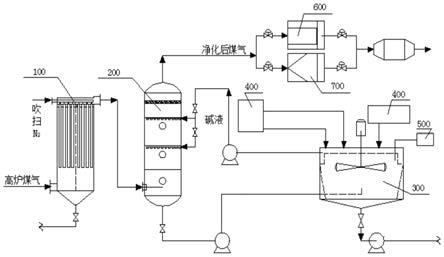
1.本发明涉及一种高炉煤气高效脱硫工艺,属于环保技术领域,具体地涉及一种高炉煤气高效脱硫装置及方法。
背景技术:
2.高炉煤气是钢铁厂重要的二次能源,是高炉炼铁生产过程中的副产品,每吨生铁产出煤气1600~2000m3/h,含有h2(1.5
‑
3.0%)、ch4(0.2
‑
0.5%)、co(25
‑
30%)、co2(9
‑
19.2%)、n2(50
‑
60%)、o2(0.2
‑
0.4%)及少量的硫化物(h2s、cos等),热值一般为3300
‑
4200kj/m3。除尘后高炉煤气常被单独用作热风炉、焦炉和锅炉的燃料,也可和焦炉煤气混合,成为发热值1100~2000kcal/nm3的混合煤气,作为均热炉、加热炉、热处理炉等的燃料,并用于烧结机点火等。随着钢铁行业环保要求提高及生态环境部等五部委联合发布了《关于推进实施钢铁行业超低排放的意见》,其中对高炉热风炉、轧钢热处理炉等中大气污染物中二氧化硫的超低排放限值要求分别为100mg/m3和50mg/m3。由于钢铁企业热风炉、加热炉烟气无相应的脱硫设备,热风炉、加热炉排放的二氧化硫浓度一般为100
‑
200mg/m3,距离超低排放指标要求还有一些差距。由于钢企使用高炉煤气的点位众多,研究表明,通过在热风炉、热处理炉等新建烟气脱硫设备,存在投资大、运行费用高、实用性不强以及带来大量的脱硫副产物,对环境造成二次污染等问题,目前在源头进行高炉煤气碱法脱硫系统还存在脱硫效果低、塔体结垢和腐蚀问题。综上,研究开发高炉煤气高效脱硫装置及方法以克服上述问题对高炉煤气高效脱硫剂稳定运行至关重要。
技术实现要素:
3.为解决上述技术问题,本发明公开一种高炉煤气高效脱硫装置及方法,可有效解决高炉煤气总硫含量高导致用户so2超标问题,提高了碱液脱硫效率,同时对减轻煤气中氟氯氰化物等对管网腐蚀问题及对煤气热值提升也有较好效果。
4.为实现上述目的,本发明公开了一种高炉煤气高效脱硫装置及方法。
5.一种高炉煤气脱硫装置,其包括水解催化塔及脱硫塔,所述水解催化塔的出口与所述脱硫塔的入口相连通,所述水解催化塔包括塔体、氮气吹扫装置、第一组除尘催化剂陶瓷管件、第二组催化剂陶瓷管件及多孔隔板,所述多孔隔板设置于所述塔体内的轴向方向,所述多孔隔板用于间隔所述第一组除尘催化剂陶瓷管件、第二组催化剂陶瓷管件所述第一组除尘催化剂陶瓷管件和第二组催化剂陶瓷管件相对于所述多孔隔板对称分布,所述氮气吹扫装置用于对所述第一组除尘催化剂陶瓷管件的管内向管外吹扫氮气,所述第一组除尘催化剂陶瓷管件包括多个第一除尘催化剂陶瓷管,所述第二组催化剂陶瓷管件包括多个第二催化剂陶瓷管,所述第一除尘催化剂陶瓷管的外壁设置有除尘涂层,所述第二催化剂陶瓷管的主体材质为载体和催化剂的混合。
6.优选地,所述多孔隔板上均匀分布有孔径为5
‑
10mm的通孔。
7.优选地,所述多孔隔板为不锈钢板或涂层碳钢板。
8.优选地,所述第一除尘催化剂陶瓷管的涂层的材质为al2o3、tio2、zro2、sio2或sic中的一种或任意两种以上的组合。
9.优选地,所述第一除尘催化剂陶瓷管的除尘涂层的孔密度为200
‑
400cpsi,所述除尘涂层的厚度为100
‑
500μm。
10.优选地,所述第一除尘催化剂陶瓷管的内层是催化剂为碱金属k2o或na2o为活性成分,载体以γ
‑
al2o3或tio2或zro2中的一种或任意两种以上的组合。
11.优选地,所述第二组催化剂陶瓷管件载体为γ
‑
al2o3或tio2或zro2中的一种或任意两种以上的组合,所述催化剂为碱金属氧化物、mgo或fe2o3中的任意一种或两种及以上组合而成的复合催化剂。
12.优选地,所述碱金属氧化物为k2o或na2o。
