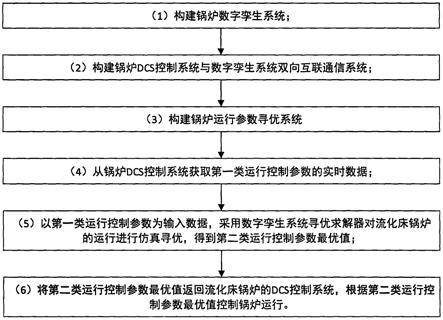
1.本发明属于燃煤流化床锅炉领域,特别涉及一种基于数字孪生的流化床锅炉运行优化方法与系统。
背景技术:
2.燃煤流化床锅炉的燃料适应性广、燃烧稳定性强,特别适合燃用煤矸石、贫煤等劣质煤,对大量处理劣质煤提供了可行的燃烧利用方法。但是,流化床锅炉运行中,时常出现炉膛结焦、管道磨损、低温腐蚀、飞灰含碳量高等多种问题,锅炉运行安全、经济性受到威胁。一般运行中,主要依靠运行人员的操作经验对流化床锅炉进行优化调整,虽然一定程度上缓解了上述问题,但仍有很大的优化空间。流化床锅炉系统复杂,各子系统相互匹配、协同工作,单纯依靠人工经验很难达到运行的最优化,并且仅仅对锅炉运行某个方面的优化可能导致另一个方面运行经济性或安全性下降,无法达到锅炉运行整体的最优化,为此,需要从锅炉整体的安全、经济和环保性考虑,实现流化床锅炉的整体性运行优化。
技术实现要素:
3.本发明提出一种基于数字孪生的流化床锅炉运行优化方法,其特征在于,包括步骤:
4.(1)构建锅炉的数字孪生系统;
5.(2)构建锅炉dcs控制系统与数字孪生体双向互联通信系统;
6.(3)构建锅炉运行参数寻优系统;
7.(4)从锅炉dcs控制系统获取第一类运行控制参数的实时数据;
8.(5)以第一类运行控制参数为输入数据,采用锅炉运行参数寻优系统对流化床锅炉的运行进行寻优,得到第二类运行控制参数最优值;
9.(6)将第二类运行控制参数最优值返回流化床锅炉的dcs控制系统,根据第二类运行控制参数最优值控制锅炉运行。
10.所述构建锅炉的数字孪生系统,包括步骤:(a)构建锅炉燃烧、换热、治污仿真系统,包括构建锅炉物理结构参数库,构建炉膛、分离器、外置换热器、冷渣器、尾部烟道内的煤颗粒与空气两相流动模型、气体扩散传质模型,受热面管内工质流动模型、煤颗粒燃烧模型、煤颗粒破碎模型、炉膛火焰与壁面换热模型、炉内温度场与气氛场演变模型、烟气与受热面换热模型、受热面沾污积灰模型、受热面氧化与磨损模型、低温腐蚀模型、炉内石灰石脱硫模型、scr系统脱硝模型、电除尘器除尘模型;(b)构建锅炉燃烧、换热、治污仿真系统模型求解器,构建仿真寻优求解器;(c)采用从锅炉dcs控制系统实时获取的第一类运行控制参数作为边界条件运行锅炉燃烧和换热仿真系统,获得炉膛、分离器、受热面与尾部烟道内的流动、燃烧、换热、脱硫、脱硝、除尘过程的仿真结果;(d)将仿真结果与从dcs系统获得的与仿真结果相对应参数的实测结果进行对比,采用误差反向传播算法修改锅炉燃烧和换热仿真系统中的模型,以减小仿真结果与实测结果间的误差到1%以下。
11.所述仿真结果包括:床温、物料循环倍率、床层压差、低温过热器出口蒸汽温度、低温过热器出口烟气温度、高温过热器出口蒸汽温度、高温过热器出口烟气温度、低温再热器出口蒸汽温度、低温再热器出口烟气温度、高温再热器出口蒸汽温度、高温再热器出口烟气温度、省煤器出口工质温度、省煤器出口烟气温度、空预器出口烟气温度、热一次风温度、热二次风温度、分离器出口no浓度、scr出口no浓度、喷氨量、排烟so2浓度、排烟氧量、排渣温度、外置床循环灰出口温度、外置床出口工质温度、飞灰含碳量、炉渣含碳量。
12.所述锅炉dcs控制系统与数字孪生体双向互联通信系统,采用千兆以太网物理链路实现dcs控制系统与数字孪生系统双向通信。
13.所述从锅炉dcs控制系统获取第一类运行控制参数的实时数据,频率为0.2hz,即5s每次。
14.所述第一类运行控制参数包括:锅炉负荷、给水压力、给水温度、主蒸汽压力、主蒸汽流量、再热蒸汽压力、再热蒸汽流量、入炉煤工业分析、入炉煤元素分析、入炉煤灰成分、入炉煤可磨性指数、入炉煤粒径分布、入炉煤燃烧特性指数、入炉煤灰熔点、送风温度。
