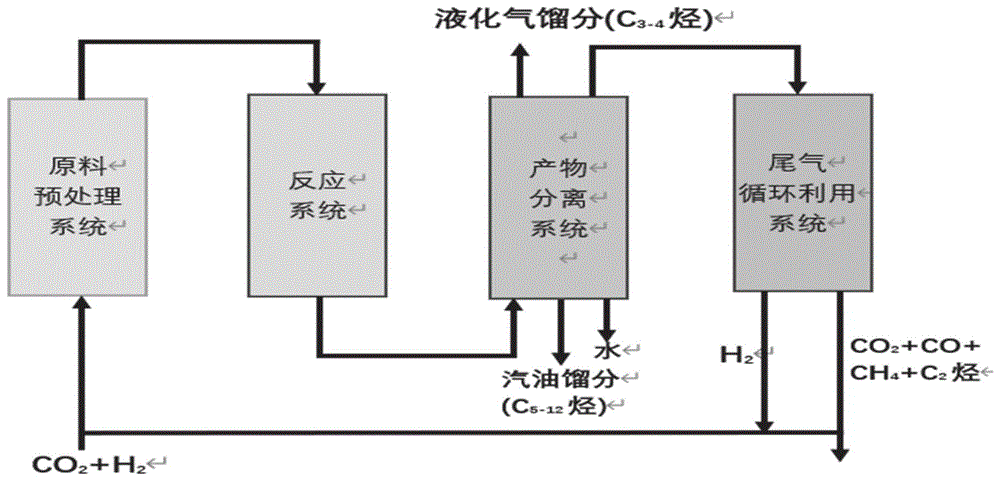
本申请涉及一种二氧化碳催化加氢制汽油的装置,属于生产汽油的化工工艺领域。
背景技术:
二氧化碳转化制液态燃料和高值化学品在我国的能源和化工领域具有潜在的重要意义,不仅有利于二氧化碳的减排,同时有利于二氧化碳的资源化有效利用。此外,借助可再生能源(水能、太阳能、风能等)电解水制得的氢,二氧化碳可转化为液态燃料和高值化学品,还可解决一直困扰可再生能源的能量储存问题,因此二氧化碳加氢制液态燃料和高值化学品过程在未来的能源体系中将扮演重要角色。众多产物中,汽油是重要的运输燃料,在世界范围内应用最为广泛,拥有最为完善的储存和运输基础设施,如能实现二氧化碳加氢制汽油的应用化,无疑对可再生能源的推广利用具有极大的推动作用。
但由于co2的化学惰性,co2加氢转化为甲烷、甲醇等低碳化合物相对容易,但是转化为含有高碳化合物则极具挑战性,因而需要开发更有效的催化剂体系。co2加氢高选择性合成汽油烃类化合物的研究可分为两类:一种是经过甲醇等含氧中间物种的反应;另一种是经过类似费托合成(fts)的反应。目前,大部分的研究工作主要采用类fts反应路径,即co2先通过逆水煤气变换(rwgs)反应生成co,然后co加氢再发生fts反应。无论哪种路径,二氧化碳的单程收率均有待进一步提高;此外,关于二氧化碳加氢制汽油过程反应装置及反应器的研究较少,由于该过程是一个快速放热反应,如何保持催化剂床层反应热的均匀分布和反应热的及时移除也是该过程走向应用亟待解决的重要问题。现有技术涉及到一种二氧化碳加氢直接制汽油的装置及方法。该装置及方法中采用了氧化铟/分子筛(in2o3/hzsm-5)双功能复合催化剂,反应器选用了外带循环换热机构的列管式合成反应器,反应器出口经多级冷却,分子筛吸附器脱水,并经气液分离后,其中的气相组分部分循环回用,部分作为驰放气外排火炬系统。该装置的特点适合in2o3/hzsm-5催化二氧化碳制汽油反应的特点,即低转化率、高汽油产品选择性、产物中水含量低。但对于催化二氧化碳加氢制汽油高转化率、高汽油产品选择性和产物高水含量的铁基/分子筛(na-fe3o4/hzsm-5)多功能复合催化剂不太合适,如反应器出口对混合气进行脱水的分子筛吸附器不适用于含有非微量水分混合气的脱水;同时,驰放气中大量未反应原料气组分直接排放,也降低了反应总转化率。因此,开发适合铁基/分子筛(na-fe3o4/hzsm-5)多功能复合催化剂分子筛特点的反应装置系统是必要的。
技术实现要素:
针对目前co2加氢制汽油反应所需装置特点,本实用新型主要适合na-fe3o4/hzsm-5催化co2加氢制汽油反应过程特点的反应装置,同时达到设计的反应装置系统具有高汽油收率、装置能耗低、经济环保等特点。
根据本申请的一个方面,提供了一种二氧化碳催化加氢制汽油的装置,该装置为各系统的有效结合运用,包括预处理单元-反应单元-反应产物分离-尾气循环利用等组成,其中预处理单元指预处理原料气co2和h2气体,使之满足铁催化剂上co2和氢气制汽油反应对气体和反应条件的要求;反应单元是指铁催化剂上进行co2转化制汽油的进行,本实用新型的反应单元包括含有换热部件的反应器等,反应器中催化剂采用多层稀释填装,达到了系统运行时反应热的均匀分布和过多反应热量地及时脱除,保证了co2加氢制汽油反应的稳定运行;产物分离单元采用传统的变压吸附分离,采用合适条件保证了汽油产物的回收;尾气循环利用单元则采用了膜分离系统,使分离出的氢气和含有co2的尾气可根据原料气循环的需要循环进原料气二次转化利用,进一步提高反应装置的转化效率。
一种二氧化碳催化加氢制汽油的装置,所述装置包括预处理单元、反应单元、产物分离单元和尾气循环利用单元;
所述预处理单元、反应单元、产物分离单元和尾气循环利用单元依次相连通。
可选地,所述反应单元为反应器;
所述反应器包括原料气分布器、第一段反应区、第二段反应区;
所述第一段反应区内放置有催化剂ⅰ,所述第二段反应区内放置有催化剂ⅱ;
所述原料气分布器位于所述第一段反应区,且与第一段反应区连通;
所述第二段反应区位于第一段反应区下部,且相互连通。
可选地,所述原料气分布器的根数为1~100,优化为1~50,最优为1~10。如果反应器与分布器差别很大的情况下,有可能装更多分布器,极端情况下,可能达到100根或更多,在应用过程中,根据实际情况相应的调整即可。
可选地,所述原料气分布器包括壳体ⅰ,所述壳体ⅰ围合成柱状的空腔;
所述壳体沿轴向设有多个气孔组;
每个所述气孔组中均含有沿周向设置的多个排出气孔;
相邻两个所述气孔组之间的间距沿轴向从上至下按照预设方式ⅰ设置;
