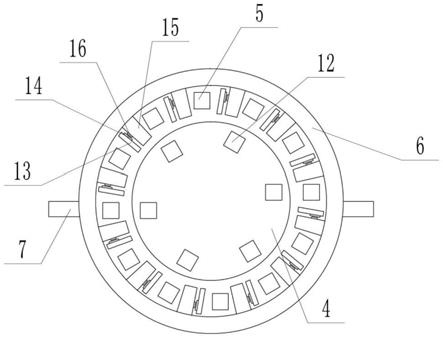
1.本发明属于金属表面处理技术领域,具体涉及用于压铸铝合金的智能表面处理系统及方法。
背景技术:
2.铝合金是以铝为基添加一定量其他合金化元素的合金,是轻金属材料之一,适合压铸工艺的铝就是压铸铝,通常是压铸铝合金。
3.喷砂是用净化压缩空气将玻璃微珠喷到铝制品表面,从而去除表面缺陷的一种机械加工方法,其作用有:去除工件表面的毛刺,铸件熔渣,及其他缺陷和垢物;可强化金属表面,减少应力和疲劳,改善合金机械性能;可使合金表面呈现均匀磨砂效果,表面美观。
4.申请号为cn202011267301.2公开了一种铝合金型材表面处理用喷砂装置,包括喷砂箱,喷砂箱一侧壁上设有物料进口且另外一侧壁上设有物料出口,喷砂箱的物料进口、物料出口之间设有传送网带,喷砂箱内在传送网带上方设有喷砂装置、下方设有铁锈分离装置,铁锈分离装置包括旋转安装的磁选筒,喷砂箱内在物料进口、物料出口端设有两组振荡装置,每组振荡装置均包括设置在传送网带传送方向两侧的振荡板,振荡板与喷砂箱内顶部之间设有弹簧,振荡板正上方设有振荡推杆,振荡推杆连有振荡气缸,振荡板底部通过弹力绳连有振荡弹球。上述能够在对铝合金型材进行喷砂处理的同时,利用铁锈分离装置对砂料和铁屑同步分离,振荡装置起到辅助振荡下料的作用。上述方案在对铝合金进行喷砂时,当工件面积变化时,喷砂装置的喷砂量相同,工件面积较小时,喷砂量较多,会造成喷砂料浪费和增加循环回收系统工作量。
技术实现要素:
5.本方案提供一种可调节喷砂量的用于压铸铝合金的智能表面处理系统及方法。
6.为了达到上述目的,本方案提供一种用于压铸铝合金的智能表面处理系统,包括:机架、工件传送网带、喷砂管、喷砂板与喷砂箱;所述喷砂箱一侧壁上设有物料进口且相对的另外一侧壁上设有物料出口;所述喷砂箱的物料进口和物料出口之间设有工件传送网带;所述喷砂板与喷砂箱内壁固定连接,喷砂板位于工件传送网带上方;还包括:旋转块、旋转轴、带动旋转轴转动的电机、图像采集模块、图像分析模块与plc控制器;所述图像采集模块用于采集工件信息,并将工件信息发送到图像分析模块;所述图像分析模块用于接收图像采集模块的工件信息,提取工件面积信息并将工件与存储在图像分析模块中的喷砂板面积信息进行对比,并生成调节信息发送到plc控制器;所述plc控制器与电机电连接;所述电机固定安装在喷砂箱顶部;所述旋转轴穿过喷砂箱与电机输出轴固定连接;所述喷砂板与旋转块转动连接,旋转块位于喷砂板外侧;所述旋转块与旋转轴固定连接;所述喷砂板分为内板与外板,内板上设有若干个第二通孔,第二通孔处安装有第二喷砂嘴,外板上设有若干个第一通孔,第一通孔处安装有第一喷砂嘴;所述第一喷砂嘴与第二喷砂嘴均与喷砂管连通;所述旋转块上设有若干个用于打开和关闭第一喷砂嘴的挡板,挡板与第一喷砂嘴位置
相配合;所述第一喷砂嘴远离挡板一端设有压力传感器,压力传感器与plc控制器电连接;所述plc控制器根据调节信息控制打开电机,然后根据压力传感器数值控制关闭电机和打开喷砂管。
7.本方案原理:工件传送网带将工件从喷砂箱的物料进口传送到物料出口处,在这个过程中图像采集模块采集工件信息,并将工件信息发送到图像分析模块,图像分析模块提取工件信息分析提取出工件面积,根据工件面积与喷砂板面积对比,当工件板面积小于喷砂板内板面积时,图像分析模块向plc控制器发送调节信息,plc控制器控制电机反转,电机带动旋转轴与旋转块转动,旋转块带动挡板转动,挡板挡住第一喷砂嘴,从而改变工件的喷砂量和喷砂面积,当第一喷砂嘴上压力传感器感受有数值后,压力传感器使plc控制器使电机停止转动,调节好后打开喷砂管对工件进行喷砂加工。
