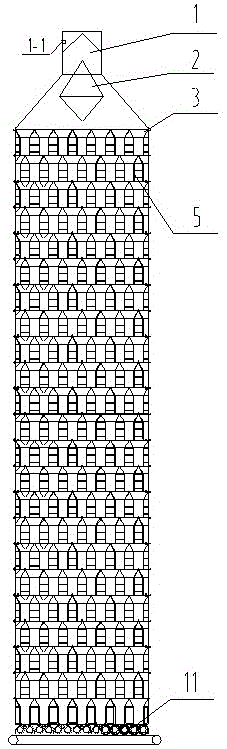
本实用新型涉及煤化工技术领域,尤其涉及一种管壳浮动装配式半焦炉装置。
背景技术:
我国以煤为主的能源结构在未来相当长的时间内不会改变,低价煤(褐煤、长焰煤、弱黏煤、不黏煤)在我国煤炭蕴藏量中约占50%(其中褐煤约13%),产量约占目前总量的30%.如何清洁利用我国丰富的低价煤资源,实现利用效率和经济效率最大化,是新型煤化工产业的重要课题。
低价煤由于含水量、挥发分高,当堆积高度大于2米时易产生自燃,所以不能远距离运输,只能在煤矿附近进行加工,加工方式主要是对煤进行干燥、提质分馏。低价煤在200度以下干燥,去除一定的挥发分和水分后可以长距离运输。低价煤的提质是在干馏设备内将煤在隔离空气的条件下将煤加热到500-650度温度下使煤中的水分、有机气体、煤焦油分离出来,使煤变成半焦俗称兰炭,使低价煤得到高效清洁利用。低价煤的提质是在干馏设备内进行,分内热式和外热式。
内热式都是用燃烧烟气对煤直接加热,因烟气要穿过煤层所以用的煤必须是块煤,粉煤必须筛掉,所产的煤气由于混入了燃烧烟气而热值低利用率不高,熄焦大多数采用水熄焦热量利用率低,焦出焦后再要烘干,产生大量废水、废气,污染严重,因此制约了产业的发展。
我国低价煤主要分布在陕西的陕北、宁夏、内蒙、新疆等地,现在由于机械化开采可用于内热式生产半焦的块煤不足30%,余下70%多的粉煤高效清洁利用是个难题。国内不少大学、研究所、生产企业针对粉煤的清洁利用开发了不少设备,如热载体技术、流化床技术、外热式的回转炉技术等,都因煤在炉内高温下需要机械传动而带来一系列的问题,如密封、磨损、煤气中煤尘太多等问题;所以不能长期使用而不能产业化。
目前在正常生产的焦炉、半焦炉,煤在成焦过程中几乎是没有机械传动的,如焦炉只有装煤与推焦,煤在成焦过程中是不动的;而半焦炉中煤在成焦过程中是以煤的自身重力向下移动的,煤移动不需外力,所以在生产过程中稳定可靠,但还是存在许多需要改进的问题,如密封性不够带来的跑烟问题,以及半焦炉主体由不锈耐热钢制作而成,而钢材热胀冷缩后的变形对炉体的损伤等等,急需解决。
技术实现要素:
本实用新型的目的在于克服上述不足,提供一种管壳浮动装配式半焦炉装置,对粉煤进行加热、气体的分馏、半焦的冷却,加热、冷却气体走管程,粉煤加热、分馏气体出口、半焦冷却走壳程。
本实用新型的目的是这样实现的:
一种管壳浮动装配式半焦炉装置,它包括加煤装置、换热器装置和出焦装置;所述加煤装置包括直煤斗和布煤分流锥,所述布煤分流锥设置在直煤斗的下方,
所述加煤装置下方设置换热器装置,所述换热器装置包括由上至下依次间隔布置的a型模块和b型模块,最上层的a型模块设置在布煤分流锥下方,最下层的b型模块设置在出焦装置上方;
所述a型模块包括多个u形列管,所述u形列管上方设置锥形分流锥,u形列管下方设有分馏气体出口通道,所述锥形分流锥的两边和中间各设有一块承重条,承重条下部连接承重块,承重块与分馏气体出口通道连接,所述分流锥、分馏气体出口通道与承重条、承重块刚性连接;所述b型模块与a型模块仅u形列管、分流锥的排布位置不同,b型模块的分流锥设置在上方a型模块的两个u形列管之间;所述u形列管的下层开口设为u形管气体进口,上层开口设为u形管气体出口;所述一个u形列管的u形管气体出口与上方的u形列管的u形管气体进口之间设有气体连接容器连接;
