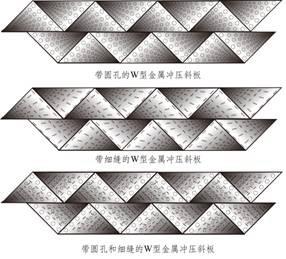
本发明属于化工分离应用领域,具体涉及一种非均相三组元液体燃料的快速分离系统及方法。
背景技术:
非均相三组元液体燃料,通常由两种共聚化合物材料、一种氧化剂溶液组成,如丙烯酸甲酯、丙二醇硝酸酯、pba,以及液氧/液氢、丁二醇、煤油等。通过该液体燃料制备的推进剂产物能够充分燃烧,其体积能量密度要远远超过一元燃料单独使用时的密度,可以显著增加火箭发动机效率或鱼雷等武器射程。同时,其燃烧产物溶于水,对于减少鱼雷航迹、提高鱼雷隐身性能具有重要意义。因而三组元液体燃料是一种前景广阔的新型化工材料。但是,三组元液体燃料制备的原工艺,通常还是依靠传统的釜式搅拌,再静置完成分离,属于间歇性操作,存在分离效率低、静止时间长(4h)、夹带量大(>2%)等问题,极大影响了后处理单元。同时,单一组元燃料正常下安定,但多元溶剂在非正常状态下混合后与强氧化剂长时间共聚同一反应釜,具备爆炸潜力且爆炸界限不明,存在极大的安全隐患和风险。目前,试验安全问题已经严重阻碍三组元液体燃料的开发和生产,亟需开发一种快速的液-液分离技术,能够使此类混合溶液制备过程中在较短的时间内完全分开,保障非均相三组元液体燃料的安全应用。
离心分离技术是一种通过离心力场实现液-液两相快速分离的技术,该技术具有分离时间短、结构紧凑、处理量大等优点。对于分离体系的要求,离心分离技术的应用一般仅需要两相具有一定的密度差(>0.1g/cm3),互不溶解。非均相三组元液体燃料实际是氧化剂溶液与复合物燃料组成的两相体系,它们的密度差达到0.15-0.5g/cm3,因此,采用离心分离技术来实现非均相三组元液体燃料的快速分离是十分适合的。
中国发明专利cn110082402a公开了一种易爆溶剂体系用充氮测氧本质安全型离心萃取方法,通过充氮单元向离心分离器内部引入氮气,置换掉离心分离器内部的空气,使离心分离器内部使用易燃易爆溶剂时的氧含量控制在预设安全范围之内;发明专利cn110117034a提出了一种离心萃取高浓度含酚废水及其资源化的方法,利用多级离心分离器的逆流串联和络合萃取、反萃取技术,克服了化学萃取可逆性差的不足,提高脱酚率,以降低生化处理或者后续处理的压力;实用新型cn209865380u涉及一种三级串联控温离心萃取分离装置,将控温、传质与分离汇集一体,适用于萃取分离效果与温度高度敏感的料液处理工艺;发明专利cn108654139a公开了一种制药用三级逆流离心萃取器,通过螺纹槽中旋转活动杆的延伸长度进行调节,改变与萃取药液之间的接触面积,进而实现了对离心力场的改变。但是,上述公开专利无论是分离设备还是分离方法均存在分离方式单一、传质效率低、相夹带严重等问题,使得非均相三组元液体燃料混合溶液通常存在以下问题:1、高速离心力场中,物料与旋转件之间摩擦导致的发热和静电,存在安全隐患;2、在环隙区域传质不均匀导致局部乳化严重,形成非正常状态混合;3、分离效率不高,分离后燃料溶液仍然存在少量相夹带影响后处理单元。因此,为了满足非均相三组元液体燃料制备工艺的要求,本领域迫切需要开发出一种混合效果好、传质效率高以及能够实现快速分离的技术,并设计出相应的分离装置。
技术实现要素:
为了解决上述现有技术存在的问题,本发明的目的在于,提供一种非均相三组元液体燃料的快速分离系统及方法。
一方面,本发明提供了一种非均相三组元液体燃料的快速分离方法,包括以下步骤:
(a)收集非均相三组元液体燃料的混合溶液;
(b)对步骤(a)收集的混合溶液通过物料进料泵增压,按入口流量均分成至少三股,每一股混合溶液对应进入一个离心分离器中;
(c)每个离心分离器对步骤(b)中均分后输入的混合溶液进行离心分离,得到重相强氧化剂溶液和轻相复合燃料;
(d)将步骤(c)中得到的重相强氧化剂溶液汇总后经重相增压泵送入重相收集罐,将得到的轻相复合燃料汇总后经轻相增压泵送入轻相收集罐。
(e)对重相收集罐中的重相强氧化剂溶液采用分离内件进行物理分离得到强氧化剂溶液和复合燃料;同时,对轻相收集罐中的轻相复合燃料采用分离内件进行物理分离得到强氧化剂溶液和复合燃料;将重相收集罐和轻相收集罐输出的强氧化剂溶液汇总,将输出的复合燃料汇总。
