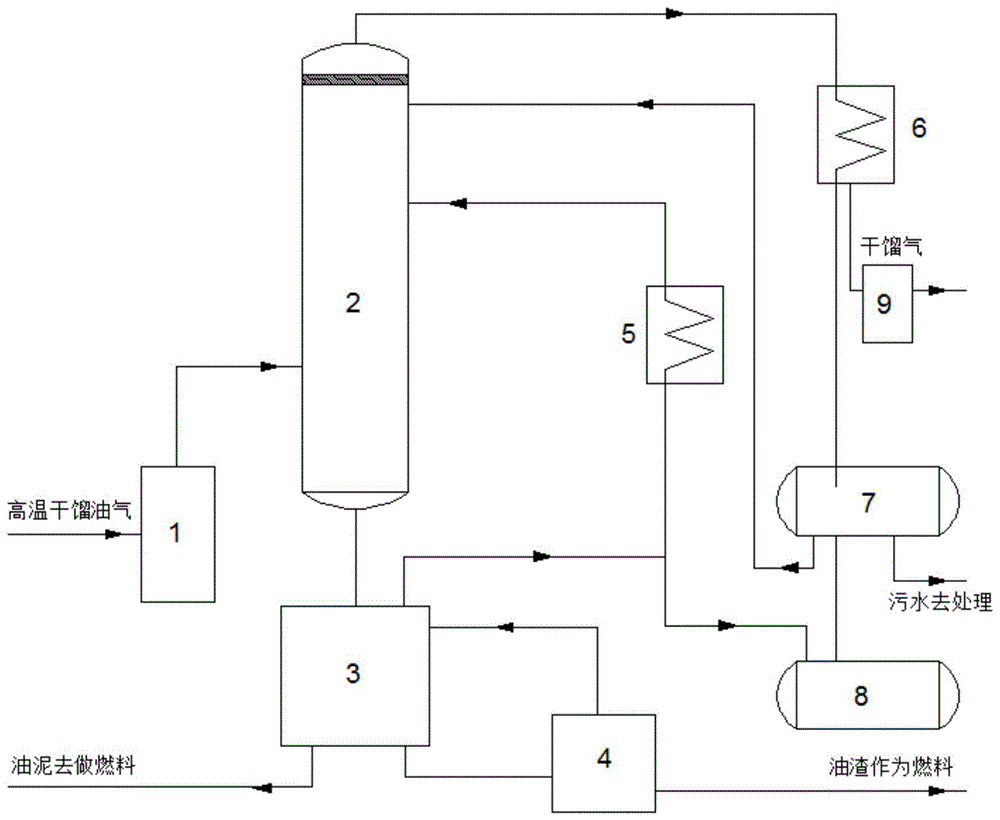
本发明属于垃圾处理领域,具体涉及一种高温垃圾干馏油气油洗分离系统及方法。
背景技术:
垃圾干馏是在无氧条件下,利用高温使生活垃圾中有机高分子的化学键发生断裂,释放出各种挥发份的反应过程,其产物为碳化物、干馏气(h2、ch4、co等)和可凝液体(焦油、水、酸等)。焦油在高温时呈气态,与干馏气完全混合,而在低温时(一般200℃以下)凝结为黏稠液态,容易与水、焦炭等结合在一起堵塞输气管道,使设备运行发生困难。
目前焦油和干馏气主要分离去处技术有水洗,干法,热裂解法,和催化裂解。
水洗法是最常见的湿法脱焦油方式包括水洗塔和湿静电除尘器。水洗塔结构简单,价格低廉,可将所有的重质焦油完全冷凝去除。但轻质焦油液滴和气态/液态烟雾能被气流带走,因此效率也最低。水洗法成本低,操作简单,但大量焦油流失,造成能量的浪费;净化过程产生废水由于会造成二次污染;如果处理废水由于含有焦油则后续处理过程繁琐,操作费用较高。所以要使水洗法脱除焦油得到更广泛的应用,必须找到适合的废水处理方法。
干法其主要是利用吸附剂的多孔特性,让燃气穿过吸附材料,或者使燃气穿过装有滤纸或陶瓷芯的过滤器,把燃气中的焦油吸附去除。可根据燃气中所含较多杂质的特点,采用多级吸附的净化方法。但实际操作净化效果不理想,主要是焦油沉积和沾附,降低脱除效率,同时沾附焦油的滤料也难以处理,所以多与其他净化装置连用。
热裂解是指在1100℃以上,通过加热断裂化学键,使大分子化合物裂解成小分子气态化合物。大量文献证明,当温度在900℃以下时,焦油的裂解率随着温度的升高而增加,在900℃时焦油的裂解率达到60%左右,只有在温度超过1100℃时,裂解率才能继续升高,最高可达99%,但过高温度对设备的要求很高、裂解能耗大、费用高,同时还容易生成焦炭。
催化裂解法是是通过催化剂降低焦油裂解的活化能,使焦油在700~900℃时裂解成小分子的碳氢化合物的裂解率达到90%以上,但是由于催化剂较贵,同时容易被干馏气中的焦油,硫等中毒,同时焦油中含有的灰尘会把催化剂床层堵住,造成系统无法正常运行,不适合大面积的工业生产。
国内外垃圾干馏油气的分离目前主要还是以水洗法为主,没有油洗相关的应用和专利,国内外油洗分离专利主要几种页油岩油气分离或者低阶煤。
专利1cn101619223b中塔底温度高控制在150-300℃,这样就存在随着装置运行时间长,细小的灰尘集聚,塔釜重组分越来越多,循环油的流动性越来越差,需要进行再生或者添加辅助轻油来改善流动性,能耗高,同时一级油洗加水冷的组合方式,也无法避免水冷工艺中多余污水排放的问题
专利2cn108753372a设置了两级油洗加两级水冷的组分分离方式,一级循环油的流动性是通过二级轻油返回与一级循环油混合来改善重油的流动性,工艺流程复杂,同时也无法避免水冷工艺中多余污水排放的问题。
