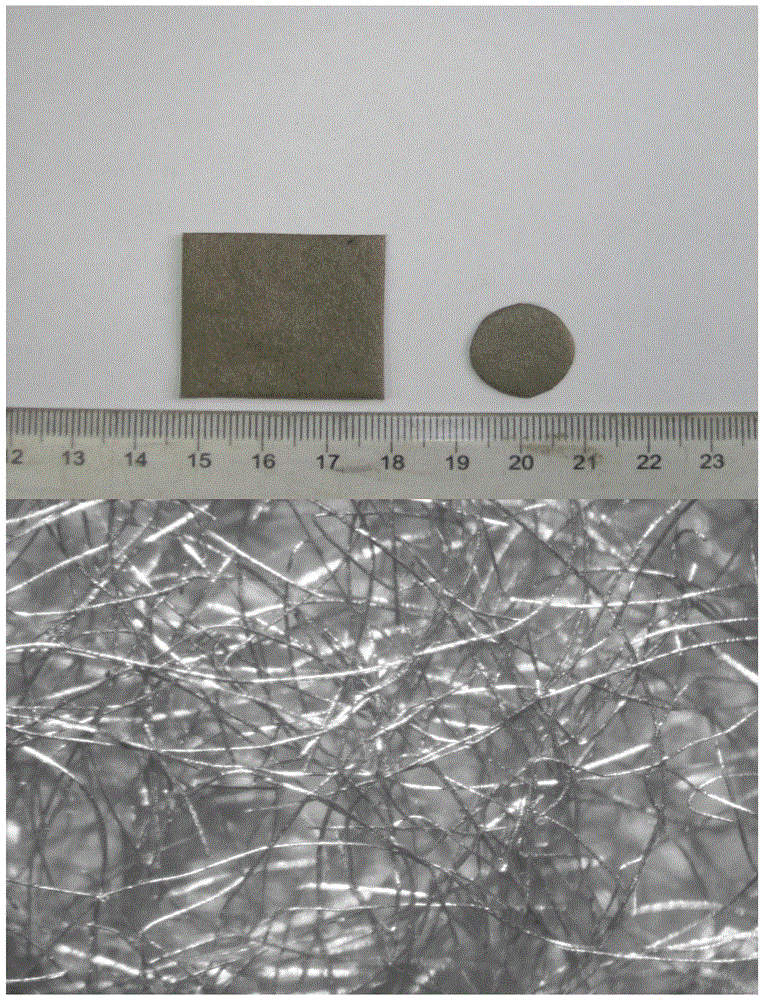
本发明涉及石油化工技术领域,具体而言,涉及一种硫酸催化制备烷基化油的方法。
背景技术:
随着中国经济的高速增长,以往高污染、高能耗、高排放的经济发展方式已不再适合现阶段的我国国情,急需转型升级。随着汽油国六标准的实施和环保要求的不断提高,炼油产业急需升级换代,而烷基化油是最理想的汽油调和组分,但烷基化油在我国汽油池中的占比不足5%,主要依赖进口,自身产能严重不足,因此推进烷基化技术发展对我国能源模式的转型升级具有重要意义。
目前异丁烷/丁烯的烷基化工艺主要有硫酸法、氢氟酸法、离子液体法和固体酸法。在全世界范围内,硫酸法和氢氟酸法占据全球烷基化产能的90%,由于氢氟酸法对环境污染严重,新建烷基化装置已经基本弃用氢氟酸法。虽然离子液体法和固体酸法清洁高效,但尚处于研究开发阶段,尚未得到普及推广。硫酸法是相对稳定安全的烷基化油生产工艺,但也存在设备腐蚀、酸烃分离困难、酸耗高及能耗大等缺点。在我国现阶段烷基化油产能不足的情况下,改进的硫酸法烷基化工艺仍具有不错的工业化应用前景。
在硫酸法烷基化反应中,异丁烷与丁烯在浓硫酸催化作用下,生成c6 烷基化油,该反应为快速强放热反应。为了提高传质及传热速率,反应器需配备搅拌混合器或者静态内构件,使物料之间具有较高的相界面积以利于传质传热。硫酸法烷基化油生产的反应温度通常在15℃以下,因此反应器需要配备制冷系统,使反应物处于最佳的反应温度并及时移出反应热,而异丁烷压缩制冷是常用的制冷方法。硫酸法烷基化是目前最成熟的烷基化油生产工艺,在全世界范围内均有广泛的应用,其存在的问题有:酸烃分离困难、能耗及酸耗高,设备腐蚀严重等问题。
鉴于此,特提出本发明。
技术实现要素:
本发明的目的是为了克服上述现有技术存在的缺陷而提供一种硫酸催化制备烷基化油的方法。
本发明是这样实现的:
本发明提供一种硫酸催化制备烷基化油的方法,以异丁烷和c4烯烃为原料,浓硫酸为催化剂,整体式烧结金属微纤为填充材料,使原料与催化剂在反应器中相接触发生烷基化反应,回收所得到的烷基化油。
本发明具有以下有益效果:
本发明提供一种硫酸催化制备烷基化油的方法,硫酸法制备烷基化油的过程中以整体式烧结金属微纤作为填料,整体式烧结金属微纤可以促进浓硫酸和混合烃分散成小液滴,增进混合效果,并且整体式烧结金属微纤具有良好的热传导性可及时移除反应产生的热量,使反应床层温度均一,进而提高反应效率和碳八组分选择性。
附图说明
为了更清楚地说明本发明实施例的技术方案,下面将对实施例中所需要使用的附图作简单地介绍,应当理解,以下附图仅示出了本发明的某些实施例,因此不应被看作是对范围的限定,对于本领域普通技术人员来讲,在不付出创造性劳动的前提下,还可以根据这些附图获得其他相关的附图。
图1是实施例1中的整体式金属微纤s-ni的光学照片;
图2是实施例2中的整体式金属微纤s-ss的光学照片;
图3是实施例1中的整体式金属微纤s-ni的sem照片;
图4为本发明实施例中的烷基化油的反应流程示意图。