进一步的,所述强氧化剂溶液与复合燃料的流量比为1:1-3:1,压降为0.1-0.3mpa,流速为0.5-1.5m/s。
另一方面,本发明提供了一种非均相三组元液体燃料制备工艺中快速分离系统,包括:
物料进料泵,用于将上游反应单元汇集的非均相三组元液体燃料混合溶液进行加压输送至离心分离器;
与物料进料泵连接的至少三台离心分离器,用于对输入的混合溶液进行离心分离,离心分离器的重相出口输出重相强氧化剂溶液,轻相出口输出轻相复合燃料;
与离心分离器轻相出口、重相出口分别相连接的两个增压泵,用于对离心分离器输出的重相强氧化剂溶液和轻相复合燃料分别加压输送至重相收集罐和轻相收集罐;
与轻相增压泵连接的轻相收集罐,用于对重相强氧化剂溶液进行强化分离,进一步去除少量相夹带;
与重相增压泵连接的重相收集罐,用于对轻相复合燃料进行强化分离,进一步去除少量相夹带。
重相收集罐的下半部分、轻相收集罐的上半部分内部分别设有分离内件和液位控制阀;轻相收集罐的物料入口设置在罐体下半部分,物料出口设置在罐体上部且位于分离内件上方;重相收集罐的物料入口设置在罐体的上半部分,物料出口设置在罐体底部且位于分离内件下方。
进一步的,所述重相增压泵和轻相增压泵均为防爆型蠕动泵,其流量范围为进料量的1.5-2倍,出口压力为0.7-1.2mpa;
进一步的,所述重相收集罐和轻相收集罐中的分离内件采用纤维聚结板叠加而成,也可采用w型金属冲压斜板叠加而成,所述纤维聚结板由亲疏水性材料混合编制而成,其孔隙率为80-100%;w型金属冲压斜板的顶角90°,斜板形成的通道与垂直方向成45°,斜板上均布多个ф5-10mm的孔或(和)长3-5mm的沟槽,开孔率为15-30%。
进一步的,所述防乳化离心分离器包括转筒和外壳体,所述外壳体同轴设置于转筒外侧;所述转筒相对于外壳体能够旋转;所述转筒和外壳体之间同轴设置有防乳化布液套筒,防乳化布液套筒包括两端开口的圆柱筒,所述圆柱筒的环形展开面上有多层第一布液孔。
进一步的,在所述圆柱筒的环形展开面上的第一布液孔的层数为2-6层;在所述圆柱筒上位于同一层上的第一布液孔间距相等;所述防乳化布液套筒上开孔范围开始于圆柱筒上端;所述第一布液孔的孔径为5-10mm,开孔率为环形展开面的40%-60%。
进一步的,每层所述第一布液孔下方的圆柱筒内壁上分别设置有导液槽;所述导液槽的宽度为5-10mm,导液槽中心线与每层第一布液孔中心线间距为第一布液孔孔径的2-3倍。
进一步的,所述外壳体内壁的周向设有多层垂直于外壳体内壁的环形布液板,每个所述环形布液板上均布第二布液孔,所述外壳体内壁上设置环形布液板的层数为2-3层;所述环形布液板的内径为转筒外径的1.5-2倍,厚度为2-4mm;所述环形布液板设置高度为转筒高度的1/2-1/3处;所述第二布液孔的孔径范围为5-10mm,开孔率为所有环形布液板的40%-60%。
进一步的,在所述转筒外壁周向上等距设置多片轴向布液挡板;所述布液挡板上设有多个第三布液孔;所述转筒外壁上设置轴向布液挡板的片数为4-6片;所述转筒外壁周向上所有的布液挡板组成的外轮廓圆的直径为转筒外壁外径的1.2-1.6倍,所述布液挡板的长宽比为6-10,厚度为2-4mm;所述第三布液孔的孔径范围为5-10mm,开孔率为所有布液挡板展开面的40%-60%。
相较于现有技术,本发明的有益效果如下:
1、本发明首次采用离心分离技术多级并联加纤维强化聚结分离技术的组合分离方式,在离心分离器离心分离的基础上进一步精细分离,其中,采用离心分离器至少三台并联能够让进料、分离和出料的过程连续,从而提高分离效率,其分离时间≤1.5h,与原工艺相比,处理时间缩短60%以上,能够达到快速分离,有效提高了安全性;离心分离器单级分离效率高于99%;其中轻重相出口的夹带量<0.5%;
2、采用安装了分离内件和液位控制阀的重相收集罐和轻相收集罐,能够将离心分离后得到的混合溶液进行进一步的精细分离,有效去除了离心分离器输出的混合溶液中的少量夹带,使得分离更彻底。