相邻两个所述气孔组中的所述排出气孔的孔径,也沿轴向从上至下按照预设方式ⅱ设置。
可选地,所述预设方式ⅰ为逐渐增大;或者,
所述预设方式ⅰ为逐渐增大再保持不变。
可选地,所述预设方式ⅱ为逐渐减小;或者,
所述预设方式ⅱ为逐渐减小再保持不变。
可选地,所述预设方式ⅱ为不变而后逐渐减小;或者,
所述预设方式ⅱ为逐渐减小再保持不变后再减小。
可选地,所述相邻两个所述气孔组之间的间距为n,相邻所述间距的差为δn;
其中,0≤δn/n≤5;
可选地,0≤δn/n≤3。
可选地,0.2≤δn/n≤1。
可选地,每排的出气孔上下错开。
作为一种优选的实施方式,第一排出气孔和第二排出气孔的孔径大小均为0.5mm,间距为0.5cm;第三排出气孔和第四排出气孔的孔径大小均为0.4mm,间距为1.5cm,第二排和第三排出气孔的间距为1cm;;第五排出气孔和第六排出气孔的孔径大小均为0.3mm,间距为2cm,第四排和第五排出气孔的间距为2cm。
作为一种优选的实施方式,第一排出气孔和第二排出气孔的孔径大小分别为0.7mm和0.5mm,间距为0.7cm;第三排出气孔和第四排出气孔的孔径大小均为0.4mm,间距为1.5cm,第二排和第三排出气孔的间距为1.0cm;第四排出气孔的孔径大小均为0.2mm,间距为2.0cm。
可选地,第1排出气孔离原料气分布器顶端的距离大于等于原料气分布器总长度的八分之一。
可选地,第1排出气孔离原料气分布器顶端的距离大于等于原料气分布器总长度的二分之一。
本申请中,对原料气分布器的长度,内径,以及出气孔的孔径不作严格限定,在实际使用过程中,根据具体选择的反应器的规格进行相应的匹配选择即可。
可选地,所述反应器还包括导热装置;
所述导热装置的入口连接于第一段反应区;
所述导热装置的出口连接于第二段反应区。
可选地,所述导热装置为含有导热油的换热系统。导热油经导热油入口进入反应器,经反应器中的导热油管线从反应的导热油管出口流出进入到导热油的换热设备,以及时脱除反应热。
本实用新型的反应单元包括含有换热部件的反应器等,反应器中催化剂采用多层稀释填装(铁催化剂稀释、分子筛催化剂组分不稀释),同时采用了含有原料分布器、导热器的反应器,达到系统运行时反应热的均匀分布和过多反应热量地及时脱除,保证了co2加氢制汽油反应的稳定运行。
传统固定反应器填装催化剂,催化剂床层极易出现床层热点,出现床层飞温现象。正常催化剂反应温度为320℃,但反应后催化剂床层出现热点温度,且迅速(2小时内)升温至500℃以上,不仅使反应无法进行,而且破坏了催化剂结构,严重影响了催化剂的反应性能。而采用本实用新型设计的反应器,催化剂的床层温度基本控制在320℃左右,且催化剂床层热点不明显,不超过350℃,反应可稳定运行近千小时。
可选地,所述产物分离单元包括变压吸附分离装置。产物分离系统中含有二级脱轻塔,其主要功能是保证了主要烃类副产物液化石油气的分离提纯,增加了该过程的产品附加值和过程的经济性。
可选地,所述变压吸附分离装置包括高压分离罐、产物分离罐、脱轻塔i和脱轻塔ii;
所述高压分离罐、产物分离罐、脱轻塔i和脱轻塔ii依次连通。
可选地,所述高压分离罐、产物分离罐、脱轻塔i和脱轻塔ii各自之间连接有减压阀。
可选地,所述高压分离罐分离出气体部分和液体部分,液体部分经产物分离罐分离出轻烃气体、液态油和废水;液态油经脱轻塔i分离得到汽油,经脱轻塔ii分离得到液化石油气。
可选地,脱轻塔i后连接有产品输送泵i,脱轻塔ii后连接有产品输送泵ii。
可选地,所述高压分离罐前设置有热交换器和冷却器。
具体地,产物分离单元采用传统的变压吸附分离,采用合适条件保证了汽油产物的回收。包括:001.热交换器和冷却器,002.高压分离罐,003.减压阀i,004.减压阀ii;005.产物分离罐,006.减压阀iii,007.脱轻塔i,008.脱轻塔ii,009.产品输送泵i,010.产品输送泵ii,011.减压阀iv,012.减压阀v,013.减压阀vi.该系统中,反应器出口气流经热交换器和冷却器001进行降温处理后,冷的气体(-30-10℃)进入高压分离罐002后,得到气体和液体,其中气体部分经减压阀ii004后进入尾气循环利用系统,液体经减压阀i003后进入产物分离罐005,产物分离罐压力0.5-2.5mpa,分离出的少量轻烃气体经减压阀iii006后进入尾气循环系统;分离出的液态油经减压阀iv011减压,送下游脱轻塔i007进一步精馏提纯;分离出的液态水连续外排;脱轻塔i007的顶部气相管道的气体经减压阀v012进入脱轻塔ii008,脱轻塔i007的底部液相出口管道连通着产品输送泵009进口,产品输送泵009出口管道外送合格汽油产品;脱轻塔ii008的顶部气相管道的气体经减压阀v013进入尾气利用系统,底部液相出口管道连通着产品输送泵010进口,产品输送泵010出口管道外送合格高值副产品液化石油气。
