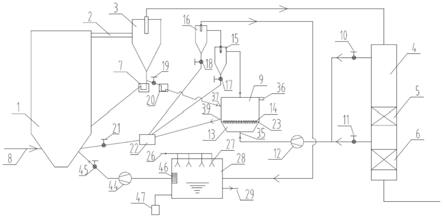
1.本发明属于资源回收技术领域,具体涉及一种废弃风机叶片热解回收系统及其工作方法。
背景技术:
2.近年来,风力发电行业呈现快速发展趋势,每年新增装机量不断增加。而从另一个角度,废旧叶片的综合处置值得关注。由于风机叶片的设计寿命不超过20年,早期风机将不退役或进行叶片更换等提质增效改造,将出现大量淘汰叶片,加之叶片在运行中的损毁、叶片企业的生产边角废料,共同构成了大量需要综合处置的废旧叶片(统称)。
3.从材料构成上,风机叶片主要由复合材料(环氧树脂等)、纤维增强材料(如玻璃纤维等)、胶粘剂(如环氧胶粘剂、聚氨酯胶粘剂等)和涂层等组成,在重量上,复合材料占叶片重量比例已超过90%。加之废旧叶片总量较大,需要对叶片复合材料再利用,避免对环境造成二次污染。
4.叶片再利用包括能量利用和原料利用。能量利用指的是焚烧叶片以利用复合材料等的热值,比如华能清能院设计的焚烧废旧叶片的循环流化床锅炉系统及其工作方法(发明专利申请号:202011304148.6);原料利用指将废旧叶片的复合材料参与到相似的资源流中,比如将叶片切碎用于不同产品和过程的重复使用、水泥生产等。总体上,叶片复合材料的高效回收仍是一个挑战,除了简单的焚烧回收热量法,行业也在持续探索更有前景的叶片材料回收方法,如化学回收等。
5.从材料大致分类上,叶片复合材料可认为属于热固性塑料,包括热固性树脂(环氧树脂等)和填充增强材料(玻璃纤维等)。热固性塑料具有不熔不溶的性质,但在高温下会出现热分解,而温度的控制将决定分解的程度。对叶片热固性塑料进行热分解,分解产物回收后可作为原材料使用,相比焚烧等方式,资源回收利用的属性更为突出,但是目前还没有成熟的技术。
技术实现要素:
6.为了解决上述现有技术中存在的缺陷,本发明的目的在于提供一种废弃风机叶片热解回收系统及其工作方法,可有效裂解废弃叶片中的复合材料并回收裂解油,总体上实现了风机废弃叶片的无害化与资源化处理。
7.本发明通过以下技术方案来实现:
8.本发明公开了一种废弃风机叶片热解回收系统,包括破碎粉碎系统、循环流化床锅炉系统、热解反应器、集料及输送装置、热解气气固分离系统和裂解油分离系统;
9.热解反应器内部包括热解腔室和风室,风室设在热解腔室下方,风室的底部连接有热解器烟气入口,风室与热解腔室之间设有布风板,布风板上设有若干风帽;热解反应器上分别设有叶片颗粒入口、循环灰入口、热解气出口和半焦出口;
10.破碎粉碎系统与叶片颗粒入口连接;
11.循环流化床锅炉系统包括依次连接的炉膛、水平烟道、第一旋风分离器和水平烟道,第一旋风分离器底部出口连接有两条支路,一条支路连接有第一返料器,第一返料器与炉膛的返料入口连接,另一条支路与循环灰入口连接;第一旋风分离器底部出口与循环灰入口之间的管路上设有第二返料器;水平烟道上设有抽气口,抽气口与热解器烟气入口连接;
12.热解气出口与热解气气固分离系统连接,热解气气固分离系统的固体出口和半焦出口均与集料及输送装置连接,集料及输送装置与炉膛连接;热解气气固分离系统的气体出口与裂解油分离系统连接;
13.裂解油分离系统的裂解油出口连接有裂解油储仓,裂解油分离系统的气体出口与炉膛连接。
14.优选地,破碎粉碎系统包括依次连接的破碎机、除铁器、皮带输送器和粉碎机,粉碎机通过第一绞龙与叶片颗粒入口。
15.优选地,抽气口分别设在水平烟道的省煤器和空预器的上游处,两个抽气口连接的管路上分别设有第一截止阀和第二截止阀,第一截止阀和第二截止阀与热解器烟气入口之间的连接管路上设有第一引风机。