8.本方案有益效果:通过采集工件信息改变喷砂嘴数量,从而改变工件喷砂量和喷砂面积,使工件的喷砂效果更好;同时节约砂料减轻砂料循环回收的压力。
9.进一步,所述喷砂板设有定位块,定位块上设有第一磁体;所述挡板上设有第二磁体,第二磁体与第一磁体相互吸引。通过第二磁体与第一磁体相互吸引固定住挡板,防止喷砂嘴进行喷砂时,挡板晃动挡住第一喷砂嘴,影响工件喷砂效果。
10.进一步,所述第二磁体与第一磁体相对面设有橡胶垫,橡胶垫位于第二磁体边缘处。橡胶垫位于边缘处,不会影响磁体间相互吸引,同时可以第二磁体移动时,防止磁体间相碰撞,减小损伤;还可以使磁体容易相互脱离。
11.进一步,所述挡板与旋转块可拆卸连接。在长期使用后,挡板容易在砂料冲击下损坏,方便更换挡板。
12.进一步,所述喷砂料为玻璃珠,玻璃珠直径不大于5mm。玻璃珠透明、清晰的球状结构产品在使用时不会有粒子嵌入工件、污染工件或产生其它损坏。
13.进一步,还包括限位杆;所述旋转轴上设有第一凹槽;所述喷砂箱表面设有若干个第二凹槽;所述限位杆位一端位于第一凹槽内,限位杆另外一端位于第二凹槽内。限位杆用于限制旋转轴继续转动,影响喷砂效果。
14.进一步,所述喷砂箱上设有透明玻璃窗。方便看到工件加工状态,可以方便对喷砂系统进行调整,使喷砂效果更好。
15.为了达到上述目的,本方案提供一种用于压铸铝合金的智能表面处理方法,包括:步骤一:将工件放置到工件传送网带上,启动工件传送网带;步骤二:图像采集模块采集工件信息发送到图像分析模块;步骤三:图像分析模块获取图像采集模块工件信息,分析得到工件面积信息,对比喷砂块面积信息获得调节信号,并将调节信号发送到plc控制器;步骤四:plc控制器控制电机转动,电机转动带动挡板控制第一喷砂嘴的打开和关闭;步骤五:打开喷砂管对工件进行喷砂加工。
附图说明
16.图1为本发明实施例1的结构示意图。
17.图2为本发明实施例1的喷砂板与旋转块的仰视图。
18.图3为本发明实施例2的钝化处理子系统结构示意图。
19.图4为本发明实施例2的高硅压铸铝合金的钝化膜表面形貌。
20.图5为本发明实施例2图4钝化膜的截面形貌。
具体实施方式
21.下面通过具体实施方式进一步详细的说明:说明书附图中的附图标记包括:机架1、工件传送网带2、喷砂箱3、喷砂板4、第一喷砂嘴5、旋转块6、旋转轴7、连接架8、支撑板9、电机10、喷砂管11、第二喷砂嘴12、定位块13、第一磁体14、挡板15、第二磁体16、加工台17、钝化液箱18、水箱19、流量控制管20、第一电动针阀21、混合管22、喷头23、湿度传感器24、锌溶液箱25、冷风机26。
22.实施例1:用于压铸铝合金的智能表面处理系统,如附图1所示,包括:机架1、工件传送网带2、喷砂管11、喷砂板4与喷砂箱3,喷砂箱3一侧壁上设有物料进口且相对的另外一侧壁上设有物料出口,喷砂箱3的物料进口和物料出口之间设有工件传送网带2,喷砂箱3底部设有开口,喷砂箱3底部设有密封块,密封块用于封住开口,喷砂箱3底部可以用于收集对工件加工后从工件传送网带2掉落的喷砂料,然后对喷砂料与杂质进行分离,循环使用喷砂料。喷砂料为玻璃珠,玻璃珠的直径不大于5mm。玻璃珠透明、清晰的球状结构产品在使用时不会有粒子嵌入工件、污染工件或产生其它损坏。
23.如附图2所示,还包括:旋转块6、旋转轴7、带动旋转轴7转动的电机10、图像采集模块、图像分析模块与plc控制器。喷砂箱3顶部焊接有支撑板9,支撑板9为倒l形,电机10焊接在支撑板9上。电机10为16mm直流减速电机,额定转速为50
‑
400(rpm)。
