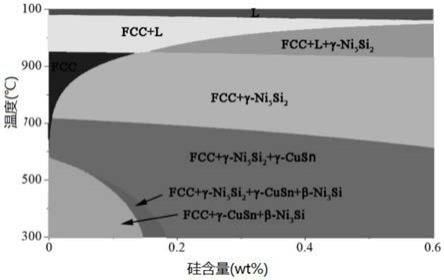
1.本发明涉及合金技术领域,具体涉及一种铜镍锡硅合金及其制备方法和应用。
背景技术:
2.铜镍锡合金是一类较新型的铜合金,具有高强度、高弹性、耐磨和耐腐蚀等优点,在航空航天、轨道交通、重载机械及海洋工程等领域的应用前景十分广阔。但是,铜镍锡合金的制备有两个技术难题,一是凝固过程中锡元素的偏析,产生大量的富锡相;二是热处理过程中不连续沉淀γ相的大量产生,这将损害合金的力学性能。通过合金化元素的添加结合合理的热处理工艺可以在一定程度上解决上述两个难题。例如,现有技术“cu
‑
9.5ni
‑
2.3sn
‑
0.5si合金的固溶处理工艺与组织性能研究”(参见刘东辉,廖钰敏,邓丽华.cu
‑
9.5ni
‑
2.3sn
‑
0.5si合金的固溶处理工艺与组织性能研究[j].热处理,2014,29(04):29
‑
32.)公开了一种cu
‑
9.5ni
‑
2.3sn
‑
0.5si合金,合金中形成了ni2si、ni
31
si
12
相并占据形核位置,该合金的维氏硬度为152hv。然而,上述合金由于锡元素含量低,时效处理过程产生的析出相有限,所以合金的硬度不够高。
技术实现要素:
[0003]
有鉴于此,本发明的目的在于提供一种铜镍锡硅合金及其制备方法和应用,本发明提供的铜镍锡硅合金硬度高、强度高、摩擦磨损性能优异,具有优异的综合力学性能。
[0004]
为了实现上述发明目的,本发明提供以下技术方案:
[0005]
本发明提供了一种铜镍锡硅合金,化学组成包括6wt%ni,6wt%sn,0.15~1wt%si和余量铜;
[0006]
所述铜镍锡硅合金具有γ
‑
ni5si2初生相、do
22
型析出相和l12型析出相。
[0007]
本发明提供了上述技术方案所述铜镍锡硅合金的制备方法,包括以下步骤:
[0008]
将合金原料进行熔炼,得到合金液,将所述合金液进行浇注,得到铸态合金;
[0009]
将所述铸态合金依次进行热轧和固溶处理,得到固溶态合金;所述固溶处理的温度为725~875℃;
[0010]
将所述固溶态合金依次进行冷轧和时效处理,得到铜镍锡硅合金;所述时效处理的温度为250~450℃。
[0011]
优选的,浇注时所述合金液的温度为1200~1250℃。
[0012]
优选的,所述热轧的温度为800~900℃,总变形量为50~80%。
[0013]
优选的,所述固溶处理的保温时间为4~8h。
[0014]
优选的,所述冷轧的温度为室温,总变形量为30~50%。
[0015]
优选的,所述时效处理的保温时间为0.5~4h。
[0016]
优选的,所述合金原料的化学组成、固溶处理的温度和时效处理的温度通过pandat软件模拟计算得到。
[0017]
本发明提供了上述技术方案所述铜镍锡硅合金或上述技术方案所述制备方法得
到的铜镍锡硅合金在高端滑动轴承、航空航天、轨道交通、重载机械或海洋工程中应用。
[0018]
本发明提供了一种铜镍锡硅合金,化学组成包括6wt%ni,6wt%sn,0.15~1wt%si和余量铜;所述铜镍锡硅合金具有γ
‑
ni5si2初生相、do
22
型析出相和l12型析出相。在本发明中,所述铜镍锡硅合金中铜作为基体,镍可以与铜形成无限固溶体,锡在铜中也具有一定的固溶度且可降低镍在铜中的溶解度,而且当锡含量超过4%时合金为典型的调幅分解强化型合金,通过时效处理可以发生调幅分解同时产生do
22
