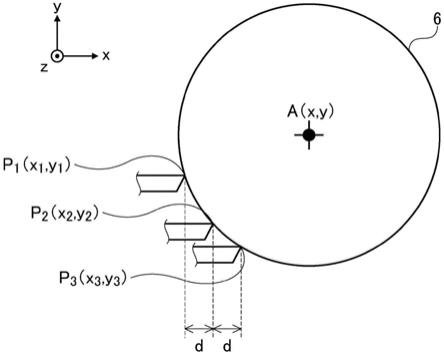
1.本公开涉及使用切削刀具来切削被切削材料(工件)的切削装置。
背景技术:
2.以往,作为切削装置中的原点设定的方法,进行了利用测定器测定切削刀具的刀尖位置并调整刀尖位置的处理。另外,作为其他方法,还进行了以下处理:利用切削刀具对被切削材料进行一次加工,利用测定器测定加工后的被切削材料的形状,并根据测定结果修正刀尖位置。这些都是利用测定器的原点设定方法。
3.专利文献1公开了检测与安装于加工机的主轴的旋转刀具的接触的接触检测装置。该接触检测装置具备能够与旋转刀具接触的圆板状的接触件(probe,探针)、以及检测接触件与旋转刀具接触时的接触振动的振动传感器。通过使旋转刀具与接触件的平面部和侧面部接触,来测定旋转刀具的长度和外径,从而掌握旋转刀具的准确的位置。
4.专利文献2公开了一种刀具位置控制方法,使切削刀具的刀尖与被接触物相对移动而使两者接触,基于接触时的移动装置的移动位置,来控制后续的刀具与被加工物的相对移动。在该方法中,利用当刀尖与被接触物接触时电路闭合而电流流过的现象来检测此时的切削刀具移动装置的位置。所检测的位置成为之后的切削刀具的移动控制的基准位置。
5.专利文献3公开了以下技术:对从x轴伺服单元输入的位置偏差与位置偏差基准值设定单元所设定的基准值进行比较,在位置偏差超过了基准值时,判断工件与探针的接触。
6.(现有技术文献)
7.(专利文献)
8.专利文献1:日本特开2004
‑
90199号公报
9.专利文献2:日本特开2002
‑
120130号公报
10.专利文献3:日本特开2009
‑
34738号公报
技术实现要素:
11.(发明所要解决的问题)
12.以原点设定为目的,设置测定刀尖位置、加工后的被切削材料形状等的测定器,则成本高而不优选。因此,希望无需使用测定器,而实现高精度的原点设定。
13.本公开是鉴于上述情况而完成的,其目的之一在于,提供一种无需附加测定器而确定刀具刀尖与被切削材料等的对象物的相对位置关系的技术、或者为了确定两者的相对位置关系而所需的技术。
14.(解决问题所采取的措施)
15.为了解决上述课题,本发明的一个实施方式的切削装置具备:旋转机构,使安装有切削刀具或被切削材料的主轴旋转;进给机构,使切削刀具相对于被切削材料或部件相对移动;以及控制部,控制基于旋转机构的主轴的旋转及基于进给机构的切削刀具的相对移
动。控制部具有如下功能:利用接触传感器的检测信息、或者与旋转机构和/或进给机构所包含的驱动电机相关的检测值的时序数据来获取切削刀具与被切削材料或部件接触时的坐标值。控制部根据切削刀具在与车削加工时的切削刀具的旋转角度位置不同的至少两个位置与基准面接触时的坐标值来确定切削刀具与被切削材料的旋转中心的相对位置关系,其中,所述基准面与车削加工后的被切削材料或与被切削材料的旋转中心的相对位置关系已知。
16.本发明的另一个实施方式也是一种切削装置。该切削装置具备:旋转机构,使安装有切削刀具或被切削材料的主轴旋转;进给机构,使切削刀具相对于对象物相对移动;以及控制部,控制基于旋转机构的主轴的旋转及基于进给机构的切削刀具的相对移动。控制部具有如下功能:使切削刀具相对于具有已知形状的物体相对移动,并利用接触传感器的检测信息、或者与旋转机构和/或进给机构所包含的驱动电机相关的检测值的时序数据来获取切削刀具的刀尖与物体的已知形状部分接触时的坐标值。控制部根据切削刀具的刀尖在物体的已知形状部分的至少三个位置接触时的坐标值来求出刀具刀尖的刀尖半径、刀具刀尖的中心坐标、刀具刀尖的形状误差中的至少一个。
17.本发明的另一个实施方式也是一种切削装置。该切削装置具备:旋转机构,使安装有切削刀具或被切削材料的主轴旋转;进给机构,使切削刀具相对于被切削材料相对移动;以及控制部,控制基于旋转机构的主轴的旋转及基于进给机构的切削刀具的相对移动。控制部具有如下功能:利用接触传感器的检测信息、或者与旋转机构和/或进给机构所包含的驱动电机相关的检测值的时序数据来获取切削刀具与被切削材料接触时的坐标值。控制部利用在切削加工时未利用的移动方向的基于进给机构的进给功能而使切削刀具相对于切削加工后的被切削材料相对移动,并根据切削刀具在至少两个位置接触时的坐标值来确定切削刀具的安装误差、刀具刀尖的形状误差、切削刀具相对于被切削材料的相对移动方向的偏差中的至少一个。
18.本发明的另一个实施方式也是一种切削装置。该切削装置具备:旋转机构,使安装有切削刀具或被切削材料的主轴旋转;进给机构,使切削刀具相对于被切削材料相对移动;以及控制部,根据与旋转机构和/或进给机构所包含的驱动电机相关的检测值的时序数据来确定切削刀具与被切削材料的接触位置。控制部根据接触前所获取的检测值的第一时序数据和接触后所获取的检测值的第二时序数据来确定接触位置。
19.需要说明的是,以上的构成要素的任意组合、将本公开的表现形式在方法、装置、系统、记录介质、计算机程序等之间进行变换后的实施方式,作为本公开的实施方式也是有效的。
20.(发明的效果)
21.根据本公开,能够提供一种确定刀具刀尖与对象物的相对位置关系的技术、或者确定两者的相对位置关系而所需的技术。
附图说明
22.图1是示出切削装置的概略结构的图。
23.图2是示出关于接触检测方法的实验的概要的图。
24.图3是示出刀尖与工件接触而切入的状态的图。
25.图4是示出实验中的与进给轴相关的内部信息的时间变化的图。
26.图5是示出实验中的与主轴旋转轴相关的内部信息的时间变化的图。
27.图6是示出刀尖的切入量的时间变化的图。
28.图7是示出基于外部传感器的切削力的主分力的检测值的变化的图。
29.图8是示出转矩输出的检测值的变化的图。
30.图9是示出对主分力的检测值进行信号处理而除去了干扰的主分力变化的图。
31.图10是示出对转矩检测值进行信号处理而除去了干扰的转矩变化的图。
32.图11是用于说明确定切削刀具与被切削材料旋转中心的相对位置关系的方法的图。
33.图12是示出a点坐标的导出方法的图。
34.图13是用于说明基准面的图。
35.图14是示出将切削刀具以能够c轴旋转的方式安装的切削装置的一例的图。
36.图15是示出刀尖与基准块的已知形状部分接触的情况的图。
37.图16是示出刀尖与基准块的位置关系的图。
38.图17是示意性地示出与基准块的上表面接触时的切削刀具的倾斜状态的图。
39.图18是示出接触位置的高度变化的图。
40.图19是示出将切削刀具以能够c轴旋转的方式安装的切削装置的另一例的图。
41.图20是示出刀尖与基准块的已知形状部分接触的情况的图。
42.图21是示出刀尖与基准块的位置关系的图。
43.图22是示出使基准块的已知形状的部分与刀尖接触的状态的图。
44.图23是示出对被切削材料进行加工的情况的图。
45.图24是用于说明导出刀具中心的安装误差的方法的图。
46.图25是用于说明确定刀具刀尖的形状误差的方法的图。
47.图26是用于说明确定被切削材料旋转轴与刀具直进轴的平行度的方法的图。
48.图27是用于说明确定被切削材料旋转轴与刀具直进轴的正交度的方法的图。
49.图28是用于说明推定刀具中心的安装误差的方法的图。
50.图29是用于说明推定刀具中心的安装误差的方法的图。
51.图30是用于说明推定刀具中心的安装误差的方法的图。
52.图31是用于说明导出b轴旋转中心的方法的图。
53.图32是概念性地示出扫描线加工中的切削进给方向和周期进给方向的图。
54.图33是用于说明推定刀具中心的安装误差的方法的图。
55.图34是用于说明推定刀具中心的安装误差的方法的图。
56.图35是示出测定刀尖形状误差的方法的图。
57.图36是示出由直线切削刃进行加工的情况的图。
58.图37是用于说明识别方法(identify method)的图。
59.图38是用于说明坐标变换的图。
60.图39是示出使刀尖与加工面接触的状态的图。
61.图40是示出球头立铣刀的两种不同姿态的图。
62.图41是用于说明确定偏心量的方法的图。
63.图42是用于说明确定b轴旋转中心的偏差量的方法的图。
64.图43是用于说明确定距x轴与z轴间的直角的偏差量的方法的图。
65.图44是概念性地示出扫描线加工中的切削进给方向和周期进给方向的图。
66.图45是用于说明推定刀具中心的安装误差的方法的图。
67.图46是用于说明推定刀具中心的安装误差的方法的图。
68.图47是示出测定刀尖形状误差的方法的图。
具体实施方式
69.图1示出实施方式的切削装置1的概略结构。图1所示的切削装置1是使切削刀具11的刀尖11a与被切削材料6接触而进行车削加工的切削装置。切削装置1可以是nc机床。图1所示的切削装置1是对圆筒状的被切削材料6进行车削而加工轧制用轧辊的轧辊车床,但也可以是车削以外的其他类型的切削装置,例如也可以是使用立铣刀等的旋转刀具的切削装置。
70.切削装置1在床身5上具备可旋转地支承被切削材料6的主轴台2和尾座3,以及支承切削刀具11的刀架4。旋转机构8设置在主轴台2的内部而使安装有被切削材料6的主轴2a旋转。进给机构7设置在床身5上而使切削刀具11相对于被切削材料6相对地移动。在该切削装置1中,进给机构7使刀架4在x轴、y轴、z轴方向移动,由此使切削刀具11相对于被切削材料6相对地移动。
71.在图1中,x轴方向是水平方向且是与被切削材料6的轴方向正交的切入方向,y轴方向是作为铅直方向的切削方向,z轴方向是与被切削材料6的轴方向平行的进给方向。需要说明的是,在图1中,x轴、y轴、z轴的正负表示从切削刀具11侧观察的方向,但由于在切削刀具11与被切削材料6之间正负方向是相对的,因此在本说明书中,并没有特别严格地定义各轴的正负方向,在提及正负方向时遵循各图所示的方向。
72.控制部20具备:旋转控制部21,控制由旋转机构8进行的主轴2a的旋转;移动控制部22,在主轴2a的旋转过程中通过进给机构7使切削刀具11与被切削材料6接触而进行基于切削刀具11的加工;以及位置关系导出部23,导出被切削材料6与切削刀具11的相对位置关系。移动控制部22以刀尖11a的坐标为基准控制切削刀具11的移动也可。旋转机构8和进给机构7分别具有驱动电机等的驱动部而构成,旋转控制部21和移动控制部22分别调整向驱动部的供给电力而控制旋转机构8和进给机构7各自的动作。
73.在实施方式的切削装置1中,被切削材料6安装于主轴2a而在旋转机构8的作用下旋转,但在其他例子中,也可以将作为旋转刀具的切削刀具安装于主轴2a而在旋转机构8的作用下旋转。另外,进给机构7只要使切削刀具11相对于被切削材料6相对移动即可,只要具有使切削刀具11或被切削材料6中的至少一方移动的机构即可。