24.电机10输出轴与旋转轴7通过连接架8焊接在一起,旋转轴7穿过喷砂箱3与连接架8焊接在一起。喷砂板4与旋转块6转动连接,旋转块6位于喷砂板4外侧,旋转块6与旋转轴7焊接在一起,旋转轴7数量为两个,可以使旋转块6转动时更加稳定。
25.喷砂板4与喷砂箱3内壁通过连接块焊接在一起,喷砂板4位于工件传送网带2上方。喷砂板4分为内板与外板,内板上设有若6个第二通孔,第二通孔处均安装有第二喷砂嘴12,外板上设有12个第一通孔,第一通孔处均安装有第一喷砂嘴5,第一喷砂嘴5与第二喷砂嘴12均与喷砂管11连通;旋转块6上设有若干个用于打开和关闭第一喷砂嘴5的挡板15,挡板15与第一喷砂嘴5位置相配合。挡板15与旋转块6可拆卸连接。在长期使用后,挡板15容易在砂料冲击下损坏,方便更换挡板15。第一喷砂嘴5远离挡板15一端设有压力传感器,压力传感器通过螺栓固定在第一喷砂嘴5表面,压力传感器与plc控制器电连接。压力传感器为bf350
‑
3aa应变计用压力传感器。
26.喷砂板4焊接有定位块13,定位块13上焊接有第一磁体14,挡板15上焊接有第二磁体16,第二磁体16与第一磁体14相互吸引。通过第二磁体16与第一磁体14相互吸引固定住挡板15,防止喷砂嘴进行喷砂时,挡板15晃动挡住第一喷砂嘴5,影响工件喷砂效果。第二磁体16与第一磁体14相对面设有橡胶垫,橡胶垫位于第二磁体16边缘处。橡胶垫位于边缘处,不会影响磁体间相互吸引,同时可以第二磁体16移动时,防止磁体间相碰撞,减小损伤;还可以使磁体容易相互脱离。
27.图像采集模块用于采集工件信息,并将工件信息发送到图像分析模块,本实施例中采用hikvision网络摄像头对施工现场进行拍照,网络摄像头有两个,可以多角度对施工现场进行拍照,进行多方位信息采集,使用照片建模时更加准确,获取的工件信息更加准
确。工件信息为工件照片。
28.图像分析模块用于接收图像采集模块的工件信息,提取工件面积信息并将工件与与存储在图像分析模块中的喷砂板4面积信息进行对比,并生成调节信息发送到plc控制器。 plc控制器与电机10电连接,具体的控制器采用stm32f103c8t6的单片机。plc控制器控制电机10转动,第一喷砂嘴5远离挡板15一端设有压力传感器,压力传感器与plc控制器电连接。
29.工件传送网带2将工件从喷砂箱3的物料进口传送到物料出口处,在这个过程中图像采集模块采集工件信息,图像分析模块提取工件信息分析提取出工件面积,根据工件面积与喷砂板4面积对比,plc控制器控制电机10反转,电机10带动旋转轴7与旋转块6转动,旋转块6带动挡板15转动,挡板15挡住第一喷砂嘴5,从而改变工件的喷砂量和喷砂面积。通过采集工件信息改变喷砂嘴数量,从而改变工件喷砂量和喷砂面积,使工件的喷砂效果更好;同时节约砂料减轻砂料循环回收的压力。
30.还包括限位杆,旋转轴7上设有第一凹槽,喷砂箱3表面设有若干个第二凹槽,限位杆位一端位于第一凹槽内,限位杆另外一端位于第二凹槽内。限位杆用于限制旋转轴7继续转动,影响喷砂效果。
31.喷砂箱3上设有透明玻璃窗。方便看到工件加工状态,可以方便对喷砂系统进行调整,使喷砂效果更好。
32.本方案还提供一种用于压铸铝合金的智能表面处理方法,具体步骤如下:步骤一:将工件放置到工件传送网带2上,启动工件传送网带2;步骤二:图像采集模块采集工件信息发送到图像分析模块;步骤三:图像分析模块获取图像采集模块工件信息,分析得到工件面积信息,对比喷砂块面积信息获得调节信号,并将调节信号发送到plc控制器;步骤四:plc控制器控制电机10转动,电机10转动带动挡板15控制第一喷砂嘴5的打开和关闭;步骤五:打开喷砂管11对工件进行喷砂加工。