所述a型模块与b型模块之间通过十字定位销钉定位,使两模块前后左右不能移动,上下由模块自身的重力锁定;所述a型模块与b型模块之间的内密封由模块内的粉煤自身密封,四周对外密封采用密封上法兰和密封下法兰密封,密封上法兰和密封下法兰之间设有密封条。
进一步地,所述分馏气体出口通道的前端与u形列管焊接密封的一端一起焊接密封,并安装有氮气吹扫口,所述分馏气体出口通道后端连接粉尘沉降容器,粉尘沉降容器的另一端与单模块分馏气汇集管相连接。
进一步地,上下的a型模块与b型模块之间设有4个十字定位销,其中在一个模块上固定安装定位销,另一模块相对应的位置上加工有xy方向的长槽;当定位销插入后x槽方向的在x方向可移动,y方向不能移动,y槽方向的插入后x方向不能移动;当上下模块温差大时,上下x、y方向的热胀冷缩量增大造成应力,十字定位销可在xy方向都不受冷热伸缩约束,可移动。
进一步地,所述换热器装置分为上部的预热干燥段、中部的分馏段和下部的冷却段,冷却段中最上层模块中的u形管气体出口通过热气通道连接预热干燥段最下层模块中的u形管气体进口;分馏段最上层模块中u形管气体出口设为加温冷烟气出口,热烟气被煤换热后得到降温后的烟气从此出来,然后进入空气热交换器对燃气炉的空气、煤气预热;分馏段最下层模块中u形管气体进口设为加温热烟气进口,由此进入的热烟气对煤加热,被煤换热降温后从加温冷烟气出口出去。
进一步地,最下层的b型模块的u形管气体进口设为冷气进口,最上层的a型模块的u形管气体出口设为冷气出口。
进一步地,所述换热器装置外围设置外固定框架。
进一步地,所述出焦装置包括传动齿轮、出焦分流锥、出焦轴和承重方管,出焦装置设置在换热器装置最下层模块的分馏气体出口通道下方,其结构与换热器装置的a型模块、b型模块相似,仅将模块的u形列管和分馏气体出口通道替换为承重整个炉体的承重方管。
进一步地,所述承重方管的两端与外固定框架连接固定;相邻两个承重方管之间设有一个出焦分流锥,所述出焦分流锥的两侧分别设有一个出焦轴,所述出焦轴由传动齿轮带动,控制出焦。
进一步地,所述出焦轴上设有存储焦粉沟槽,出焦轴和出焦分流锥与上面的承重方管之间留有间距,使焦流入间距内。
进一步地,所述换热器装置的内部涂有耐磨损陶瓷涂层,涂层的厚度为0.1-0.8mm。
与现有技术相比,本实用新型的有益效果是:
(1)本实用新型的加煤装置中在煤斗下方设置布煤分流锥,加煤时粉煤加入煤斗,煤位由传感器控制,煤流动到布煤分流锥上,分流锥上的煤通过粉煤的堆放安息角自然流动到换热器装置中,实现自动加煤。
(2)本实用新型的换热器装置不用刚性连接,模块外密封由上下模块上的密封法兰中的密封条密封,内密封由每层模块中的粉体(煤、焦)密封;模块与模块无刚性连接只有十字定位使其在装配后不能前后左右移动;模块中的加热、冷却管道采用u形列管,使列管受冷热后产生的变形对模块无影响,可避免热胀冷缩对整个炉体的影响。
(3)本实用新型的换热器装置由a、b型换热模块拼装而成,根据换热方式不同,组合成上面的预热干燥段、中间的加温分馏段、下面的熄焦冷却段;预热干燥段是由下面熄焦冷却段来的热气,通过模块中的u形列管内上行与u形列管外下行的粉煤逆向换热,使流动到分馏段的粉煤得到预热;加温分馏段由燃气热烟气通过模块中的u形列管管内对管外下行的预热粉煤进一步换热升温,逆向上行的热烟气降温后排出炉外再利用;熄焦冷却段由最下面模块中的u形列管管内通入冷气,逆向对管外从分馏段下行的热半焦进行换热,冷气通过换热升温后通入上面的预热干燥段;使煤流在炉内换热时煤的内外层得到交换,提高了换热效率,大大降低了燃料的费用。
