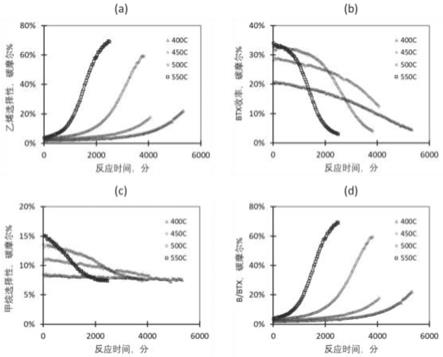
1.本发明涉及由轻烃生产芳烃和/或液体燃料的方法。
背景技术:
2.自2000年中期以来,页岩气的革命导致北美天然气(ng)和天然气液体(ngls)产量呈指数增长。这直接导致了ngl组分尤其是乙烷的价格在近几年达到了低谷。丰富且低价的乙烷也使得乙烯的生产从传统的以石脑油为原料转换为以乙烷为主要原料,并且由于供应量不断增加,价格也趋于低下。另一方面,从石脑油催化重整切换至乙烷裂化,也使得芳烃生产量不足,价格上涨。客观上形成了与乙烷、乙烯价格上的一个较大的落差。
3.将轻烃直接转化成芳烃化合物一直以来是学术界和工业界的主要兴趣之一。在过去的数十年中,shell oil、exxon mobil、sabic和其它一些发明者已被授权或正在申请多项相关专利。从化学反应机理的角度来看,乙烷至芳烃的转化需要经过乙烯作为中间产物的步骤。即乙烷首先需要被脱氢活化至具有高反应性的中间体乙烯。然后,乙烯在酸性位上低聚/芳构化转化成芳烃化合物等。脱氢步骤通常需要由pt、pd等贵金属的脱氢功能来实现,低聚/芳构化则通常在沸石催化剂如zsm-5上实现。因此,通过一步法将乙烷直接转化为芳烃产物需要在双功能催化剂存在下实现。然而由于热力学的限制,烷烃脱氢需要在较高温度下完成,例如乙烷脱氢,理想的条件是750℃以上。另一方面,zsm-5分子筛催化的烯烃芳构化反应是放热过程,以400-500℃为适当的温度范围,过高的温度将导致焦化和大量裂解产物甲烷的生成,从而使催化剂快速失活。
4.鉴于此,目前的一步法工艺开发一般是选在550-650℃的温度范围内进行的,显然,这是为了兼顾两步反应条件的一种折衷的选择。在此温度条件下,乙烷转换率是有限的,最高乙烷至乙烯的平衡转化率低于30%,但对分子筛催化的碳氢化合物之间的转换,此温度已经过高,积碳和副产物生成严重。
5.从产物组成来说,一步法的主要缺点是裂解产物甲烷和重组分(一般是指碳数大于10的芳烃组分)的选择性甚高,从而导致碳利用率的低下。例如,在us8946107b2公开的结果中,甲烷选择性高达38%,通过添加0.08%的fe可以降低甲烷选择性至24%,但同时乙烷转化率也降低了约10%。再例如,us10087124公开了在540-560℃、whsv为1.0g-c2h6/g-cat.hr下从流化床反应器获得的乙烷芳构化结果,在三个循环寿命运行中的平均乙烷转化率仅为约30%,总芳烃选择性(a6 )接近70%,而重质芳烃组分(a10 )接近总碳基产物的20%,占总芳烃产物的30%。从而导致碳基原料的损失。
6.一步法中使用的双功能催化剂的另一个缺点是贵金属如pt会在高温下烧结,经过若干次循环使用后,再生会越来越困难,催化剂活性也随之下降。在极端的情况下,需要使用氯化再分散的再生手段,但效果也是有限的。
技术实现要素:
7.本发明的目的是为了克服现有技术中,轻烃转化为芳烃过程中存在的芳烃收率
低,碳利用率低,催化剂容易失活等问题,提供一种新的轻烃脱氢芳构化生产芳烃的方法,通过该方法能够获得较高的芳烃收率和碳利用率,且能够有效地解决催化剂失活等问题,使催化剂的使用寿命大大延长。
8.如前所述,一步法的温度选择是一个两难问题,目前一步法用于将烷烃转化为芳烃的主要缺点是(1)由于温度限制而限制了乙烷转化率;(2)由焦化引起的催化剂快速失活,因而需要频繁再生;(3)裂解产物甲烷含量较高;(4)液体产物中重质芳烃组分例如萘的比例高,由于甲烷和重质芳烃组分都是不希望得到的副产物,它们的生成导致碳利用率的降低;(5)贵金属如pt作为主要催化剂组分,其价格昂贵、容易烧结,难以再生;(6)催化剂单程寿命只有数小时,因而在工艺设计中必须考虑使用复杂的反应器系统如流化床或移动床,这将不可避免地增加工艺的复杂性以及设备和运营成本。