专利3cn104946317a未设置精度高的除尘装置,只提到除尘效率低传统的旋风除尘方式,剩下的灰尘和半焦颗粒通过油洗过程中洗涤进入油洗塔内中,在未有很好的除尘装置的情况下,细小的灰尘集聚,塔釜重组分越来越多,循环油的流动性越来越差,同时油洗塔内设置填料段,工程上可能很快造成内件堵塞,不能实现连续运行。
本专利针对上述问题,采用直接油冷和间接水冷的工艺组合,大幅度降低了原来水洗工艺带来的大量废水,同时废水中苯、萘、酚等物质大大减少,降低污水处理难度,同时提高了干馏气中的焦油回收率。通过采用旋风预除尘与膜除尘相结合的方式,在高温状态下除去干馏油气中的灰尘,效率可达99.9%以上,是实现后续油洗分离工艺连续运行的关键技术。结合高精度的除尘技术,油洗塔塔底温度控制在100-150℃,保证循环油的流动性,与传统油洗工艺相比,无需设置中段侧采和回流,无需设置专门的减粘装置,大大降低系统能耗,简化了系统配置和操作。
技术实现要素:
本发明的目的在于:提供垃圾干馏可燃气的燃气焦油分离脱除方法,以克服上述现有技术存在的缺陷,该方法生产工艺简单,能耗小,更能避免含酚废水的污染问题,能够实现长周期稳定运行。
本发明的技术方案如下:
一种高温垃圾干馏油气油洗分离净化系统,包括高温除尘装置、急冷除油塔、急冷油循环罐、油尘分离装置、急冷油冷却器、轻油冷凝器、油水分离罐、焦油储罐、电捕焦油器;
其中,高温干馏油气由高温除尘装置进口进入,高温除尘装置的出口连接急冷除油塔的中部进口,急冷除油塔的塔釜下部出口与急冷油循环罐进口相连接;
急冷油循环罐上部出口管道分为两个支路,一个支路连接急冷油冷却器的进口,另一支路连接焦油储罐的重油进口;急冷油循环罐下部出口与油尘分离装置进口相连接;
油尘分离装置油相出口与急冷油循环罐油品补充口相连接;
油尘分离装置渣油出口连接至外部用户;
急冷油冷却器的出口与急冷油除油塔中上部的进口连接;
急冷后的干馏气由急冷除油塔塔顶送出,急冷除油塔塔顶气进口与轻油冷凝器的顶部进口连接,轻油冷凝器的塔底出口与油水分离罐的顶部进口连接;
油水分离罐的底部出口与焦油储罐的轻油进口连接;
轻油冷凝器气相出口与电捕焦油器的进口相连接。
进一步的,如上所述的一种垃圾干馏油气的分离系统,所述的高温除尘装置用于除去高温干馏油气中的灰尘颗粒,为旋风除尘加膜除尘器的组合工艺,可以实现灰尘脱除效率99.9%以上,脱除精度可以在0.5um以上。
进一步的,如上所述的一种垃圾干馏油气的分离系统,高温除尘装置外部设置蒸汽盘管,电加热,或开工过程中采用高温氮气或者高温烟气进行预热,防止大量灰尘颗粒在后续降温过程中与焦油混合,堵塞管路和设备。
进一步的,如上所述的一种垃圾干馏油气的分离系统,所述的急冷除油塔用于含油的干馏气在其内部与循环的急冷油进行气液接触,利用相似相容原理将干馏气中的重油溶于急冷油中,达到油气分离的目的;
干馏油气中带的细小灰尘在急冷洗涤过程中也随着重油进入在于急冷除油塔塔釜;轻组分沿急冷除油塔上升与来自油水分离罐的轻油进行进一步气液传质;干馏气以及轻油从急冷除油塔塔顶送出至轻油冷凝器,通过循环冷却水进行间接冷凝。
进一步的,如上所述的一种垃圾干馏油气的分离系统,所述的急冷除油塔结构为空塔结构、包含防堵内构件结构中的一种;