16.优选地,热解反应器倾斜设置,叶片颗粒入口、循环灰入口和热解气出口依次设置在热解反应器的上壁,叶片颗粒入口与循环灰入口之间设有落粒板,落粒板上设有若干圆孔,圆孔的直径大于叶片颗粒的粒径;循环灰入口与热解气出口之间设有第一隔板;落粒板和第一隔板的上端均与热解反应器的上壁连接,下部均与布风板存在间距;热解气出口的下方设有第二隔板,第二隔板的一端与第一隔板连接,另一端与热解反应器侧壁存在间距。
17.进一步优选地,落粒板和第一隔板均与布风板垂直,第二隔板与布风板平行。
18.优选地,风室的截面积沿热解器烟气入口至布风板渐扩;热解器烟气入口设在风室底部的中心处。
19.优选地,热解气气固分离系统包括两级串联的第二旋风分离器和第三旋风分离器,第二旋风分离器的气体出口与第三旋风分离器的入口连接,第二旋风分离器的底部出口和第三旋风分离器的底部出口均与集料及输送装置连接,第二旋风分离器的底部出口与集料及输送装置的连接管路上设有第六截止阀,第三旋风分离器的底部出口与集料及输送装置的连接管路上设有第七截止阀;第三旋风分离器的气体出口与裂解油分离系统连接。
20.优选地,裂解油分离系统包括喷淋冷却器,喷淋冷却器内部设有若干喷淋喷嘴,喷淋冷却器上设有冷却水出口、裂解油出口和裂解气出口,裂解油出口与裂解油储仓连接,裂解气出口与炉膛连接。
21.进一步优选地,裂解气出口处设有除雾器,裂解气出口与炉膛之间的连接管路上设有第二引风机和第五截止阀。
22.本发明公开的上述废弃风机叶片热解回收系统的工作方法,包括:
23.废旧叶片经破碎粉碎系统处理后成为叶片颗粒输送至叶片颗粒入口;第一旋风分离器分离的高温循环灰的一部分输送至热解反应器内,尾部烟道上的抽气口抽取烟气由热解器烟气入口进入热解反应器流经风室和风帽进入热解腔室内,作为流化烟气使叶片颗粒与高温循环灰充分混合进行热解;气态的裂解油与裂解气、流化烟气和细小颗粒一起从热解气出口排出,经热解气气固分离系统后,固体颗粒与半焦出口排出的热解半焦一起进入
集料及输送装置后送回炉膛参与焚烧;热解气气固分离系统流出的裂解气进入裂解油分离系统,分离出的裂解油进入裂解油储仓内,供下一步处理。
24.与现有技术相比,本发明具有以下有益的技术效果:
25.本发明公开的一种废弃风机叶片热解回收系统,结构独立灵活,可以实现cfb锅炉与热解回收系统协同运行或是cfb锅炉的单独运行,同时还可进行其它热固性废弃塑料的综合处置。本系统基于高效热解反应器及流程的设计,可有效裂解废弃叶片中的复合材料并回收裂解产生的裂解油,裂解油可用于生产燃料油或作为合成环氧树脂等原料,可循环利用制作风机叶片。热解前叶片前置处理较少,只需对废弃叶片进行破碎与粉碎,对叶片材料挑剔性低,在高温环境下,叶片上的其他物质,如粘合胶、叶片支撑结构等,亦将被热解回收利用,并不会较大的改变裂解油的成分与含量等。而裂解气被抽送至炉膛有效焚烧,所含热值被有效利用,并且燃烧过程中产生的污染物借助原有锅炉系统配备的环保装置(如脱硫脱硝装置等)可实现达标排放。在尾部烟道抽取烟气作为热解反应器内流化气体,即可用于初步加热叶片颗粒,又为叶片颗粒裂解提供了低氧环境,有利于叶片复合材料更多的裂解并析出热解油。热解反应器内缺氧氛围下的热解反应有效避免了废弃叶片直接焚烧潜在的二噁英生成与排放等问题,总体上实现了风机废弃叶片的无害化与资源化处理。热解的叶片颗粒总量相比机组燃煤量较小,热解系统对锅炉运行的影响较小,而热解半焦送回炉膛焚烧,对锅炉运行与飞灰/底渣的成分影响可忽略。在叶片材料综合回收利用技术成熟并大规模利用前,能够有效解决废旧叶片对环境的危害等影响,能够产生良好的环保效益与经济效益。