13.优选地,所述第二催化剂陶瓷管的壁厚为15
‑
25mm,陶瓷管表面微孔直径为50
‑
100微米。
14.优选地,所述第一组和第二组催化剂陶瓷管件还包括有多个文氏管,每个文氏管与对应的催化剂陶瓷管利用法兰连接。
15.优选地,所述高炉煤气脱硫装置还包括辐流沉淀池、自动加药系统及ph在线检测设备,从所述脱硫塔底端流出的吸收剂往辐流沉淀池处理后经循环泵送脱硫塔循环使用,所述自动加药系统的出口连通于所述辐流沉淀池,所述ph在线检测设备用于监测所述辐流沉淀池的溶液的ph值。
16.利用所述的高炉煤气脱硫装置的脱硫方法,包括如下步骤:
17.将布袋除尘器精除尘后的高炉煤气送入所述水解催化塔,水解催化塔轴向设置多孔隔板;使煤气在水解催化塔内分两条路径净化,一部分煤气通过第一组除尘催化剂陶瓷管件净化后排出;一部分煤气依次经过第一组除尘催化剂陶瓷管外侧,再通过多孔隔板进入第二组催化剂陶瓷管件净化后排出;
18.将水解催化后的煤气送入脱硫塔,通过吸收剂除去煤气中的酸性气体;
19.将脱硫和除雾后的煤气送入trt或减压阀再经脱水器后送入煤气管网或者煤气用户使用。
20.优选地,当所述第一组除尘催化剂陶瓷管件的催化剂陶瓷管中内外压降达到800~1000pa时,使高压氮气由管内向管外通过脉冲反吹,吹扫时间为5
‑
15s。
21.优选地,控制煤气进入水解催化塔的温度为80℃
‑
180℃,水汽含量控制在3
‑
10wt%,空速2000
‑
3000h
‑1。
22.本发明的有益效果:
23.1.本发明解决了高炉煤气中由于有机硫cos及无机硫h2s等引起总硫高而导致煤气燃烧后so2不能满足环保要求问题。
24.2.本工艺利用高炉煤气的特性及余压、温度通过水解实现了高炉煤气中羰基硫(cos)高效转化为无机硫(h2s),h2s脱除率达90%以上。
25.3.本工艺即实现了煤气脱硫(h2s),又降低了煤气中hcl、cl2、co2等酸性气体,对减轻煤气中氯元素对管网腐蚀及提高煤气热值也有较好效果。
26.4.本工艺与同类工艺相比,具有脱硫系统不结垢,脱硫效率高,占地面积小,投资省,运行费用低,实用性强,且对环境不造成二次污染等问题,具有较好的环保效益和经济
效益。
附图说明
27.图1为本发明高炉煤气脱硫装置的结构示意图。
28.图2为图1中水解催化塔的结构示意图。
29.图3为图1中的第一除尘催化剂陶瓷管的结构示意图。
30.图4为图1中的第二除尘催化剂陶瓷管的结构示意图。
31.图5为图1中的催化剂陶瓷管件的结构示意图。
32.图6为图1中的脱硫塔的结构示意图。。
33.图7为图1中的水解催化塔中的清灰控制系统的示意图。
具体实施方式
34.下面将结合本发明实施例中的附图,对本发明实施例中的技术方案进行清楚、完整地描述,所描述的实施例仅仅是本发明一部分实施例,而不局限以下实施例。
35.如图1所示,本发明提供了一种高炉煤气脱硫装置,包括水解催化塔100、脱硫塔200、辐流沉淀池300、自动加药系统400及ph在线检测设备500。
36.如图2所示,水解催化塔100的出口与脱硫塔200的入口相连通。水解催化塔100包括塔体120、氮气吹扫装置140、第一组除尘催化剂陶瓷管件160、多孔隔板130及第二组催化剂陶瓷管件180。第一组除尘催化剂陶瓷管件160及第二组催化剂陶瓷管件180均设置于塔体120的内部。第一组除尘催化剂陶瓷管件160及第二组催化剂陶瓷管件180相对多孔隔板130对称分布。氮气吹扫装置140用于对第一组除尘催化剂陶瓷管件160的管内向管外吹扫氮气。第一组除尘催化剂陶瓷管件160包括多个第一除尘催化剂陶瓷管162,所述第二组催化剂陶瓷管件180包括多个第二催化剂陶瓷管182。
