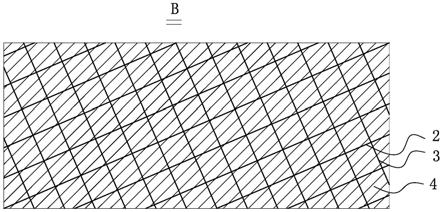
一种基于3d打印技术的抛丸梯度功能叶片成型方法
技术领域
1.该发明涉及抛丸叶片技术领域,具体是一种抛丸叶片的成型方法。
背景技术:
2.抛丸机是利用抛丸器射出高速弹丸轰击工件表面从而达到清理和强化等目的,而抛丸机叶片作为抛丸机的重要部件,其材料性能的高低直接决定了抛丸过程的效率和质量。
3.抛丸叶片在工作的过程中,电机带动其高速旋转,叶片不仅要受到弹丸对其的冲击,同时,弹丸在抛射出的瞬间,其还受到不同程度的磨损,而叶片的失效就是由于这两种损伤的共同结果。
4.首先,当叶片受到弹丸冲击时,周期性的应力作用对抛丸机叶片造成变形,而冲击留下的冲击坑使得材料变形从而向周围方向挤压,这就造成了材料会发生不同程度的应力集中。其次,弹丸抛射时对叶片的磨损,又加速了抛丸机叶片的变形和材料的流失。最终,叶片由于受到累积的周期应力的作用和磨损,会发生脱落、裂纹及变形等现象,最后直接造成叶片的断裂。
5.目前,抛丸机叶片主要使用模具钢,其中,cr元素主要参与其硬质相的组成,而添加的mo、v等元素虽然能对其冲击韧性、热加工性能等进行改善,但似乎耐磨性与其冲击韧性还是不尽人意,还有很大的改善空间。从材料性能的角度来讲,我们一般认为硬度越高的材料韧性就越低,恰巧在抛丸叶片的工况下,我们对这两种性能的需求最大,这就使设计人员对其材料与工艺方法的把握与挑选显得尤为重要。
技术实现要素:
6.为了解决现有技术的不足,本发明提供一种基于3d打印技术的抛丸梯度功能叶片成型方法,目的是通过不同的工艺与多种复合材料的有机结合,使其达到高硬度高韧性的目的,从而提高抛丸叶片的使用寿命,降低工业成本。
7.本发明解决其技术问题所采用的技术方案为:一种基于3d打印技术的抛丸梯度功能叶片成型方法,包括叶片基板成型;其特征在于,还包括如下步骤:
8.步骤1)、首先提供三种合金粉末:
9.第一合金粉末为耐磨相打印粉末,其元素质量分数配比为:c≤3%、cr:12%、b:6%、si:4%、fe:8%、ti:17%、co:10%,余量为ni;
10.第二合金粉末为增强相打印粉末;其元素质量分数配比为:c:1.5%、si:0.5%、mn:1%、s≤3%、p≤3%、cr:12%、mo:0.5%、v:0.3%,余量为fe;
11.第三合金粉末为基础相打印粉末;其元素质量分数配比为:c:1.5%、ni:33%、cr:8%、b:2%、si:3%,余量为fe;
12.步骤2)、以yg15模具钢为基板,在基板的上下两表面分别以基础相打印粉末为原材料进行激光3d打印;激光功率为1500w,送粉率为5l/min、打印速率为300mm/min、离焦量
为15mm;搭接率为45%,基础相层厚分别控制为1.5
±
0.1mm;
13.步骤3)、以所述的增强相打印粉末为原材料在基板两表面分别进行激光3d打印,制备多条线状的增强相层;打印激光功率为2000w、送粉率为4l/min、打印速度为500mm/min,打印增强相层时,在步骤2)yg15钢上打印的两基础相层表面分别进行,每一面的增强相层打印方向为沿基础相层对角线平行打印,打印方式为单道往复式;同一表面的增强相层第一方向打印结束后更换为第二方向交叉打印,打印时两种方向交叉的角度为90
°
,两种方向打印的两组线状的增强相层构成交叉网状;
14.步骤4)、利用耐磨相粉末打印以填充上、下表面的上述增强相层构成的交叉网状的菱形空隙,耐磨相粉末打印的激光功率为1800w、送粉率为6.5l/min、打印速率为500mm/min、离焦量为15mm;在同一表面每个菱形空隙内打印形成的耐磨菱形打印体高度与同表面上线状增强相层的壁高度相同;
