炉膛1的返料口相连通。在进料室41的下方设置有流化风布风装置44,并且在该流化风布风装置44上设置有流化风入口,与流化风风管连通,用于向进料室41内供应流化风l。所述第二气化剂布风装置45设置在反应室42的下方,在该第二气化剂布风装置上设置有所述第二气化剂入口,与第二气化剂管连通。
有利地,所述反应室42的与水平面平行的截面的横截面积大于或等于所述进料室41的与水平面平行的截面的横截面积,例如,反应室42的横截面积af是进料室41的横截面积aj的1.21倍。
其中,气化炉炉膛(1)的返料口位于输送区(12),并且燃料入口和第一气化剂入口位于鼓泡区(11),而所述固体产品出口设置在鼓泡区(11)上。
图1的循环流化床部分气化装置对应的循环流化床部分气化方法包括如下步骤:
a)将燃料a与第一气化剂b通入气化炉炉膛1,发生部分气化反应,反应生成的部分固体产品从固体产品出口离开循环流化床炉膛(1),反应生成的气体携带部分固体物料进入气固分离装置(2),分离后的气体产品(g)离开循环流化床;
b)使从气固分离器2分离的循环物料通入返料器4,并在返料器4内发生反应;
c)将返料器4内生成的产物返回气化炉炉膛1。
具体地,步骤b)包括:将第二气化剂s通入返料器4,与被气固分离装置2分离并进入返料器4的循环物料发生反应。这里,所述返料器被配置为可供通入的第二气化剂与循环物料发生氧化-还原反应,生成高温气体及高温固体,并将反应生成的高温气体及高温固体送入所述气化炉炉膛,同时,保证立管3、返料器4中的气固两相流向气化炉炉膛1方向流动,阻止气化炉炉膛1内气体反向进入气固分离装置2,破坏物料循环。因此,燃料与第一气化剂被通入气化炉炉膛的鼓泡区,发生部分气化反应,反应生成的较大粒径固体物料从炉膛底部的固体产品出口(粗焦排渣口)排出;反应生成的气体携带较小粒径的固体物料上升进入输送区,与来自返料器的高温气体及高温固体接触,发生反应后,生成的含有半焦的气固混合物进入气固分离装置进行分离,分离后的气体离开循环流化床。
下面以一个具体示例为例描述根据实施例一的循环流化床部分气化装置和循环流化床部分气化方法的运行过程。在运行时,粒径为0~8mm、含灰量为7%、所含灰在弱还原性气氛状态下的软化温度为1350℃的燃料a和第一气化剂b通入气化炉炉膛1的鼓泡区11,发生气化反应;其中,第一气化剂b为空气,第一气化剂b中所含氧量与给入气化炉炉膛的燃料a完全燃烧所需的氧量的比值为0.12。燃料a和第一气化剂b在800℃的反应温度下发生部分气化反应,反应生成的大颗粒气化半焦f从炉膛底部的粗焦排渣口排出,生成的气体携带较小粒径的含有半焦的固体物料上升进入输送区12。第二气化剂s通过第二气化剂布风装置45进入反应室42,与被气固分离装置2分离后作为循环半焦进入返料器4的半焦固体物料发生氧化-还原反应,反应温度为1200-1300℃,生成高温气体及高温固体,并通过返料管43将所生成高温气体及高温固体送回气化炉炉膛1。
需要说明的是,高温气体及高温固体进入输送区12后,由于高温固体粒径小,输送区12的流化速度高,因此绝大部分高温固体直接被气体携带向上运动,在此过程中与来自鼓泡区11的气体和较小粒径的固体物料发生反应,最终生成的气固混合物进入气固分离装置2进行分离,分离后的气体g离开循环流化床。并且,进入反应室42的循环半焦的含灰量较低(灰质量浓度约为35%),可以实现在较高的反应温度下不结焦。通过调整第二气化剂s的富氧浓度和水蒸汽量,控制反应室42内温度为1200℃-1300℃,流化速度为0.6-1m/s,且第二气化剂s中氧气占第一气化剂和第二气化剂中所含氧气总量的10%-15%。
其中,所述反应室42的与水平面平行的截面的横截面积大于或等于所述进料室41的与水平面平行的截面的横截面积,且所述反应室的横截面积与反应室内设定的流化速度、反应室内温度及第二气化剂的气体组成相关:在设定的反应室内流化速度条件和第二气化剂气体组成一定的条件下,反应室内所需温度越高,反应室的横截面积越大;在设定的反应室内流化速度条件和反应室内所需温度一定的条件下,第二气化剂中富氧浓度(富氧浓度=标况下氧气体积/(标况下氧气体积 标况下氮气体积))越小、水蒸气给入量越大,则反应室的横截面积越大。
在其它示例中,反应室42内的流化速度可以为0.4~2.5m/s。优选地,反应室42内的流化速度为0.4~1m/s。根据本发明的一个优选实施例,控制反应室42内的温度高于气化炉炉膛1内的返料口以下的最高温度,并比燃料中灰在弱还原性气氛状态下的软化温度低50-150℃。