型析出相和l12型析出相及不连续沉淀γ相,硅在铜中的固溶度极小,而且添加到铜镍锡三元合金中时主要以γ
‑
ni5si2初生相的形式存在,可以抑制合金凝固过程中锡元素的偏析及热处理过程中不连续沉淀γ相的大量产生。本发明提供的铜镍锡硅合金中经过最终的时效处理之后合金的组织中同时有相对粗大的γ
‑
ni5si2初生相及细小的do
22
型和l12型析出相分布于基体之上,合金的综合性能得到了明显的提高。如实施例结果所示,本发明提供的铜镍锡硅合金的抗拉强度为783~967mpa,屈服强度为712~912mpa,断后伸长率为10~14%,硬度为241~327hb,边界润滑条件下对轴承钢的摩擦系数为0.12~0.15,说明,本发明提供的铜镍锡硅合金的综合力学性能和耐磨性能优异。
[0019]
本发明提供了上述技术方案所述铜镍锡硅合金的制备方法。本发明提供的制备方法,针对典型的铜镍锡合金制备中面临的偏析和不连续沉淀γ相大量产生的难题,通过成分设计,在cu
‑
6ni
‑
6sn合金中添加0.15~1%合金化元素si并且合理控制后续的热处理温度和时间以解决铜镍锡合金制备所面临的这一共性难题,具体的,通过成分设计及控制固溶处理的温度,避免了铜镍锡硅合金在固溶处理过程中发生重熔;通过初生相的作用及控制时效处理的温度,避免产生大量的不连续沉淀相,从而提高了铜镍锡合金的力学性能和耐磨性能;而且,本发明提供的制备方法操作简单、成本低、效率高,适宜工业化生产。
附图说明
[0020]
图1为cu
‑
6ni
‑
6sn
‑
xsi合金的模拟相图;
[0021]
图2为实施例1制备的铸态cu
‑
6ni
‑
6sn
‑
0.6si合金的金相图;
[0022]
图3为实施例1制备的铸态cu
‑
6ni
‑
6sn
‑
0.6si合金的sem图和能谱分析结果图,其中,(a)为sem图,a为黑色物相,b为白色物相,c为基体物相,(b)为黑色物相的能谱分析结果,(c)为白色物相的能谱分析结果,(d)为基体物相的能谱分析结果;
[0023]
图4为图2中白色物相b的透射电镜图、选区电子衍射图、高分辨透射电镜图和傅里叶变换图,其中,(a)为透射明场像图,(b)为选区电子衍射图,(c)为高分辨透射电镜图,(d)为傅里叶变换图;
[0024]
图5为实施例1制备的固溶态cu
‑
6ni
‑
6sn
‑
0.6si合金的sem图和能谱分析结果,其中,(a)为sem图,(b)为eds spot1的能谱分析结果,(c)为eds spot2的能谱分析结果,(d)为eds spot3的能谱分析结果;
[0025]
图6为图4中eds spot1的透射电镜图、选区电子衍射图、高分辨透射电镜图和傅里叶变换图,其中,(a)透射明场像图,(b)为选区电子衍射图,(c)为高分辨透射电镜图,(d)为傅里叶变换图;
[0026]
图7为实施例1制备的时效态cu
‑
6ni
‑
6sn
‑
0.6si合金的金相图;
[0027]
图8为本实施例1制备的时效态cu
‑
6ni
‑
6sn
‑
0.6si合金的tem图,其中,(a)为透射
明场像图,(b)为选区电子衍射图,(c)为高分辨透射电镜图,(d)为傅里叶变换图;
[0028]
图9为对比例1制备的铸态cu
‑
6ni
‑
6sn合金的金相图;
[0029]
图10为对比例1制备的时效态cu
‑
6ni
‑
6sn合金的金相图;
[0030]
图11为对比例1制备的时效态cu
‑
6ni
‑
6sn合金的透射明场像图;
