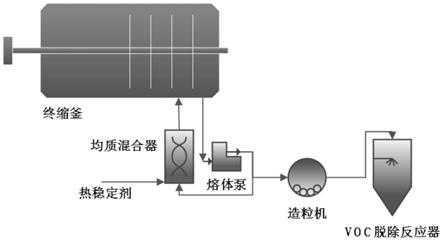
1.本发明涉及聚酯领域,具体涉及一种低乙醛瓶坯聚酯的生产方法及装置。
背景技术:
2.聚对苯二甲酸乙二醇酯(pet)是一种半结晶热塑性聚酯,它广泛的用来制造纤维、薄膜、片材以及食品托盘和饮料容器。用于生产饮料容器类聚合物一般通过公知的现有技术连续熔融聚合、固相增粘反应制造的,然后通过注塑过程将该聚合物粒子制备成瓶坯,瓶坯再经过吹拉成型获得饮料容器。熔融聚合制造的基础粒子中一般含有大于60μg/g聚合的乙醛,经过固相聚合过程聚合物中乙醛(aa)含量降至1.0μg/g以下。聚酯粒子经过螺杆塑化,熔体中的乙醛前驱体(如端乙烯基)在热和氧的作用下生成新的aa,并与原粒子中游离的aa一起残留在瓶坯中,瓶坯中aa提高到(5-10)μg/g。乙醛的存在从味觉的观点看是有害的,特别是对于敏感的饮料如可乐、啤酒和水,特别希望乙醛含量尽可能低。
3.目前,降低聚酯瓶坯中乙醛含量的方法有:1)添加乙醛稳定剂,通过添加稳定剂提高聚酯热稳定性能。美国专利5.874.517中描述了在熔融聚合过程中,添加抗氧剂-1010及p-epq降低乙醛含量,制得的pet乙醛含量至少减少25%。间日春向pet中添加适量改性剂,降低因热降解反应引起的乙醛量,瓶坯乙醛含量至少可降低30%。道公司生产的超低乙醛含量的pet通过添加一定量的乙醛清除剂稳定剂,将生成的乙醛除去,并添加一定量的调色剂改善色相。2)改进后加工工序,青木大一等人描述一种可降低容器乙醛渗出量的方法,增加降低乙醛工序,即通过短时间高温加热制品,降低制品的渗出量。
4.现有专利主要通过在反应初期或者螺杆里添加微量的热稳定剂、抗氧剂及乙醛清除剂来提高聚酯热稳定性、降低热氧降解及吸收加工过程中产生的乙醛来实现的,在生产及加工过程中聚酯催化剂仍在一定程度上起到催化降解反应的作用,瓶坯中乙醛含量仍在5μg/g以上。在螺杆中加入乙醛清除剂可以降低瓶坯中乙醛含量,但乙醛清除剂会使聚酯品质变差。因此,从聚酯催化剂失活角度,开发一种新的生产方法,可以更有效的降低瓶坯中乙醛含量。
技术实现要素:
5.本发明是针对上述存在的技术问题提供一种低乙醛瓶坯聚酯的生产方法及装置。
6.本发明的目的可以通过以下技术方案实现:
7.一种低乙醛瓶坯聚酯的生产方法,该方法是以对苯二甲酸、乙二醇为原料,添加二元酸或二元醇类物质作为改性单体,钛、锑或锗系金属化合物作为聚合催化剂,在终缩釜中进行反应制备得到聚酯熔体;将与终缩釜相连的熔体泵出口熔体分流,其中一部分输送至均质混合器中与稳定剂混合,将混合后的熔体再输送至终缩釜并与终缩釜中的熔体混合均匀,另一部分直接输送至造粒机中进行造粒,得到球形结晶颗粒,所述的球形结晶颗粒送入voc脱除反应器进行反应得到聚酯粒子,将聚酯粒子经干燥后,在注塑机上注塑成瓶坯。
8.本发明技术方案中:所述改性单体为间苯二甲酸、新戊二醇和2-甲基-1,3-丙二醇
等中的一种或几种。
9.本发明技术方案中:在均质混合器中稳定剂的浓度为50-500μg/g,所述的稳定剂为磷酸、磷酸三甲酯、磷酸三乙酯、磷酸三苯酯、磷酰基乙酸三乙酯和磷酸二苯基异辛酯中的一种或几种。