3、采用了防乳化结构设计的离心分离器,其中,防乳化布液套筒能够实现转筒旋转时靠近其壁面的周向泰勒涡流中两相混合时颗粒的粒径均一,避免细小、易乳化的液滴产生;防乳化多层环形布液板的结构设计能够有效改善环隙区域内层流和湍流引起的少量轴向返混,通过布液板上均布小孔实现整流,形成多级梯度主动控制液滴粒径范围并降低滞液率;另外,针对两相密度差大和难萃取体系,在转筒外壁增加防乳化轴向布液挡板设计,强化环流中液滴周向剪切力,同时配合布液孔的均布整流和分散粒径的效果,实现既混合均匀又具有配合转筒周向剪切力的防乳化功能,真正达到转筒内快速分离的目的。三种优化结构设计单独应用后均能有效提高环隙混合区域的传质效率25-40%、降低滞液率50%以上,优化后离心萃取机环隙内的液滴平均粒径范围控制在40-50μm。使得产品的夹带量大大降低、分离效率大幅升高,回收产品收率和品质大幅提高。离心萃取机单级级效率高于99%,轻重相出口的夹带量<0.5%。
附图说明
根据附图进行的如下详细说明,本发明的目的和特征将变得更加明显。附图用以提供对本发明的进一步理解,它只是构成本说明书的一部分以进一步解释本发明,并不构成对本发明的限制。
图1是本发明的非均相三组元液体燃料的快速分离系统及方法流程图。
图2是本发明的系统中采用的防乳化离心分离器的三维结构示意图.
其中,1:电机、2:机盖、3:联轴器、4:电机安装座、5:盖板、6:旋转轴、7:堰板压盖、8:重相堰板、9:重相出口、10:轻相出口、11:转筒、12:防乳化挡板组合、13:防乳化布液套筒、14:转子组件、15:卡盘、16:上底板、17:收集室、18:重相进口管、19:重相出口管、20:轻相出口管、21:轻相进口管、22:筒身、23:下底板、24:底部法兰、25、机架。
图3(a)是根据本发明的一个实施例中的防乳化布液套筒左视图,图3(b)是根据图3(a)的a-a剖面内件结构示意图,图3(c)是该防乳化布液套筒的三维轴测图。
其中,101:第一布液孔、102:导液槽。
图4(a)是防乳化离心分离器中的径向防乳化布液结构(即外壳体上设置多层环形布液板)左视图,图4(b)是该防乳化布液结构的三维轴测图,图4(c)是第一层环形布液板的俯视图,图4(d)是第二层环形布液板的俯视图。
其中,201:环形布液板、202:外壳体内壁、203:第二布液孔。
图5(a)是防乳化离心分离器中的轴向防乳化布液结构(即转筒外壁上设置多片轴向布液挡板)左视图,图5(b)是该轴向布液挡板安装结构的俯视图。
其中,301:转筒外壁、302:第三布液孔。
图6是本发明的装置中的填料层中材料的结构示意图。其中,图6(a)是纤维聚结板;图6(b)是w型金属冲压斜板,由上到下分别是带圆孔的w型金属冲压斜板、带细缝的w型金属冲压斜板、带圆孔和细缝的w型金属冲压斜板。
具体实施方式
本申请的发明人经过长期的工程实践与实验研究过程,针对现有技术存在的自动化程度低、静止时间长、乳化严重、分离效率低等问题,不但难以满足新型燃料集成化生产的发展需要,也无法实现新技术生产操作过程的安全应用,基于“高效、分离、安全”的思想,因此提出了一种非均相三组元液体燃料制备工艺中的快速分离方法及装置,本发明的方法及装置高效、节能,在实施过程中通过离心分离技术与聚结分离技术相结合的方式,完成在短时间内两相分离,并且产品无相夹带,整个系统安全可靠,实现连续化操作。
以下通过附图和实施例对本发明做进一步阐述:
本发明提供的非均相三组元液体燃料的快速分离方法,包括以下步骤:
(a)收集非均相三组元液体燃料的混合溶液(待分离物料),该混合溶液含有共聚化合物、强氧化剂和水;
(b)对步骤(a)收集的混合溶液通过物料进料泵(即物料蠕动泵)增压,按入口流量均分成至少三股,每一股混合溶液对应进入一个离心分离器中;
(c)每个离心分离器对步骤(b)中均分后输入的混合溶液进行离心分离,得到重相强氧化剂溶液和轻相复合燃料。
具体的:在每个离心分离器内,混合溶液被离心分离,其中的重相强氧化剂溶液被甩至离心分离器的转筒壁处,经过重相堰板流入重相收集室,从重相出口流出。轻相复合燃料(即共聚化合物)被挤至离心分离器的转筒中心处,经轻相堰板流入轻相收集室,从轻相出口流出;