74.另外,进给机构7不限于x轴、y轴、z轴的平移方向的进给功能,还可以具有a轴、b轴、c轴的旋转方向的进给功能。优选地,实施方式的进给机构7不仅具有切削加工时所需的移动方向的进给功能,还具有在切削加工时未利用的移动方向的进给功能。即,进给机构7可构成为除了在切削加工时利用的方向的进给功能以外,还具有在切削加工中不需要的(所谓的冗余的)移动方向的进给功能。冗余的方向的进给功能可以在使切削刀具11相对于后述的预加工面相对移动时利用。
75.在更换刀具时等将切削刀具11重新安装于切削装置1时,为了使移动控制部22发挥高的移动精度(加工精度),需要适当地实施原点设定而确定刀尖11a的准确的坐标值。在实施方式中,在进行原点设定时,移动控制部22使刀尖11a移动而与对象物(例如预加工后的被切削材料6)接触,确定所接触的时刻(timing),并根据此时的移动控制部22的控制信息来确定接触位置。因此,切削装置1可以具有用于检测刀尖11a与对象物接触的接触传感器。接触传感器例如可以是用于检测接触时的振动的振动传感器、或用于检测刀尖与对象物接触时的导通的传感器。
76.需要说明的是,实施方式的切削装置1也可以搭载以下功能:分析刀尖11a与对象物接触时发生变化的切削装置1的内部信息的历史记录而检测刀尖11a与对象物的接触。作为内部信息利用与旋转机构8和/或进给机构7所包含的驱动电机相关的检测值,据此不必追加新的部件。在切削装置1搭载了该功能的情况下,不需要用于检测接触的传感器,但也可以以提高接触检测精度为目的而设置接触传感器。
77.图2示出关于接触检测技术的实验的概要。该实验是为了验证利用了内部信息的接触检测方法而实施的实验,原点设定是以实施完成为前提。工件w使用h3250 c4641be(海军黄铜(naval brass))且直径为70mm的圆棒。在实验中,旋转控制部21使安装有工件w的主轴以120rpm的旋转速度旋转。移动控制部22以0.2mm/rev的进给速度使切削刀具11接近而切削至0.1mm的切入深度后,以相同的进给速度拉开。图3示出刀尖11a与工件w接触而切入的状态。
78.图4示出实验中的与进给轴相关的内部信息的时间变化。移动控制部22在时间t2开始切削刀具11的进给,以0.2mm/rev的恒定的进给速度在切入方向进给切削刀具11并切削到0.1mm的深度(时间t3)。然后,移动控制部22以0.2mm/rev的进给速度拉开切削刀具11。
79.图5示出实验中的与主轴旋转轴相关的内部信息的时间变化。旋转控制部21在时间t1开始主轴的旋转。旋转速度为120rpm。
80.图6示出刀尖的切入量的时间变化。根据图4所示的进给轴的内部信息计算出切入量。
81.图7示出基于外部传感器的切削力的主分力的检测值的变化。在该实验中所使用的切削装置搭载有用于检测切削力的外部传感器,在图7中示出了外部传感器所检测出的切削力的时间变化。
82.图8示出转矩输出的检测值的变化。转矩检测值是利用切削装置所搭载的推定功能而被计算。转矩值与电机电流值成比例,切削装置获取主轴的驱动电机的电机电流而计算转矩输出。
83.图7所示的主分力的波形与图8所示的转矩值的波形大致一致。因此,可知通过分析转矩输出(电机电流),来能够检测工件w与切削刀具11的接触。
84.图9示出对主分力的检测值进行信号处理而除去了干扰的主分力变化。
85.图10示出对转矩检测值进行信号处理而除去了干扰的转矩变化。通过除去干扰,来能够提高转矩检测值的时序数据的可靠性。
86.以下,示出控制部20根据信号处理后的转矩检测值的时序数据来判断切削刀具11与工件w的接触的方法。需要说明的是,控制部20也可以利用信号处理前的转矩检测值的时序数据来判断接触。实施方式的位置关系导出部23具有根据与旋转机构8和/或进给机构7
所包含的驱动电机相关的检测值的时序数据来确定接触位置的功能。
87.在基于移动控制部22的切削刀具11的进给结束后,位置关系导出部23获取图10所示的转矩推定值的时序数据而确定在接触前所获取的检测值的第一时序数据和在接触后所获取的检测值的第二时序数据。此时,由于位置关系导出部23没有掌握接触的时刻,因此基于以下基准来确定第一时序数据和第二时序数据。
88.如图5所示,旋转控制部21从时间t1开始主轴的旋转,如图4所示,移动控制部22从时间t2开始切削刀具11的进给。因此,在时间t1到t2之间,主轴处于旋转中,并且切削刀具11确实处于未接触的状态。因此,位置关系导出部23将在时间t1到t2之间所计算出的转矩检测值的时序数据确定为接触前的第一时序数据。需要说明的是,即使是切削刀具11的进给开始之后、即时间t2之后,只要是接触前的确实的时间段,则在该时间段所获取的转矩检测值也可包含于第一时序数据中。
89.位置关系导出部23计算所确定的第一时序数据的平均值m1和标准差σ1。在该实验中,计算得到:
90.m1=0.1045
91.σ1=0.0043。
92.在图10中,线l1表示接触前的转矩平均值m1,线l2表示平均值m1 2σ1,线l3表示m1‑
2σ1。
93.接下来,位置关系导出部23确定接触后所获取的转矩检测值的第二时序数据。位置关系导出部23可以将超过了规定的阈值的转矩检测值的时序数据确定为第二时序数据。位置关系导出部23可以基于第一时序数据来设定规定的阈值。例如,位置关系导出部23将规定的阈值设定为(m1 3σ1),并将超过了该阈值的转矩检测值的连续时序数据确定为第二时序数据。需要说明的是,在确定第二时序数据时,对于包含以规定比率(例如2%)以下阈值不满的转矩检测值的时间段,可以将其作为实质上超过了阈值的时间段而包含于第二时序数据中。位置关系导出部23将从时间t3往前倒(追溯)而转矩检测值成为(m1 3σ1)以下的时间为止的时间段内的转矩检测值确定为第二时序数据。
94.位置关系导出部23根据对第二时序数据进行回归分析而求出的回归方程和第一时序数据的平均值,来计算刀尖11a与工件w接触的时刻。作为回归分析的方法,利用适当的方法即可,例如位置关系导出部23通过最小二乘法导出第二时序数据的回归方程和标准差σ2,并求出该回归方程与转矩平均值m1的交点。在该实验中,由下式计算得到:
95.[数学式1]
[0096]
一次近似直线y=0.3068
×
x
‑
2.4155
[0097]
σ2=0.0031。
[0098]
x轴是时间,y轴是转矩输出。需要说明的是,回归方程也可以用二次以上的近似曲线来表示。在图10中,线l4表示表示一次近似直线的回归方程,线l2、l3表示将回归方程在y轴方向分别偏移了2σ2、
‑
2σ2后的线。
[0099]
在图10中,
○
标记的点是线l1和线l4的交点。因此,通过下式:
[0100]
[数学式2]
[0101]
m1=0.3068
×
p2‑
2.4155
[0102]
计算出推定为刀尖11a与工件w接触的时刻p
z
。
[0103]
需要说明的是,当设定置信区间为95%(2σ)来推定最大误差时,
△
标记的点是线l3与线l5的交点,
□
标记的点是线l2与线l4的交点。因此,通过下式:
[0104]
[数学式3]
[0105]
m1‑
2σ1=0.3068
×
p1‑
2.4155 2σ2[0106]
[数学式4]
[0107]
m1 2σ1=0.3068
×
p3‑
2.4155
‑
2σ2[0108]
计算出包含最大时间误差的接触时刻p1、p3。其结果,基于实验的接触位置的最大误差e
p
求出为0.019mm。
[0109]
这样,位置关系导出部23根据与驱动电机相关的检测值的时序数据,来计算接触的时刻。与单纯地将检测量超过了规定的阈值的时刻判定为接触时刻相比,在本方法中,由于使用由检测量的历史记录导出的回归方程,因此能够求出检测量达到阈值之前的准确的接触时刻。
[0110]
在本方法中,由于使切削刀具11或工件w一边旋转或反向旋转一边接近而进行细微的切削或者抛光(平坦化),因此在工件w的表面上残留细微的切削痕或者压痕。因此,本方法并不适合在最终精加工后应用,但如果在之前的阶段应用本方法,然后进行最终精加工,则在应用本方法时没有残留细微的切削痕/压痕的问题。
[0111]
在连续车削的情况下,如图10所示,获取随着刀尖11a缓慢地切入而缓慢地增大的检测值。另一方面,在如铣削那样断续切削的情况下,通过一边旋转一边接触而断续地产生切削力或抛光力。在测定与像这样断续的力对应的主轴旋转电机的电流值时,可以采用将在其各旋转周期、各切削刃通过周期内所测定的值的平均值、最大值作为检测值的时序数据。如上所述,在本方法中,某种程度加工掉工件w,由此增大接触区域而能够提高分辨能力,另外,在旋转刀具的情况下也不需要确定旋转位置,能够实现实用的接触检测。
[0112]
实施方式的切削装置1获取与切削刀具11和工件w接触后的驱动电机相关的检测值的历史记录而追溯到接触前的检测值进行分析,由此能够准确地导出切削刀具11与工件w的接触时刻而确定接触位置。在上述实验中,将通过搭载于切削装置的功能推定出的转矩输出值用作与驱动电机相关的检测值,但在不具有转矩推定功能的切削装置中,也可以使用主轴旋转电机的电流检测值、进给轴旋转电机的电流检测值的时序数据、或者基于编码器的检测值的时序数据等进行接触检测。
[0113]
这样,控制部20具有:控制进给机构7使切削刀具11相对移动而获取刀尖11a与被切削材料6等的接触对象物接触时的坐标值的功能。需要说明的是,切削装置1也可以具有接触传感器,控制部20根据来自接触传感器的检测数据检测接触而获取接触时的坐标值。以下,以具有接触检测功能为前提,对在切削装置1中确定切削刀具11与对象物的相对位置关系的方法进行说明。需要说明的是,在实施例1中,被切削材料6的旋转中心与主轴2a的旋转中心意思相同。
[0114]
<实施例1>
[0115]
图11是用于说明确定切削刀具与被切削材料旋转中心的相对位置关系的方法的图。以下,对计算被切削材料6的旋转轴中心a(x,y)的方法进行说明。在该例子中,被切削材料6处于经过一次车削加工后的状态。需要说明的是,从防止锋利的刀具切削刃的缺损的观点出发,优选为使被切削材料6在主轴2a的作用下处于旋转的状态,但被切削材料6也可以
不旋转。
[0116]