9.本发明的发明人发现,通过将脱氢与低聚/芳构化进行分离,分步骤执行,可以容易地获得高烷烃转化率和液体芳烃的收率,在整个两步法工艺中,无需使用贵金属催化剂,从而可以有效地降低催化剂成本。
10.本发明提供了一种轻烃脱氢芳构化生产芳烃的方法,该方法包括以下步骤:
11.1)在脱氢反应条件下,将轻烃物流进行脱氢反应,得到含烯烃的物流;
12.2)在芳构化反应条件下,将含烯烃的物流与芳构化催化剂接触,进行低聚/芳构化反应,得到含有芳烃和/或液体燃料的物流;
13.其中,所述芳构化催化剂含有沸石分子筛和负载在沸石分子筛上的活性金属组分和可选的粘结剂。
14.如上所述,本发明打破现有技术使用双功能催化剂的思维定势,通过将脱氢与低聚/芳构化进行分离,步骤1)可以包括乙烷的催化脱氢、热脱氢和水蒸汽裂化等常规且成熟的工艺。步骤2)使用金属如ga改性的沸石分子筛如zsm-5作为催化剂,可以在低温条件下,特别是在350-550℃的范围内,选择性地将从步骤1)产生的烯烃(主要是乙烯)转化成芳族化合物,例如苯、甲苯、二甲苯和/或其它液体烃类。本发明使用不同的条件分步骤执行,获得了如下效果:1)可以通过改变脱氢区的条件来独立地控制轻烃转化,以实现高烷烃转化率和最小的失活;2)产物选择性可在低聚/芳构化步骤中由工艺条件控制;3)通过使用负载金属的沸石分子筛催化剂,能够进一步降低反应温度,提高芳烃及液体油品的收率。从而通过该方法能够获得(1)较高的烷烃转化率,(2)较高的碳利用率,(3)较高的单循环芳烃生成量;且催化剂失活缓慢,单程寿命长,易再生,并具有良好的多循环稳定性。由于低温操作且催化剂寿命长、可以选择固定床反应器用于工业化生产,这将使工艺设计简单易行、成本低。鉴于这些技术优点和已证明的催化剂性能,可以预见,本发明方法在进行中试放大,以至实现商业化规模生产的过程中技术壁垒较小。
附图说明
15.图1是本发明方法的一种实施方式的工艺流程图。
16.图2是实施例1通过串联反应器,基于乙烷计算的btx收率和产物选择性随时间变化的结果图。
17.图3是对比例1和对比例2中,一步法btx收率随时间变化的结果图。
18.图4是通过串联反应器,基于乙烷计算的在450℃下,通过含镓与不含镓的催化剂,
btx收率随时间变化的比较。
19.图5是在450℃、3bar多循环寿命实验中第一个循环运行中,根据乙烯计算的乙烯转化率、btx收率、甲烷选择性(a)以及btx组分选择性分布(b)随时间的变化。
20.图6是图5实验中催化剂循环稳定性的结果图,其中(a)为btx收率或乙烯转化率达到一定水平所需的时间,(b)为催化剂的乙烯转化容量,(c)为催化剂的btx生产容量。
具体实施方式
21.在本文中所披露的范围的端点和任何值都不限于该精确的范围或值,这些范围或值应当理解为包含接近这些范围或值的值。对于数值范围来说,各个范围的端点值之间、各个范围的端点值和单独的点值之间,以及单独的点值之间可以彼此组合而得到一个或多个新的数值范围,这些数值范围应被视为在本文中具体公开。
22.图1是显示本发明方法的简化工艺流程图。如图1所示,轻烃(轻质烷烃,沸点不超过-10℃)如乙烷将首先进行脱氢,生成对应的烯烃如乙烯,然后烯烃再进行低聚/芳构化,生成芳烃和其它液体燃料。