[0031]
图12为实施例1制备的cu
‑
6ni
‑
6sn
‑
0.6si合金和对比例1制备的cu
‑
6ni
‑
6sn合金拉伸试样的断口形貌sem图;
[0032]
图13为对比例5制备的cu
‑
6ni
‑
6sn
‑
0.6si合金固溶处理后的金相图;
[0033]
图14为对比例7制备的cu
‑
6ni
‑
6sn
‑
0.6si合金时效处理后的金相图;
[0034]
图15为实施例1制备的cu
‑
6ni
‑
6sn
‑
0.6si合金和对比例1制备的cu
‑
6ni
‑
6sn合金的拉伸曲线;
[0035]
图16为实施例1制备的cu
‑
6ni
‑
6sn
‑
0.6si合金三组摩擦磨损试验结果;
[0036]
图17为对比例1制备的cu
‑
6ni
‑
6sn合金三组摩擦磨损试验结果。
具体实施方式
[0037]
本发明提供了一种铜镍锡硅合金(记为cu
‑
6ni
‑
6sn
‑
(0.15~1)si),化学组成包括6wt%ni,6wt%sn,0.15~1wt%si和余量铜;所述铜镍锡硅合金具有γ
‑
ni5si2初生相、do
22
型析出相和l12型析出相。在本发明中,所述铜镍锡硅合金中si的含量优选为0.2~0.9wt%,更优选为0.3~0.8wt%,进一步优选为0.4~0.7wt%,最优选为0.5~0.6wt%。
[0038]
本发明提供了上述技术方案所述铜镍锡硅合金的制备方法,包括以下步骤:
[0039]
将合金原料进行熔炼,得到合金液,将所述合金液进行浇注,得到铸态合金;
[0040]
将所述铸态合金依次进行热轧和固溶处理,得到固溶态合金;所述固溶处理的温度为725~875℃;
[0041]
将所述固溶态合金依次进行冷轧和时效处理,得到铜镍锡硅合金;所述时效处理的温度为250~450℃。
[0042]
在本发明中,若无特殊说明,所有的原料组分均为本领域技术人员熟知的市售商品。
[0043]
本发明将合金原料进行熔炼,得到合金液,将所述合金液进行浇注,得到铸态合金。
[0044]
在本发明中,所述合金原料优选为电解铜、镍、锡和硅,所述电解铜的纯度优选≥99.97%,所述镍的纯度优选≥99.8%,所述锡的纯度优选≥99.9%,所述硅的纯度优选≥99.99%;在本发明中,所述合金原料中电解铜、镍、锡和硅的用量比满足上述技术方案所述铜镍锡硅合金的化学组成。在本发明中,将合金原料进行熔炼,优选为将电解铜、镍和锡熔化,得到熔体,当所述熔体的温度保持在1250~1350℃时加入硅进行保温熔炼,得到合金液;所述熔化的温度优选为1100~1400℃,更优选为1200~1300℃;所述保温熔炼的温度优选为1250~1350℃,更优选为1300℃;所述保温熔炼的时间优选为5~15min,更优选为10min。在本发明中,所述熔炼优选在中频感应炉的石墨坩埚中进行。
[0045]
在本发明中,浇注时所述合金液的温度优选为1200~1250℃,更优选为1210~1240℃,进一步优选为1220~1230℃。在本发明中,所述浇注采用的模具优选为预热钢模,所述预热钢模的温度优选为200~400℃,更优选为300℃。
[0046]
所述浇注后本发明优选还包括冷却至室温、脱模和表面切割,得到铸态合金;本发明对于所述冷却和脱模的方式没有特殊限定,采用本领域技术人员熟知的冷却和脱模的方式即可。本发明对于所述表面切割没有特殊限定,能够将铸态合金表面的缩孔和氧化皮去除即可。在本发明中,所述铸态合金的组织中存在γ