(4)本实用新型的a型和b型模块中的u形列管等位置错开(列管换热器中的三角形排列),使粉煤在下行时从a到b模块中位置得到置换,使加热速度加快且均匀,同时留出了气体分馏的空间及通道,还避免了粉煤的压实现象。
(5)本实用新型每个u形列管下方都有一个分馏气体出口通道,使粉煤在流过每个u形列管加温后将能分馏的气体及时的通向炉外,避免了分馏气体在炉内集中排出而引起的煤气流速太大带来的煤气中粉尘含量大及焦油二次分解的问题。
(6)本实用新型的出焦装置是由出焦轴控制控制出焦速度的,出焦轴不动不出焦,轴转动快出焦就快。
(7)本实用新型可实现生产自动化,具有节能、节水、废水废气产生量少、半焦质量可控、煤气和焦油品质好及煤尘少等特点;煤在预热干燥、分馏成焦、熄焦冷却过程中无需机械动作,避开了机械动作在高温下带来的不稳定因素。
附图说明
图1为本实用新型的结构示意图。
图2为本实用新型的a-a剖视图。
图3为本实用新型的布煤装置的结构示意图。
图4为图3的i处局部放大图。
图5为本实用新型的换热模块的结构示意图。
图6为本实用新型的u形列管的结构示意图。
图7为本实用新型的承重结构示意图。
图8为本实用新型的出焦装置示意图。
图9为本实用新型的上下模块销钉十字定位示意图。
图10为本实用新型的粉煤在炉体内流动的状态示意图。
其中:
直煤斗1、煤位传感器1-1、布煤分流锥2、a型模块3、冷气出口4、b型模块5、热气通道6、加温冷烟气出口7、加温热烟气进口8、外固定框架9、冷气进口10、出焦装置11、传动齿轮11-1、出焦分流锥11-2、出焦轴11-3、承重方管11-4、密封上法兰12、密封下法兰13、密封条14、气体连接容器15、u形列管16、u形管气体进口16-1、u形管气体出口16-2、粉尘沉降容器17、单模块分馏气汇集管18、分馏气体出口通道19、承重块20、承重条21、十字定位销钉23、氮气吹扫口24。
具体实施方式
实施例1:
参见图1-10,本实用新型涉及的一种管壳浮动装配式半焦炉装置,它包括加煤装置、换热器装置和出焦装置11。
所述加煤装置包括直煤斗1和布煤分流锥2,所述布煤分流锥2设置在直煤斗1的下方,所述直煤斗1内安装有煤位传感器1-1。
所述加煤装置下方设置换热器装置,所述换热器装置包括由上至下依次间隔布置的a型模块3和b型模块5,最上层的a型模块3设置在布煤分流锥2下方,最下层的b型模块5设置在出焦装置11上方。
所述a型模块3包括8个u形列管16,b型模块5包括7个u形列管16,所述u形列管16上方设置锥形分流锥,u形列管16下方设有分馏气体出口通道19,所述锥形分流锥的两边和中间各设有一块承重条21,承重条21下部连接承重块20,承重块20与分馏气体出口通道19连接,所述分流锥、分馏气体出口通道19与承重条21、承重块20刚性连接,形成一个刚性的模块框架。
所述b型模块5与a型模块3仅u形列管16、分流锥的排布位置不同,b型模块5的分流锥设置在上方a型模块3的两个u形列管16之间。