在其它示例中,第一气化剂(b)中所含氧量与给入气化炉炉膛(1)的燃料完全燃烧所需的氧量的比值为0.08-0.3。所述第二气化剂为氧气或空气,或上述二者的混合物,或上述二者中的至少一者与水蒸气的混合物。
有利地,鼓泡区(11)的流化速度为1m/s-2.5m/s,并且输送区(12)的流化速度大于2.5m/s;鼓泡区(11)的温度为500-900℃,并且输送区(12)的温度850-1300℃。
取决于具体情况,第二气化剂中的氧气可以占第一气化剂和第二气化剂中所含氧气总量的5%-25%,优选地为10%-15%。
在其它示例中,所述喉口段(13)的最小横截面积与输送区(12)的最大横截面积的比值可以为0.7-0.95。
实施例二
图2为根据本发明的实施例二的循环流化床部分气化装置的示意图。
与实施例一的不同之处在于:
所述鼓泡区(11)具有变径结构,并且鼓泡区(11)的下部的横截面积小于鼓泡区(11)的中部的横截面积,从而保证在第一气化剂为纯氧或富氧时,鼓泡区11的流化速度基本一致;
在鼓泡区11和输送区12之间设置有喉口段13,喉口段的最小横截面积a3与输送区12最大横截面积a2的比值为0.9,并且气化炉炉膛的返料口位于输送区,从而使得由返料口返回的小颗粒固体物料在喉口处的结构约束和高流化速度作用下,更多地向气化炉炉膛1的输送区12运动,减少了向炉膛下部的返混,提高了小颗粒固体物料在喉口段13以上高温循环回路内的浓度,增强对焦油的催化效果;
除在反应室42下方设置有第二气化剂布风装置45,供第二气化剂s通入外,在返料管43上还设置有附加第二气化剂布风装置46,在该附加第二气化剂布风装置上设置有附加第二气化剂入口,与附加第二气化剂管连通,用于向返料管43内供应附加第二气化剂s1。
优选地,所述附加第二气化剂布风装置46设置在返料管43的底部。
相应地,在本实施例中,所述循环流化床部分气化方法还包括:向返料器(4)的返料管(43)内供应附加第二气化剂(s1)。
下面以一个具体示例为例描述根据实施例二的循环流化床部分气化装置和循环流化床部分气化方法的运行过程。在运行时,第一气化剂b为富氧,第一气化剂b中所含氧量与给入气化炉炉膛的燃料a完全燃烧所需的氧量的比值为0.1。燃料a和第一气化剂b在850℃的反应温度下发生部分气化反应,反应生成的大颗粒气化半焦f从炉膛底部的粗焦排渣口排出,生成的气体携带较小粒径的含有半焦的固体物料上升进入输送区12。第二气化剂s通过第二气化剂布风装置45进入反应室42,与被气固分离装置2分离后进入返料器4的半焦发生氧化-还原反应,反应温度1250℃,生成的高温气体及高温固体通过返料管43返回输送区12。其中,返料器4内生成的高温气固混合物进入返料管43后,受重力的影响,返料管43底部形成高温固体料层,气体位于返料管43上部,附加第二气化剂s1从底部进入返料管后,先与高温固体接触,发生反应,有利于进一步提高返回炉膛的气固混合物的温度。
需要说明的是,高温气体及高温固体进入输送区12后,由于高温固体粒径小,输送区12的流化速度高,因此绝大部分高温固体直接被气体携带向上运动,在此过程中与来自鼓泡区11的气体和较小粒径的固体物料发生反应,最终生成的气固混合物进入气固分离装置2进行分离,分离后的气体g离开循环流化床。并且,进入反应室42的循环半焦的含灰量较低(灰质量浓度约为30%),可以实在较高的反应温度下不结焦。通过调整第二气化剂s的富氧浓度和水蒸汽量,控制反应室42内温度为1200℃-1300℃,流化速度约为0.4-0.9m/s,且第二气化剂s和附加第二气化剂s1的总氧气量占第一气化剂和第二气化剂中所含氧气总量的15%-25%。
根据本发明的一个优选实施例,进入返料器4的反应室42的第二气化剂与进入返料器4的返料管43的附加第二气化剂的组成不同,从而在保证反应室流化速度的条件下,提高返回气化炉炉膛的循环物料的温度。
实施例三
图3为根据本发明的实施例三的循环流化床部分气化装置的示意图。
与实施例一的不同之处在于:
在鼓泡区11和输送区12之间设置有喉口段13,并且在喉口段13设置配风口,用于供应配风(b1),配风b1的为含氧气体,可以与装置内其他用于气化的气体(例如第一气化剂、第二气化剂)的成分相同。配风b1可以从配风口进入气化炉炉膛1,一方面,这进一步提高了喉口段13的流化速度,使得由返料口返回的小颗粒固体物料在喉口处更多地向气化炉炉膛1的输送区12运动,减少向炉膛下部的返混,提高了小颗粒固体物料在喉口以上高温循环回路内的浓度,增强对焦油的催化效果;另一方面,有利于提高气化炉炉膛1的输送区12的温度,从而促进对焦油的裂解。