33.本方案操作方法:工件传送网带2将工件从喷砂箱3的物料进口传送到物料出口处,在这个过程中图像采集模块采集工件信息,并将工件信息发送到图像分析模块,图像分析模块提取工件信息分析提取出工件面积,根据工件面积与喷砂板4面积对比,当工件板面积小于喷砂板4内板面积时,图像分析模块向plc控制器发送调节信息,plc控制器控制电机10反转,电机10带动旋转轴7与旋转块6转动,旋转块6带动挡板15转动,第一磁体14与第二磁体16在电机10作用下相脱离,当压力传感器有数值时,plc控制电机10停止转动,然后操作人员使用限位杆,使限位杆一端位于第一凹槽内,另外一端位于第二凹槽内,防止挡板15会晃动影响阻挡第一喷砂嘴5,影响喷砂效果。挡板15挡住第一喷砂嘴5,从而改变工件的喷砂量和喷砂面积。本方案通过采集工件信息改变喷砂嘴数量,从而改变工件喷砂量和喷砂面积,使工件的喷砂效果更好;同时节约砂料减轻砂料循环回收的压力;自动控制喷砂量与喷砂面积,减少工作人员工作量。
34.实施例2:本实施例与实施例1不同之处在于,还包括钝化处理子系统,如附图3所示,本实施例压铸铝合金为高硅压铸铝合金,具体包括:钝化液箱18与水箱19,机架1上焊接有加工台
17,加工台17上放置有工件。机架1上焊接有支架,支架位于加工台17正上方,支架上设有两个放置槽,放置槽用于放置钝化液箱18与水箱19,钝化液箱18填充有钝化原液,在使用时,需要对钝化液原液进行稀释使用。支架上设有凹槽,凹槽内安装有流量控制管20和混合管22,流量控制管20两端分别与钝化液箱18和水箱19连通,流量控制管20与钝化液箱18和水箱19连通处均设有第一电动针阀21,第一电动针阀21用于控制钝化液或者水的量。流量控制管20水平安装在凹槽中,流量控制管20为v形,混合管22竖直安装在凹槽中,可以方便钝化液和水在混合管22进行充分混合,不需要搅拌轴等进行搅拌。混合管22连通有喷头23,喷头23用于向工件喷洒稀释后的钝化液。机架1上螺栓安装有湿度传感器24,具体采用安科瑞whd48
‑
11温湿度传感器24,机架1上螺栓安装有plc控制器, plc控制器和湿度传感器24与第一电动针阀21均电连接。通过湿度传感器2410检测环境湿度,湿度传感器24使plc控制器对第一电动针阀21进行控制,当湿度传感器2410检测到环境湿度小于设定值时,此时环境比较干燥,plc控制器控制第一电动针阀21调大截面面积,使通过的水流变大,改变钝化液的稀释程度,增加雾状药液中水含量,通过改变水雾中水含量防止药液接触工件3时成为半固态影响;当湿度传感器24检测到环境湿度大于设定值时,此时环境比较湿润,plc控制器控制第一电动针阀21调小截面面积,使通过的水流变小,改变钝化液的稀释程度,减少雾状药液中水含量,减少废液量,减少废液循环回收工作量。
35.所述机架1上设有锌溶液箱25,锌溶液箱25与流量控制管20连通,锌溶液箱25与流量控制管20连通处设有第二电动针阀,第二电动针阀与plc控制器电连接。所述机架1上设有定时器,plc控制器与定时器电连接。还包括图像识别模块,所述图像识别模块用于采集识别高硅压铸铝合金信息,并发送添加信号到plc控制器;所述plc控制器接收添加信息,用于控制打开定时器,并根据定时器数据进行调整第二电动针阀添加锌溶液到流量控制管20中,plc控制器在打开第二电动针阀设定时间后控制定时器清零并打开冷风机26对钝化后的高硅压铸铝合金进行干燥。
36.锌溶液箱25放置在支架上的凹槽内,凹槽对锌溶液箱25进行限位。锌溶液为氧化锌溶液,锌溶液箱25底部设有出口,出口处连通有添加管道,添加管道另外一端与流量控制管20连通,控制锌溶液箱25的第二电动针阀位于锌溶液箱25的开口处,防止在不需要添加锌溶液时,锌溶液残留在添加管道内,影响锌溶液效果。定时器螺栓安装在机架1上,具体采用hh系列的时间控制器,具体规格为hh4