23.关于该两步法工艺,本发明的发明人在之前的专利文献中提到过,其将低级烷烃至芳族化合物的转化分成两步,其中步骤1)的目标是烷烃脱氢以取得步骤2)进料适当高的烯烃浓度,步骤2)的目标是通过含烯烃物料的催化转换以取得高芳烃及其它液体燃料的生成量和系统效率。
24.本发明将继续并扩展该两步法概念,集中于在较低温度条件下操作的步骤2),以在btx收率、催化剂寿命、整体碳利用率和催化剂长期稳定性方面进一步改进为目的,优化工艺条件和催化剂性能。另外,产物构成不限于芳烃化合物,也可以包括汽油范围的烃类。该方法可以设计成不同的操作模式,例如以芳烃化合物最大化为目标、以汽油最大化为目标和整体催化剂性能和系统效率最佳为目标。操作模式的选择可以取决于市场、需求和经济性。
25.通过将乙烯芳构化(步骤2)从乙烷脱氢(步骤1)中分离出,两个步骤都可以在它们的最佳条件下操作。
26.本发明中,步骤2)优选在较低温度条件下操作,例如350-600℃,优选400-550℃。本发明的发明人发现,较高温度有利于btx的形成,但同时ch4和碳原子数大于10的重质芳烃产物(a10 )的生成也大幅增加,导致以轻质芳烃(a6-a9)和低碳碳氢化合物(c2-c5)产物量的总和定义并计算的碳利用率降低。
27.具体的,以btx为目标产物时,步骤2)的温度优选为450-550℃。
28.以汽油等其他液体燃料为目标产物时,步骤2)的温度优选为350-450℃。
29.本发明中,液体燃料是指c5以上非芳烃碳氢化合物组分即汽油组分。
30.以整体催化剂性能和系统效率最大化为目标时,步骤2)的温度优选为400-500℃。
31.步骤2)可以在常压下进行,也可以在1-5巴压力下进行。
32.以乙烯计的液体时空速率whsv可以为0.5-10g/g-cat/hr,优选为0.75-3.0g/g-cat/hr。
33.步骤2)可以在常用的固定床反应器、流化床反应器、移动床反应器中进行。
34.步骤2)的催化剂为含有或不含有活性金属组分的沸石分子筛和用于催化剂成型
的粘结剂。
35.所述活性金属组分可以是元素周期表第iiia族、第viii族、第vib族金属元素,例如ga、fe、ni、ag和mo中的一种或多种,优选为ga、ni中的一种或多种。以催化剂的总量为基准,以元素计,活性金属组分的含量为0.4-5重量%优选为0.8-2.5重量%,例如0.4、0.5、0.8、1、1.2、1.4、2、2.1、2.2、2.3、2.4、2.5重量%。
36.本发明中,所述沸石分子筛可以是各种具有沸石结构的分子筛,优选地,所述沸石分子筛的硅铝摩尔比为5-300,进一步优选为zsm-5、zsm-11、zsm-12、zsm-23、zsm-35、y型沸石、贝塔沸石、镁碱沸石(ferrierite)和丝光沸石中的一种或多种。
37.以催化剂的总量为基准,沸石分子筛的含量优选不低于50重量%,更优选70重量%以上,例如75-85重量%。
38.所述芳构化催化剂可以是粉末也可以是成型体,优选地,所述芳构化催化剂为成型体,含有活性金属,沸石分子筛和粘结剂。所述粘结剂可以是各种能够使沸石分子筛成型为有型催化剂的物质,例如可以为二氧化硅、三氧化二铝、粘土、磷酸铝、氧化锆中的一种或多种。优选地,沸石分子筛和粘结剂的重量比为50-99:1-50,优选为70-90:10-30,进一步优选为75-85:15-25。
39.根据本发明的一种优选实施方案,以芳构化催化剂的总量为基准,所述活性金属组分的含量为0.4-4重量%,优选0.8-2.4重量%,所述沸石分子筛的含量为50-99重量%,优选70-90重量%,所述粘结剂的含量为0.6-49.6重量%,优选7.6-29.2重量%。