(d)将步骤(c)中得到的重相强氧化剂溶液汇总后经重相增压泵送入重相收集罐,将得到的轻相复合燃料汇总后经轻相增压泵送入轻相收集罐。
由于重相收集罐中的重相强氧化剂溶液中通常混有少量的复合燃料,而轻相收集罐中的轻相复合燃料中通常混有少量的强氧化剂溶液,因此本发明对这些溶液进行了进一步的强化分离。具体是:
(e)对重相收集罐中的重相强氧化剂溶液采用分离内件进行物理分离得到强氧化剂溶液和复合燃料;同时,对轻相收集罐中的轻相复合燃料采用分离内件进行物理分离得到强氧化剂溶液和复合燃料;将重相收集罐和轻相收集罐输出的强氧化剂溶液汇总,将输出的复合燃料汇总。
该步骤是对重相强氧化剂溶液和轻相复合燃料分别进行进一步的精细分离,也即去除少量相夹带。
上述技术方案中,将混合溶液分为至少三股分别进入对应离心分离器,能够让进料、分离和出料的过程连续,也即当一台进料时,其他两台可以分别处于分离和出料状态,使得生产过程连续不用等待,实现连续操作从而提高生产效率。经离心分离器输出的重相混合溶液以及轻相混合溶液分别采用重相收集罐和轻相收集罐收集,然后进一步精细分离后输出,有效去除了离心分离器输出的混合溶液中的少量夹带,使得分离更加彻底。
优选的,离心分离过程中所述的重相和轻相需对应待分离体系中单一组元溶液的密度而言,上述步骤仅为其中某一体系的情况说明,其他非均相三组元液体燃料体系的分离处理同上述步骤。
优选的,物料注入量、分离后产物排出量均通过蠕动泵和增压泵进行远程调节,离心分离器、各收集罐上均设有温度及压力报警,直接反馈于各离心分离器和各收集罐进料控制。
优选的,进入重相收集罐和轻相收集罐中的强氧化剂溶液与复合燃料的流量比为1:1-3:1,压降为0.1-0.3mpa,流速为0.5-1.5m/s。
另一方面,本发明提供了一种非均相三组元液体燃料制备工艺中快速分离系统,包括:
物料进料泵,用于将上游反应单元(如非均相三组元液体燃料的卤化取代反应)汇集的非均相三组元液体燃料混合溶液进行加压输送至离心分离器;
与物料进料泵连接的至少三台离心分离器,用于对输入的混合溶液进行离心分离。离心分离器的重相出口输出重相强氧化剂溶液,轻相出口输出轻相复合燃料;
与离心分离器轻相出口、重相出口分别相连接的两个增压泵,用于对离心分离器输出的重相强氧化剂溶液和轻相复合燃料分别加压输送至重相收集罐和轻相收集罐。
与轻相增压泵连接的轻相收集罐,用于对重相强氧化剂溶液进行强化分离,进一步去除少量相夹带。
与重相增压泵连接的重相收集罐,用于对轻相复合燃料进行强化分离,进一步去除少量相夹带。
重相收集罐的下半部分、轻相收集罐的上半部分内部分别设有分离内件和液位控制阀。分离内件具体为填料层,填料层厚度为罐体高度的10-20%;轻相收集罐的物料入口设置在罐体下半部分,物料出口设置在罐体上部且位于分离内件上方;重相收集罐的物料入口设置在罐体的上半部分,物料出口设置在罐体底部且位于分离内件下方。
本发明的系统可用于本发明的工艺。
上述技术方案中,采用离心分离器至少三台是为了能够让进料、分离和出料的过程连续,也即当一台进料时,其他两台可以分别处于分离和出料状态,使得生产过程连续不用等待,从而提高生产效率。其具体数目根据实际需要进行增减。优选的,采用三台离心分离器,均采用立式结构且并联设置。
采用重相收集罐和轻相收集罐是为了将离心分离器分离后得到的混合溶液进行进一步的精细分离,有效去除了离心分离器输出的混合溶液中的少量夹带,使得分离更彻底。
在上述技术方案应用时,物料进料泵将非均相三组元液体燃料的卤化取代反应后的混合溶液加压输送至至少三台离心分离器中,离心分离器内,重相强氧化剂溶液被甩至转筒壁处,经过重相堰流入重相收集室,从重相出口流出。轻相复合燃料则被挤至转筒中心处,经轻相堰流入轻相收集室,从轻相出口流出。经过离心分离出的复合燃料和氧化剂溶液中仍存在少量的夹带(<0.5%),此时,采用两个增压泵将得到的两种混合溶液分别送入重相收集罐和轻相收集罐去除部分夹带。
