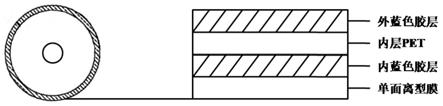
1.本发明属于胶带领域,具体涉及一种锂电池铝壳用保护胶带及其制备方法。
背景技术:
2.随着市场信息化电子化时代的到来,小型化移动电子设备终端逐渐在人们生活中随处可寻并且变得不可缺少;锂离子电池以其轻巧的外形、相对其他类型电池较高的电压、长时间的使用寿命以及无记忆等优良性能,为电子设备提供持久的电力,人们使用的更方便,更长久;而胶带是生活中常见的材料也是现代工业生产中的重要材料,应用十分广泛,其被大量应用于锂离子聚合物电池外部,起到绝缘和固定的作用。且为避免保护板及上面器件锋利的边角挫伤电池及确保电池在放入电子设备中不发生漏电现象,保证消费者使用电子产品的安全性,需要将电池除去对外连接的正、负极耳部分之外的电池边缘、保护板周围都要包裹上绝缘胶带。
3.现有技术如公开号cn110396374a公开了一种锂电池壳保护胶带及其制备方法和使用方法;该锂电池保护胶带包含pet基材层、粘合剂层和硅离型纸层,按重量份计,粘合剂层的制备原料包含30~80份的丙烯酸树脂组合物、5~45份的环氧树脂组合物和30~100份的溶剂;制得的锂电池壳保护胶带对锂电池铝壳的剪切强度高、粘结强度好,抗反弹性好,与设备匹配度好;但目前研究的丙烯酸酯树脂胶带的耐磨性、耐高温性、耐酸碱、耐腐蚀、绝缘阻燃等性能尚有待提高。
技术实现要素:
4.本发明的目的在于提供一种具有优良的耐高温、耐酸碱腐蚀性、绝缘阻燃性以及耐电解液的锂电池铝壳用保护胶带,将其应用于新能源动力电池方形铝壳的包覆,其复合结构对电池铝壳表面有很好的保护作用。
5.本发明为实现上述目的所采取的技术方案为:
6.一种保护胶带,包括:单面离型膜、内蓝色胶层、内层pet、外蓝色胶层;内层pet为基材;内层pet的一侧设有内蓝色胶层;内蓝色胶层一侧设有单面离型膜;内层pet的另一侧设有外蓝色胶层。
7.进一步地,在本发明的一些实施例中,单面离型膜的厚度为20~30μm;内蓝色胶层的厚度为15
‑
25μm;内层pet的厚度为20
‑
30μm;外蓝色胶层的厚度为25
‑
35μm。
8.进一步地,在本发明的一些实施例中,蓝色胶层的成分组成为:聚丙烯酸树脂75
‑
85%,耐高温促进剂2
‑
3%,色母0.5
‑
2%,氢氧化铝粉10
‑
25%,硬化剂1.5
‑
3%。
9.进一步地,在本发明的一些实施例中,蓝色胶层的成分组成为:聚丙烯酸树脂80
‑
85%,耐高温促进剂2
‑
3%,色母0.5
‑
1%,氢氧化铝粉10
‑
20%,硬化剂1.5
‑
2%。
10.本发明采用聚丙烯酸树脂、耐高温促进剂、色母、氢氧化铝粉、硬化剂作为蓝色胶层的组成成分,并将其涂布在pet基材的两侧,再在内蓝色胶层一侧贴合单面离型膜制得保护胶带;该保护胶带具有优良的耐高温、耐酸碱、耐腐蚀、绝缘阻燃性能;将其应用于新能源
动力电池方形铝壳的包覆,其复合结构对电池铝壳表面有很好的保护作用,对锂电池铝壳具有较高的剥离强度与持粘力,包覆性能好,即具有优良的粘结力,进而达到保护电池铝壳的效果,以提高电池的使用寿命。
11.本发明还公开了一种保护胶带在电池铝壳中的用途。
12.本发明还公开了一种锂电池铝壳用保护胶带的制备方法,包括以下步骤:
13.(1)制备蓝色胶层用混合物:将聚丙烯酸树脂、耐高温促进剂、色母、氢氧化铝粉、硬化剂和溶剂在反应釜中混合搅拌均匀,得到蓝色胶层用混合物;
