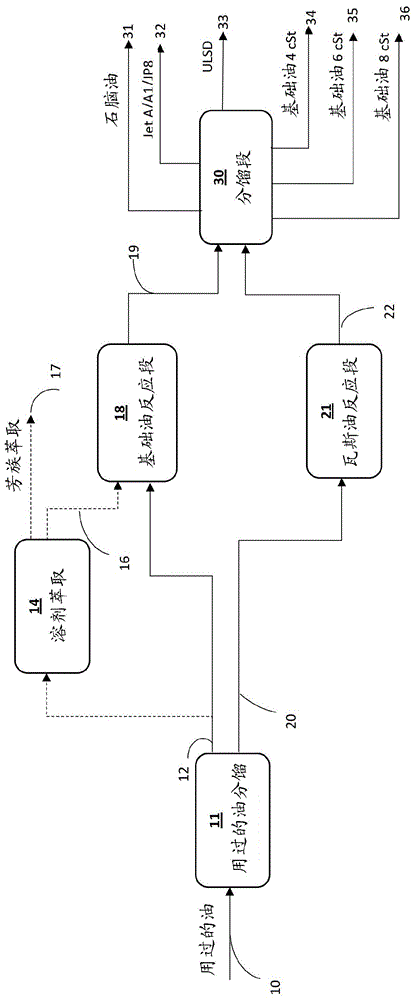
本发明涉及一种改进的方法,其用于加工用过的废油以生产符合规格的iii/iii 类基础油,该基础油随后可以与添加剂调和以生产发动机机油。
背景技术:
润滑油用于使彼此接触的机械部件之间的摩擦和磨损最小化,并且对于广泛种类的汽车、工业和船舶应用是必需的。润滑油的生命周期与包括温室气体排放的环境影响有关。润滑油的制造是原油精炼厂中最耗能的工艺,并且用过的润滑油通常在工业或商业锅炉中燃烧,释放包括二氧化碳的多种污染物。
对于用过的润滑油存在替代选项:收集和再精炼。已经开发了用过的油的管理程序以减少用过的油的实际损失量,并鼓励用过的油的再循环和再利用。当润滑油不再以预期的规格表现时,其必须停止使用。这在添加剂包变得被耗尽,且润滑剂变得受到污染时发生。
然而,润滑剂的基础油部分在使用过程中不分解。因此,可以将用过的发动机油和其它润滑油再精炼以除去水、污染物和添加剂,以生产与直馏基础油(virginbaseoil)相同质量的基础油。使用再精炼的基础油配制的润滑剂又可以满足与使用直馏基础油料(basestock)的那些相同的性能标准。
各种基础油的特性通常定义为如下:
i类基础油定义为具有80至120的粘度指数、高于0.03重量%的硫含量和不超过90重量%的饱和物。它们通过溶剂萃取原油的馏出物而制备。这种相对容易的加工方法使得该类比其它更精炼的等级相对更便宜。由于精炼的质量较低,i类基础油倾向于质量较低。尽管它们不可以用于多数应用,但它们对于普通应用仍具有良好的质量。配合它们的成本,这使得它们是许多润滑剂的原料。
ii类基础油与i类基础油类似,主要区别在于饱和物的量更高(高于90重量%)和硫含量更低(<0.03重量%)。通常,ii类基础油总体上表现得优于i类基础油,但是因为它们需要不同的精炼工艺,所以它们更昂贵。馏出物被加氢处理而不是溶剂萃取。
iii类基础油类似于ii类基础油,区别在于更高的粘度指数(高于120)。通常,iii类基础油表现得甚至优于ii类基础油,因为它们被更多地加氢处理。优异的特性使得iii类基础油为优质产品,并且它们通常与添加剂结合使用以制备高性能润滑剂。
iv类基础油定义为聚α烯烃(pao)。这些是化学工程化的基础油,并且具有非常低的倾点。因为它们是合成的,pao具有优异的质量,并表现出可想象到的最高水平。
v类基础油定义为不可以放在其它4类中的所有可能基础油。这些包括酯、聚亚烷基二醇(pag)、硅酮、环烷烃(naphthenics)和聚丁烷。它们通常具有极高的质量参数,因为它们是合成的基础油。表1显示了不同类别的基础油的一些性质。
表1
由于新的汽车发动机需要更多的低粘度油,所以基础油工业现在转向iii类基础油料的利用。在要求碳排放减少的监管规定的驱动下,原始设备制造商(oem)已经转向新的车辆发动机设计,其将继续推动润滑油工业至更高等级的基础油使用。这些驱动因素有望将基础油工业推向可以通过使用iii类和iv类基础油料实现的低粘度、优质性能的机油。
现有技术限于从废油生产i类和ii类基础油,如例如在美国专利7,261,808中所述,其由此通过引用并入本文。申请人已经用所公开的发明解决了缺乏有效的废油加工方法,以制备vi超过120的基础油和满足sae粘度等级的冷启动模拟器,从而用于加工用过的废油来生产符合规格的iii/iii 类基础油,该iii/iii 类基础油可以与添加剂调和来生产发动机机油。
另外,美国专利10,174,264教导了从来源于工业应用或发动机应用的废油生产工业白油或食用或药用油的方法,并且其由此通过引用并入本文。然而,没有现有技术教导如申请人在下文中描述的将用过的油或废油加工成iii/iv 类基础油的有效且高效的方法。
技术实现要素:
如上所述,由于新的车辆发动机需要更多的低粘度油,基础油工业正向iii类基础油料应用转变。在要求碳排放减少的监管规定的驱动下,原始设备制造商(oem)已经转向新的车辆发动机设计,其将继续推动润滑油工业至更高等级的基础油应用。因此,这种车辆的驱动因素有望将基础油工业推向可以通过使用iii类和iv类基础油料实现的低粘度、优质性能的机油。
申请人已经用新型设计解决了这种新需求,该新型设计利用加工具有高杂质和不同加工目标的分开进料的独立反应段系列装置(trains)。
更具体地,申请人已经开发了一种将废油加工成iii/iii 类基础原料的方法,包括:
a)将用过的油原料进料到分馏器中,以提供基础油物流和瓦斯油物流;
b)将所述瓦斯油物流进料至加氢处理反应器,以提供加氢处理的全馏程柴油物流;
c)将所述基础油物流进料至基础油反应器,以提供改质的基础油物流;
d)在两步分馏法中加工所述改质的基础油物流和所述经加氢处理的全馏程柴油物流,其中首先常压分馏且随后真空分馏所述改质的基础油物流和所述经加氢处理的全馏程柴油物流;以及
其中所述两步分馏法提供超低硫柴油物流、石脑油物流、喷气燃料物流和全部具有大于4厘沲的粘度的多种改质的基础油物流。
步骤a)、c)和d)是生产iii/iii 类基础油所必须的。任选地,如果需要将瓦斯油改质为ulsd和/或no.2燃料,则可以将步骤b)并入方法中。
根据原料的性质和基础油物流的所需性质,步骤c)可进一步包括以下任一:
c1)在氢气存在下使部分改质的用过的油与加氢脱金属催化剂接触;
c2)在氢气存在下使步骤(c1)的流出物与加氢处理催化剂接触;
c3)在氢气存在下使步骤(c2)的流出物与脱蜡催化剂接触;以及
c4)在氢气存在下使步骤(c3)的流出物与加氢处理催化剂接触。
或
c1)在氢气存在下使所述基础油物流与加氢脱金属催化剂接触;以及
c2)在氢气存在下使步骤(a)的流出物与加氢处理催化剂接触。
附图说明
图1显示了申请人的用于加工用过的废油以生产符合规格的iii/iii 类基础油的新型方法的示意图,所述iii/iii 类基础油可以与添加剂调和以生产发动机机油。
具体实施方式
图1显示了申请人的用于加工用过的废油以生产符合规格的iii/iii 类基础油的新型方法的示意图,所述iii/iii 类基础油可以与添加剂调和以生产发动机机油。
用作根据本发明方法的原料的用过的油(下文也称为废油)一般是由烃构成的矿物油,通常但不限于石油来源。这些油含有添加剂,如例如防锈剂、抗氧化剂、乳化剂、倾点下降剂(ppd)或粘度指数改进剂(viis)。它们在用于工业机器或内燃机中之后,通过氧化或形成基于碳的残余物或未燃烧的烃而部分降解。过滤废油原料以除去悬浮液中的固体颗粒,然后在脱水阶段通过本领域技术人员已知的任何方法,例如通过滗析或中度加热和任选蒸馏除去原料中所含有的水。
在根据上述加工之后,将废油物流10进料到汽提塔单元11,以将流出物分馏成调和基础油料物流12和柴油物流20,调和基础油料物流12通常具有下表2中确定的性质。一列显示由欧洲的典型原始废油物流生成的调和基础油物流12的典型性质,其通常具有较高水平的污染物,并且另一列显示了由来自美国的典型原始废油物流生成的调和基础油物流12的那些性质,其中污染物通常较低。
表2
柴油物流20通常具有astmd86t90%、282℃至338℃的温度和900kg/m3的最大密度。沥青质也在该步骤中除去。
在独立的反应段中加工用过的油衍生的调和基础油料物流12和柴油物流20是申请人的发明的关键特征,因为它允许在每个段中优化操作条件,以满足基于那些特定原料特性的所需产品规格。
废油物流10含有大量的金属污染物,这些金属污染物来自于调和在(用于润滑发动机的)基础油中的添加剂而存在。在汽提塔单元11中分馏之后,那些金属杂质主要集中在具有高浓度的硅(silica)和磷的柴油物流20中。这些金属是催化剂毒物,并且需要将大体积的催化剂负载在反应器中,以解决由金属中毒引起的催化剂失活。此外,废油物流10中的氯化物污染物也主要集中在柴油物流20中。