重相强氧化剂溶液从重相收集罐的上半部分进入罐体,向下通过分离内件后从罐体底部流出,夹带的少量复合燃料上浮,在罐体顶部累积,当复合燃料达到低液位时,液位控制阀打开,复合燃料由罐体上部被排出至复合燃料出料总管。同时,轻相复合燃料从轻相收集罐的下半部分进入罐体,向上经分离内件后从收集罐顶部送出,其内夹带的少量氧化剂溶液被分离内件阻挡且因重力沉降到收集罐底部,当强氧化剂溶液积累到高液位时,液位控制阀打开,排出氧化剂溶液至低液位(强氧化剂溶液总管)。
在本申请中,用于承担混合液体萃取分离作用的离心分离器的选择,对于最终分离效率的影响至关重要,通常,在离心分离器环隙区域的混合过程中,轻相分散在重相中,由于分散相液滴受到泰勒涡流的作用,沿着漩涡对重相的顺时针涡到达泰勒涡流交会处,而上方的漩涡对轻相的逆时针涡将连续相液滴带回交会处,从而使两相混合主要集中在转筒外壁面附近。由于需要萃取分离处理的大部分非均相体系中待萃液(连续相)与萃取剂(分散相)的两相密度差较小,粒径分布不均匀,受原有离心分离器转筒设计结构的周向剪切力影响较大,导致待萃液与萃取剂在环隙区域混合后乳化严重,影响转筒内的分离效率。因此,为了解决环隙区域混合溶液乳化严重的问题,本发明在通用型的离心分离器的基础上,增加了防乳化功能设计的布液套筒及其他布液结构。
如图1所示,本发明中的离心分离器可以根据不同的萃取分离体系进行水力学参数设计,包括传动部件、机架25、旋转组件和旋转组件的外壳体。萃取系统若采用多级串联或并联操作的,离心分离器均采用立式结构。其中:
传动部件用于为旋转组件提供旋转动力。传动部件包括电机1、机盖2、变频器和联轴器3,传动部件设置于机架25的顶部;其中电机1设置于机盖2的上方,根据不同的工艺要求和作业环境选用防爆型或非防爆型。机盖2通过电机安装座4固定在机架25顶部,机盖2与电机安装座4通过螺栓连接。联轴器3经轴承与电机1连接,并延伸至电机安装座4内与旋转组件的旋转轴6同轴固定。
外壳体包括筒身22、收集室17和盖板5。外壳体设置于旋转组件外侧且同轴,盖板5与机架25、机盖2分别通过螺栓连接固定。外壳体作为旋转组件的承载支撑构件,起到安全保护作用。收集室17位于圆柱状的筒身22的上部,筒身22外壁处同轴凸设有法兰构造的上底板16和下底板23,下底板23与底部法兰24构成法兰配合。收集室17内分为重相收集室和轻相收集室。底部法兰24设计采用4-12个平板或涡状叶片作为导流叶片,与转筒的混合液吸入口间距为5-20mm。
旋转组件设置于电机安装座4的下方。旋转组件包括转筒11、旋转轴6和堰板压盖7。其中堰板压盖7是旋转组件的固定装置,堰板压盖7通过螺栓与转筒11连接固定。转筒11包括转筒外壁301、转子组件14、轻相堰板和重相堰板8,其中转筒外壁301同轴固定于旋转轴6,其上部按不同高度设有导流孔作为重相出口9和轻相出口10。转子组件14位于转筒外壁301内,旋转轴6下端穿出电机安装座4并伸入转筒外壁301内与转子组件14的中心轴固定。重相堰板8和轻相堰板通过堰板压盖7压住,它们呈环状自上而下固定于转筒11内腔的顶部。
上述方案中,机架25的作用是支撑和固定。优选的,机架25上部的安装法兰采用剖分形式以便安装和拆卸。机架25底部安装有橡胶减振器,使装置的振动不会传递到基础上。变频器可在0-60hz的频率范围内进行任意调节,从而实现电机在0-2000r/min范围内的无极调速。
优选的,底部法兰24设有排污导淋,防止临时停车造成非均相三组元液体燃料混合积液的爆炸隐患。
为了解决待萃液与萃取剂在离心分离器环隙区域乳化严重的问题,在通用的离心分离器的外壳体的筒身22和转筒的转筒外壁301之间设置有防乳化布液套筒13,该防乳化布液套筒13包括两端开口的圆柱筒,该圆柱筒与筒身22、转筒外壁301三者同轴,防乳化布液套筒13下端通过焊接或螺接形式固定于底部法兰24上。
防乳化布液套筒13的内径大于底部法兰24导流叶片的外接圆轮廓直径。
防乳化布液套筒13的环形展开面上设有多层第一布液孔101,每层的第一布液孔101间距相等;孔径范围为5-10mm,开孔率为环形展开面的40%-60%(经试验,开孔率为40%时防乳化效果最优),开孔范围从靠近传动部件的防乳化布液套筒13上端开始;其轴向长度为防乳化布液套筒13总长的1/3-2/3。
