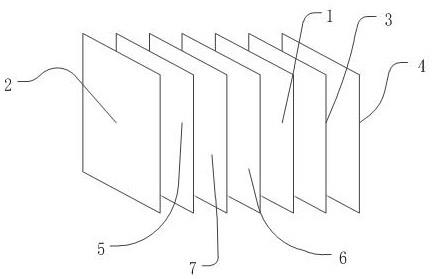
1.本发明涉及一种定向传热的半导体发热薄膜及其制备方法,属于电热薄膜技术领域。
背景技术:
2.现有技术中的电热元件主要有合金电热丝和碳基电热膜。合金电热丝是较为传统的电热元件,其属于线状热源,具有散热面积小、电热丝易断裂和抗震性能差等缺点。同时由于其有部分电能会被转化为光能,因而电能转换效率也较低,仅为60%左右。
3.碳基电热膜是有机不透明电热膜,是将导电涂料经喷涂或丝网印刷等方式涂覆于绝缘材料表面制得的,其是面状热源、散热均匀且电能转换效率较高,因此逐渐取代了合金电热丝。但是碳基电热膜在制备过程中需要使用大量的有机物,有机物会导致碳基电热膜的功率衰减严重,同时制备及使用过程中,也会污染环境及影响人体健康。另外,由于碳基电热膜的是双面散热的,而远离受热面一侧的热量利用率较低,造成了资源的浪费。
技术实现要素:
4.本技术的目的在于,提供一种定向传热的半导体发热薄膜及其制备方法,以解决现有技术中碳基电热膜存在的功率衰减严重及资源浪费的技术问题。
5.本发明的第一方面公开了一种定向传热的半导体发热薄膜,包括:基底、发热层和红外反射层;所述发热层设置于所述基底的第一表面,用于产生热量;所述发热层的发热材质为金属氧化物半导体制热材料;所述红外反射层设置于所述基底的第二表面,用于将传输至所述基底的所述热量定向反射至所述发热层。
6.优选地,所述红外反射层包括第一薄膜和第二薄膜;所述第一薄膜设置在所述基底的第二表面;所述第二薄膜设置在所述第一薄膜的另一表面上;所述第一薄膜的折射率大于所述第二薄膜的折射率。
7.优选地,所述第一薄膜的材质为硅或者硅铝;所述第二薄膜的材质为氟化镁。
8.优选地,所述金属氧化物半导体制热材料为氧化锡锑、氧化铟锡、氧化锌铝、氧化锌镓和氧化锌铟中的一种或多种。
9.优选地,还包括阻挡层;所述阻挡层设置于所述发热层与所述基底之间,用于阻挡所述基底产生的杂质及水汽进入所述发热层,阻挡层中包括iva族元素的氧化物,具体可为二氧化硅或者二氧化锡等。
10.优选地,还包括平滑层;
所述平滑层设置于所述基底与所述阻挡层之间,用于降低所述基底的粗糙度,平滑层的材质为聚氨酯。
11.优选地,还包括耐温层;所述耐温层设置于所述平滑层与所述阻挡层之间,用于减小所述基底的热膨胀系数,耐温层的材质为丙烯酸酯。
12.本发明的第二方面公开了一种定向传热的半导体发热薄膜的制备方法,包括:将金属氧化物半导体制热材料镀设在基底的第一表面,形成发热层;其中金属氧化物半导体制热材料,具体为:氧化锡锑、氧化铟锡、氧化锌铝、氧化锌镓和氧化锌铟中的一种或多种;在所述基底的第二表面镀设红外反射层,所述红外反射层用于将传输至所述基底的热量反射至所述发热层。
13.优选地,在所述基底的第二表面镀设红外反射层,具体为:在所述基底的第二表面镀设第一薄膜;在所述第一薄膜的另一表面镀设第二薄膜;所述第一薄膜的折射率大于所述第二薄膜的折射率。
14.优选地,在所述基底的第二表面镀设第一薄膜,具体为:利用磁控溅射方法在所述基底的第二表面镀设第一薄膜;在所述第一薄膜的另一表面镀设第二薄膜,具体为:利用电子束蒸镀方法在所述第一薄膜的另一表面镀设第二薄膜。
15.具体地,镀设第一薄膜使用的靶材为硅或硅铝;镀设第二薄膜使用的膜料为氟化镁。
16.优选地,在将金属氧化物半导体制热材料镀设在基底的第一表面,形成发热层之前,还包括:将iva族元素的氧化物镀设在所述基底的第一表面,形成阻挡层;其中那个iva族元素的氧化物可为二氧化锡或者二氧化硅等。
17.相应的,将金属氧化物半导体制热材料镀设在基底的第一表面,形成发热层,具体为:将金属氧化物半导体制热材料镀设在阻挡层上,形成发热层。