‑
ni5si2初生相。
[0047]
在本发明中,所述合金原料的化学组成(即铜镍锡硅合金的化学组成)优选利用pandat软件确定,利用pandat软件进行铜镍锡硅合金(记为cu
‑
6ni
‑
6sn
‑
xsi,其中,x为铜镍锡硅合金中si的质量百分含量)的模拟相图计算,根据模拟相图计算的结果预测cu
‑
6ni
‑
6sn
‑
xsi合金的凝固过程中的物相组成,确定物相组成中是否会有初生相产生并预测初生相的类型;具体步骤如下:打开pandat软件,选取cu,ni,sn,si四种元素,设定ni质量百分含量为6%,sn质量百分含量为6%,si为变量,余量为cu;设定计算温度为300~1200℃;计算相图并输出结果,得到cu
‑
6ni
‑
6sn
‑
xsi合金的模拟相图结果;根据模拟相图结果确定si含量以及cu
‑
6ni
‑
6sn
‑
xsi合金的凝固过程中的物相组成,只有初生相是不能通过固溶处理消除掉的,进而可以在后续的时效处理过程中抑制不连续沉淀γ相的大量产生。固溶处理和时效处理温度是根据模拟相图中的物相转变线(固相线、液相线及其他相界线)并结合实验表征确定的。
[0048]
得到铸态合金后,本发明将所述铸态合金依次进行热轧和固溶处理,得到固溶态合金。在本发明中,所述热轧的温度优选为725~875℃,更优选为750~850℃,进一步优选为800℃;所述热轧的总变形量优选为50~80%,更优选为55~75%,进一步优选为60~70%。在本发明中,所述固溶处理的温度为725~875℃,优选为750~850℃,更优选为800℃;所述固溶处理的保温时间优选为4~8h,更优选为5~7h,进一步优选为6h。在本发明中,经过热轧和固溶处理后,γ
‑
ni5si2初生相分布状态和尺寸发生改变,具体为γ
‑
ni5si2初生相尺寸更加细小,形貌趋于椭球形,分布更加弥散且晶界处居多。
[0049]
得到固溶态合金后,本发明将所述固溶态合金依次进行冷轧和时效处理,得到铜镍锡硅合金。在本发明中,所述冷轧的温度优选为室温(20~25℃);所述冷轧的总变形量优选为30~50%,更优选为35~45%,进一步优选为40%。在本发明中,所述时效处理的温度为250~450℃,优选为300~400℃,更优选为350℃;所述时效处理的保温时间优选为0.5~4h,更优选为1~3h,进一步优选为2h。在本发明中,所述时效处理后合金中产生了细小且呈弥散分布的析出相,由于初生相γ
‑
ni5si2的作用,合金中不连续沉淀相的产生得到抑制,从而提高了铜镍锡硅合金的力学性能和耐磨性能。
[0050]
对于铜镍锡硅合金而言,成分设计和组织调控是决定其性能的关键,也直接影响此类合金的实际使用。成分设计:本发明通过模拟计算和实验表征相结合的方法,进行铜镍锡硅合金的成分设计并制备cu
‑
6ni6sn
‑
xsi合金,具体的,采用专业的热力学和动力学计算软件pandat软件进行cu
‑
6ni6sn
‑
xsi合金的模拟相图计算,根据计算结果预测合金的物相组成及在合金的凝固过程中是否会有初生相产生并预测初生相的类型;通过sem、epma及tem等实验表征手段对cu
‑
6ni6sn
‑
xsi合金的组织进行分析,确定合金的物相组成及初生相的类型。组织调控机制:利用进行cu
‑
6ni6sn
‑