14.(2)制备保护胶带:将蓝色胶层用混合物采用旋涂法涂布在内层pet的一侧,烘干,得到外蓝色胶层;将蓝色胶层用混合物采用旋涂法涂布在内层pet的另一侧,烘干,得到内蓝色胶层;在内蓝色胶层的一侧贴合单面离型膜,收卷,熟化,得到锂电池铝壳用保护胶带。
15.进一步地,在本发明的一些实施例中,离型膜层在贴合面涂布理性膜硅油,硅油转移率为1.5
‑
3.5%。
16.进一步地,在本发明的一些实施例中,蓝色胶层的成分组成中聚丙烯酸树脂为改性聚丙烯酸树脂;改性聚丙烯酸由改性环氧树脂改性聚丙酸树脂。
17.进一步地,在本发明的一些实施例中,改性环氧树脂由3
‑
乙氧基
‑
异草酸改性环氧树脂。
18.本发明采用3
‑
乙氧基
‑
异草酸改性环氧树脂,将改性环氧树脂改性聚丙烯酸树脂,再将其与聚丙烯酸树脂结合制得改性聚丙烯酸树脂,将该改性聚丙烯酸树脂用于蓝色胶层的成分,制得保护胶带,其进一步提高了保护胶带的剥离强度与持粘力,使其具有更高的粘结力;同时使保护胶带具有优良的阻燃性、耐电解液与耐磨性能。
19.进一步地,在本发明的一些实施例中,改性聚丙烯酸树脂的制备方法为:将聚丙烯酸树脂与环氧树脂溶于溶剂中,搅拌均匀,加热,加入催化剂进行反应,得到改性聚丙烯酸树脂。
20.进一步地,在本发明的一些实施例中,改性环氧树脂的制备方法为:将环氧树脂与3
‑
乙氧基
‑
异草酸置于容器中,加入催化剂反应1.5
‑
2.5h,得到改性环氧树脂。
21.更进一步地,在本发明的一些实施例中,催化剂为伯胺、叔胺、醇胺中一种。
22.本发明由于采用聚丙烯酸树脂、耐高温促进剂、色母、氢氧化铝粉、硬化剂作为蓝色胶层的组成成分,并将其涂布在pet基材的两侧,再在内蓝色胶层一侧贴合单面离型膜制得保护胶带,因而具有如下有益效果:该保护胶带具有优良的耐高温、耐酸碱腐蚀性、绝缘阻燃性能;将其应用于新能源动力电池方形铝壳的包覆,其复合结构对电池铝壳表面有很好的保护作用,对锂电池铝壳具有较高的剥离强度与持粘力,包覆性能好,即具有优良的粘结力,进而达到保护电池铝壳的效果,以提高电池的使用寿命。因此,本发明是一种具有优良的耐高温、耐酸碱、耐腐蚀、绝缘阻燃性以及耐电解液的锂电池铝壳用保护胶带,将其应用于新能源动力电池方形铝壳的包覆,其复合结构对电池铝壳表面有很好的保护作用。
附图说明
23.图1为锂电池铝壳用保护胶带的结构示意图;
24.图2为环氧树脂、改性环氧树脂和实施例5中改性聚丙烯酸树脂的红外光谱图;
25.图3为保护胶带的自熄时间;
26.图4为保护胶带的质量损失。
具体实施方式
27.进一步地,为了更好地说明本发明的技术方案,以下结合具体实施方式和附图对本发明的技术方案作进一步详细描述;但应当理解的是,这些实施例是在以本发明技术方案为前提下进行实施,给出了详细的实施方式和具体的操作过程,只是为进一步说明本发明的特征和优点,而不是对本发明权利要求的限制,本发明的保护范围也不限于下述的实施例。
28.需要说明地是,本发明制得的锂电池铝壳用保护胶带的结构示意图如图1所示。
29.需要说明地是,在本发明的一些实施例中,一种锂电池铝壳用保护胶带的制备方法,包括以下步骤:
30.(1)制备蓝色胶层用混合物:按质量百分比,将聚丙烯酸树脂75
‑
85%、耐高温促进剂2
‑
3%、色母0.5
‑
2%、氢氧化铝粉10
‑
25%、硬化剂1.5
‑
3%和丙酮20
‑
30%(占反应物料的20
‑
30%)在反应釜中混合搅拌2
‑