18.优选地,在将iva族元素的氧化物镀设在所述基底的第一表面,形成阻挡层之前,还包括:将丙烯酸酯涂覆于所述基底的第一表面,形成耐温层;相应的,将iva族元素的氧化物镀设在所述基底的第一表面,形成阻挡层,具体为:将iva族元素的氧化物镀设在所述耐温层上,形成阻挡层。
19.优选地,在将丙烯酸酯涂覆于所述基底的第一表面,形成耐温层之前,还包括:将聚氨酯涂覆于所述基底的第一表面,形成平滑层;相应的,将丙烯酸酯涂覆于所述基底的第一表面,形成耐温层,具体为:将丙烯酸酯涂覆于所述平滑层上,形成耐温层。
20.本发明的定向传热的半导体发热薄膜及其制备方法相较于现有技术,具有如下有益效果:
本发明提供的定向传热的半导体发热薄膜,其发热层的发热材质为金属氧化物半导体制热材料(metal
‑
oxide
‑
semiconductor
‑
heating,简称mosh),该种制热材料化学性质稳定,长期受热结构不会改变,具有高均匀性,使得利用其制备的半导体发热薄膜发热均匀,低温辐射偏差为
±
1℃。另外,金属氧化物半导体制热材料(mosh)还具有电阻低、透过率高的优点,因此利用其制备的发热薄膜具有高效的电热转换性能并且其透过率高达80%以上。本发明使用的半导体发热薄膜的材质为无机物,制备过程不会污染环境,使用过程也不会散发异味导致影响人体健康,同时也不存在碳基电热膜使用有机物导致功率衰减严重的问题。
21.进一步地,本发明的半导体发热薄膜中还设置了红外反射层,其可将发热层传输至基底侧的热量定向反射至发热层侧,使热量集中于发热层一侧而非两侧,从而使得热量流失率降低、利用率大幅提高,从而避免了资源的浪费。
附图说明
22.图1为本发明实施例提供的定向传热的半导体发热薄膜的一种结构的结构示意图;图2为本发明实施例提供的定向传热的半导体发热薄膜的另一种结构的结构示意图;图3为本发明实施例提供的定向传热的半导体发热薄膜的制备方法的流程图。
23.图中1为基底;2为发热层;3为第一薄膜;4为第二薄膜;5为阻挡层;6为平滑层;7为耐温层。
具体实施方式
24.以下描述中,为了说明而不是为了限定,提出了诸如特定系统结构、技术之类的具体细节,以便透彻理解本发明实施例。然而,本领域的技术人员应当清楚,在没有这些具体细节的其它实施例中也可以实现本发明。在其它情况中,省略对众所周知的系统、装置、电路以及方法的详细说明,以免不必要的细节妨碍本发明的描述。
25.图1为本发明实施例提供的定向传热的半导体发热薄膜的一种结构的结构示意图;如图1所示,本发明实施例的定向传热的半导体发热薄膜包括基底1、发热层2和红外反射层;其中发热层2设置于基底1的第一表面,用于产生热量。
26.发热层2的发热材质为mosh材料,本发明实施例中金属氧化物半导体制热材料为氧化锡锑、氧化铟锡、氧化锌铝、氧化锌镓和氧化锌铟中的一种或多种。
27.进一步地,发热层2的厚度为15
‑
500nm,具体地,可为15nm、18nm、20nm、40nm、80nm、125nm、200nm、275nm、350nm、400nm、500nm等等,优选为18nm。当为氧化锌铝(azo)时,发热层的材质厚度可以做到500nm。
28.mosh材料化学性质稳定,长期受热结构不会改变,具有高均匀性,使得利用其制备的半导体发热薄膜发热均匀,低温辐射偏差为
±
1℃。另外,mosh材料还具有电阻低、透过率高的优点,因此利用其制备的半导体发热薄膜具有高效的电热转换性能并且其透过率高达
80%以上。本发明使用的半导体发热薄膜的材质为无机物,制备过程不会污染环境,使用过程也不会散发异味导致影响人体健康,同时也不存在碳基电热膜使用有机物导致功率衰减严重的问题。
29.本实施例中的红外反射层设置于基底1的第二表面,用于将传输至基底1的热量定向反射至发热层2。
30.红外反射层可将发热层2传输至基底1侧的热量定向反射至发热层2侧,使热量集中于发热层2一侧而非两侧,使得热量流失率降低、利用率大幅提高,从而避免了资源的浪费。
