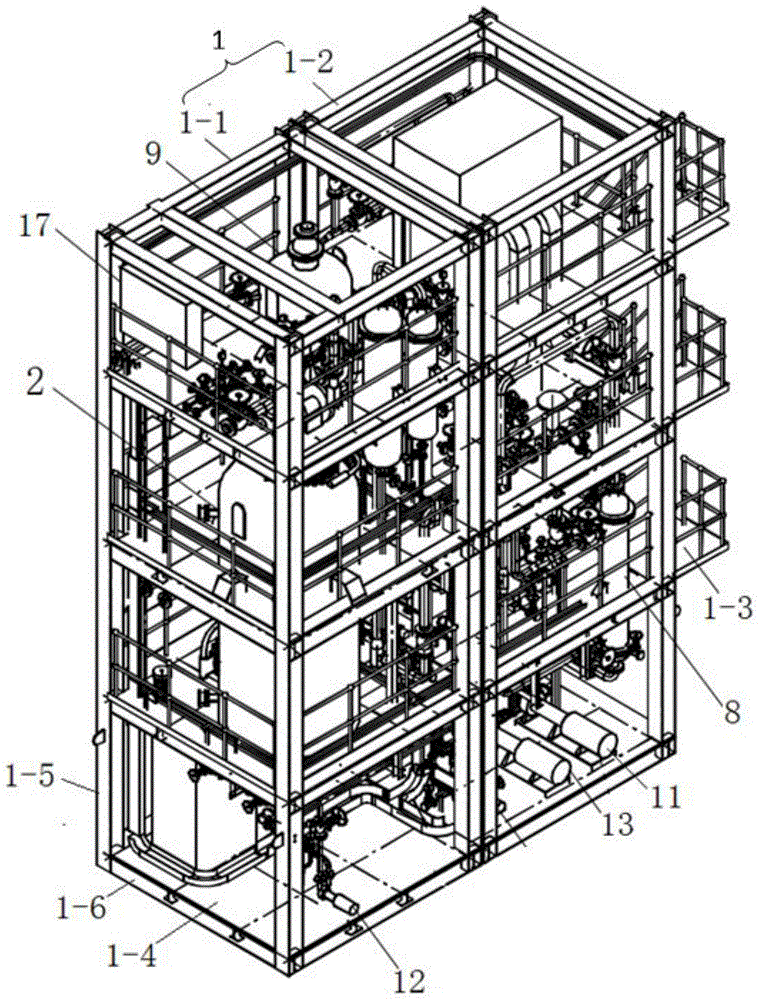
本实用新型涉及天然气脱硫技术领域,尤其涉及一种硫回收装置及浮式液化天然气处理系统。
背景技术:
近年来,随着我国深海天然气勘探的逐渐深入,越来越多的深海气田、中小型边际气田及伴生气田亟待开发。
目前,陆上气田开采的工艺和设备已经比较成熟,但是深海气田开采时,由于海上特殊环境的限制,导致海上天然气田的开采难度较大。现有技术中,可以将陆地上的气田开采设备设置船体上来进行海上气田的开发。但是,由于船体上的面积的限制,因此,陆地上的气田开采设备设置在船体的难度较大,尤其是气田开采设备中的天然气的硫回收装置,设备复杂、占地面积较大,导致将硫回收装置设于船体上的难度较大。
技术实现要素:
本实用新型的目的在于提供一种硫回收装置及浮式液化天然气处理系统,能够减小硫回收装置的占地面积。
为了实现上述目的,本实用新型提供了一种硫回收装置。该硫回收装置包括橇体、氧化反应器、再生槽和固液分离器。其中,所述橇体为多层结构。所述再生槽与所述氧化反应器连通、所述固液分离器与所述氧化反应器和所述再生槽均连通。所述氧化反应器、所述再生槽和所述固液分离器分设于所述橇体的多层结构上。
与现有技术相比,本实用新型提供的硫回收装置中,再生槽与氧化反应器连通,再生槽内的贫液能够进入氧化反应器内,与进入氧化反应器内的含h2s的酸气进行接触,使得贫液能够将含h2s的酸气中的h2s还原为硫单质,从而可以脱除含h2s的酸气中的h2s。同时,贫液氧化为富液,与硫单质混合成硫浆。
固液分离器与氧化反应器和再生槽均连通,使得氧化反应器内的硫浆能够进入至固液分离器中进行固液分离,即可分离出硫磺和富液。将硫磺进行回收,并将富液通入至再生槽内进行再生,使得富液再生为贫液后,再通入至氧化反应器中进行循环使用。由此可知,上述氧化反应器、再生槽和固液分离器相互配合,能够对含硫化氢的酸气进行脱硫处理并进行硫回收。
同时,橇体为多层结构,氧化反应器、再生槽和固液分离器分设于所述橇体的多层结构上,从而能够减小氧化反应器、再生槽和固液分离器的占用面积,进而可以减小硫回收装置的占用面积,从而可以更方便地将硫回收装置设于船体上。
本实用新型还提供了一种浮式液化天然气处理系统。该浮式液化天然气生产储卸装置包括船体和上述硫回收装置,硫回收装置的橇体的底端连接于船体上。
与现有技术相比,本实用新型提供的硫回收装置的占地面积较小,因此,将上述硫回收装置设于船体上时,能够减小硫回收装置的占用面积,使得硫回收装置能够方便地设于船体上。
附图说明
此处所说明的附图用来提供对本实用新型的进一步理解,构成本实用新型的一部分,本实用新型的示意性实施例及其说明用于解释本实用新型,并不构成对本实用新型的不当限定。在附图中:
图1为本实用新型提供的硫回收装置的结构示意图之一;
图2为本实用新型提供的硫回收装置的结构示意图之二;
图3为本实用新型提供的硫回收装置的结构示意图之三;
图4为本实用新型提供的橇体的局部示意图;
图5为本实用新型提供的硫回收装置中氧化反应器的结构示意图;
图6为本实用新型提供的硫回收装置的结构示意图之四;
图7为本实用新型提供的硫回收装置的结构示意图之五;
图8为本实用新型提供的硫回收装置的结构示意图之六;
图9为本实用新型提供的硫回收装置的结构示意图之七;
图10为本实用新型提供的硫回收装置的结构示意图之八;
图11为本实用新型提供的硫回收装置的结构示意图之九;
图12为本实用新型提供的浮式液化天然气处理系统的结构示意图。
具体实施方式
下面将结合本实用新型实施例中的附图,对本实用新型实施例中的技术方案进行清楚、完整地描述,显然,所描述的实施例仅仅是本实用新型一部分实施例,而不是全部的实施例。基于本实用新型中的实施例,本领域普通技术人员在没有作出创造性劳动前提下所获得的所有其他实施例,都属于本实用新型保护的范围。
下面将结合本实用新型实施例中的附图,对本实用新型实施例中的技术方案进行清楚、完整地描述,显然,所描述的实施例仅仅是本实用新型一部分实施例,而不是全部的实施例。基于本实用新型中的实施例,本领域普通技术人员在没有做出创造性劳动前提下所获得的所有其他实施例,都属于本实用新型保护的范围。
在本实用新型的描述中,需要理解的是,术语“中心”、“上”、“下”、“前”、“后”、“左”、“右”、“竖直”、“水平”、“顶”、“底”、“内”、“外”等指示的方位或位置关系为基于附图所示的方位或位置关系,仅是为了便于描述本实用新型和简化描述,而不是指示或暗示所指的装置或元件必须具有特定的方位、以特定的方位构造和操作,因此不能理解为对本实用新型的限制。
