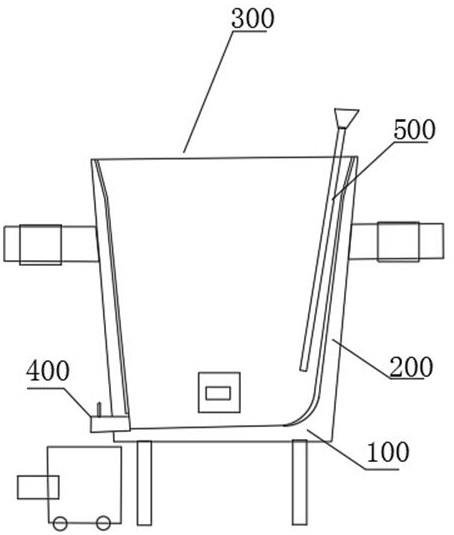
1.本实用新型涉及钢渣分离领域,具体涉及一种分离钢水和钢渣的炼渣炉。
背景技术:
2.钢渣是冶金工业中产生的废渣,其产生率为粗钢产量的8%~15%,是炼钢过程中的一种副产品,钢渣的主要矿物组成为硅酸三钙、硅酸二钙、钙镁橄榄石、钙镁蔷薇辉石、铁酸二钙、ro(镁、铁、锰的氧化物,即feo、mgo、mno形成的固熔体)、游离石灰(f-cao)等。钢渣不仅可以作为冶炼溶剂在本厂循环利用,还可以代替石灰石,且可以从中回收大量的金属铁和其他有用元素,更是可以作为制造筑路材料、建筑材料或农业肥料的原材料。
3.熔融状态下的钢渣和钢水的密度是不同的,熔融的钢渣浮在钢水的上方。钢厂炼钢过程中,需将钢水上方的钢渣倒入渣罐,通过运输车辆将渣罐中的钢渣倒入炼渣炉。一方面,熔融的钢渣浮在钢水的上方,倾倒钢炉时,难免会将钢水倒入渣罐;此外,为了保障钢水的纯度,一般会多倒入一些钢水,这给后续的钢渣处理和利用带来了困难:
4.一是钢渣中混入了较多的钢水,给钢渣处理工艺中钢铁回收工艺如磁选工艺等带来了挑战和困难;现有钢渣粒化处理工艺,通过风淬法对钢渣进行粒化处理后,因为含有钢粒,需要将钢粒和钢渣粒进行分离,目前采用磁选法分离,不仅分离不干净、不彻底,而且非常麻烦;
5.二是残余钢水在炼渣炉透气砖表面被渣粘附,造成热修理透气砖困难,严重影响炼渣炉透气砖底吹效果,对安全生产造成威胁;
6.三是残余钢水在炼渣炉底部冷却凝结后造成炼渣炉容积减小,重量变大;
7.四是由于粘渣物非常坚硬且与炼渣炉表面结合牢固,去除十分困难,拆除时间长,造成炼渣炉修理困难;
8.五是因为钢厂和钢渣处理区分属不同的区域,混有钢水的钢渣要通过运输车辆运输到钢渣处理区处理,钢渣与钢水在运输途中温度降低导致凝结,对后续钢渣粒化处理工艺如风淬法对钢渣进行造粒等带来了挑战,凝结的钢渣、钢水无法进行风淬,更无法进行后续的钢铁与渣粒的磁选分离。
技术实现要素:
9.为了解决上述技术问题,本实用新型提出一种能够分离钢水和钢渣的炼渣炉,包括炉底、侧壁和炉口,侧壁环绕炉底一周且侧壁底部与炉底连接在一起形成炉腔,侧壁环绕炉底一周上部形成开口为炉口,在侧壁的下部、炉底的上端还设有导流装置。
10.进一步的,所述导流装置包括导流管、闸门,导流管为长方体状,沿导流管纵向,在导流管的中部设有贯通的导流孔,导流管的上部还设有与闸门配套的闸门插入槽,所述闸门插入闸门插入槽内截断导流孔;所述闸门由石墨材料制成,所述导流管也由石墨材料制成。
11.进一步的,所述侧壁上还设有加料管,所述加料管固定在侧壁上,加料管的上端伸
出炼渣炉,加料管的下端通入炼渣炉的下部。
12.进一步的,所述加料管的一侧内壁上设有上滑板,上滑板与加料管的内壁之间的夹角10
‑
80度,在加料管另一侧的侧壁上设有下滑板,下滑板与加料管的内壁之间的夹角10
‑
80度;上滑板与下滑板错位设置,上滑板位于下滑板的上端,所述上滑板的底端位于下滑板中部的上部,上滑板的底端与下滑板中部之间设有间隙,上滑板的底端与下滑板顶端一端的加料管内壁之间的距离为加料管内径的25%
‑
50%,下滑板的底端与下滑板顶端一端的加料管内壁之间的距离为加料管内径的25%
‑
50%。
13.进一步的,所述上滑板底端设有圆弧,所述下滑板的底端设有圆弧。