首先,移动控制部22使刀具刀尖从下方向上方(y轴正方向)缓慢地移动而在p1点与车削加工完毕的被切削材料6接触。需要说明的是,p1点的x轴方向的坐标x1是事先设定的,y轴方向的坐标为变量。接触检测可以由位置关系导出部23通过上述方法进行,或者也可以利用接触传感器的检测数据来进行。需要说明的是,根据上述的接触检测方法,位置关系导出部23根据接触后的检测值变化来生成回归直线,在事后确定接触位置。因此,在移动控制部22使刀具刀尖在p1点接触的瞬间,位置关系导出部23还不能确定接触位置,虽然实际上在p1点接触,但移动控制部22需要使刀具刀尖向比p1点稍靠上方移动(进行相应的量的切削)。
[0117]
如果位置关系导出部23利用回归直线导出接触的时刻,移动控制部22则将接触时刻的坐标、即p1点坐标(x1,y1)提供给位置关系导出部23。需要说明的是,严格地说,移动控制部22并不管理切削刀具11的刀尖11a的坐标,而是管理切削刀具11的坐标,但是由于刀尖坐标与切削刀具坐标为一对一的关系,因此以下根据刀尖坐标进行说明。
[0118]
需要说明的是,如上所述,被切削材料6使用已经车削加工完毕的工件。这是为了在以被切削材料6的旋转轴、即主轴2a的旋转轴为中心的相同直径的圆的圆周上检测p1点和后述的p2点坐标、p3点坐标。因此,位置关系导出部23使刀具刀尖在p1点与车削加工后的被切削材料6接触,但也可以将作为预加工而进行的车削加工时的x轴和y轴的坐标值设为p1点。
[0119]
接着,移动控制部22使刀具刀尖向下方(图11中的y轴负方向)下降足够的距离而向x轴正方向前进已知的距离d。然后,移动控制部22使刀具刀尖向上方(y轴正方向)缓慢地移动而在p2点与被切削材料6接触。如果位置关系导出部23检测到接触而导出接触时刻,移动控制部22则将接触时刻的坐标、即p2点坐标(x2,y2)提供给位置关系导出部23。
[0120]
接着,移动控制部22使刀具刀尖向下方(y轴负方向)下降足够的距离而向x轴正方向前进已知的距离d。需要说明的是,前进的距离只要是已知的距离即可,与p1点坐标与p2点坐标之间的x轴方向距离(d)不同也可。然后,移动控制部22使刀具刀尖向上方(y轴正方向)缓慢地移动而在p3点与被切削材料6接触。如果位置关系导出部23检测到接触而导出接触时刻,移动控制部22则将接触时刻的坐标、即p3点坐标(x3,y3)提供给位置关系导出部23。需要说明的是,在一边使主轴2a旋转一边进行接触检测的情况下,由于在接触时进行了轻微的切削而半径减小,因此p1点、p2点以及p3点各自的接触检测在不同的z轴方向位置进行为好。
[0121]
位置关系导出部23根据切削刀具11在与车削加工时的切削刀具11的旋转角度位置不同的至少两个位置接触时的坐标值,来确定切削刀具11与被切削材料6的旋转中心的相对位置关系。例如,在将作为预加工而进行的车削加工时的x轴和y轴的坐标值设为p1点时,位置关系导出部23根据与p1点成为分别不同的旋转角度位置的p2点、p3点的坐标值,来确定切削刀具11与被切削材料6的旋转中心的相对位置关系。需要说明的是,在实施例1中,位置关系导出部23根据三个旋转角度位置各自不同的接触点、即p1点、p2点、p3点的坐标值,来确定切削刀具11与被切削材料6的旋转中心的相对位置关系。位置关系导出部23利用确定一个通过三点的圆,来计算作为被切削材料6的旋转中心的a点的坐标(x,y)和半径r。
[0122]
图12(a)、(b)示出a点坐标的导出方法。如图12(a)所示,能够通过计算线l1与线l2
的交点来求出坐标a。线l1、l2分别由以下的(式5)、(式6)表示。
[0123]
[数学式5]
[0124][0125]
[数学式6]
[0126][0127]
根据(式5)、(式6),导出(式7)。
[0128]
[数学式7]
[0129][0130]
其中,
[0131]
x1‑
x2=
‑
d
[0132]
x2‑
x3=
‑
d,
[0133]
将p2点坐标(x2,y2)定义为(0,0)后,则可以由
[0134]
[数学式8]
[0135][0136]
导出a点的x坐标。
[0137]
另外,图12(b)所示的线l3由以下的(式9)表示。
[0138]
[数学式9]
[0139][0140]
如果将由(式8)求得的x代入(式9),有下式:
[0141]
[数学式10]
[0142][0143]
由此导出a点的y坐标。
[0144]
需要说明的是,被切削材料6的旋转半径如下式求出。
[0145]
[数学式11]
[0146][0147]
这样,位置关系导出部23导出将p2点坐标(x2,y2)设为(0,0)时的a点坐标。由此,位置关系导出部23根据三个接触位置的坐标值,来确定切削刀具11与被切削材料6的旋转中心的相对位置关系。
[0148]
以下,对a点坐标和半径r的计算精度进行考察。关于图10,计算出了接触检测中的
接触位置检测误差e
p
,以下,对该检测误差e
p
对a点坐标和半径r的精度所带来的影响进行验证。
[0149]
x坐标的误差设为e
x
,y坐标的误差设为e
y
,半径r的误差设为e
r
。
[0150]
则按下式考虑误差。
[0151]
[数学式12]
[0152][0153]
在这样考虑了误差的情况下,由(式8)表示的a点的x坐标值、由(式10)表示的a点的y坐标值、由(式11)表示的半径r表示如下。
[0154]
[数学式13]
[0155][0156][0157]
按下式求出误差e
x
:
[0158]
[数学式14]
[0159][0160]
其中,
[0161]
因为可以近似为下式:
[0162]
[数学式15]
[0163][0164]
因此可导出误差e
x
如下。
[0165]
[数学式16]
[0166][0167]
同样地,按下式求出误差e
y
:
[0168]
[数学式17]
[0169][0170]
其中,因为可以近似为下式:
[0171]
[数学式18]
[0172][0173]
所以可导出误差e
y
如下。
[0174]
[数学式19]
[0175]
e
y
≈e
p
[0176]
误差e
r
由下式表示。
[0177]
[数学式20]
[0178][0179]
这样,x坐标的误差e
x
、y坐标的误差e
y
、半径r的误差e
r
均可以用接触位置检测误差e
p
来表示,确认了通过减小接触位置检测误差e
p
来提高加工精度的情况。
[0180]
如在实施例1中说明的那样,如果能够确定切削刀具11与被切削材料6的旋转中心(主轴中心)的相对位置,则在圆筒面的加工时能够精加工成准确的直径,在加工端面时,由于刀具刀尖的中心高度不会波动,因此不会残留所谓的凹陷,对于球面、非球面加工也能够实现高的加工精度。
[0181]
<实施例2>
[0182]
在实施例2中,位置关系导出部23检测切削刀具11与在安装被切削材料6的部件上设置的基准面的接触而确定切削刀具11相对于部件基准面的相对位置也可。作为部件的例子,例如可以是支承被切削材料6的主轴2a,通过使切削刀具11与设置于主轴2a的端面、周面的基准面接触,位置关系导出部23确定切削刀具11与主轴2a的接触位置,由此可以导出切削刀具11与被切削材料6的安装面、旋转中心等的相对位置关系。
[0183]
图13是用于说明基准面的图。对于基准面,可设定与工件w的安装面、旋转中心等的相对位置关系已知的面。在该例子中,在使工件w绕中心轴线旋转而进行车削加工的切削装置中,将用于固定工件w的主轴2b的端面设定为基准面1,将主轴2b的周面设定为基准面2。即,基准面1是与主轴旋转轴垂直的平面,基准面2是以主轴旋转中心为中心的圆筒面。位置关系导出部23根据与工件w的安装面、旋转中心等的相对位置关系已知的基准面上的接触位置的坐标值,来确定切削刀具与工件w的安装面、旋转中心等的相对位置关系。
[0184]
如上所述,位置关系导出部23检测切削刀具11与作为部件的主轴2b的接触而能够确定该接触位置。
[0185]
在此,位置关系导出部23通过对基准面1进行刀具刀尖的接触检测,能够准确地获知工件w的长度方向(图中的左右方向)的刀具刀尖原点(工件w的安装面、即刀具刀尖相对于工件w的左端的面的相对位置)。由此,在对工件w的端面(图中的右端的面)进行加工时,能够准确地精加工出工件w的长度(左右方向的长度)。
[0186]
另外,位置关系导出部23通过在与实施例1同样地在y轴位置不同的三点(如果直径已知则两点即可)对基准面2进行刀具刀尖的接触检测,能够准确地获知工件w的半径方向的刀具刀尖原点(刀具刀尖相对于工件w的旋转中心的相对位置)。由此,在加工工件w的圆筒面时,能够准确地精加工出工件w的直径。
[0187]
基准面也可以设定在工件w的一部分上。例如,在图13中,在基准面1是工件w的一部分的情况下,能够准确地精加工出从该面到工件w的右端面的长度。需要说明的是,在图13中示出了车削加工的例子,但如果是刨削加工,则只要在基准面(准确的平面)上的三点进行接触检测就能够确定该平面,因此能够以准确的高度精加工出与基准面平行的面。另外,如果基准面是与z轴准确地垂直的平面,则仅通过在一点进行接触检测,就能够以准确的高度精加工出与底面(与基准面接触的工件w的面)平行的面。
[0188]
在以下的实施例3~13中,主要对应用了在实施例1中说明的三点接触检测的技术进行说明。在以下说明所使用的附图中,a轴是指以x轴为中心的旋转轴,b轴是指以y轴为中心的旋转轴,c轴是指以z轴为中心的旋转轴。另外,在本说明书和附图中,关于带有尖角(caret)(帽形(hat))的记号,例如当记号是“y”时,需要注意的是,为了表记上的方便,按如下方式表示。
[0189]
[数学式21]
[0190][0191]
即,在记号y的上方附加尖角(帽形)的记号与在相同的记号y的旁边附加尖角的记号表示相同的变量。在实施例中,带有尖角的记号是指应求出的变量。需要说明的是,上方附加有尖角的记号在数学式中使用,而在旁边附加有尖角的记号在文章中使用。另外需要注意的是,在不同的实施例的附图中重复使用的记号是为了便于理解各个实施例。
[0192]
<实施例3>
[0193]
在实施例1中,控制部20根据车削加工后的、换言之预加工后的被切削材料6上的三点的坐标值,来确定切削刀具11与被切削材料6的旋转中心的相对位置关系。在实施例3中,控制部20利用用于设定刀尖的原点而高精度地加工的具有已知形状的物体,来确定切削刀具11与具有已知形状的物体的相对位置关系,从而确定与切削刀具11的刀尖相关的信息。以下,将为了确定与切削刀具11的刀尖相关的信息的物体称为“基准块”。控制部20通过使切削刀具11的刀尖与基准块接触来识别(identify)刀尖位置,因此作为其前提,至少掌握要去接触的基准块的形状。
[0194]
