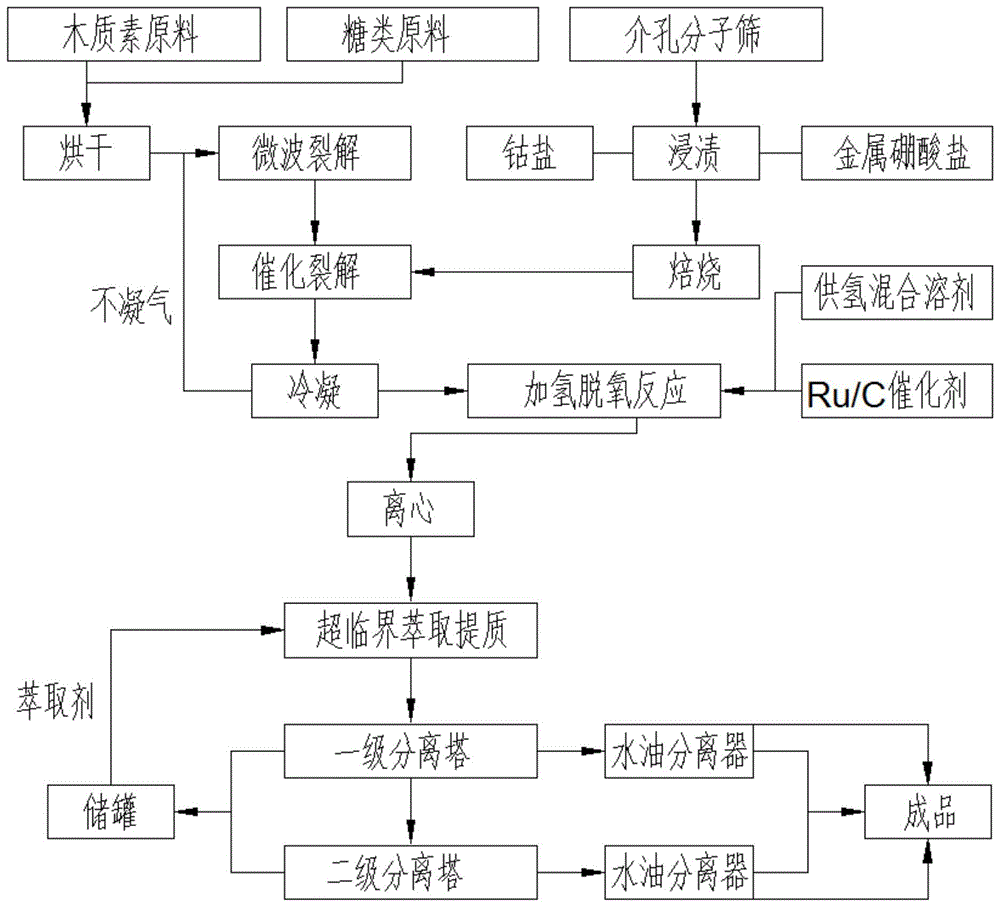
本发明涉及一种裂解催化生产生物质液体燃料的方法,属于生物质液体燃料生产技术领域。
背景技术:
随着人们对能源需求的不断增加,以绿色的生物质能源替化石能源是能源可持续发展的重要途径,利用生物质资源如农作物秸秆和农业加工剩余物、薪材及林业加工剩余物、禽畜粪便、工业有机废水和废渣、城市生活垃圾和能源植物等生产液体燃料,可有效减少有害气体、烟尘和温室气体,益于改善环境质量。生物质主要通过生物化学转化、热化学转化为可利用能源,通过沼气池厌氧发酵分解甲烷和二氧化碳热能较高沼气或酵母进行糖类发酵分解成乙醇等生物方法,存在生化反应时间长、后处理复杂和副产品难以利用且对生化反应影响较大的技术缺陷,而包括燃烧、汽化、液化、氢化和热裂解的化学过程可将生物质直接氢化或分解,有利于简化操作、经济性更好。
热裂解制程为间接加热将碳氢化合物分解后重组,将高沸点、巨大分子的有机物质裂解或分解为较低分子的物质如轻油及柴油等高价物质,但传统热裂解对导热性较低的生物质原料加热升温时间较长,至少在500-600℃以上才能裂解导致处理量有限,操作和能源成本较高,且快速热裂解产品中含有大量水和酸值,影响燃烧稳定性且无法与传统燃油混合,含氧量低、重整脱除工艺复杂、液态油收率和燃烧热值不高,难以满足燃料生产和应用需求。
技术实现要素:
本发明的目的是针对现有技术的缺陷,提供一种裂解催化生产生物质液体燃料的方法,改性的mcm-48分子筛催化剂两步法催化裂解生物质木质素原料和糖类原料,加氢脱氧反应后经超临界萃取提质和减压分离,降低了生物质液体燃料的反应温度和酸值,提高了液气转化率、高碳数油液收率和产品热值。
本发明是通过如下的技术方案予以实现的:
一种裂解催化生产生物质液体燃料的方法,其中,其方法如下:
s1:取mcm-48介孔分子筛和浸渍在钴盐和金属硼酸盐混合的等质量比溶液中,过滤经焙烧处理获得分子筛催化剂,所述钴盐为乙二胺四乙酸二钠钴盐,金属硼酸盐为硼酸锡或硼酸钼,焙烧温度为350-450℃、焙烧时间为2-3h;
s2:取木质素原料、糖类原料经过烘干处理、投入设有微波发生器的裂解反应流化床中,所述木质素原料和糖类原料包括的木材、树皮、小麦、水稻、农林废弃物、甘蔗和田菜一种或多种、并控制含水量低于20%;
在负压厌氧条件下升温裂解生成灰分和油气,油气送入裂解反应流化床上层的催化反应区中,在分子筛催化剂作用下进一步裂解、并冷凝回收油液,收集床底灰分,裂解反应流化床的反应压力为-5.5~-0.6mpa,反应温度为320-385℃,微波发生器的微波功率为50-800w,微波频率500-1000mhz,裂解时间为3-6h,油气冷凝时产生的不冷凝气体用于循环并提供催化裂解反应流化床部分热量;
s3:取油液与供氢混合溶剂、ru/c催化剂投入高压反应器中进行加氢脱氧反应,油液与供氢混合溶剂的质量比为100:(6-15),所述供氢混合溶剂由苯甲醇、四氢喹啉、四氢酚萘、乙酸乙酯、苯甲酸苄酯中的两种或两种以上按等质量比组成,高压反应器中的反应压力为5-8mpa,反应温度为280-370℃,高压反应器内设有间歇开启且搅拌速率为80-150r/min的搅拌器,反应时间为1-2h;
随后离心、取液态物置于萃取塔中,萃取剂经高压泵加压和预热后进入萃取塔进行超临界萃取提质,萃取剂为二氧化碳或甲烷,萃取釜压力为4-6mpa,超临界存取温度为100-155℃;