xsi合金固溶和时效处理的模拟计算,预测不同温度下合金的物相组成和相转变机制,并通过sem、epma及tem等实验手段进行验证,以此制备的铜镍锡硅合金具有优异的力学性能和摩擦磨损性能。本发明提供的制备方法,操作简便,容易实施,不需要大量的原材料和试验,大大节省了时间,提高效率并降低试验和材
料的成本。
[0051]
本发明提供了上述技术方案所述铜镍锡硅合金或上述技术方案所述制备方法得到的铜镍锡硅合金在高端滑动轴承、航空航天、轨道交通、重载机械或海洋工程中的应用。
[0052]
在本发明中,所制备的cu
‑
6ni
‑
6sn
‑
(0.15~1)si合金可在航空航天中作为起落架、在轨道交通中作为支撑弹簧、在重载机械中作为轴套和衬套、在海洋工程中作为船用柴油发动机的滑动轴承和轴套以及海上石油钻井平台钻井杆的保护套。
[0053]
下面将结合本发明中的实施例,对本发明中的技术方案进行清楚、完整地描述。显然,所描述的实施例仅仅是本发明一部分实施例,而不是全部的实施例。基于本发明中的实施例,本领域普通技术人员在没有做出创造性劳动前提下所获得的所有其他实施例,都属于本发明保护的范围。
[0054]
实施例1
[0055]
铜镍锡硅合金的化学组成设计利用pandat软件进行,打开pandat软件,选取cu,ni,sn,si四种元素,设定ni质量百分含量为6%,sn质量百分含量为6%,si为变量,余量为cu;设定计算温度为300~1200℃;计算相图并输出结果,cu
‑
6ni
‑
6sn
‑
xsi合金的模拟相图结果如图1所示,其中,fcc表示面心立方结构,l表示液相。由图1可知,当si含量超过0.15wt%时,合金在凝固过程中会产生γ
‑
ni5si2相,而且与fcc基体和l相伴生存在,可以从理论上说明γ
‑
ni5si2是初生相,而且可以预测通过固溶处理是消除不掉的。
[0056]
根据图1确定合金组成为6wt%ni,6wt%sn,0.6wt%si和余量铜(记为cu
‑
6ni
‑
6sn
‑
0.6si)。
[0057]
将纯度为99.97%的电解铜、99.8%的镍和99.9%的锡置于中频感应炉的石墨坩埚中进行熔化,待所得熔体温度为1250~1350℃时加入纯度为99.99%的硅,并在此温度下保温熔炼10min,然后得到温度为1200~1250℃的合金液;将所述合金液浇注到预热到300℃的钢模中,冷却至室温后脱模,然后进行表面切割去除缩孔和氧化皮,得到铸态合金。
[0058]
将所述铸态合金在850℃条件下进行热轧,然后在850℃条件下固溶处理6h,得到固溶态合金,其中,热轧的总变形量为50%。
[0059]
将所述固溶态合金在室温条件下进行冷轧,然后在350℃条件下时效处理2h,得到铜镍锡硅合金(记为cu
‑
6ni
‑
6sn
‑
0.6si合金),其中,冷轧的总变形量为30%。
[0060]
本实施例制备的铸态合金的金相图如图2所示,由图2可知,铸态合金的晶粒或枝晶得到了细化,锡元素的严重偏析现象得到了改善,没有出现大量的锡元素偏析产生的富锡相。本实施例制备的铸态合金的sem图和能谱分析结果如图3所示,其中(a)为sem图,a为黑色物相,b为白色物相,c为基体物相;(b)为黑色物相的能谱分析结果,(c)为白色物相的能谱分析结果,(d)为基体物相的能谱分析结果。白色物相b的透射明场像图、选区电子衍射图、高分辨透射电镜图及其傅里叶变换如图4所示,其中,(a)透射明场像图,(b)为选区电子衍射图,(c)为高分辨透射电镜图,(d)为傅里叶变换图。由图3~4可知,铸态合金有明显的两类物相(黑色物相a和白色物相b)分布在基体c上;白色物相的si含量高,且ni和si的原子比接近5:2;黑色物相中sn含量高,可判定为合金在凝固过程中由于sn元素的偏析产生的富sn相;基体中si和sn含量较低,可认定为单相的fcc固溶体。由白色物相的透射电镜图、选区电子衍射、高分辨及其傅里叶变换图可进一步确认和证明白色的物相为初生相γ
