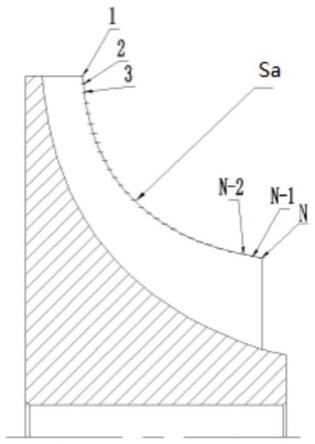
1.本发明属于叶轮技术领域,尤其是涉及一种半开式磁悬浮叶轮叶顶间隙自调节方法。
背景技术:
2.鼓风机广泛应用于冶金、建材、化工、市政等高能耗行业,在国民经济发展中起着至关重要的作用。鼓风机的能耗大,例如污水处理厂中曝气鼓风机的能耗占污水处理厂总能耗的50%
‑
60%,可见提高鼓风机的运行效率,将带来可观的经济效益。
3.半开式叶轮鼓风机的整机效率可分为叶轮效率和扩压器、蜗壳等静止部件的效率;当扩压器、蜗壳等静止部件的效率一定时,提高叶轮效率必然使整机效率提升,半开式叶轮叶顶间隙对叶轮效率有明显的影响,学者何毅通过cfd计算和大量实际测试得出,叶顶间隙比每增加1%将导致级效率下降超过0.5%,并且级比越高,效率下降越大。控制叶轮叶顶间隙是学者们研究的共同话题,例如专利号:cn105201904a,一种半开式叶轮叶顶间隙的控制方法,该方法虽然能达到控制叶顶间隙的效果,但操作较为繁琐。为了解决其不足之处,本发明创新的提出了一种半开式磁悬浮叶轮叶顶间隙自调节方法。
技术实现要素:
4.本发明为了克服现有技术的不足,提供一种半开式磁悬浮叶轮叶顶间隙自调节方法。
5.为了实现上述目的,本发明采用以下技术方案:一种半开式磁悬浮叶轮叶顶间隙自调节方法,包括以下步骤:
6.a、计算确定三元流叶轮的外形尺寸及轮廓;
7.b、建立叶轮三维模型,对叶轮三维模型进行切片处理;
8.c、将叶轮三维模型的中轴线与水平方向呈45
°
角放置,在叶轮三维模型中与水平方向夹角小于40
°
的叶片部位下端添加网格工艺支撑模型,网格工艺支撑模型由叶片下端连接到水平放置的盖板上表面;盖板下表面与基板之间添加实体支撑;
9.d、根据s
‑
04/s
‑
08高强不锈钢材料特点设定激光选区熔化成形加工工艺参数;
10.e、按照步骤d设定的工艺参数,在惰性气体的保护下进行激光选区熔化成形;
11.f、激光选区熔化成形完成后清理浮粉,线切割去除基板;
12.g、去除网格工艺支撑;
13.h、对叶轮进行表面处理和热处理,所述表面处理包括喷砂、三元振动、磨料流和打磨处理;
14.i、计算整机效率最高时半开式叶轮和叶轮盖的最佳间隙δ;
15.j、将半开式叶轮叶顶型线sa均分成n
‑
1段;
16.k、计算运行工况下,所分割叶顶型线sa各端点向叶轮盖方向的最大偏移量δ1δ2···
δ
n
‑1δ
n
;
17.l、以叶顶型线sa为基准,各端点向叶轮盖方向移量(δ δ1,δ δ2···
δ δ
n
‑1,δ δ
n
)并用样条曲线连接各点形成曲线sc,曲线sc即位即为叶轮盖基体的内表面轮廓加工曲线;
18.其中,所述步骤h中的打磨处理操作为将叶轮放入到打磨系统内完成叶轮的打磨处理,所述打磨系统包括处理台和设于所述处理台一侧的输送装置,所述处理台上设有加工槽,所述加工槽内设有第一打磨块,所述输送装置包括设于所述处理台一侧的底座、设于所述底座上的连接盘及设于所述连接盘上的多个第一连接板,所述底座上设有用于驱动连接盘转动的第二电机,所述连接盘底部设有连接环,所述底座上设有与所述连接环相配合的环槽,所述第一连接板上设有与所述加工槽相对应的第一通孔,所述第一通孔内壁上设有第一活动槽,所述第一活动槽内设有支撑板;所述处理台上设有设备腔,所述设备腔内设有第一气缸,所述第一气缸的活塞杆上设有承接板,所述处理台上方设有用于驱动叶轮转动的第一电机;叶轮在做表面处理时将叶轮放入到第一通孔内,支撑板处于第一通孔底部,连接盘转动带动叶轮转动,叶轮转动至加工槽上方,第一气缸推动承接板往上运动,承接板上升至第一通孔底部,支撑板进入到第一活动槽内,第一通孔内的叶轮掉落在承接板上,承接板带动叶轮往下运动至加工槽内,第一连接板继续转动从加工槽上方移开,第一电机驱动叶轮转动,第一打磨块与叶轮侧壁相接触打磨叶轮侧壁,完成叶轮的打磨处理;叶轮打磨完成后,连接盘继续转动,第一连接板再次转动至加工槽上方,承接板带动叶轮往上运动,支撑板进入到第一活动槽内后,叶轮进入到第一通孔内,随后支撑板从第一活动槽内伸出移动至叶轮底部,承接板下降,第一连接板转动将叶轮运出。