急冷除油塔塔顶设置高效除沫器,以除去微小油雾滴;
急冷除油塔上层布置多个环周喷嘴,保证急冷油雾化效果均匀;
急冷除油塔的塔釜设有蒸汽加热盘管或者电加热,以防止塔底重油堵塞塔体,并用于开车时将塔釜内初次充填的洗油进行加热。
进一步的,如上所述的一种垃圾干馏油气的分离系统,急冷除油塔塔底的温度控制在100~150℃,保证干馏气中的重油及轻油分被吸收至塔底,以降低后续油水分离的难度,并保证急冷油的黏度在正常操作范围内。
进一步的,如上所述的一种垃圾干馏油气的分离系统,所述急冷油循环罐,安装于急冷除油塔塔底,用于将油和泥渣进行沉降分离,沉降时间为1~2个小时,同时作为急冷油中间罐使用;
急冷油循环罐底部含固体杂质的油品定期排放送至油尘分离装置进一步分离油和油泥渣,油泥分离装置可以为三相离心机,也可为刮膜蒸发器,具体设备选型可以根据系统配套的除尘装置精度和灰尘的粒径分布来选型;
油尘分离装置分出的油泥渣送至用热设备作为燃料;
油尘分离装置分出油返回急冷油循环罐进行进一步沉降分离;
经急冷油循环罐沉降后的油品一部分作为急冷油经过急冷油冷却器降温后返回至急冷除油塔中部,循环喷淋洗涤干馏油气,防止含尘急冷油循环回急冷除油塔引起塔内堵塞结焦;另一部分油品送至焦油储罐储存;
急冷油冷却器为间接管式换热器,采用循环冷却水作为冷媒冷却急冷油,防止温度过低导致急冷油过度粘稠堵塞管道和设备,其中循环冷却水走管内,急冷油走壳程。
进一步的,如上所述的一种垃圾干馏油气的分离系统,所述的轻油冷凝器为立式管壳式换热器;
干馏油气在轻油冷凝器中通过循环冷却水进行冷凝,含轻油的干馏气走壳程,冷却水走管程;
冷凝分离出来的干馏气经过电捕焦油器捕捉干馏气中的微小油雾,以深度脱除焦油;
冷凝后的轻油和水混合物在油水分离罐内静置1~3小时后实现油水分离;
静置分离后得到的轻油一部分送至急冷除油塔的塔顶,控制急冷除油塔塔顶气体出口温度在70~90℃,且高于干馏气水露点温度,保证塔底中组分不含水。
一种利用上述的分离系统的分离方法,包括以下步骤:
步骤一,从干馏炉出来的高温干馏油气500-700℃未经任何余热回收,首先经过高温除尘装置除去干馏气中灰尘颗粒,防止大量灰尘颗粒在后续降温过程中析出焦油,吸附灰尘堵塞除尘装置以及后续系统;
步骤二,除尘后含油的干馏气从急冷除油塔中部送入塔内,循环急冷油从塔顶部喷入塔内,两种物料在塔内部进行气液直接接触,利用相似相容原理,使干馏油气中重油溶入循环急冷油中并一同进入塔釜;
循环急冷油进入塔顶的温度为60~80℃,其中干馏油气中夹带的细小灰尘也连同急冷油进入急冷除油塔塔釜;
轻组分沿急冷除油塔上升与来自油水分离罐的轻油进一步气液传质,分离后含焦油的干馏气从急冷除油塔的塔顶送出;
步骤三,控制急冷除油塔塔顶温度在70~90℃,高于干馏气水露点温度,保证干馏气中的水分呈气态随塔顶干馏气进入轻油冷凝器,实现气液分离;
控制急冷除油塔的塔底温度在100~150℃,保证干馏气中轻油吸收至塔底,同时保证急冷油的黏度在正常操作范围内,以实现急冷油的循环喷淋;