31.进一步地,本实施例的红外反射层包括第一薄膜3和第二薄膜4;第一薄膜3设置在基底1的第二表面;第二薄膜4设置在第一薄膜3的另一表面;第一薄膜3的折射率大于第二薄膜4的折射率。
32.本实施例的红外反射层为双层折射膜,双层折射膜相较于单层折射膜,其散射得到大幅降低,从而可以确保发热层2产生的远红外光线得到最大程度的红外反射,减少保温材料的使用,特别适合于汽车玻璃等需要高透过且不具备保温性的应用场景。同时,使用双层折射膜的半导体发热薄膜,其膜层较薄,占用空间小,实用性更强。
33.本实施例中基底1的材质为聚酯薄膜或聚酰亚胺薄膜,厚度为150
‑
200μm,具体可为150μm、160μm、175μm、188μm、200μm,优选为188μm;第一薄膜3为高折射率反射膜,其材质为硅或者硅铝,厚度为30
‑
50nm,具体可为30nm、40nm、50nm,优选为40nm,折射率为2.6
‑
3.69,具体可为2.6、2.7、2.87、3.1、3.5、3.69,优选为2.87;第二薄膜4为低折射率反射膜,其材质为氟化镁或者氟化钡,厚度为50
‑
120nm,具体可为50nm、70nm、80nm、90nm、120nm,优选为80nm,折射率为1.3
‑
1.4,具体可为:1.31、1.33、1.36、1.38、1.40,优选为1.38。
34.具备上述参数的第一薄膜3和第二薄膜4组成的红外反射层,其红外反射能力更强,热量的损失最小。需要说明的是,本发明实施例对第一薄膜3和第二薄膜4的具体材质不作限制,只要能达到红外反射的效果即可。
35.为阻挡基底1中的杂质向发热层2扩散及防止基底1产生的水汽渗透入发热层2,损害发热层2的发热效率及寿命,本实施例在基底1和发热层2之间还设置了阻挡层5。本实施例的阻挡层5为iva族元素的氧化物,例如可为含硅氧化物或者含锡氧化物等,本发明实施例具体以阻挡层5的材质为二氧化硅,厚度为15nm
‑
30nm为例进行说明。其中阻挡层的厚度具体可为:15nm、18nm、22nm、24nm、25nm、28nm、30nm,优选为25nm。
36.本实施例设置的阻挡层5不仅具有阻挡杂质及水汽进入发热层2的功能,其还能够使得基底1和发热层2的热膨胀系数和晶格常数匹配,使各层结构之间连接可靠,延长使用寿命。
37.本发明的实施例还公开了另一种结构的定向传热的半导体发热薄膜,其结构见图2。
38.该种结构的定向传热的半导体发热薄膜,其是在第一种结构的半导体发热薄膜上的进一步改进。
39.由于基底1的表面粗糙度较大,会影响阻挡层5的膜层镀制。本实施例在对基底1进行清洗之后对基底1进行降粗糙度处理。降粗糙度处理的方法为使用平滑层6降低基底1的
粗糙度。具体地,在基底1上辊涂聚氨酯材质的平滑层6,聚氨酯呈液态,通过流平作用实现基底1平滑性处理,辊涂聚氨酯之后基底1的粗糙度降低有利于阻挡层5的附着。同时聚氨酯也有阻隔杂质的效果,能结合阻挡层5进一步阻止基底1中的杂质及水汽扩散至发热层。本发明实施例中聚氨酯可以是聚酯型,也可以是聚醚型,本发明实施例对平滑层6的具体材质不作限定,只要能达到降低基底粗糙度的材质均可。平滑层的厚度为2
‑
5μm,具体可为2μm、3μm、4μm、5μm,优选为3μm。
40.本实施例中的基底1材料为聚酯薄膜或聚酰亚胺薄膜,在需要高温使用的场合,其本身耐温性小于玻璃等刚性基底。当发热层2加热一定时间后,基底1会因受热发生形变,具体表现在中心部位应力最集中,薄膜表面出现“凹陷”现象;而发热层2本身的膨胀系数小,如果基底1膨胀系数大,两者不匹配,整个薄膜的形变向附着发热层的这一面弯曲变形,这种变形破坏薄膜的表面结构。
41.因此,本实施例在平滑层6与阻挡层5之间还设置了耐温层7。耐温层7是通过在平滑层6上辊涂丙烯酸酯制得的,其使得基底1材料能够耐高温且减小基底1材料的热膨胀系数,改善基底1性能。本发明实施例中丙烯酸酯可以是丙烯酸甲酯、丙烯酸乙酯、丙烯酸丁酯等任一种化合物,本发明实施例对耐温层7的具体材质不作限定,只能要耐高温且减小基底1材料的热膨胀系数即可。耐温层的厚度为2