‑
ni5si2。
[0061]
本实施例制备的固溶态合金sem图和能谱分析结果如图5所示,其中(a)为sem图,
基体上分布有第二相(eds spot1、eds spot2和eds spot3);(b)为eds spot1的能谱分析结果,(c)为eds spot2的能谱分析结果,(d)为eds spot3的能谱分析结果。eds spot1的透射电镜图、选区电子衍射图、高分辨透射电镜图和傅里叶变换图如图6所示,其中,(a)为第二相的明场像图,(b)为第二相的选区电子衍射图,(c)为高分辨透射电镜图,(d)为傅里叶变换图。由图5~6可知,固溶态合金中依然有其他物相(第二相)分布在基体上;通过能谱结果可知这类物相的si含量较高,而且ni和si的原子比接近5:2;通过图6证明该物相依然是和铸态合金组织中相同的γ
‑
ni5si2相,只是在热轧和固溶处理之后该物相的形态发生了变化;同时,铸态合金组织中由于sn元素偏析产生的富锡相完全消失,即完全固溶到了基体中。因此,γ
‑
ni5si2相是无法通过固溶处理消除掉的初生相。实验结果和利用pandat软件理论模拟计算完全一致。
[0062]
本实施例制备的cu
‑
6ni
‑
6sn
‑
0.6si合金的金相图如图7所示,可见合金经过时效之后没有大量的不连续沉淀γ相出现且晶粒非常细小。本实施例制备的cu
‑
6ni
‑
6sn
‑
0.6si合金的透射电镜图、选区电子衍射图、高分辨透射电镜图和傅里叶变换图如图8所示,其中,(a)为透射明场像图,(b)为选区电子衍射图,(c)为高分辨透射电镜图,(d)为傅里叶变换图。由图8可知,cu
‑
6ni
‑
6sn
‑
0.6si合金的经过时效处理后组织中有明显的细小的析出相产生,通过选取电子衍射、高分辨投射电镜及傅里叶变换图可以判定这类析出相是do
22
型和l12型,并非不连续沉淀γ相。
[0063]
实施例2~5
[0064]
按照实施例1的方法制备铜镍锡硅合金,实施例2~5的制备条件如表1所示。
[0065]
对比例1~7
[0066]
按照实施例1的方法制备铜镍锡硅合金,对比例1~7的制备条件如表1所示。
[0067]
表1实施例1~5和对比例1~7的制备条件
[0068]
[0069][0070]
对比例1制备的铸态合金的金相图如图9所示,由图9可知,铸态合金的晶粒或枝晶比较粗大,且存在大量的由于锡元素的偏析产生的黑色富锡相。对比例1制备的cu
‑
6ni
‑
6sn合金的金相图如图10所示,由图10可知,cu
‑
6ni
‑
6sn合金经过时效处理之后出现了大量的黑色不连续沉淀γ相
[0071]
对比例1制备的cu
‑
6ni
‑
6sn合金的透射明场像图如图11所示,由图11可知,不添加硅的cu
‑
6ni
‑
6sn合金经过时效处理之后出现了大量的不连续沉淀γ相,不连续沉淀γ相会对合金的力学性能及摩擦磨损性能产生严重损害。
[0072]
实施例1制备的cu
‑
6ni
‑
6sn
‑
0.6si合金和对比例1制备的cu
‑
6ni
‑
6sn合金的拉伸试样断口形貌sem图如图12所示,由图12可知,本发明实施例制备的cu
‑
6ni