37.如图3所示,每个第一除尘催化剂陶瓷管162的外壁设置有除尘涂层1622。除尘涂层1622的材质为al2o3、tio2、zro2、sio2或sic中的一种或任意两种以上的组合。除尘涂层1622的孔密度为200
‑
400cpsi,所述除尘涂层1622的厚度为100
‑
500μm。内层1624是催化剂为碱金属k2o或na2o为活性成分,载体以γ
‑
al2o3或tio2或zro2中的一种或任意两种以上的组合。每个第一除尘催化剂陶瓷管162通过法兰1626与其他组件固定。
38.如图4所示,每个第二催化剂陶瓷管182的主体材质1822为载体和催化剂的混合。载体为γ
‑
al2o3、tio2或zro2中的一种或任意两种以上的组合,催化剂为碱金属氧化物(k2o、na2o),mgo或fe2o3中的任意一种或两种及以上组合而成的复合催化剂。每个第二催化剂陶瓷管182的内壁表面微孔直径为50
‑
100微米。每个第二催化剂陶瓷管182通过法兰1824与其他组件固定。
39.如图5所示,在本实施例中,每组催化剂陶瓷管件还包括有多个文氏管。以第一催化剂陶瓷管162为例,每个文氏管164与对应的催化剂陶瓷管162利用法兰1626连接。催化剂陶瓷管162和182的管径为150mm
‑
200mm,管壁厚度为5
‑
10mm;外管法兰面外径为190mm
‑
240mm,法兰面厚度20mm
‑
30mm,管长为1000
‑
3000mm。氮气吹扫装置140包括吹扫喷头142和吹扫管144。
40.可以理解的是,水解催化塔100的设置根据现场煤气指标设置多级串联或并联,可
有效满足羰基硫cos去除及硫脱除效果状况下的系统连续生产需求。
41.如图6所示,脱硫塔200内设置有人孔220、雾化喷嘴240及丝网除雾器260。雾化喷嘴240喷射出碱液雾滴粒子与煤气中的酸性气体反应;雾化喷嘴240可设置多层(如2
‑
4层),雾滴直径应小于<30μm,雾化器压力来源于碱源增压泵。丝网除雾器260用于除雾,雾滴随煤气上升过程中在丝网除雾器260中凝结成大粒径雾滴液体降低了煤气中的水分含量,雾滴液体回到塔底,而脱硫后的煤气经出气口排至减压阀600或高炉煤气余压透平发电装置(trt)700减压后再进入脱水器800脱水后进入煤气管道再送到用户系统。
42.从脱硫塔200底端流出的吸收剂往辐流沉淀池300处理后经循环泵送脱硫塔200循环使用,不外排。自动加药系统400的出口连通于辐流沉淀池300。自动加药系统400包括naoh、ca(oh)2溶液加药装置、絮凝剂加药装置及缓蚀阻垢剂加药装置。ph在线检测设备500用于检测辐流沉淀池300的溶液的ph值,确保水质ph、悬浮物浓度、碱度和硬度受控,其中水质中ph值在11
‑
13、悬浮物浓度低于20mg/l;碱液水质碳钢挂片,年垢厚度应低于0.3mm;孔蚀深度应低于0.4mm。辐流沉淀池300内絮凝及反应沉淀的污泥由污泥泵送至污泥池处置,最终脱水干化后送烧结系统处置。
43.本实施例还提供一种高炉煤气脱硫方法,包括以下步骤:
44.s100,将布袋除尘器精除尘后的高炉煤气送入所述水解催化塔100,控制第一组除尘催化剂陶瓷管件160为过滤除尘催化,控制第二组催化剂陶瓷管件180为催化,其中绝大部分cos被转化成h2s;
45.s200,将水解催化后的煤气送入脱硫塔200,通过由碱液、混凝剂和复合阻垢缓蚀剂等不同药剂配制而成的吸收剂脱除煤气中的h2s等酸性气体,得到净化后的高炉煤气;
46.s300,将脱硫和除雾后的煤气送入trt700或减压阀600再经脱水器800后送入煤气管网或者煤气用户使用,而脱硫碱洗液(循环液)经回流泵送往辐流沉淀池300处理后泵送脱硫塔循环使用。