14.进一步的,所述侧壁包括两层,内层为耐火材料层,外层为奥氏体不锈钢层,在耐火材料层与奥氏体不锈钢层之间还设有中频感应线圈,还包括脉宽调制或中频交流电转换设备,所述脉宽调制或中频交流电转换设备,将50hz市电转换成200
‑
6000hz中频电源,中频电源对中频感应线圈供电,中频感应线圈对炼渣炉内的钢铁和钢渣进行感应加热。
15.进一步的,还包括密度检测装置和密度显示装置,所述密度检测装置用于检测导流装置流出的液体的密度,并将检测到的密度值发送给密度显示装置显示。
16.进一步的,还包括密度报警系统和报警装置,所述密度报警系统安装在密度显示装置上,用于实施监控密度检测装置发送来的密度值,当密度发生变化时,发送指令为报警装置,报警装置通过声音、图像或数字显示,通知操作人员去关闭导流装置。
17.本发明还提出一种从炼渣炉分离钢水的方法,通过如下步骤将钢水与钢渣分离:
18.步骤s1,运渣车辆运输渣罐,将渣罐升起后倾斜,将混有钢水的钢渣从炉口处倒入炼渣炉;
19.步骤s2,对中频感应线圈通电,炼渣炉在中频感应线圈的作用下,钢水产生自热从而保持钢水的流动性;
20.步骤s3,持续倒入混有钢水的钢渣,当炼渣炉内的钢水与钢渣满荷时,将炼渣炉的钢渣与钢水静止一段时间,钢水密度与钢渣密度不同,钢水密度大于钢渣密度密度的原因,钢水位于炼钢炉的下层,钢渣漂浮在钢水的上层,钢水与钢渣分离;
21.步骤s3,通过加料管加入氧化铁皮颗粒或铁矿粉,氧化铁皮颗粒或铁矿粉与钢水发生化学反应产生热量,对钢渣进行加热,使得凝固的钢渣重新融化成液态和或保持钢渣液态;
22.步骤s4,打开导流装置的闸门,钢水通过导流装置流出;
23.步骤s5,当炼渣炉内的钢水流尽或即将流尽,或液体钢渣流出时,关闭闸门。
24.进一步的,步骤s1还包括,
25.s11干燥氧化铁皮或氧化铁皮颗粒或铁矿粉的步骤,将氧化铁皮或氧化铁皮颗粒或铁矿粉通过烘干或日晒或风吹的方式进行干燥,保证氧化铁皮或氧化铁皮颗粒或铁矿粉处于干燥状态;
26.s12在将混有钢水的钢渣从炉口处倒入炼渣炉之前,在炼渣炉内放置干燥的氧化铁皮或氧化铁皮颗粒或铁矿粉的步骤;当混有钢水的钢渣从炉口处倒入炼渣炉后,钢渣、钢水、氧化铁皮或氧化铁皮颗粒或铁矿粉三者因为密度不同,静止一段时间后,钢水在下层,氧化铁皮或氧化铁皮颗粒或铁矿粉在中层,漂浮在钢水上,钢渣在最上层,氧化铁皮或氧化铁皮颗粒或铁矿粉与钢水发生剧烈反应,产生大量热,对钢渣进行加热,使得钢渣保持在熔
融状态即液态;
27.步骤s5还包括,采用密度检测装置检测导流装置流出液体的密度的步骤;采用密度检测装置检测导流装置流出液体的密度,当检测到密度发生变化时,通过声音、图像、文字显示、或灯光闪烁的方式通知操作人员关闭闸门。
28.有益效果:本实用新型在炼渣炉下部设置了导流装置,可以将钢水从导流装置流出,从而使得钢渣与钢水分离,确保了钢渣的纯度,解决了后续钢渣粒化处理工艺后钢铁与渣粒分离的难题。在炼渣炉上设有中频感应线圈对炼渣炉内的钢铁和钢渣进行感应加热,使得钢水保持液态,防止了钢水在炼渣炉底部凝结,解决了现有炼渣炉残余钢水在炼渣炉底部冷却凝结后造成炼渣炉容积减小,重量变大的难题,以及残余钢水在炼渣炉透气砖表面被渣粘附,造成热修理透气砖困难,严重影响炼渣炉透气砖底吹效果,解决了安全生产的难题;通过加料管加入氧化铁皮颗粒或铁矿粉以及在将混有钢水的钢渣从炉口处倒入炼渣炉之前,在炼渣炉内放置干燥的氧化铁皮或氧化铁皮颗粒或铁矿粉的工艺,氧化铁皮颗粒或铁矿粉与钢水发生化学反应产生大量的热,对炼渣炉上部的钢渣包括凝结的钢渣进行加热,使得钢渣保持在熔融状态即液态,不仅解决了钢渣粒化工艺中钢渣凝结无法粒化的难题,还解决了炼渣炉粘渣物粘结的难题。