19.利用本发明的叶轮叶顶间隙自调节方法,在保正安全的前提下,利用叶轮运行工况自身产生的变形量,使得叶顶与叶轮盖的间隙始终处于最佳间隙δ;同时,半开式叶轮和叶轮盖的间隙增大,减低整机装配的难度,提高装配效率;通过输送装置和加工台的配合,可自动的完成叶轮的加工,提升叶轮加工效率,降低叶轮加工难度,以便快速得到所需叶轮,完成对叶轮的各项数据采集,从而提高整个方法的实施效率,进一步的增加风机的装配效率;利用承接板的升降运动,使叶轮更加平稳的放入到加工槽内,避免叶轮从高处落下造成损坏;同时利用承接板以便对叶轮起定位作用,将叶轮以指定位置放置于加工台上,提升对叶轮的加工效果;通过输送装置可自动的完成叶轮的送料和出料,无需人工参与,提升叶轮加工过程中的自动化程度。
20.步骤j中叶顶型线san取值不小于20。
21.步骤k分割叶顶型线sa各端点向叶轮盖方向的最大偏移量δ1δ2···
δ
n
‑1δ
n
采用有限元仿真软件计算得出。
22.所述第一电机上方设有第二气缸,所述第一电机设于所述第二气缸的活塞杆上,所述第一电机的输出轴上设有第一连接杆,所述第一连接杆上设有安装槽,所述安装槽内设有第二打磨块;所述第一连接杆侧壁上还设有第二活动槽,所述第二活动槽内设有第一固定块,所述加工槽内壁上设有第三活动槽,所述第三活动槽内设有第二固定块;叶轮放置于加工槽内后,第一连接板从加工槽上方转开,第二气缸驱动第一连接杆往下运动,第一连接杆插入到叶轮轴孔内,第二固定块从第三活动槽内伸出抵在叶轮侧壁上,第一电机驱动第一连接杆转动,第一连接杆相对于叶轮转动,第二打磨块与叶轮轴孔内壁相接触,对叶轮轴孔内壁做打磨;叶轮轴孔内壁打磨完成后,第一连接杆往上运动,第二固定块进入到第三活动槽内,第一固定块从第二活动槽内伸出,第一固定块抵叶轮轴孔内壁上,第一电机带动
第一连接杆转动时带动叶轮转动,叶轮侧壁与第一打磨块相接触,完成叶轮侧面的打磨处理。
23.所述第二固定块侧壁上设有第一连接弹簧,所述第三活动槽底部设有第一传动槽,所述第一传动槽底部设有第四活动槽,所述第一传动槽内设有与所述第二固定块相配合的第一传动辊;所述承接板上设有凹槽,所述凹槽侧壁上设有第一通腔,所述第一通腔内壁上设有第一活动腔,所述第一通腔内穿设有与所述第四活动槽相配合的第一传动板,所述第一传动板上设有第一限位杆,所述第一限位杆上设有第一复位弹簧;所述凹槽内设有气囊,所述气囊顶部设有第一推板;叶轮处于承接板上时,叶轮的轴孔处于第一推板位置,第一连接杆往下运动插入到叶轮轴孔内后,第一连接杆推动第一推板往下运动,第一推板推动气囊形变,气囊内的空气进入到第一通腔内,气压推动第一传动板往空腔外移动,第一传动板插入到第四活动槽内,第一传动板带动第一传动辊转动,第一传动辊带动第二固定块往第三活动槽外侧移动,第二固定块伸入到加工槽内抵在叶轮侧壁上,第一连接杆相对叶轮转动,对叶轮的轴孔内壁做打磨处理。
24.所述第一电机的输出轴上设有第二连接杆,所述第一连接杆上设有第二通腔,所述第二连接杆穿设于所述第二通腔内,所述第二通腔内壁上设有第二活动腔,所述第二连接杆上设有与所述第二活动腔相配合的第一限位板,所述第一限位板底部设有第二复位弹簧,所述第二活动腔顶部设有与所述第二活动槽相通的第五活动槽,所述第一固定块上设有第三连接杆,所述第三连接杆穿设于所述第五活动槽内,所述第五活动槽内可转动连接有第一传动杆,所述第五活动槽底部穿设有推杆,所述推杆上设有第一滑块,所述第五活动槽内壁上设有与所述第一滑块相配合的第一滑槽;第一连接杆往下运动时,第一连接杆插入到叶轮的轴孔内,第一连接杆移动至叶轮轴孔底部后,第二连接杆相对于第一连接杆移动,第二连接杆推动第一推板往下运动,第一推板挤压气囊,第二固定块从第三活动槽内伸出抵在叶轮侧壁上;当叶轮轴孔内壁打磨完成后,第二连接杆相对于第一连接杆往上运动,第一推板往上运动,第一传动板进入到第一通腔内,第二固定块进入到第三活动槽内;第一限位板随第二连接杆往上运动,第一限位板推动推杆往上运动,推杆推动第一传动杆一端转动,第一传动杆绕连接点转动,第一传动杆另一端推动第三连接杆移动,第三连接杆带动第一固定块往第二活动槽外移动,第一固定块从第二活动槽内伸出抵在叶轮轴孔内壁上,完成第一连接杆与叶轮的连接,第一电机驱动第二连接杆转动时带动第一连接杆转动,叶轮随第一连接杆转动,对叶轮侧壁做打磨处理。