步骤四,急冷除油塔塔釜内产生的急冷油含有少量灰渣流入急冷油循环罐,通过1~2小时的沉降以后,根据油和固体杂质的密度差实现分离,急冷油循环罐罐底含固体杂质的油定期排放至油尘分离装置,分离出油泥渣;
除渣后的急冷油送入急冷油循环罐作为急冷油补充;
急冷油循环罐沉降后一部分急冷油作为循环急冷油使用,首先在急冷油冷却器内与冷却水换热后降温至60~80℃,然后返回至急冷除油塔的中上部循环喷淋洗涤来自干馏炉的高温干馏油气;另一部分急冷油送去焦油储罐储存;经过油尘分离装置分离后的油泥渣用于做燃料;
步骤五,含轻油的干馏气从急冷除油塔的塔顶出来后进入轻油冷凝器内,通过循环冷却水进行间接冷凝至40℃;
所述的轻油冷凝器,为立式管壳式换热器,含少量轻油的干馏气走壳程,冷却水走管程,冷凝后的轻油和水在油水分离罐内静置分离;分离出来的干馏气经过电捕焦油器除去油雾;
步骤六,冷凝后的轻油和水的混合物在油水分离罐内静置分离,分离后的轻油一部分送回急冷除油塔塔顶,以控制塔顶温度,其余生成的轻油送入焦油储罐储存,用于作为燃料油或者化工原料。
本发明的显著效果在于:本发明由于采用直接油冷和间接水冷的工艺组合,大幅度降低了原来水洗工艺带来的大量废水,同时废水中苯、萘、酚等物质大大减少,降低污水处理难度,同时提高了干馏气中的焦油回收率。同时避免只采用间接水冷工艺带来的焦油中的重物质在低温状态下容易造成冷凝设备严重堵塞,从而影响系统连续运行。同时本发明与传统的乙烯裂解工艺和页岩油回收油工艺相比,无需设置中段侧采和回流,无需设置专门的减粘装置,大大简化了系统配置和操作。
附图说明
图1为本发明所述的一种高温垃圾干馏油气分离系统的结构示意图;
图中:1.高温除尘装置、2.急冷除油塔、3.急冷油储存罐、4.油尘分离装置、5.急冷油换热器、6.轻油冷凝器、7.油水分离罐、8.焦油储罐、9.电捕焦油器。
具体实施方式
下面结合附图及具体实施例对本发明所述的作进一步详细说明。
如图1所示,本发明的工作原理是利用相似相溶原理,即范德华力作用,用直接油洗方法吸收干馏气中的苯、萘等较重物质,配合使用间接水冷实现轻油与干馏气的分离。
一种高温垃圾干馏油气油洗分离净化系统,包括高温除尘装置1、急冷除油塔2、急冷油循环罐3、油尘分离装置4、急冷油冷却器5、轻油冷凝器6、油水分离罐7、焦油储罐8、电捕焦油器9;
其中,高温干馏油气由高温除尘装置1进口进入,高温除尘装置1的出口连接急冷除油塔2的中部进口,急冷除油塔2的塔釜下部出口与急冷油循环罐3进口相连接;
急冷油循环罐3上部出口管道分为两个支路,一个支路连接急冷油冷却器5的进口,另一支路连接焦油储罐8的重油进口;急冷油循环罐3下部出口与油尘分离装置4进口相连接;
油尘分离装置4油相出口与急冷油循环罐3油品补充口相连接;
油尘分离装置4渣油出口连接至外部用户;
急冷油冷却器5的出口与急冷油除油塔2中上部的进口连接;
急冷后的干馏气由急冷除油塔2塔顶送出,急冷除油塔2塔顶气进口与轻油冷凝器6的顶部进口连接,轻油冷凝器6的塔底出口与油水分离罐7的顶部进口连接;