此后将柴油物流20进料到瓦斯油反应加氢处理器21,其中通过减少硫、氮和/或金属含量来改质柴油物流20,以产生改质的柴油原料22,其准备用于最后的两步分馏段30。
瓦斯油反应加氢处理器21通常在以下条件下操作:压力为3.5mpa至10.0mpa,且优选压力为4.0mpa至5.5mpa;lhsv为0.05至5h-1,且优选lhsv为0.1至1h-1;进料的h2/烃的比为100至5000nm3/m3;温度为200至400℃,且优选300至400℃(572至752℉);最低氢分压为2.5mpa。
用于hds单元21的催化剂可以包括任何合适的加氢处理催化剂,例如以下催化剂:其包含至少一种第viii族的金属(例如选自ni、co及其组合)和至少一种第vib族的金属(例如选自mo、w及其组合),任选地包括合适的载体和/或填料材料(例如包括氧化铝、二氧化硅、二氧化钛、氧化锆或其组合)。根据本发明的方面的加氢处理催化剂可以是本体催化剂或负载型催化剂。生产负载型催化剂的技术是本领域公知的。
在加氢处理器21中的加氢处理过程中,氯化物转化为hcl。如果试图从反应器流出物中回收热,加氢处理器21中产生的hcl与氨一起存在,可以在热回收网络中快速沉淀。而与下文所述的基础油流出物物流19相比,改质柴油原料22的收率低。高浓度的氯化物和金属可以控制对热集成和脱金属催化剂藏量(catalystinventory)的限制。
调合基础油料物流12由i/i /ii/ii 类基础油组成,并且此后任选地送到溶剂萃取单元14。溶剂萃取单元14除去包括硫、氮、芳族化合物和金属的杂质,由此产生芳族萃取物流17和由i /ii/ii 类基础油组成的改质调合基础油原料物流16。芳族萃取物流17是可以作为燃料出售的副产物。
调和基础油料物流12和改质调和基础油原料物流16将通常具有下表3所示的性质:
表3
改质共混基础油原料物流16在进料苛刻度方面有明显的改进,并且因此(如果溶剂萃取单元14已经存在于设备流程方案中)提供了运行溶剂萃取单元14的动机。然而,通过提高基础油加氢处理器18中操作条件的苛刻度,使得调和基础油料物流12也适合用于在基础油加氢处理器18中改质,因此,如图1所示,在申请人的用于废机油改质的新型加工方案中,溶剂萃取单元14被认为是任选的。
改质的调和基础油物流16可以替代性地源自用过的油的分馏、分馏和溶剂萃取(糠醛或nmp:n-甲基吡咯烷酮作为溶剂)或分馏和加氢处理,或上述任意组合。
改质的调和基础油原料16或调和基础油料物流12随后与氢气(未示出)一起送往配备有进料扩散器和高效液体分配器塔盘的基础油反应器18的顶部,以将液体和蒸气均匀地分布穿过催化剂床,从而产生基础油流出物物流19。基础油反应器18在顶部和同一反应器中的每个床之间配备有液体分配器塔盘,以将蒸气和液体重新分布穿过催化剂床。基础油反应器18是下流式反应器,其中进料和氢气同向流动穿过所有催化剂床。
分配的液体优选与加氢脱金属催化剂接触,以除去金属污染物。脱金属床(当存在时)的数量可以优选为1至8,甚至更优选1至3。在这种情况下,来自脱金属步骤的流出物与加氢处理催化剂接触,或者直接堆叠在脱金属催化剂床下,或者在脱金属催化剂下的一个或多个分离床中。加氢处理床的数目可以优选在1至8,甚至更优选1至5。
基础油反应器18通常以以下操作:(i)200℃至400℃的温度,(ii)5.0mpa至30.0mpa的压力,和(iii)0.1h-1至10h-1的lhsv,且其中脱金属催化剂的第viiib族金属含量为1重量%至10重量%且第vib族金属含量为2重量%至15重量%;(v)在(i)负载型的基于镍和基于钼的催化剂,或(ii)基于镍和基于钨的催化剂的存在下,使所述脱金属的产物经受加氢处理阶段,以生产深度加氢处理产物,其中所述深度加氢处理在以下条件下进行:(i)250℃至450℃的温度,(ii)5.0mpa至30.0mpa的压力,(iii)0.05h-1至10h-1的lhsv,和(iv)100至3,000标准升/升原料的氢气流量。
