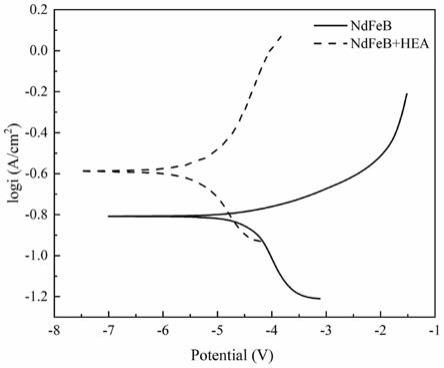
1.本发明防腐涂层技术领域,特别涉及一种在钕铁硼表面制备耐蚀涂层的方法。
背景技术:
2.1984年日本住友特殊金属公司采用粉末冶金法首先制备出以nd2fe14b化合物为基体的烧结钕铁硼永磁合金,开创了第三代永磁材料。钕铁硼永磁材料具有高内禀矫顽力,高剩磁和高磁能积等特点被广泛应用于新能源汽车、节能变频空调、电子、医疗及智能制造领域。钕铁硼磁体由于其特殊烧结工艺,其本身存在大量的孔隙和疏松,具有温度稳定性差,容易发生氧化腐蚀的缺陷;此外,由于钕铁硼磁体本身为多相组织,各相间存在较大的化学电位差,导致晶间富钕相和复硼相优先分解,使nd2fe
14
b遭到破坏,严重影响其磁性能,从而影响其机械性能和使用性能。
3.目前,提高烧结钕铁硼永磁体抗腐蚀性能的方法主要有合金化法和表面防护处理法。合金化法是在钕铁硼永磁体中添加合金元素,例如,co元素可以形成富nd相或金属化合物,金属化合物在晶界上的偏析提高了晶界的耐蚀性,但是合金元素的加入会在一定程度上降低钕铁硼永磁体的磁性能。
4.表面防护处理法主要有磷化处理、电镀和电泳涂覆等。现有的表面防护处理形成的涂层主要为有机类涂层,其防腐效果尚不能达到较高的水平。
技术实现要素:
5.有鉴于此,本发明目的在于一种在钕铁硼表面制备耐蚀涂层的方法。本发明提供的方法所得涂层具有优异的耐腐蚀性。
6.为了实现上述发明目的,本发明提供以下技术方案:
7.本发明提供了一种在钕铁硼表面制备耐蚀涂层的方法,包括以下步骤:
8.在钕铁硼基体表面热喷涂涂层原料,得到耐蚀涂层;
9.所述涂层原料为陶瓷和/或高熵合金,所述陶瓷为ti4o7和/或cro2,所述高熵合金为fecocrnimn、fecocrnial、alcocunisiti、alcocrfeniti和cocrfeninb中的一种或几种。
10.优选的,所述耐蚀涂层的厚度为20~50μm。
11.优选的,所述涂层原料为陶瓷时,所述热喷涂为等离子喷涂;
12.所述涂层原料为高熵合金时,所述热喷涂为超音速火焰喷涂。
13.优选的,所述等离子喷涂的主气为氩气,所述主气的流量为2~3.5m3/h;
14.所述等离子喷涂的辅气为氢气,所述辅气的流量为0.3~0.8m3/h。
15.优选的,所述等离子喷涂的电流为600~900a,送粉率为20~40g/min,喷涂距离为60~90mm,单次喷涂的厚度≤15μm。
16.优选的,所述超音速火焰喷涂的燃料气体为煤油,所述燃料气体的流量为5~6.5gal/h;
17.所述超音速火焰喷涂的助燃气体为氧气,所述助燃气体的流量为1600~
2200scfh;
18.所述超音速火焰喷涂的送粉气体为氮气,所述送粉气体的流量为20~30scfh。
19.优选的,所述超音速火焰喷涂的送粉率为20~70g/min,喷涂距离为300~380mm,单次喷涂的厚度≤10μm。
20.优选的,所述热喷涂时钕铁硼基体的温度为25~70℃。
21.优选的,所述热喷涂前,还包括对所述钕铁硼基体进行预处理,所述预处理为:
22.对所述钕铁硼基体依次进行酸洗、干燥和喷砂处理。
23.优选的,所述热喷涂后,还包括对所得涂层进行封孔处理。