所述u形列管16的下层开口设为u形管气体进口16-1,上层开口设为u形管气体出口16-2。
所述一个u形列管16的u形管气体出口16-2与上方的u形列管16的u形管气体进口16-1之间设有气体连接容器15连接,气体连接容器15将下模块上多个u形管气体出口16-2出来的气汇在一起后再分配到上一个模块上的多个u形管气体进口16-1中。
所述分馏气体出口通道19的前端与u形列管焊接密封的一端一起焊接密封,并安装有氮气吹扫口24,所述分馏气体出口通道19后端连接粉尘沉降容器17,粉尘沉降容器17的另一端与单模块分馏气汇集管18相连接,当分馏的气体进入容器17得到减速使粉尘沉降后,一个模块上的多个分馏的气体汇入单模块分馏气汇集管18,在模块上的多个分馏气体汇入后通向总的集气管内后由喷淋氨水冷却。
所述粉尘沉降容器17、单模块分馏气汇集管18上都设有加热保温装置,使它们的温度保持在内部气体的露点以上,以防气体中的水蒸汽、焦油蒸气结露。
所述a型模块3与b型模块5之间通过十字定位销钉23定位,使两模块前后左右不能移动,上下由模块自身的重力锁定;所述a型模块3与b型模块5之间的内密封由模块内的粉煤自身密封,四周对外密封采用密封上法兰12和密封下法兰13密封,密封上法兰12和密封下法兰13之间设有密封条14。
上下的a型模块3与b型模块5之间设有4个十字定位销23,其中在一个模块上固定安装定位销,另一模块相对应的位置上加工有xy方向的长槽;当定位销插入后x槽方向的在x方向可移动,y方向不能移动,y槽方向的插入后x方向不能移动;当上下模块温差大时,上下x、y方向的热胀冷缩量增大造成应力,十字定位销23可在xy方向都不受冷热伸缩约束,可以移动。
所述换热器装置分为上部的预热干燥段、中部的分馏段和下部的冷却段,冷却段中最上层模块中的u形管气体出口16-2通过热气通道6连接预热干燥段最下层模块中的u形管气体进口16-1;分馏段最上层模块中u形管气体出口16-2设为加温冷烟气出口7,热烟气被煤换热后得到降温后的烟气从此出来,然后进入空气热交换器对燃气炉的空气、煤气预热;分馏段最下层模块中u形管气体进口16-1设为加温热烟气进口8,由此进入的热烟气对煤加热,被煤换热降温后从加温冷烟气出口7出去。
最下层的b型模块5的u形管气体进口16-1设为冷气进口10,最上层的a型模块3的u形管气体出口16-2设为冷气出口4。
所述换热器装置外围设置外固定框架9,对炉体支撑固定,固定方式跟上下模块的方式同理采用十字定位,使炉体受到热后不受膨胀的影响。
所述出焦装置11包括传动齿轮11-1、出焦分流锥11-2、出焦轴11-3和承重方管11-4,出焦装置11设置在换热器装置最下层模块的分馏气体出口通道19下方,其结构与换热器装置的a型模块3、b型模块5相似,仅将模块的u形列管16和分馏气体出口通道19替换为承重整个炉体的承重方管11-4,所述承重方管11-4的两端与外固定框架9连接固定;相邻两个承重方管11-4之间设有一个出焦分流锥11-2,焦下行时将下行的焦一分为二;所述出焦分流锥11-2的两侧分别设有一个出焦轴11-3,所述出焦轴11-3由传动齿轮11-1带动,控制焦的出焦与不出焦及快与慢;