‑
5μm,具体可为2μm、3μm、4μm、5μm,优选为4μm。
42.本发明实施例中的半导体发热薄膜由于使用了mosh材料,具有发热均匀、低温辐射偏差为
±
1℃、电热转换性能高、透过率高达80%以上、寿命长、使用过程安全等优点。其克服了现有技术中碳基电热膜存在的有机物导致功率衰减、寿命短、使用过程中散发味道严重、影响人体健康等问题。同时,由于本发明实施例中还设置了红外反射层,其可将发热层传输至基底侧的热量定向反射至发热层侧,使热量集中于发热层一侧而非两侧,使得热量流失率降低、利用率大幅提高,从而避免了资源的浪费。
43.本发明实施例还公开了一种上述定向传热的半导体发热薄膜的制备方法,其流程见图3,包括:步骤1、将mosh材料镀设在基底的第一表面,形成发热层,具体为:以mosh材料为靶材,利用真空镀膜方法在基底的第一表面镀设发热层;其中真空镀膜方法可采用磁控溅射、离子溅射或者电子束蒸镀等方法。而由于磁控溅射方法具有沉积速度快、基底温升低、对发热层的损伤小、发热层与基底结合较好、发热层纯度高、致密性好、成膜均匀性好等优点,因此,本实施例优选使用磁控溅射的方法在基底的第一表面上镀设发热层。
44.上述mosh材料具体可为氧化锡锑、氧化铟锡、氧化锌铝、氧化锌镓和氧化锌铟中的一种或多种。基底为聚酯薄膜或聚酰亚胺薄膜;更为具体地,磁控溅射采用的靶材是氧化铟锡(英文简称ito),该靶材中in2o3和 sno2的质量比为7:1至12:1,具体可为:7:1、8:1、9:1、10:1、11:1或者12:1,优选为8:1,本底真空度< 1
×
10
‑3pa,基底温度为常温,溅射功率面密度为0.7
‑
2.5w/cm2,具体可为:0.7w/cm2、0.9w/cm2、1.0w/cm2、1.2w/cm2、1.6w/cm2、2.0w/cm2、2.5w/cm2,优选为1w/cm2,在溅射过程中通入氩气作为保护气体,氧气作为反应气,氩气和氧气的气体流量均为800
‑
1200ml/min,具体可为:800ml/min、900ml/min、1000ml/min、1100ml/min、1200ml/min,优选地,氩气的气流流量为1200ml/min,氧气的气体流量也为1200ml/min,氩气和氧气的气体流量也可
不同。本实施例溅射所得发热层的厚度为15
‑
500nm。
45.步骤2、在基底的第二表面镀设红外反射层,红外反射层用于将传输至基底的热量反射至发热层,具体为:步骤2.1、在基底的第二表面利用真空镀膜方法镀设第一薄膜,真空镀膜方法可使用离子溅射、磁控溅射或者电子束蒸镀等,本实施例使用磁控溅射方法镀设第一薄膜。磁控溅射使用的靶材为硅或硅铝,形成的第一薄膜的材质为二氧化硅。溅射过程中通入氧气作为反应气体,通入氩气作为保护气体,常温溅射形成第一薄膜。
46.更为具体地,溅射形成第一薄膜时溅射采用4n的靶材硅或硅铝,其中铝掺杂量为0.3wt%
‑
1.5wt%,具体可为0.3wt%、0.5wt%、0.7wt%、1.1wt%、1.5wt%,优选为0.5wt%,溅射功率面密度为7
‑
12w/cm2,具体可为7w/cm2、8w/cm2、8.5w/cm2、9.5w/cm2、11w/cm2或者12w/cm2,优选为8.5w/cm2。在溅射过程中通入氧气作为反应气体,氩气作为保护气体,氩气和氧气的质量比为5:1
‑
15:1,具体可为:5:1、8:1、10:1、11:1、13:1、15:1,优选为10:1,氩气和氧气的总气体流量为100
‑
500ml/min,具体可为100ml/min、200ml/min、300ml/min、400ml/min或者500ml/min,优选为500ml/min,本底真空度< 1
×
10
‑3pa,基底温度为常温,在基底表面制备厚度为30nm
‑