25.所述加工槽内壁上设有第六活动槽,所述第六活动槽内设有第一连接块,所述第一连接块上设有第二连接弹簧,所述第一连接块上设有第一连接槽,所述第一打磨块设于所述第一连接槽内,所述第一连接槽内壁上设有第三复位弹簧;所述处理台上设有用于连通所述第三活动槽和所述第六活动槽的连接腔,所述连接腔内壁上设有空腔,所述空腔内壁上设有第三连接弹簧,所述第三连接弹簧上设有第二推板,所述空腔内壁上设有与所述第二推板相配合的密封块;所述第六活动槽内壁上设有第七活动槽,所述第七活动槽内壁上设有第四连接弹簧,所述第四连接弹簧一端设有第二连接板,所述第二连接板上设有第一棘齿;所述空腔内壁上设有第八活动槽,所述第八活动槽内壁上设有第五连接弹簧,所述第五连接弹簧一端设有第三连接板,所述第三连接板上设有第二棘齿;第一连接块处于第六活动槽内,第二固定块处于第三活动槽内时,空腔处于开启状态,第二推板处于靠近空腔
内壁位置处;叶轮放入到加工槽内时,第二固定块从第三活动槽内时伸出,第二推板推动空腔内的空气进入到连接腔内,第二推板移动至第三连接板一侧,第二推板与第三连接板相接触,第二棘齿将第二推板固定在密封块上,第二推板处于空腔入口处将空腔封闭;当叶轮轴孔内壁打磨完成后,第二固定块进入到第三活动槽内,第二固定块挤压第三活动槽内的空气,空气通过连接腔进入到第六活动槽内,气压推动第一连接块从第六活动槽内伸出,第一棘齿与第一连接块侧壁相接触将第一连接块固定;当叶轮侧壁打磨完成后,第二连接板进入到第七活动槽内,第三连接板进入到第八活动槽内,第一连接块往第六活动槽内移动,第一连接块推动第六活动槽内空气进入到空腔内,空气再次存储在空腔内。
26.所述处理台上设有第九活动槽,所述第九活动槽内穿设有第四连接杆,所述第四连接杆底部设有第二限位板,所述第二限位板上设有第四复位弹簧,所述第二连接板和所述第三连接板上分别设有第一连接绳和第二连接绳,所述第一连接绳和所述第二连接杆一端均固连于所述第四连接杆上;所述第四连接杆顶部设有第四连接板;所述第一电机下方设有连接柱,所述连接柱上设有第三通腔,所述第一连接杆穿设于所述第三通腔内,所述第一连接杆侧壁上设有第二滑块,所述第三通腔内壁上设有与所述第二滑块相配合的第二滑槽,所述第二滑槽内壁上设有第十活动槽,所述第十活动槽内设有第六连接弹簧,所述第六连接弹簧一端设有限位块;所述连接柱侧壁上设有与所述第十活动槽相通的第十一活动槽,所述第十一活动槽内设有活动块,所述活动块上设有第三连接绳,所述第三连接绳一端固连于所述限位块上;所述处理台上方设有防尘罩,所述防尘罩上设有与所述连接柱相配合的第一通槽,所述防尘罩内壁上设有与所述第四连接板相配合的第一凸块;叶轮放置在加工槽内后,防尘罩往下运动罩在加工槽内,第二气缸推动第一连接杆往下运动,第一连接杆穿入到叶轮的轴孔内,对叶轮做打磨处理;叶轮打磨完成后,罩壳往上运动,罩壳内壁上的第一凸块与第四连接板相接触,第一凸块带动第四连接板一同往上运动,第四连接板带动第四连接杆往上运动,第一连接绳和第二连接绳拉动第二连接板和第三连接板移动,第一连接块进入到第六活动槽内;罩壳继续往上移动时,第一通槽内壁与活动块侧壁相接触,罩壳带动活动块往上运动,活动块带动限位块往第十活动槽内移动,第二连接杆往上运动带动第一连接杆往上运动,第一连接杆从叶轮轴孔内脱出;第二气缸推动第二连接杆往下运动时,第二连接杆带动第一连接杆往下运动,第二滑块移动至第二滑槽底端,第二滑块夹在第二滑槽内壁和限位块之间,将第二滑块固定,第二连接杆可相对第一连接杆移动,对第一固定块和第二固定块的运动做控制。
27.所述第一活动槽顶部设有第十二活动槽,所述第十二活动槽内设有与所述支撑板相配合的第二传动辊,所述第一连接板底部设有与所述第十二活动槽相通的第十三活动槽,所述第十三活动槽内设有与第二传动辊相配合的第二传动杆,所述第二传动杆顶部设有第五复位弹簧,底部设有第五连接杆;所述第十二活动槽内壁上设有第十四活动槽,所述第十四活动槽内设有第五连接板,所述第二传动辊两端分别设有连接轴,所述连接轴穿设于所述第五连接板上,所述第五连接板上设有第二凸块,所述第二传动杆设有与所述第二凸块相配合的第三凸块;第一连接板带动叶轮移动至加工槽上方时,承接板往上运动推动第五连接杆往上运动,第五连接杆带动第二传动杆往上运动,第二传动杆带动第二传动辊转动,第二传动辊带动支撑板往第一活动槽内移动,叶轮从第一通孔内掉落在承接板上,随承接板进入到加工槽内;叶轮加工完成后,第一连接板再次转动至加工槽上方,承接板带动