具体地,热交换器和冷却器与高压分离罐相连,高压分离罐一端经减压阀排出尾气,一端经减压阀和产物分离罐相连;产物分离罐一端经减压阀排出尾气,一端排出废水,一端经减压阀和脱轻塔i相连;脱轻塔i一端经产品输送泵i输送出汽油,一端经减压阀和脱轻塔ii相连;脱轻塔ii一端经产品输送泵ii输送出液化石油气,一端经减压阀排出废气。
可选地,所述尾气循环利用单元包括膜分离系统;
所述膜分离系统包括透氢膜分离系统和/或透co2膜分离系统。
尾气循环利用单元采用了膜分离器和催化燃烧器,其目的是保证了含碳尾气的全部循环利用,既增强了过程的环保性能,又提高了过程的资源利用率。
可选地,所述透氢膜分离系统包括透氢膜分离器和催化燃烧器;
所述催化燃烧器设置在透氢膜分离器后面,以使透氢膜分离器分离出氢气后的气体催化燃烧得到二氧化碳。
可选地,所述催化燃烧器后设置有热交换器和冷凝器,热交换器和冷凝器后设置有气液分离器。
可选地,所述透co2膜分离系统将尾气分离出二氧化碳和透co2膜分离尾气。
可选地,所述透氢膜分离系统和透co2膜分离系统同时存在时,透氢膜分离系统设置在透co2膜分离系统之后。
可选地,所述透氢膜分离系统选自有机透氢膜分离系统、透氢钯膜分离系统中的一种。
可选地,所述透氢膜分离系统选自低温有机透氢膜分离系统、高温透氢钯膜分离系统中的一种。
本申请中,采用透氢膜分离系统以实现将尾气分离出氢气,采用透co2膜分离系统以实现将尾气分离出co2。在具体的实际应用场景中,可根据实际情况选择相应的透氢膜和透co2膜组件。
可选地,所述膜分离系统前设置有热交换器和预热器。
具体地,尾气循环利用单元则采用了膜分离系统,使分离出的氢气和含有co2的尾气可根据原料气循环的需要循环进原料气二次转化利用,进一步提高反应装置的转化效率。包括:a01.热交换器和预热器,a02.膜分离器,a03.催化燃烧器,a04.热交换器和冷凝器,a05.气液分离器,a06.流量调节阀i,a07.流量调节阀ii,a08.汇总连接器。该系统中,从产物分离系统流入的尾气经热交换器和预热器a01进入膜分离系统a02,膜分离系统a02渗透侧的氢气可根据循环需要经流量调节阀ia06、汇总连接器a08循环进新鲜原料气进行原料气二次利用。膜分离尾气流入催化燃烧器a03,催化燃烧器中尾气中的还原性气体低碳烃、co均完全燃烧生成二氧化碳和水,与尾气中含有的co2经热交换器和冷凝器a04后,进入a05气液分离器,分离出的液态水连续外排,而气体二氧化碳则可根据循环需要经流量调节阀iia07、汇总连接器a08循环进新鲜原料气进行原料气二次利用。
具体地,热交换器和预热器与透氢膜分离器相连;一端分离出氢气,一端和催化燃烧器相连,催化燃烧器后连接有热交换器和冷凝器,热交换器和冷凝器后连接有气液分离器,气液分离器一端排出废水,一端得到二氧化碳,氢气和二氧化碳各自经流量调节阀经过汇总连接器得到新鲜原料气。
具体地,热交换器和预热器与透二氧化碳膜分离器相连;一端分离出二氧化碳,一端分离出氢气、一氧化碳和低碳烃,二氧化碳和氢气各自经流量调节阀经过汇总连接器得到新鲜原料气。
具体地,热交换器和预热器与透二氧化碳膜分离器相连,一端分离出二氧化碳,一端与透氢膜分离器相连;透氢膜分离器一端分离出氢气,一端和催化燃烧器相连,催化燃烧器后连接有热交换器和冷凝器,热交换器和冷凝器后连接有气液分离器,气液分离器一端排出废水,一端得到二氧化碳;透二氧化碳膜分离器分离出的二氧化碳、透氢膜分离器分离出的氢气和气液分离器分离得到的二氧化碳各自经流量调节阀经过汇总连接器得到新鲜原料气。
可选地,所述预处理单元包括干燥器、脱氧器和热交换器;
所述干燥器、脱氧器和热交换器依次连通。
可选地,所述脱氧器和热交换器之间依次设置有压缩机,截止阀,流量计。
可选地,所述预处理单元还包括催化剂的气体预处理部分;包括干燥器、脱氧器;该部分通过截止阀连接与汇总连接器。
本申请的预处理单元具有双重功能,一是对催化剂的还原处理;二是对原料的预处理。具体操作中,可以通过对气体的切换来实现。
具体地,预处理气(氢气或含有氢气的气体)经干燥器4脱除预处理气的微量水、脱氧器6脱除预处理气的微量氧,依次经流量计8、截止阀11、汇总连接器12、热交换器13预热后定量进入反应系统14进行催化剂的常压预处理;催化剂预处理完毕后,切换原料气开始反应。
