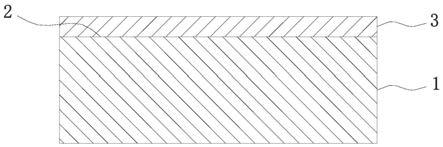
1.本发明属于电子产品装饰技术领域,尤其涉及一种电子终端的壳体、壳体制备方法及电子终端。
背景技术:
2.陶瓷材料具有高硬度、高强度,以及温润如玉的质感,近年来备受关注,已有厂商将陶瓷材料用作消费类电子产品的壳体材料;黄金具有璀璨的外观和金属质感,给人一种尊贵感和富丽感,同时还具有优异的耐腐蚀性能。一些手机的壳体表面会采用黄金进行装饰,通常采用电镀、上釉、喷漆的方式,然而采用相关技术手段制备的壳体表面黄金质感不强、附着力不强、不耐刮擦,影响用户体验。
技术实现要素:
3.为解决上述技术问题,本发明的实施方式提供了一种电子终端的壳体、壳体制备方法及电子终端。
4.本发明实施方式的电子终端的壳体,包括:
5.基体,所述基体包括表面处理区;和
6.覆盖所述表面处理区的金膜,所述金膜的颜色具有65.0-95.0内的l值、-10.0-5.0内的a值和20.0-40.0内的b值,所述金膜的厚度大于100nm。
7.本发明实施方式的壳体制备方法包括步骤:
8.对陶瓷需装饰的表面进行表面处理,形成表面处理区;
9.在陶瓷的所述表面处理区施加金涂料,所述金涂料包括金属树脂酸盐、填充剂和有机溶剂,所述金涂料包括金属成分及其重量百分比如下:au 5-20%、pt 0.01-0.5%、bi 0.25-0.5%、rh 0.05-0.1%,所述金涂料还包括金属成分及其重量百分比如下cr 0.05-0.1%和/或ni 0-0.1%;
10.对施加好金涂料的所述陶瓷进行烘烤,烘烤的最高温度范围在700-850℃内,烘烤时在所述最高温度范围内的持续时间在20-60min内,使所述金涂料在所述表面处理区形成金膜。
11.本发明实施方式的电子终端,包括如上所述的壳体。
12.本发明实施方式的电子终端的壳体、壳体制备方法及电子终端中,陶瓷壳体表面的黄金膜层具有强烈黄金质感、附着力强且耐刮擦,能够提升用户体验。
附图说明
13.图1是本发明的第一种实现方式的电子终端的壳体的剖面示意图;
14.图2是本发明的第二种实现方式的电子终端的壳体的剖面示意图;
15.图3是本发明的第三种实现方式的电子终端的壳体的剖面示意图;
16.图4是本发明的第四种实现方式的电子终端的壳体的剖面示意图;
90.0内的l值、-6.0-4.0内的a值和24.0-36.0内的b值。如此,壳体的表面可以既有彩釉效果又有强烈的黄金效果,外观颜色更加丰富。
30.根据本发明的实施例,金膜3的厚度可以进一步地设置在100-200nm。在这个厚度一方面可以使外壳具有强烈的黄金质感,耐刮擦,另一方面可以节约金涂料的使用,降低成本。
31.在本发明的一些实施例中,基体1的材料为陶瓷且包括氧化锆、氧化钛、氧化钇、氧化铝、氧化硅、碳化硅、碳化钨、碳化钨-钴和碳化钨-钴-铬中的至少一种。采用上述材料可以使壳体的外观表面硬度更高,耐磨性更好,且触感更佳。
32.在本发明实施例的第二个方面,提出了一种壳体制备方法。
33.根据本发明的实施例,如图5所示,壳体制备方法包括步骤:
34.s100、对陶瓷需装饰的表面进行表面处理,形成表面处理区;
35.s200、在陶瓷的表面处理区施加金涂料,金涂料包括金属树脂酸盐、填充剂和有机溶剂,金涂料包括金属成分及其重量百分比如下:au(金)5-20%、pt(铂)0.01-0.5%、bi(铋)0.25-0.5%、rh(铑)0.05-0.1%,金涂料还包括金属成分及其重量百分比如下cr(铬)0.05-0.1%和/或ni(镍)0-0.1%;
36.s300、对施加好金涂料的陶瓷进行烘烤,烘烤的最高温度范围在700-850℃内,烘烤时在最高温度范围内的持续时间在20-60min内,使金涂料在表面处理区形成金膜。