附图说明
29.图1为本实用新型分离钢水和钢渣的炼渣炉结构示意图;
30.图2为导流装置正视结构示意图;
31.图3为导流装置剖面结构示意图;
32.图4为加料管结构示意图。
具体实施方式
33.实施例1:现有的炼渣炉或炼渣罐均没有这种导流装置,普遍采用用挡渣块篦住钢渣,倾斜倾倒的方式将钢水倒出,这种倾倒的方式一方面钢渣与钢水分离不彻底;另一方面,钢水和钢渣容易凝固,导致粘渣,钢水凝结在炉底;第三,炼渣炉容易损坏;第四,若操作不慎,还存在钢水和钢渣洒出甚至是喷溅出炼渣炉、炼渣罐的风险,导致生产作业非常不安全。如图1所示,本实用新型提出一种能够分离钢水和钢渣的炼渣炉,包括炉底100、侧壁200和炉口300,侧壁200环绕炉底100一周且侧壁底部与炉底连接在一起形成炉腔,侧壁200环绕炉底一周上部形成开口为炉口300,在侧壁的下部、炉底的上端还设有导流装置400。
34.本实用新型在炼渣炉下部设置了导流装置400,可以将钢水从导流装置400流出,不需要倾斜炼渣炉,也不需要人工投入挡渣块,不仅解决了炼渣炉容易损坏,以及生产作业安全的难题,更是使得钢渣与钢水分离,确保了钢渣的纯度,解决了后续钢渣粒化处理工艺后钢铁与渣粒分离的难题。
35.进一步的,如图2、3所示,所述导流装置400包括导流管401、闸门402,导流管401为长方体状,沿导流管纵向,在导流管的中部设有贯通的导流孔403,导流管401的上部还设有与闸门402配套的闸门插入槽404,所述闸门402插入闸门插入槽内404截断导流孔403。因为钢水温度非常高,一般在1250
‑
2360摄氏度之间,一般在1700摄氏度左右,普通材料的导流装置无法满足在如此高温下工作,本实用新型闸门402由石墨材料制成,所述导流管401也
由石墨材料制成。
36.进一步的,所述导流孔403的最底面与炉底100的上表面位于同一水平面,或低于炉底100的上表面,进一步的,所述炉底100具有一定的坡度,且导流孔403位于炉底100的坡度的最底端,确保钢水流出彻底无残留。
37.进一步的,如图1所示,所述侧壁200上还设有加料管500,所述加料管500固定在侧壁200上,加料管500的上端伸出炼渣炉,加料管500的下端通入炼渣炉的下部,并与炉底100保持一定距离。
38.进一步的,所述加料管500设有2
‑
5个,分别均匀固定分布在侧壁200上。
39.进一步的,如图4所示,所述加料管500的一侧内壁上设有上滑板501,上滑板501与加料管500的内壁之间的夹角10
‑
80度,在加料管500另一侧的侧壁上设有下滑板502,下滑板502与加料管的内壁之间的夹角10
‑
80度;上滑板501与下滑板502错位设置,上滑板501位于下滑板502的上端,所述上滑板501的底端5011位于下滑板5022中部的上部,上滑板501的底端5011与下滑板中部5022之间设有间隙,上滑板的底端5011与下滑板顶端5013一端的加料管内壁之间的距离为加料管内径的25%
‑
50%,下滑板的底端5021与下滑板顶端5023一端的加料管内壁之间的距离为加料管内径的25%
‑
50%。
40.进一步的,所述上滑板底端5011设有圆弧,所述下滑板的底端5021设有圆弧。