任选地,使来自基础油反应器18的流出物与脱蜡催化剂接触以改进基础油流出物物流19的倾点。来自脱蜡催化剂的流出物可优选在小层加氢处理催化剂中进一步加工,以处理可在脱蜡床中形成的任何发色体(colorbody)。脱蜡催化剂的入口温度可以与加氢处理催化剂出口的温度相同,或者可以使用氢气或来自分馏的流出物产物骤冷以降低脱蜡催化剂入口温度。将骤冷剂注入,并在混合装置中混合,随后至液体分配器塔盘中。在不同步骤中使用的催化剂可为单一类型的催化剂或具有相同功能的不同催化剂的组合或包。
合适的脱蜡催化剂是多相催化剂,其包含分子筛或zsm-5型沸石,并任选地与具有加氢功能的金属官能组合。合适的金属是第viii族金属,例如镍、钴、铂和钯。铂和钯的组合以及镍或钴与第vib族金属的组合(例如nimo或niw)也是可能。通过以以下操作催化剂来实施脱蜡功能(i)相同温度或比加氢处理催化剂低优选150℃,更优选40℃,甚至更优选低20℃至相同温度的温度,(ii)5.0mpa至30.0mpa的压力,和(iii)0.1h-1至10h-1的lhsv,和(iv)100至3,000标准升/升原料的氢气流量。来自脱蜡催化剂的流出物在加氢处理催化剂上进一步处理,以处理在脱蜡过程中可能已经形成的任何发色体。使用加氢处理催化剂以以下实施加氢处理功能(i)250℃至450℃的温度,(ii)5.0mpa至30.0mpa的压力,(iii)1h-1至20h-1的lhsv,和(iv)100至3,000标准升/升原料的氢气流量。在另一个实施方案中,使用氢气、再循环的分馏反应器流出物或任何类型的换热器(包括但不限于tema管壳式换热器、板式换热器、螺旋管式换热器)降低脱蜡催化剂温度。
基础油流出物物流19与改质柴油原料22一起随后进料至共同的分馏段30,在所述共同的分馏段30这些物流经受几个步骤,在其中两个物流在共同的分馏塔中加工。第一步需要除去轻质烃,并且可以在汽提塔(stripper)或常压分馏器(未示出)之一的压力下实现,其中根据所需产物除去石脑油和轻馏分或锭子油馏分和轻馏分。该第1步分离的操作压力通常为0mpa至2.0mpa,并且温度通常为65℃至370℃。
第二步涉及在真空条件下生产润滑油,以生产轻锭子油馏分和粘度大于4cst的多种iii 类基础油。如本文所用,多种(个)是指至少2种(个),优选至少3种(个),并且最优选3个iii 类基础油物流。在两步分馏段30中分馏在反应器18中产生的基础油沸腾材料(boilingmaterial),使得大量基础油馏分的粘度不合规格。
iii类基础油以各等级的特定粘度范围出售。在加氢处理器中,对于加氢处理的基础油,基础油材料的总体积粘度将低于进料基础油。反应器操作苛刻度由脱硫要求(通常并非约束)、芳族化合物饱和要求(通常并非约束)、粘度指数改进要求或基础油的总体积粘度设定。为了保持基础油收率,基础油反应器18的苛刻度将被限制为满足加氢脱硫、芳族化合物饱和或粘度指数改进要求。
优选地,分馏段30提供石脑油物流31、喷气燃料物流(a/a1/jp8)32(如果需要)、超低硫柴油物流33、4厘沲等级的基础油物流34(通常为4.0±0.3cst)、6厘沲等级的基础油物流35(通常为6.0±0.3cst)和/或8厘沲等级的基础油物流36(通常为8.0±0.3cst)。此后,可根据需要将化学添加剂加入4厘沲等级的基础油物流34、6厘沲等级的基础油物流35和/或8厘沲等级的基础油物流36中。
可以使用的化学添加剂的一个实例是chimec6043,其剂量比优选为10wppm至10,000wppm,更优选为20wppm至500wppm,甚至更优选为50wppm至100wppm。
100℃下的成品总粘度规格可以通过第二步分馏中将大量基础油流出物分馏成4厘沲等级的基础油物流34馏分、6厘沲等级的基础油物流35馏分或是8厘沲等级的基础油物流36馏分来满足。在下表4中可以看到以特定等级分馏大量基础油的优点,其中仅在选项2和选项4中生产符合规格的基础油。