所述出焦轴11-3上设有存储焦粉沟槽,出焦轴11-3和出焦分流锥11-2与上面的承重方管11-4之间留有一个间距,使焦流入间距内,此间距以焦在轴静止时,间距内的焦也静止时为准;出焦轴11-3上朝上的沟槽中充满焦粉,当出焦轴11-3转动时存储在沟槽中的焦粉依此落下,同时利用出焦轴11-3与焦的摩擦力带动间距内的焦粉一起落入下面的输送带上。
整个炉子的产量和质量由下面的轴控制,轴转动快产量就高,轴转速在一转7分钟左右,使上面的粉煤流速在每分钟40mm左右。
所述换热器装置的内部涂有耐磨损陶瓷涂层,涂层的厚度为0.3-0.5mm,解决煤在流动时对不锈耐热钢炉体产生摩擦磨损、腐蚀等问题。
工作原理:
所述煤斗置于分流锥上方,煤斗中安装有煤位传感器;加煤时粉煤加入煤斗,煤位由传感器控制,煤流动到布煤分流锥上,分流锥上的煤通过粉煤的堆放安息角自然流动到换热器模块中;当下面出焦装置出焦后,上面的煤向下流动破坏了堆放安息角角度,煤斗中的煤自然补上,煤斗中的煤由煤位传感器自动补上。
所述换热器装置由多个ab型换热模块组成上面的预热干燥段、中间的组成分馏段、下面的组成冷却段;预热干燥段由下面冷却段换热得到的热气对煤预热干燥,热气与煤换热后变成冷气后从上部排出;中间的分馏段由外面的燃气热气从分馏段下面的列管进入对流入模块的预热煤换热加温,使煤达到所要的分馏温度,换热后的气体还是有一定的温度,此气体从分馏段上部排出后还可再利用,通过换热气器对燃气锅炉所需要的空气预热,使热能利用最大化;下面的冷却段由下面的列管进入的冷气对上面下行的热焦逆向换热冷却,得到的热气通过管道进入预热干燥段,冷却后的半焦由出焦部分排出。这样炉子所需要的热是煤中水份的蒸发、煤气的蒸馏的热,还有熄焦冷却、预热干燥中换热效率上损失的热,因此大大降低了燃料的费用。
所述换热模块a和b是由多个由方管加工成为u形的列管、锥形分流锥、分馏气体出口通道、承受炉体重量的承重块、承重条及模块外四周的密封法兰组成;锥形分流锥、分馏气体出口通道与承重条、承重块刚性连接,形式一个刚性的模块框架;u形的列管只与一边的承重条块连接,当列管受热或冷变形时在模块内不受模块约束;这样当模块ab拼装后就形式了一个管壳浮动装配式炉体。模块中的列管采用了u形的列管后可消除大部分热胀冷缩对模块带来的应力;ab模块装配式结构减缓了模块前后左右的冷热应力、消除了炉体受热后每个模块向上热胀变形带来的应力。ab模块由于锥形分流锥、分馏气体出口通道、u形的列管排列的位置不同,错开了一个锥形分馏锥的位置,装配成炉体后,从a模块中的煤流动到b模块中时,被b模块中的锥形分流锥一分为二,使a模块中靠近列管的煤流入b模块中的煤在中间,中间的靠近了b模块的列管,实现了煤流动层的置换,使加热冷却均匀、速度加快。同时整个炉体内的煤从a模块流动到b模块,煤的流动实况其实是在虚似的料斗中流动的状态,因此可将整个炉体视作为是全部由单个煤斗组合而成的,是煤从上一个煤斗流动到下一个煤斗的关系,下一个煤斗煤流掉多少上面的煤斗就补多少,也不会多流,因为煤的流动状态是粉煤的堆放状态,与上面的布煤装置是一个原理;只要锥形分流锥的锥度大于煤的堆放安息角就不会出现架桥现象。