叶轮往上运动,叶轮进入到第一通孔内后承接板推动第五连接杆继续往上运动,第三凸块与第二凸块相接触,第三凸块推动第二凸块往上运动,第二凸块带动第五连接板往上运动,第五连接板带动第二传动辊往上运动,第二传动辊与支撑板脱开接触,支撑板从第一活动槽内伸出,承接板下降,叶轮处于第一通孔内随第一连接板运出。
28.所述第一连接槽内壁上设有第三滑槽,所述第二打磨块侧壁上设有与所述第三滑槽相配合的第三滑块,所述第三滑块上设有第一斜槽,所述第三滑槽顶部设有第十五活动槽,所述第六活动槽顶部设有开口,所述开口内设有挡块,所述开口内壁上设有与所述第十五活动槽相配合的第十六活动槽,所述挡块侧壁上设有与所述第十六活动槽相配合的第六连接杆,所述第十五活动槽内穿设有第二限位杆,所述第二限位杆上设有第二连接块,所述第六连接杆上设有于所述第二连接块相配合的第二连接槽;所述防尘罩上设有储水腔,所述储水腔侧壁上设有多个喷水口,所述储水腔顶部设有进水管;所述承接板上设有第二通槽,所述加工槽底部设有与所述第二通槽相通的排水腔;叶轮做打磨处理时,防尘罩罩在加工槽上,水流从进水管处进入到储水腔内,储水腔内装满水流后,水流从喷水口处喷出,水流喷洒在加工槽内,水流写到粉尘进入到第二通槽内,从排水腔内排出;在对第一打磨块做更换时,往上拉动第六连接杆,第六连接杆带动第二限位杆往上运动,第二限位杆从第十五活动槽内取出,第三复位弹簧推动第三滑块移动至第三滑槽一端,沿第十五活动槽将第一打磨块从第一连接槽内取出,对第一打磨块做更换;新的第一打磨块从第十五活动槽处装入后,将第二限位杆连接于第六连接杆上后,再将第二限位杆插入到第十五活动槽内,第二限位杆抵在第一斜槽上,第二限位杆推动第三滑块移动,直至第二限位杆完全插入到第十五活动槽内,完成第一打磨块的更换。
29.本发明具有以下优点:1.保正叶轮叶顶间隙安全的前提下,利用叶轮运行工况自身产生的变形量,使得叶顶与叶轮盖的间隙始终处于最佳间隙δ;2.半开式叶轮和叶轮盖的间隙增大,减低整机装配的难度,提供装配效率。
附图说明
30.图1为本发明叶轮叶顶分割示意图。
31.图2为本发明中叶轮运行工况状态形变示意图。
32.图3为本发明中叶轮盖内表面轮廓加工曲线sc示意图c。
33.图4为本发明中叶轮与叶轮盖的装配示意。
34.图5为本发明打磨系统的结构示意图。
35.图6为本发明打磨系统的正视图。
36.图7为图6中沿a
‑
a处的剖视图。
37.图8为图7中的a处放大图。
38.图9为图7中的b处放大图。
39.图10为图6中沿b
‑
b处的剖视图。
40.图11为图10中的c处放大图。
41.图12为图6中沿c
‑
c处的剖视图。
42.图13为图12中的d处放大图。
43.图14为图6中沿e
‑
e处的剖视图。
44.图15为图14中的e处放大图。
45.图16为图6中沿f
‑
f处的剖视图。
46.图17为图16中的f处放大图。
47.图18为图6中沿g
‑
g处的剖视图。
48.图19为图18中的g处放大图。
49.图20为图6中沿h
‑
h处的剖视图。
50.图21为图20中的h处放大图。
51.图22为本发明打磨系统的右视图。
52.图23为图22中沿i
‑
i处的剖视图。
53.图24为图23中的i处放大图。
54.图25为图23中的j处放大图。
具体实施方式
55.一种半开式磁悬浮叶轮叶顶间隙自调节方法,包括以下步骤:
56.a、计算确定三元流叶轮的外形尺寸及轮廓;
57.b、建立叶轮三维模型,对叶轮三维模型进行切片处理;
58.c、将叶轮三维模型的中轴线与水平方向呈45
°
角放置,在叶轮三维模型中与水平方向夹角小于40
°
的叶片部位下端添加网格工艺支撑模型,网格工艺支撑模型由叶片下端连接到水平放置的盖板上表面;盖板下表面与基板之间添加实体支撑;
59.d、根据s
‑
04/s
‑
08高强不锈钢材料特点设定激光选区熔化成形加工工艺参数;
60.e、按照步骤d设定的工艺参数,在惰性气体的保护下进行激光选区熔化成形;
61.f、激光选区熔化成形完成后清理浮粉,线切割去除基板;
62.g、去除网格工艺支撑;
63.h、对叶轮进行表面处理和热处理,所述表面处理包括喷砂、三元振动、磨料流和打磨处理;
64.i、计算整机效率最高时半开式叶轮和叶轮盖的最佳间隙δ;
65.j、将半开式叶轮叶顶型线sa均分成n