具体实施方式
为使本发明实施例的目的、技术方案和优点更加清楚,下面将对本发明实施例中的技术方案进行清楚、完整地描述。实施例中未注明具体条件者,按照常规条件或制造商建议的条件进行。所用试剂或仪器未注明生产厂商者,均为可以通过市售购买获得的常规产品。
本发明的目的在于提供一种硫酸催化制备烷基化油的方法,该方法提出:以浓硫酸为催化剂,以整体式烧结金属微纤为填充材料,使原料与催化剂在反应器中相接触发生烷基化反应。
本发明的目的是这样实现的:
本发明实施例提供一种硫酸催化制备烷基化油的方法,以异丁烷和c4烯烃为原料,浓硫酸为催化剂,整体式烧结金属微纤为填充材料,使原料与催化剂在反应器中相接触发生烷基化反应,回收所得到的烷基化油。
本发明实施例提供一种硫酸催化制备烷基化油的方法,突破传统烷基化油的制备方法,由于硫酸催化烷基化反应为快速强放热反应,因此反应过程中必须快速及时移除反应过程中产生的热量,本发明实施例提出的硫酸法烷基化油的制备,在反应器中添加了具有良好热传导性可及时移除反应产生的热量的填料,可使反应快速进行,效率高时间短,产物易于分离。
在可选的实施方式中,整体式烧结金属微纤的材质为镍、不锈钢、铝、锌、紫铜或黄铜。
在可选的实施方式中,金属微纤的直径为2-100微米,长度为2-10毫米。
在可选的实施方式中,整体式烧结金属微纤的空隙率为88-98%。
本发明实施例提供的硫酸法烷基化油的制备过程中,将整体式金属微纤材料填充于反应管内用于硫酸法烷基化反应,该整体式烧结金属微纤是一种三维网状的、大体积/面积比的微纤结构,整体式烧结金属微纤起到混合搅拌的作用,且可使浓硫酸和混合烃分散成微米级的小液滴,使其反应更加高效充分,进而提升反应效率和碳八组分选择性。该整体式烧结金属微纤材料具有大空隙率及良好的传质传热性能,压降小,成本低,其良好的热传导性可及时移除反应产生的热量,使反应床层温度均一,进而提高反应效率和碳八组分选择性。
在可选的实施方式中,c4烯烃为1-丁烯、2-丁烯、异丁烯或者上述烯烃混合物。
在可选的实施方式中,原料异丁烷和c4烯烃的摩尔比为8-30:1,优选为10-25:1,进一步优选为12-20:1。本发明实施例中的烷烯摩尔比是指异丁烷与c4烯烃的摩尔比,反应过程中异丁烷比例越高,烯烃的转化率就越高,但过高的烷烯比会造成反应效率降低,能耗增加。
在可选的实施方式中,浓硫酸与原料的体积比为0.5-8:1,优选为0.5-4:1,进一步优选为0.5-2:1。本发明实施例中的酸烃体积比是指浓硫酸与混合烃的体积比,在所述酸烃比条件下能够保证浓硫酸为连续相,使酸烃乳化效果更均匀,混合效果更好,反应效果更佳,反应效率更高。
在可选的实施方式中,烷基化反应的温度控制在2-15℃为宜,优选为2-10℃。
在可选的实施方式中,浓硫酸的质量浓度大于80%,优选为85-99%,进一步优选为90-98%。
