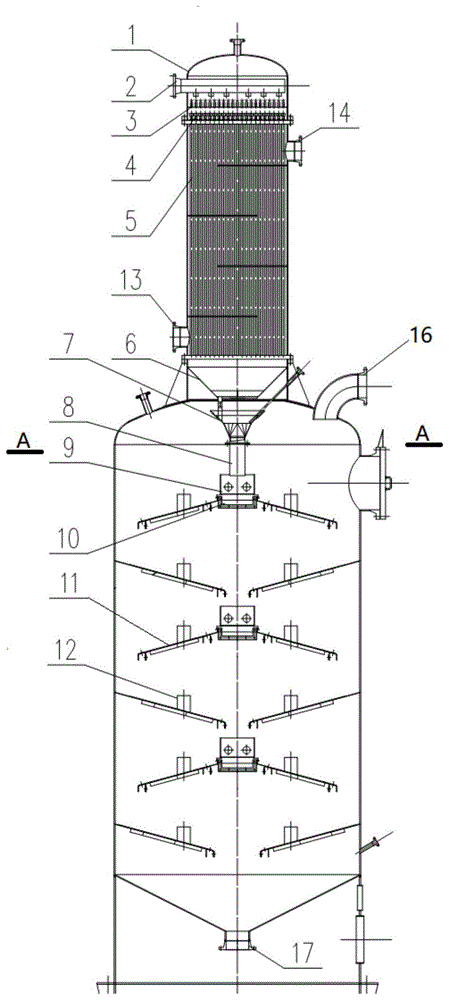
本实用新型涉及焦化设备技术领域,特别是涉及一种立式多段加热与蒸馏一体化洗油再生设备。
背景技术:
焦炉煤气中含有苯烃,通常在煤气的粗苯蒸馏工段进行回收和制取粗苯。目前,我国焦化行业生产的苯类产品仍占有很重要的地位,所以焦化企业有效地回收苯类可以取得良好的经济效益。
苯回收通常采用的方法是循环洗油吸收法,用蒸汽汽提富油得到苯汽,再冷凝而得到最终产品。洗油质量的好坏对回收苯起着非常重要的作用,洗油在长期循环过程中会发生部分组分聚合,吸收各种煤气中的杂质,其质量会逐渐恶化,影响吸收苯的能力,为了稳定和保证循环洗油质量,在粗苯产品生产过程中,必须对洗油进行再生处理。
目前,传统洗油再生设备为水平折流板再生器,洗油先用燃气管式炉或换热器被加热后进入再生器顶部,从再生器下部直接通入蒸汽对洗油进行蒸馏净化再生。这种洗油再生装置,存在加剧洗油聚合、换热器传热差、蒸汽大量损耗、废水量增加、输送能耗高、操作不便,设备占地大等缺点。
技术实现要素:
为克服现有技术缺陷,本实用新型解决的技术问题是提供一种立式多段加热与蒸馏一体化洗油再生设备,结构紧凑,加热段传热系数高,蒸汽热量梯次利用,洗油停留时间短,减少洗油的高温聚合损失,洗油回收率高。
为了达到上述目的,本实用新型采用以下技术方案实现:
一种立式多段加热与蒸馏一体化洗油再生设备,包括本体、洗油入口管、液体分布器、液体分布头、换热管、一段收集锥、二段收集锥、分布管、洗油收集槽、满流槽、带升气管的凸形倾斜隔板、带升气管的凹形倾斜隔板、过热蒸汽入口、蒸汽出口、蒸汽加热管、油气出口和残渣出口,其特征在于,所述洗油入口管、液体分布器、液体分布头、换热管从上至下依次设置在本体的上部构成加热段,所述过热蒸汽入口设置在加热段下部本体上,所述蒸汽出口设置在加热段上部本体上;所述一段收集锥、二段收集锥从上至下依次设置在加热段下本体的中部构成分离段;所述分布管上端与二段收集锥连接、下端与内部设有蒸汽加热管的洗油收集槽连接,洗油收集槽下设有满溜槽,满溜槽的满流口下设有带升气管的凸形倾斜隔板,其内端与满溜槽连接、外端悬空,带升气管的凸形倾斜隔板下方设有带升气管的凹形倾斜隔板,其外端与本体内壁连接、内端悬空,洗油收集槽、满流槽、带升气管的凸形倾斜隔板、带升气管的凹形倾斜隔板构成蒸馏层,多个蒸馏层从上至下依次设置在本体的下部构成蒸馏段;所述残渣出口设置在蒸馏段下本体上;所述油气出口设置在分离段本体中部。
与现有技术相比,本实用新型的有益效果是:
1)采用一种多段加热与蒸馏一体化的立式塔器,结构紧凑占地面积小;
2)加热段高效的液体分布器和液体分布头,确保洗油在每个换热管内壁形成均匀液膜流动,传热系数高,洗油停留时间短,减少洗油的高温聚合损失;
3)分离段设二段液相收集锥,提供充足的气液分离空间,有效实现气液分离,促进洗油气液分离,气相从再生器分离段气相出口排出,液相通过分布管降至蒸馏段,采用二次多段加热洗油,进一步蒸发洗油轻质组分,洗油回收率高;
4)蒸馏段为带升气管的多层倾斜隔板结构,利用隔板加大蒸发面积,经过多次加热、蒸馏,进一步蒸发洗油轻质组分,以降低洗油消耗;
5)在蒸馏段,过热蒸汽热量被梯次利用,过热蒸汽先经过蒸馏段洗油收集槽,蒸汽温度为375~450℃,充分利用蒸汽高温显热加热洗油,然后蒸汽进入上部加热段,主要利用蒸汽潜热,结合加热段的技术特点,继续与洗油进行热交换,在低温差下到达最大传热效果。