40.上述催化剂可以为市售品,也可以采用已知的方法制备得到。例如首先采用浸渍法,如饱和浸渍法将活性金属组分负载到沸石分子筛上,然后采用已知的挤条法,将沸石分子筛与粘结剂挤出成型得到,例如成型为条型、柱形或三叶草型。
41.根据本发明的一种优选实施方式,芳构化催化剂的合成通过湿浸渍将具有沸石分子筛粉末与粘合剂如勃姆石、水和活性金属组分的硝酸盐溶液混合以制成糊剂。将该糊状物挤出、干燥并在500-650℃下煅烧8-12小时。将煅烧后的挤条粉碎并过筛,取20-40目的颗粒用于催化反应。
42.本发明中,步骤1)脱氢反应可以是(乙烷)热脱氢、蒸汽裂化、催化脱氢和氧化脱氢(odh)中的任意一种方式。
43.由于脱氢反应独立进行,因此可以设定该脱氢反应的条件使得可以实现相当高的转化率(例如>50%),且温度可显著低于典型的乙烷裂化器的出口温度(一般>850℃),脱氢的温度例如为约750℃。由于相对较低的温度,在该区域中没有蒸汽时焦化可忽略不计,因此可以不通入蒸汽。为了促进降低烷烃的分压以促进轻烃的转化,优选向反应器中通入稀释剂,例如氮气。
44.如果在脱氢反应中没有使用蒸汽,产物流可以直接用于下一步的低聚/芳构化反应而无需冷却分离以除去水并重新加热进行反应。这将节省整个工艺的成本。由于低聚/芳构化反应也是独立进行,因此可以通过选择合适的催化剂和控制反应条件,使脱氢反应得到的产物流(一般为烷烃/烯烃/氢气混合物)选择性地转化成芳族化合物或汽油产物。由于该步骤仅需发生低聚/芳构化反应,无需发生需要高活化能的低碳烷烃脱氢反应,因此使用的催化剂可以不含有强脱氢功能的贵金属如pt,进而可以降低乙烯加氢成乙烷并进一步氢解成甲烷等主要副反应,从而甲烷的生成量将显著减少。
45.本发明中,所述脱氢反应可以在有脱氢催化剂的情况下进行,也可以在无脱氢催化剂的情况下进行。
46.所述脱氢催化剂可以是各种具有烷烃脱氢功能的催化剂,优选地,所述脱氢催化剂为负载型催化剂,该负载型催化剂含有载体和负载在该载体上的具有脱氢活性的金属组分,所述载体为不具有酸性中心的无机耐热氧化物。
47.优选地,所述具有脱氢活性的金属组分为贵金属组分如pt或pd。
48.根据本发明的一种实施方式,以所述脱氢催化剂的总量为基准,所述具有脱氢活性的金属组分的含量为0.01-2.0重量%,优选为0.02-0.2重量%。
49.优选地,所述载体为二氧化硅、氧化铝、碳化硅、粘土、氧化铈、氧化镧、氧化镁、氧化钛、氧化锆中的一种或多种。
50.上述催化剂可以为市售品,也可以通过已知的方法制备得到。
51.如上所述,由于本发明中脱氢反应独立进行,因此脱氢反应可以在有利于脱氢的条件下进行,优选地,所述脱氢反应在脱氢催化剂存在下进行时,所述脱氢反应在温度为低于900℃,优选为650-850℃,更优选650-800℃下进行。该温度低于一般的乙烷裂解反应温度(通常大于850℃)。
52.优选地,轻烃物流的ghsv为500-20000h-1
优选为800-5000h-1
。
53.根据本发明的另一种实施方式,所述脱氢反应在没有所述脱氢催化剂存在下进行。此时,脱氢反应的温度优选为700-900℃。反应物停留时间优选为0.05-30秒。本发明中,反应物停留时间是指反应物在上述700-900℃的脱氢反应温度下停留的时间,也即脱氢反应的时间。
54.为了促进降低烷烃的分压以促进轻烃的转化,优选地,向脱氢反应器中通入稀释剂。所述稀释剂例如可以是氮气等对反应不产生不利影响的惰性气体。