47.在步骤s100中,控制第一组除尘催化剂陶瓷管件160为除尘催化管件,控制第二组催化剂陶瓷管件180为催化管件。水解催化塔轴向设置多孔隔板;使煤气在水解催化塔内分两条路径净化,一部分煤气通过第一组除尘催化剂陶瓷管件160净化后排出;一部分煤气依次经过第一组除尘催化剂陶瓷管外侧,再通过多孔隔板进入第二组催化剂陶瓷管件净化后排出。如图7所示,以水解催化塔进出口总管压差作为控制参数,压差设定范围在800~1000pa之间,当压差值到了设定值时,压差控制器输出压差接点信号,plc通过清灰系统带动脉冲阀启动,实现高压氮气反吹控制。第一组除尘催化剂陶瓷管件高压氮气由管内向管外通过脉冲反吹,吹扫时间为5
‑
15s,以维持陶瓷管件160的催化剂陶瓷管中内外压降低于800~1000pa,进而可以实现对陶瓷管件160内外压降的控制,保证正常的生产。煤气在水解催化塔发生的反应如下:
48.cos h2o
→
co2 h2s
49.在步骤s100中,控制煤气进入催化剂陶瓷管的温度为80℃
‑
180℃,水汽含量控制在3
‑
10wt%,空速2000
‑
3000h
‑1。
50.经过上述该处理系统及方法有效的解决了高炉煤气总硫含量高导致用户so2超标问题,提高了碱液脱硫效率,同时对减轻煤气中氟氯氰化物等对管网腐蚀问题及对煤气热值提升也有较好效果。
51.为更好的解释本发明技术方案,以下结合具体实施例进行详细说明。
52.实施例1
53.参照图1所示的高炉煤气高效脱硫工艺装置系统及方法的流程工作图,具体按照下述步骤进行:
54.经布袋除尘器精除尘后的高炉煤气送入水解催化塔进行水解催化,其中绝大部分cos被转化成h2s,然后用ph为11的碱溶液脱除煤气中的h2s,煤气在脱硫塔中经脱硫和除雾器除雾后送入trt或减压阀再经脱水器后送入煤气管网或者煤气用户使用。高炉煤气硫化物去除效果见表1所示。
55.表1.高炉煤气硫化物脱除效果
[0056][0057][0058]
实施例2
[0059]
参照图1所示的高炉煤气高效脱硫工艺装置系统及方法的流程工作图,具体按照下述步骤进行:
[0060]
经布袋除尘器精除尘后的高炉煤气送入水解催化塔进行水解催化,其中绝大部分cos被转化成h2s,然后用ph为12的碱溶液脱除煤气中的h2s,煤气在脱硫塔中经脱硫和除雾器除雾后送入trt或减压阀再经脱水器后送入煤气管网或者煤气用户使用。高炉煤气硫化物去除效果见表2所示。
[0061]
表2.高炉煤气硫化物脱除效果
[0062][0063]
实施例3
[0064]
参照图1所示的高炉煤气高效脱硫工艺装置系统及方法的流程工作图,具体按照下述步骤进行:
[0065]
经布袋除尘器精除尘后的高炉煤气送入水解催化塔进行水解催化,其中绝大部分cos被转化成h2s,然后用ph为13的碱溶液脱除煤气中的h2s,煤气在脱硫塔中经脱硫和除雾器除雾后送入trt或减压阀再经脱水器后送入煤气管网或者煤气用户使用。高炉煤气硫化物去除效果见表3所示。
[0066]
表3.高炉煤气硫化物脱除效果
[0067][0068]
实施例4
[0069]
参照图1所示的高炉煤气高效脱硫工艺装置系统及方法的流程工作图,具体按照下述步骤进行:
[0070]
经布袋除尘器精除尘后的高炉煤气送入水解催化塔进行水解催化,其中绝大部分cos被转化成h2s,然后用ph为12的碱溶液脱除煤气中的h2s,煤气在脱硫塔中经脱硫和除雾器除雾后送入trt或减压阀再经脱水器后送入煤气管网或者煤气用户使用。高炉煤气硫化物去除效果见表4所示。
[0071]
表4.高炉煤气硫化物脱除效果
[0072][0073]
实施例5
[0074]
参照图1所示的高炉煤气高效脱硫工艺装置系统及方法的流程工作图,具体按照下述步骤进行:
[0075]