具体地,预处理系统指预处理原料气co2和h2气体,使之满足铁催化剂上co2和氢气制汽油反应对气体和反应条件的要求;该系统包括:1.原料气出口,2.预处理气出口,3.干燥器,4.干燥器,5.脱氧器,6.脱氧器,7.压缩机,8.流量计,9.截止阀,10.流量计,11.截止阀,12.汇总连接器。在该系统中,催化剂体系进行反应前,需要进行还原预处理,此时预处理气出口2流入的预处理气(氢气或含有氢气的气体)经干燥器4脱除预处理气的微量水、脱氧器6脱除预处理气的微量氧,依次经流量计8、截止阀11、汇总连接器12、热交换器13预热后定量进入反应系统14进行催化剂的常压预处理;催化剂预处理完毕后,切换原料气开始反应:原料气出口1流入的原料气(含有氢气、二氧化碳等原料的气体)经干燥器3脱除原料气的微量水、脱氧器5脱除原料气的微量氧,依次经压缩机7、截止阀9、流量计10、汇总连接器12、热交换器13预热后定量进入高压反应系统14进行催化剂的高压反应。
具体地,原料气出口和干燥器相连,干燥器和脱氧器相连,脱氧器后依次连接有压缩机,截止阀,流量计。
具体地,预处理气出口和干燥器相连,干燥器和脱氧器相连,脱氧器后依次连接有流量计,截止阀。
具体地,原料气和预处理气最终通过汇总连接器,汇总连接器后连接有热交换器(预热器)通向反应系统。
本实用新型的二氧化碳加氢直接制汽油装置包括预处理单元-反应单元-反应产物分离-尾气循环利用等组成。其中,
预处理单元指预处理原料气co2和h2气体,使之满足铁催化剂上co2和氢气制汽油反应对气体和反应条件的要求;该系统包括原料气净化系统(脱水管、脱氧管),压缩机、换热器和加热器。
反应单元是指铁催化剂上进行co2转化制汽油的进行,本实用新型的反应系统包括含有换热部件的反应器等,反应器中催化剂采用多层稀释填装,达到了系统运行时反应热的均匀分布和过多反应热量地及时脱除,保证了co2加氢制汽油反应的稳定运行。
产物分离单元采用传统的变压吸附分离,采用合适条件保证了汽油产物的回收。
尾气循环利用单元则采用了高温透氢膜,使分离出的氢气和含有co2的尾气可根据原料气循环的需要循环进原料气二次转化利用,进一步提高反应装置的转化效率。
采用上述装置进行二氧化碳催化加氢制备汽油的方法,包括以下步骤:
(a)将含有co2和h2的原料气经预处理单元处理,得到预处理的物料;
(b)将所述预处理的物料在反应单元中进行催化反应,得到物流i;
(c)将所述的物流i在产物分离单元进行分离,分离出尾气、废水,得到液化石油气和汽油;
(d)将所述尾气经尾气循环利用单元处理得到新鲜原料气;
所述制备汽油的方法采用上述所述的装置中的一种。
步骤(b)中,催化反应分两段进行。即催化剂分两段填装。第一段反应区装填有铁基催化剂。第一段反应区为入口段,在该催化剂上发生的是二氧化碳加氢经co合成低碳烯烃的过程,该段总包反应为强放热反应。
第二段反应区装填有酸性分子筛催化剂。第二段反应区为出口段,该段催化剂上发生的是中间产物低碳烯烃聚合、加氢、异构、芳构化生成汽油馏分烃过程,该段总包反应为温和的放热反应。
本申请中,催化剂分多段段填装,铁基催化剂填装于原料气入口段,可根据实际情况,分一段和多段填装;分子筛催化剂填装于反应器原料气出口段,可根据实际情况,分一段或多段填装。
本申请中,采用原料分布器进料,根据反应器管径调整原料分布器的根数(1-3根),不仅使得反应器催化剂1床层段的轴向进料分布均衡,同时使得催化剂1床层段的径向进料分布均匀。同时结合导热系统,可使反应器的反应热,特别是铁基催化剂上的反应热能够及时均匀移除,提高系统的稳定操作运行。
具体地,在铁催化剂上进行co2转化制汽油的进行,本实用新型的反应单元包括含有换热部件的反应器等,反应器中催化剂采用多层稀释填装(铁催化剂稀释、分子筛催化剂组分不稀释),同时采用了含有原料分布器、导热器的反应器,达到系统运行时反应热的均匀分布和过多反应热量地及时脱除,保证了co2加氢制汽油反应的稳定运行。经预处理单元处理后的原料气经原料分布器进入反应器进入催化剂1(na-fe3o4)床层,而后再流入催化剂2(hzsm-5)床层,反应后的含有汽油产物的气体流出反应气进入产物分离系统。反应运行时同时启动反应装置的含有导热油的换热系统(导热油经导热油入口进入反应器,经反应器中的导热油管线从反应的导热油管出口流出进入到导热油的换热设备)以及时脱除反应热。值得注意的是,分布器进入的原料气仅在催化剂1床层中分布流出,反应后再进入催化剂2床层。
步骤(c)中,高压分离罐压力为1.0~5.0mpa;产物分离罐压力0.5-2.5mpa;脱轻塔i的压力为0.3-2.0mpa;脱轻塔ii的压力为0.3-1.0mpa;
物流i在高压分离罐分离得到气体部分和液体部分,气体部分进入尾气循环利用单元;
液体部分经产物分离罐分离出轻烃气体、液态油和废水,轻烃气体进入尾气循环利用单元,废水排出;
液态油经经脱轻塔i分离得到汽油,经脱轻塔ii分离得到液化石油气。