41.通过加料管500向炼渣炉内加入氧化铁皮颗粒或铁矿粉时,氧化铁皮颗粒或铁矿粉与钢水发生剧烈的化学反应,产生大量的热,甚至是气泡,如果氧化铁皮颗粒或铁矿粉干燥不彻底,钢水会沿着加料管喷溅而出,导致安全生产事故。本实用新型在加料管500内设置了错位分布具有坡度的上滑板501与下滑板502,不仅能保证氧化铁皮颗粒或铁矿粉能沿着加料管500滑入炼渣炉,更是能防止钢水沿着加料管500喷出,保证了生产安全。
42.进一步的,为了保证加入氧化铁皮颗粒或铁矿粉方便,在加料管500的上端还设有漏斗。
43.本实用新型通过加料管500加入氧化铁皮颗粒或铁矿粉,氧化铁皮颗粒或铁矿粉与钢水发生化学反应产生大量的热,对炼渣炉上部的钢渣包括凝结的钢渣进行加热,使得钢渣保持在熔融状态即液态,不仅解决了钢渣粒化工艺中钢渣凝结无法粒化的难题,还解决了炼渣炉粘渣物粘结的难题。
44.进一步的,所述侧壁200包括两层,内层为耐火材料层,进一步的,耐火材料层为耐火砖层;外层为奥氏体不锈钢层,奥氏体不锈钢具有弱磁性,采用该种材料制成的炼渣炉,才通过中频感应线圈对钢水进行磁反应,使钢水产生自热,从而确保钢水呈液态。在耐火材料层与奥氏体不锈钢层之间还设有中频感应线圈,还包括脉宽调制或中频交流电转换设备,所述脉宽调制或中频交流电转换设备,将50hz市电转换成200
‑
6000hz中频电源,中频电源对中频感应线圈供电,中频感应线圈对炼渣炉内的钢铁和钢渣进行感应加热。
45.在炼渣炉上设有中频感应线圈对炼渣炉内的钢铁和钢渣进行感应加热,使得钢水保持液态,防止了钢水在炼渣炉底部凝结,解决了现有炼渣炉残余钢水在炼渣炉底部冷却凝结后造成炼渣炉容积减小,重量变大的难题,以及残余钢水在炼渣炉透气砖表面被渣粘附,造成热修理透气砖困难,严重影响炼渣炉透气砖底吹效果,解决了安全生产的难题。
46.进一步的,还包括密度检测装置和密度显示装置,所述密度检测装置设置在导流装置400的斜上方,用于检测导流装置流出的液体的密度,并将检测到的密度值发送给密度
显示装置显示。
47.进一步的所述密度检测装置为阿米巴感应摄像头。该阿米巴感应摄像头具备检测密度的功能,还具有检测密度变化并进行提醒的功能。该阿米巴感应摄像头为市场现有产品,产自芬兰企业,可以从芬兰购买得到,本实用新型仅是集成了该设备,关于密度检测装置检测密度,以及检测密度变化进行提醒的技术属于现有技术,本实用新型在此不在累述。
48.进一步的,还包括密度报警系统和报警装置,所述密度报警系统安装在密度显示装置上,用于实施监控密度检测装置发送来的密度值,当密度发生变化时,发送指令为报警装置,报警装置通过声音、图像或数字显示,通知操作人员去关闭导流装置。
49.进一步的,在侧200壁上还设有吊壁和倾倒吊耳,所述吊壁有2个,对称设置在侧壁上,所述吊耳设在炼渣炉的中下部。
50.进一步的还包括钢包,沿着导流装置流出的钢水流入钢包。
51.进一步的,所述炉底100还设有支撑架。钢包的高度低于支撑架,钢包下部还设有万向轮,钢包的上部为开口。
52.实施例2:本发明还提出一种从炼渣炉分离钢水的方法,通过如下步骤将钢水与钢渣分离:
53.步骤s1,运渣车辆运输渣罐,将渣罐升起后倾斜,将混有钢水的钢渣从炉口处倒入炼渣炉;
54.步骤s2,对中频感应线圈通电,炼渣炉在中频感应线圈的作用下,钢水产生自热从而保持钢水的流动性;
55.步骤s3,持续倒入混有钢水的钢渣,当炼渣炉内的钢水与钢渣满荷时,将炼渣炉的钢渣与钢水静止一段时间,钢水密度与钢渣密度不同,钢水密度大于钢渣密度,密度的原因,钢水位于炼钢炉的下层,钢渣漂浮在钢水的上层,钢水与钢渣分离;