图14示出将切削刀具11以能够c轴旋转的方式安装的切削装置1的一例。图14(a)示出从x轴方向观察的切削装置1的情况,图14(b)示出从z轴方向观察的切削装置1的情况。切削刀具11由支承装置42支承,支承装置42以能够c轴旋转的方式固定于安装轴41。
[0195]
在b轴工作台43上配置有作为具有已知形状的物体的基准块40。在实施例3中,为了确定切削刀具11的刀尖位置,控制部20使刀尖与基准块40至少接触三次,并利用该接触点的位置坐标来确定与切削刀具11的安装位置相关的信息。在实施例3中,进给机构7具有使b轴工作台43移动的功能,移动控制部22使b轴工作台43移动而使切削刀具11的刀尖11a与基准块40的已知形状部分在多个点接触。基准块40由高硬度的材料形成,以便不易因与刀尖11a的接触而损伤。在实施例3中,刀尖11a的刀尖半径、刀尖圆角的中心坐标、刀尖形状的误差未知,对确定这些信息的方法进行说明。以下,设定为刀尖11a的前端具有恒定的曲率(刀尖半径),刀尖圆角的中心也称为“刀具中心”。
[0196]
在图14(a)所示的yz平面中,求出刀尖半径r^和yz平面中的刀具中心(z^,y^)。
[0197]
图15示出刀尖11a与基准块40的已知形状部分在一点接触的情况。如上所述,刀尖11a具有恒定的曲率,并具有刀尖半径为r^的圆弧面。需要说明的是,刀尖半径r^未知。另一方面,基准块40在形状已知的部分上与刀尖11a接触。在实施例3中形状已知是指,位置关系导出部23知道刀尖11a有可能接触的部位的形状的情况。
[0198]
基准块40只要至少在与刀尖11a接触的部位具有已知的形状即可,位置关系导出部23不需要知道不可能与刀尖11a接触的部位的形状。在图15所示的例子中,基准块40具有以“ ”示出的位置为中心的半径为rw的圆弧面,在进行刀尖11a的原点设定时,位置关系导出部23知道刀尖11a与该圆弧面接触的情况。换言之,在原点设定时,移动控制部22控制进
给机构7而使b轴工作台43移动,以使刀尖11a与作为基准块40的已知形状的圆弧面接触。该圆弧面的形状数据可以记录于未图示的存储器中。
[0199]
移动控制部22使b轴工作台43朝向切削刀具11的刀尖11a从下方向上方(y轴正方向)缓慢地移动。在图15中,刀尖11a与基准块40在用
○
表示的接触点接触。位置关系导出部23将此时的基准块40中的圆弧的旋转中心位置“ ”的坐标定义为“0,0”。
[0200]
然后,移动控制部22以初始的接触位置为基准,使基准块40在z轴方向移动了 δz、
‑
δz的位置与刀尖11a接触。无论在哪种情况下,基准块40的刀尖11a接触的位置均位于半径为rw的圆弧面上。具体而言,移动控制部22从图15所示的状态开始,使基准块40向y轴负方向下降足够的距离之后向z轴负方向移动δz,并从该位置起向y轴正方向缓慢地移动,从而使基准块40的圆弧面与刀尖11a接触。此时的接触点在图中用
△
表示。接着,移动控制部22使基准块40向y轴负方向下降足够的距离之后向z轴正方向移动2δz,从该位置起向y轴正方向缓慢地移动,从而使基准块40的圆弧面与刀尖11a接触。此时的接触点在图中用
□
表示。需要说明的是,在第二次移动时,也可以省略y轴负方向的移动。
[0201]
这样,移动控制部22使切削刀具11的刀尖11a与基准块40的已知形状部分至少在三点接触,并将接触位置的坐标值提供给位置关系导出部23。位置关系导出部23根据各个接触位置的坐标值来确定与切削刀具11的安装位置相关的信息。
[0202]
图16示出刀尖11a与基准块40的位置关系。在图15中,在用
□
表示的接触点接触的情况下,已知圆弧中心的坐标为(δz,h2)。h2是移动控制部22的检测值。另外,在图15中,在用
△
表示的接触点接触的情况下,已知圆弧中心的坐标为(
‑
δz,
‑
h1)。h1也是移动控制部22的检测值。
[0203]
如图16所示,将第一次接触时的基准块40中的圆弧面的半径中心设为(0,0),将刀具中心设为(z^,y^)时,有下式。
[0204]
[数学式22]
[0205][0206][0207][0208]
联立后,有下式。
[0209]
[数学式23]
[0210][0211][0212]
利用由上式得到的z^、y^求出r^。
[0213]
[数学式24]
[0214]
[0215]
如上所述,位置关系导出部23根据在三个位置接触时的坐标值,来确定与切削刀具11的安装位置相关的信息。具体而言,作为与安装位置相关的信息,位置关系导出部23求出刀尖的刀尖半径r和刀具中心坐标(z,y)。
[0216]
需要说明的是,如果对具有已知的圆弧形状的基准块40在除了上述三个接触位置以外的圆弧上的点中至少一个点以上接触,则利用如上所求得的刀尖半径r和刀具中心坐标(z,y)而预测的从接触位置的偏差,作为刀具刀尖的从上述刀尖半径r的圆弧的偏差(误差)来被求出。
[0217]
接下来,位置关系导出部23进行在图14(b)所示的xy平面中求出从c轴旋转中心到刀尖11a前端的距离l^和初始的安装角度θ^的计算。例如在加工复杂的自由曲面形状的情况下,有时重复进行同时控制xyc轴的切削进给和z轴方向的周期进给(pick feed)。这样,在c轴包含于切削进给运动中的情况下,如果从c轴旋转中心到刀尖11a前端的距离l^与初始的安装角度θ^存在误差,则会导致加工精度下降。因此,位置关系导出部23根据将刀尖11a在xy平面移动时的、与基准块40的已知形状部分的至少三点的接触坐标值,来确定与切削刀具11的安装位置相关的信息。
[0218]
图17示意性地示出使切削刀具11逆时针旋转而使刀尖11a与基准块40的上表面(y基准面)接触时的切削刀具11的倾斜状态。移动控制部22控制进给机构7而使切削刀具11绕c轴旋转。基准块40的上表面与y轴的垂直面平行,如图14(b)所示,基准块40的上表面位置已知。
[0219]
移动控制部22使b轴工作台43朝向切削刀具11的刀尖11a从下方向上方(y轴正向)缓慢地移动而使基准块40的上表面与刀尖11a接触。然后,移动控制部22使基准块40向y轴负方向下降足够的距离之后使切削刀具11向逆时针方向旋转δc,然后使基准块40向y轴正方向缓慢地移动而使基准块40的上表面与刀尖11a接触。接着,移动控制部22使基准块40向y轴负方向下降足够的距离之后使切削刀具11向逆时针方向进一步旋转δc,然后使基准块40向y轴正方向缓慢地移动而使基准块40的上表面与刀尖11a接触。由此,位置关系导出部23获取三点的接触位置的y轴方向的高度(y位置)。
[0220]
图18示出从初始的接触位置(初始y位置)旋转δc时的接触位置的高度变化δy1。以初始的接触位置为基准,进一步旋转δc时的接触位置的高度变化为δy2。此时,关于δy1、δy2,有以下式子成立。
[0221]
[数学式25]
[0222][0223][0224]
联立后从两式消去l^,
[0225]
[数学式26]
[0226]
[0227][0228]
利用得到的θ^求出l^。
[0229]
[数学式27]
[0230][0231]
如上所述,关于c轴旋转,位置关系导出部23根据在三个位置接触时的坐标值,来获取与切削刀具11的初始的安装位置相关的信息。具体而言,位置关系导出部23作为与安装位置相关的信息来导出从c轴旋转中心到刀尖11a的距离l和初始的安装角度θ。这样,在实施例3中,通过使用基准块40来位置关系导出部23能够高精度地确定与安装位置相关的信息。
[0232]
<实施例4>
[0233]
在实施例4中也采用:控制部20利用用于设定刀尖的原点而高精度地加工的具有已知形状的物体(基准块40),来确定切削刀具11与基准块40的相对位置关系,从而确定与切削刀具11的安装位置相关的信息。
[0234]
图19示出将切削刀具11以能够c轴旋转的方式安装的切削装置1的另一例。图19(a)示出从x轴方向观察的切削装置1的情况,图19(b)示出从z轴方向观察的切削装置1的情况。切削刀具11由支承装置42支承,支承装置42以能够c轴旋转的方式固定于安装轴41。
[0235]
在b轴工作台43上配置有作为具有已知形状的物体的基准块40。在实施例4中也采用:为了确定切削刀具11的刀尖位置,控制部20使刀尖与基准块40至少接触三次,并利用该接触点的位置坐标来确定与切削刀具11的安装位置相关的信息。实施例4也与实施例3同样地,移动控制部22使b轴工作台43移动而使切削刀具11的刀尖11a与基准块40的已知形状部分在多个点接触。
[0236]
首先对求出刀尖半径r^和xy平面的刀具中心(x^,y^)的方法进行说明。
[0237]
图20示出刀尖11a与基准块40的已知形状部分在一点接触的情况。刀尖11a具有恒定的曲率,并具有刀尖半径r^的圆弧面。刀尖半径r^未知。基准块40在形状已知的部分上与刀尖11a接触。需要说明的是,形状已知是指,位置关系导出部23知道刀尖11a有可能接触的部位的形状的情况。
[0238]
在图20所示的例子中,基准块40具有以“ ”所示的位置为中心的半径为rw的圆弧面,在进行刀尖11a的原点设定时,位置关系导出部23知道刀尖11a与该圆弧面接触的情况。换言之,在原点设定时,移动控制部22控制进给机构7而使b轴工作台43移动,以使刀尖11a与作为基准块40的已知形状的圆弧面接触。该圆弧面的形状数据可以记录于未图示的存储器中。
[0239]
移动控制部22使b轴工作台43朝向切削刀具11的刀尖11a从下方向上方(y轴正方向)缓慢地移动。在图20中,刀尖11a与基准块40在用
○
表示的接触点接触。位置关系导出部23将此时的基准块40中的圆弧的旋转中心位置“ ”的坐标定义为“0,0”。
[0240]
然后,移动控制部22以初始的接触位置为基准,使基准块40在x轴方向移动了 δx、
‑
δx的位置与刀尖11a接触。无论在哪种情况下,基准块40的与刀尖11a接触的位置均位
于半径为rw的圆弧面上。具体而言,移动控制部22从图20所示的状态开始,使基准块40向y轴负方向下降足够的距离之后向x轴负方向移动δx,并从该位置起向y轴正方向缓慢地移动,从而使基准块40的圆弧面与刀尖11a接触。此时的接触点在图中用
△
表示。接着,移动控制部22使基准块40向y轴负方向下降足够的距离之后向x轴正方向移动2δx,从该位置起向y轴正方向缓慢地移动,从而使基准块40的圆弧面与刀尖11a接触。此时的接触点在图中用
□
表示。需要说明的是,在第二次移动时,也可以省略y轴负方向的移动。
[0241]