表4
如上所举例说明,两步分馏和各种等级的iii/iii 类基础油的生产导致在单元中生产的总基础油的更高收率。该第二步分离的操作压力通常为7mmhg(绝对压力)至760mmhg(绝对压力),并且温度通常为65℃至370℃。真空系统可以是多级真空泵、抽气泵和在有或没有预冷凝器情况下的前述两种设备的任何组合。
在第二步分馏中,分离至少两种产物,锭子油馏分和iii/iii 类粘度等级的基础油之一。在第二步中生产的iii/iii 类基础油将满足noack规格和各个等级的粘度范围。在该方法中,第二步分馏可以生产仅锭子油馏分和一个等级的iii/iii 类基础油,或者锭子油馏分和两个等级的iii/iii 类基础油,或者锭子油馏分和三个等级的iii/iii 类基础油。对分馏的基础油的等级数目的优选不受限,并且基于废油进料组成。在第二分馏步骤中生产的基础油数目的任何组合将满足在下表5中总结的等级中至少一个的质量规格。
表5
另外,当需要生产4cst等级基础油和6cst等级基础油或者4cst等级基础油、6cst等级基础油和8cst等级基础油产品时,考虑以下设计考虑因素以用于第二步分馏:限制闪蒸段温度低于350℃,过汽化量(overflash)为30%至600%的塔底产物流量,并将过汽化量重新导入真空塔加热器入口,汽提蒸汽注入流量为50至500kg/sm3塔底产物,优选110至120kg/sm3的塔底产物,蒸汽仅在加热器入口注入或仅在真空分馏器底部注入,或以任何比例在加热器入口和真空分馏器底部两个位置注入。
所有上述基础油物流是iii/iii 类基础油,并且此后可以用于制造低粘度、优质性能的机油。
实施例1
通过以下实施例将进一步描述本发明,所述以下实施例不应被解释为限制本发明的范围。
在废油再精炼中加工大量废油物流。分馏该大量废油以脱水和分馏以下物流:石脑油和轻尾馏分(ends)、柴油、基础油和沥青稀释油。废油的柴油和基础油馏分用作本实施例的进料。该进料的相关性质列于下表6中:
表6
在典型的柴油加氢处理器中,用加氢处理催化剂对柴油物流进行加氢处理以除去硫。进料中的高金属含量要求柴油在氢气存在下与脱金属催化剂接触,然后与加氢处理催化剂接触。柴油加氢处理段中的典型操作条件和收率为:wabt,320至390℃,
氢分压4.6mpamin,h2/hc再循环比500sm3/m3,柴油收率>98重量%,且流出物柴油硫含量<10wppm。
然后在加氢处理器中对基础油物流进行加氢处理。下表7显示了基于是否使用脱蜡催化剂的两种不同操作条件。在不使用脱蜡催化剂来满足基础油倾点的操作方案中,需要化学添加剂调和以将基础油倾点降低至商售iii类基础油规格-15℃。脱蜡催化剂用于催化改进处理过的基础油的倾点,并且这两种可能的条件和流出物物流性质总结在下表7中:
表7
然后,来自柴油反应段和基础油反应段的处理过的流出物在两步法中分馏,其中获自分馏排出(ex-fractionation)的iii/iii 类基础油具有在本申请的具体实施方式部分的上表5中所示的性质。
两步分馏法特别设计成使用蒸馏满足产品规格而不降低产品质量。在这种情况下,重要的是保持流出物操作温度低于390℃,并且更优选低于350℃,因此,第一步通常在0.02mpa至1.0mpa的压力下进行,其中分离轻馏分如石脑油和/或jeta/a1/jp8和/或ulsd,同时保持温度低于350℃。第二步分离在真空条件下实施,操作压力为5mmhg(绝对压力)至600mmhg(绝对压力)。
已经根据具体实施方案和应用公开了本文所述的发明。然而,这些细节不意味着限制,并且根据本教导,其它实施方案对于本领域技术人员将是显而易见的。因此,应当理解,附图和描述是对本发明原理的说明,并且不应当被解释为限制其范围。
本文用于企业家、创业者技术爱好者查询,结果仅供参考。