经布袋除尘器精除尘后的高炉煤气送入水解催化塔进行水解催化,其中绝大部分cos被转化成h2s,然后用ph为11的碱溶液脱除煤气中的h2s,煤气在0脱硫塔中经脱硫和除雾器除雾后送入trt或减压阀再经脱水器后送入煤气管网或者煤气用户使用。高炉煤气硫化物去除效果见表5所示。
[0076]
表5.高炉煤气硫化物脱除效果
[0077]
[0078][0079]
实施例6
[0080]
参照图1所示的高炉煤气高效脱硫工艺装置系统及方法的流程工作图,具体按照下述步骤进行:
[0081]
经布袋除尘器精除尘后的高炉煤气送入水解催化塔进行水解催化,其中绝大部分cos被转化成h2s,然后用ph为12的碱溶液脱除煤气中的h2s,煤气在脱硫塔中经脱硫和除雾器除雾后送入trt或减压阀再经脱水器后送入煤气管网或者煤气用户使用。高炉煤气硫化物去除效果见表6所示。
[0082]
表6.高炉煤气硫化物脱除效果
[0083][0084]
实施例7
[0085]
参照图1所示的高炉煤气高效脱硫工艺装置系统及方法的流程工作图,具体按照下述步骤进行:
[0086]
经布袋除尘器精除尘后的高炉煤气送入水解催化塔进行水解催化,其中绝大部分cos被转化成h2s,然后用ph为12的碱溶液脱除煤气中的h2s,煤气在脱硫塔中经脱硫和除雾器除雾后送入trt或减压阀再经脱水器后送入煤气管网或者煤气用户使用。高炉煤气硫化物去除效果见表7所示。
[0087]
表7.高炉煤气硫化物脱除效果
[0088][0089]
实施例8
[0090]
参照图1所示的高炉煤气高效脱硫工艺装置系统及方法的流程工作图,具体按照下述步骤进行:
[0091]
经布袋除尘器精除尘后的高炉煤气送入水解催化塔进行水解催化,其中绝大部分cos被转化成h2s,然后用ph为12的碱溶液脱除煤气中的h2s,煤气在脱硫塔中经脱硫和除雾器除雾后送入trt或减压阀再经脱水器后送入煤气管网或者煤气用户使用。高炉煤气硫化物去除效果见表8所示。
[0092]
表8.高炉煤气硫化物脱除效果
[0093][0094]
对比例1
[0095]
经布袋除尘器精除尘后的高炉煤气送入水解催化塔进行水解催化,其中绝大部分cos被转化成h2s,然后用ph为11的碱溶液脱除煤气中的h2s,煤气在脱硫塔中经脱硫和除雾器除雾后送入trt或减压阀再经脱水器后送入煤气管网或者煤气用户使用。高炉煤气硫化物去除效果见表9所示。
[0096]
表9.高炉煤气硫化物脱除效果
[0097]
[0098][0099]
对比例2
[0100]
经布袋除尘器精除尘后的高炉煤气送入水解催化塔进行水解催化,其中绝大部分cos被转化成h2s,然后用ph为11的碱溶液脱除煤气中的h2s,煤气在脱硫塔中经脱硫和除雾器除雾后送入trt或减压阀再经脱水器后送入煤气管网或者煤气用户使用。高炉煤气硫化物去除效果见表10所示。
[0101]
表10.高炉煤气硫化物脱除效果
[0102][0103]
实施例1
‑
2和对比例1
‑
2考查了水解催化剂塔采用除尘催化剂组件和不含有除尘的催化剂陶瓷管组件的情况。从表1与表9和表10对比情况来看,若将水解催化塔内的两组陶瓷管均设置为带有除尘涂层的催化剂陶瓷管,高炉煤气中的cos和h2s去除率没有明显提高,但还存在如下弊端:1、陶瓷管制备成本费用高;2、压降大,清灰频繁且氮气消耗量大,也降低了高炉煤气的热值;若将水解催化塔内的两组陶瓷管均设置为无除尘涂层的催化剂陶瓷管,存在cos转化率低的问题,这可能是与布袋除尘后为微细颗粒物堵塞、磨损陶瓷管催化剂活性位有关,导致其不能有效降低煤气中的总硫的含量。因此,综合对投资运行成本、维护成本和对总硫的去除效率等各方面因素综合分析,本发明设置两组不同催化剂管件,
即催化剂管件160为除尘催化剂管件,催化剂管件180为不含除尘涂层的催化剂管件方案取得了意料不到的技术效果。
再多了解一些
本文用于企业家、创业者技术爱好者查询,结果仅供参考。