在本实用新型的描述中,需要说明的是,除非另有明确的规定和限定,术语“安装”、“相连”、“连接”应做广义理解,例如,可以是固定连接,也可以是可拆卸连接,或一体地连接;对于本领域的普通技术人员而言,可以具体情况理解上述术语在本实用新型中的具体含义。
在本实用新型的描述中,除非另有说明,“多个”的含义是两个或两个以上。
天然气(liquefiednaturalgas,缩写为lng)作为一种清洁、高效、方便、安全的能源,以其热值高、污染少和储运方便等特点成为了现代社会人们可选择的优质能源之一。
将气田开采到的原料气进行液化,即可得到液化天然气。而由于从气田开采到的原料中含有酸性气体(如co2、so2和h2s),因此,为了防止原料气中的酸性气体在液化过程中冻结堵塞后续管道,一般需要先将原料气进行净化,去除原料气中的酸性气体之后,再进行液化处理。
现有技术中,可以采用化学吸收法来去除原料气中的酸性气体。化学吸收法去除原料气中的酸性气体时,以碱性溶液(如烷基醇胺溶液)为吸收溶剂,在低温高压的条件下,吸收原料气中的酸性气体,即可去除原料气中的酸性气体。然后,将吸收了酸性气体的碱性溶液在高温低压的条件下进行再生,吸收了酸性气体的碱性溶液分解释放出酸性气体后,再循环至高温低压环境中对原料气进行净化。而吸收了酸性气体的碱性溶液释放的酸性气体中包含h2s气体,因此,需要对释放的酸性气体进行硫回收,从而减小对空气的污染。
目前,陆上天然气净化、硫回收和液化的工艺和设备已经非常成熟。而随着我国深海天然气勘探的逐渐深入,越来越多的深海气田、中小型边际气田及伴生气田亟待开发。传统的海上天然气田采用生产平台和海底管道结合的方式进行开采。但是,传统的开发方式具有一定的局限性。如果气田距海岸太远或规模较小,使用传统的开发方式经济效益会降低,甚至无法收回投资。同时,海底管道的铺设较为困难,导致传统的开发方式也难以实现。
为了方便海上气田的开发,浮式液化天然器设施(floatingliquefiednaturalgas,缩写为flng)越来越多地被应用到海上天然气的开发。flng需要将陆上的天然气液化工厂安装在船的甲板上,但是由于船的甲板上的面积限制,因此,船体的甲板上的面积利用是flng的关键难点,尤其是天然气的硫回收装置的设备复杂、占地面积较大,导致硫回收装置难以集成到船体的甲板上。
为了减小硫回收装置的占地面积,使得硫回收装置能够更好地集成于浮式液化天然器设施上,本实用新型提供了一种硫回收装置。参见图1和图2,上述硫回收装置包括橇体1、氧化反应器2、再生槽3和固液分离器4。
参见图3,再生槽3与氧化反应器2连通。固液分离器4与氧化反应器2和再生槽3均连通,氧化反应器2、再生槽3和固液分离器4主要用于将含h2s的酸气中的h2s还原为硫磺,并进行回收,使得本实用新型提供的硫回收装置能够对含h2s的酸气进行硫回收。
参见图1和图2,上述橇体1为多层结构,上述氧化反应器2、再生槽3和固液分离器4分设于橇体1的多层结构上,使得氧化反应器2、再生槽3和固液分离器4的占用的面积减小,从而可以减小硫回收装置的占地面积,使得硫回收装置能够更方便地设于船体上。
需要说明的是,上述橇体1为多层结构指的是橇体1沿高度方向具有多层容纳空间,多层容纳空间用于支撑硫回收装置的氧化反应器2、再生槽3和固液分离器4。
上述橇体1的容纳空间的层数可以根据实际情况进行选择,橇体1的层数可以为两层、三层或者四层,橇体1内氧化反应器2、再生槽3和固液分离器4的布置方式也不做限定。
例如:当上述橇体1的层数为两层时,可以将上述氧化反应器2设于橇体1的底层,并使氧化反应器2穿过橇体1的第二层。使固液分离器4设于橇体1的第一层,再生槽3设于橇体1的第二层,且固液分离器4设于再生槽3的正下方。此时,橇体1在占用面积的较小,同时橇体1的高度较低,从而可以方便橇体的安装和维修。(上述橇体1的层数自下至上逐依次增大,橇体1的底层为第一层)。
当上述橇体1的层数为三层时,可以将上述固液分离器4、氧化反应器2和再生槽3分设于橇体1的不同层上,具体固液分离器4、氧化反应器2和再生槽3设于橇体1的哪一层不做限定。
例如:上述固液分离器4设于橇体1的第一层上,氧化反应器2设于橇体1的第二层上,再生槽3设于橇体1的第三层上。此时,硫回收装置占用的面积最小。
参见图1和图2,当上述橇体1的层数为四层时,使氧化反应器2贯穿橇体1的第一层、第二层和第三层,并使固液分离器4设于橇体1的第二层,再生槽3设于橇体1的第三层,再生槽3设于固液分离器4的正上方,橇体其余的层用于放置其他设备。
示例性的,当上述橇体1的层数为四层时,参见图1和图2,为了使橇体1能够在内陆运输,上述橇体1包括并排设置的氧化橇体1-1和再生橇体1-2,氧化橇体1-1和再生橇体1-2均为四层结构。氧化反应器2设于氧化橇体1-1内。再生槽3和固液分离器4设于再生橇体1-2内。