优选的,在所述圆柱筒的环形展开面上的第一布液孔101的层数为2-6层,经试验,设计为5层防乳化效果最优。
优选的,防乳化布液套筒13的内径优选设计尺寸为转筒外壁301外径和筒身22内径环比差值的1/2-1/3,长径比为1.5-2,套筒13厚度为2-4mm。
防乳化布液套筒13内壁在每层第一布液孔101下方分别设置有一导液槽102,槽宽范围为5-10mm,导液槽102中心线与每层第一布液孔101中心线间距为布液孔101孔径的2-3倍,导液槽102的长度除两侧留出开槽加工距离外需延伸至整个套筒13的环形展开面。该技术方案中,在每层第一布液孔下方设置导液槽,是为了配合离心分离器环隙内的多向层流,将均布分散后的液滴群进行梯级主动控制,形成两相有效传质空间,不影响离心力场对流形的分布,进一步有效减少乳化发生。
优选的,离心分离器的转筒11、轻重相堰板8、密封板、进出料端子(即重相进口管18、重相出口管19、轻相出口管20、轻相进口管21)、防乳化布液套筒13或布液结构、转子组件14的材质根据不同的萃取分离两相体系的材料相容性原则以及耐腐蚀性考虑选择2205高强度不锈钢、316l不锈钢、高分子复合材料、碳钢喷涂中的一种。
对于离心分离器防乳化结构的改进还可以有如下设计:如图4所示,在外壳体内壁202(即筒身22内壁)的周向(径向)设有多层垂直于外壳体内壁202的环形布液板201,该环形布液板201的内径为转筒11的转筒外壁301外径的1.5-2倍,厚度为2-4mm。每个环形布液板201上均布第二布液孔203,孔径范围为5-10mm,开孔率为所有环形布液板201的40%-60%(经试验,设计为50%时防乳化效果最优)。环形布液板201设置高度为转筒11高度的1/2-1/3处,可设置2-3层(经试验,设计为3层时防乳化效果最优)。环形布液板上第二布液孔203的分布密度由上到下逐层减小,其设计的主要目的是为了防止混合均匀的两相混合液体系被布液孔的周向剪切力重新强制剪切成游离态的小液滴群,产生轴向返混负作用,进而影响防乳化效果。
对于离心分离器防乳化结构的改进还可以有如下设计:如图5所示,在转筒外壁301周向上等距设置多片轴向布液挡板12,可设4-6片(经试验,设计为6片时防乳化效果最优)。该布液挡板12的长宽比为6-10,厚度为2-4mm。布液挡板12上设有多个第三布液孔302,孔径范围为5-10mm,开孔率为所有布液挡板12展开面的40%-60%(经试验,开孔率为40%时防乳化效果最优)。每个布液挡板12上的第三布液孔302的分布由上到下逐渐稀疏,其设计目的同布液套筒、环形布液板的开孔密度类似,主要是为了防止周向剪切力作用重新破坏已稳定的两相混合液体系,对防乳化效果产生负影响。所有布液挡板12组成的外轮廓圆的直径为转筒外壁301外径的1.2-1.6倍。
优选的,所述离心分离器的防乳化装置,根据萃取分离体系的易乳化程度可进行功能性结构组合设计,进一步优化其防乳化效果。具体方案如防乳化布液套筒 外壳体内壁的环形布液板、防乳化布液套筒 转筒外壁的轴向布液挡板,防乳化布液套筒 外壳体内壁的环形布液板 转筒外壁的轴向布液挡板的防乳化结构等。上述组合方案中的防乳化结构设计参数与技术方案中单独使用的防乳化结构设计参数描述一致,但设计时应注意其尺寸不能产生结构相互间的机械干涉。
优选的,为了在重相收集罐和轻相收集罐中对离心分离器输出的混合液体进一步精细分离,满足分离内件所需的进料流速,以取得最优的分离效果,本发明的装置中,重相增压泵和轻相增压泵均选型为防爆型蠕动泵,其流量范围为进料量的1.5-2倍,出口压力为0.7-1.2mpa。
优选的,重相收集罐和轻相收集罐中的分离内件(填料层)根据不同的非均相三组元液体燃料分离体系进行设计,可采用有机物和无机物组合编织的纤维聚结板(见图6(a))叠加而成,也可采用不同结构形式的w型金属冲压斜板(见图6(b))叠加而成。具体的,纤维聚结板以纤维表面的亲疏水特性实现非均相体系混合液的物理分离,具有不添加化学试剂、无二次污染、稳定可靠等特性。纤维聚结板由亲疏水性材料(如聚四氟乙烯、玻璃纤维、不锈钢金属丝等)混合编制而成,其孔隙率为80-100%;w型金属冲压斜板的顶角90°,斜板形成的通道与垂直方向成45°,斜板上均布多个ф5-10mm的小孔或(和)长约3-5mm的沟槽(或细缝),以控制两相液滴的粒径范围,并形成双向渗透,开孔率为15-30%。
