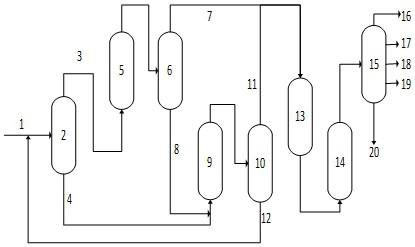
1.本发明属于石油化工技术领域,涉及一种重油转化组合工艺及系统,特别是涉及一种包括溶剂脱沥青、加氢处理、催化裂解等工艺过程的组合工艺,最大限度实现重油轻质化,同时大幅度延长装置的运转周期。
背景技术:
2.随着原油资源重质劣质化加剧,市场对轻质油品需求不断增加以及环保法规日益严格,重质稠油的高效转化和清洁高效利用是目前炼油行业关注的焦点。如何用最少的重油来获取最大量的轻质油品是石油加工业面临的紧迫任务,同时也是规避石油资源风险的一项重要而且有效的措施。目前重油的常规工艺包括蒸馏以及之后的各种裂解、溶剂精炼、以及加氢转化工艺,以便生产所需的系列产品。随着重油中硫、氮、金属等杂质含量越来越高,目前现有加工路线在加工重质劣质重油中存在较大的缺陷,难以获取最大量的轻质油品。
3.对于重质稠油,采用常减压蒸馏工艺获得液体收率较低,为提高轻油收率,通常对减压渣油进行焦化加工或者固定床渣油加氢;焦化工艺生成的油品性质差,同时会产生相当大量的低附加值高硫石油焦,而固定床渣油加氢存在对原料的适应性差、加氢装置空速低、催化剂失活快、运行周期短等问题。
4.溶剂脱沥青工艺在重油深度加工方面有较强的优势和吸引力。溶剂脱沥青工艺加工原料具有广泛性,物理抽提过程,没有催化系统,不存在催化剂中毒和失活的问题,可加工残炭值和金属含量较高的稠油;同时,工艺操作空间较大,通过改变溶剂组成和操作参数可以加工不同黏度的重质原料油。加氢技术也是解决劣质重油深加工的高效方法,具有原料适应性广、操作灵活、转化率高、产品质量好、运转周期长等特点,可以实现重劣质油的高效转化以及超清洁油品生产的双重目标。
5.cn102041082公开了重油加工转化的组合工艺,但是所述组合工艺只是根据不同装置的液体进料要求进行装置的联合使用,没有具体结合各种工艺的特征,尽量发挥各工艺的最大优势。如何根据目前重油加工工艺的特点,将各个工艺过程有机地结合起来,进而最大限度实现重油轻质化,同时大幅度延长装置的运转周期,是目前炼厂亟待解决的问题。
技术实现要素:
6.针对现有技术中的不足之处,本发明提供了一种重油转化组合工艺及系统,所述组合工艺可以最大程度实现重油轻质化,最大量生产低碳烯烃,同时大幅度延长装置的运转周期。
7.本发明第一方面提供一种重油转化组合工艺,所述工艺包括如下内容:(1)重油原料进入溶剂脱沥青单元,处理后得到脱油沥青和脱沥青油;(2)来自溶剂脱沥青单元的脱沥青油进入沸腾床加氢反应单元,在沸腾床加氢处理催化剂和氢气存在条件下进行反应,反应流出物经分离后得到第一轻馏分和第一尾油;
(3)来自步骤(2)得到的第一尾油和步骤(1)得到的脱油沥青混合后进入悬浮床加氢反应单元,在氢气和催化剂作用下进行加氢反应,反应流出物分离后得到第二轻馏分和第二尾油,所述第二尾油循环回溶剂脱沥青单元;(4)步骤(2)得到的第一轻馏分和步骤(3)得到的第二轻馏分混合进入预处理单元进行处理;(5)步骤(4)得到的预处理反应流出物直接进入催化裂解单元,反应流出物经分离后得到干气、液化气、催化汽油、催化柴油、催化重油。
8.上述重油转化组合工艺中,步骤(5)中所述催化柴油循环回悬浮床加氢反应单元。
9.上述重油转化组合工艺中,步骤(5)中所述催化重油循环回溶剂脱沥青单元。
10.上述重油转化组合工艺中,步骤(1)中涉及的重油原料中金属含量至少为150μg/g,优选为200μg/g 以上。所述重油原料可以为常压渣油、减压渣油、稠油等劣质油中的至少一种。
11.上述重油转化组合工艺中,步骤(1)中所述第二尾油和催化重油占溶剂脱沥青总进料重量的30%以下。