附图说明
图1是本实用新型的结构原理示意主视图;
图2是图1的a-a剖向结构(凸形倾斜隔板、凹形倾斜隔板及洗油收集槽内蒸汽加热管局部)原理示意图。
图中:1-本体2-洗油入口管3-液体分布器4-液体分布头5-换热管6-一段收集锥7-二段收集锥8-分布管9-洗油收集槽10-满流槽11-带升气管的凸形倾斜隔板12-带升气管的凹形倾斜隔板13-过热蒸汽入口14-蒸汽出口15-蒸汽加热管16-油气出口17-残渣出口
具体实施方式
下面结合附图对本实用新型的具体实施方式作进一步说明:
见图1-图2所示,本实用新型涉及的一种立式多段加热与蒸馏一体化洗油再生设备,包括本体1、洗油入口管2、液体分布器3、液体分布头4、换热管5、一段收集锥6、二段收集锥7、分布管8、洗油收集槽9、满流槽10、带升气管的凸形倾斜隔板11、带升气管的凹形倾斜隔板12、过热蒸汽入口13、蒸汽出口14、蒸汽加热管15、油气出口16和残渣出口17,所述洗油入口管2、液体分布器3、液体分布头4、换热管5从上至下依次设置在本体1的上部构成加热段,所述过热蒸汽入口13设置在加热段下部本体1上,所述蒸汽出口14设置在加热段上部本体1上;所述一段收集锥6、二段收集锥7从上至下依次设置在加热段下本体1的中部构成分离段;所述分布管8上端与二段收集锥7连接、下端与内部设有蒸汽加热管15的洗油收集槽9连接,洗油收集槽9下设有满溜槽10,满溜槽10的满流口下设有带升气管的凸形倾斜隔板11,其内端与满溜槽10连接、外端悬空,带升气管的凸形倾斜隔板11下方设有带升气管的凹形倾斜隔板12,其外端与本体1内壁连接、内端悬空(下方接下一层的洗油收集槽9),洗油收集槽9、满流槽10、带升气管的凸形倾斜隔板11、带升气管的凹形倾斜隔板12构成蒸馏层,多个蒸馏层从上至下依次设置在本体1的下部构成蒸馏段;所述残渣出口17设置在蒸馏段下本体1上;所述油气出口16设置在分离段本体1的中部。
工作原理:
1)洗油通过洗油入口管2进入,在高效的液体分布器3和液体分布头4共同作用下,洗油被均匀分配到每个换热管5内,洗油在重力的作用下均匀地在垂直顶部周边呈膜状沿换热管5内壁向下流动,与换热管5间的蒸汽高效传热,洗油在换热管5停留时间短,减少洗油的高温聚合损失,加热后的洗油汇集的到一段收集锥6内,进入分离段;
2)分离段的一段收集锥6、二段收集锥7,提供充足的气液分离空间,可有效实现气液分离,洗油先后流经一段收集锥6、二段收集锥7,气相从分离段油气出口16排出,液相通过分布管8降至蒸馏段;
3)洗油经分布管8进入洗油收集槽9,在蒸汽加热管15加热后的洗油平缓进入满流槽10,满流后均匀溢流到凸形倾斜隔板11,利用凸形倾斜隔板11加大蒸发面积,进一步蒸发洗油轻质组分,经过从上至下多个蒸馏层的多次加热、蒸馏,以降低洗油消耗,未气化的洗油重组分流入底部,由残渣出口17排出。
在蒸馏段,过热蒸汽热量被梯次利用,过热蒸汽先经过蒸馏段洗油收集槽9,蒸汽温度为375~450℃,充分利用蒸汽高温显热加热洗油,然后蒸汽进入上部加热段,主要利用蒸汽潜热,结合加热段的技术特点,继续与洗油进行热交换,在低温差下到达最大传热效果。
以上所述,仅为本实用新型较佳的具体实施方式,但本实用新型的保护范围并不局限于此,任何熟悉本技术领域的技术人员在本实用新型揭露的技术范围内,根据本实用新型的技术方案及其实用新型构思加以等同替换或改变,都应涵盖在本实用新型的保护范围之内。
本文用于企业家、创业者技术爱好者查询,结果仅供参考。