步骤(d)中,尾气经透氢膜分离系统分离得到氢气和透氢膜膜分离尾气,透氢膜膜分离尾气经催化燃烧得到二氧化碳,氢气和二氧化碳混合后二次利用。
步骤(d)中,尾气经透co2膜分离系统分离得到co2和透co2膜分离尾气。
步骤(d)中,透co2膜分离尾气再次经透氢膜分离系统分离得到氢气和和透氢膜膜分离尾气,透氢膜膜分离尾气经催化燃烧得到二氧化碳,氢气和二氧化碳混合后二次利用。
本申请能产生的有益效果包括:
1)本申请实现了铁基催化剂上二氧化碳直接加氢高效转化制汽油,汽油收率明显高于已有二氧化碳加氢制汽油装置。反应系统同时采用含有原料分布器、导热器的反应器,且原料分布器的出气口在多段催化剂的第一床层段分布,保证了反应热不仅在催化剂床层的均匀分布,而且可均匀移除,保证了反应的稳定进行。
2)本申请提供的二氧化碳加氢反应装置与汽油产品分离纯化集一体,在保证反应原料气有效循环利用的同时,降低了反应装置和分离装置的能耗,进而降低了二氧化碳制汽油的生产成本。
3)本申请的尾气循环利用系统采用了膜分离器和催化燃烧器,可大幅度减少外排的废气,不仅充分利用了二氧化碳资源,同时大幅度降低了排放尾气对环境的影响。
4)本申请的产物分离系统除生产合格的汽油产品外,同时副产合格的高值副产品液化石油气,提高了系统的碳资源利用率。
5)本申请的二氧化碳加氢制汽油装置各系统的有效结合运用,可使得本过程的碳资源利用率明显提高,二氧化碳资源的利用率可达到80%以上,甚至90%以上,本过程几乎无废气排放,明显提高了过程的环保性。同时,本实用新型采用的反应系统,保证了整个系统的稳定运行。
附图说明
图1为二氧化碳催化加氢制汽油的反应装置系统示意图。
图2为催化加氢制汽油预处理系统装置示意图。
图3为二氧化碳催化加氢制汽油反应系统示意图。
图4为二氧化碳催化加氢制汽油反应系统原料气分布器示意图。
图5为二氧化碳催化加氢制汽油产物分离系统示意图。
图6为二氧化碳催化加氢制汽油尾气循环利用示意图。
图7为二氧化碳催化加氢制汽油含有二氧化碳分离膜尾气循环利用示意图。
图8为二氧化碳催化加氢制汽油同时含有透氢膜和二氧化碳分离膜尾气循环利用示意图。
图2中,1.原料气出口2.预处理气出口3.干燥器
4.干燥器5.脱氧器6.脱氧器
7.压缩机8.流量计9.截止阀
10.流量计11.截止阀12.汇总连接器
13.热交换器(预热器)14反应系统
图5中,001.热交换器和冷却器002.高压分离罐
003.减压阀i004.减压阀ii
005.产物分离罐006.减压阀iii
007.脱轻塔i008.脱轻塔ii
009.产品输送泵i010.产品输送泵ii
011.减压阀iv012.减压阀v
013.减压阀vi
图6中,a01.热交换器和预热器a02.膜分离器
a03.催化燃烧器a04.热交换器和冷凝器
a05.气液分离器a06.流量调节阀i
a07.流量调节阀iia08.汇总连接器
图7中,b01.热交换器和预热器b02.膜分离器
b03.流量调节阀ib04.流量调节阀ii
b05.汇总连接器
图8中,c01.热交换器和预热器c02.二氧化碳膜分离器
c03.透氢膜分离器c04.催化燃烧器
c05.热交换器和冷凝器c05.气液分离器
c07.流量调节阀ic08.流量调节阀ii
c09.汇总连接器c10.流量调节阀iii
具体实施方式
下面结合实施例详述本申请,但本申请并不局限于这些实施例。
如无特别说明,本申请的实施例中的原料和催化剂均通过商业途径购买。如无特别说明,测试方法均采用常规方法,仪器设置均采用厂家推荐的设置。
其中,铁基催化剂选用na-fe3o4,来自中国科学院大连化学物理研究所。
hzsm-5购自南开大学催化剂厂,硅铝比为25~400。
透氢膜分离系统来自中国科学院大连化学物理研究所,其透氢膜的主要组件为金属钯透氢膜核心组件。
透二氧化碳膜分离系统来自中国科学院大连化学物理研究所,其二氧化碳膜分离系统的主要组件为分子筛复合膜分离系统。
反应物co2的转化率和汽油产品收率计算公式如下:
co2的单程转化率(%)=co2转化摩尔数/co2进料摩尔数х100%
汽油产品单程收率(mg汽油·g催化剂-1·h-1)=原料体积空速(ml·g催化剂-1·h-1)×原料中co2体积百分数(%)×co2转化率(%)×汽油产品选择性(%)/22400×汽油摩尔质量(mg/mol)
co2的循环利用率(%)=co2循环转化为烃类燃料的摩尔数/co2循环转化的摩尔数х100%
附图1为二氧化碳加氢直接制汽油馏分烃的装置,包括预处理系统、反应系统、反应产物分离系统和尾气循环利用系统四部分组成;其中,