15.步骤5)、最后,在所述的交叉网状区域及耐磨菱形打印体构成的区域两侧分别以增强相打印粉末打印凸台,铣床精加工后完成叶片总成。
16.作为本发明的进一步的技术方案:在基板的同一表面上,每道所述线状的增强相层壁高为1.5mm;且同一表面每个菱形空隙内打印形成的耐磨菱形打印体高为1.5mm。
17.更进一步的:所述线状的增强相层线宽为1cm。
18.进一步的:所述第一方向打印的线状增强相层为多条平行且间距相等,所述第二方向打印的线状增强相层为多条平行且间距相等。
19.更进一步的:所述第一方向打印的线状增强相层之间的间距与第一方向打印的线状增强相层之间的间距相等。
20.本发明的有益效果是:本发明主要通过材料、工艺方法两方面,对叶片在实际工况下的服役性能进行考量。利用3d打印技术,将两种不同性质的粉末通过高功率激光能量束进行合金的冶金结合,且该成型技术为一种熔池快速凝固、冷却的过程,成型后的合金与预期性能相差可忽略不计。其中,对耐磨相层与增强相层墙的材料设计,使得叶片具有较高的耐磨性能,同时增强相层墙分布在叶片内部,对叶片变形时起到了缓冲作用,且上述两种粉末皆为常用金属,经济性能良好。此外,该发明中耐磨相层在制备时,增强相层墙不易被融化;且耐磨相层与增强相层纸件制备完成后静应力小,性能好,不容易产生损坏。交叉夹角处因为熔塌产生的夹角变化能控制在
±
3.5
‑
5%;同时,对于三种增强相的熔覆工艺参数进行了优化,在保证其力学性能的前提下,结合三种粉末的热物性的差异进行的熔覆实验参数的设定,使其能够在打印某一种粉末的同时,另一种打印层在微观上与其呈现良好的冶金结合,且不会因激光束能量过高而发生大面积的塌陷,从而最大程度上发挥增强相与耐磨相的力学性能。
附图说明
21.下面结合附图和实施例对本发明进行进一步的解释和说明:
22.图1为叶片成型后的立体结构示意图;
23.图2为叶片成型后的截面示意图(图1的a向);
24.图3为本发明实施例中具体打印方向的示意图(图2的b处局部俯视放大示意图);
25.图4为打印完成后的增强相层、耐磨菱形打印体的剖视图;
26.图中:1基板,2第一方向的增强相层,3第二方向的增强相层,4耐磨菱形打印体,5凸台,6基础相层。
具体实施方式
27.如图1
‑
4所示,该基于3d打印技术的抛丸机叶片制备方法,包括叶片基体成型;其特征在于,还包括如下步骤:
28.步骤1)、首先提供两种合金粉末:
29.第一合金粉末为耐磨相打印粉末,其元素质量分数配比为:c≤3%、cr:12%、b:6%、si:4%、fe:8%、ti:17%、co:10%,余量为ni;
30.所述的耐磨相打印粉末以ni粉末为主体元素,其中添加的ti、b元素在熔池中通过原位自生成为tib2,tib2在熔池凝固过程中,逐渐生成tib,tib作为耐磨相层的主要支撑物,具有较高的硬度与耐磨性,因tib是原位自生形成,其在各元素在熔池中的流动性与润湿性颇高,这就使得tib在耐磨相层中分布主要为弥散分布;且cr元素与ni元素其形成的合金为单相奥氏体组织,且组织性能稳定,具有较好的塑性、韧性、冷冲压性与可焊性,能够满足3d打印技术对材料的基本要求与成型后叶片对工况的适应性。
31.第二合金粉末为增强相打印粉末;其元素质量分数配比为:c:1.5%、si:0.5%、mn:1%、s≤3%、p≤3%、cr:12%、mo:0.5%、v:0.3%,余量为fe;