4h,得到蓝色胶层用混合物;
31.(2)制备保护胶带:采用刮刀旋转旋涂布的方式将蓝色胶层用混合物涂布在内层pet基材的一侧,其中内层pet基材的厚度为20~30μm,将其置于70
‑
90℃,干燥2
‑
4min,然后升温至120
‑
140℃下干燥2
‑
5min,得到外蓝色胶层,其厚度为25~35μm;按照同样的方法将蓝色胶层用混合物涂布在内层pet的另一侧,将其置于70
‑
90℃,干燥2
‑
4min,然后升温至120
‑
140℃下干燥2
‑
5min,得到内蓝色胶层,其厚度为15~25μm;在内蓝色胶层的一侧贴合单面离型膜,其厚度为20~30μm,离型膜层在贴合面涂布离型膜硅油,硅油转移率为1.5
‑
3.5%,收卷,将收卷后的胶带置于65
‑
75℃下熟化80
‑
90h,分条、模切,得到锂电池铝壳用保护胶带,其中保护胶带的厚度为95
‑
110μm。
32.需要说明地是,在本发明的一些实施例中,改性环氧树脂的制备方法为:按重量份计,将85
‑
105份环氧树脂与30
‑
50份3
‑
乙氧基
‑
异草酸置于装有搅拌器、温度计和冷凝管的烧瓶中,升温至85
‑
95℃,加入醇胺反应1.5
‑
2.5h,得到改性环氧树脂。
33.具体地,需要说明地是,在本发明的一些实施例中,改性环氧树脂的制备方法为:按重量份计,将100份环氧树脂e12(购自济南晴天化工科技有限公司)与42份3
‑
乙氧基
‑
异草酸置于装有搅拌器、温度计和冷凝管的烧瓶中,升温至90℃,加入n,n
‑
二甲基乙醇胺反应2h,得到改性环氧树脂。
34.需要说明地是,在本发明的一些实施例中,改性聚丙烯酸树脂的制备方法为:将聚丙烯酸树脂溶于无水乙醇中,配制成浓度为200
‑
300g/l的溶液;将改性环氧树脂溶于混合溶剂(正丁醇:乙二醇丁醚[v:v]=0.25
‑
0.35:0.65
‑
0.75)中,配制成浓度为450
‑
550g/l的溶液,然后将聚丙烯酸树脂溶液与改性环氧树脂溶液搅拌均匀,并升温至85
‑
95℃,然后加入叔胺进行反应,其中聚丙烯酸树脂重羧基、改性环氧树脂中环氧基与叔胺的摩尔比为4
‑
6:1:1
‑
3,反应1
‑
3h,在反应20
‑
30min后加入10
‑
20%的水,得到改性聚丙烯酸树脂。
[0035]
为了使其他胶层与内层pet基材具有优良的粘结作用,同时提高保护胶带的物理化学性能,采取的优选措施还包括:将pet基材浸泡在含有硅烷偶联剂、3,4
‑
二甲氧基
‑5‑
羟基苯甲酸的溶液中进行表面处理,改善内层pet基材表面的物理化学性能,进而得到性能更为优良的保护胶带。
[0036]
具体地,内层pet基材表面处理的方法为:将pet薄膜基材浸泡在浓度为150
‑
250g/l的氢氧化钠溶液中,在55
‑
65℃下处理25
‑
45min,使pet薄膜基材表面富含活性官能团,然后再浸泡在γ
‑
巯丙基三乙氧基硅烷、3,4
‑
二甲氧基
‑5‑
羟基苯甲酸与乙酸乙酯的混合溶液中,混合溶液没过pet基材表面,然后在室温下处理30
‑
60min,其中γ
‑
巯丙基三乙氧基硅烷、3,4
‑
二甲氧基
‑5‑
羟基苯甲酸与乙酸乙酯的质量比为0.5
‑
2.5:0.1
‑
0.8:15
‑
30,处理结束后,用无水乙醇充分洗涤pet基材,并置于75
‑
85℃下干燥20
‑
30min,得到表面改性的内层pet基材。
[0037]
实施例1:
[0038]