55.由于本发明步骤1)是为了使轻烃脱氢,目标产物为对应的烯烃,因此脱氢反应的目标以尽可能获得更多的烯烃为准,故将脱氢反应的产物称为“含烯烃的物流”。所述含烯烃的物流可以不经分离直接进行步骤2)所述的低聚/芳构化反应,由此一方面可以节省冷却分离和再次升温以达到低聚/芳构化反应所需温度的时间,缩短流程,还能大大降低由此产生的费用。因此,优选地,所述含烯烃的物流不经分离直接进行步骤2)所述低聚/芳构化反应。
56.本发明中,步骤2)所述低聚/芳构化反应是指步骤1)脱氢得到的烯烃物流发生低聚并芳构化形成芳烃的反应。需要说明的是,步骤2)低聚/芳构化反应的原料可以全部来源于步骤1),也可以根据需要在步骤1)产物的基础上进行调整得到,优选使其中乙烯含量不低于20重量%,优选20-50重量%。
57.根据本发明,所述轻烃物流中的烃可以是各种能够发生脱氢反应进行低聚/芳构化反应生成芳烃的物质,例如可以是各种碳原子数不超过5的烷烃。优选地,所述轻烃物流中乙烷的含量不低于65重量%,优选75-100重量%。
58.优选地,所述主要含烯烃的物流中乙烯含量不低于20重量%,优选20-50重量%。
59.优选地,步骤1)所述脱氢反应和步骤2)所述低聚/芳构化反应在同一个反应器的不同区中进行,或者在不同的反应器中进行。为了使反应能够连续进行,不因催化剂的失活而造成停工,优选地,用于步骤1)所述脱氢反应和步骤2)所述低聚/芳构化反应分别为并联
设置的至少两个,由此可以使得催化剂失活后将反应切入另一个反应器中,原反应器用于失活催化剂的再生。所述反应器可以是固定床反应器,也可以是流化床反应器。
60.根据本发明的一种优选实施方式,为了获得纯度更高的液体燃料如芳烃、汽油产品和使轻烃尽可能多地被转化为目标产品,优选地,如图1所示,该方法还包括将步骤2)得到的含有液体燃料的物流进行气液分离,得到含有液体燃料的液相物流,该含有液体燃料的液相物流作为产物外排或者送入后续分离工序。
61.优选地,进一步将分离得到的气相物流进行气体分离,得到氢气流、燃料气流和轻烃流。
62.进一步优选地,将轻烃流(c2-c4组分)返回步骤1)作为原料进行脱氢反应。
63.以下将通过实施例对本发明进行详细描述。以下实施例中,低聚/芳构化催化剂中使用的分子筛均为zeolyst公司的市售品。除非另有说明,活性金属组分的含量为相对于分子筛的重量百分含量。
64.在以下结果计算中,有基于乙烷进料量和乙烯进料量两种。所有“量”的定义均为碳摩尔量。
65.乙烷转化率的计算公式为:乙烷转化率,%=100%
×
(乙烷进量-反应后乙烷出量)/乙烷进量
66.乙烯转化率的计算公式为:乙烯转化率,%=100%
×
(乙烯进量-反应后乙烯出量)/乙烯进量
67.组分选择性的计算公式为:组分y的选择性=100%
×
(组分y的生成量/反应掉的乙烷或乙烯的量)
68.组分y产率的计算为:乙烷或乙烯的转化率
×
组分y的选择性(基于乙烷或乙烯)
69.为了计算乙烯转化容量和btx生产容量,在所获得的乙烯转化率和btx收率随时间变化的曲线中,通常以乙烯转化率或btx收率定义若干计算下限(略为“下限”)。例如,定义基于乙烯计算的btx收率下限为30%,在寿命实验中可以获得从反应开始至“下限”的时间,即单程催化剂寿命(略为“寿命”)并计算这一反应时间段内的平均转化率。
70.乙烯转化容量的计算为:达到所定义下限的寿命
×
在这一段反应时间内基于乙烷或乙烯计算的的平均转化率
×
乙烷或乙烯进料的液体时空速率
71.btx生成容量的计算为:达到所定义下限的寿命
×
在这一段反应时间内基于乙烷或乙烯计算的btx平均收率
×
乙烷或乙烯进料的液体时空速率