硫酸法烷基化反应中,异丁烷和c4烯烃在浓硫酸催化作用下,生成c6 烷基化油,该反应为快速强放热反应。本发明提出的烷基化油的制备方法,在反应器中填充整体式烧结金属微纤作为填料,该整体式烧结金属微纤材料具有大空隙率及良好的传质传热性能,可及时移除反应产生的热量,因此,在烷基化油的制备过程中,控制温度在2-15℃之间,反应器中的原料与催化剂相接触之后,可在几秒钟之内完成烷基化反应,反应效率也大幅提高,反应时间极大的缩短。
在可选的实施方式中,按以下步骤进行:将整体式金属微纤剪成数个直径与反应器直径相同的小圆片叠放于直径为t型圆管反应器内,并将该t型圆管反应器置于12℃以下的冰水浴中,用泵分别打入浓度为80-99%的浓硫酸和烷烯摩尔比为8-30:1的异丁烷和c4烯烃混合烃原料,且浓硫酸与烷烯的体积比为0.5-8:1,浓硫酸和混合烃经过整体式金属烧结微纤分散后,进行烷基化反应,反应完成后,产物从t型圆管反应器流出,静置分离后得到上层的烷基化油。
可见,本发明实施例提供的烷基化油的制备方法,其特点是:以整体式烧结金属微纤为填充材料,其空隙率为88-98%,将其裁剪成适合大小,叠放填充于圆管中,浓硫酸和混合碳四烃分别经过有整体式烧结金属微纤填充的圆管后,混合反应。所用金属微纤的材质是镍、不锈钢、铝、锌、紫铜或黄铜;金属微纤直径为2-100微米,长度为2-10毫米。
以下结合实施例对本发明的特征和性能作进一步的详细描述。
整体式烧结金属微纤的制备步骤如下:
采用造纸/后烧结技术,制备具有大空隙率、三维网状结构的烧结金属微纤,具体制备过程为:将10g长2-3mm的金属微纤和3.3g纤维素加入到1l水中打浆,在纸页成型器上制成薄层滤饼,经110℃烘干,450℃空气气氛中氧化脱除纤维素后,再于氢气氛围中烧结1h,形成具有三维微米孔结构的整体式烧结金属微纤ni-fiber(参见图1)及steel-fiber(参见图2),金属微纤分别是:8微米直径的ni微纤,12微米直径的不锈钢(合金,ss-316l)微纤,8微米直径的cu微纤和8微米直径的al微纤;制备整体式烧结金属微纤的氢气氛围中烧结温度分别为:950℃,1200℃,850℃和700℃。
制得的整体式烧结金属微纤分别表示为:s-ni,s-ss,s-cu和s-al;其空隙率分别为95%(体积分数),92%(体积分数),93%(体积分数)和90%(体积分数)。
整体式烧结金属微纤s-ni的光学照片参阅图1,扫描电镜(sem)照片参阅图3。
实施例1
将制得的整体式金属微纤s-ni剪成数个直径为6毫米的小圆片叠放于直径为6毫米的t型圆管反应器内,并将该t型圆管反应器置于2度左右的冰水浴中,如图4所示,用泵分别打入浓度为98%的浓硫酸和烷烯摩尔比为15:1的异丁烷和正丁烯混合烃原料,浓硫酸和混合烃的体积比为1:1,流速均为20毫升/分,浓硫酸和混合烃经过整体式镍微纤分散后,进一步混合反应后,产物从t型圆管反应器流出,静置分离后得到上层的烷基化油产物。
实施例1中整体式烧结金属微纤s-ni的光学照片参阅图1,扫描电镜(sem)照片参阅图3。
实施例2-4
分别用制得的s-ss,s-cu和s-al整体式金属微纤替代实施例1中的s-ni整体式金属微纤进行反应,其它同实施例1。