预处理系统(附图2)包括:1.原料气出口,2.预处理气出口,3.干燥器,4.干燥器,5.脱氧器,6.脱氧器,7.压缩机,8.流量计,9.截止阀,10.流量计,11.截止阀,12.汇总连接器。在该系统中,催化剂体系进行反应前,需要进行还原预处理,此时预处理气出口2流入的预处理气(氢气或含有氢气的气体)经干燥器4脱除预处理气的微量水、脱氧器6脱除预处理气的微量氧,依次经流量计8、截止阀11、汇总连接器12、热交换器13预热后定量进入反应系统14进行催化剂的常压预处理;催化剂预处理完毕后,切换原料气开始反应:原料气出口1流入的原料气(含有氢气、二氧化碳等原料的气体)经干燥器3脱除原料气的微量水、脱氧器5脱除原料气的微量氧,依次经压缩机7、截止阀9、流量计10、汇总连接器12、热交换器13预热后定量进入高压反应系统14进行催化剂的高压反应。
反应系统(附图3)包括含有换热部件的反应器等,反应器中催化剂采用多层稀释填装(铁催化剂稀释、分子筛催化剂组分不稀释),同时采用了含有原料分布器(附图4)、导热器的反应器。该系统中,经预处理系统处理后的原料气经原料分布器进入反应器进入催化剂1(na-fe3o4)床层,而后再流入催化剂2(hzsm-5)床层,反应后的含有汽油产物的气体流出反应气进入产物分离系统。反应运行时同时启动反应装置的含有导热油的换热系统(导热油经导热油入口进入反应器,经反应器中的导热油管线从反应的导热油管出口流出进入到导热油的换热设备)以及时脱除反应热。值得注意的是,分布器进入的原料气仅在催化剂1床层中分布流出,反应后再进入催化剂2床层。
如图4所示,为原料分布器的示意图,采用φ12不锈钢管,沿轴向设置有6排出气孔组,每排8个孔,每排的孔上下错开,第一排出气孔组离原料气分布器顶端的距离为原料气分布器总长度的四分之三。第一排和第二排出气孔的孔径为0.5mm,第三排和第四排出气孔的孔径为0.4mm,第五排和第六排出气孔的孔径为0.3mm,第一排出气孔组到第六排出气孔组各排出气孔组的间距依次为0.5cm、1cm、1.5cm、2cm、2cm,其中,第六排出气孔组离底端的距离为0.7cm。
如图3所示,为二氧化碳加氢制汽油的反应器的示意图,管状壳体自上而下分为第一段反应区、第二段反应区、出口段区,第一段反应区内放置有催化剂1,第二段反应区内放置有催化剂2;导热油入口和第一段反应区上部相连,导热油出口和反应器底部相连;原料气分布器位于所述第一段反应区上部,且与第一段反应区连通。
产物分离系统(附图5)包括:001.热交换器和冷却器,002.高压分离罐,003.减压阀i,004.减压阀ii;005.产物分离罐,006.减压阀iii,007.脱轻塔i,008.脱轻塔ii,009.产品输送泵i,010.产品输送泵ii,011.减压阀iv,012.减压阀v,013.减压阀vi.该系统中,反应器出口气流经热交换器和冷却器001进行降温处理后,进入高压分离罐002后,得到气体和液体,其中气体部分经减压阀ii004后进入尾气循环利用系统,液体经减压阀i003后进入产物分离罐005,产物分离罐压力0.5-2.5mpa,分离出的少量轻烃气体经减压阀iii006后进入尾气循环系统;分离出的液态油经减压阀iv011减压,送下游脱轻塔i007进一步精馏提纯;分离出的液态水连续外排;脱轻塔i007的顶部气相管道的气体经减压阀v012进入脱轻塔ii008,脱轻塔i007的底部液相出口管道连通着产品输送泵009进口,产品输送泵009出口管道外送合格汽油产品;脱轻塔ii008的顶部气相管道的气体经减压阀v013进入尾气利用系统,底部液相出口管道连通着产品输送泵010进口,产品输送泵010出口管道外送合格高值副产品液化石油气。
尾气循环利用系统(附图6)包括:a01.热交换器和预热器,a02.膜分离器,a03.催化燃烧器,a04.热交换器和冷凝器,a05.气液分离器,a06.流量调节阀i,a07.流量调节阀ii,a08.汇总连接器。该系统中,从产物分离系统流入的尾气经热交换器和预热器a01进入膜分离系统a02,膜分离系统a02渗透侧的氢气可根据循环需要经流量调节阀ia06、汇总连接器a08循环进新鲜原料气进行原料气二次利用。膜分离尾气流入催化燃烧器a03,催化燃烧器中尾气中的还原性气体低碳烃、co均完全燃烧生成二氧化碳和水,与尾气中含有的co2经热交换器和冷凝器a04后,进入a05气液分离器,分离出的液态水连续外排,而气体二氧化碳则可根据循环需要经流量调节阀iia07、汇总连接器a08循环进新鲜原料气进行原料气二次利用。
图7为二氧化碳催化加氢制汽油含有二氧化碳分离膜尾气循环利用示意图。该示意图中,从产物分离系统流入的尾气经热交换器和预热器b01进入膜分离系统b02,膜分离系统b02渗透侧的二氧化碳可根据循环需要经流量调节阀ib04、汇总连接器b05循环进新鲜原料气进行原料气二次利用。膜分离尾气则可根据循环需要经流量调节阀iib03、汇总连接器b05循环进新鲜原料气进行原料气二次利用。