72.产物的组成采用气相色谱在线或离线测定。
73.实施例1
74.采用图1所示的工艺,将体积比为1.67:1的c2h6/n2混合气体送入串联的脱氢和低聚/芳构化两个反应器,脱氢温度设定在750℃,乙烷的ghsv为1000h-1
,压力为常压,反应在无催化剂条件下进行。在该条件下,乙烷的转化率约为57%,脱氢产物气流中乙烯的浓度约为22体积%。低聚/芳构化固定床反应器的设定温度分别为400℃、450℃、500℃和550℃,whsv=2.68g-c2h6/g-cat
·
hr(相当于1.6g-c2h4/g-cat
·
hr),压力为常压(1巴),催化剂为采用饱和浸渍法制备的ga/zsm-5/al2o3催化剂(ga的含量为2.0重量%,zsm-5的硅铝摩尔比为30,分子筛与粘结剂al2o3的重量比为82.5/17.5)。基于乙烷计算的btx收率和产物选择性结果如表1和图2所示。
75.图2中(a)所示的c2h4选择性代表了低聚/芳构化反应器中未转化的c2h4的量。数据显示随着温度的升高,未转换的乙烯量增加,表明高温条件下催化剂快速失活。在四个温度条件下,c2h4选择性增至20%的运行时间分别为:在400℃下5190分钟、在450℃下4291分钟、在500℃下2530分钟和在550℃下1159分钟。
76.从图2中(b)可以看出,btx的收率也受温度影响很大。温度越高,btx的初始产率越高,但由于焦化,降低得也更快。在这四个温度下btx产率降至下限15%时的运行时间分别为:400℃下2705分钟、450℃下3772分钟、500℃下2747分钟和550℃下1494分钟。
77.图2中(c)显示了在四个温度条件下的ch4选择性。在400℃下测量的ch4选择性约为8%。由于串联模式操作,该8%的ch4大部分来自于步骤1,增加的部分是在步骤2低聚/芳构化中新形成的。与btx的生成相对应,在高温条件下,甲烷的初始选择性较高,但随着催化剂失活也迅速降低。
78.在btx产品中,苯馏分受温度影响较大,如图2中(d)所示,温度越高,btx收率越高。关于产物中苯的价值,其取决于目标产品的定义。如果以轻质芳烃btx作为目标产物,苯具有较高的价值。但以汽油为目标产品时,苯的含量受到严格限制,以低值为好。
79.根据btx收率随时间变化的曲线(图2-b)计算的,以15%btx收率为下限的btx生产容量为400℃下22.5、450℃下40.3、500℃下34.0和550℃下18.4g-btx/g-cat,参见表1。
80.总之,高温条件可以促进更多的btx生成,其代价是催化剂寿命短,以及更多的裂解产物甲烷的生成。
81.对比例1
82.按照实施例1的方法进行乙烷的转化,不同的是,使用pt/zsm-5催化剂进行一步法乙烷芳构化。具体的,以乙烷-氮气的混合气作为进料。脱氢/低聚/芳构化温度设定在630℃,whsv=1.34g-c2h6/g-cat.hr,压力为常压,催化剂为pt负载量为0.05重量%的pt/zsm-5/al2o3(zsm-5的硅铝摩尔比为30,分子筛与粘结剂al2o3的重量比为70/30)。结果如表1和图3中的(a)所示。从图3中的(a)可以看出,尽管whsv只有实施例1的一半,但btx产率随反应时间快速下降,一个单循环运行仅能持续约400分钟,在此btx产率已下降至下限15%。
83.对比例2