10.本发明技术方案中:熔体泵出口熔体进行分流,5%~30%的熔体输送至均质混合器中,剩余部分熔体输送至造粒机中进行造粒。
11.本发明技术方案中:造粒后结晶粒子结晶度为36~45%。
12.一种用实现上述的低乙醛瓶坯聚酯的生产方法的装置,该装置包括终缩釜,均质混合器以及voc脱除反应器,所述终缩釜尾部的出料端通过熔体泵相连,熔体泵的一个输出端通过均质混合器与终缩釜相连,另一个输出端通过造粒机与voc脱除反应器,所述的voc脱除反应器与注塑机相连。
13.上述装置中:所述的终缩釜为横向设置,左侧为其头部,右侧为其尾部,所述的均质混合器与终缩釜相连的位置位于终缩釜尾部出料端的左端。
14.上述装置中:终缩釜尾部出料口的出口与终缩釜的横截面积的比为1:10~1:15。
15.上述装置中:在voc脱除反应器中进行反应的条件为:脱醛温度140-180℃,停留时间15~36小时。
16.上述装置中:聚酯粒子特性粘度为(0.75-0.87)dl/g,aa值小于0.5μg/g;聚酯熔体的特性粘度为(0.75-0.85)dl/g。
17.本发明的有益效果:
18.本发明制备工艺简单,容易工业化应用,且制备得到的低乙醛瓶坯中乙醛含量低于3μg/g。
附图说明
19.图1为本发明生产工艺的示意图。
具体实施方式
20.下面结合实施例对本发明做进一步说明,但本发明的保护范围不限于此:
21.如图1,一种低乙醛瓶坯聚酯的生产装置,该装置包括终缩釜,均质混合器以及voc脱除反应器,所述终缩釜尾部的出料端通过熔体泵相连,熔体泵的一个输出端通过均质混合器与终缩釜相连,另一个输出端通过造粒机与voc脱除反应器。其中:均质混合器与终缩釜相连的位置位于缩釜尾部出料端的左端,所述的voc脱除反应器与注塑机相连。终缩釜尾部出料口的出口与终缩釜的横截面积的比为1:10(实施例1),1:12(实施例2),1:14(实施例3),1:15(实施例4)。
22.对比例
23.在万吨瓶用聚酯生产线上,以对苯二甲酸、乙二醇为主原料添加第三单体:间苯二甲酸,打浆釜内同时添加聚合催化剂、醚抑制剂;由第二酯化釜添加热稳定剂浓磷酸(p含量聚酯总重15μg/g),通过熔融聚合的方法制备瓶级基础切片,特性粘度0.630dl/g。瓶级基础切片经过预结晶、结晶工序,然后在210℃温度下,将粘度提高到预定粘度,然后冷却、输送至料仓。最终获得瓶用聚酯切片特性粘度为0.800dl/g,
△
b:-1.0,端羧基:28mol/t,二甘
醇:1.2%,乙醛:0.70μg/g。
24.实施例1
25.在万吨瓶用聚酯生产线上,以对苯二甲酸、乙二醇为原料,添加第三单体:间苯二甲酸,打浆釜内同时添加聚合催化剂、醚抑制剂,采用现有酯化、聚合工艺制备高粘熔体,当聚酯熔体粘度达到0.75dl/g时,经熔体泵将熔体输出,在熔体泵出口分流10%熔体通过均质混合器与乙二醇磷稳定剂(p含量占终聚釜聚酯总重50μg/g)混合,将混合后熔体再输送到终缩反应釜,从底部进入与终缩釜中熔体混合。其余90%熔体进入水下造粒机,获得高粘聚酯颗粒,将该聚酯颗粒经管道送至voc脱除反应器中,反应器物料温度140℃,停留时间36小时,然后冷却、输送至料仓。最终获得瓶用聚酯切片:特性粘度为0.751dl/g,