此时,氧化橇体1-1和再生橇体1-2均能够设于货车的车体或船舶上,从而使得氧化橇体1-1和再生橇体1-2能够满足内陆公路运输的要求的同时,还能满足海上船舶运输。
需要说明的是,上述氧化反应器2在氧化橇体1~1上的安装方式可以根据实际情况进行选择。
例如:可以在氧化反应器2的底部设置支腿,并将支腿设于氧化橇体1-1上,从而可以将氧化反应器2设于氧化橇体1-1上。
还可以在氧化反应器2上设有支耳,氧化反应器2通过支耳挂接于氧化橇体1-1上,从而能够方便氧化反应器2的安装和拆卸。
同时,当氧化反应器2通过支耳挂接于氧化橇体1-1上时,为了保证氧化反应器2与橇体1连接的稳定性,上述氧化反应器2沿轴向均匀分布有多个支耳,多个支耳均挂接于氧化橇体1-1上。
并且,为了进一步保证氧化反应器2工作时的稳定性,上述氧化反应器2的支耳设于氧化反应器2的上部,且氧化反应器2的支耳挂接于氧化橇体1-1的第三层上。
当上述橇体1安装在船上时,氧化橇体1-1和再生橇体1-2之间的距离可以根据实际情况进行选择。
例如:参见图1,上述氧化橇体1-1和再生橇体1-2之间的距离至少为50mm,能够防止氧化橇体1-1和再生橇体1-2晃动时出现相互碰撞的现象,使得氧化橇体1-1和再生橇体1-2在晃动条件下,稳定性和安全性较高,从而可以提高硫回收装置在工作时的稳定性和安全性。
需要说明的是,为了方便操作人员进入至橇体1的每一层对设备进行检修,上述橇体1的侧面设置有楼梯1-3,使得操作人员能够通过楼梯1-3进入至橇体1的每一层内,从而方便操作人员对硫回收装置的不同设备进行检修,同时也方便操作人员的安全疏散。
当然,也可以在橇体1上设置爬梯或者升降装置来方便操作人员进入至橇体1的每一层内。
上述楼梯1-3可以根据实际情况进行安装,如上述楼梯1-3可以安装在氧化橇体1-1的侧面,也可以安装在再生橇体1-2的侧面。
同样,上述楼梯1-3的安装方式也可以根据实际情况进行选择。例如:楼梯可以固定于橇体1的侧面上。上述楼梯1-3也可以可拆卸地连接于橇体1的侧面,从而可以使得上述硫回收装置进行运输的过程中,可以分为氧化橇体1-1、再生橇体1-2和楼梯1-3三部分进行运输,进而使得硫回收装置能够同时适用于海上运输和陆地上运输。
上述氧化橇体1-1和再生橇体1-2在陆地上运输的过程中,将氧化橇体1-1和再生橇体1-2卧倒放置于货车的车箱即可。
上述橇体1在使用时,可以先将氧化反应器2、再生槽3和固液分离器4安装在橇体1上之后,再运输至船体上进行安装,从而可以降低硫回收装置的安装风险和安装成本。
作为一种可能的实现方式,上述橇体1的结构具体结构在此也不做限制。
例如:上述橇体1为多层封闭式结构,氧化反应器2、再生槽3和固液分离器4设于橇体1内时,橇体1能够对氧化反应器2、再生槽3和固液分离器4进行遮挡,减小空气对氧化反应器2、再生槽3和固液分离器4的腐蚀,提高橇体1的使用寿命。
参见图1,橇体1还可以为多层框架式结构。此时,多层框架式结构的橇体1在制作的过程中,所需的材料较少,从而可以降低橇体1的制作成本。同时,多层框架式结构的橇体1的质量较小,可以减小硫回收装置的质量,方便硫回收装置的移动、运输和安装。并且,多层框架式结构的橇体1内的采光较好,从而可以方便操作人员对氧化反应器2、再生槽3和固液分离器4的操作和检修。
示例性的,当上述橇体1为多层框架式结构时,参见图3,每层橇体1均包括底板1-4、多个竖支撑柱1-5和多个横梁1-6,多个竖支撑柱1-5围绕底板1-4排布,相邻两个竖支撑柱1-5之间通过横梁1-6连接,底板1-4固定于横梁1-6上,竖支撑柱1-5和横梁1-6能够充分对底板1-4提供支撑力,使得橇体1具有较高的强度,保证硫回收装置在工作过程中的安全性和稳定性。
同时,为了进一步提高橇体1的强度和稳定性,上述橇体1第一层的横梁1-6和每一层的竖支撑柱1-5上均设有加劲肋。
上述橇体1-1的形状可以根据实际情况进行选择。
例如:参见图1和图4,上述橇体1呈长方体状,且每层橇体1的底板1-4也呈长方形,每层橇体1包括有四个竖支撑柱1-5和四个横梁1-6,四个竖支撑柱1-5分别设于长方形底板1-4的四个拐角处,四个横梁1-6沿长方形底板1-4的四条边排布。
需要说明的是,当设于橇体1上的部分设备较高,需要贯穿橇体1的多层时,橇体1的相对应的底板1-4上应开设有通孔,以便比较高的设备能够贯穿橇体1的多层。
例如:参见图1和图4,上述氧化反应器2的高度较高,需要贯穿氧化橇体1-1的第一层、第二层和第三层,因此氧化橇体1-1的第二层和第三层的底板1-4上均开设有能够贯穿氧化反应器2的通孔1-7。
并且,为了保证施工人员的施工安全,参见图1,每层橇体1的四个支撑柱中,相邻的两个支撑柱之间均设有防护栏。