12.上述重油转化组合工艺中,步骤(1)中涉及到的溶剂脱沥青单元所使用的的溶剂为c3~c7的烷烃、石脑油馏分或凝析油中的至少一种,操作条件为:温度为80~200℃,优选100~160℃,压力为2.0~6.0mpa,优选3.0~5.0mpa,溶剂体积比为1.0~10.0,优选3.0~8.0。脱沥青油重量收率控制在40%-80%,同时脱沥青油中金属含量不大于120μg/g。
13.上述重油转化组合工艺中,步骤(2)中沸腾床加氢反应单元中设置一个以上沸腾床反应器,优选设置1~2个,设置两个以上沸腾床反应器时,反应器以串联方式连接,反应料流依次通过串联设置的反应器。处理条件可以根据原料性质和转化率来确定。通常地,反应温度为350~450℃,优选为380~440℃,反应压力为5.0~18.0mpa,优选为10.0~18.0mpa,氢油体积比500~2000,优选为600~1500,液时体积空速为0.1~5.0h-1
,优选为0.2~2.0h-1
。
14.上述重油转化组合工艺中,步骤(2)中沸腾床加氢反应单元反应流出物经分离后得到第一轻馏分和第一尾油,所述第一轻馏分和第一尾油在高压分离器中分离,其中第一轻馏分和第一尾油的分馏点为480~550℃。
15.上述重油转化组合工艺中,步骤(2)中沸腾床加氢处理催化剂可以选用本领域现有沸腾床加氢催化剂中的任一种,如购买市售商品;也可以按照现有制备方法进行制备。通常情况下,所述沸腾床加氢处理催化剂中的活性金属组分选自第vib族和/或第 viii族非贵金属元素中的至少一种,优选所述活性金属组分为ni-w、ni-w-co、ni-mo和co-mo的组合中的任意一种;特别优选地所述沸腾床加氢处理催化剂中的活性金属组分为ni-mo的组合。所述活性金属组分以氧化物计的含量为5~40重量%,更优选为8~30重量%。催化剂具有双峰分布的孔结构,孔直径在5~50nm 的孔容占总孔容的50~90%,孔直径大于100nm的孔容占总孔容的5~25%。
16.上述重油转化组合工艺中,步骤(3)中悬浮床加氢反应单元包括一个以上加氢反应器,优选设置1~2个加氢反应器。脱油沥青、第一尾油和催化柴油混合进入悬浮床加氢反应单元在氢气和催化剂作用下进行反应,催化柴油占悬浮床总进料的重量比不大于20%。所述悬浮床加氢反应单元的操作条件为:反应压力为 8~25mpa,优选为10~20mpa,反应温度
为400~490℃,优选为400~470℃,液时体积空速为0.1~2.0h-1
,优选为0.2~1.5h-1
,氢油体积比为200~1200,优选为400~1000。
17.上述重油转化组合工艺中,步骤(3)中悬浮床加氢反应单元使用的催化剂为分散型催化剂,进一步优选所述分散型催化剂为水溶性分散型催化剂或油溶性分散型催化剂。所述催化剂中活性金属组分为mo、ni、co、w、cr和fe中的一种或几种,以所述重油原料的总重量为基准,所述分散型催化剂的加入量为10~1000μg/g。
18.上述重油转化组合工艺中,所述第二轻馏分和第二尾油的分馏点为350~550℃,优选480~540℃。
19.上述重油转化组合工艺中,步骤(4)中所述预处理单元中包括一个以上预处理反应器,所述预处理反应器为具有全返混功能的反应器,反应器内可以设置有搅拌器实现物料混合均匀,反应器内装填有加氢催化剂,进一步优选加氢催化剂固定装填在催化剂栏框中,所述加氢催化剂含有活性金属和载体,其中活性金属含有第vib族金属和/或viii族金属中的至少一种,载体含有氧化铝、无定型硅铝和二氧化硅中的至少一种。预处理单元操作条件为:温度为370℃~420℃,优选350℃~400℃;压力10mpa~ 25mpa,优选15mpa~20mpa。