实施例5
催化剂采用浓度为94%的浓硫酸反应,其它同实施例1。
实施例6
反应原料采用烷烯摩尔比为8:1的异丁烷和正丁烯混合烃,其它同实施例1。
实施例7
反应原料采用烷烯摩尔比为30:1的异丁烷和正丁烯混合烃,其它同实施例1。
实施例8
浓硫酸和混合烃的体积比为2:1,浓硫酸的流速为20毫升/分,混合烃的流速为10毫升/分,其它同实施例1。
对比例
将100毫升(约184克)浓度为98%的浓硫酸倒入400毫升反应釜中,首先用氮气置换反应釜中的空气,启动搅拌,控制转速在1000转/分,启动制冷,温度控制在8℃,氮气充压至0.4mpa;随后,用泵打入烷烯体积比为15:1的异丁烷和正丁烯混合烃原料100毫升进行烷基化反应8分钟。反应完成后,静置分离后得到烷基化油产物。
以下表1为上述实施例1-8和对比例1的反应结果。
表1反应结果
从表1中可以看出,相比釜式反应的对比例,添加整体式烧结金属微纤作为填充材料时,烷基化油产物的选择性、产品质量和反应效率有了很大提高。具体体现在反应产物中c8含量特别是tmp(三甲基戊烷)的含量大幅提高,c5-7以及c9 的含量大幅降低,同时,产品辛烷值也有明显提高,且反应时间由分钟级缩短为秒级。以实施例1为例可以看出,添加整体式烧结金属微纤作为填充材料时,与对比例中纯浓硫酸烷基化的效果相比,产物中tmp的选择性提高了34.35个百分点,c8选择性提高了31.35个百分点,c9 的选择性降低了25.49个百分点,研究法辛烷值由85提高到了95。
可见采用填充整体烧结金属微纤的t型圆管反应器的c8选择性和tmp选择性大幅提高,且反应效率也大幅提高(反应时间缩短),充分体现了金属微纤的优越性。
综上,本发明实施例提供了一种硫酸催化制备烷基化油的方法,以异丁烷和c4烯烃为原料,浓硫酸为催化剂,整体式烧结金属微纤为填充材料,使原料与催化剂在反应器中相接触发生烷基化反应,回收所得到的烷基化油。本发明实施例提供的烷基化油的制备方法,以整体式烧结金属微纤为填充材料,将其裁剪成适合大小,叠放填充于圆管中,浓硫酸和混合碳四烃分别经过有整体式烧结金属微纤填充的圆管后,混合反应,该整体式金属微纤材料具有大空隙率及良好的传质传热性能,压降小,成本低,其具有良好的热传导性可及时移除反应产生的热量,使反应床层温度均一,进而提高反应效率和碳八组分选择性。
本发明提供的硫酸法烷基化油的生产方法有以下优点:
(1)、整体式金属微纤是具有大空隙率、三维网状结构烧结的金属微纤。
(2)、整体式金属微纤具有良好的渗透性及传质传热性能。
(3)、工艺简单,生产成本低。
(4)、浓硫酸和混合烃分散混合效果好,反应效率高,碳八组分选择性好,烷基化油辛烷值高。
以上仅为本发明的优选实施例而已,并不用于限制本发明,对于本领域的技术人员来说,本发明可以有各种更改和变化。凡在本发明的精神和原则之内,所作的任何修改、等同替换、改进等,均应包含在本发明的保护范围之内。
本文用于企业家、创业者技术爱好者查询,结果仅供参考。