26.进一步地,破碎粉碎系统通过破碎机和粉碎机逐级将叶片处理成粒径较小的颗粒,有利于充分热解;同时,除铁器出去原料内夹带的金属件(如小型螺栓等),避免金属器件流入热解器与锅炉系统产生不利影响。
27.进一步地,省煤器上游的抽气温度一般在500~550℃,空预器上游的抽气温度一般在300~350℃,通过调节第一截止阀和第二截止阀的开度控制抽气量,两股烟气混合后温度在350~450℃,可作为热解反应器内的流化烟气。
28.进一步地,热解反应器内落粒板与第一隔板的设置,使得叶片颗粒与高温循环灰可以较长时间充分接触换热;同时,第二隔板的阻隔作用,被风帽出口高速气流搅动的循环灰与叶片颗粒被阻挡并掉落,多次反复,实现了充分的热解反应,有效避免了解热半焦(包含循环灰、叶片颗粒与热解后的颗粒)被气流直接带出,降低了热解气出口中气流的颗粒浓度。依靠颗粒重力与布风板不同区域以不同角度安装的风帽的出口气流作用,叶片颗粒与循环灰在充分热解后能顺利运送至侧底部的半焦出口,并被顺利卸出,避免了堵塞。
29.进一步地,热解气气固分离系统采用两级旋风分离器,分离效率高、效果好。
30.本发明公开的上述废弃风机叶片热解回收系统的工作方法,结合废弃叶片热解处置的需求,可灵活控制cfb锅炉的单独运行或cfb锅炉与废弃叶片热解回收装置的协同运行。热解的叶片颗粒总量相比机组燃煤量较小,热解系统对锅炉运行的影响较小,而热解半焦送回炉膛焚烧,对锅炉运行与飞灰/底渣的成分影响可忽略。大量的废旧叶片处理量可依靠cfb锅炉的持续运行实现。处理过程中充分利用了资源,总体上实现了风机废弃叶片的无害化与资源化处理,产生良好的环保效益与经济效益。
附图说明
31.图1为本发明的废弃风机叶片热解回收系统的整体结构示意图;
32.图2为本发明的破碎粉碎系统的结构示意图;
33.图3为本发明的热解反应器的结构示意图;
34.图4为本发明的热解反应器内落粒板的结构示意图。
35.图中:1为炉膛;2为水平烟道;3为第一旋风分离器;4为尾部烟道;5为省煤器;6为空预器;7为第一返料器;8为二次风管;9为热解反应器;10为第一截止阀;11为第二截止阀;12为第一引风机;13为风室;14为风帽;15为第二旋风分离器;16为第三旋风分离器;17为第六截止阀;18为第七截止阀;19为第三截止阀;20为第二返料器;21.第四截止阀;22为集料及输送装置;23为布风板;26为冷却水入口;27为喷淋喷嘴;28为喷淋冷却器;29为冷却水出口;30为破碎机;31为除铁器;32为皮带输送器;33为粉碎机;34为第一绞龙;35为热解器烟气入口;36为叶片颗粒入口;37为循环灰入口;38为热解气出口;39为半焦出口;40为第2绞龙;41为落粒板;42为第一隔板;43为第二隔板;44为第2引风机;45为第5截止阀;46为除雾器;47为裂解油储仓。
具体实施方式
36.下面结合附图和具体实施例对本发明做进一步详细描述,其内容是对本发明的解释而不是限定:
37.如图1,本发明的废弃风机叶片热解回收系统,主要有3部分组成:
38.第1部分是常规的循环流化床锅炉,包括炉膛1、水平烟道2、第一旋风分离器3、尾部烟道4、省煤器5、空预器6、第1返料器7、二次风管8以及在图1中未呈现的cfb锅炉的其他设备装置,如一次风系统、受热面、除尘器与烟囱等。作为常规的燃煤发电装置,无论风机叶片热解回收装置是否运行,该cfb锅炉系统都能正常运行。