在所述返料器(4)上设置有次级固体产品出口(细焦排渣口),用于排出次级固体产品。在高循环量的情况下,可以从通过细焦排渣口排出部分小颗粒的次级固体产品(半焦)f1,以增加系统半焦产量。
相应地,在本实施例中,所述循环流化床部分气化方法还包括:使配风(b1)从配风口进入气化炉炉膛(1),和/或,通过返料器(4)上的次级固体产品出口排出次级固体产品(f1)。
此外,所述返料器(4)可以包括附加燃料入口,用于向返料器(4)内供应附加燃料,所述附加燃料入口设置在反应室上;并且,所述反应室(42)还可以设置有气体出口,所述气体出口与气化炉炉膛(1)的上部相连通。进一步地,所述循环流化床部分气化装置还可以设置有二级回料阀,设置在气化炉炉膛(1)和返料管(43)之间,所述二级回料阀的进口与返料管(43)的出口连通,所述二级回料阀的出口与气化炉炉膛(1)连通。
由此,所述循环流化床部分气化方法还包括:向返料器(4)供应附加燃料。并且,步骤c)中将返料器4内生成的产物返回气化炉炉膛1可以包括:将返料器4内生成的部分气体产物通过平衡管h返回气化炉炉膛1的上部;以及将返料器4内生成的其它产物通过返料管43返回气化炉炉膛1。
在运行时,第二气化剂s(氧气和水蒸气混合气体)与循环半焦在反应室42内发生气化反应,因此,从返料器4离开的气体量大于进入返料器4的总气体量。在反应室42上设置与气化炉炉膛上部连通的气体出口,一方面,可以减少通过返料管43离开返料器4的气体量,减小返料管43的直径;另一方面,反应室42内生成的高温气体进入气化炉炉膛上部,作为热源,直接提高气化炉炉膛上部温度,促进气化炉炉膛上部气化反应的进行。
所述二级回料阀用来调节系统压力平衡,确保来自于返料管43的气固两相流向气化炉炉膛方向流动,阻止气化炉炉膛1内气体反向进入返料器4。
根据本发明的循环流化床部分气化装置以及循环流化床部分气化方法,在炉膛鼓泡区,燃料与第一气化剂在较低的气化剂氧当量比(气化剂中氧气量与燃料完全燃烧所需氧气量的比值)和反应温度条件下发生部分气化反应,生成大量半焦和含有焦油气的煤气,由于鼓泡区流化速度较低,较大颗粒的气化半焦不会被携带到炉膛上部,而是作为产品半焦从炉膛底部的固体产品出口(粗焦排渣口)排出;含有焦油气的煤气携带小颗粒半焦上升进入炉膛输送区;同时,1200℃-1300℃的高温气体及大量高温固体从返料器进入输送区,由于高温固体粒径小,在输送区的横截面积缩小的情况下,输送区的流化速度高,因此绝大部分高温固体直接被携带向上运动,在此过程中,一方面,高温气体及大量高温固体带入炉膛的热量使炉膛温度升高,使煤气中的焦油裂解,另一方面,来自鼓泡区的小颗粒半焦和来自返料器的半焦作为催化剂,对焦油进行催化重整,从而有效地降低了最终煤气中的焦油含量。
因此,本发明的循环流化床部分气化装置以及循环流化床部分气化方法能够在温和反应条件下生产高附加值煤气及半焦产品,可以有效降低煤气中的焦油含量,并且能够简化系统工艺,降低运行成本。
另外,在本发明中,第二气化剂通入返料器的反应室,反应室内只有循环半焦及从进料室进入反应室的少量的流化风,几乎没有有效气,从而避免了第二气化剂对有效气,尤其是ch4的消耗,在保证送入炉膛输送区的热量的同时,有效提高最终煤气的热值。
本发明还具有如下有益效果:
1)可实现产品气中焦油含量低于50mg/nm3。
2)不需要添加额外催化剂,运行成本低。
3)煤气中ch4含量高,从而有效提高产品煤气热值。
4)炉膛下部反应温度低,提高产品半焦的产率。
5)反应过程在一个反应器中完成,系统结构简单。
本发明也适用于其他含碳固体燃料的部分气化。
尽管已经示出和描述了本发明的实施例,对于本领域的普通技术人员而言,可以理解在不脱离本发明的原理和精神的情况下可以对这些实施例进行变化。本发明的适用范围由所附权利要求及其等同物限定。
附图标记列表:
1气化炉炉膛
2气固分离装置
3立管
4返料器
41进料室
42反应室
43返料管
44流化风布风装置
45第二气化剂布风装置
46附加第二气化剂布风装置
11鼓泡区
12输送区
13喉口段
a燃料
b第一气化剂
f固体产品
g气体产品
s第二气化剂
l流化风
s1附加第二气化剂
b1配风
f1次级固体产品
本文用于企业家、创业者技术爱好者查询,结果仅供参考。