50nm的第一薄膜,具体可为30nm、40nm或者50nm,优选为40nm,第一薄膜的材质为 sio2,薄膜折射率为2.6
‑
3.69,具体可为2.6、2.7、2.87、3.1、 3.5、3.69,优选为2.87。
47.步骤2.2、在第一薄膜远离基底的表面上镀设第二薄膜;第一薄膜的折射率大于第二薄膜的折射率;其中镀设可使用离子溅射、磁控溅射或者电子束蒸镀等,本实施例使用电子束蒸镀的方法镀设第二薄膜,蒸镀第二薄膜使用的膜料为氟化镁。具体地,在本底真空度< 1
×
10
‑3pa,沉积速率为1
å
/s
‑3å
/s,具体可为1
å
/s、1.5
å
/s、2
å
/s、2.5
å
/s或者3
å
/s,优选为2.5
å
/s,基底温度80℃
‑
150℃,具体可为80℃、90℃、100℃、110℃、120℃、130℃、140℃或者150℃,优选为150℃,在第一薄膜上镀设厚度为50nm
‑
120nm的mgf2薄膜,具体可为:50nm、70nm、80nm、90nm或者120nm,优选为80nm,薄膜折射率为1.3
‑
1.4,具体可为:1.31、1.33、1.36、1.38、1.40,优选为1.38。
48.为阻挡基底中的杂质向发热层扩散及防止基底产生的水汽渗透入发热层,损害发热层的发热效率及寿命,在步骤1之前,还包括:将iva族元素的氧化物镀设在基底的第一表面,形成阻挡层。其中iva族元素的氧化物包括含硅氧化物或者含锡氧化物等、采用的镀设方法为磁控溅射。
49.更为具体地,采用4n的靶材硅,溅射功率面密度为1
‑
8w/cm2,具体可为:1w/cm2、1.5w/cm2、2w/cm2、2.5w/cm2、3w/cm2、3.5w/cm2、4w/cm2、4.5w/cm2、5w/cm2、5.5w/cm2、6w/cm2、6.5w/cm2、7w/cm2、7.5w/cm2或者8w/cm2优选为1.5w/cm2。在溅射过程中通入氧气作为反应气体,氩气作为保护气体,氩气和氧气的质量比为10:1
‑
20:1,具体可为:10:1、11:1、12:1、13:1、14:1、15:1、16:1、17:1、18:1、19:1、20:1,优选为13:1,氧气的气体流量为50
‑
100ml/min,具体可为:50ml/min、60ml/min、70ml/min、80ml/min、90ml/min或者100ml/min,优选为80ml/min;氩气的气体流量为300
‑
800ml/min,具体可为300ml/min、400ml/min、500ml/min、600ml/min、700ml/min或者800ml/min,优选为800ml/min,本底真空度< 1
×
10
‑3pa,基底温度为常温,在基底表面镀设厚度为15nm
‑
30nm,具体可为15nm、18nm、22nm、24nm、25nm、28nm、30nm,优选为23nm的 sio2层即为阻挡层。
50.相应的,步骤1、将mosh材料镀设在基底的第一表面,形成发热层,具体为:将mosh材料镀设在阻挡层上,形成发热层。
51.在将iva族元素的氧化物镀设在基底的第一表面,形成阻挡层之前,需要对基底进行清洗,具体为采用玻璃清洗液、氢氧化钠配制的碱液和去离子水各超声清洗20min
‑
40min,具体可为20min、30min或者40min,优选为30min,然后吹干备用。
52.清洗后在基底上涂覆2
‑
5μm厚的平滑层,平滑层的厚度具体可为2μm、3μm、4μm、5μm,优选为3μm,其可采用辊涂的方式,并于100
‑
150℃烘干,烘干温度具体可为100℃、110℃、120℃、130℃、140℃或者150℃,优选为100℃;烘干时间为30
‑
50min,具体可为30min、40min或者50min,优选为30min。
53.烘干后在平滑层上涂覆耐温层,具体为:在平滑层上辊涂2
‑