24.本发明提供了一种在钕铁硼表面制备耐蚀涂层的方法,包括以下步骤:在钕铁硼基体表面热喷涂涂层原料,得到耐蚀涂层;所述涂层原料为陶瓷和/或高熵合金,所述陶瓷为ti4o7和/或cro2,所述高熵合金为fecocrnimn、fecocrnial、alcocunisiti、alcocrfeniti和cocrfeninb中的一种或几种。本发明以陶瓷和/或高熵合金作为涂层原料,其中陶瓷为ti4o7和/或cro2,所述高熵合金为fecocrnimn、fecocrnial、alcocunisiti、alcocrfeniti和cocrfeninb中的一种或几种,这些材料具有优异的耐腐蚀性能,在钕铁硼基体表面形成涂层后能够有效提高钕铁硼基体的腐蚀电位,并降低腐蚀电流密度;本发明采用热喷涂的方式喷涂涂层原料,具有工艺简单、加工效率高、涂层结合力高的优点。
附图说明
25.图1是本发明实施例1制备得到的具有高熵合金涂层的钕铁硼磁体以及钕铁硼磁体的动电位极化曲线图;
26.图2是本发明实施例2制备得到的具有cro2涂层的钕铁硼磁体以及钕铁硼磁体的动电位极化曲线图;
27.图3是本发明实施例3制备得到的具有ti4o7涂层的钕铁硼磁体以及钕铁硼磁体的动电位极化曲线图。
具体实施方式
28.本发明提供了一种在钕铁硼表面制备耐蚀涂层的方法,包括以下步骤:
29.在钕铁硼基体表面热喷涂涂层原料,得到耐蚀涂层;
30.所述涂层原料为陶瓷和/或高熵合金,所述陶瓷为ti4o7和/或cro2,所述高熵合金为fecocrnimn、fecocrnial、alcocunisiti、alcocrfeniti和cocrfeninb中的一种或几种。
31.本发明对所述钕铁硼基体的成分、规格没有特殊的要求,本领域熟知的钕铁硼基体均能使用本发明提供的方法制备耐腐蚀涂层。作为本发明的一个具体实施例,所述钕铁硼基体的规格为13
×
13
×
3mm。
32.在本发明中,所述热喷涂前,还包括对所述钕铁硼基体进行预处理,所述预处理优选为:
33.对所述钕铁硼基体依次进行酸洗、干燥和喷砂处理。
34.在本发明中,所述酸洗用酸洗剂优选为硝酸溶液,所述硝酸溶液的质量浓度优选为3~8%,更优选为5%。本发明对所述酸洗的方式没有特殊的要求,使用本领域技术人员熟知的酸洗方式即可。
35.本发明对所述干燥的方式没有特殊的要求,使用本领域技术人员熟知的干燥方式即可。
36.在本发明中,所述喷砂处理使用的砂料为白刚玉,所述砂料的粒径优选为20~46目,更优选为30~40目。在本发明中,所述喷砂处理时喷砂的角度优选为60~80
°
,更优选为70
°
;喷砂的距离优选为80~100mm,更优选为90mm。在本发明中,所述喷砂处理时的空气压力优选为0.4~0.5mpa,更优选为0.45mpa。在本发明中,所述喷砂处理后钕铁硼基体的表面粗糙度优选为8~12μm,更优选为9~10μm。
37.在本发明中,所述耐蚀涂层的厚度优选为20~50μm,更优选为30~40μm。
38.在本发明中,所述涂层原料为陶瓷和/或高熵合金,所述陶瓷为ti4o7和/或cro2。当所述陶瓷为ti4o7和cro2时,本发明对二者的比例没有特殊的要求。在本发明中,所述陶瓷的粒度优选为20~70μm,更优选为40~50μm。