‑
1段;
66.k、计算运行工况下,所分割叶顶型线sa各端点向叶轮盖方向的最大偏移量δ1δ2···
δ
n
‑1δ
n
;
67.l、以叶顶型线sa为基准,各端点向叶轮盖方向移量(δ δ1,δ δ2···
δ δ
n
‑1,δ δ
n
)并用样条曲线连接各点形成曲线sc,曲线sc即位即为叶轮盖基体的内表面轮廓加工曲线。
68.步骤j中叶顶型线san取值不小于20;步骤k分割叶顶型线sa各端点向叶轮盖方向的最大偏移量δ1δ2···
δ
n
‑1δ
n
采用有限元仿真软件计算得出;所述步骤b中,使用建模软件pro/engineer或ug建立叶轮三维模型,并导出stl格式三维模型,不设置收缩,切片厚度为30~40μm;所述步骤e中,叶轮激光选区熔化成形加工工艺参数包括:激光功率为300~320w,扫描速度为800~1000mm/s,扫描间距为0.08~0.12mm,相位角为67
°
/105
°
;网格工艺支撑激光选区熔化成形加工工艺参数包括:激光功率为250~280w,扫描速度为2200~2600mm/s,网格间距为0.6mm,扫描间距为0.08~0.12mm,相位角为67
°
/105
°
;实体支撑与叶轮激光选区熔化成形加工工艺参数相同;其中,s
‑
04/s
‑
08高强不锈钢粉末的粒度分布为
d10为15~25μm,d50为25~35μm,d90为55~65μm,粉末的松装密度为4~4.5g/cm3,50g粉的流动性≤30s;所述步骤f中,所述惰性气体为氩气,成形过程中气氛氧含量小于1000ppm;所述步骤g中所述线切割采用高速往复走丝电火花线切割,脉冲宽度设定为28~48μs,脉冲间隔为112~170μs,波形为矩形脉冲;所述步骤h中所述去除网格工艺支撑时保证型面光顺;所述步骤i中,喷砂用于对叶轮的整体初步光整,三元振动用于叶轮外型面的精光整,磨料流用于叶片型面的抛光光整;喷砂工艺要求包括:材质为刚玉砂,粒度为40目~60目,吹砂时间为6min~8min;三元振动工艺要求包括:磨料采用三种规格的棕刚玉磨料混合,其中斜圆柱规格为φ4mm
×
8mm,斜三角规格为5mm
×
5mm,圆球磨料规格为sφ6mm,斜圆柱:斜三角:圆球磨料的质量比为1:1:4;激振频率为48hz,加工时间为24h;磨料流工艺要求包括:采用中等硬度磨料粗磨,磨粒目数100目,磨削压力4.5mpa,加工时间60min;采用软性磨料精磨,磨粒目数400目,磨削压力4mpa,加工时间45min;所述步骤j中,热处理工艺包括:在1130℃保温3h作为预处理,然后空冷;在1040℃~1110℃保温2h进行固溶,然后空冷;在
‑
70℃保温2h进行冷处理,然后在空气中恢复至室温,在250℃~350℃保温3h进行时效,然后空冷。
69.图1将半开式叶轮叶顶型线sa均分成n
‑
1段(n≥20);图2中局部放大图中δ
m
为叶轮轴向变形量
△
a和径向变形量
△
r矢量和(δ
m
为δ1,δ2···
δ
n
‑1,δ
n
),用样条曲线依次连接δ
m
各点形成叶片形变曲线sb;图3为曲线sb沿叶轮盖方向偏移δ形成曲线sc,曲线sc即为叶轮盖基体的内表面轮廓加工曲线;图4为叶轮和叶轮盖组装后的间隙(δ δ1,δ δ2···
δ δ
n
‑1,δ δ
n
)示意图,该间隙保正安全的前提下,利用叶轮运行工况自身产生的变形量,使得叶顶与叶轮盖的间隙始终处于最佳间隙δ,进而提高了整机的效率。
70.其中,所述步骤h中的打磨处理操作为将叶轮放入到打磨系统内完成叶轮的打磨处理,如图5
‑
25所示,所述打磨系统包括处理台10和设于所述处理台10一侧的输送装置,所述处理台10上设有加工槽,所述加工槽内设有第一打磨块14,所述输送装置包括设于所述处理台10一侧的底座20、设于所述底座20上的连接盘21及设于所述连接盘21上的多个第一连接板22,所述底座上设有用于驱动连接盘转动的第二电机,所述连接盘底部设有连接环,所述底座上设有与所述连接环相配合的环槽;在连接环和环槽设置下使第一连接板转动更加稳定;所述第一连接板22上设有与所述加工槽相对应的第一通孔,所述第一通孔内壁上设有第一活动槽,所述第一活动槽内设有支撑板23;所述处理台10上设有设备腔,所述设备腔内设有第一气缸11,所述第一气缸11的活塞杆上设有承接板12,所述处理台10上方设有用于驱动叶