84.按照对比例1的方法进行乙烷的转化,不同的是,使用pt-zn-sn/zsm-5催化剂进行一步法乙烷芳构化。具体的,以乙烷-氮气的混合气作为进料。脱氢/低聚/芳构化温度设定在630℃,whsv=1.34g-c2h6/g-cat.hr,压力为常压,催化剂为pt负载量为0.05重量%,zn负载量为0.017重量%,sn负载量为0.03重量%pt-zn-sn/zsm-5/al2o3(zsm-5的硅铝摩尔比为30,分子筛与粘结剂al2o3的重量比为70/30)。结果如表1和图3中的(b)所示。从图3中的(b)可以看出,btx产率下降较图3中的(a)缓慢,但反应也仅能运行400分钟。
85.此外,比较实施例1和对比例1,2两种类型操作的单循环btx生产容量,发现1步法(对比例1,2)的数值不高于5g-btx/g-cat;而通过两步法,在400-550℃温度范围内,单循环btx生产容量为18-40g-btx/g-cat,是一步法的数倍,参见表1。
86.对比例3
87.按照实施例1的方法进行乙烷的转化,不同的是使用的乙烯芳构化催化剂为无金属添加的zsm-5(zsm-5同实施例1,分子筛与粘结剂al2o3的重量比为82.5/17.5),反应仅在450℃一个温度条件下进行。btx收率随时间变化的结果如图4所示。根据该曲线计算的,以
15%btx收率为下限的btx生产容量为16.5g-btx/g-cat.
88.表1
[0089][0090]
实施例2
[0091]
与实施例1的方法不同,使用按照实施例1中步骤1)的产物组成简化调配的混合物气流,其组成和体积比为c2h4/h2/n2=1:1:1。催化剂与实施例1中低聚/芳构化的催化剂相同,即采用饱和浸渍法制备的ga/zsm-5/al2o3催化剂(ga的含量为2.0重量%,zsm-5的硅铝摩尔比为30,分子筛与粘结剂al2o3的重量比为82.5/17.5)。芳构化的条件为450℃和550℃、常压、whsv=0.75g-c2h4/g-cat
·
hr,反应时间为6小时。基于乙烯计算的6小时平均的btx产率和产物选择性的结果如表2所示。
[0092]
对比例4
[0093]
按照实施例2的方法进行实验,不同的是,乙烯芳构化使用的催化剂为无金属添加的zsm-5(zsm-5同实施例1)。450℃下反应6小时的平均结果如表2所示。
[0094]
实施例4
[0095]
按照实施例2的方法进行实验,不同的是,乙烯芳构化使用的催化剂为含有分子筛总重量1%镍的zsm-5(zsm-5同实施例1)。450℃下反应6小时的平均结果如表2所示。
[0096]
实施例5
[0097]
按照实施例2的方法进行实验,不同的是,乙烯芳构化使用的催化剂为含有分子筛总重量1%铁的zsm-5(zsm-5同实施例1)。450℃下反应6小时的平均结果如表2所示。
[0098]
实施例6
[0099]
按照实施例2的方法进行实验,不同的是,乙烯芳构化使用的催化剂为含有分子筛总重量1%银的zsm-5(zsm-5同实施例1)。450℃下反应6小时的平均结果如表2所示。
[0100]
表2
[0101][0102][0103]
从上表2中实施例2的数据可以看出,在550℃下,btx产率可高达63.5%;ch4和重质芳烃(a10 )的选择性分别为11.7%和9.0%。通过加和可以计算出c2-c5和a6-a9的集合选择性,按照前文中定义的碳利用率,即(c2-c5) (a6-a9),则在该反应条件下,碳利用率约为80%。
[0104]
在450℃,btx产率为55.1%,较550℃低8.4%,但ch4和a10 的选择性也较低,碳利用率为90%左右,较550℃高约10%。
[0105]
由于c2-c5中的组分以轻烃乙烷,丙烷为主,这些组分可以通过图1所示的循环路