油水分离罐7的底部出口与焦油储罐8的轻油进口连接;
轻油冷凝器6气相出口与电捕焦油器9的进口相连接。
经过电捕焦油器9净化后的干馏气中焦油含量达到10mg/nm3,该干馏气暂时储存或者外运至用户作为燃料或者化工原料。
所述的高温除尘装置1用于除去高温干馏油气中的灰尘颗粒,为多级旋风组合、旋风除尘加聚结器组合中的一种。
高温除尘装置1外部设置蒸汽盘管,电加热,或开工过程中采用高温氮气或者高温烟气进行预热,防止大量灰尘颗粒在后续降温过程中与焦油混合,堵塞管路和设备。
高温除尘装置1除去高温干馏油气中的灰尘颗粒后,含尘量降至10~40mg/nm3。
所述的急冷除油塔2用于含油的干馏气在其内部与循环的急冷油进行气液接触,利用相似相容原理将干馏气中的重油溶于急冷油中,达到油气分离的目的;
干馏油气中带的细小灰尘在急冷洗涤过程中也随着重油进入在于急冷除油塔2塔釜;
轻组分沿急冷除油塔2上升与来自油水分离罐7的轻油进行进一步气液传质;
干馏气以及轻油从急冷除油塔2塔顶送出至轻油冷凝器6,通过循环冷却水进行间接冷凝。
所述的急冷除油塔2结构为空塔结构、包含防堵内构件结构中的一种;
急冷除油塔2塔顶设置高效除沫器,以除去微小颗粒;
急冷除油塔2上层布置多个环周喷嘴,保证急冷油雾化效果均匀;
急冷除油塔2的塔釜设有蒸汽加热盘管或者电加热,以防止塔底重油堵塞塔体,并用于开车时将塔釜内初次充填的洗油进行加热。
急冷除油塔2结构根据干馏气中的油品特性而定,既要保证气液充分接触,同时也要防止焦油和细小尘粒造成的塔体结焦和堵塞。
急冷除油塔2塔底的温度控制在100~150℃,保证干馏气中的重油及轻油分被吸收至塔底,以降低后续油水分离的难度,并保证急冷油的黏度在正常操作范围内。
所述急冷油循环罐3,安装于急冷除油塔2塔底,用于将油和泥渣进行沉降分离,沉降时间为1~2个小时,同时作为急冷油中间罐使用;
急冷油循环罐3底部含固体杂质的油品定期排放送至油尘分离装置4进一步分离油和油泥渣;
油尘分离装置4分出的油泥渣送至用热设备作为燃料;
油尘分离装置4分出油返回急冷油循环罐3进行进一步沉降分离;
经急冷油循环罐3沉降后的油品一部分作为急冷油经过急冷油冷却器5降温后返回至急冷除油塔2中部,循环喷淋洗涤干馏油气,防止含尘急冷油循环回急冷除油塔2引起塔内堵塞结焦;另一部分油品送至焦油储罐8储存;
急冷油冷却器5为间接管式换热器,采用循环冷却水作为冷媒冷却急冷油,防止温度过低导致急冷油过度粘稠堵塞管道和设备,其中循环冷却水走管内,急冷油走壳程。
所述的轻油冷凝器6为立式管壳式换热器;
干馏油气在轻油冷凝器6中通过循环冷却水进行冷凝,含轻油的干馏气走壳程,冷却水走管程;
冷凝分离出来的干馏气经过电捕焦油器9捕捉干馏气中的微小油雾,以深度脱除焦油;
冷凝后的轻油和水混合物在油水分离罐7内静置1~3小时后实现油水分离;
静置分离后得到的轻油一部分送至急冷除油塔2的塔顶,控制急冷除油塔2塔顶气体出口温度在70~90℃,且高于干馏气水露点温度,保证塔底中组分不含水。
一种利用如上所述的分离系统的分离方法,包括以下步骤:
步骤一,从干馏炉出来的高温干馏油气500~700℃未经任何余热回收,首先经过高温除尘装置1除去干馏气中灰尘颗粒,除尘效率可以达到99.9%,防止大量灰尘颗粒在后续降温过程中析出焦油,吸附灰尘堵塞高温除尘装置1以及后续系统;
步骤二,除尘后含油的干馏气从急冷除油塔2中部送入塔内,循环急冷油从塔顶部喷入塔内,两种物料在塔内部进行气液直接接触,利用相似相容原理,使干馏油气中重油溶入循环急冷油中并一同进入塔釜;
循环急冷油进入塔顶的温度为60~80℃;其中干馏油气中夹带的细小灰尘也连同急冷油进入急冷除油塔2塔釜;
轻组分沿急冷除油塔2上升与来自油水分离罐7的轻油进一步气液传质,分离后含焦油的干馏气从急冷除油塔2的塔顶送出;
步骤三,控制急冷除油塔2塔顶温度在70~90℃,高于干馏气水露点温度,保证干馏气中的水分呈气态随塔顶干馏气进入轻油冷凝器7,实现气液分离;
控制急冷除油塔2的塔底温度在100~150℃,保证干馏气中轻油吸收至塔底,同时保证急冷油的黏度在正常操作范围内,以实现急冷油的循环喷淋;
步骤四,急冷除油塔2塔釜内产生的急冷油含有少量灰渣流入急冷油循环罐3,通过1~2小时的沉降以后,根据油和固体杂质的密度差实现分离,急冷油循环罐3罐底含固体杂质的油定期排放至油尘分离装置4,分离出油泥渣送至外部作为燃料;
除渣后的急冷油送入急冷油循环罐3作为急冷油补充;
急冷油循环罐3沉降后一部分急冷油作为循环急冷油使用,首先在急冷油冷却器5内与冷却水换热后降温至60~80℃,然后返回至急冷除油塔2的中上部循环喷淋洗涤来自干馏炉的高温干馏油气;另一部分急冷油送去焦油储罐8储存;经过油尘分离装置4分离后的油泥渣用于做燃料;
步骤五,含轻油的干馏气从急冷除油塔2的塔顶出来后进入轻油冷凝器6内,通过循环冷却水进行间接冷凝至40℃;
所述的轻油冷凝器6,为立式管壳式换热器,含少量轻油的干馏气走壳程,冷却水走管程,冷凝后的轻油和水在油水分离罐7内静置分离;分离出来的干馏气经过电捕焦油器9除去油雾;
步骤六,冷凝后的轻油和水的混合物在油水分离罐7内静置分离,分离后的轻油一部分送回急冷除油塔2塔顶,以控制塔顶温度,其余生成的轻油送入焦油储罐8储存,用于作为燃料油或者化工原料。
本发明的显著效果在于:
利用高温干馏油气在急冷油洗塔内与冷却的循环急冷油直接接触降温实现干馏油气分离,同时塔顶含轻油的干馏气再经过轻油冷凝器内进行焦油冷凝分离,这种直接油洗和间接水冷结合的工艺大幅度降低了原来水洗工艺带来的大量废水,废水中苯、萘、酚等物质大大减少,降低污水处理难度,提高了干馏气中的焦油回收率。
采用旋风预除尘与膜除尘相结合的分级高效除尘方式,在高温状态下除去干馏油气中的灰尘,与油洗塔塔底温度控制(100-150℃)相结合,大大降低了循环急冷油的粘度,保证循环急冷油的流动性,与传统油洗工艺相比,无需设置中段侧采和回流,无需设置专门的减粘装置,大大降低系统能耗,简化了系统配置和操作,避免了灰尘和焦油混合堵塞系统,实现后续油洗分离工艺连续运行的关键技术。
本文用于企业家、创业者技术爱好者查询,结果仅供参考。