s4:萃取塔顶部物料经管路输送进入减压的一级分离塔和二级分离塔中进行连续减压分离,一级分离塔压力为2.1-3mpa、温度为70-110℃,二级分离塔的压力为1-2mpa、温度为65-100℃,分离后的萃取剂进入储罐用于萃取循环,一级分离塔和二级分离塔的塔底产物粉分别送入水油分离器分离,获得的单一油相或油相混合品作为生物质液体燃料成品,所述生物质液体燃料的总酸值为80-135mgkohg-1,热值为38-51mjkg-1。
本发明的有益效果为:
(1)采用木质素原料和糖类原料作为原料并控制含水量,裂解过程中在负压厌氧条件下升温裂解,利用微波辅助提高穿透性能避免温差梯度,三维螺旋孔道网络的mcm-48介孔分子筛经过钴盐和金属硼酸盐的酸性改性edta-2naco-sn/mo-mcm-48,两步法在催化裂解过程中避免结焦失活现象、延长催化剂活性和寿命,副产品灰分可用于生产固体燃料,催化剂方便回收,且各种酸类转化为酯类,利于降低反应温度、提高液气转化率和高碳数油液收率;
(2)通过与供氢混合溶剂、ru/c催化剂在高压反应器中进行加氢脱氧反应,使c-o键断裂、c-h键形成,以减小油液中的酸值和含氧化合物含量,有效抑制了可见焦炭的形成,采用优化条件通过超临界萃取提质、两级分离塔减压分离,水油分离提取单一油相或油相混合品作为生物质液体燃料成品,有利于提高产值传热、抑制生物油聚合结焦反应,酸类、醛类转化为酯类和缩醛,降低生物质液体燃料的氧和酸值,有利于提高产品热值。
附图说明
图1为本发明工艺流程图。
具体实施方式
下面结合附图和实施例对本发明的具体实施方式作进一步说明。
实施例1:
一种裂解催化生产生物质液体燃料的方法,其中,其方法如下:
s1:取2kgmcm-48介孔分子筛和浸渍在1kg钴盐和1kg金属硼酸盐加水混合的等质量比溶液中,过滤经焙烧处理获得分子筛催化剂,所述钴盐为乙二胺四乙酸二钠钴盐,金属硼酸盐为硼酸钼,焙烧温度为365℃、焙烧时间为2h;
s2:取40kg质量木质素原料、60kg糖类原料经过烘干处理、投入设有微波发生器的裂解反应流化床中,所述木质素原料和糖类原料包括的木材、树皮、农林废弃物稻壳、甘蔗、并控制含水量低于15%;
在负压厌氧条件下升温裂解生成灰分和油气,油气送入裂解反应流化床上层的催化反应区中,在分子筛催化剂作用下进一步裂解、并冷凝回收油液,收集床底灰分,裂解反应流化床的反应压力为-3mpa,反应温度为365℃,微波发生器的微波功率为500w,微波频率800mhz,裂解时间为4h,油气冷凝时产生的不冷凝气体用于循环并提供催化裂解反应流化床部分热量;
s3:取油液与供氢混合溶剂、ru/c催化剂投入高压反应器中进行加氢脱氧反应,油液与供氢混合溶剂的质量比为100:12,所述供氢混合溶剂由苯甲醇、四氢酚萘按等质量比组成,高压反应器中的反应压力为5mpa,反应温度为290℃,高压反应器内设有间歇开启且搅拌速率为100r/min的搅拌器,反应时间为2h;
随后离心、取液态物置于萃取塔中,萃取剂经高压泵加压和预热后进入萃取塔进行超临界萃取提质,萃取剂为二氧化碳,萃取釜压力为5mpa,超临界存取温度为120℃;
s4:萃取塔顶部物料经管路输送进入减压的一级分离塔和二级分离塔中进行连续减压分离,一级分离塔压力为2.5mpa、温度为85℃,二级分离塔的压力为1.3mpa、温度为78℃,分离后的萃取剂进入储罐用于萃取循环,一级分离塔和二级分离塔的塔底产物粉分别送入水油分离器分离,获得的单一油相作为生物质液体燃料成品,一级分离塔和二级分离塔的生物质液体燃料的总酸值分别为112mgkohg-1、95mgkohg-1,热值分别为42mjkg-1、50mjkg-11。