径回到脱氢反应器进而产生更多的液体产品,因而高的碳利用率是在工艺条件优化中也需要考虑的因素。
[0106]
在液体产物中,在550℃下苯馏分明显高于450℃的值,所以如果以高苯含量为目标,则反应器需要操作在高温条件下。
[0107]
从表2和图4的比较结果可以看出,在450℃条件下,在无镓添加的催化反应中(对比例3,对比例4),btx收率低于实施例2,而在产物中,丙烷、丁烷等的选择性明显高于前者,从而揭示了镓的主要功效是通过使丙烷、丁烷进行芳构化从而提高btx产率。
[0108]
实施例7
[0109]
按照实施例2的方法进行实验,不同的是,乙烯芳构化的条件为450℃,3巴,whsv=1.5g-c2h4/g-cat
·
hr,体积比为0.67:1:1:1的c2h6/c2h4/h2/n2的气体混合物。该反应进行了3个月的多循环寿命试验。每个循环运行包括约100小时的反应和约24小时的催化剂再生。催化剂再生使用了体积比50:50的空气/氮气混合气体。
[0110]
对于每个循环,分别计算了催化剂寿命,乙烯转化容量和btx生产容量,其下限定义为(a)基于乙烯计算的30%的btx收率和(b)80%的乙烯转化率。
[0111]
在该长期稳定性试验中,完成了17个循环的试验,共转化了1990g-c2h4/g-cat(以80%乙烯转化率为下限),生成了858g的btx产物。平均于每一个循环,乙烯转化容量为117g-c2h4/g-cat,btx生产容量为50g-btx/g-cat。
[0112]
图5揭示了在第一个催化循环中,乙烯转化率、btx收率、甲烷选择性随时间的变化(a)以及btx中各组分的选择性随时间的变化(b)。在所完成的近100个小时的寿命实验中,根据定义的两个下限,即30%的btx收率(下限1)和80%的乙烯转化率(下限2),计算得到的乙烯转化容量和btx生产容量分别为127g-c2h4/g-cat(下限1)和140g-c2h4/g-cat(下限1),62g-btx/g-cat(下限2)和66g-btx/g-cat(下限2)。
[0113]
图6综合了催化剂寿命,乙烯转化容量和btx生产容量随循环次数的变化。从图6可以看出,在最初的5-6个循环中,观测到了容量数值有所下降,但之后趋于稳定。总体而言,催化剂具有较好的长期稳定性。
[0114]
上述实施例充分说明,由于两个反应步骤可以各自在优化的条件下操作,本发明提供的两步法具有明显的技术优势。具体的,步骤1)可以是工业上已经成熟的乙烷裂化工艺,步骤2)可以在较低温度范围,例如350-550℃下操作,并且可以根据目标产物来选择合适的工艺条件:(1)以btx特别是苯为目标产物,步骤2)可以在500-550℃的温度范围内进行;(2)以汽油产品为目标产物,则步骤2)的最佳温度范围为350-400℃之间;(3)以btx产率,催化剂寿命和碳利用率最高为目标,则步骤2)在约450℃下进行,可获得整体催化剂和效率的最优的表现。
[0115]
此外,低温操作还具有其它益处,从工程来看,较低的温度操作和相对较长的催化剂寿命将允许使用简单容易的固定床反应器,并且对反应器材料的要求相对低。所有这些优点都将有助于降低设备成本(反应器构造和材料)和操作成本。
[0116]
以上详细描述了本发明的优选实施方式,但是,本发明并不限于此。在本发明的技术构思范围内,可以对本发明的技术方案进行多种简单变型,包括各个技术特征以任何其它的合适方式进行组合,这些简单变型和组合同样应当视为本发明所公开的内容,均属于本发明的保护范围。
再多了解一些
本文用于企业家、创业者技术爱好者查询,结果仅供参考。