较佳地,离心分离器和液位控制器均可采用dcs远程控制,实现人机隔离操作。
实施例1:
如图1所示,本实施例的分离方法包括如下步骤:
(a)收集非均相三组元液体燃料的混合溶液,该混合溶液含有鱼推-3燃料、高氯酸羟胺溶液和水;
(b)对步骤(a)收集的混合溶液通过物料进料泵增压,按入口流量均分成至少三股,每一股混合溶液对应进入一个离心分离器中;
(c)每个离心分离器对步骤(b)中均分后输入的混合溶液进行离心分离,得到重相强氧化剂溶液和轻相复合燃料。
(d)将步骤(c)中得到的重相强氧化剂溶液汇总后经重相增压泵送入重相收集罐,将得到的轻相复合燃料汇总后经轻相增压泵送入轻相收集罐。
(e)对重相收集罐中的重相强氧化剂溶液采用分离内件进行物理分离得到强氧化剂溶液和复合燃料;同时,对轻相收集罐中的轻相复合燃料采用分离内件进行物理分离得到强氧化剂溶液和复合燃料;将重相收集罐和轻相收集罐输出的强氧化剂溶液汇总,将输出的复合燃料汇总。
本实施例采用如下分离系统执行上述工艺:
物料进料泵,用于将非均相三组元液体燃料的卤化取代反应汇集的非均相三组元液体燃料混合溶液进行加压输送至离心分离器;
与物料进料泵连接的三台离心分离器,用于对输入的混合溶液进行离心分离。离心分离器的重相出口输出重相强氧化剂溶液,轻相出口输出轻相复合燃料;
与离心分离器轻相出口、重相出口分别相连接的两个增压泵,用于对离心分离器输出的重相强氧化剂溶液和轻相复合燃料分别加压输送至重相收集罐和轻相收集罐。
与轻相增压泵连接的轻相收集罐,用于对重相强氧化剂溶液进行强化分离,进一步去除少量相夹带。
与重相增压泵连接的重相收集罐,用于对轻相复合燃料进行强化分离,进一步去除少量相夹带。
轻相收集罐和重相收集罐中均设有分离内件和液位控制阀,分离内件安装在对应的收集罐上部;
离心分离器和收集罐中的混合溶液的流量比为2:1,压降为0.15mpa,流速为1.5m/s。进料泵和增压泵均采用防爆蠕动泵,泵选型的流量范围为进料量的1.5倍,出口压力为0.8mpa。
分离内件采用聚四氟乙烯、玻璃纤维混合编制的纤维聚结板,长度为收集罐总长度的10%。
离心分离器采用如下结构的防乳化离心分离器:
电机1选用防爆型三相异步电机。底部法兰24设计采用8个涡状叶片作为导流叶片,与转筒的混合液吸入口间距为5mm。旋转组件中,转筒外壁301上部每隔35mm分别设有导流孔作为重相出口9和轻相出口10;重相堰板8及轻相堰板之间的间隔为20mm。
防乳化布液套筒13通过焊接固定于底部法兰24上。防乳化布液套筒13的内径为转筒11外径和外壳体内径环比差值的1/3,长径比为2,厚度为2mm。防乳化布液套筒13的环形展开面上开有五层第一布液孔101,其中上3层的密度相同,下2层的密度相同,且上3层的开孔密度大于下2层的开孔密度;第一布液孔101的孔径为5mm,开孔率为环形展开面的40%。防乳化布液套筒13上导液槽102的槽宽为5mm,导液槽102中心线与每层小孔101中心线间距为小孔101孔径的2倍。
在外壳体内壁202的周向设有3层垂直于外壳体内壁202的环形布液板201,该环形布液板201的内径为转筒11外径的2倍,厚度为4mm。其中环形布液板201只需要均布开小孔,无需开导液槽,孔径为7.5mm,开孔率为所有环形布液板201的50%。防乳化环形结构设置高度自转筒11高度的1/3处起,每隔300mm设置一层布液板,共设置3层。
在转筒外壁301周向上等距设置6片轴向布液挡板12,布液挡板12的长宽比为7.5,厚度为2mm。每片布液挡板上只需要均布开小孔,无需开导液槽,孔径为5mm,开孔率为所有挡板展开面的40%。防乳化挡板组合设计的外轮廓圆直径为转筒11外径的1.5倍且与防乳化布液套筒13内径间隙为10mm。