一种锂电池铝壳用保护胶带的制备方法,包括以下步骤:
[0039]
(1)制备蓝色胶层用混合物:按质量百分比,将聚丙烯酸树脂(购自上海麦克林生化科技有限公司,固含量为30%)为80%、耐高温促进剂(购自衡水松杉化工有限公司)为2.5%、色母(购自东莞金塑颜塑胶科技有限公司)为1%、氢氧化铝粉(购自广州市新稀冶金化工有限公司)为15%、硬化剂(购自湖北形影河化工有限公司)1.5%和丙酮(购自温州鼎诚化工有限公司)为25%(占反应物料的25%)在反应釜中混合搅拌3h,得到蓝色胶层用混合物;
[0040]
(2)制备保护胶带:采用刮刀旋转旋涂布的方式将上述蓝色胶层用混合物涂布在内层pet基材的一侧,其中内层pet基材的厚度为25μm,将其置于80℃,干燥3min,然后升温至125℃下干燥4min,得到外蓝色胶层,其厚度为30μm;按照同样的方法将蓝色胶层用混合物涂布在内层pet的另一侧,将其置于80℃,干燥3min,然后升温至125℃下干燥4min,得到内蓝色胶层,其厚度为20μm;在内蓝色胶层的一侧贴合单面离型膜,其厚度为25μm,离型膜层在贴合面涂布离型膜硅油,硅油转移率为2.65%,收卷,将收卷后的胶带置于70℃下熟化80h,分条、模切,得到锂电池铝壳用保护胶带,其中保护胶带的厚度为100μm。
[0041]
实施例2:
[0042]
一种锂电池铝壳用保护胶带的制备方法,其他步骤均与实施例1相同,与实施例1不同的是:
[0043]
(1)制备蓝色胶层用混合物:按质量百分比,将聚丙烯酸树脂为75%、耐高温促进剂为2.5%、色母为1.5%、氢氧化铝粉为19%、硬化剂2%和丙酮(购自温州鼎诚化工有限公司)为30%(占反应物料的30%)在反应釜中混合搅拌3h,得到蓝色胶层用混合物,其中得到的保护胶带的厚度为103μm。
[0044]
实施例3:
[0045]
一种锂电池铝壳用保护胶带的制备方法,其他步骤均与实施例1相同,与实施例1不同的是:
[0046]
(1)制备蓝色胶层用混合物:按质量百分比,将聚丙烯酸树脂为81%、耐高温促进剂为2%、色母为0.5%、氢氧化铝粉为15%、硬化剂1.5%和丙酮(购自温州鼎诚化工有限公司)为30%(占反应物料的30%)在反应釜中混合搅拌3h,得到蓝色胶层用混合物,其中得到的保护胶带的厚度为103μm。
[0047]
实施例4:
[0048]
一种锂电池铝壳用保护胶带的制备方法,其他步骤均与实施例1相同,与实施例1不同的是:
[0049]
(2)制备保护胶带:采用刮刀旋转旋涂布的方式将上述蓝色胶层用混合物涂布在内层pet基材的一侧,其中内层pet基材的厚度为27μm,将其置于75℃,干燥2min,然后升温至135℃下干燥2min,得到外蓝色胶层,其厚度为30μm;按照同样的方法将蓝色胶层用混合物涂布在内层pet的另一侧,将其置于75℃,干燥2min,然后升温至135℃下干燥2min,得到内蓝色胶层,其厚度为18μm;在内蓝色胶层的一侧贴合单面离型膜,其厚度为25μm,离型膜层在贴合面涂布离型膜硅油,硅油转移率为3.5%,收卷,将收卷后的胶带置于75℃下熟化90h,分条、模切,得到锂电池铝壳用保护胶带,其中保护胶带的厚度为100μm。
[0050]
实施例5:
[0051]
一种锂电池铝壳用保护胶带的制备方法,其他步骤均与实施例1相同,与实施例1不同的是:
[0052]
在步骤(1)制备蓝色胶层用混合物中,将聚丙烯酸树脂改为改性聚丙烯酸树脂;