上述橇体1的材质在此也不做限定,可以根据实际情况进行选择。例如橇体1采用高强度钢材。
当上述橇体1位框架式结构式,橇体1的竖支撑梁和横梁1-6的型号为q345-b,橇体1的底板1-4的钢材的强度不低于q325-b。
在一些实施例中,为了进一步提高橇体1的防腐性能,上述橇体1的表面上涂覆有防腐涂层,从而可以进一步提高硫回收装置的防腐性能,进而可以进一步延长硫回收装置的使用寿命,进一步提高硫回收装置在使用时的稳定性和安全性。
需要说明的是,上述防腐涂层可以根据情况进行选择。例如,防腐涂层包括依次涂覆的氧锌黄底漆层、环氧云铁防锈漆层和脂肪族聚氨酯面漆层,且上述氧锌黄底漆层中锌含量约为80%,使得防腐涂层具有较好的防腐性能的同时,还能够降低防腐涂层对环境的危害。
在一些可能的实现方式中,为了方便橇体1运输、移动、调整和安装,上述橇体1的顶部和侧面均设有吊耳,以便于橇体1在运输、移动、调整和安装的过程中起吊。
当上述橇体1包括氧化橇体1-1和再生橇体1-2时,上述氧化橇体1-1和再生橇体1-2的顶部和侧面均设有吊耳。
需要说明的是,氧化反应器2、再生槽3和固液分离器4的具体结构和具体连接方式不影响本实用新型的目的的实现,因此,对氧化反应器2、再生槽3和固液分离器4的具体结构不进行限定。
例如:参见图3,上述氧化反应器2具有氧化反应器的硫浆出口2-3、氧化反应器的进料口2-1和氧化反应器的尾气出口2-2,且氧化反应器的进料口2-1用于向氧化反应器2内通入含h2s的酸气。
再生槽3具有再生槽的富液进口3-1和再生槽的贫液出口3-2,且再生槽的贫液出口3-2与氧化反应器2连通,使得再生槽3内的贫液能够通过再生槽的贫液出口3-2进入氧化反应器2中。
固液分离器4具有固液分离器的硫浆进口4-1、固液分离器的硫磺出口4-2和固液分离器的富液出口4-3,且固液分离器的硫磺出口4-2用于将固液分离器4分离出的硫磺排出固液分离器4之外。其中,固液分离器的硫浆进口4-1与氧化反应器的硫浆出口2-3连通,使得氧化反应器2内的硫浆能够依次通过氧化反应器的硫浆出口2-3和固液分离器的硫浆进口4-1进入至固液分离器4内进行固液分离。固液分离器的富液出口4-3与再生槽的富液进口3-1连通,使得固液分离器4分离出的富液能够依次通过固液分离器的富液出口4-3和再生槽的富液进口3-1进入至再生槽3进行再生。
当上述硫回收装置工作时,先将再生槽3内的贫液通入至氧化反应器2内,再向氧化反应器2内通入含h2s的酸气,含h2s的酸气与贫液接触后,贫液能够将含h2s的酸气中的h2s还原成硫磺沉积在氧化反应器2的底部,然后脱除了h2s的尾气从氧化反应器的尾气出口2-2排出氧化反应器2外。同时,贫液被氧化成富液,富液与硫磺混合形成硫浆。
硫浆依次通过氧化反应器的硫浆出口2-3和固液分离器的硫浆进口4-1进入至固液分离器4内进行固液分离,得到硫磺和富液。将分离出富液依次通过固液分离器的富液出口4-3和再生槽的富液进口3-1通入至再生槽3内进行再生,使得富液再生为贫液后,再通入至氧化反应器2中进行循环使用。将分离出的硫磺从固液分离器的硫磺出口4-2排出后进行回收,即可对含h2s的酸气进行硫回收。
贫液和富液可以根据实际情况进行选择,例如:上述贫液为fe3 的络合物溶液,富液为fe2 的络合物溶液。当上述贫液与含h2s的酸气在氧化反应器2中接触时,fe3 的络合物溶液将含h2s的酸气中的h2s氧化为单质硫,同时fe3 的络合物溶液被还原为fe2 的络合物溶液,其反应式为:
h2s 2fe3 ln→2fe2 ln 1/8s8 2h ;
然后,fe2 的络合物溶液能够在再生槽3内利用空气氧化为fe3 的络合物溶液循环使用,其反应式为:
2fe2 ln 1/2o2 1/2h2o→2fe3 ln 2oh-。
可以理解的是,上述固液分离器4的种类可以根据实际情况进行选择。例如;上述固液分离器4可以为电动筛。
上述固液分离器4也可以为离心机,离心机具有较高的固液分离效率,从而能够进一步提高硫回收装置的硫回收效率。
上述再生槽3的种类也可以根据实际情况进行选择,只要再生槽3能够将富液再生为贫液即可。例如:上述再生槽3为电化学再生槽,电化学再生槽具有较高的再生效率,使得富液转化为贫液的效率较高,从而可以更进一步地提高硫回收装置的硫回收效率。
要说明的是,当上述再生槽3为电化学再生槽3时,上述再生槽3上还应具有空气进口。
需要说明的是,参见图3,上述氧化反应器的尾气出口2-2和氧化反应器的硫浆出口2-3的位置可以根据实际情况进行开设。
例如:参见图3,上述氧化反应器的尾气出口2-2设于氧化反应器2的顶端,从而可以方便氧化反应器2中的脱除h2s的尾气从氧化反应器的尾气出口2-2排出氧化反应器2之外。
