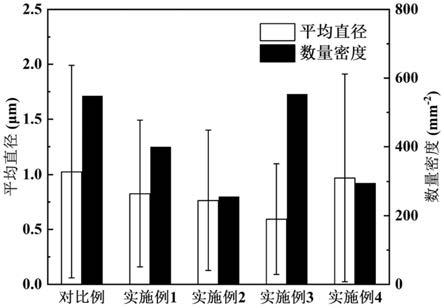
1.本发明属于冶金技术领域,特别涉及一种真空感应冶炼制备超低氧轴承钢铸锭的方法。
背景技术:
2.轴承是许多重要高端设备的关键基础部件,轴承服役的环境十分复杂,往往需要承受高接触应力、交变载荷以及滑动磨损,这就对轴承钢的各种性能,尤其是滚动疲劳接触寿命和稳定性提出了极高的要求。
3.为了提高轴承钢的寿命和稳定性,大量的研究发现轴承钢的疲劳寿命和稳定性与钢中的有害杂质元素含量尤其是氧含量有直接的关系,因此日本山阳特钢和瑞典ovaka均将轴承钢中氧含量控制在5ppm以下(isij,1985,71(14),1631
‑
1638);而当钢中氧含量足够低时,钢中的氮化钛夹杂、大尺寸脆性夹杂、偏析和液析碳化物成为了更重要的影响因素,因此为了满足航空轴承钢更高的质量要求,“真空感应熔炼 真空电弧重熔”(双真空熔炼工艺)成为了航空轴承钢的通用冶炼流程。
4.虽然双真空熔炼工艺虽然有利于脱气、改善偏析,但是该工艺过程中缺乏精炼渣吸附去除夹杂物,成品钢终点氧含量主要取决于原料中的氧含量,例如“一种极纯高碳铬轴承钢的冶炼生产方法”(cn2005100273940/2006)认为只有当真空感应熔炼原料中的氧含量不超过7ppm时,冶炼得到的成品钢中氧含量才会低于3ppm,而过高的原料洁净度要求势必会提高轴承钢的冶炼成本;此外钢中的夹杂物尺寸和分布特征也无法得到有效控制。
技术实现要素:
5.本发明的目的是提供一种真空感应冶炼制备超低氧轴承钢铸锭的方法,采用真空脱氧、铝脱氧和稀土镁处理的三步组合脱氧方法,有效降低钢的终点氧含量,提高钢液的洁净度水平,减小钢中的夹杂物尺寸和数量密度,降低真空感应冶炼对原料纯洁度的要求,采用全氧含量大于80ppm的原料,冶炼出氧含量不超过4ppm的超纯净轴承钢。
6.本发明的方法包括以下步骤:
7.(1)按轴承钢成分准备原料以及金属铝、稀土镁脱氧剂;将原料中碳源分为第一部分碳源和第二部分碳源;将原料中易挥发或易氧化的不同金属和/或合金置于真空感应炉的不同料仓中,将金属铝置于真空感应炉的单独的料仓中,将稀土镁脱氧剂置于真空感应炉的单独的料仓中,将第二部分碳源置于真空感应炉的单独的料仓中,将其余原料和第一部分碳源置于真空感应炉的坩埚内;
8.(2)启动真空感应炉,抽真空并升温至坩埚内物料开始熔化时,停止抽真空,向真空感应炉内充入氩气,当坩埚内的物料全部熔化后,将第二部分碳源加入坩埚内,再对真空感应炉抽真空,并控制温度使坩埚内物料处于熔融状态进行真空脱氧;
9.(3)真空脱氧结束后,向真空感应炉内充入氩气;将易挥发或易氧化的原料放入坩埚内,控制温度使坩埚内物料处于熔融状态;当坩埚内全部物料熔化后,将金属铝放入坩埚
内,控制温度使坩埚内物料处于熔融状态;当金属铝完全熔化后保温进行铝脱氧;
10.(4)铝脱氧结束后,将稀土镁脱氧剂放入坩埚内,控制温度使坩埚内物料处于熔融状态;当稀土镁脱氧剂完全熔化后,保温进行稀土镁脱氧。
11.上述方法中,稀土镁脱氧结束后,将坩埚内物料调节温度至浇注温度,然后进行浇注,获得超低氧轴承钢铸锭。
12.上述方法中,稀土镁脱氧剂为稀土镁合金;当轴承钢中含有镍时,稀土镁脱氧剂为稀土镁合金,或者为金属稀土和镁镍合金。
13.上述方法中,挥发或易氧化的原料包括硅源,锰源,钒源和铌源;其中硅源选用工业硅或硅铁合金,锰源选用电解锰或锰铁,钒源选用金属钒或钒铁合金,铌源选用金属铌或铌铁合金。
14.上述的步骤(2)中,第一次抽真空至真空感应炉内气压≤3pa,第二次抽真空至真空感应炉内气压≤20pa。