39.在本发明中,所述高熵合金为fecocrnimn、fecocrnial、alcocunisiti、alcocrfeniti和cocrfeninb中的一种或几种。在本发明中,所述fecocrnimn中fe、co、cr、ni、mn元素的原子比优选为1:1:1:1:1;所述fecocrnial中fe、co、cr、ni、al元素的原子比优选为1:1:1:1:1;所述alcocunisiti中al、co、cu、ni、si、ti元素的原子比优选为1:1:1:1:1:1;所述alcocrfeniti中al、co、cr、fe、ni、ti元素的原子比优选为1:1:1:1:1:1;所述cocrfeninb中co、cr、fe、ni、nb元素的原子比优选为1:1:1:1:1。在本发明中,所述高熵合金的粒度优选为15~50μm,更优选为30~40μm。
40.在本发明中,所述热喷涂时钕铁硼基体的温度优选为25~70℃,更优选为40~60℃。
41.在本发明中,当所述涂层原料为陶瓷时,所述热喷涂为等离子喷涂。在本发明中,所述等离子喷涂的主气优选为氩气,所述主气的流量优选为2~3.5m3/h,更优选为2.5~3m3/h;所述等离子喷涂的辅气优选为氢气,所述辅气的流量优选为0.3~0.8m3/h,更优选为0.4~0.6m3/h。
42.在本发明中,所述等离子喷涂的电流优选为600~900a,更优选为700~800a;送粉率优选为20~40g/min,更优选为25~35g/min;喷涂距离优选为60~90mm,更优选为70~80mm;单次喷涂的厚度优选≤15μm,更优选为10~15μm。
43.在本发明中,当所述涂层原料为高熵合金时,所述热喷涂为超音速火焰喷涂。在本发明中,所述超音速火焰喷涂的燃料气体优选为煤油,更优选为航空煤油;所述燃料气体的流量优选为5~6.5gal/h,更优选为5.5~6gal/h;所述超音速火焰喷涂的助燃气体优选为氧气,所述助燃气体的流量优选为1600~2200scfh,更优选为1800~2000scfh;所述超音速火焰喷涂的送粉气体优选为氮气,所述送粉气体的流量优选为20~30scfh,更优选为25scfh。
44.在本发明中,所述超音速火焰喷涂的送粉率优选为20~70g/min,更优选为40~60g/min;喷涂距离优选为300~380mm,更优选为320~350mm;单次喷涂的厚度优选≤10μm,更优选为5~10μm。
45.所述热喷涂后,本发明还优选包括对所得涂层进行封孔处理。在本发明中,所述封孔处理为:将封孔剂涂覆于涂层表面。
46.在本发明中,所述封孔剂优选为石蜡或树脂。在本发明中,所述封孔剂的涂覆量优
选为100~200g/m2,更优选为140~160g/m2。
47.下面结合实施例对本发明提供的在钕铁硼表面制备耐蚀涂层的方法进行详细的说明,但是不能把它们理解为对本发明保护范围的限定。
48.实施例1
49.一种在钕铁硼表面制备耐蚀涂层的方法,包括以下步骤:
50.(1)喷砂处理:选用规格为13
×
13
×
3mm的商用块状烧结钕铁硼磁体,喷涂前将基体用5%的硝酸溶液进行酸洗干净并烘干,在用白刚玉喷砂粗化处理,喷砂角度为80
°
,空气压力为0.5mpa,喷砂距离为100mm,喷砂毛化处理后的基体表面粗糙度为10μm。