参见图3,上述氧化反应器的硫浆出口2-3设于氧化反应器2的底端,使得氧化反应器2底部沉积的硫浆能够更充分地从氧化反应器2的硫浆出口排出氧化反应器2之外。
同时,参见图3,为了方便硫磺在氧化反应器2底部沉积和出料,上述氧化反应器2的底部呈锥形。
而上述氧化反应器2与再生槽的贫液出口3-2连通的位置可以根据实际情况进行选择。
例如:参见图5,可以在氧化反应器2的上部设置氧化反应器的进液口2-4,并使氧化反应器的进液口2-4与再生槽的贫液出口3-2连通。
在此情况下,氧化反应器的进料口2-1应设于氧化反应器2的底部。氧化反应器2在工作时,再生槽3内的贫液从氧化反应器的进液口2-4进入至氧化反应器2后,在重力的作用下向氧化反应器2的下部滴落。同时含h2s的酸气从氧化反应器的进料口2-1进入至氧化反应器2后,向氧化反应器2的上部移动。含h2s的酸气与贫液逆流接触,使含h2s的酸气与贫液更加充分地接触,从而能够使含h2s的酸气中的h2s能够被贫液充分还原成硫磺进行回收,从而提高硫回收装置的硫回收效率。
参见图6,上述再生槽3也可以通过氧化反应器的进料口2-1与氧化反应器2连通。上述氧化反应器的进料口2-1可以沿高度方向设于氧化反应器的硫浆出口2-3和氧化反应器的尾气出口2-2之间。
在此情况下,含h2s的酸气和贫液均通过进料口2-1进入至氧化反应器2内,因此,氧化反应器的进料口2-1处应设有三通结构。同时,氧化反应器2上还应设有溢流出口2-5,溢流出口2-5沿高度方向设于氧化反应器的进料口2-1和氧化反应器的尾气出口2-2之间,且溢流出口2-5与再生槽3的贫液出口3-2连通。
氧化反应器2在工作时,再生槽3内的贫液进入至氧化反应器2内,在氧化反应器2内的贫液能够从溢流出口2-5溢流出氧化反应器2之外时,持续向氧化反应器2内通入贫液。然后从氧化反应器的进料口2-1向氧化反应器2内通入含h2s的酸气。含h2s的酸气能够直接通入至贫液的液面之下,使得含h2s的酸气能够与贫液充分接触,贫液能够充分将含h2s的酸气中的h2s还原为硫磺,实现含h2s的酸气的硫回收。同时,脱除了h2s的尾气向上逐渐移动至贫液液面的上方,最后从氧化反应器的尾气出口2-2排出氧化反应器2之外。
作为一种实施例,参见图1和图2,为了方便对固液分离器4分离出来的硫磺进行收集,上述硫回收装置还包括硫磺回收桶5,且硫磺回收桶5设于再生橇体1-2的第一层。此时,固液分离器4分离出的硫磺能够在重力的作用下进入至硫磺回收桶5中,方便了硫磺的收集。同时,硫磺回收桶5设于再生橇体1-2的第一层,能够方便操作人员定期将硫磺回收桶5收集的硫磺运送至陆地。
同时,参见图1和图2,为了避免固液分离器4分离出的富液流向再生槽3时,对再生槽3产生较大的冲击,上述硫回收装置还包括富液缓冲罐20。富液缓冲罐20的进液口与固液分离器4的富液出口4-3连通,富液缓冲罐20的出液口与再生槽3的富液进口3-1连通。
此时,从固液分离器4分离出的富液能够进入至富液缓冲罐20中进行缓冲后再流入至再生槽3内,从而可以降低固液分离器4分离出的富液对再生槽3的冲击,保证再生槽3工作的稳定性。
具体的,参见图1和图2,富液缓冲罐20设于再生橇体1-2的第一层。此时,无需设置额外的液泵,固液分离器4分离出的富液能够重力的作用下进入至富液缓冲罐20中。
作为一种实施例,参见图1、图2和图7,上述硫回收装置还包括尾气洗涤器6,尾气洗涤器6具有尾气洗涤器的硫浆出口6-1、尾气洗涤器的尾气进口6-2、尾气洗涤器的贫液进口6-3和尾气洗涤器的尾气出口6-4。其中,尾气洗涤器的尾气进口6-2与氧化反应器的尾气出口2-2连通,使得氧化反应器2内脱除了h2s的尾气能够进入至尾气洗涤器6中。尾气洗涤器的贫液进口6-3与再生槽的贫液出口3-2连通,使得再生槽3内的贫液能够进入至尾气洗涤器6中。
此时,进入至尾气洗涤器6中的脱除了h2s的尾气和贫液充分接触,贫液能够对脱除了h2s的尾气中残留的h2s气体进行再次硫回收,能够提高含h2s的酸气的硫回收效率,并且进一步减小脱除了h2s的尾气中h2s气体的含量,减小了脱除了h2s的尾气对空气的污染。
同时,参见图1和图2,尾气洗涤器6设于氧化橇体1-1上,且尾气洗涤器6设于氧化反应器2的上层,即尾气洗涤器6设于氧化橇体1-1的第四层。此时,尾气洗涤器6内脱除了h2s的尾气能够在自身浮力的作用下进入至尾气洗涤器6中,无需任何气泵的辅助,从而可以简化硫回收装置,进一步减小硫回收装置的占用空间。
具体的,参见图7,为了防止为氧化反应器的尾气出口2-2与尾气洗涤器的尾气进口6-2之间出现管道积气的现象,用于连通氧化反应器的尾气出口2-2与尾气洗涤器的尾气进口6-2的管道为直线型管道,且连通氧化反应器的尾气出口2-2与尾气洗涤器的尾气进口6-2的管道倾斜设于氧化反应器的尾气出口2-2与尾气洗涤器的尾气进口6-2之间。