20.上述重油转化组合工艺中,步骤(5)中所述催化裂解单元可以设置一套或多套,每套装置至少应包括一个反应器、一个再生器和分馏塔,其中,反应器采用提升管反应器,所述分馏塔可以每套装置单独设置,也可以多套装置共用一个分馏塔。催化裂解单元的反应器中装填有催化裂解催化剂,所述催化裂解催化剂选自本领域现有商品催化剂或者根据现有方法制备得到的催化裂解催化剂。一般来讲,所述催化裂解催化剂中含有沸石、无机氧化物以及任选的粘土,以所述催化裂解催化剂的总重量计,所述沸石的含量为10~50重量%,无机氧化物的含量为5~90重量%,粘土的含量为0~70重量%;其中,所述沸石可以选自含或不含稀土的y型或hy型沸石、含或不含稀土的超稳y型沸石、具有mfi结构的沸石中的至少一种。所述催化裂解单元的反应条件如下:反应温度为500~650℃,优选540~600℃,重时空速为0.1~750h-1
,优选0.1~500h-1
,反应压力为0.10~1.0mpa,优选0.10~0.5mpa,剂油重量比为5~50,优选5~10;与催化剂接触时间0.1~15.0秒,优选0.5~5.0秒。
21.本发明第二方面提供一种重油转化组合系统,所述系统包括:溶剂脱沥青单元:其用于接收并处理重油原料,重油原料与溶剂处理后得到脱油沥青和脱沥青油;沸腾床加氢反应单元:其用于接收并处理来自溶剂脱沥青单元的脱沥青油,在氢气和沸腾床加氢处理催化剂作用下进行加氢反应;第一分离单元:其用于接收来自沸腾床加氢反应单元的反应流出物,分离后得到第一轻馏分和第一尾油;悬浮床加氢反应单元:其用于接收来自溶剂脱沥青单元脱油沥青和第一分离单元的第一尾油,在氢气和催化剂作用下进行反应;第二分离单元:其用于接收来自悬浮床加氢反应单元的反应流出物,分离后得到第二轻馏分和第二尾油;预处理单元:其用于接收并处理来自第一分离单元的第一轻馏分和来自第二分离单元的第二轻馏分;
催化裂解单元:其用于接收并处理来自预处理单元的预处理流出物,催化裂解反应流出物经分离后得到干气、液化气、催化汽油、催化柴油、催化重油。
22.上述重油转化组合系统中,催化柴油经管线循环回悬浮床加氢反应单元。
23.上述重油转化组合系统中,第二尾油经管线循环回溶剂脱沥青单元。
24.上述重油转化组合系统中,催化重油经管线循环回溶剂脱沥青单元。
25.上述重油转化组合系统中,所述溶剂脱沥青单元采用现有溶剂脱沥青装置,所述溶剂脱沥青装置可以设置一个以上,当设置两个以上溶剂脱沥青装置时,以串联方式连接。
26.上述重油转化组合系统中,沸腾床加氢反应单元中设置一个以上沸腾床反应器,优选设置1~2个,设置两个以上沸腾床反应器时,反应器以串联方式连接,料流依次通过串联设置的反应器。
27.上述重油转化组合系统中,悬浮床加氢反应单元包括一个以上加氢反应器,优选设置1~2个加氢反应器。
28.上述重油转化组合系统中,所述第一分离单元可以为高压分离器。
29.上述重油转化组合系统中,所述催化裂解单元可以设置一套或多套,每套装置至少应包括一个反应器、一个再生器和分馏塔,其中,反应器采用提升管反应器,所述分馏塔可以每套装置单独设置,也可以多套装置共用一个分馏塔。
30.与现有技术相比,本发明重油转化组合工艺及系统具有以下优点:1、本发明所述重油转化组合工艺中,根据各工艺特性,将溶剂脱沥青、沸腾床加氢、悬浮床加氢及催化裂解多种工艺有机结合,能够处理更加劣质重质的原料油,尤其是镍钒等金属含量较高的劣质渣油,且通过几种组合工艺的使用,可以降低装置操作苛刻度,增加装置空速,提高装置处理量,同时延长装置运作周期,降低装置运行成本。