实施例2:
一种裂解催化生产生物质液体燃料的方法,其中,其方法如下:
s1:取2kgmcm-48介孔分子筛和浸渍在1kg钴盐和1kg金属硼酸盐加水混合的等质量比溶液中,过滤经焙烧处理获得分子筛催化剂,所述钴盐为乙二胺四乙酸二钠钴盐,金属硼酸盐为硼酸锡,焙烧温度为410℃、焙烧时间为2h;
s2:取50kg木质素原料、50kg糖类原料经过烘干处理、投入设有微波发生器的裂解反应流化床中,所述木质素原料和糖类原料包括的小麦、和田菜、并控制含水量低于20%;
在负压厌氧条件下升温裂解生成灰分和油气,油气送入裂解反应流化床上层的催化反应区中,在分子筛催化剂作用下进一步裂解、并冷凝回收油液,收集床底灰分,裂解反应流化床的反应压力为-4.2mpa,反应温度为374℃,微波发生器的微波功率为350w,微波频率600mhz,裂解时间为3h,油气冷凝时产生的不冷凝气体用于循环并提供催化裂解反应流化床部分热量;
s3:取油液与供氢混合溶剂、ru/c催化剂投入高压反应器中进行加氢脱氧反应,油液与供氢混合溶剂的质量比为100:10,所述供氢混合溶剂由苯甲醇、四氢喹啉、乙酸乙酯、苯甲酸苄酯按等质量比组成,高压反应器中的反应压力为6mpa,反应温度为350℃,高压反应器内设有间歇开启且搅拌速率为130r/min的搅拌器,反应时间为1.5h;
随后离心、取液态物置于萃取塔中,萃取剂经高压泵加压和预热后进入萃取塔进行超临界萃取提质,萃取剂为甲烷,萃取釜压力为5mpa,超临界存取温度为152℃;
s4:萃取塔顶部物料经管路输送进入减压的一级分离塔和二级分离塔中进行连续减压分离,一级分离塔压力为2.1mpa、温度为80℃,二级分离塔的压力为1mpa、温度为80℃,分离后的萃取剂进入储罐用于萃取循环,一级分离塔和二级分离塔的塔底产物粉分别送入水油分离器分离,获得的油相混合品作为生物质液体燃料成品,所述生物质液体燃料的总酸值为102mgkohg-1,热值为47mjkg-1。
实施例3:
一种裂解催化生产生物质液体燃料的方法,其中,其方法如下:
s1:取2kgmcm-48介孔分子筛和浸渍在1kg钴盐和1kg金属硼酸盐加水混合的等质量比溶液中,过滤经焙烧处理获得分子筛催化剂,所述钴盐为乙二胺四乙酸二钠钴盐,金属硼酸盐为硼酸锡,焙烧温度为440℃、焙烧时间为3h;
s2:取80kg木质素原料、20kg糖类原料经过烘干处理、投入设有微波发生器的裂解反应流化床中,所述木质素原料和糖类原料包括的木材、水稻、甘蔗和田菜、并控制含水量低于19%;
在负压厌氧条件下升温裂解生成灰分和油气,油气送入裂解反应流化床上层的催化反应区中,在分子筛催化剂作用下进一步裂解、并冷凝回收油液,收集床底灰分,裂解反应流化床的反应压力为-1.8mpa,反应温度为370℃,微波发生器的微波功率为600w,微波频率850mhz,裂解时间为4h,油气冷凝时产生的不冷凝气体用于循环并提供催化裂解反应流化床部分热量;
s3:取油液与供氢混合溶剂、ru/c催化剂投入高压反应器中进行加氢脱氧反应,油液与供氢混合溶剂的质量比为100:9,所述供氢混合溶剂由乙酸乙酯、苯甲酸苄酯按等质量比组成,高压反应器中的反应压力为8mpa,反应温度为295℃,高压反应器内设有间歇开启且搅拌速率为110r/min的搅拌器,反应时间为2h;