[0053]
其中,改性聚丙烯酸树脂的制备方法为:将聚丙烯酸树脂溶于无水乙醇中,配制成浓度为250g/l的溶液;将改性环氧树脂溶于混合溶剂(正丁醇:乙二醇丁醚[v:v]=0.25:0.75)中,配制成浓度为450g/l的溶液,然后将聚丙烯酸树脂溶液与改性环氧树脂溶液搅拌均匀,并升温至85℃,然后加入十二叔胺进行反应,其中聚丙烯酸树脂中羧基、改性环氧树脂中环氧基与十二叔胺的摩尔比为4:1:1.5,反应2h,在反应25min后加入15%的水,得到改性聚丙烯酸树脂。
[0054]
实施例6:
[0055]
一种锂电池铝壳用保护胶带的制备方法,其他步骤均与实施例6相同,与实施例6不同的是:
[0056]
改性聚丙烯酸树脂的制备方法为:将聚丙烯酸树脂溶于无水乙醇中,配制成浓度为250g/l的溶液;将改性环氧树脂溶于混合溶剂(正丁醇:乙二醇丁醚[v:v]=0.35:0.65)中,配制成浓度为450g/l的溶液,然后将聚丙烯酸树脂溶液与改性环氧树脂溶液搅拌均匀,并升温至90℃,然后加入十二叔胺进行反应,其中聚丙烯酸树脂中羧基、改性环氧树脂中环氧基与十二叔胺的摩尔比为5:1:3,反应2h,在反应25min后加入17.5%的水,得到改性聚丙烯酸树脂。
[0057]
实施例7:
[0058]
一种锂电池铝壳用保护胶带的制备方法,其他步骤均与实施例1相同,与实施例1不同的是:
[0059]
在步骤(1)制备蓝色胶层用混合物中,对内层pet基材进行表面处理;
[0060]
其中,内层pet基材表面处理的方法为:将pet薄膜基材浸泡在浓度为200g/l的氢氧化钠溶液中,在60℃下处理30min,使pet薄膜基材表面富含活性官能团,然后再浸泡在γ
‑
巯丙基三乙氧基硅烷、3,4
‑
二甲氧基
‑5‑
羟基苯甲酸与乙酸乙酯的混合溶液中,混合溶液没过pet基材表面,然后在室温下处理30min,其中γ
‑
巯丙基三乙氧基硅烷、3,4
‑
二甲氧基
‑5‑
羟基苯甲酸与乙酸乙酯的质量比为0.75:0.25:20,处理结束后,用无水乙醇充分洗涤pet基材,并置于80℃下干燥25min,得到表面改性的内层pet基材。
[0061]
实施例8:
[0062]
一种锂电池铝壳用保护胶带的制备方法,其他步骤均与实施例7相同,与实施例7不同的是:
[0063]
其中,内层pet基材表面处理的方法中,混合溶液中,γ
‑
巯丙基三乙氧基硅烷、3,4
‑
二甲氧基
‑5‑
羟基苯甲酸与乙酸乙酯的质量比为1.5:0.75:30。
[0064]
实施例9:
[0065]
一种锂电池铝壳用保护胶带的制备方法,其他步骤均与实施例5相同,与实施例5不同的是:
[0066]
在步骤(1)制备蓝色胶层用混合物中,对内层pet基材进行表面处理;内层pet基材的处理方法同实施例7。
[0067]
实施例10:
[0068]
一种锂电池铝壳用保护胶带的制备方法,其他步骤均与实施例6相同,与实施例6不同的是:
[0069]
在步骤(1)制备蓝色胶层用混合物中,对内层pet基材进行表面处理;内层pet基材的处理方法同实施例7。
[0070]
试验例1:
[0071]
1.改性聚丙烯酸树脂红外光谱测定
[0072]
采用ftir8300(岛津公司)红外仪,kbr压片法,测定树脂的红外光谱图,扫描范围为4000
‑
400cm
‑1。
[0073]
图2为环氧树脂、改性环氧树脂和实施例5中改性聚丙烯酸树脂的红外光谱图。由图2可以看出,相对于环氧树脂,在改性环氧树脂的红外光谱中,在3038.6cm