轮转动的第一电机31;叶轮在做表面处理时将叶轮放入到第一通孔内,支撑板23处于第一通孔底部,连接盘21转动带动叶轮转动,叶轮转动至加工槽上方,第一气缸11推动承接板12往上运动,承接板12上升至第一通孔底部,支撑板23进入到第一活动槽内,第一通孔内的叶轮掉落在承接板12上,承接板12带动叶轮往下运动至加工槽内,第一连接板22继续转动从加工槽上方移开,第一电机31驱动叶轮转动,第一打磨块14与叶轮侧壁相接触打磨叶轮侧壁,完成叶轮的打磨处理;叶轮打磨完成后,连接盘21继续转动,第一连接板22再次转动至加工槽上方,承接板12带动叶轮往上运动,支撑板23进入到第一活动槽内后,叶轮进入到第一通孔内,随后支撑板23从第一活动槽内伸出移动至叶轮底部,承接板12下降,第一连接板22转动将叶轮运出。
71.如图7、8、9、18所示,所述第一电机31上方设有第二气缸30,所述第一电机31设于所述第二气缸30的活塞杆上,所述第一电机31的输出轴上设有第一连接杆33,所述第一连
接杆33上设有安装槽,所述安装槽内设有第二打磨块331;所述第一连接杆33侧壁上还设有第二活动槽,所述第二活动槽内设有第一固定块332,所述加工槽内壁上设有第三活动槽,所述第三活动槽内设有第二固定块18;叶轮放置于加工槽内后,第一连接板22从加工槽上方转开,第二气缸30驱动第一连接杆33往下运动,第一连接杆33插入到叶轮轴孔内,第二固定块18从第三活动槽内伸出抵在叶轮侧壁上,第一电机31驱动第一连接杆33转动,第一连接杆33相对于叶轮转动,第二打磨块331与叶轮轴孔内壁相接触,对叶轮轴孔内壁做打磨;叶轮轴孔内壁打磨完成后,第一连接杆33往上运动,第二固定块18进入到第三活动槽内,第一固定块332从第二活动槽内伸出,第一固定块332抵叶轮轴孔内壁上,第一电机31带动第一连接杆33转动时带动叶轮转动,叶轮侧壁与第一打磨块14相接触,完成叶轮侧面的打磨处理。
72.如图9、18、21所示,所述第二固定块18侧壁上设有第一连接弹簧181,所述第三活动槽底部设有第一传动槽,所述第一传动槽底部设有第四活动槽,所述第一传动槽内设有与所述第二固定块18相配合的第一传动辊140;所述承接板12上设有凹槽,所述凹槽侧壁上设有第一通腔,所述第一通腔内壁上设有第一活动腔,所述第一通腔内穿设有与所述第四活动槽相配合的第一传动板123,所述第一传动板123上设有第一限位杆124,所述第一限位杆124上设有第一复位弹簧125;所述凹槽内设有气囊122,所述气囊122顶部设有第一推板121;叶轮处于承接板12上时,叶轮的轴孔处于第一推板121位置,第一连接杆33往下运动插入到叶轮轴孔内后,第一连接杆33推动第一推板121往下运动,第一推板121推动气囊122形变,气囊122内的空气进入到第一通腔内,气压推动第一传动板123往空腔外移动,第一传动板123插入到第四活动槽内,第一传动板123带动第一传动辊140转动,第一传动辊140带动第二固定块18往第三活动槽外侧移动,第二固定块18伸入到加工槽内抵在叶轮侧壁上,第一连接杆33相对叶轮转动,对叶轮的轴孔内壁做打磨处理。
73.如图8所示,所述第一电机31的输出轴上设有第二连接杆34,所述第一连接杆33上设有第二通腔,所述第二连接杆34穿设于所述第二通腔内,所述第二通腔内壁上设有第二活动腔,所述第二连接杆34上设有与所述第二活动腔相配合的第一限位板341,所述第一限位板341底部设有第二复位弹簧342,所述第二活动腔顶部设有与所述第二活动槽相通的第五活动槽,所述第一固定块332上设有第三连接杆333,所述第三连接杆333穿设于所述第五活动槽内,所述第五活动槽内可转动连接有第一传动杆334,第一传动杆中部可转动连接于第五活动槽内壁上,所述第五活动槽底部穿设有推杆335,所述推杆335上设有第一滑块,所述第五活动槽内壁上设有与所述第一滑块相配合的第一滑槽;第一连接杆33往下运动时,第一连接杆33插入到叶轮的轴孔内,第一连接杆33移动至叶轮轴孔底部后,第二连接杆34相对于第一连接杆33移动,第二连接杆34推动第一推板121往下运动,第一推板121挤压气囊122,第二固定块18从第三活动槽内伸出抵在叶轮侧壁上;当叶轮轴孔内壁打磨完成后,第二连接杆34相对于第一连接杆33往上运动,第一推板121往上运动,第一传动板123进入到第一通腔内,第二固定块18进入到第三活动槽内;第一限位板341随第二连接杆34往上运动,第一限位板341推动推杆335往上运动,推杆335推动第一传动杆334一端转动,第一传动杆334绕连接点转动,第一传动杆334另一端推动第三连接杆333移动,第三连接杆333带动第一固定块332往第二活动槽外移动,第一固定块332从第二活动槽内伸出抵在叶轮轴孔内壁上,完成第一连接杆33与叶轮的连接,第一电机31驱动第二连接杆34转动时带动第一连