56.步骤s3,通过加料管加入氧化铁皮颗粒或铁矿粉,氧化铁皮颗粒或铁矿粉与钢水发生化学反应产生热量,对钢渣进行加热,使得凝固的钢渣重新融化成液态和或保持钢渣液态;
57.步骤s4,打开导流装置的闸门,钢水通过导流装置流出;
58.步骤s5,当炼渣炉内的钢水流尽或即将流尽,或液体钢渣流出时,关闭闸门。
59.实施例3:一种从炼渣炉分离钢水的方法,通过如下步骤将钢水与钢渣分离:
60.第一步:s11干燥氧化铁皮或氧化铁皮颗粒或铁矿粉的步骤,将氧化铁皮或氧化铁皮颗粒或铁矿粉通过烘干或日晒或风吹的方式进行干燥,保证氧化铁皮或氧化铁皮颗粒或铁矿粉处于干燥状态。
61.氧化铁皮或氧化铁皮颗粒或铁矿粉干燥后,当氧化铁皮或氧化铁皮颗粒或铁矿粉与钢水发生剧烈化学反应时,能防止水蒸汽导致的钢水钢渣喷溅,甚至是爆炸。
62.第二步:在将混有钢水的钢渣从炉口处倒入炼渣炉之前,在炼渣炉内放置干燥的氧化铁皮或氧化铁皮颗粒或铁矿粉的步骤;
63.进一步的,采用蛇皮袋或塑料包装袋将氧化铁皮或氧化铁皮颗粒或铁矿粉包住,丢入炼渣炉,采用蛇皮袋或塑料包装袋包装,能防止运渣车辆倒入混有钢水的钢渣时,产生剧烈反映造成液体喷溅,造成生产安全事故。
64.第三步:运渣车辆运输渣罐,将渣罐升起后倾斜,将混有钢水的钢渣从炉口处倒入
炼渣炉;因为钢厂与炼渣厂大多不在同一个区域,运渣车辆在运输过程中,钢渣甚至钢水会因为冷却导致凝结,钢水钢渣混合物尤其是钢渣会失去流动性。当混有钢水的钢渣从炉口处倒入炼渣炉后,钢渣、钢水、氧化铁皮或氧化铁皮颗粒或铁矿粉三者因为密度不同,静止一段时间后,钢水在下层,氧化铁皮或氧化铁皮颗粒或铁矿粉在中层,漂浮在钢水上,钢渣在最上层,氧化铁皮或氧化铁皮颗粒或铁矿粉与钢水发生剧烈反应,产生大量热,对钢渣进行加热,使得钢渣保持在熔融状态即液态。
65.第四步,对中频感应线圈通电,炼渣炉在中频感应线圈的作用下,钢水产生自热从而保持钢水的流动性。中频感应线圈对钢水进行磁反应,使钢水自热的原理和技术属于现有技术,在此本实用新型不在累述。
66.第五步,持续倒入混有钢水的钢渣,当炼渣炉内的钢水与钢渣满荷时,将炼渣炉的钢渣与钢水静止一段时间,钢水密度与钢渣密度不同,钢水密度大于钢渣密度,密度的原因,钢水位于炼钢炉的下层,钢渣漂浮在钢水的上层,钢水与钢渣分离。
67.第六步,通过加料管加入氧化铁皮颗粒或铁矿粉,氧化铁皮颗粒或铁矿粉与钢水发生化学反应产生热量,对钢渣进行加热,使得凝固的钢渣重新融化成液态和或保持钢渣液态。
68.第七步,对炼渣炉进行震荡或摇晃,使得钢水与钢渣分离彻底,防止和减少钢水残留在钢渣内,使得钢渣漂浮在钢水上。
69.第八步,静止一端时间,确保钢水和钢渣分离完全。
70.第九步,打开导流装置的闸门,钢水通过导流装置流出。
71.第十步,采用密度检测装置检测导流装置流出液体的密度,当检测到密度发生变化时,通过声音、图像、文字显示、或灯光闪烁的方式通知操作人员关闭闸门。当炼渣炉内的钢水流尽或即将流尽,或液体钢渣流出时,操作人员关闭闸门。
72.第十一步,操作人员关闭闸门。
73.第十二步,操作人员操作外部设备,将炼渣炉内的钢渣送入钢渣粒化设备进行造粒工艺的处理。
74.进一步的,第八步中,还可以包括向炼渣炉内伸入燃烧喷嘴,通过管路将氧气和天然气送入燃烧喷嘴进行燃烧对钢渣进行加热的步骤。
再多了解一些
本文用于企业家、创业者技术爱好者查询,结果仅供参考。