51.(2)采用超音速火焰热喷涂技术将涂层原料涂覆在烧结钕铁硼磁体表面制备热喷涂涂层,采用的涂层原料为高熵合金fecocrnimn,粒度为15~50μm。超音速火焰热喷涂工艺条件如下:燃料气体为航空煤油,煤油流量为5.5gal/h,助燃气体为氧气,氧气流量为2000scfh,送粉气体为氮气,氮气流量为23scfh;送粉率为50g/min,喷涂距离为350mm,控制单次厚度≤10μm。
52.(3)将形成的热喷涂涂层在常温条件下,用刷子均匀将封孔剂石蜡涂在表面,待室温下干燥。
53.所得具有高熵合金涂层的钕铁硼磁体以及单纯钕铁硼磁体的动电位极化曲线图如图1所示。由图1可以看出,具有高熵合金涂层的钕铁硼磁体的腐蚀电位较钕铁硼基体提高2.21mv,而腐蚀电流密度较钕铁硼基体降低1个数量级。
54.实施例2
55.一种在钕铁硼表面制备耐蚀涂层的方法,包括以下步骤:
56.(1)磁体预处理:选用规格为13
×
13
×
3mm的商用块状烧结钕铁硼磁体,喷涂前将基体用8%的硝酸溶液进行酸洗干净并烘干,在用白刚玉喷砂粗化处理,喷砂角度为80
°
,空气压力为0.5mpa,喷砂距离为100mm,喷砂毛化处理后的基体表面粗糙度为8~12μm。
57.(2)采用等离子喷涂技术将喷涂材料涂覆在烧结钕铁硼磁体表面制备涂层,采用涂层材料为cro2,粒度为20~70μm。所述等离子喷涂的工艺为:喷涂主气为氩气,氩气流量为3.5m3/h,喷涂辅气为氢气,氢气流量为0.4m3/h;电流为800a,送粉率为35g/min,喷涂距离为80mm,控制单次厚度≤15μm。
58.(3)将形成的热喷涂涂层在常温条件下,用刷子均匀将封孔剂石蜡涂在表面,待室温下干燥。
59.所得具有cro2涂层的钕铁硼磁体以及单纯钕铁硼磁体的动电位极化曲线图如图2所示。由图2可以看出,具有cro2涂层的钕铁硼磁体的腐蚀电位较钕铁硼基体提高45mv,而腐蚀电流密度较钕铁硼基体降低1个数量级。
60.实施例3
61.一种在钕铁硼表面制备耐蚀涂层的方法,包括以下步骤:
62.(1)磁体预处理:选用规格为13
×
13
×
3mm的商用块状烧结钕铁硼磁体,喷涂前将基体用6%的硝酸溶液进行酸洗干净并烘干,在用白刚玉喷砂粗化处理,喷砂角度为70
°
,空气压力为0.5mpa,喷砂距离为100mm,喷砂毛化处理后的基体表面粗糙度为8~12μm。
63.(2)采用等离子喷涂技术将喷涂材料涂覆在烧结钕铁硼磁体表面制备涂层,采用涂层材料为ti4o7,粒度为20~90μm。所述等离子喷涂的工艺为:喷涂主气为氩气,氩气流量
为3.5m3/h,喷涂辅气为氢气,氢气流量为0.35m3/h;电流为700a,送粉率为30g/min,喷涂距离为75mm,控制单次厚度≤15μm。
64.(3)将形成的热喷涂涂层在常温条件下,用刷子均匀将封孔剂石蜡涂在表面,待室温下干燥。
65.所得具有ti4o7涂层的钕铁硼磁体以及单纯钕铁硼磁体的动电位极化曲线图如图3所示。由图3可以看出,具有ti4o7涂层的钕铁硼磁体的腐蚀电位较钕铁硼基体提高83mv,而腐蚀电流密度较钕铁硼基体降低1个数量级。
66.以上所述仅是本发明的优选实施方式,应当指出,对于本技术领域的普通技术人员来说,在不脱离本发明原理的前提下,还可以做出若干改进和润饰,这些改进和润饰也应视为本发明的保护范围。
再多了解一些
本文用于企业家、创业者技术爱好者查询,结果仅供参考。