15.上述的步骤(2)和(3)中,向真空感应炉内充入氩气至气压为20000~40000pa。
16.上述的碳源选用石墨。
17.上述的易挥发或易氧化的原料包括硅源,锰源,钒源和铌源;其中硅源选用工业硅或硅铁合金,锰源选用电解锰或锰铁,钒源选用金属钒或钒铁合金,铌源选用金属铌或铌铁合金。
18.上述的步骤(2)中,真空脱氧时间10~60min。
19.上述的步骤(3)中,铝脱氧时间5~30min。
20.上述的步骤(4)中,稀土镁脱氧时间2~10min。
21.上述的金属稀土为金属铈或金属镧。
22.上述的镁镍合金按质量百分比含mg 20~25%,其余为ni。
23.上述的步骤(1)中,全部原料的总含氧量为80~280ppm。
24.上述的超低氧轴承钢铸锭的含氧量为0.1~4.0ppm。
25.上述的第一部分碳源占全部碳源质量的40~60%。
26.上述的步骤(3)中,金属铝加入量的计算公式为:
27.m1=(0.1~0.5)a/b
ꢀꢀꢀꢀꢀꢀꢀꢀ
(1);
28.式中,a为全部原料总质量,单位为t,b为al的收得率,m1为金属铝的加入量,单位kg;其中铝的收得率b选值为95~100%。
29.当稀土镁脱氧剂为稀土镁合金时,上述的步骤(4)中,稀土镁脱氧剂的加入量的计算公式为:
30.m2=(0.05~0.5)a/(c*d)
ꢀꢀꢀꢀꢀꢀꢀ
(2);
31.式中,a为全部原料总质量,单位为t,c为稀土的收得率,d为re在稀土镁合金中的质量百分比,m2为稀土镁脱氧剂的加入量,单位kg;其中稀土的收得率c选值为5~60%。
32.当稀土镁脱氧剂为金属稀土和镁镍合金时,上述的步骤(4)中,金属稀土的加入量的计算公式为:
33.m3=(0.05~0.5)a/(c*e)
ꢀꢀꢀꢀꢀꢀꢀ
(3);
34.式中,a为全部原料总质量,单位为t,c为稀土的收得率,e为re在金属稀土中的质量百分比,m3为金属稀土的加入量,单位kg;其中稀土的收得率c选值为5~60%;
35.镁镍合金的加入量的计算公式为:
36.m4=(0.01~0.05)a/(f*g)
ꢀꢀꢀꢀꢀꢀꢀ
(4);
37.式中,a为全部原料总质量,单位为t,f为镁的收得率,g为mg在镁镍合金中的质量百分比,m4为镁镍合金的加入量,单位kg;其中镁的收得率选值为1~20%。
38.相比现有技术,本发明具有以下有益效果:
39.(1)三步脱氧,化学反应充分,可以将原料中的氧从80ppm以上降低至4ppm以下;
40.(2)添加的稀土可以进一步降低钢中的氧、硫含量,降低钢中的夹杂物体积分数,并且可以对含铝夹杂物进行改性处理,将夹杂物无害化;
41.(3)添加的镁也可以和稀土夹杂物反应形成密度更小的含镁夹杂物,能够促进夹杂物的上浮,在浇注过程中停留在坩埚内;此外镁处理生成的夹杂物细小弥散,可以细化枝晶、显著改善铸锭的凝固组织。
附图说明
42.图1为本发明实施例中的超低氧轴承钢铸锭外观照片图;
43.图2为本发明实施例中超低氧轴承钢铸锭以及对比试验的夹杂物面积分数曲线图;
44.图3为本发明实施例中超低氧轴承钢铸以及对比试验的夹杂物数量密度
‑
平均直径曲线图。
具体实施方式
45.本发明实施例中的超低氧轴承钢铸锭的成分为m50航空轴承钢。
46.本发明实施例中按轴承钢成分准备原料为工业纯铁。
47.本发明实施例中工业纯铁中氧的质量含量0.0032%。
48.本发明实施例中金属铬中氧的质量含量0.131%。
49.本发明实施例中采用的坩埚材质为镁铝尖晶石。
50.本发明实施例中的金属铝为铝豆。
51.本发明实施例中加入稀土镁脱氧剂时,将稀土镁脱氧剂分别放置在不同料仓中,平均分为3~5批加入,当前一批稀土镁脱氧剂全部熔化后,再加入下一批。