随后离心、取液态物置于萃取塔中,萃取剂经高压泵加压和预热后进入萃取塔进行超临界萃取提质,萃取剂为二氧化碳或甲烷,萃取釜压力为5mpa,超临界存取温度为130℃;
s4:萃取塔顶部物料经管路输送进入减压的一级分离塔和二级分离塔中进行连续减压分离,一级分离塔压力为2.8mpa、温度为90℃,二级分离塔的压力为2mpa、温度为85℃,分离后的萃取剂进入储罐用于萃取循环,一级分离塔和二级分离塔的塔底产物粉分别送入水油分离器分离,获得的单一油相或油相混合品作为生物质液体燃料成品,所述生物质液体燃料的总酸值为98mgkohg-1,热值为48mjkg-1。
将实施例1-3与市购生物柴油(济南嘉旭化工)作为对比例,按照表中试验标准进行性能检测,实施例1a,实施例1b分别为实施例一级分离塔和二级分离塔的生物质液体燃料,结果如下所示:
由上表可知本发明的机理为:
(1)采用木质素原料和糖类原料作为原料并控制含水量,通过催化裂解和脱氧作用,发生c-c键断裂和c-h键断裂。长碳链裂解呈短碳链、糖类分解为低聚糖甚至单糖或脱氢酐单糖缩合,使得油气冷凝收集的液态油产品中包括低分子烷烃、不饱和烃类、酸类、酯类、醇类、酮类、酚类、碳化合物、呋喃类有机成分和相关离子无机成分,分离的副产品灰分可用于生产固体燃料提高副产品收益;
(2)裂解过程中采用在负压厌氧条件下升温裂解,并以油气冷凝时产生的不冷凝气体用于循环并提供催化裂解反应流化床部分热量,利用微波辅助裂解提高升温速率、充分利用穿透性能提高特别是导热性较低的生物质原料的热传导作用,微波磁场的高频振动使加热均匀,避免温差梯度产生外焦内生现象,并对高分子裂解有明显催化作用,清洁环保从而提高能源利用率,减小裂解热能能耗和损耗;
(3)催化裂解过程中,mcm-48介孔分子筛购自于吉仓纳米有限公司,具有约2.6nm左右的均一孔径及两套相互独立的三维螺旋孔道网络结构,cm-48介孔分子筛经过钴盐和金属硼酸盐的酸性改性edta-2naco-sn/mo-mcm-48,两步法在催化裂解过程中避免结焦失活现象、延长催化剂活性和寿命,各种酸类转化为酯类,有利于降低反应温度、提高液气转化率和高碳数油液收率,适用于柴油成品和与机油半成品的混合,避免硫化污染;
(4)通过与供氢混合溶剂、ru/c催化剂在高压反应器中进行加氢脱氧反应,生物质原料裂解油液中的含氧基团氧原子与氢原子作用、使c-o键断裂、c-h键形成,以减小油液中的酸值和含氧化合物含量,提高油液热值,有效抑制了可见焦炭的形成,满足燃烧稳定性和燃烧充分需求,加氢脱氧生产的二氧化碳还可用于萃取、降低成本;
(5)采用优化条件通过超临界萃取提质、两级分离塔减压分离,水油分离提取单一油相或油相混合品作为生物质液体燃料成品,减小脱氧过程中生成的水,且具有良好的溶解性和扩散性,有利于提高产值传热、抑制生物油聚合结焦反应,萃取剂甲醇可很好地与生物油中的酸类、醛类反应生产酯类和缩醛,从而降低生物质液体燃料的水分和酸值,有利于提高产品热值。
以上所述,仅为本发明较佳的具体实施方式,但本发明的保护范围并不局限于此,任何熟悉本技术领域的技术人员在本发明揭露的技术范围内,可轻易想到的变化或替换,都应涵盖在本发明的保护范围内。因此,本发明的保护范围应该以权利要求书的保护范围为准。
本文用于企业家、创业者技术爱好者查询,结果仅供参考。