以日加工240吨粉煤x0.6产率=144吨半焦,年产5万吨半焦的中试炉子为例;模块的尺寸定为长3372、宽3000、高660,模块中两列管中心距480mm,尽间距240mm,煤的容积为3.34立方*0.8比重=2.67吨煤。炉子由22个模块装配而成,其中上面加温段8个、分馏段6个、冷却段8个;煤以每分钟44mm流下,则流过一个模块660/44=15分钟,煤从加入要经过2小时加温预热、1.5小时分馏、2小时冷却,22个模块总共需5.5小时;也就是每小时4个模块中的煤4*2.67=10.68吨*0.6产率=6.4吨半焦,一天半焦产量6.4*24=153.6吨。
生产时由加煤装置将整个炉体加满直到加煤自动停止为止,开动出焦装置观察煤是否顺畅落下,正常后关闭;打开氮气吹扫口,将炉内的空气全部置换后关闭;开启燃气炉,首先以300度左右的热烟气由分馏段下面的加温烟气进口进入对煤加温,当煤温传感器温度上升时开动出焦装置,同时逐步提高燃气温度到700度,开动冷气风机,冷风从冷却段下面的冷气进口进入冷却段;进入冷却模块中的冷气经过u形列管的换热,使下行的焦逐渐冷却,上行的冷气得到升温,升温的气体由u形管气体出口经热气通道、u形管气体进口进入预热干燥段,进入的热气与煤换热冷却后从上部的冷气出口排出。考虑到炉体的热胀冷缩加温不能太快,此过程到正常出焦至少需要7-8小时的热平衡;在中间要经常观察炉内煤、气体、焦的温度仪表的变化,调节加温、冷却的风量,调节出焦速度;及时检测分馏气体、半焦的成分,使其合格后确定工艺参数。
分馏段下部的煤被加热到600度时已成为半焦,下行到冷却段的每个模块中被逐个从u形列管中经过的冷气换热冷却,半焦到出焦时被冷却到100度以下;冷气从冷却段的进口进入,进入的冷气全部吸收了半焦从600度冷却到100度所释放的热量;从进口进入的常温气体到冷却段换热后出口气体的温度是由进入气体的温度、冷却气体的流量、出焦速度、出焦温度决定的,是一个变量关系,一般控制在400-450度;冷却段换热后的热气进入预热干燥段对煤预热,最终得到的煤的预热温度也是一个变量关系,煤的流速、加热气体的流速及温度是由下面的冷却段决定的,冬天夏天的煤温、煤的湿度将影响煤的预热温度,预热温度一般在250-300度。煤的分馏段只要根据半焦的质量要求,成焦温度可在500-650度调节,温度由烟气流量、烟气温度及出焦速度控制。所以整个生产过程主要由半焦的质量、产量、热能的利用来精准调节;热能的充分利用主要是半焦、预热段气体的出口温度的降低;提高的一种办法是增加每个段的模块。
在整个炉体中,煤在受加温后能分解有利用气体的温度是在200度以上,炉中能有此温度的为预热干燥段的下面的3个模块、分馏段6个模块、冷却段上部的5个,这14个模块中都有分馏气析出,其中冷却段下3个析出的量比较少;这14个模块中有用的气体经每个模块上的7个分馏气体出口通道19、经过7个粉尘沉降容器17汇集到单模块分馏气汇集管18后一起通往煤气初冷集气管。能正常析出煤气的是上面3个、中间6个、下面2个共11个(下面3个不计),11个模块中有分馏气体出口通道19为11*7=77个;每个通道的载面积0.228*0.09=0.02052平方,77个为1.58平方;炉子每小时干馏10吨煤,吨煤产净煤气200立方,在炉中荒煤气330度下体积为2.6倍,则200*2.6=520立方,到蒸馏时吨煤中蒸发水分80公斤的水蒸气为80*1.7=136立方。则煤气在分馏气体出口通道内的平均流速为(520 136)*10吨=6560立方/1.58平方/3600秒=1.15米/秒,此速度流入载面为0.228*0.25=0.057平方的粉尘沉降容器17减速,比例为0.057/0.02052=2.78倍,减速后为1.15/2.78=0.415米/秒。此流速足以使直径0.05mm的煤尘下沉,下沉的煤尘流回到炉体的煤流中去。