31.2、本发明所述重油转化组合工艺中,脱油沥青和沸腾床未转化的尾油进入悬浮床加氢处理,能够最大化实现渣油轻质化,同时掺炼部分催化柴油,能够保证悬浮床加氢反应单元操作的稳定性,降低加氢过程的结焦现象发生,实现装置长周期平稳运行。
32.3、本发明所述重油转化组合工艺中,将沸腾床加氢反应单元得到的第一轻馏分和悬浮床加氢反应单元得到的第二轻馏分混合进行预处理,将物料中的硫、氮杂质脱除掉一部分,同时将第二轻馏分中含有较高含量的芳烃进行适当加氢饱和,由于预处理单元处理后的物料进入后续催化裂解单元进行处理,所以预处理单元处理后的物料性质对催化裂解产品的性质分布都有较大影响。本发明工艺中通过第一轻馏分和第二轻馏分两股物流自身含有的氢气满足其自身加氢反应的需要,控制其加氢程度,将物料进行适当加氢处理,本发明工艺中在预处理阶段无需额外补充氢气,而且,适当的进行加氢脱除s、n等杂质和饱和芳烃,避免催化裂解单元催化剂的失活,同时可以改善催化裂解单元的产品分布,提高目的产品收率。
33.4、本发明所述重油转化组合工艺中,通过将悬浮床加氢反应单元得到的尾油和催化重油循环至溶剂脱沥青单元,一方面可以提高溶剂抽提过程中传质效率,同时进一步将尾油和重油中不同烃类组分分离,实现渣油的高效转化。
34.5、本发明所述重油转化组合工艺中,在沸腾床加氢反应单元,过高的转化率将会使得轻质馏分油转化成甲烷等干气,从而降低后续目标产物低碳烯烃(尤其是丙烯)产量,本发明方法中通过控制适宜的沸腾床加氢转化率,沸腾床未转化的第一尾油进入到悬浮床
加氢单元,针对性针对这部分重油进行转化,从而实现重质劣质原料的高效轻质化转化。
附图说明
35.图1 为用于重油转化组合工艺的示意图。
36.其中:1-原料油,2-溶剂脱沥青单元,3-脱沥青油,4-脱油沥青,5-沸腾床加氢反应单元,6-第一分离单元,7-第一轻馏分,8-第一尾油,9-悬浮床加氢反应单元,10-第二分离单元,11-第二轻馏分,12-第二尾油,13-预处理单元,14-催化裂解单元,15-分馏装置,16-干气,17-液化气,18-催化汽油,19-催化柴油,20-催化重油。
37.图2为对比例1中所述的重油转化组合工艺示意图。
38.其中:1-原料油,2-溶剂脱沥青单元,3-脱沥青油物流,4-脱油沥青物流,5-沸腾床加氢反应单元,6-分离单元,7-沸腾床加氢轻馏分,8-沸腾床加氢尾油,9-催化裂解单元,10-分馏装置,11-干气,12-液化气,13-催化汽油,14-催化柴油,15-催化重油。
具体实施方式
39.下一步通过实施例和附图进一步描述本发明,但这些实施例不能限制本发明。
40.如图1所示,本发明提供一种重油转化组合工艺,所示组合工艺包括如下内容:渣油原料1和溶剂分别从溶剂脱沥青单元2中抽提塔的上部和下部进入抽提塔,逆向萃取后得到脱沥青油3和脱油沥青4,脱沥青油3和氢气混合后进入沸腾床加氢反应单元5,加氢生成油进入第一分离单元(高压分离器)6,分离成第一轻馏分7和第一尾油8;脱油沥青4、第一尾油8以及催化柴油19进入悬浮床加氢反应单元9,加氢生成油进入第二分离单元10,分离后得到第二轻馏分11和第二尾油12,第二尾油12循环到溶剂脱沥青单元2;第一轻馏分7和第二轻馏分11混合后进入预处理单元13,生成油进入催化裂解单元14反应;催化裂解单元生成油进入分馏装置15,产物分离成干气16、液化气17、催化汽油18、催化柴油19和催化重油20,催化柴油循环回悬浮床加氢反应单元,催化重油20循环到溶剂脱沥青单元2中。