接杆33转动,叶轮随第一连接杆33转动,对叶轮侧壁做打磨处理。
74.如图9、18、19所示,所述加工槽内壁上设有第六活动槽,所述第六活动槽内设有第一连接块13,所述第一连接块13上设有第二连接弹簧131,所述第一连接块13上设有第一连接槽,所述第一打磨块14设于所述第一连接槽内,所述第一连接槽内壁上设有第三复位弹簧132;所述处理台10上设有用于连通所述第三活动槽和所述第六活动槽的连接腔,所述连接腔内壁上设有空腔,所述空腔内壁上设有第三连接弹簧181,所述第三连接弹簧181上设有第二推板18,所述空腔内壁上设有与所述第二推板18相配合的密封块19;所述第六活动槽内壁上设有第七活动槽,所述第七活动槽内壁上设有第四连接弹簧1201,所述第四连接弹簧1201一端设有第二连接板120,所述第二连接板120上设有第一棘齿;所述空腔内壁上设有第八活动槽,所述第八活动槽内壁上设有第五连接弹簧,所述第五连接弹簧一端设有第三连接板110,所述第三连接板110上设有第二棘齿;所述第一连接块上设有伸缩管130;第一连接块13处于第六活动槽内,第二固定块18处于第三活动槽内时,空腔处于开启状态,第二推板18处于靠近空腔内壁位置处;叶轮放入到加工槽内时,第二固定块18从第三活动槽内时伸出,第二推板18推动空腔内的空气进入到连接腔内,第二推板18移动至第三连接板110一侧,第二推板18与第三连接板110相接触,第二棘齿将第二推板18固定在密封块19上,第二推板18处于空腔入口处将空腔封闭;当叶轮轴孔内壁打磨完成后,第二固定块18进入到第三活动槽内,第二固定块18挤压第三活动槽内的空气,空气通过连接腔进入到伸缩管内,气压推动第一连接块13从第六活动槽内伸出,第一棘齿与第一连接块13侧壁相接触将第一连接块13固定;当叶轮侧壁打磨完成后,第二连接板120进入到第七活动槽内,第三连接板110进入到第八活动槽内,第一连接块13往第六活动槽内移动,第一连接块13推动第六活动槽内空气进入到空腔内,空气再次存储在空腔内。
75.如图7、13、18、24所示,所述处理台10上设有第九活动槽,所述第九活动槽内穿设有第四连接杆16,所述第四连接杆16底部设有第二限位板162,所述第二限位板162上设有第四复位弹簧163,所述第二连接板120和所述第三连接板110上分别设有第一连接绳和第二连接绳,所述第一连接绳和所述第二连接杆34一端均固连于所述第四连接杆16上;所述第四连接杆16顶部设有第四连接板161;所述第一电机31下方设有连接柱32,连接柱固连于厂房天花板上,所述连接柱32上设有第三通腔,所述第一连接杆33穿设于所述第三通腔内,所述第一连接杆33侧壁上设有第二滑块336,所述第三通腔内壁上设有与所述第二滑块336相配合的第二滑槽,第二滑块为圆盘形结构,第二滑槽为圆管形结构,保证第一连接杆能够正常转动;所述第二滑槽内壁上设有第十活动槽,所述第十活动槽内设有第六连接弹簧322,所述第六连接弹簧322一端设有限位块321;限位块上设有第二斜槽,在第二斜槽设置下使第二滑块往下运动时可直接推动限位块进入到第十活动槽内;所述连接柱32侧壁上设有与所述第十活动槽相通的第十一活动槽,所述第十一活动槽内设有活动块323,所述活动块323上设有第三连接绳324,所述第三连接绳324一端固连于所述限位块321上;所述处理台10上方设有防尘罩40,所述防尘罩40上设有与所述连接柱32相配合的第一通槽,所述防尘罩40内壁上设有与所述第四连接板161相配合的第一凸块41;叶轮放置在加工槽内后,防尘罩40往下运动罩在加工槽内,第二气缸30推动第一连接杆33往下运动,第一连接杆33穿入到叶轮的轴孔内,对叶轮做打磨处理;叶轮打磨完成后,罩壳往上运动,罩壳内壁上的第一凸块41与第四连接板161相接触,第一凸块41带动第四连接板161一同往上运动,第四连