52.本发明实施例中,稀土镁合金中按质量百分比含re 15~45%,mg 5~25%,其余为ni,其中re为la或ce。
53.本发明实施例中,准备原料按全部原料与稀土镁脱氧剂总量折算收得率计量。
54.本发明实施例中,全部原料的总含氧量为80~280ppm。
55.本发明实施例中,由于采用相同反应炉,因此收得率以及系数按相同取值计算。
56.以下为本发明优选实施例。
57.实施例1
58.按m50航空轴承钢的成分,准备原料工业纯铁、金属铬、钼条、金属钒、电解锰、石墨、铝豆(金属铝)、稀土金属和镁合金;稀土金属采用金属铈,纯度大于99%;镁合金采用镁镍合金,镁含量为20.62%;
59.将石墨分为第一部分石墨和第二部分石墨;第一部分石墨占全部石墨质量的
60%;
60.将工业纯铁、金属铬、钼条和第一部分石墨置于真空感应炉的坩埚内;
61.将第二部分石墨、电解锰、金属钒、铝豆、镁镍合金和金属铈按顺序依次放入真空感应炉的不同料仓中;
62.启动真空感应炉,抽真空至气压≤3pa,并升温至坩埚内物料开始熔化时,停止抽真空,向真空感应炉内充入氩气至气压为40000pa;采用30kg真空感应炉,开始时功率10kw,功率达到40kw时开始熔化;
63.坩埚内的物料全部熔化后,将第二部分石墨加入坩埚内,再对真空感应炉抽真空至压力≤20pa,控制温度使坩埚内物料处于熔融状态,并保温30min进行真空脱氧;
64.真空脱氧结束后,向真空感应炉内充入氩气至气压为40000pa;将电解锰和金属钒放入坩埚内,控制温度使坩埚内物料处于熔融状态;当坩埚内全部物料熔化后,将铝豆放入坩埚内,控制温度使坩埚内物料处于熔融状态;当铝豆完全熔化后,保温5min进行铝脱氧;
65.铝脱氧结束后,将镁镍合金和金属铈放入坩埚内,控制温度使坩埚内物料处于熔融状态;当稀土镁脱氧剂完全熔化后,保温3min进行稀土镁脱氧;
66.稀土镁脱氧结束后,将坩埚内物料调节温度至浇注温度,然后进行浇注,获得超低氧轴承钢铸锭;
67.铝豆的加入量m1=0.15a/99%=0.15kg/t;
68.金属铈的加入量m3=0.25a/(50%*99%)=0.51kg/t;
69.镁镍合金加入量m4=0.04a/(5%*20.62%)=3.88kg/t;
70.超低氧轴承钢铸锭的o含量为0.00013%,s含量为0.0010%;
71.超低氧轴承钢铸锭的外观照片如图1所示,夹杂物面积分数曲线如图2所示,夹杂物数量密度
‑
平均直径曲线如图3所示;
72.采用相同原料,按传统真空脱氧方法,进行相同材料的制备,进行对比试验,获得的铸锭o含量为0.0020%,s含量为0.0021%,铸锭的外观照片如图1所示,夹杂物面积分数曲线如图2所示,夹杂物数量密度
‑
平均直径曲线如图3所示。
73.实施例2
74.方法同实施例1,不同点在于:
75.(1)第一部分石墨占全部石墨质量的50%;
76.(2)坩埚内物料开始熔化时,停止抽真空,充入氩气至气压为30000pa;
77.(3)保温40min进行真空脱氧;
78.(4)保温10min进行铝脱氧;
79.(5)保温6min进行稀土镁脱氧;
80.(6)金属铈的加入量m3=0.15a/(50%*99%)=0.3kg/t;镁镍合金加入量m4=0.02a/(5%*20.62%)=1.94kg/t;超低氧轴承钢铸锭的o含量为0.00027%,s含量为0.0015%。
81.实施例3
82.方法同实施例1,不同点在于:
83.(1)金属稀土采用金属镧,纯度大于99%;第一部分石墨占全部石墨质量的40%;
84.(2)坩埚内物料开始熔化时,停止抽真空,充入氩气至气压为20000pa;