39.第2部分是废弃叶片的破碎粉碎装置。如图2,废旧叶片在风电场和叶片企业分割成2~3米长的段状并集中运输至cfb锅炉所在地临时存放。开始热解处置时,将段状叶片送入破碎机30,通过破碎机30内相互咬合切割的机械结构,将叶片初步破碎成长度2~5cm的块状原料,完成破碎后从破碎机30出口排出后直接掉入下游的除铁器31,除铁器31内设电磁吸附系统,可吸附原料内夹带的金属件(如小型螺栓等),避免金属器件流入热解与锅炉系统对系统装置产生不利影响。在除铁器31出口的下方布置具有一定角度的皮带输送器32,将块状原料提升至与热解反应器9安装在同等高度的粉碎机33入口处,粉碎机33进一步将块状原料粉碎为平均粒度在3~5mm的颗粒。叶片颗粒经第一绞龙34从粉碎机33里卸出并输送至热解反应器9的叶片颗粒入口36。
40.第3部分是叶片颗粒的热解回收利用部分。如图1,在cfb锅炉的尾部烟道4的省煤器5和空预器6上游的合适位置各设置抽气口,连接抽气管道,由第一引风机12提供动力,抽取不同温度的尾部烟道烟气。省煤器5上游抽气温度在500~550℃,空预器6上游抽气温度在300~350℃之间。通过调节第1截止阀10和第2截止阀11的开度控制抽气量,两股烟气混合后温度在350~450℃,作为热解反应器9内的流化烟气,经热解气烟气入口35进入热解反应器9的风室13。由于尾部烟道4中烟气含氧量较低,约为3%,可认为热解反应器9处于低氧氛围,有利于叶片颗粒的受热与裂解。在本发明的一个较优的实施例中,省煤器5和空预器6
上游抽气口连接的管路共同连接至一个内腔圆滑的混气室,经充分混匀后输出。
41.图3为热解反应器9的详细结构设计图,热解反应器9整体为方型结构,底部为锥台形状的风室13,风室13底部中心处设置热解器烟气入口35,而风室13顶部为布风板23,布风板23上分区域分别以不同角度布置有风帽14。热解反应器9顶部设置三个进/出口,分别为叶片颗粒入口36、循环灰入口37和热解气出口38。
42.破碎后的叶片颗粒经第一绞龙34输送至直立的叶片颗粒入口36并掉落在落粒板41上。如图4,落粒板41为方型平板,在上面规则地布置特定直径(略大于叶片颗粒的平均直径)的圆孔,将热解反应器9分隔出方型腔室,出口斜朝下。叶片颗粒掉落后,在风帽14出口气流与颗粒自身重力的作用下,一部分通过落粒板41的孔洞掉落,其余沿着落粒板41滑下,与风帽14的出口气流充分作用,被初步加热。
43.热解反应器9的落粒板41下方同样设置有第一隔板42,在二者之间又形成了另一个腔室,腔室上表面设置有循环灰入口37。在cfb锅炉正常运行时,由第一旋风分离器3分离的高温循环灰经第一返料器7被回送至炉膛1,在第一返料器7上游的立管合适位置外接一条管道,通过调节第三截止阀19开度,可以将小部分的循环灰引流至热解反应器9内。在热解反应器9运行时,部分循环灰经第三截止阀19和第四返料器20作用,流动至循环灰入口37。循环灰落入第一隔板42与落粒板41间的腔室,与落入的叶片颗粒混合,将叶片颗粒快速加热,在重力作用下,并由第一隔板42底部附近的倾斜布置(即与布风板23为垂直布置,具体见图3)的风帽14的快速气流作用,将高温循环灰与叶片颗粒的混合物顺利推进到下端。由于第二隔板43的阻隔作用,被风帽14出口高速气流搅动的循环灰与叶片颗粒被阻挡并掉落,多次反复,实现了充分的热解反应,最终落到侧底部的半焦出口39,最终经第二绞龙40排出。叶片颗粒自经落粒板41与循环灰初步混合起,到与循环灰一起被排出热解反应器9,整个过程时间较长,在风帽14出口高速气流等作用下,叶片颗粒收热充分,热解较为充分。叶片颗粒中无法分解的玻璃纤维等随循环灰一并排出。