37.通过不同的表面处理后在陶瓷上形成的表面处理区可以具有不同的表面效果,之后在表面处理区施加金涂料,金涂料中的金和铂为显色物质,能使最后形成的金膜具有更高的亮度,铋、铑、铬、镍为助熔剂,作用是提升金膜与陶瓷基材的结合力,提升金膜的耐磨性,其中铑和铬也能提升最后形成的金膜的亮度,施加完金涂料之后进行烘烤,最终在陶瓷表面形成厚度为100-200nm金膜,各金属成分按上述重量百分比配制且烘烤过程按上述条件进行可以使加工形成的金膜与陶瓷之间具有更高的附着力、黄金效果更加强烈、耐刮擦且更加节约成本,并且工艺简单适于工业生产。
38.在金涂料中,au(金)的质量百分比可以为5%、6%、7%、8%、9%、10%、11%、12%、13%、14%、15%、16%、17%、18%、19%、20%等;pt(铂)的质量百分比可以为0.01%、0.05%、0.10%、0.15%、0.20%、0.25%、0.30%、0.35%、0.40%、0.45%、0.50%等;bi(铋)的质量百分比可以为0.25%、0.26%、0.27%、0.28%、0.29%、0.30%、0.31%、0.32%、0.33%、0.34%、0.35%、0.36%、0.37%、0.38%、0.39%、0.40%、0.41%、0.42%、0.43%、0.44%、0.45%、0.46%、0.47%、0.48%、0.49%、0.50%等;rh(铑)的质量百分比可以为0.05%、0.06%、0.07%、0.08%、0.09%、0.10%等;cr(铬)的质量百分比可以为0.05%、0.06%、0.07%、0.08%、0.09%、0.10%等;ni(镍)的质量百分比可以为0.01%、0.02%、0.03%、0.04%、0.05%、0.06%、0.07%、0.08%、0.09%、0.10%等。
39.在烘烤的过程中,最高温度可以是700℃、705℃、710℃、715℃、720℃、735℃、740℃、745℃、750℃、755℃、760℃、765℃、770℃、775℃、780℃、785℃、790℃、795℃、800℃、805℃、810℃、815℃、820℃、835℃、840℃、845℃、850℃等;烘烤时在最高温度范围内的持续时间可以为20min、25min、30min、35min、40min、45min、50min、55min、60min等。
40.本发明的实施例提供四种对陶瓷表面进行表面处理的实现方式:
41.如图6所示,在第一种实现方式中,对陶瓷需装饰的表面进行表面处理包括:
42.s101、对陶瓷需装饰的表面进行抛光,使抛光后的表面的粗糙度ra<50nm,获得高光效果。抛光方式可以是钻石抛光、水和抛光、火焰抛光、机械化学抛光、湿式化学抛光等,只要能使陶瓷抛光后的表面粗糙度达到ra<50nm的效果即可。通过这种实现方式的表面处理,后续形成的金膜具有光滑且高亮的外观效果。
43.如图7所示,在第二种实现方式中,对陶瓷需装饰的表面进行表面处理包括:
44.s102、对陶瓷需装饰的表面进行喷砂处理,使喷砂后的表面获得哑光效果。
45.具体的,在本实现方式中,喷砂处理中使用的砂粒材料为金刚砂或刚玉砂,砂粒目数在10-200目内,优选的,砂粒目数可以在50-150目以内,这样可以使陶瓷表面得到具有一定粗糙度的哑光效果,通过这种实现方式的表面处理,后续形成的金膜可以具有哑光的外观效果且具有适度粗糙的触感。
46.如图8所示,在第三种实现方式中,对陶瓷需装饰的表面进行表面处理包括:
47.s103、对陶瓷需装饰的表面进行镭雕处理(镭雕也叫激光雕刻,是指材料在激光照射下瞬间的熔化和气化,从而在材料表面留下图形或文字),使镭雕后的表面形成字符、纹理和图形中任意一种或多种的组合。
48.本实现方式中,镭雕处理中的镭雕深度在0.1-100μm内,通过这种实现方式的表面处理,可以使后续形成金膜为具有深度的字符、纹理和图形等。
49.如图9所示,在第四种实现方式中,对陶瓷需装饰的表面进行表面处理包括:
50.s104、对陶瓷需装饰的表面进行上釉处理,使陶瓷的表面形成彩釉效果,彩釉效果包括字符、纹理和图形中任意一种或多种的组合,上釉处理过程中釉料的烧结温度大于900℃。通过这种实现方式的表面处理,可以使后续形成的金膜效果与彩釉效果相结合,使陶瓷表面的外观效果更加丰富。