85.(3)保温30min进行真空脱氧;
86.(4)保温3min进行稀土镁脱氧;
87.(5)金属镧的加入量m3=0.25a/(50%*99%)=0.51kg/t;镁镍合金加入量m4=0.02a/(5%*20.62%)=1.94kg/t;超低氧轴承钢铸锭的o含量为0.00016%,s含量为0.0010%。
88.实施例4
89.方法同实施例1,不同点在于:
90.(1)稀土镁脱氧剂为稀土镁合金,按质量百分比含ce 30%,mg 15%,其余为ni;
91.(2)第一部分石墨占全部石墨质量的55%;将稀土镁合金置于一个料仓中;
92.(3)坩埚内物料开始熔化时,停止抽真空,充入氩气至气压为35000pa;
93.(4)保温60min进行真空脱氧;
94.(5)真空脱氧结束后,充入氩气至气压为30000pa;
95.(6)保温10min进行铝脱氧;
96.(7)铝脱氧结束后,将稀土镁合金放入坩埚内;保温5min进行稀土镁脱氧;
97.(8)稀土镁合金的加入量m2=0.2a/(30%*30%)=2.22kg/t;超低氧轴承钢铸锭的o含量为0.00040%,s含量为0.0010%。
98.实施例5
99.方法同实施例1,不同点在于:
100.(1)稀土镁脱氧剂为稀土镁合金,按质量百分比含la 45%,mg 5%,其余为ni;
101.(2)第一部分石墨占全部石墨质量的55%;将稀土镁合金置于一个料仓中;
102.(3)坩埚内物料开始熔化时,停止抽真空,充入氩气至气压为30000pa;采用10kg真空感应炉,真空感应炉开始时功率5kw,功率达到15kw时开始熔化;
103.(4)保温10min进行真空脱氧;
104.(5)真空脱氧结束后,充入氩气至气压为20000pa;
105.(6)铝脱氧结束后,将稀土镁合金放入坩埚内;保温2min进行稀土镁脱氧;
106.(7)稀土镁合金的加入量m2=0.2a/(30%*45%)=1.48kg/t;超低氧轴承钢铸锭的o含量为0.00038%,s含量为0.0012%。
107.实施例6
108.方法同实施例1,不同点在于:
109.(1)稀土镁脱氧剂为稀土镁合金,按质量百分比含la 15%,mg 25%,其余为ni;
110.(2)第一部分石墨占全部石墨质量的45%;将稀土镁合金置于一个料仓中;
111.(3)坩埚内物料开始熔化时,停止抽真空,充入氩气至气压为25000pa;采用100kg真空感应炉,真空感应炉开始时功率20kw,功率达到100kw时开始熔化;
112.(4)保温30min进行铝脱氧;
113.(5)铝脱氧结束后,将稀土镁合金放入坩埚内;保温10min进行稀土镁脱氧;
114.(6)稀土镁合金的加入量m2=0.1a/(30%*15%)=2.22kg/t;超低氧轴承钢铸锭的o含量为0.00033%,s含量为0.0011%。
115.实施例7
116.方法同实施例1,不同点在于:
117.(1)第一部分石墨占全部石墨质量的50%;
118.(2)坩埚内物料开始熔化时,停止抽真空,充入氩气至气压为30000pa;采用1t真空感应炉,真空感应炉开始时功率120kw,功率达到380kw时开始熔化;
119.(3)保温60min进行真空脱氧;
120.(4)保温20min进行铝脱氧;
121.(5)保温8min进行稀土镁脱氧;
122.(6)金属铈的加入量m3=0.2a/(50%*99%)=0.4kg/t;镁镍合金加入量m4=0.02a/(5%*20.62%)=1.94kg/t;超低氧轴承钢铸锭的o含量为0.00029%,s含量为0.0014%。
再多了解一些
本文用于企业家、创业者技术爱好者查询,结果仅供参考。