这样,移动控制部22使切削刀具11的刀尖11a与基准块40的已知形状部分至少在三点接触,并将接触位置的坐标值提供给位置关系导出部23。位置关系导出部23根据各个接触位置的坐标值来确定与切削刀具11的安装位置相关的信息。
[0242]
图21示出刀尖11a与基准块40的位置关系。在图20中,在用
□
表示的接触点接触的情况下,已知圆弧中心的坐标为(δx,h2)。h2是移动控制部22的检测值。另外,在图20中,在用
△
表示的接触点接触的情况下,已知圆弧中心的坐标为(
‑
δx,
‑
h1)。h1也是移动控制部22的检测值。
[0243]
如图21所示,将第一次接触时的基准块40中的圆弧面的半径中心设为(0,0),刀具中心设为(x^,y^)时,有下式。
[0244]
[数学式28]
[0245][0246][0247][0248]
联立后,有下式。
[0249]
[数学式29]
[0250][0251][0252]
利用由上式得到的x^、y^求出r^。
[0253]
[数学式30]
[0254][0255]
如上所述,位置关系导出部23根据在三个位置接触时的坐标值,来确定与切削刀具11的安装位置相关的信息。具体而言,作为与安装位置相关的信息,位置关系导出部23求出刀尖的刀尖半径r和刀具中心坐标(x,y)。
[0256]
接下来,位置关系导出部23求出刀尖11a的z坐标。
[0257]
图22示出使基准块40的已知形状的部分与切削刀具11的刀尖11a接触的状态。位置关系导出部23通过获取此时的z坐标值来确定刀尖的前端点。
[0258]
需要说明的是,移动控制部22需要移动基准块40而使基准块40中的已知的圆弧面
与刀尖11a接触。例如在移动基准块40时,会有在基准块40的圆弧面与刀尖11a接触之前与切削刀具11的前刀面接触的情况。在图示的例子中,在初始安装状态下的前刀面的角度相对于z轴小于90度的情况下,因基准块40的z轴方向的位置,会有基准块40的圆弧面与切削刀具11的前刀面接触而基准块40的圆弧面不能与刀尖11a接触的情况。此时,移动控制部22使基准块40向y轴负方向偏移而使刀尖11a在已知圆弧面的上部侧接触为好。
[0259]
这样,在实施例4中,通过使用基准块40来位置关系导出部23能够高精度地确定与安装位置相关的信息。
[0260]
<实施例5>
[0261]
在切削刀具11存在安装误差的情况下,切削加工后的被切削材料6则成为具有与本来预定的形状不同的形状。因此,在实施例5中,利用实际车削加工后的被切削材料6的加工面与理想车削加工时的被切削材料6的加工面(即设计上的加工面)的差量,来确定刀具中心的安装误差(δx^,δy^,δz^)。如果能够确定刀具中心的安装误差,则能够计算对所确定的安装误差进行修正的切削刀具11的进给路径。在实施例5中,移动控制部22利用在切削加工时未利用的移动方向的进给机构7的进给功能而使切削刀具11相对于切削加工后的被切削材料6相对移动,并根据切削刀具11在至少两个位置接触时的坐标值来确定刀具刀尖的安装误差。
[0262]
以下,有时将为了导出误差而进行了车削加工后的被切削材料6的加工面称为“预加工面”或“已加工面”。需要说明的是,通过预先将预加工面形成为比最终精加工面的厚度厚,在加工最终精加工面时,能够以修正后的进给路径进行精加工。即,在最终的精加工前的中间精加工后,利用该加工面来确定安装误差即可。
[0263]
控制部20根据被切削材料6的预加工面上的至少三点的坐标值,来求出切削刀具11的安装误差。在利用在预加工面的切削加工时所获取的一点的坐标值的情况下,控制部20也可以获取使切削刀具11在与车削加工时的切削刀具11的旋转角度位置不同的位置与预加工面接触的至少两点的坐标值,来求出切削刀具11的安装误差。即,控制部20也可以获取使切削刀具11在不同的y位置与预加工面接触的至少两点的坐标值,来求出切削刀具11的安装误差。
[0264]
需要说明的是,考虑到在预加工时获取的坐标值与通过接触预加工面而获取的坐标值的精度稍微不同的可能性,控制部20也可以不使用在预加工时获取的坐标值,而利用使切削刀具11在不同的y位置与预加工面接触的至少三点的坐标值,来求出切削刀具11的安装误差。
[0265]
需要说明的是,如在实施例1中说明的那样,在获取接触点坐标值时,从防止刀尖11a缺损的观点出发,有时使被切削材料6旋转。在此情况下,由于在接触点产生细微的开槽的情况,因此在获取下一个接触点坐标值时,将z位置在实质上可视为相同的范围内稍微偏移为好。以下,示出控制部20利用三点的坐标值来求出安装误差的例子,但为了提高安装误差的检测精度,也可以利用四点以上的坐标值。
[0266]
图23(a)示出将被切削材料6加工成具有圆筒面和半球面的形状的情况。被切削材料6以能够旋转的方式支承于安装轴41。在实施例5中,切削刀具11以(δx^,δy^,δz^)的安装误差安装于切削装置1。
[0267]
图23(b)示出zx平面的安装误差(δx^,δz^)。c2表示理想的刀具中心位置,c1表
示包含误差的刀具中心位置。图23(c)示出xy平面的安装误差(δx^,δy^)。
[0268]
在图23(a)中,箭头所示的进给路径是理想中心c2所通过的路径。在nc机床中,以刀具中心位于c2为前提,计算进给路径。移动控制部22利用进给机构7的z轴平移方向的进给功能和c轴旋转方向的进给功能而利用切削刀具11对被切削材料6进行加工。在图23(a)中,虚线表示刀具中心位于c2时的理想的加工面。在该车削加工中,加工半径为rw的圆筒面被确定为设计值。
[0269]
然而,在实际的刀具中心包含安装误差而位于c1的情况下,如果移动控制部22使切削刀具11按照所计算出的进给路径移动,则成为形成实线所示的加工面。
[0270]
图24(a)、(b)是用于说明导出刀具中心的安装误差(δx^,δy^)的方法的图。由于xy平面的安装误差(δx^,δy^),圆筒面的半径不是rw,而是rw’。移动控制部22利用在切削加工时未利用的移动方向的进给机构7的进给功能而使切削刀具11相对于切削加工后的被切削材料6相对移动,从而获取切削刀具11在至少两个位置接触时的坐标值。在实施例5中,移动控制部22利用进给机构7的x轴平移方向和y轴平移方向的进给功能而获取多个接触坐标值。
[0271]
即使利用与预加工时相同的移动方向的进给机构7的进给功能而使切削刀具11与预加工面接触,理论上也会成为在与加工时相同的坐标位置接触的情况。因此,在实施例5中,为了通过预加工面与切削刀具11的接触来导出刀具中心的安装误差,利用与在预加工时所利用的移动方向的进给机构7的进给功能不同的移动方向的进给功能而使切削刀具11与预加工面接触。即,利用预加工时所需的移动方向的进给功能以外的进给功能而导出切削刀具11的接触位置。如上所述,移动控制部22在预加工时利用了zc轴的进给功能,但在安装误差的推定处理时,利用xy轴的进给功能来获取接触点坐标。
[0272]
如在实施例1中说明的那样,位置关系导出部23获取圆筒面上的三个点的坐标值。
[0273]
图中,
□
表示圆筒面上的点,
[0274]
点1:(rw δx^,δy^)
[0275]
点2:(rw δx^
‑
δx1,
‑
δy δy^)
[0276]
点3:(rw δx^
‑
δx2,
‑
2δy δy^)
[0277]
δx1、δx2是由移动控制部22检测的值。
[0278]
需要说明的是,在该例子中,作为点1示出的坐标值利用了在预加工时所获取的坐标,但移动控制部22也可以通过在三点使刀尖11a与圆筒面接触来获取三点的坐标值。此时,在从防止刀尖11a缺损的观点出发而使被切削材料6旋转的情况下,移动控制部22使刀尖11a在圆筒面上的不同的z位置接触而获取三点的接触坐标值为好。
[0279]
位置关系导出部23进行以下计算。
[0280]
[数学式31]
[0281]
[式
‑
1]
[0282]
[式
‑
2]
[0283]
[式
‑
3]
[0284]
将[式
‑
1]和[式
‑
2]联立:
[0285][0286]
根据[式
‑
2]和[式
‑
3]得:
[0287][0288]
由两式按δy^进行联立:
[0289][0290][0291]
如上所述,位置关系导出部23能够导出(δx^,δy^)。
[0292]
如在实施例2中说明的那样,z轴方向的安装误差δz^可以利用例如安装轴41的基准面而由位置关系导出部23导出。如以上所述,确定刀具中心的安装误差(δx^,δy^,δz^)。这样,在实施例5中,通过利用预加工面与作为目标的设计加工面的差量来确定刀具中心的安装误差(δx^,δy^,δz^),并且移动控制部22能够重新计算修正了安装误差的进给路径。
[0293]
<实施例6>
[0294]
在实施例6中,对测定刀尖11a的形状走样的方法进行说明。
[0295]
如在实施例3中说明的那样,刀尖11a上有时存在凹凸。因此,以下示出以下方法:测定刀尖形状被转印到预加工面的凹凸,并根据加工面的凹凸来确定刀具刀尖的形状误差。在实施例6中,在可以推定因刀尖的形状走样以外的形状误差因素所引起的形状误差的情况下,在切削加工时未利用的移动方向的进给机构7的进给运动设为准确的动作且利用一个刀尖点而测定预加工面的形状,因此通过所推定的预加工面上的各点的位置与检测的位置的差量来确定刀具刀尖的形状误差。在实施例6中,移动控制部22利用在切削加工时未利用的移动方向的进给机构7的进给功能而使切削刀具11相对于切削加工后的被切削材料6相对移动,并根据切削刀具11在至少两个位置接触时的坐标值,来确定刀具刀尖的安装误差。
[0296]
图25(a)示出加工半球面的情况。移动控制部22利用进给机构7的x轴和z轴平移方向的进给功能以及c轴旋转方向的进给功能而利用切削刀具11对被切削材料6进行加工。图25(a)示出了没有刀具中心的安装误差而以理想的进给路径进行加工的情况。需要说明的是,在存在刀具中心的安装误差的情况下,在推定刀具刀尖的形状误差之前,如在实施例5中说明的那样预先测定好安装误差(δx^,δy^,δz^)为好。以下,位置关系导出部23根据与半球面的理想的预加工面的形状的偏差而推定刀尖的形状误差。
[0297]
如图25(a)所示,在该球面加工中,进行了不使切削刀具11进行b轴旋转的车削加工。参照图25(a)和(c),刀尖11a的a点的形状被转印为被切削材料6上的a点的形状,刀尖11a的b点的形状被转印为被切削材料6上的b点的形状,刀尖11a的c点的形状被转印为被切削材料6上的c点的形状。这样,在被切削材料6的从a到c的预加工面上被转印刀尖11a的从a到c的形状。
[0298]