△
b:-2.0,端羧基:25mol/t,二甘醇:1.2%,乙醛:0.50μg/g。
26.实施例2
27.在万吨瓶用聚酯生产线上,以对苯二甲酸、乙二醇为原料,添加第三单体:新戊二醇,打浆釜内同时添加聚合催化剂、醚抑制剂,采用现有酯化、聚合工艺制备高粘熔体,当聚酯熔体粘度达到0.85dl/g时,经熔体泵将熔体输出,在熔体泵出口分流30%熔体通过均质混合器与磷酸稳定剂(p含量占终聚釜聚酯总重500μg/g)混合,将混合后熔体再输送到终缩反应釜,从底部进入与终缩釜中熔体混合。其余70%熔体进入水下造粒机,获得高粘聚酯颗粒,将该聚酯颗粒经管道送至脱醛反应器中,反应器物料温度180℃,停留时间15小时,然后冷却、输送至料仓。最终获得瓶用聚酯切片:特性粘度为0.87dl/g,
△
b:-1.8,端羧基:25mol/t,二甘醇:1.1%,乙醛:0.51μg/g。
28.实施例3
29.在万吨瓶用聚酯生产线上,以对苯二甲酸、乙二醇为原料,添加第三单体:2-甲基1,3丙二醇,打浆釜内同时添加聚合催化剂、醚抑制剂。采用现有酯化、聚合工艺制备高粘熔体,当聚酯熔体粘度达到0.80dl/g时,经熔体泵将熔体输出,在熔体泵出口分流5%熔体通过均质混合器与磷酸稳定剂(p含量占终聚釜聚酯总重300μg/g)混合,将混合后熔体再输送到终缩反应釜,从底部进入与终缩釜中熔体混合。其余95%熔体进入水下造粒机,获得高粘聚酯颗粒,将该聚酯颗粒经管道送至voc脱除反应器中,反应器物料温度170℃,停留时间24小时,然后冷却、输送至料仓。最终获得瓶用聚酯切片:特性粘度为0.801dl/g,
△
b:-2.2,端羧基:26mol/t,二甘醇:1.1%,乙醛:0.48μg/g。
30.实施例4
31.在万吨瓶用聚酯生产线上,以对苯二甲酸、乙二醇为原料,添加第三单体:环己烷二甲醇,打浆釜内同时添加聚合催化剂、醚抑制剂。采用现有酯化、聚合工艺制备高粘熔体,当聚酯熔体粘度达到0.82dl/g时,经熔体泵将熔体输出,在熔体泵出口分流10%熔体通过均质混合器与磷酸稳定剂(p含量占终聚釜聚酯总重400μg/g)混合,将混合后熔体再输送到终缩反应釜,从底部进入与终缩釜中熔体混合。其余90%熔体进入水下造粒机,获得高粘聚酯颗粒,将该聚酯颗粒经管道送至voc脱除反应器中,反应器物料温度160℃,停留时间30小时,然后冷却、输送至料仓。最终获得瓶用聚酯切片:特性粘度为0.82dl/g,
△
b:-2.0,端羧基:25mol/t,二甘醇:1.0%,乙醛:0.4μg/g。
32.由上述方法制备的瓶级聚酯,经过干燥后,在注塑机上制成32g聚酯瓶坯,参照瓶级聚酯中乙醛测试标准(gb17931-2003),测试瓶坯中乙醛含量。试验结果如下表:
33.
再多了解一些
本文用于企业家、创业者技术爱好者查询,结果仅供参考。