14个模块中分馏的煤气压力由煤气初冷集气管控制,一般在300-500帕,高了对炉体的对外密封带来压力;为了防止煤气内部串气,把预热干燥段上面余下的5个模块上的单模块分馏气汇集管一起接入一个容器,容器内的压力等近于煤气压力,压差不大于或小于50帕;下面冷却段余下的3个模块同样处理,如压力不够可喷水增压;模块中的粉煤本来自己已形成密封,这样的方式形成了内部炉内的煤气密封,使其不能串气。
装配后ab模块之间的对外密封由模块上的上下法兰之间的有一定弹性的陶瓷绳实现,直径15mm,安装3条,两法兰距离12mm,陶瓷绳的压实由模块自重实现;由于炉内分馏气体压力不高,3条陶瓷绳在静密封的情况下又形成了阶梯密封,所以就算是有泄漏也是微量的。
煤在分馏段分馏温度为600度,煤预热温度250度,所需要的热是250-600=350度,250度时煤的比热大约为2.2千焦,1千焦=0.24大卡,每升温1度为2.2*0.24*1000=528大卡/吨,350度则为528*350=184800大卡/吨,如用1900大卡的荒煤气加热则要184800/1900=97立方,用炭化硅电加热则184800/860大卡/度=215度/吨。本炉每小时处理10吨常温粉煤,在炉中煤到250度温度处已不满9吨,只能8吨多点,到600度处成焦后为6吨左右;视煤的品种、温度、湿度、粗细粒度,吨煤所需的热量由于工艺参数不同也不同。
炉中ab模块中的两个u形列管之间的距离也是煤流的厚度为240mm,b型模块两边上的煤流为120mm;在模块中两个u形列管之间的煤被中间的承重块20隔开形成了一个长1320*高460*宽240容煤的直煤斗,煤下降时被下模块上的处于240mm煤流宽中间的分流锥一分为二,形式与炉上面的布煤装置一样,这样煤流是上一个直煤斗的煤被分流到下面二个直煤斗中煤一半的关系。也可看作为下面模块上的二个分流锥的顶角之间的距离480mm以上460mm高、1320mm长的虚似直煤斗,二分流锥的内二边为煤斗的钭边,这样形成了一虚似的尺寸为长1320、宽480、总高660下面出煤口宽240mm的矩形煤斗;斗中出煤口的煤流入下二个斗中。影响煤流的流动性主要看b型模块二边上的煤流宽120mm上是否有架桥现象,经过试验6mm以下堆放安息角49.4度的粉煤,在80mm宽500mm长600mm高的煤斗中以每分钟20mm速度下移无阻滞、架桥现象。
煤流在炉中从a模块流动到b模块,从a模块的两个u形列管之间240mm煤流的两边上30mm的煤得到了加热,当流动到b模块时有二个边上的30mm的热煤流动到下一个240mm煤流的中间,此60mm的热煤流在b模块中也成热源可对旁边的煤热扩散,同时a模块240mm煤流中间的冷煤流动到b模块列管边上得到加热,再流动到下一模块煤流内外又得到交换;使列管与煤的温差变大,且内外煤得到升温后粉煤的导热系数得到了提高,传热加快,加温均匀。
以上仅是本实用新型的具体应用范例,对本实用新型的保护范围不构成任何限制。凡采用等同变换或者等效替换而形成的技术方案,均落在本实用新型权利保护范围之内。
本文用于企业家、创业者技术爱好者查询,结果仅供参考。