具体的,参见图7,上述尾气洗涤器的尾气进口6-2设于尾气洗涤器的贫液进口6-3下方。此时,进入至尾气洗涤器6中的贫液和脱除了h2s的尾气能够逆流接触,使得贫液和脱除了h2s的尾气接触的更加充分,从而可以提高尾气洗涤器6对脱除了h2s的尾气进行硫回收的效率。
需要说明的是,上述尾气洗涤器的尾气出口6-3和尾气洗涤器的硫浆出口6-1的位置可以根据实际情况进行选择。
例如:尾气洗涤器的尾气出口6-3设于尾气洗涤器6的顶端,能够方便尾气洗涤器6中尾气的排放。
尾气洗涤器的硫浆出口6-1设于尾气洗涤器6的底端,使得尾气洗涤器6内的硫浆能够充分流出尾气洗涤器6外进行分离回收。
尾气洗涤的硫浆出口6-1流出的硫浆的固液分离的方式有多种。
例如:可以在尾气洗涤器6的下部设置固液分离器4,来将尾气洗涤器6的硫浆出口排出的硫浆进行固液分离,从而可以将尾气洗涤器6排出的硫浆中进行硫回收。
当然,本实用新型中,参见图7,上述氧化反应器2具有氧化反应器的硫浆进口2-6,上述尾气洗涤器的硫浆出口6-1与氧化反应器的硫浆进口2-6连通,使得尾气洗涤器6中的硫浆能够在重力的作用下依次通过尾气洗涤器的硫浆出口6-1和氧化反应器的硫浆进口2-6进入至氧化反应器2中。尾气洗涤器6中的硫浆进入至氧化反应器2中后,能够沉积在氧化反应器2的底部,与氧化反应器2内的硫浆一起通过氧化反应器的硫浆出口2-3进入至固液分离器4中进行固液分离。此时,使用一个固液分离器4即可完成尾气洗涤器6中硫浆的硫回收和氧化反应器2内硫浆的硫回收,从而可以进一步简化硫回收装置。
具体的,参见图7,为了防止氧化反应器的硫浆进口2-6与尾气洗涤器的硫浆出口6-1之间出现管道积液的现象,用于连通氧化反应器的硫浆进口2-6与尾气洗涤器的硫浆出口6-1的管道为直线型管道,且用于连通氧化反应器的硫浆进口2-6与尾气洗涤器的硫浆出口6-1的管道倾斜设于氧化反应器的硫浆进口2-6与尾气洗涤器的硫浆出口6-1。
作为一种实施例,参见图1和图2,上述尾气洗涤器6的尾气出口处设有尾气风机7,使得尾气洗涤器6中的脱除了h2s的尾气与贫液接触后,能够在尾气风机7的作用下通过尾气洗涤器6的尾气出口流出尾气洗涤器之外,从而能够提高尾气洗涤器6对脱除了h2s的尾气的硫回收效率。
作为一种可能的实现方式,参见图1、图2和图8,上述硫回收装置还包括脱硫液冷却器8,脱硫液冷却器的进液口8-1与再生槽的贫液出口3-2连通,脱硫液冷却器的出液口8-2与尾气洗涤器的贫液进口6-3和氧化反应器均连通,且脱硫液冷却器8内通有冷却介质,使得再生槽3流出的贫液能够经过脱硫液冷却器8冷却后再进入至氧化反应器2和尾气洗涤器6中。
此时,由于富液在再生槽3内再生为贫液的过程中,会发生氧化还原反应释放出大量的热量,导致从再生槽的贫液出口3-2流出的贫液的温度较高。脱硫液冷却器8能够对贫液进行降温,使得贫液的温度降低后再进入至进氧化反应器2和尾气洗涤器6中,能够防止进入至氧化反应器2和尾气洗涤器6中的贫液温度较高导致贫液与h2s发生反应时出现爆炸现象,进而提高本申请的硫回收装置进行硫回收时的安全性能。
同时,参见图1和图2,上述脱硫液冷却器8设于再生橇体1-2上,且脱硫液冷却器8与固液分离器4设于再生橇体1-2的同一层。例如:上述再生橇体1-2具有四层,固液分离器4设于再生橇体1-2的第二层,脱硫液冷却器8设于再生橇体1-2的第二层,再生槽3设于再生橇体1-2的第三层。此时,无需在再生槽3和脱硫液冷却器之间设置液泵,再生槽3内的贫液能够在重力的作用下进入至脱硫液冷却器8中,从而可以进一步简化硫回收装置,进而可以进一步减小硫回收装置的占地面积。
具体的,参见图1和图2,上述氧化反应器2的上部的高度与集液槽3的高度相对应,上述氧化反应器2的下部的高度与脱硫液冷却器8的高度相对应。
作为一种实施例,参见图1、图2和图9,上述硫回收装置还包括气液分离器9,气液分离器9具有气液分离器的进液口9-1、气液分离器的出液口9-2和气液分离器的出气口9-3。其中,气液分离器的出气口9-3用于将气液分离器9分离出的空气排出气液分离器9之外。上述气液分离器的进液口9-1与脱硫液冷却器的出液口8-2连通,气液分离器的出液口9-2与尾气洗涤器的贫液进口6-3和氧化反应器2均连通,使得经脱硫液冷却器8冷却后的贫液能够在气液分离器9中进行气液分离后,再进入至氧化反应器2和尾气洗涤器6中。此时,气液分离器9可以脱除冷却后的贫液中的空气,使得贫液能够更充分地与氧化反应器2内的含h2s的酸气或尾气洗涤器6内的脱除了h2s后的尾气中的h2s进行氧化还原反应,从而进一步提高硫回收装置的硫回收效率。