51.对同一陶瓷的表面可以任选上述四种实现方式中的一种进行处理,也可以在上述四种实现方式中同时选择多种进行处理。上述四种实现方式的表面处理仅仅是示例,本发明中的表面处理并不限于上述四种实现方式。
52.对陶瓷进行表面处理之后,还包括步骤:
53.s110、将表面处理好的陶瓷进行清洗,以去除陶瓷表面的油污,从而保证后续加工过程中金膜与陶瓷之间的结合力。
54.本发明中,填充剂包括松香、硝化松香、硫化树脂中的至少一种,以促进烘烤过程中金膜的形成;有机溶剂包括樟脑油、松节油、环己醇、四氯萘、乙酸正丁酯中的至少一种,作用为保证金涂料的存储稳定性,调节金涂料的粘度和施工度。
55.金涂料中金属树脂酸盐、填充剂和有机溶剂的重量百分比的范围依次分别在35-60%、10-45%、10-45%。
56.本发明中,提供两种形式的金涂料,其中一种金涂料是金水形式,金水中金属树脂酸盐、填充剂和有机溶剂的重量百分比的范围依次分别在35-55%、10-25%和25-45%,金水为胶体溶液,金水的粘度为30-100cst(厘斯),本发明中金水形式的金涂料采用笔描、刷涂、喷涂或淋涂等方式施加到陶瓷的表面。金水形式时,金属树脂酸盐的重量百分比可以是35%、36%、37%、38%、39%、40%、41%、42%、43%、44%、45%、46%、47%、48%、49%、50%、51%、52%、53%、54%、55%等;填充剂的重量百分比可以是10%、11%、12%、13%、14%、15%、16%、17%、18%、19%、20%、21%、22%、23%、24%、25%等;有机溶剂的重量
百分比可以是25%、26%、27%、28%、29%、30%、31%、32%、33%、34%、35%、36%、37%、38%、39%、40%、41%、42%、43%、44%、45%等。
57.另一种金涂料是金膏形式,金膏中金属树脂酸盐、填充剂和有机溶剂的重量百分比的范围依次分别在40-60%、25-45%和10-30%,金膏的粘度为500-2000pa
·
s,金膏可以通过丝印方式施加到陶瓷的表面处理区,也可以通过将金膏丝印到花纸上,之后将花纸贴在陶瓷的表面处理区,本发明中丝印网版丝印网版的目数为100-500目,网版目数太大则图案不清晰,网版目数太小则印金膏太薄,烧出的金层容易出现薄金、红边等现象,本发明设置的丝印网版的目数可以使丝印出的金膏图案清晰且厚度均匀,从而保证最后形成的金膜的外观效果和质量。金膏形式时,金属树脂酸盐的重量百分比可以是40%、41%、42%、43%、44%、45%、46%、47%、48%、49%、50%、51%、52%、53%、54%、55%、56%、57%、58%、59%、60%等;填充剂的重量百分比可以是25%、26%、27%、28%、29%、30%、31%、32%、33%、34%、35%、36%、37%、38%、39%、40%、41%、42%、43%、44%、45%等;有机溶剂的重量百分比可以是10%、11%、12%、13%、14%、15%、16%、17%、18%、19%、20%、21%、22%、23%、24%、25%、26%、27%、28%、29%、30%等。
58.本发明中,为了保证烘烤过程中金膜的完整性和连续性,对施加好金涂料的陶瓷进行烘烤的过程中,自室温至200℃的升温阶段,升温速率低于10℃/min。此阶段主要为有机溶剂挥发过程,若升温速率过快,则溶剂猛烈沸腾,导致最终金膜破裂或错位,而将升温速率控制在低于10℃/min可以使有机溶剂挥发过程更加温和,从而保证金膜的质量。
59.本发明中,形成金膜后,还包括步骤:
60.s400、对烘烤后的陶瓷进行清洗,对金膜进行抛光。通过清洗和对形成的金膜进行抛光,可以进一步地提升金膜的亮度,使黄金质感更加强烈。