41.本发明实施例和对比例中使用原料油为中东减压渣油,具体性质见表1。
42.表1 渣油原料的性质本发明实施例和比较例中,所述沸腾床加氢反应单元设置两个沸腾床反应器,两个沸腾床反应器以串联方式连接,且两个沸腾床反应器中装填的催化剂相同,均为微球形的以氧化铝为载体的ni-mo催化剂,其中,以催化剂的总量为基准,催化剂中含有重量12.3%的moo3和3.0重量%的nio,催化剂比表面积为250m2/g,孔直径在5~50nm 的孔容占总孔容的
75%,孔直径大于100nm的孔容占总孔容的21%。
43.本发明实施例和比较例中,催化裂解单元使用的催化剂选用mmc-2(中国石油化工股份有限公司催化剂齐鲁分公司生产)。
44.本发明实施例和比较例中,悬浮床加氢反应单元使用的催化剂为油溶性分散型催化剂环烷酸钼。
45.本发明实施例和比较例中,预处理单元使用的催化剂为抚顺石油化工研究院开发的ff-24催化剂。
46.实施例1实施例采用本发明图1所示流程,其中溶剂脱沥青单元中使用的溶剂为正丁烷,抽提温度为135℃,压力4.0mpa,溶剂体积比为4.8。脱沥青油(dao)收率为63.5%,脱油沥青(doa)收率为36.5%。沸腾床加氢反应单元反应压力14mpa,剂油体积比700,其中第一反应器反应温度390℃,液时体积空速0.4 h-1
,第二反应器反应温度405℃,液时体积空速0.5h-1
。悬浮床加氢反应单元设置1个反应器,进料中第一尾油8和催化柴油19占总进料重量比分别为25.2%和5.1%,反应压力为17mpa,反应温度450℃,液时体积空速为0.35h-1
,氢油体积比800。所述油溶性分散型催化剂用量为原料油的800μg/g。催化裂解单元采反应器压力设为0.20mpa,反应温度580℃,剂油比10,重时空速为160 h-1
,剂油重量比为8.0,具体的产品的分布见表2。
47.实施例2与实施例1基本相同,不同之处在于其中溶剂脱沥青单元中使用的溶剂为正丁烷与异丁烷混合溶剂(50%∶50%),抽提温度为125℃,压力4.0mpa,溶剂体积比为4.8。沸腾床加氢反应单元反应压力15mpa,剂油体积比800,其中第一反应器反应温度395℃,液时体积空速0.4 h-1
,第二反应器反应温度410℃,液时体积空速0.5h-1
。悬浮床加氢反应单元设置1个反应器,反应压力为16mpa,反应温度460℃,液时体积空速为0.30h-1
,氢油体积比800。所述油溶性分散型催化剂用量为原料油的1000μg/g。催化裂解单元采反应器压力设为0.20mpa,反应温度550℃,剂油比10,重时空速为160 h-1
,剂油重量比为8.0,具体的产品的分布见表2。
48.对比例1对比例1采用图2所示工艺流程,对比例1为常规的溶剂脱沥青-沸腾床加氢-催化裂解重油加工组合路线,渣油原料1和溶剂分别从溶剂脱沥青单元2中抽提塔的上部和下部进入逆向萃取得到脱沥青油物流3和脱油沥青物流4,脱油沥青4和氢气混合后进入沸腾床加氢单元5,加氢生成油进入高压分离单元6,分离成轻馏分7和尾油8,脱沥青油物流3和轻馏分7混合进入催化裂解单元,生成油进入分馏单元10,分离成干气11、液化气12、汽油13、催化柴油14和催化重油15,催化重油15和尾油8循环到溶剂脱沥青单元2。工艺参数同实施例1,具体的产品的分布见表2。
49.对比例2与实施例1基本相同,不同之处在于没有设置预处理单元,第一轻馏分和第二轻馏分直接进入催化裂解单元,具体的产品的分布见表2。
50.表2 实施例和对比例方案的产品分布
再多了解一些
本文用于企业家、创业者技术爱好者查询,结果仅供参考。