此时,如果从a到c的形状具有理想的圆弧形状,则所加工的球面的截面具有理想的圆弧。然而,如图25(c)所示,在刀尖11a上存在凹凸的情况下,该凹凸将被转印到被切削材料6的加工面上。
[0299]
图25(b)示出测定被切削材料6的球面形状的情况。移动控制部22利用进给机构7的y轴和z轴平移方向的进给功能而获取多个接触坐标值。移动控制部22在使刀具中心与c轴旋转中心一致后,不改变x位置(x=0)并使θn偏移,同时使刀尖11a朝向半球面原点方向移动,从而使其在多个点接触。通过减小θn的偏移量,能够增加接触点。位置关系导出部23通过获取多个接触点的坐标来确定在x=0时的球面上的圆弧的形状。位置关系导出部23通过获取被切削材料6的实际的球面形状,能够获取与所推定的球面形状的偏差量,从而能够导出刀尖11a的走样形状。图25(d)示出θn处的球面的偏差量的检测值为δr
w,n
,但此时刀尖11a的半径方向走样为δrn^(=
‑
δr
w,n
)(参照图25(c))。这样,位置关系导出部23能够测定刀尖形状。
[0300]
根据实施例6,移动控制部22对切削后的被切削材料6使用在切削加工时未利用的y轴平移方向的进给功能,由此位置关系导出部23能够根据从理想形状时应该接触的位置的偏差量来确定刀尖形状的轮廓。位置关系导出部23确定刀尖的形状的轮廓,由此移动控制部22能够计算加入了刀尖的形状的轮廓的进给路径。或者,在推定为其他的加工误差因素较小的情况下,直接以实施例6中所测定的形状误差的量修正刀具移动路径而进行最终精加工也可。
[0301]
<实施例7>
[0302]
在实施例5中,对在切削刀具11存在安装误差的情况下导出刀具中心的安装误差(δx^,δy^,δz^)的方法进行了说明。在实施例7中,对不仅在切削刀具11存在安装误差,而且刀具的进给方向上也存在误差的情况下导出这些误差的方法进行说明。
[0303]
在实施例7中也采用,移动控制部22利用在切削加工时未利用的移动方向的进给机构7的进给功能而使切削刀具11相对于切削加工后的被切削材料6相对移动,并根据切削刀具11在至少两个位置接触时的坐标值,来确定刀具刀尖的安装误差。
[0304]
图26(a)示出使切削刀具11在z轴方向移动而进行了预加工时的情况。移动控制部22利用进给机构7的z轴平移方向的进给功能和c轴旋转方向的进给功能而利用切削刀具11对被切削材料6进行加工。在该车削加工中,沿着与z轴平行的线l1进给切削刀具11,结果,由于存在实施例5中说明的刀具中心的安装误差以及z轴与c轴旋转中心不平行等理由,因此在作为目标的圆筒面产生了加工误差。附带说一下线l1,在nc机床中,线l1沿着z轴,因此以与c轴旋转中心平行为前提,计算了切削刀具11的进给路径,结果,由于z轴与c轴旋转中心实际上不平行,因此移动控制部22使刀尖11a按照作为进给路径的以实线箭头所示的路径移动。因此,制成了与目标不同的形状的预加工面。
[0305]
需要说明的是,关于该平行度的误差因素,除了机床制造时的组装误差以外,还考虑了设置时、进给机构移动时、安装被切削材料时的重量分布变化引起的变形、加工力引起的变形、气温/加工热量引起的热变形等。其中,在考虑加工力引起的变形的情况下,优选为设定在预加工时和最终精加工时加工力程度相同的加工条件。
[0306]
在误差导出处理中,移动控制部22利用进给机构7的x轴平移方向、y轴平移方向以及z轴平移方向的进给功能而获取多个接触坐标值。移动控制部22导出在作为z位置的z1、
z2分别使y位置变化并在x方向各移动三次时的刀尖11a的接触坐标值。通过导出三点的接触坐标值,来如在实施例5中说明的那样导出与作为理想的刀具中心位置的位置偏差量(δx^1,δy^1)、(δx^2,δy^2)。
[0307]
位置关系导出部23通过导出(δx^1,δy^1,z1)、(δx^2,δy^2,z2)而能够计算出进给路径的轨道。在此,在任意的z中,将预想为对于c轴旋转中心相对地具有的位置误差设为(δx^,δy^),则有下式。
[0308]
[数学式32]
[0309][0310]
因此有下式。
[0311]
[数学式33]
[0312][0313]
需要说明的是,在此对两个z位置的位置偏差进行了线性插值,但也可以测定三个以上的z位置的位置偏差来增加插值的次数。
[0314]
这样,根据实施例7,移动控制部22对于切削后的被切削材料6利用在切削加工时未利用的x轴和y轴平移方向的进给功能,由此位置关系导出部23能够根据与理想形状时应该接触的位置的偏差量来推定相对于c轴的切削刀具11的进给方向的平行度。在实施例7中,通过推定相对于c轴的切削刀具11的进给方向的平行度,来位置关系导出部23能够确定切削刀具11相对于被切削材料6的相对移动方向的偏差。如上式所示,通过求出任意的z时的位置误差,移动控制部22能够计算出修正了该位置误差的进给路径。
[0315]
<实施例8>
[0316]
图27示出使切削刀具11在x轴方向和z轴方向移动而对球面进行了预加工时的情况。在该车削加工中,x轴与c轴正交,但因正交性被破坏而在球面产生了加工误差。在nc机床中,计算成为用于以x轴为基准而加工球面的线l2的进给路径,结果,由于用于刀具控制的x轴与成为被切削材料6的旋转轴的c轴的正交性被破坏,因此移动控制部22使刀尖11a按照作为进给路径的实线箭头所示的路径移动。
[0317]
在误差导出处理中,移动控制部22使刀尖11a在与某加工点p1相对于c轴对称的点p2接触。根据此时的x方向的移动距离(2δx)与y方向检测值(δz)的差量,来通过以下的式子求出表示c轴与x轴间的正交度的θ^。
[0318]
[数学式34]
[0319][0320]
这样,如果表示正交度的θ^被求出,移动控制部22则计算出该θ^为0的刀具的进给路径而进行修正。
[0321]
需要说明的是,该方法也可以应用于球面以外的面(包括平面、非球面)。
[0322]
在实施例8中也移动控制部22利用在切削加工时未利用的移动方向的进给机构7的进给功能而使切削刀具11相对于切削加工后的被切削材料6相对移动,并根据切削刀具11在至少两个位置接触时的坐标值,来确定刀具刀尖的安装误差。
[0323]
这样,在实施例8中,通过推定相对于c轴的x轴的正交度,来位置关系导出部23能够确定相对于被切削材料6的切削刀具11的相对移动方向的偏差量。
[0324]
<实施例9>
[0325]
在实施例5中,利用使刀尖11a与圆筒面接触时的坐标值来推定了刀具中心的安装误差(δx^,δy^,δz^)。在实施例9中,对利用使刀尖11a与预加工后的球面接触时的坐标值来推定刀具中心的安装误差(δx^,δy^,δz^)的方法进行说明。预加工后的球面可以是例如从图23所示的被切削材料6除去圆筒面后的球面。移动控制部22利用进给机构7的x轴平移方向的进给功能、z轴平移方向的进给功能以及c轴旋转方向的进给功能而利用切削刀具11对被切削材料6进行预加工。
[0326]
在实施例9所示的方法中,以使刀尖11a与位于相同的z位置的三点接触的方式对刀尖11a进行移动控制。在误差导出处理中,移动控制部22利用进给机构7的x轴平移方向、y轴平移方向以及z轴平移方向的进给功能而获取多个接触坐标值。
[0327]
图28(a)示出刀尖11a正在加工p1的情况。nc机床上的刀具中心坐标已知,为(x1,0,z1)。另外,连结工件中心o
c
和p1的线段相对于xy平面的角度为θ1。若将刀尖11a的刀尖半径设为r,则也作为加工点的p1的坐标如下。
[0328]
p1:(x1‑
rcosθ1,0,z1‑
rsinθ1)
[0329]
如果p1的坐标被确定,则位于与p1相同的z位置(z1‑
rsinθ1)(参照图28(b))并从p1向y轴负方向位移了δy、2δy的位置(参照图28(c))上设定应要接触的p2、p3。另外,在xy面内内,将连结c轴旋转中心和p1的线段与连结c轴旋转中心和p2的线段间的角度设为α,将连结c轴旋转中心和p1的线段与连结c轴旋转中心和p3的线段间的角度设为β(参照图28(b))。
[0330]
图29示出对于xy平面的、连结工件中心o
c
与接触点的线段的角度。其中,将与p2的线段的角度设为θ2,将与p3的线段的角度设为θ3。
[0331]
因此,如下计算用于与p2接触的刀具中心坐标(c2)、用于与p3接触的刀具中心坐标(c3)。
[0332]
c2:(x2 rcosθ2,
‑
δy,z1‑
rsinθ1 rsinθ2)
[0333]
c3:(x3 rcosθ3,
‑
2δy,z1‑
rsinθ1 rsinθ3)
[0334]
位置关系导出部23通过以下的几何学关系式来计算x2、x3、α、β、θ1、θ2、θ3。
[0335]
[数学式35]
[0336][0337]
各坐标值的原点是o
c
,o
c
是位于c轴旋转中心线上且具有与加工点的轨迹(为圆弧且在与xz面平行的平面上)的中心(在存在刀具安装误差的情况下,相应地从c轴旋转中心线偏离)相同的z坐标值的点。
[0338]
移动控制部22使刀尖11a与p2、p3接触。此时,移动控制部22使刀尖11a的中心坐标的(y,z)分别与c2、c3的上述坐标值一致,然后在x方向移动而使刀尖11a与球面接触。此时,如果以与计算值相同的x坐标值进行接触,则判定为没有中心坐标的安装误差。另一方面,如果在与计算值不同的nc机床上的刀具中心的x位置进行接触,则x方向的移动量作为误差来被检测。
[0339]
检测c2:(x2 δx2 rcosθ2,
‑
δy,z1‑
rsinθ1 rsinθ2)
[0340]
检测c3:(x3 δx3 rcosθ3,
‑
2δy,z1‑
rsinθ1 rsinθ3)
[0341]
δx2、δx3是检测值。
[0342]
根据检测值,可以按下式近似地导出p2、p3。
[0343]
检测p2:(x2 δx2,
‑
δy,z1‑
rsinθ1)
[0344]
检测p3:(x3 δx3,
‑
2δy,z1‑
rsinθ1)
[0345]
需要说明的是,就z位置的误差而言,刀具刀尖半径相对于加工面半径一般较小,即使假设有安装误差,加工点的轨迹形状(在与xz面平行的平面上)也仅平行移动了安装误差的量,在y方向观察的曲率是准确的(在z方向观察xy截面的曲率具有误差),因此与x位置相比,z位置的偏差小。因此可以忽略z位置的偏差。
[0346]
图30(a)示出由p1、p2和p3形成的初始圆与利用从初始圆导出的误差(δx2、δx3)而形成的假想圆的关系。假想圆通过p1、检测p2、检测p3。(δx’,δy’)是假想圆的中心。
[0347]