44.通过调节热解循环灰与叶片颗粒的重量比例,可有效控制混合物的平均温度。比如,循环灰的温度较高(850~950℃),叶片颗粒多循环灰少的搭配,经流化烟气的搅拌作用,可控制热解反应器9平均温度在400~450℃,在该最佳温度范围下,叶片复合材料(如环氧树脂等)可分解成裂解油和裂解气,且裂解油占比更高。裂解油含复合材料原料单体或它的低分子聚合物等,裂解气主要含co、co2、c1~c4的烷烃和烯烃等。该热解反应器设计与温度控制下,分解产物中裂解油较多,裂解气少,是本专利希望实现的热解效果。
45.在热解反应器9的高温环境中,裂解油亦呈气态,与裂解气、流化烟气和细小颗粒一并从热解气出口38排出。如图3所示,热解反应器9内设置有第二隔板43,有效避免了解热半焦(包含循环灰、叶片颗粒与热解后的颗粒)被气流直接带出,降低了热解气出口38中气流的颗粒浓度。
46.热解气出口38下游串联连接两个旋风分离器,即第二旋风分离器15和第三旋风分离器16,用以分离热解气中携带的粉尘颗粒,第三旋风分离器16内部气流旋转流速更高,可将更细的颗粒分离。分离出的颗粒分别经过第六截止阀17和第七截止阀18,并与半焦出口39排出的热解半焦一并落入集料与输运器22中,汇集后最终被送回cfb锅炉的炉膛1参与焚烧。回送管道末端附近位置设置有第四截止阀21,防止炉膛1烟气反窜。在热解系统运行时,通过调整第六截止阀17和第七截止阀18的开度,使得分离器分离出的粉尘颗粒能顺利通过
并经管道落入集料与输运器22内,结合第四截止阀21,可避免炉膛1烟气进入两个旋风分离器。图1中,集料与输运器22类似于返料器,其与第一返料器7和第四返料器20均通过管道与罗茨风机相连接,由罗茨风机提供高压流化风以顺利实现流化,避免局部堵塞。由于cfb锅炉的返料器系统较为成熟,罗茨风机与各返料器连接的管道在图1中未画出)。
47.从第三旋风分离器16出口流出的裂解气(为流化烟气、叶片颗粒裂解气与极低浓度的颗粒的混合物,简称裂解气或热解气),将其引入喷淋冷却器28,喷淋冷却器28内部在顶面规则布置有较多数量的喷淋喷嘴27,喷淋喷嘴27连接至冷却水入口26,用以将冷却水雾化并喷淋而下,雾化后的水滴与高温裂解气充分接触换热,冷却水由冷却水出口29排出,裂解气内气态裂解油受冷凝结,大部分附着在冷却水滴上,掉入喷淋冷却器28底部的蓄水层。热解气受冷体积缩小,但因为有冷却水滴蒸发成水蒸气,经热交换后的热解气温度可保持在110℃,可使得封闭的喷淋冷却器28内压力不会出现较大变化。
48.因裂解油重量较大,将积聚在底部并被抽出至裂解油储仓47内,供下一步集中处理。收集到的裂解油成分比较复杂,经除尘处理后,经高压加氢反应,可生产出燃料油,或作为合成环氧树脂等的化工原料。
49.喷淋冷却后的裂解气经除雾器46作用将携带雾滴/水滴脱除,成分主要为n2、co2、co、h2o、c1~c4的烷烃和烯烃,还有低浓度的o2。这些气体在第二引风机44的作用下,经第五截止阀45被送入炉膛1,可燃成分参与燃烧并释放热值。同样地,经第四截止阀21进入锅炉的热解半焦在高温环境下也发生充分反应,即叶片颗粒内残留的可燃复合材料被焚烧,玻璃纤维颗粒等其他不燃物在炉膛1内反复碰撞与破碎,形成飞灰或底渣。玻璃纤维飞灰颗粒与其他常规飞灰颗粒最终被尾部烟道4末端的除尘器等捕捉,玻璃纤维成分为铝、钙、纳、镁等金属元素的硅酸盐,其成分与燃煤飞灰的成分较为接近,加之与cfb锅炉燃煤相比,热解反应器9处置的废弃叶片量较小,可认为焚烧热解半焦对原有飞灰的品质影响可以忽略。