离心萃取机中转筒11、轻相堰板、重相堰板8、密封板、进出料端子(即重相进口管18、重相出口管19、轻相出口管20、轻相进口管21)、防乳化布液套筒13、转子组件14的材质均选用316l不锈钢。
离心分离器和液位控制器采用dcs远程控制,实现人机隔离操作。
本实施例中,离心分离器的轻重相出口的夹带量为0.3%,鱼推-3燃料收率95.2%;总处理时间为1.4小时,相较于操作时间4小时的现有工艺方法,大大缩短了处理时间,提高了分离效率。
实施例2:
本实施例与实施例1的区别如下:
进料泵和增压泵的流量为进料量的1.8倍,出口压力为1.0mpa。
分离内件采用聚四氟乙烯、不锈钢丝混合编制的纤维聚结板,厚度为收集罐高度的20%。
防乳化离心分离器中,防乳化布液套筒13的内径为转筒11外径和外壳体内径环比差值的1/2,长径比为2,厚度为3mm。防乳化布液套筒13的环形展开面上开有四层第一布液孔101,其中上2层的密度相同,下2层的密度相同;第一布液孔101的孔径为10mm,开孔率为环形展开面的60%。防乳化布液套筒13上导液槽102的槽宽为8mm,导液槽102中心线与每层小孔101中心线间距为小孔101孔径的2倍。
在外壳体内壁202的周向设有2层垂直于外壳体内壁202的环形布液板201,该环形布液板201的内径为转筒11外径的2倍,厚度为4mm。其中环形布液板201均布开小孔,孔径为7.5mm,开孔率为所有环形布液板201的40%。防乳化环形结构设置高度自转筒11高度的1/2处起设置。
在转筒外壁301周向上等距设置6片轴向布液挡板12,布液挡板12的长宽比为8,厚度为3mm。每片布液挡板上只需要均布开小孔,无需开导液槽,孔径为8mm,开孔率为所有挡板展开面的50%。防乳化挡板组合设计的外轮廓圆直径为转筒11外径的1.2倍且与防乳化布液套筒13内径间隙为10mm。
本实施例中,离心分离器的轻重相出口的夹带量为0.2%,鱼推-3燃料收率94.6%;总处理时间为1.3小时,相较于操作时间4小时的现有工艺方法,大大缩短了处理时间,提高了分离效率。
实施例3:
本实施例与实施例1的区别如下:
离心分离器和收集罐中的混合溶液的流量比为1.5:1,压降为0.2mpa,流速为1.3m/s。进料泵和增压泵的流量为进料量的2倍,出口压力为1.2mpa。
分离内件采用w型金属冲压斜板,其顶角90°,斜板形成的通道与垂直方向成45°,斜板上均布多个ф10mm的孔和长约5mm的沟槽,开孔率为20%。
防乳化离心分离器中,防乳化布液套筒13的内径为转筒11外径和外壳体内径环比差值的1/3,长径比为1.5,厚度为4mm。防乳化布液套筒13的环形展开面上开有五层第一布液孔101,其中上3层的密度相同,下2层的密度相同;第一布液孔101的孔径为8mm,开孔率为环形展开面的50%。防乳化布液套筒13上导液槽102的槽宽为10mm,导液槽102中心线与每层小孔101中心线间距为小孔101孔径的3倍。
在外壳体内壁202的周向设有3层垂直于外壳体内壁202的环形布液板201,该环形布液板201的内径为转筒11外径的2倍,厚度为4mm。其中环形布液板201均布开孔,孔径为7.5mm,开孔率为所有环形布液板201的60%。防乳化环形结构设置高度自转筒11高度的1/2处起。
在转筒外壁301周向上等距设置5片轴向布液挡板12,布液挡板12的长宽比为10,厚度为4mm。每片布液挡板上均布开孔,孔径为10mm,开孔率为所有挡板展开面的40%。防乳化挡板组合设计的外轮廓圆直径为转筒11外径的1.6倍且与防乳化布液套筒13内径间隙为10mm。
本实施例中,离心分离器的轻重相出口的夹带量为0.3%,鱼推-3燃料收率93.8%;总处理时间为1.5小时,相较于操作时间4小时的现有工艺方法,大大缩短了处理时间,提高了分离效率。
在本发明提及的所有文献都在本申请中引用作为参考。此外应说明的是,在阅读了本发明的上述技术内容之后,本领域技术人员可以对本发明作各种等价功能的常规改动或修改,这些等价形式同样落于本申请所附权利要求书所限定的范围。
本文用于企业家、创业者技术爱好者查询,结果仅供参考。