图30(b)示出将假想圆的中心坐标还原到原点后的坐标系。此时,通过下式推定刀具安装误差(δx^,δy^)。
[0348]
(δx^,δy^)=(
‑
δx’,
‑
δy’)
[0349]
位置关系导出部23利用所推定出的刀具安装误差(δx^,δy^)并通过以下的几何学关系式,重新计算x2、x3、α、β、θ1(对于第一个接触点来说,保持与加工时相同,与初始的接触时没有变化。因此与x1、z1相同,θ1也没有变化,不一定必须重新计算)、θ2、θ3。
[0350]
[数学式36]
[0351][0352]
由此导出下式。
[0353]
c2:(x2‑
δx^ rcosθ2,
‑
δy,z1‑
rsinθ1 rsinθ2)
[0354]
c3:(x3‑
δx^ rcosθ3,
‑
2δy,z1‑
rsinθ1 rsinθ3)
[0355]
移动控制部22利用所导出的c2、c3而使刀尖11a与新的p2、p3接触。移动控制部22使刀尖11a的中心坐标的(y,z)分别与c2、c3的上述坐标值一致,然后在x方向移动而使刀尖11a与球面接触。此时,如果以与计算值相同的中心坐标进行接触,则判定为中心坐标的安装误差的推定值没有推定误差。通过重复进行该处理,在可视为与计算值相同的中心坐标处,刀尖11a与被切削材料6的球面接触,即推测误差变得足够小,从而可求出准确的安装误差。
[0356]
在实施例9中也采用:移动控制部22利用在切削加工时未利用的移动方向的进给机构7的进给功能而使切削刀具11相对于切削加工后的被切削材料6相对移动,并根据切削刀具11在至少两个位置接触时的坐标值,来确定刀具刀尖的安装误差。
[0357]
这样,在实施例9中,通过反复计算而使预加工后的球面与作为目标的设计加工面的差量收敛,由此确定刀具中心的安装误差(δx^,δy^,δz^)。
[0358]
<实施例10>
[0359]
在实施例5~9中,对使切削刀具11不进行b轴旋转的车削加工进行了说明,在实施例10中,对使切削刀具11进行b轴旋转并仅利用刀尖11a的一个点的加工进行说明。
[0360]
图31(a)示出在加工时刀尖11a的一个点被用于切削的情况。在这样的加工中,如果相对于b轴中心o
b
的相对的刀具中心c的安装位置存在误差,则会产生加工误差。
[0361]
图31(b)是用于说明求出b轴中心o
b
与刀具中心c间的距离l^和初始的安装角度θ^的说明图。如图所示,移动控制部22在规定的y坐标、z坐标中将安装角度变更 δb、
‑
δb的量而检测刀尖11a的接触点上的x坐标的增量δx1、δx2,并利用它们按下式进行计算。
[0362]
[数学式37]
[0363]
[式
‑
1]
[0364]
[式
‑
2]
[0365]
利用[式
‑
1]和[式
‑
2]而按θ^整理l^:
[0366][0367][0368]
再将l^代入[式
‑
1]:
[0369][0370]
如以上所述,求出相对于b轴旋转中心的相对的刀具中心c的安装位置,即距离l^和角度θ^。
[0371]
<实施例11>
[0372]
在实施例11中,利用基于扫描线加工的预加工面而首先识别c轴旋转中心的误差。在实施例11中也使刀尖11a与预加工面在多个点接触而导出与理想轮廓的差量,由此识别从刀具中心观察的相对的c轴旋转中心位置的误差。
[0373]
图32概念性地示出扫描线加工中的xz面内的切削进给方向和yz面内的周期进给(pick feed)方向。为了识别c轴旋转中心的误差,可以利用yz平面内的工件形状和xz平面内的工件形状。
[0374]
<利用yz平面内的工件形状>
[0375]
图33(a)示出加工时的刀尖11a的情况。在图33(a)中,虚线表示加工时的刀具中心的切削运动轮廓,实线表示预加工面轮廓。理想的刀具中心的切削运动轮廓和预加工面轮廓已知。
[0376]
图33(b)示出将c轴(在此,在刀具侧安装有c轴)从加工时的姿态旋转90度后使刀尖11a与预加工面在多个点接触的情况。在图33(b)中,实线表示连接接触点的接触面轮廓。
[0377]
位置关系导出部23通过数值分析来识别c轴旋转中心的y方向误差(c轴旋转后、旋转前的x方向误差),以使接触面轮廓与预加工面轮廓最为匹配。具体而言,位置关系导出部23在通过预加工面轮廓来推定出各接触位置的基础上,导出与实际接触的检测位置的误差,并以该误差的总和最小的方式识别c轴旋转中心坐标。
[0378]
<利用xz平面内的工件形状>
[0379]
图34(a)示出加工时的刀尖11a的情况。在图34(a)中,虚线表示加工时的刀具中心的切削运动轮廓,实线表示预加工面轮廓。理想的刀具中心的切削运动轮廓和预加工面轮廓已知。
[0380]
图34(b)示出将c轴从加工时的姿态旋转90度后使刀尖11a与预加工面在多个点接触的情况。在图34(b)中,实线表示连接接触点的接触面轮廓。
[0381]
位置关系导出部23通过数值分析来识别c轴旋转中心的x方向误差(c轴旋转后、旋转前的y方向误差),以使接触面轮廓与预加工面轮廓最为匹配。具体而言,位置关系导出部23在通过预加工面轮廓来推定出各接触位置的基础上,导出与实际接触的检测位置的误差,并以该误差的总和最小的方式识别c轴旋转中心坐标。
[0382]
如图33(b)或图34(b)所示,从刀具中心观察的相对的c轴旋转中心位置被识别。如果c轴旋转中心位置被识别,则利用该位置能够测定刀尖11a的形状误差。
[0383]
图35示出测定刀尖形状误差的方法。移动控制部22使c轴从加工时的姿态旋转90
度而在预加工面上使刀尖11a以相同的刀尖位置接触的方式沿着曲线在多个点接触。图35表示沿着虚线所示的脊线在刀尖的z方向最低点与预加工面接触的情况。位置关系导出部23根据各接触点处的计算上的接触位置与所检测出的接触位置的偏差量来与实施例6相同地测定刀尖形状的走样。
[0384]
<实施例12>
[0385]
在实施例12中,利用基于等高线加工的预加工面来识别c轴旋转中心的误差。在此情况下,位置关系导出部23如在实施例9中说明的那样不改变c轴和z轴的位置,而是利用改变xy位置而接触的两点以上的坐标值,由此能够识别c轴旋转中心与刀尖11a的xy相对位置。
[0386]
另外,在c轴旋转位置与预加工时相差90度的姿态下,通过在相同的刀尖位置接触的曲线上进行多点接触,能够测定刀具刀尖的形状误差。另外,如在实施例7中说明的那样,改变z位置而在c轴旋转位置与预加工时相差90度的姿态进行两点以上的接触,据此能够识别c轴旋转中心与z轴的平行度(倾斜)。
[0387]
<实施例13>
[0388]
在实施例13中,对利用转印了直线切削刃的加工面来识别刀具的安装角度和b轴旋转中心位置的方法进行说明。
[0389]
图36示出作为直线切削刃的刀尖11a正在进行加工的情况。以下,对识别由刀具的安装角度决定的已加工面的微细沟槽的主要倾斜面的倾斜b轴旋转中心与刀尖前端的距离l^、相对于z轴的倾斜β^的方法进行说明。倾斜是以从
‑
x轴开始逆时针旋转为正的角度,倾斜β^是以从
‑
z轴开始的角度。
[0390]
图37是用于说明识别方法的图。移动控制部22使刀尖11a以任意的角度θ1与预加工面在p1接触,并检测作为p1的z位置的z1。移动控制部22保持相同的姿态下使刀尖11a在与预加工面偏移dx的p2接触,并检测作为p2的z位置的z2。
[0391]
由此,如果设dz=z2‑
z1,则可按下式计算。
[0392]
(dz/|dx|)
[0393]
在该倾斜角度与目标形状的倾斜角度偏离的情况下,通过利用b轴修正该差量来能够在最终精加工中进行具有更准确的倾斜面的微细沟槽加工。
[0394]
图38是用于说明坐标变换的图。
[0395]
刀尖前端点和b轴旋转中心的相对关系表示如下。
[0396]
[数学式38]
[0397][0398]
为了使切削位置处的z坐标为0,利用变换坐标系后如下。
[0399]
[数学式39]
[0400][0401]
图39(a)、(b)分别示出使刀尖11a的姿态变化而与预加工面接触的状态。
[0402]
图39(a)示出在使b轴旋转θ1的状态下使刀尖11a在与倾斜垂直的方向(与z’轴平行)移动而与预加工面接触的状态。图39(b)示出在使b轴旋转了θ2的状态下使刀尖11a在与倾斜垂直的方向(与z’轴平行)移动而与预加工面接触的状态。θ1、θ2以逆时针的角度为正。此时,作为z值,分别检测出z
’1和z
’2。
[0403]
因此,有以下关系成立。
[0404]
[数学式40]
[0405][0406][0407]
需要说明的是,x’1
、x’2
是适当的偏移量,也可以不偏移。
[0408]
上述两个接触点的z’坐标按以下求出。
[0409]
[数学式41]
[0410][0411][0412]
联立求解后,有下式。
[0413]
[数学式42]
[0414][0415]
因此,
[0416]
[数学式43]
[0417][0418][0419]
因此,按以下方式计算。
[0420]
[数学式44]
[0421][0422]
从计算出:
[0423][0424][0425]
这样,根据实施例13,在转印了直线切削刃的加工面上通过使刀尖11a在多个点接触,能够导出b轴旋转中心。例如像在自由曲面上形成微细沟槽的复杂形状那样,为了微细沟槽的倾斜面的角度发生变化而需要使b轴旋转后进行加工的情况下,通过获知准确的b轴旋转中心,能够防止刀具刀尖的xy位置偏离而加工精度降低(如果相对于刀具刀尖位置的相对的b轴旋转中心位置存在误差,则b轴旋转而导致刀具刀尖的xy位置产生误差)的情况。
[0426]
在以下的实施例14~18中,对与作为旋转刀具的切削刀具11相关的偏差量的确定处理进行说明。在实施例14~18中,移动控制部22利用在切削加工时未利用的移动方向的进给机构7的进给功能而使切削刀具11相对于切削加工后的被切削材料相对移动,位置关系导出部23根据切削刀具11在至少两个位置接触时的坐标值,来确定与切削刀具11相关的偏差量。在所有实施例中,均代表旋转刀具而求出与在前端具有半球状的球部的球头立铣刀的偏差量,但对于圆角立铣刀等的其他种类的旋转刀具,也能够同样地确定偏差量。
[0427]
<实施例14>
[0428]
在实施例14中,对确定球头立铣刀的切削刃的形状误差的方法进行说明。
[0429]
图40示出与被切削材料6的预加工面接触的球头立铣刀的两种不同的姿态a、b。在两种姿态a、b下,从球部的中心观察,不同角度位置的刀尖与预加工面接触。姿态a也可以是例如形成预加工面时的姿态。在实施例14中,以切削刃半径r的走样以外的值已知为前提。