‑
6sn
‑
0.6si合金断口的韧窝更小更深,也进一步说明其塑性更好。
[0073]
对比例5制备的固溶态合金的金相图如图13所示,由图13可知,当固溶处理时温度为900℃时,cu
‑
6ni
‑
6sn
‑
0.6si合金会出现重熔,对合金的损害是不可逆的,而且会严重影响合金的后续时效处理以及合金的性能。
[0074]
对比例7制备的cu
‑
6ni
‑
6sn
‑
0.6si合金的金相图如图14所示,由图14可知,当时效处理的温度为500℃时会产生大量的不连续沉淀相,进而导致cu
‑
6ni
‑
6sn
‑
0.6si合金的力学性能显著下降。
[0075]
测试例1
[0076]
力学性能和耐磨性测试
[0077]
抗拉强度、屈服强度和断后伸长率测试:室温单轴拉伸实验,测试方法为gb/t 228.1
‑
2010金属材料拉伸试验第1部分:室温试验方法。
[0078]
硬度测试:室温布氏硬度测试,测试方法为gb/t 231.1
‑
2009《金属材料布氏硬度试验第一部分:试验方法》。
[0079]
摩擦系数测试:采用srv
‑
iv微动摩擦磨损试验机,分机将实施例1~5和对比例1~7制备的合金与轴承钢进行往复式摩擦磨损试验,具体步骤为滴2μl润滑油,在加载荷为50n条件下预磨30s,然后将载荷加至150n连续摩擦试验90min。
[0080]
实施例1~5和对比例1~7制备的合金的力学性能和摩擦性能测试结果如表2所示。
[0081]
表2实施例1~5和对比例1~7制备的合金的性能测试结果
[0082][0083]
由表2可知,本发明制备的铜镍锡硅合金的抗拉强度为783~967mpa,屈服强度为712~912mpa,断后伸长率为10~14%,硬度为241~327hb,摩擦系数为0.12~0.15。
[0084]
实施例1制备的cu
‑
6ni
‑
6sn
‑
0.6si合金和对比例1制备的cu
‑
6ni
‑
6sn合金进行室温单轴拉伸试验,为保证试验结果的可靠性,每个合金进行了三组拉伸试验,其中最具代表性的两组对比拉伸曲线如图15所示,平均抗拉强度、平均屈服强度和平均延伸率如表2所述。由此可知,实施例1制备的cu
‑
6ni
‑
6sn
‑
0.6si合金的强度和延伸率均显著高于对比例1制备的cu
‑
6ni
‑
6sn合金。
[0085]
实施例1制备的cu
‑
6ni
‑
6sn
‑
0.6si合金和对比例1制备的cu
‑
6ni
‑
6sn合金进行摩擦磨损试验,为保证试验结果的可靠性,每个合金进行了三组摩擦磨损试验,实验结果如图16和图17所示,其中,图16为实施例1制备的cu
‑
6ni
‑
6sn
‑
0.6si合金三组摩擦磨损试验结果;图17为对比例1制备的cu
‑
6ni
‑
6sn合金三组摩擦磨损试验结果;平均摩擦系数如表2所述。由此可知,实施例1制备的cu
‑
6ni
‑
6sn
‑
0.6si合金的摩擦系数明显低于对比例1制备的cu
‑
6ni
‑
6sn合金。
[0086]
因此,实施例1制备的cu
‑
6ni
‑
6sn
‑
0.6si合金的力学性能和摩擦磨损性能均优于对比例1制备的cu
‑
6ni
‑
6sn合金。
[0087]
以上所述仅是本发明的优选实施方式,应当指出,对于本技术领域的普通技术人员来说,在不脱离本发明原理的前提下,还可以做出若干改进和润饰,这些改进和润饰也应视为本发明的保护范围。
再多了解一些
本文用于企业家、创业者技术爱好者查询,结果仅供参考。