‑1、801.7cm
‑1附近出现的特征吸收峰为苯环的伸缩振动;在1730.4cm
‑1附近出现的特征吸收峰为酯基的伸缩振动;由此可知,采用3
‑
乙氧基
‑
异草酸对环氧树脂进行改性制得改性环氧树脂;在改性聚丙烯酸树脂的红外谱图中,即将改性环氧树脂与丙烯酸树脂结合制得的改性聚丙烯酸树脂,在1730.2cm
‑1附近出现的特征吸收峰为酯基中c=o的伸缩振动,且在1700.5cm
‑1附近没有出现羧酸中c=o的伸缩振动;且在1574.9cm
‑1附近出现羧酸离子不对称o=c=o
‑
的特征吸收峰,1410.7cm
‑1附近出现羧酸离子对称o=c=o
‑
的特征吸收峰,这表明体系发生了羧基和叔胺的酸碱反应,季铵盐由于没有特征吸收谱带,因此从红外谱图中不容易观察;除此之外,在913.8cm
‑1原有的环氧基吸收峰消失,这表明体系发生了环氧开环的化学反应,由此可知,采用改性环氧树脂与聚丙烯酸树脂结合,制得改性聚丙烯酸树脂。
[0074]
试验例2:
[0075]
1.保护胶带180
°
剥离强度与持粘力测定
[0076]
180
°
剥离强度:按照gb2792
‑
2014标准制样,采用hb
‑
b01
‑
d型电脑拉力试验机,剥离速度为300mm/min,测试样品为5个,取平均值;被贴基材为锂电池铝壳(购自深圳市旭达兴五金机械有限公司),即将保护胶带去除离型膜,粘贴在锂电池铝壳(用酒精擦拭干净)上。
[0077]
持粘力:参照gb/t4851
‑
2014进行测试,测试时需注意待其试验架的样品不再摆动再开始计时,悬挂的砝码为1.5kg,保护胶带的持粘力用样品开始计时到掉下间的时间来衡量。
[0078]
表1保护胶带180
°
剥离强度与持粘力时间
[0079]
试样180
°
剥离强度/(n/25mm)持粘力时间/h实施例19.8552
实施例29.7355实施例39.9158实施例49.7951实施例510.4760实施例610.2558实施例79.9755实施例810.0453实施例910.5672实施例1010.4268
[0080]
由表1可以看出,实施例1
‑
4中保护胶带的180
°
剥离强度高于9.72n/25mm,持粘力时间高于50h;这说明采用内层pet作为基材,在其两侧涂布蓝色胶层,制得的保护胶带具有较高的剥离强度以及优良的持粘力,即该保护胶带具有较好的粘结力,对锂电池铝壳具有较好的包覆性能;实施例5
‑
6中保护胶带的180
°
剥离强度不低于10.25n/25mm,持粘力时间高于57h;对比实施例1与实施例5
‑
6,实施例5
‑
6中保护胶带的180
°
剥离强度与持粘力时间均高于实施例1,这说明采用3
‑
乙氧基
‑
异草酸对环氧树脂进行改性,然后将改性树脂改性聚丙烯酸树脂,并将其作为蓝色胶层的成分,其提高了保护胶带的粘结力,可能是因为改性环氧树脂增加了聚丙烯酸树脂的网络结构,进而增大了聚丙烯树脂的内聚强度,保护胶带的粘结力得到一定的提升;实施例7
‑
8中保护胶带的180
°
剥离强度不低于9.95n/25mm,持粘力时间高于52h;实施例9
‑
10中保护胶带的180
°
剥离强度不低于10.4n/25mm,持粘力时间高于67h;对比实施例1与实施例7
‑
8、实施例9与实施例5、实施例10与实施例6,实施例7
‑
8中保护胶带的180
°