61.本发明实施例的第三方面提供一种电子终端,包括壳体,壳体为上述各实施例的壳体,基体可以覆盖壳体的整个结构,也可以是壳体中的部分结构,电子终端可以是手机、平板电脑、显示屏、gps导航仪、mp3、智能穿戴设备等等。如此,电子终端可以具有黄金质感的外观效果,还可以使电子终端的外表具有优良的耐腐蚀性能和耐刮擦性能。
62.根据上述壳体制备方法,以下表1示出了一些具体实施示例,能使陶瓷表面形成的金膜与陶瓷之间具有更高的附着力、黄金效果更加强烈、耐刮擦且更加节约成本。
63.下面参考具体实施例,对本发明进行描述,需要说明的是,这些实施例仅是描述性的,而不以任何方式限制本发明。
64.对比例1
65.在该对比例中,陶瓷的表面处理方式为抛光,使陶瓷形成抛光效果的表面处理区,金涂料为金水,金涂料采用笔描的方式施加,烘烤温度为600℃,金膜厚度为120nm,采用上述方式在陶瓷表面形成的金膜耐钢丝绒摩擦次数为300次,金膜颜色的l值为86.2,a值为0.3,b值为25.0。
66.对比例2
67.在该对比例中,陶瓷的表面处理方式为抛光,使陶瓷形成抛光效果的表面处理区,金涂料为金水,金涂料采用笔描的方式施加,烘烤温度为950℃,金膜厚度为120nm,采用上述方式在陶瓷表面形成的金膜耐钢丝绒摩擦次数为800次,金膜颜色的l值为84.0,a值为2.5,b值为28.3。
68.对比例3
69.在该对比例中,陶瓷的表面处理方式为抛光,使陶瓷形成抛光效果的表面处理区,金涂料为金膏,金涂料采用丝印的方式施加,烘烤温度为600℃,金膜厚度为160nm,采用上述方式在陶瓷表面形成的金膜耐钢丝绒摩擦次数为400次,金膜颜色的l值为87.4,a值为-2.4,b值为26.4。
70.对比例4
71.在该对比例中,陶瓷的表面处理方式为抛光,使陶瓷形成抛光效果的表面处理区,金涂料为金膏,金涂料采用丝印的方式施加,烘烤温度为950℃,金膜厚度为160nm,采用上述方式在陶瓷表面形成的金膜耐钢丝绒摩擦次数为800次,金膜颜色的l值为79.4,a值为0.5,b值为29.5。
72.对比例5
73.在该对比例中,陶瓷的表面处理方式为抛光,使陶瓷形成抛光效果的表面处理区,金涂料为金水,金涂料采用笔描的方式施加,烘烤温度为750℃,金膜厚度为60nm,采用上述方式在陶瓷表面形成的金膜耐钢丝绒摩擦次数为400次,金膜颜色的l值为86.3,a值为3.2,b值为29.5。
74.对比例6
75.在该对比例中,陶瓷的表面处理方式为抛光,使陶瓷形成抛光效果的表面处理区,金涂料为金水,金涂料采用笔描的方式施加,烘烤温度为750℃,金膜厚度为250nm,采用上述方式在陶瓷表面形成的金膜耐钢丝绒摩擦次数为800次,金膜颜色的l值为91.5,a值为1.4,b值为33.3。
76.表1对比例1至6陶瓷壳体的制备过程的工艺参数及制备出的陶瓷壳体的测试结果
[0077][0078]
表中测试方法和设备为:
[0079]
金膜厚度:扫描电子显微镜。
[0080]
钢丝绒摩擦:钢丝绒耐磨试验机,0000#钢丝绒,负重500g,每100次检查一次,测试后无脱金、无露底材为合格。
[0081]
lab值:色差仪。
[0082]
表中金水的金属树脂酸盐、填充剂和有机溶剂的质量比依次为:45%、21%和45%,其中金水中包含的金属成分及其占总金水的质量比例依次为:金au:10%、铂pt:0.04%、铋bi:0.35%、铑rh:0.06%、铬cr:0.05%和镍ni:0.01%;表中金膏的金属树脂酸盐、填充剂和有机溶剂的质量比依次为:50%、35%和15%,其中金膏中包含的金属成分及其占总金膏的质量比例依次为:金au:10%、铂pt:0.04%、铋bi:0.35%、铑rh:0.06%、铬cr:0.05%和镍ni:0.01%。
[0083]
实施例1
[0084]