5μm厚的耐温层,耐温层的厚度具体可为:2μm、3μm、4μm或者5μm,优选为4μm。然后进行烘干,烘干温度为90℃
‑
110℃,具体可为:90℃、100℃或者110℃,优选为100℃。烘干后进行紫外线照射固化,固化时间为15min
‑
30min,具体可为15min、20min、25min或者30min,优选为20min,曝光能量为400mj
‑
600mj,具体可为400mj、450mj、500mj、550mj或者600mj,优选为500mj。
54.固化后对附有耐温层的基底进行等离子处理。
55.下面将以更为具体的实施例详述本发明的制备方法。
56.一种定向传热的半导体发热薄膜的制备方法,包括:第一步: 对基底进行清洗。
57.本实施例中基底为聚酯薄膜(英文简称pet)材质,基底厚为188μm,采用玻璃清洗液、氢氧化钠配制的碱液和去离子水各超声清洗30min后吹干备用。
58.第二步:在清洗后的基底的第一表面通过辊涂的方式涂敷一层3μm厚的平滑层,平滑层的材质为聚氨酯,尔后烘干,烘干温度为100℃、大气压下,烘干时间30min。
59.第三步:在平滑层上通过辊涂的方式再涂敷一层4μm厚的耐温层,耐温层的材质为丙烯酸酯,尔后烘干,烘干环境为100℃,大气压下,烘干时间30min,尔后进行20min的紫外固化,曝光能量为500mj。
60.第四步:为避免在基底第二表面上制备红外反射层时影响基底第一表面侧的平滑层及耐温层,因此使用铝箔包覆平滑层及耐温层。之后在基底的第二表面上采用4n的硅铝靶材进行磁控溅射,制备厚度为35nm、折射率为3.07的第一薄膜,制备得到的第一薄膜为sio2薄膜。磁控溅射时,本底真空度< 1
×
10
‑3pa,基底温度为常温,硅铝靶材中铝掺杂量为0.5wt%,溅射功率面密度为8.5w/cm2,在溅射过程中通入氧气作为反应气体,氩气作为保护气体,气体流量为300ml/min,氩气和氧气的质量比为10:1。
61.第五步:在第一薄膜上采用电子束蒸发的方式制备厚度为120nm、折射率为1.3的第二薄膜,第二薄膜的材质为氟化镁。电子束蒸发时,本底真空度< 1
×
10
‑3pa,沉积速率为2
å
/s,基底温度为150℃。
62.第六步:将平滑层与耐温层上包覆的铝箔去掉,之后使用铝箔包覆红外反射层,避免接下来发热层的制备对红外反射层的影响。
63.在制备发热层之前,首先在耐温层上以磁控溅射的方式溅射23nm厚的二氧化硅(sio2)阻挡层;溅射采用4n的硅靶材,溅射功率面密度为1.5w/cm2,在溅射过程中通入氧气作为反应气体,气体流量为80ml/min;通入氩气作为保护气体,气体流量为800ml/min,氩气
和氧气的质量比为20:1。
64.第七步:在基底处于常温的情况下,即5摄氏度至40摄氏度时,在阻挡层上以磁控溅射的方式溅射18nm厚的发热层;溅射时的靶材为in2o3和 sno2的质量比为8:1的氧化铟锡(英文简称ito),溅射功率面密度为1w/cm2,在溅射过程中通入氩气作为保护气体,气体流量为1200ml/min。
65.利用上述步骤即可制备得到定向传热的半导体发热薄膜,制备所得发热薄膜具有发热均匀、低温辐射偏差为
±
1℃、电热转换性能高、透过率高达80%以上、寿命长、使用过程安全等优点。
66.本发明的定向传热的半导体发热薄膜,其制备过程中使用的膜层均为无机材料,制程无污染,同时由于其并未使用有机物,使用过程也不会散发异味导致影响人体健康,同时也不存在碳基电热膜使用有机物导致功率衰减严重的问题。
67.以上所述,仅是本技术的几个实施例,并非对本技术做任何形式的限制,虽然本技术以较佳实施例揭示如上,然而并非用以限制本技术,任何熟悉本专业的技术人员,在不脱离本技术技术方案的范围内,利用上述揭示的技术内容做出些许的变动或修饰均等同于等效实施案例,均属于技术方案范围内。
再多了解一些
本文用于企业家、创业者技术爱好者查询,结果仅供参考。