同时,参见图1和图2,气液分离器9设于氧化橇体1-1上,且气液分离器9设于氧化反应器2的上层。例如:氧化反应器2贯穿氧化橇体1-1的第一层、第二层和第三层,气液分离器9设于氧化橇体1-1的第四层。此时,气液分离器9设于氧化反应器2的上部,使得气液分离器9内的贫液能够在重力的作用下,通过氧化反应器的进料口2-1流入至氧化反应器2内,无需任何液泵的辅助。同时,气液分离器9与尾气洗涤器6均设于氧化反应器2的上层,气液分离器9与尾气洗涤器6之间的距离较小,进而使得气液分离器9内的贫液能够更方便地流入至尾气洗涤器6中。
作为一种实施例,参见图1和图10,上述硫回收装置还包括酸气分离器10,酸气分离器10用于从分离出含h2s的酸气中的液体。
需要说明的是,酸气分离器10的具体结构和具体连接方式不影响本实用新型的目的的实现,因此,对酸气分离器10的具体结构不进行限定。
例如:参见图1、图2和图10,上述硫回收装置还包括酸气分离器10,酸气分离器的进气口10-1用于向酸气分离器10中通入含h2s的酸气,酸气分离器的出气口10-2与氧化反应器的进料口2-1连通,使得含h2s的酸气能够在酸气分离器10中进行酸气分离,分离出含h2s的酸气中液体后,再进入至氧化反应器2内。此时,进入至氧化反应器2内的含h2s的酸气的杂质较少,从而可以提高含h2s的酸气与贫液进行氧化还原反应时的反应效率,进而可以提高硫回收装置的硫回收效率。
同时,参见图1,酸气分离器10设于氧化橇体1-1上,且酸气分离器10设于氧化反应器2的上层。例如:氧化反应器2贯穿氧化橇体1-1的第一层、第二层和第三层,酸气分离器10设于氧化橇体1-1的第四层。
在一些实施例中,参见图1和图2,上述尾气洗涤器6、气液分离器9和酸气分离器10均设于氧化橇体1-1的同一层。即:氧化反应器2贯穿第一层、第二层和第三层,尾气洗涤器6、气液分离器9和酸气分离器10均设于氧化橇体1-1的第四层。此时,氧化橇体1-1上的尾气洗涤器6、气液分离器9和酸气分离器10布局紧凑,占用空间较小,能够降低氧化橇体1-1的高度,进一步方便氧化橇体1-1的运输和硫回收装置的安装、使用。
作为一种实施例,参见图1和图2,再生槽3与氧化反应器2之间设有贫液泵11,使得再生槽3内的贫液能够在贫液泵11的作用下流入至氧化反应器2内。氧化反应器2与固液分离器4设有硫浆输送泵12,使得氧化反应器2内的硫浆能够在硫浆输送泵12的作用下输送至固液分离器4内进行分离。固液分离器4与再生槽3之间设有富液泵13,使得固液分离器4分离出的富液能够在富液泵13的作用下进入至再生槽3内。
并且,硫浆输送泵12设于氧化橇体1-1的第一层,从而方便操作人员对硫浆输送泵12的操作和检修。富液泵13、贫液泵11均设于再生橇体1-2的第一层,从而可以方便操作人员对富液泵13、贫液泵11和固液分离器4进行操作和检修。
作为一种实施例,参见图1和图2,上述硫回收装置还包括仪表控制柜14、电气柜15、电气整流柜16和硫化氢在线分析柜17。其中,仪表控制柜14用于控制硫回收装置中各个设备的运行。电气柜15用于向路回收装置配送运行所需的电能。电气整流柜16用于根据硫回收装置中不同设备的运行特点,对供给不同设备的电流进行调节。硫化氢在线分析柜17能够自动监控氧化反应器2的尾气出口处硫化氢浓度,并将硫化氢浓度反馈给操作人员。
上述仪表控制柜14和电气柜15设于氧化橇体1-1的底层,能够方便操作人员检修操作。
上述仪表控制柜14、电气柜15、电气整流柜16和硫化氢在线分析柜17在橇体1上的位置可以根据实际情况进行选择,在此不做限定。
例如:上述电气整流柜16设置于所述再生槽3的上层。例如:上述再生撬体1-2为四层结构,上述再生槽3设于再生橇体1-2的第三层,电器整流柜设于再生槽3的第四层。此时,氧化橇体1-1和再生橇体1-2层数相同,方便氧化橇体1-1和再生橇体1-2的批量生产。
需要说明的是,当上述再生槽3为电化学再生槽时,电化学再生槽与电气整流柜16之间有母线槽作为连接。
硫化氢在线分析柜17设置于氧化反应器2的上层。例如:氧化橇体1-1为四层结构,上述氧化反应器2贯穿氧化橇体1-1的第一层、第二层和第三层,硫化氢在线分析柜17设于氧化橇体1-1的第四层,使得硫化氢在线分析柜17与氧化反应器2的尾气出口之间的距离较小,方便硫化氢在线分析柜17对氧化反应器2的尾气出口的硫化氢的浓度进行监控。
在一些实施例中,当上述硫回收装置包括尾气洗涤器6时,上述硫化氢在线分析柜17与尾气洗涤器6设于氧化橇体1-1的同一层,且硫化氢在线分析柜17主要用于监控尾气洗涤器6的尾气出口处的硫化氢浓度。此时,硫化氢在线分析柜17与尾气洗涤器6设于氧化橇体1-1的同一层,从而可以方便硫化氢在线分析柜17对尾气洗涤器6的尾气出口处的硫化氢的浓度的监控。