图8为二氧化碳催化加氢制汽油同时含有透氢膜和二氧化碳分离膜尾气循环利用示意图。包括:c01.热交换器和预热器,c02.二氧化碳膜分离器,c03.透氢膜分离器;c04.催化燃烧器,c05.热交换器和冷凝器,c05.气液分离器,c07.流量调节阀i,c08.流量调节阀ii,c09.汇总连接器,c10.流量调节阀iii.该系统中,来自产物分离系统流入的尾气经热交换器和预热器c01进入二氧化碳膜分离系统c02,膜分离系统c02渗透侧的二氧化碳可根据循环需要经流量调节阀iic08、汇总连接器c09循环进新鲜原料气进行原料气二次利用。二氧化碳膜分离系统的尾气则进入透氢膜分离器c03,透氢膜分离器c03渗透侧的氢气可根据循环需要经流量调节阀iiic10、汇总连接器c09循环进新鲜原料气进行原料气二次利用。透氢膜分离器的尾气流入催化燃烧器c04,催化燃烧器c04中尾气中的还原性气体低碳烃、co均完全燃烧生成二氧化碳和水,经热交换器和冷凝器c05后,进入c06气液分离器,分离出的液态水连续外排,而气体二氧化碳则可根据循环需要经流量调节阀ic07、汇总连接器c09循环进新鲜原料气进行原料气二次利用。
二氧化碳加氢直接制汽油馏分烃方法具体包括以下操作步骤:
步骤(1)催化剂进行还原预处理;预处理气出口2流入的预处理气(氢10%h2/n2)经干燥器4室温脱水、脱氧器6室温脱氧,依次经流量计8、截止阀11、汇总连接器12、热交换器13预热(230-350℃)后定量进入反应系统14进行催化剂的常压280-500℃还原预处理.
步骤(2)通入温度为10~50℃,压力为1.0~6.0mpa的新鲜原料气;
原料气出口1流入温度为5~45℃的原料气(含有氢气、二氧化碳等原料的气体)经干燥器4室温脱水、脱氧器6室温脱氧,依次经压缩机7(压缩压力为1.0~6.0mpa)、截止阀9、流量计10、汇总连接器12、热交换器13预热(230-350℃)后定量进入高压反应系统14进行催化剂的高压反应。
步骤(3)进入反应系统的高温高压反应气在本实用新型设计的反应器内进行反应,得到反应混合气,反应温度为250~450℃,压力为1.0~6.0mpa,总反应方程通式为:
nco2 (n~6n)h2=n1co n2ch4 (n3c2~n5c4) (n6c5~n12c11) n13h2o,反应催化剂为铁基/分子筛(na-fe3o4/hzsm-5)多功能复合催化剂;
步骤(4)反应器出口气流经热交换器和冷却器001进行降温处理后得到降温并部分冷凝后的低温混合气/液,低温混合气/液温度为-30~10℃;
步骤(5)低温混合气/液经高压分离罐002分离得到气体和液体,高压分离罐002压力为1.0~5.0mpa;其中气体部分经减压阀ii004减压后进入尾气循环利用系统,循环气温度为15-60℃,压力为0.2-2.0mpa。液体经减压阀i003后进入产物分离罐005,产物分离罐压力0.5-2.5mpa,分离出的少量轻烃气体经减压阀iii006后进入尾气循环系统;分离出的液态油经减压阀iv011减压,送下游脱轻塔i007进一步精馏提纯,脱轻塔i007的压力为0.3-2.0mpa;分离出的液态水连续外排;脱轻塔i007的顶部气相管道的气体经减压阀v012进入脱轻塔ii008,脱轻塔ii008的压力为0.3-1.0mpa。脱轻塔i007的底部液相出口管道连通着产品输送泵009进口,产品输送泵009出口管道外送合格汽油产品;脱轻塔ii008的顶部气相管道的气体经减压阀v013进入尾气利用系统,底部液相出口管道连通着产品输送泵010进口,产品输送泵010出口管道外送合格高值副产品液化石油气。
步骤(6)从产物分离系统流入的尾气经热交换器和预热器a01(50-400℃)进入膜分离系统a02(320-380℃),膜分离系统a02渗透侧的氢气可根据循环需要经流量调节阀ia06、汇总连接器a08循环进新鲜原料气进行原料气二次利用。膜分离尾气流入催化燃烧器a03(室温-500℃),催化燃烧器中尾气中的还原性气体低碳烃、co均完全燃烧生成二氧化碳和水,与尾气中含有的co2经热交换器和冷凝器a04后,进入a05气液分离器,分离出的液态水连续外排,而气体二氧化碳则可根据循环需要经流量调节阀iia07、汇总连接器a08循环进新鲜原料气进行原料气二次利用。
实施例1
原料气分布器采用如图4所示的原料气分布器,采用φ12不锈钢管,每排8个孔共6排孔,每排上下错开,具体孔径和间距如图4所示。本实施例中放置1根原料气分布器。
二氧化碳加氢直接制汽油馏分烃方法具体包括以下操作步骤:
步骤(1)催化剂进行还原预处理;预处理气出口2流入的预处理气(10vol%h2/n2)经干燥器4室温脱水、脱氧器6室温脱氧,依次经流量计8、截止阀11、汇总连接器12、热交换器13预热(260℃)后定量(3000ml·gcat-1·h-1)进入反应系统14进行催化剂的常压(0.1mpa)350℃还原预处理6h。
步骤(2)通入新鲜原料气;
原料气出口1流入温度为50℃的原料气(含有氢气、二氧化碳、氮气原料的气体,h2/co2体积比=3)经干燥器4室温脱水、脱氧器6室温脱氧,依次经压缩机7(压缩压力为3.5mpa)、截止阀9、流量计10、汇总连接器12、热交换器13预热(260℃)后定量(3000ml·gcat-1·h-1)进入高压反应系统14进行催化剂的高压反应。
步骤(3)进入反应系统的高温高压反应气在本实用新型设计的反应器内进行反应,得到反应混合气,反应温度为320℃,压力为3.0mpa,空速为4000ml·g催化剂-1·h-1。
催化剂i为铁基催化剂,选用na-fe3o4,用量20g,催化剂ii为酸性分子筛,铁基催化剂与酸性分子筛质量比例为1/2,酸性分子筛选用hzsm-5(硅铝比为200)。换热系统中的换热介质采用导热油。
步骤(4)反应器出口气流经热交换器和冷却器001进行降温处理后得到降温并部分冷凝后的低温混合气/液,低温混合气/液温度为5℃;
步骤(5)低温混合气/液经高压分离罐002分离得到气体和液体,高压分离罐002压力为3.0mpa;其中气体部分经减压阀ii004减压后进入尾气循环利用系统,循环气温度为20℃,压力为0.5mpa。液体经减压阀i003后进入产物分离罐005,产物分离罐压力1.5mpa,分离出的少量轻烃气体经减压阀iii006后进入尾气循环系统;分离出的液态油经减压阀iv011减压,送下游脱轻塔i007进一步精馏提纯,脱轻塔i007的压力为0.5mpa;分离出的液态水连续外排;脱轻塔i007的顶部气相管道的气体经减压阀v012进入脱轻塔ii008,脱轻塔ii008的压力为0.3mpa。脱轻塔i007的底部液相出口管道连通着产品输送泵009进口,产品输送泵009出口管道外送合格汽油产品;脱轻塔ii008的顶部气相管道的气体经减压阀v013进入尾气利用系统,底部液相出口管道连通着产品输送泵010进口,产品输送泵010出口管道外送合格高值副产品液化石油气。
步骤(6)从产物分离系统流入的尾气经热交换器和预热器a01(350℃)进入膜分离系统a02(350℃),a02为高温透氢钯膜分离系统,膜分离系统a02渗透侧的氢气可根据循环需要经流量调节阀ia06、汇总连接器a08循环进新鲜原料气进行原料气二次利用。膜分离尾气流入催化燃烧器a03(300℃),催化燃烧器中尾气中的还原性气体低碳烃、co均完全燃烧生成二氧化碳和水,与尾气中含有的co2经热交换器和冷凝器a04后,进入a05气液分离器,分离出的液态水连续外排,而气体二氧化碳则可根据循环需要经流量调节阀iia07、汇总连接器a08循环进新鲜原料气进行原料气二次利用。
co2的单程转化率为30%,汽油产品单程收率为105mg汽油·g催化剂-1·h-1,co2的循环利用率为85%。
实施例2
同实施例1,只是将尾气循环利用系统改为含有二氧化碳分离膜尾气循环利用系统(附图7)。co2的单程转化率为28%,汽油产品单程收率为95mg汽油·g催化剂-1·h-1,co2的循环利用率为87%。
实施例3
同实施例1,只是将尾气循环利用系统改为同时含有透氢膜(采用高温透氢钯膜分离系统)和二氧化碳分离膜尾气循环利用系统(附图8)。co2的转化率为31%,汽油产品收率为106mg汽油·g催化剂-1·h-1,co2的循环利用率为91%。
对比例1
同实施例1,只是反应系统采用了不含原料分布器和导热油的传统固定床反应器。
co2的转化率为50%,汽油产品单程收率为30mg汽油·g催化剂-1·h-1,co2的循环利用率为30%。
反应过程中的反应热致使反应器催化剂床层温度迅速升温至500℃以上,co2转化率迅速升高,但主要产物转化为甲烷和co,汽油产物的选择性迅速降低,这样测算下来co2的循环利用率大大降低。另外,由于催化剂床层的温度剧烈升高,而使催化剂的活性结构遭到破坏而致使催化剂的反应性能进一步下降,催化反应稳定性明显降低。
以上所述,仅是本申请的几个实施例,并非对本申请做任何形式的限制,虽然本申请以较佳实施例揭示如上,然而并非用以限制本申请,任何熟悉本专业的技术人员,在不脱离本申请技术方案的范围内,利用上述揭示的技术内容做出些许的变动或修饰均等同于等效实施案例,均属于技术方案范围内。
本文用于企业家、创业者技术爱好者查询,结果仅供参考。