[0430]
在图40中,从球部的中心到b轴中心o
b
的距离l、姿态a下的角度θ、姿态b下的角度(θ δθ)、从姿态a过渡到姿态b时的b轴中心o
b
的理想的移动量δx
r
是已知的。此时,测量b轴中心o
b
的移动量,当移动量为(δx
r
δx
er
)时,滚珠形状的走样量δr
er
^按以下求出。
[0431]
滚珠形状的走样量δr
er
^=移动的偏差量δx
er
[0432]
根据以上内容,通过以两个不同的姿态使球头立铣刀与预加工面接触,来能够测定切削刃的走样形状(形状误差)。
[0433]
<实施例15>
[0434]
在实施例15中,对确定球头立铣刀的主轴安装误差(刀具跳动量δr^)的方法进行说明。
[0435]
图41是用于说明确定球头立铣刀与主轴的偏心量的方法的图。在图41中,实线所示的球头立铣刀表示没有偏心时的轮廓形状,虚线所示的球头立铣刀表示产生了偏心时的轮廓形状。如图所示,在球头立铣刀偏心的情况下,通过轴向跳动而以大于理想值的外周进行切削。在实施例15中,以刀具跳动量δr^以外的值已知为前提。移动控制部22使球头立铣刀以两个姿态a、b与预加工面接触。
[0436]
假设主轴与z轴平行的b轴旋转相位θ0、姿态a下的角度θ、姿态b下的角度(θ δθ)已知,在姿态a与姿态b下旋转δθ而变化的跳动的量测定为δx。此时,
[0437]
[数学式45]
[0438][0439]
由此求出刀具的跳动量δr^。
[0440]
<实施例16>
[0441]
在实施例16中,对确定b轴中心o
b
的误差的方法进行说明。
[0442]
图42是用于说明确定b轴中心的偏差量的方法的图。在实施例16中,从球部的中心到b轴中心o
b
的距离l^、任意的姿态下的角度θ^未知,除此以外的值已知。移动控制部22在使球头立铣刀以任意的姿态的角度θ^与预加工面接触后,以已知的δθ先后变化两次而使球头立铣刀与预加工面接触。在实施例16中,移动控制部22以角度(θ^ δθ)、角度(θ^
‑
δθ)接触,位置关系导出部23测定了此时的x轴方向的移动量δx1、δx2。此时,用以下的式子求出l^、θ^。
[0443]
[数学式46]
[0444]
(1)
[0445]
(2)
[0446]
(3)
[0447]
由(2)、(3)得(4)
[0448]
由(1)、(2)、(4)得
[0449]
如上所述,可以通过以三种不同的姿态接触来导出未知的l^、θ^。
[0450]
<实施例17>
[0451]
在实施例17中,确定与x轴和z轴的正交度相关的指标θ
xz
^。指标θ
xz
^是从x轴与z轴间的直角的偏差量。
[0452]
图43是用于说明确定从x轴与z轴间的直角的偏差量的方法的图。从球部的中心到b轴中心o
b
的距离l、姿态a下的角度θ、姿态b下的角度(θ δθ)、从姿态a过渡到姿态b时的b轴中心o
b
的理想的移动量δx
r
(x轴与z轴正交时的移动量)、球部的切削刃半径r已知。从姿态a过渡到姿态b时,根据切削刃与预加工面接触为止的实际的移动量δx1,如下求出与x轴和z轴的正交度相关的指标θ
xz
^。
[0453]
[数学式47]
[0454][0455]
实施例17示出导出与x轴和z轴的正交度相关的指标的方法,如关于实施例7所说明的那样,通过使旋转刀具与预加工后的被切削材料6接触,来也能够推定相对于c轴的旋转刀具的进给方向的平行度。
[0456]
<实施例18>
[0457]
在实施例18中,利用基于扫描线加工的预加工面而首先识别c轴旋转中心的误差。在实施例18中也采用:使切削刀具11的切削刃与预加工面在多个点接触而导出与理想轮廓
的差量,由此识别从刀具中心观察的相对的c轴旋转中心位置的误差。
[0458]
图44概念性地示出扫描线加工中的xz面内的切削进给方向和yz面内的周期进给方向。为了识别c轴旋转中心的误差,可以利用yz平面内的工件形状和xz平面内的工件形状。
[0459]
<利用yz平面内的工件形状>
[0460]
图45(a)示出加工时的切削刃的情况。在图45(a)中,虚线表示加工时的球部中心的切削运动轮廓,实线表示预加工面轮廓。理想的球部中心的切削运动轮廓和预加工面轮廓已知。
[0461]
图45(b)示出使工件绕c轴旋转90度后,使刀尖与预加工面在多个点接触的情况。在图45(b)中,实线表示连接接触点的接触面轮廓。
[0462]
位置关系导出部23通过数值分析来识别c轴旋转中心的y方向误差(c轴旋转后、旋转前的x方向误差),以使接触面轮廓与预加工面轮廓最为匹配。具体而言,位置关系导出部23在通过预加工面轮廓推定出各接触位置的基础上,导出与实际接触的检测位置的误差,并以该误差的总和最小的方式识别c轴旋转中心坐标。
[0463]
<利用xz平面内的工件形状>
[0464]
图46(a)示出加工时的切削刃的情况。在图46(a)中,虚线表示加工时的球部中心的切削运动轮廓,实线示出预加工面轮廓。理想的球部中心的切削运动轮廓和预加工面轮廓已知。
[0465]
图46(b)示出使工件绕c轴旋转90度后,使刀尖与预加工面在多个点接触的情况。在图46(b)中,实线表示连接接触点的接触面轮廓。
[0466]
位置关系导出部23通过数值分析来识别c轴旋转中心的x方向误差(c轴旋转后、旋转前的y方向误差),以使接触面轮廓与预加工面轮廓最为匹配。具体而言,位置关系导出部23在通过预加工面轮廓推定出各接触位置的基础上,导出与实际接触的检测位置的误差,并以该误差的总和最小的方式识别c轴旋转中心坐标。
[0467]
如图45(b)或图46(b)所示,从球部中心观察的相对的c轴旋转中心位置被识别。如果c轴旋转中心位置被识别,则利用该位置能够测定刀尖的形状误差。
[0468]
图47示出测定刀尖形状误差的方法。移动控制部22使工件绕c轴旋转90度而,在预加工面上使刀尖以相同的刀尖位置接触的方式沿着曲线在多个点接触。图47表示沿着虚线所示的脊线在刀尖的z方向最低点与预加工面接触的情况。位置关系导出部23根据各接触点处的计算上的接触位置与检测出的接触位置的偏差量,来以与实施例6相同的方式测定刀尖形状的走样。
[0469]
以上,基于实施例对本公开进行了说明。本领域技术人员可以理解,该实施例是示例,这些各构成要素和各处理过程的组合可以有各种变形例,并且这样的变形例也包含在本公开的范围内。
[0470]
本公开的实施方式的概要如下。本公开的一个实施方式的切削装置具备:旋转机构,使安装有切削刀具或被切削材料的主轴旋转;进给机构,使切削刀具相对于被切削材料或部件相对移动;以及控制部,控制基于旋转机构的主轴的旋转及基于进给机构的切削刀具的相对移动。控制部具有以下功能:利用接触传感器的检测信息、或者与旋转机构和/或进给机构所包含的驱动电机相关的检测值的时序数据来获取切削刀具与被切削材料或部
件接触时的坐标值。控制部根据切削刀具在与车削加工时的切削刀具的旋转角度位置不同的至少两个位置与基准面接触时的坐标值,来确定切削刀具与被切削材料的旋转中心的相对位置关系,其中,基准面与车削加工后的被切削材料或与被切削材料的旋转中心的相对位置关系已知的。根据该方式,控制部根据两个以上的接触位置的坐标值来确定切削刀具与被切削材料的旋转中心的相对位置关系,由此不需要另外搭载用于测定位置关系的测定器等。
[0471]
本公开的另一个实施方式也是切削装置。该装置具备:旋转机构,使安装有切削刀具或被切削材料的主轴旋转;进给机构,使切削刀具相对于对象物相对移动;以及控制部,控制基于旋转机构的主轴的旋转及基于进给机构的切削刀具的相对移动。控制部具有以下功能:使切削刀具相对于具有已知形状的物体相对移动,并利用接触传感器的检测信息、或者与旋转机构和/或进给机构所包含的驱动电机相关的检测值的时序数据来获取切削刀具的刀尖与物体的已知形状部分接触时的坐标值。控制部根据切削刀具的刀尖在物体的已知形状部分的至少三个位置接触时的坐标值,来求出刀具刀尖的刀尖半径、刀具刀尖的中心坐标、刀具刀尖的形状误差中的至少一个。根据该方式,控制部能够根据三个以上的接触位置的坐标值来求出与刀具刀尖相关的值,不需要另外搭载测定器等。
[0472]
本公开的另一个实施方式也是切削装置。该装置具备:旋转机构,使安装有切削刀具或被切削材料的主轴旋转;进给机构,使切削刀具相对于被切削材料相对移动;以及控制部,控制基于旋转机构的主轴的旋转及基于进给机构的切削刀具的相对移动。控制部具有以下功能:利用接触传感器的检测信息、或者与旋转机构和/或进给机构所包含的驱动电机相关的检测值的时序数据,来获取切削刀具与被切削材料接触时的坐标值。控制部利用在切削加工时未利用的移动方向的基于进给机构的进给功能而使切削刀具相对于切削加工后的被切削材料相对移动,并根据切削刀具在至少两个位置接触时的坐标值,来确定切削刀具的安装误差、刀具刀尖的形状误差、切削刀具相对于被切削材料的相对移动方向的偏差中的至少一个。控制部利用在切削加工时未利用的移动方向的基于进给机构的进给功能,由此无需搭载测定器而能够确定切削刀具的安装误差、刀具刀尖的形状误差、切削刀具相对于被切削材料的相对移动方向的偏差中的至少一个。
[0473]
本发明的另一个实施方式也是切削装置。该装置具备:旋转机构,使安装有切削刀具或被切削材料的主轴旋转;进给机构,使切削刀具相对于被切削材料相对移动;以及控制部,根据与旋转机构和/或进给机构所包含的驱动电机相关的检测值的时序数据,来确定切削刀具与被切削材料的接触位置。控制部根据接触前所获取的检测值的第一时序数据和接触后所获取的检测值的第二时序数据来确定接触位置。根据该方式,控制部通过追溯至接触前的检测值进行分析,由此能够准确地导出切削刀具与被切削材料的接触时刻,并确定接触位置。
[0474]
控制部也可以获取包含超过了规定的阈值的检测值的第二时序数据。控制部也可以基于第一时序数据来设定规定的阈值。控制部也可以利用第一时序数据的平均值来设定规定的阈值。控制部也可以根据对第二时序数据进行回归分析而求出的回归方程和第一时序数据的平均值来确定接触位置。
[0475]
(附图标记说明)
[0476]
1:切削装置;2a:主轴;6:被切削材料;7:进给机构;8:旋转机构;
[0477]
11:切削刀具;20:控制部;21:旋转控制部;22:移动控制部;
[0478]
23:位置关系导出部;40:基准块;41:安装轴;42:支承装置;43:b轴工作台
[0479]
工业实用性
[0480]
本公开可用于使用切削刀具来切削被切削材料(工件)的切削装置。
再多了解一些
本文用于企业家、创业者技术爱好者查询,结果仅供参考。