剥离强度与持粘力时间均高于实施例1,实施例9中保护胶带的180
°
剥离强度与持粘力时间均高于实施例5,实施例10中保护胶带的180
°
剥离强度与持粘力时高于实施例6,这说明采用含有硅烷偶联剂、3,4
‑
二甲氧基
‑5‑
羟基苯甲酸的溶液对内层pet基材进行表面处理,提高了保护胶带的粘结力;可能是因为蓝色胶层中的反应物料与pet基材表面的活性基团能够发生一定的物理化学反应,进而提高了保护胶带的粘结力。
[0081]
2.保护胶带耐酸碱性测定
[0082]
将保护胶带粘贴在锂电池铝壳上,置于10%氢氧化钠溶液和10%浓硫酸溶液中浸泡5d,测试保护胶带的180
°
剥离强度(测试方法同“试验例2:保护胶带180
°
剥离强度与持粘力测定”),并观察胶带是否发生脱胶或脱落现象。
[0083]
表2保护胶带的耐酸碱性
[0084][0085]
由表2可以看出,在10%氢氧化钠溶液和10%浓硫酸溶液中浸泡5d后,实施例1
‑
10中保护胶带的180
°
剥离强度无明显变化,且在酸碱溶液中浸泡5d,保护胶带边缘均未出现脱胶、脱落现象,因此本技术方案制得的保护胶带具有优良的耐酸碱腐蚀性。
[0086]
3.保护胶带耐高温性测定
[0087]
将保护胶带粘贴在锂电池铝壳上,放置在130℃烘箱中5h,然后取出降温,冷却至室温后,用手慢慢剥离,观察锂电池铝壳上的残胶情况,进而判断保护胶带的耐热性。
[0088]
表3保护胶带的耐高温性
[0089]
[0090][0091]
由表3可以看出,在130℃烘箱中处理5h后,然后用手慢慢撕下,实施例1
‑
10中保护胶带在锂电池铝壳上均未出现残胶现象,这说明本技术方案制得的保护胶带具有优良的耐高温性能。
[0092]
4.保护胶带耐电解液性测定
[0093]
将保护胶带粘贴在锂电池铝壳上,在真空烘箱中110℃烘30min,再拿到超级净化手套箱中放置,使其与瓶装电解液、摄子同处一样的环境中,通氮气抽真空。然后在超净净化手套箱中操作,把制得的胶带装入瓶装电解液中,一次5个样并封口,放置规定时间,取出观看保护胶带的残胶情况。耐电解液性的大小以常温条件下保护胶带出现残胶或脱胶的时间为准。
[0094]
表4保护胶带的耐电解液性
[0095]
试样1d2d3d实施例1无残胶无残胶少许残胶实施例2无残胶无残胶少许残胶实施例3无残胶无残胶少许残胶实施例4无残胶无残胶少许残胶实施例5无残胶无残胶无残胶实施例6无残胶无残胶无残胶实施例7无残胶无残胶少许残胶实施例8无残胶无残胶少许残胶实施例9无残胶无残胶无残胶实施例10无残胶无残胶无残胶
[0096]
由表4可以看出,将粘贴保护胶带的锂电池铝壳置于电解液2d天后,实施例1
‑
10中保护胶带均未出现残胶现象,而在第3d时,实施例1
‑
4、实施例7
‑
8中保护胶带出现少许残胶;对比实施例1与实施例5
‑
6,在第3d时,实施例5
‑
6的保护胶带均未出现残胶现象,这说明采用3
‑
乙氧基
‑
异草酸对环氧树脂进行改性,然后将改性树脂改性聚丙烯酸树脂,并将其作为蓝色胶层的成分,其提高了保护胶带的耐电解液性能;对比实施例1与实施例7
‑
8,实施例1、实施例7
‑
8中的保护胶带均在第3d时出现少许残胶,这说明采用含有硅烷偶联剂、3,4
‑
二甲氧基
‑5‑
羟基苯甲酸的溶液对内层pet基材进行表面处理,其对保护胶带的耐电解液性能几乎无影响。
[0097]
5.保护胶带阻燃性能测定
[0098]
按照ul94
‑