50.本发明的工作过程如下:
51.废旧叶片在风电场和叶片企业分割成2~3米长的段状并集中运输至cfb锅炉所在地临时存放。热解处置前,将段状叶片送入破碎机30将叶片初步破碎成长度2~5cm的块状原料,经过破碎机30下游的除铁器31,通过电磁吸附系统除去原料内夹带的金属件(如小型螺栓等)。块状原料经与地面呈一定角度安装的皮带输送器32提升至与热解反应器9安装在同等高度的粉碎机33,进一步粉碎为平均粒度在3~5mm的颗粒。叶片颗粒经第一绞龙34从粉碎机33里卸出并输送至热解反应器9的叶片颗粒入口36。
52.依托于常规的循环流化床锅炉,将其正常运行的由第一旋风分离器3分离的高温循环灰分出一部分,输送至热解反应器9内作为废弃叶片加工成的叶片颗粒热解的主要热源。在cfb锅炉的尾部烟道4的省煤器5和空预器6上游的合适位置各设置抽气口,连接抽气管道,由第一引风机12提供动力,抽取不同温度的尾部烟道烟气。通过调节第一截止阀10和第二截止阀11的开度控制抽气量,两股烟气混合后温度在350~450℃,作为热解反应器9内的流化烟气。
53.尾部烟道4抽取的两股烟气混合后,进入热解反应器9的风室13,经布置于布风板23上的风帽14进入热解反应器9的腔室内,在其中,通过落粒板41、第一隔板42和第二隔板43对热解反应器9中布风板23上方腔室的划分,实现叶片颗粒与高温循环灰的有效混合,整个热解反应器的温度控制在400~450℃,有利于叶片复合材料尽可能多地以裂解油的形式
分解。在重力与布风板23不同区域分别设计安装角度布置的风帽14出口气流等的综合作用下,热解反应时间长,叶片颗粒实现了有效热解,且不会在内部腔室出现阻塞。叶片颗粒中无法分解的玻璃纤维等随循环灰一并排出。
54.在热解反应器9的高温环境下,裂解油亦呈气态,与裂解气、流化烟气和细小颗粒一并从热解气出口38排出。在热解气出口38下游串联连接两个旋风分离器,即第二旋风分离器15和第三旋风分离器16,用以分离热解气中携带的粉尘颗粒,第三旋风分离器16内部气流旋转流速更高,可将更细的颗粒分离。分离出的颗粒,与半焦出口39排出的热解半焦一并落入集料与输送器22,最终被送回cfb锅炉的炉膛2参与焚烧。
55.从第三旋风分离器16出口流出的裂解气,将其引入喷淋冷却器28,在其顶部规则布置的较多数量的喷淋喷嘴27将冷却水充分破碎成小雾滴,与高温裂解气充分接触换热,裂解气内气态裂解油受冷凝结,大部分附着在冷却水滴上,掉入喷淋冷却器28底部的蓄水层。利用冷却后的裂解油与水密度的不同,裂解油将积聚并被抽出至裂解油储仓47内,供下一步集中处理。而喷淋冷却后的裂解气经除雾器46作用将携带雾滴/水滴脱除后,在第二引风机44的作用下,全部被送入炉膛1焚烧处理,同样地,经第四截止阀21进入锅炉的热解半焦在炉膛1的高温环境下也发生充分反应,叶片颗粒内残留的可燃复合材料被焚烧,玻璃纤维颗粒等其他不燃物在炉膛1内形成飞灰或底渣。玻璃纤维飞灰颗粒与其他常规飞灰颗粒最终被尾部烟道4末端的除尘器等捕捉,由于热解反应器9处置的废弃叶片量较小,热解半焦通过cfb锅炉焚烧处置对原有飞灰的品质影响可以忽略。
56.需要说明的是,以上所述仅为本发明实施方式的一部分,根据本发明所描述的系统所做的等效变化,均包括在本发明的保护范围内。本发明所属技术领域的技术人员可以对所描述的具体实例做类似的方式替代,只要不偏离本发明的结构或者超越本权利要求书所定义的范围,均属于本发明的保护范围。
再多了解一些
本文用于企业家、创业者技术爱好者查询,结果仅供参考。