32.所述增强相打印粉末作为以铁基粉末为主,主要适应yg15的热物性,同时其中添加的mo、v、mn元素,使得其冲击韧性和碳化物分布得到了较大程度的提升。
33.步骤2)、以yg15模具钢为基板1,基板尺寸根据具体叶片参数而定,该实施例选用的基板尺寸为157mm*74mm*3mm;在基板的上下两表面分别以基础相打印粉末为原材料进行激光3d打印;激光功率为1500w,送粉率为5l/min、打印速率为300mm/min、离焦量为15mm;搭接率为45%,基础相层6厚分别控制为1.5
±
0.1mm,如图2所示。
34.步骤3)、以所述的增强相打印粉末为原材料在基板两表面分别进行激光3d打印,制备多条线状的增强相层;打印激光功率为2000w、送粉率为4l/min、打印速度为500mm/min,因其为单道打印,故而搭接率没有实际意义,暂不进行设定;打印增强相层时,在步骤2)yg15钢上打印的两个基础相层表面分别进行,每一面的增强相层打印方向为沿基础相层对角线平行打印,打印方式为单道往复式,该实施例中打印出的第一方向的增强相层、第二方向的增强相层壁高均为1.5mm;第一方向打印结束后制成第一方向的增强相层2,再更换为第二方向交叉打印,制成第二方向的增强相层3,打印时两种方向交叉的角度为90
°
,两种方向打印的两组线状的增强相层构成交叉网状,如图3所示。
35.该实施例中,每道所述线状的增强相层壁高为1.5mm,线状的增强相层线宽为1cm。因为在3d打印过程中会产生熔塌,所以两种方向交叉的角度最终成型并不是绝对的90
°
,该方法成型后的角度变化控制在
±
3.5
‑
5%。在保证增强相层力学性能的前提下,结合三种粉末的热物性的差异进行的熔覆实验参数的设定,使其能够在打印某一种粉末的同时,另一种打印层在微观上与其呈现良好的冶金结合,且不会因激光束能量过高而发生大面积的塌陷,从而最大程度上发挥增强相与耐磨相的力学性能。
36.此外,该步骤中所述第一方向打印的线状增强相层2为多条平行且间距相等,所述第二方向打印的线状增强相层3也为多条平行且间距相等。
37.且所述第一方向打印的线状增强相层之间的间距与第一方向打印的线状增强相层之间的间距相等。
38.步骤4)、利用耐磨相粉末打印以填充上述增强相层构成的交叉网状的菱形空隙,耐磨相粉末打印的激光功率为1800w、送粉率为6.5l/min、打印速率为500mm/min、离焦量为15mm;在每个面的菱形空隙内打印形成的耐磨菱形打印体4高均为1.5mm;因为耐磨相粉末打印的过程中,势必会引起增强相层墙的少部分的熔化,这样,使得增强相层墙与耐磨相块的熔合区在互为交融,随着过冷度的变化,熔池逐渐凝固为冶金结合。
39.步骤5)、最后,在所述的交叉网状区域及耐磨菱形打印体构成的区域两侧(也即基板1的两侧位置)分别以增强相打印粉末打印凸台5,铣床精加工后完成叶片总成。
40.该方法利用3d打印技术,将两种不同性质的粉末通过高功率激光能量束进行合金的冶金结合,且该成型技术为一种熔池快速凝固、冷却的过程,成型后的合金与预期性能相差可忽略不计。其中,对耐磨相层与增强相层墙的材料设计,使得叶片具有较高的耐磨性能,同时增强相层墙分布在叶片内部,对叶片变形时起到了缓冲作用,且上述两种粉末皆为常用金属,经济性能良好。
41.上面所述的实施例仅仅是对本发明的优选实施方式进行描述,并非对本发明的范围进行限定,在不脱离本发明设计精神的前提下,本领域相关技术人员对本发明的各种变形和改进,均应扩如本发明权利要求书所确定的保护范围内。
再多了解一些
本文用于企业家、创业者技术爱好者查询,结果仅供参考。