2006标准,采用水平
‑
垂直燃烧试验机进行测定。
[0099]
图3为保护胶带的自熄时间;由图3可以看出,实施例1
‑
4中保护胶带的自熄时间低于8.7s,其燃烧等级(ul
‑
94)达到vtm
‑
0级,这说明本技术方案制得的保护胶带具有优良的阻燃性能;实施例5
‑
6中保护胶带的自熄时间低于5s;对比实施例1与实施例5
‑
6,实施例5
‑
6中保护胶带的自熄时间低于实施例1,这说明采用3
‑
乙氧基
‑
异草酸对环氧树脂进行改性,然后将改性树脂改性聚丙烯酸树脂,并将其作为蓝色胶层的成分,其提高了保护胶带的阻燃性能;实施例7
‑
8中保护胶带的自熄时间低于6s;实施例9
‑
10中保护胶带的自熄时间低于3.5s;对比实施例1与实施例7
‑
8,实施例7
‑
8中保护胶带的自熄时间低于实施例1,这说明采用含有硅烷偶联剂、3,4
‑
二甲氧基
‑5‑
羟基苯甲酸的溶液对内层pet基材进行表面处理,进一步提高了保护胶带的阻燃性能;对比实施例9与实施例1、实施例5、实施例7
‑
8,实施例10与实施例1、实施例6、实施例7
‑
8,实施例9中保护胶带的自熄时间低于实施例1、实施例5、实施例7
‑
8,实施例10中保护胶带的自熄时间低于实施例1、实施例6、实施例7
‑
8,这说明采用3
‑
乙氧基
‑
异草酸对环氧树脂进行改性,然后将改性树脂改性聚丙烯酸树脂,并将其作为蓝色胶层的成分;同时采用含有硅烷偶联剂、3,4
‑
二甲氧基
‑5‑
羟基苯甲酸的溶液对内层pet基材进行表面处理,显著提高了保护胶带的阻燃性能。
[0100]
6.保护胶带耐磨性测定
[0101]
试验装置由双带轮驱动装置构成,每个带轮有19个凹槽和一种ru齿廓;在带轮处测量时,胶带运行速度为6500rpm,带轮之间的张力为530n,胶带节距为9.525mm,试验温度为25
±
3℃,试验时间为250h,计算试验前后胶带的质量损失,进而判断胶带的耐磨性。
[0102]
图4为保护胶带的质量损失;由图4可以看出,试验250h后,实施例1
‑
4中保护胶带的质量损失低于0.45g,因此,本技术方案制得的保护胶带具有优良的耐磨性能;实施例5
‑
6中保护胶带的质量损失低于0.2g;对比实施例1与实施例5
‑
6,实施例5
‑
6中保护胶带的质量损失低于实施例1,这说明采用3
‑
乙氧基
‑
异草酸对环氧树脂进行改性,然后将改性树脂改性聚丙烯酸树脂,并将其作为蓝色胶层的成分,其提高了保护胶带的耐磨性能;实施例7
‑
8中保护胶带的自熄时间低于0.22g;实施例9
‑
10中保护胶带的自熄时间低于0.1g;对比实施例1与实施例7
‑
8、实施例9与实施例5、实施例10与实施例6,实施例7
‑
8中保护胶带的质量损失低于实施例1,实施例9的质量损失低于实施例5,实施例10的质量损失低于实施例6,这说明采用含有硅烷偶联剂、3,4
‑
二甲氧基
‑5‑
羟基苯甲酸的溶液对内层pet基材进行表面处理,进一步提高了保护胶带的耐磨性能。
[0103]
本发明的操作步骤中的常规操作为本领域技术人员所熟知,在此不进行赘述。
[0104]
以上实施方式仅用于说明本发明,而并非对本发明的限制,本领域的普通技术人员,在不脱离本发明的精神和范围的情况下,还可以做出各种变化和变型。因此,所有等同的技术方案也属于本发明的范畴,本发明的专利保护范围应由权利要求限定。
再多了解一些
本文用于企业家、创业者技术爱好者查询,结果仅供参考。