‑
4rn。冷风机26具体型号为 hag
‑
p30a
‑
43。图像采集识别模块包括摄像头,采用hikvision网络摄像头,图像采集识别模块采集高硅压铸铝合金图片并根据存储的高硅压铸铝合金图片判断加工台17上是否有高硅压铸铝合金然后发送是否添加锌溶液信息到plc控制器中,plc控制器根据图像采集识别模块信息控制打开定时器,并根据定时器数据在进行调整第二电动针阀添加锌溶液到流量控制管20中,plc控制器在打开锌溶液箱25的第二电动针阀设定时间50s后关闭此第二电动针阀,并控制定时器清零和打开冷风机26对钝化后的高硅压铸铝合金进行干燥,冷风机26与高硅压铸铝合金间距为20cm
‑
30cm,冷风机26的冷风控制在10℃
‑
15℃。
37.高硅压铸铝合金钝化膜在钝化阶段加入含锌溶液后,钝化膜的表面如附图4所示,膜层表面散乱分布着纵横交叉的微裂纹,具体原因为,钝化阶段基本可分为四个阶段,铝合金表层的溶解、膜层迅速生长、膜层缓慢增长和膜层的生长与溶解平衡,在增加氧化锌后,由于锌和铝的金属活动性相近,且锌和铝的氢氧化物性质也相近,在膜层迅速生长阶段,锌
和铝能够和各自的氢氧化物/氧化物在工件表面形成钝化膜(的内膜),能够保证这个阶段钝化膜的稳定性,在锌被消耗之后,由于钝化膜的组成成分的变化以及内部应力的累积,会导致钝化膜(的外膜)表面形成纵横交叉的微裂纹;如果在钝化阶段不加入含锌溶液,那么钝化膜的膜层表面形成的微裂纹较少,不便于后续上漆处理(即存在漆膜与钝化膜的膜层不紧凑,在恶劣使用环境下,如温度骤然变化等,易出现分层、脱离等严重质量问题)。
38.本实施例在钝化膜在钝化处理后(50s),迅速进行干燥,由于刚形成的钝化膜的膜层的内应力还依然存在,膜层受热后会产生微小的形变(即微小的收缩,采用冷风进行膜层干燥,冷风可以去除膜层表面水分,同时膜层受冷收缩),这种形变(或者说收缩)会使得前面在钝化膜膜层表面产生的微裂纹的深度增加(提升后续漆膜与钝化膜的结合强度),形成这种裂纹状表面形貌,如附图5所示。附图5为附图4中钝化膜截面,从附图5中可以看出,钝化膜里层结构致密,没有开裂的现象,说明微裂纹仅存在于膜层表面,并未贯穿整个钝化膜(保证了钝化膜的功能性)。所以钝化膜表面即使存在大量的裂纹,钝化膜仍是完整的,其耐蚀性并没有因为裂纹的存在而变差。
39.在硅压铸铝合金钝化膜在钝化阶段通过添加锌溶液,使锌促进钝化膜的成膜反应,h
被大量消耗,使高硅压铸铝合金钝化过程中反应界面oh
‑
浓度升高,多种氢氧化物在锌层表面沉积形成钝化膜,膜层在干燥过程中,部分氢氧化物脱水形成氧化物,使外层钝化膜中各组成成分分布更加均匀,氢氧化物含量较多,膜层结构更紧凑,能够起到良好的阻挡层作用,有效地提高高硅压铸铝合金的耐蚀性,同时使用距工件20cm
‑
30cm冷风机26吹10℃
‑
15℃的风让钝化膜表面形成微裂纹扩大,提高钝化膜与漆膜的结合力,提高高硅压铸铝合金的耐腐蚀性能。
40.以上所述的仅是本发明的实施例,方案中公知的具体结构及特性等常识在此未作过多描述。应当指出,对于本领域的技术人员来说,在不脱离本发明结构的前提下,还可以作出若干变形和改进,这些也应该视为本发明的保护范围,这些都不会影响本发明实施的效果和专利的实用性。本技术要求的保护范围应当以其权利要求的内容为准,说明书中的具体实施方式等记载可以用于解释权利要求的内容。
再多了解一些
本文用于企业家、创业者技术爱好者查询,结果仅供参考。