作为一种实施例,参见图1和图2,每层氧化橇体1-1上均设有接线箱18。
具体的,参见图1和图2,上述硫回收装置中,从接线箱引出导线均贴附于橇体1上,沿橇体1的走向排布。而硫回收装置与外界的工艺管线均通过橇体1上的配对法兰连接。
作为一种实施例,参见图1、图2和图11上述硫回收装置还包括管道混合器19,管道混合器19用于使贫液和含h2s的酸气充分混合后,在通过氧化反应器的进料口2-1进入至氧化反应器内。
需要说明的是,管道混合器19的具体结构和具体连接方式不影响本实用新型的目的的实现,因此,对管道混合器19的具体结构不进行限定。
例如:管道混合器19具有管道混合器的进液口19-1、管道混合器的进气口19-2和管道混合器的出料口19-3。其中,管道混合器的进气口19-2用于向管道混合器19内输送含h2s的酸气。管道混合器的进液口19-1与再生槽的贫液出口3-2连通,使得再生槽3内的贫液能够进入至管道混合器19中。管道混合器的出料口19-3与氧化反应器的进料口2-1连通,使得含h2s的酸气与贫液在管道混合器19中进行混合均匀后,再通过管道混合器19的出料口进入至氧化反应器2内。
此时,由于进含h2s的酸气与贫液在管道混合器19中已混合均匀,因此,进入至氧化反应器2内的含h2s的酸气与贫液在较小的空间内即可充分反应,从而可以减小氧化反应器2的体积,进一步减小硫回收装置的占用面积。
在一些实施例中,上述氧化反应器2、再生槽3和固液分离器4的材质也不做限定,可根据情况选择。例如:氧化反应器2、再生槽3和固液分离器4均为316l型不锈钢材质。
需要说明的是,当上述硫回收装置包括尾气洗涤器6、脱硫液冷却器8、气液分离器9、酸气分离器10、贫液泵11、硫浆输送泵12、富液泵13、仪表控制柜14、电气柜15、电气整流柜16、硫化氢在线分析柜17、管道混合器19或楼梯1-3时,上述尾气洗涤器6、脱硫液冷却器8、气液分离器9、酸气分离器10、贫液泵11、硫浆输送泵12、富液泵13、仪表控制柜14、电气柜15、电气整流柜16、硫化氢在线分析柜17、管道混合器19或楼梯1-3也应为不锈钢材质。
作为一种实现方式,上述硫回收装置中各个设备之间连接的管道也为不锈钢材质。
具体的,上述硫回收装置中各个设备之间连接的管道贴附于橇体1设置。
作为一种实施例,上述硫回收装置中的氧化反应器2、再生槽3和固液分离器4表面均涂覆有防腐涂层,从而可以进一步提高硫回收装置的防腐性能,进而可以进一步延长硫回收装置的使用寿命,进一步提高硫回收装置在使用时的稳定性和安全性。
参见图1和图2,上述防腐涂层包括依次涂覆的氧锌黄底漆层、环氧云铁防锈漆层和脂肪族聚氨酯面漆层,使得防腐涂层具有较好的防腐性能的同时,还能够降低防腐涂层对环境的危害。
当上述硫回收装置包括尾气洗涤器6、脱硫液冷却器8、气液分离器9、酸气分离器10、贫液泵11、硫浆输送泵12、富液泵13、仪表控制柜14、电气柜15、电气整流柜16、硫化氢在线分析柜17、管道混合器19或楼梯1-3时,上述尾气洗涤器6、脱硫液冷却器8、气液分离器9、酸气分离器10、贫液泵11、硫浆输送泵12、富液泵13、仪表控制柜14、电气柜15、电气整流柜16、硫化氢在线分析柜17、管道混合器19或楼梯1-3的表面也应涂覆有防腐涂层。
具体的,上述硫回收装置中各个设备之间连接的管道也涂覆有防腐涂层。
本实用新型实施例还提供了一种浮式液化天然气处理系统。参见图12,该浮式液化天然气处理系统包括上述船体a和硫回收装置b,且上述硫回收装置b的橇体1连接于船体a上。
此时,由于上述硫回收装置b的占地面积较小,因此,将上述硫回收装置b设于船体a上时,能够减小硫回收装置b的占用面积,使得硫回收装置b能够更方便地设于船体上。
作为一种实施例,为了保证硫回收装置在船体上安装的稳定性,上述硫回收装置b的底端的拐角处均固定于船体a的强横肋和纵向肋的交叉位置。
具体的,橇体1的底端采用对穿螺栓固定在船体上,且对穿螺栓设于橇体1底端的钢梁的上翼缘上,从而可以增加橇体1的底部的刚性。
并且,橇体1与船体之间对穿螺栓上均涂覆有防腐涂层,该防腐涂层依次为渗锌层、克罗达层和环氧封闭层。
具体的,上述硫回收装置可以在陆地上橇装完成了之后,在运输至船上进行安装,从而可以降低在船上现场施工的风险和成本。
上述实施方式的描述中,具体特征、结构、材料或者特点可以在任何的一个或多个实施例或示例中以合适的方式结合。
以上所述,仅为本实用新型的具体实施方式,但本实用新型的保护范围并不局限于此,任何熟悉本技术领域的技术人员在本实用新型揭露的技术范围内,可轻易想到变化或替换,都应涵盖在本实用新型的保护范围之内。因此,本实用新型的保护范围应以所述权利要求的保护范围为准。
本文用于企业家、创业者技术爱好者查询,结果仅供参考。