在该实施例中,陶瓷的表面处理方式为抛光,使陶瓷形成抛光效果的表面处理区,金涂料为金水,金涂料采用笔描的方式施加,烘烤温度为750℃,金膜厚度为120nm,采用上述方式在陶瓷表面形成的金膜耐钢丝绒摩擦次数为800次,金膜颜色的l值为90.3,a值为1.2,b值为33.5。与对比例1中600℃条件下形成的金膜相比耐钢丝绒摩擦次数高了500次,亮度也更高。与对比例2中950℃条件下形成的金膜,亮度也更高,黄金质感更强。与对比例5中60nm厚的金膜相比,耐刮擦性能更强,亮度更高,黄金质感更强。与对比例5中250nm厚的金膜相比,耐刮擦性能差别不大,亮度差别不大,黄金质感差别不大。由此可见,烘烤温度过低会影响金膜的质感及降低金膜的耐刮擦性能,烘烤温度过高会影响金膜的质感,金膜的厚度过低会降低金膜的耐刮擦性能,金膜在200nm-250nm内的厚度范围内耐刮擦性能影响不大。
[0085]
实施例2
[0086]
在该实施例中,陶瓷的表面处理方式为喷砂,使陶瓷形成哑光效果的表面处理区,金涂料为金水,金涂料采用喷涂的方式施加,烘烤温度为750℃,金膜厚度为150nm,采用上述方式在陶瓷表面形成的金膜耐钢丝绒摩擦次数为700次,金膜颜色的l值为76.5,a值为-1.4,b值为32.5。能得到耐刮擦性能良好的哑光效果的金膜。
[0087]
实施例3
[0088]
在该实施例中,陶瓷的表面处理方式为镭雕,使陶瓷形成镭雕纹理形式的表面处理区,金涂料为金水,金涂料采用刷涂的方式施加,烘烤温度为750℃,金膜厚度为150nm,采用上述方式在陶瓷表面形成的金膜耐钢丝绒摩擦次数为700次,金膜颜色的l值为71.8,a值为-0.3,b值为31.5。能得到耐刮擦性能良好的纹理效果的金膜。
[0089]
实施例4
[0090]
在该实施例中,陶瓷的表面处理方式为抛光,使陶瓷形成抛光效果的表面处理区,金涂料为金膏,金涂料采用丝印的方式施加,烘烤温度为750℃,金膜厚度为160nm,采用上述方式在陶瓷表面形成的金膜耐钢丝绒摩擦次数为900次,金膜颜色的l值为92.3,a值为-1.3,b值为34.6。与对比例3和对比例4相比,能得到耐刮擦性能良好且具有高亮黄金质感的金膜。
[0091]
实施例5
[0092]
在该实施例中,陶瓷的表面处理方式为喷砂,使陶瓷形成哑光效果的表面处理区,金涂料为金膏,金涂料采用花纸转印的方式施加,烘烤温度为750℃,金膜厚度为140nm,采用上述方式在陶瓷表面形成的金膜耐钢丝绒摩擦次数为600次,金膜颜色的l值为75.3,a值为-0.4,b值为32.3。
[0093]
实施例6
[0094]
在该实施例中,陶瓷的表面处理方式为镭雕,使陶瓷形成镭雕纹理形式的表面处理区,金涂料为金膏,金涂料采用花纸转印的方式施加,烘烤温度为750℃,金膜厚度为140nm,采用上述方式在陶瓷表面形成的金膜耐钢丝绒摩擦次数为700次,金膜颜色的l值为70.4,a值为1.4,b值为31.5。能得到耐刮擦性能良好的纹理效果的金膜。
[0095]
表2实施例1至6陶瓷壳体的制备过程的工艺参数及制备出的陶瓷壳体的测试结果
[0096][0097]
表中测试方法和设备为:
[0098]
金膜厚度:扫描电子显微镜。
[0099]
钢丝绒摩擦:钢丝绒耐磨试验机,0000#钢丝绒,负重500g,每100次检查一次,测试后无脱金、无露底材为合格。
[0100]
lab值:色差仪。
[0101]
表中金水的金属树脂酸盐、填充剂和有机溶剂的质量比依次为:45%、21%和45%,其中金水中包含的金属成分及其占总金水的质量比例依次为:金au:10%、铂pt:0.04%、铋bi:0.35%、铑rh:0.06%、铬cr:0.05%和镍ni:0.01%;
[0102]
表中金膏的金属树脂酸盐、填充剂和有机溶剂的质量比依次为:50%、35%和15%,其中金膏中包含的金属成分及其占总金膏的质量比例依次为:金au:10%、铂pt:0.04%、铋bi:0.35%、铑rh:0.06%、铬cr:0.05%和镍ni:0.01%。
[0103]
以上所述仅为本发明的较佳实施例而已,并不用以限制本发明,凡在本发明的精神和原则之内所作的任何修改、等同替换和改进等,均应包含在本发明的保护范围之内。
再多了解一些
本文用于企业家、创业者技术爱好者查询,结果仅供参考。