接板161带动第四连接杆16往上运动,第一连接绳和第二连接绳拉动第二连接板120和第三连接板110移动,第一连接块13进入到第六活动槽内;罩壳继续往上移动时,第一通槽内壁与活动块323侧壁相接触,罩壳带动活动块323往上运动,活动块323带动限位块321往第十活动槽内移动,第二连接杆34往上运动带动第一连接杆33往上运动,第一连接杆33从叶轮轴孔内脱出;第二气缸30推动第二连接杆34往下运动时,第二连接杆34带动第一连接杆33往下运动,第二滑块336移动至第二滑槽底端,第二滑块336夹在第二滑槽内壁和限位块321之间,将第二滑块336固定,第二连接杆34可相对第一连接杆33移动,对第一固定块332和第二固定块18的运动做控制。
76.如图9、17所示,所述第一活动槽顶部设有第十二活动槽,所述第十二活动槽内设有与所述支撑板23相配合的第二传动辊24,所述第一连接板22底部设有与所述第十二活动槽相通的第十三活动槽,所述第十三活动槽内设有与第二传动辊24相配合的第二传动杆25,所述第二传动杆25顶部设有第五复位弹簧252,底部设有第五连接杆251;所述第十二活动槽内壁上设有第十四活动槽,所述第十四活动槽内设有第五连接板26,所述第二传动辊24两端分别设有连接轴241,所述连接轴241穿设于所述第五连接板26上,所述第五连接板26上设有第二凸块261,所述第二传动杆25设有与所述第二凸块261相配合的第三凸块253;第一连接板22带动叶轮移动至加工槽上方时,承接板12往上运动推动第五连接杆251往上运动,第五连接杆251带动第二传动杆25往上运动,第二传动杆25带动第二传动辊24转动,第二传动辊24带动支撑板23往第一活动槽内移动,叶轮从第一通孔内掉落在承接板12上,随承接板12进入到加工槽内;叶轮加工完成后,第一连接板22再次转动至加工槽上方,承接板12带动叶轮往上运动,叶轮进入到第一通孔内后承接板12推动第五连接杆251继续往上运动,第三凸块253与第二凸块261相接触,第三凸块253推动第二凸块261往上运动,第二凸块261带动第五连接板26往上运动,第五连接板26带动第二传动辊24往上运动,第二传动辊24与支撑板23脱开接触,支撑板23从第一活动槽内伸出,承接板12下降,叶轮处于第一通孔内随第一连接板22运出。
77.如图9、11所示,所述第一连接槽内壁上设有第三滑槽,所述第二打磨块331侧壁上设有与所述第三滑槽相配合的第三滑块141,所述第三滑块141上设有第一斜槽,所述第三滑槽顶部设有第十五活动槽,所述第六活动槽顶部设有开口,所述开口内设有挡块15,所述开口内壁上设有与所述第十五活动槽相配合的第十六活动槽,所述挡块15侧壁上设有与所述第十六活动槽相配合的第六连接杆151,所述第十五活动槽内穿设有第二限位杆152,所述第二限位杆152上设有第二连接块153,所述第六连接杆151上设有于所述第二连接块153相配合的第二连接槽;所述防尘罩40上设有储水腔,所述储水腔侧壁上设有多个喷水口,所述储水腔顶部设有进水管;所述承接板12上设有第二通槽,所述加工槽底部设有与所述第二通槽相通的排水腔;叶轮做打磨处理时,防尘罩40罩在加工槽上,水流从进水管处进入到储水腔内,储水腔内装满水流后,水流从喷水口处喷出,水流喷洒在加工槽内,水流写到粉尘进入到第二通槽内,从排水腔内排出;在对第一打磨块14做更换时,往上拉动第六连接杆151,第六连接杆151带动第二限位杆152往上运动,第二限位杆152从第十五活动槽内取出,第三复位弹簧132推动第三滑块141移动至第三滑槽一端,沿第十五活动槽将第一打磨块14从第一连接槽内取出,对第一打磨块14做更换;新的第一打磨块14从第十五活动槽处装入后,将第二限位杆152连接于第六连接杆151上后,再将第二限位杆152插入到第十五活动槽
内,第二限位杆152抵在第一斜槽上,第二限位杆152推动第三滑块141移动,直至第二限位杆152完全插入到第十五活动槽内,完成第一打磨块14的更换;在防尘罩设置下对灰尘起聚集作用,避免打磨产生的粉尘飘散在厂房内,减少粉尘对厂房环境的影响;通过清水喷淋作用,进一步的减少粉尘的飘散,使粉尘的收集更加方便,以便对粉尘做统一处理。本技术附图仅为示意图,打磨系统的具体尺寸以实际实施为准。
再多了解一些
本文用于企业家、创业者技术爱好者查询,结果仅供参考。