15.所述第二类运行控制参数包括:一次风量、一次风温、二次风量、二次风温、给煤量、回料温度、排渣量、减温水量、烟气挡板开度、外置床循环灰量、石灰石投入量、喷氨量、除尘电流。
16.所述锅炉运行参数寻优系统的优化目标为:
17.min{c
c
c
p
c
pa
c
sa
c
df
c
nox
c
so2
c
dd
c
pl
}
18.其中:
19.c
c
为燃煤成本;
20.c
p
为制粉系统运行成本;
21.c
pa
为一次风机运行成本;
22.c
sa
为二次风机运行成本;
23.c
df
为引风机运行成本;
24.c
nox
为脱硝系统运行成本;
25.c
so2
为脱硫系统运行成本;
26.c
dd
为除尘系统运行成本;
27.c
pl
为管道磨损成本;
28.约束条件为:
[0029][0030]
其中
[0031]
为仿真计算所得的主蒸汽温度;
[0032]
为设定的主蒸汽温度目标值;
[0033]
为仿真所得的再热蒸汽温度;
[0034]
为设定的再热蒸汽温度目标值;
[0035]
q
mdw
为过热蒸汽减温水量;
[0036]
为过热蒸汽减温水最大允许量;
[0037]
q
rdw
为再热蒸汽减温水量;
[0038]
为再热蒸汽减温水最大允许量;
[0039]
t
dpz
为密相区床温;
[0040]
t
d
为入炉煤的灰变形温度;
[0041]
为床层最小允许厚度;
[0042]
l
b
为仿真计算所得的床层厚度;
[0043]
为床层最大允许厚度。
[0044]
所述数字孪生系统具备锅炉故障预警系统、设备寿命预测系统,故障预警模块包含炉膛结焦预警、管壁超温预警、受热面低温腐蚀预警、空预器堵灰预警模块,寿命预测模块包含受热面管道寿命预测、scr催化剂寿命预测模块,所述故障预警模块、设备寿命预测模块采用设备的故障预测模型、寿命损耗模型结合从dcs系统读取的实时运行参数完成故障预警和寿命预测。
[0045]
所述数字孪生系统单独运行于专用服务器上,与dcs系统不在同一服务器上,当数字孪生系统的运行出现非正常运行时,dcs系统将切除与数字孪生系统的通信,而且数字孪生系统的非正常运行不影响流化床锅炉的运行控制。
附图说明
[0046]
图1为数字孪生系统与锅炉dcs系统网络关系图,其中,图1标记如下:1、流化床锅炉;2、dcs控制系统;3、千兆以太网物理链路;4、锅炉数字孪生系统。
[0047]
图2为基于数字孪生的流化床锅炉运行优化方法示意图。
[0048]
图3为数字孪生系统构成及其与dcs控制系统数据交互示意图。
具体实施方式
[0049]
下面结合附图说明一种基于数字孪生的流化床锅炉运行优化方法与系统的具体实施方式。如图1,所述锅炉数字孪生系统单独运行于专用服务器4上,与dcs系统2不在同一服务器上,采用千兆以太网物理链路3实现dcs控制系统与数字孪生系统双向通信,采用tcp/ip协议实现两个系统的互联通信,当数字孪生系统的运行出现非正常运行时,dcs系统将切除与数字孪生系统的通信,而且数字孪生系统的非正常运行不影响流化床锅炉1的运行控制。
[0050]
如图2,基于数字孪生的流化床锅炉运行优化方法包括步骤:
[0051]
(1)构建锅炉的数字孪生系统;
[0052]
(2)构建锅炉dcs控制系统与数字孪生体双向互联通信协议与系统;
[0053]
(3)构建锅炉运行参数寻优系统
[0054]
(4)从锅炉dcs控制系统获取第一类运行控制参数的实时数据;
[0055]
(5)以第一类运行控制参数为输入数据,采用锅炉运行参数寻优系统对流化床锅
炉的运行进行仿真寻优,得到第二类运行控制参数最优值;
[0056]
(6)将第二类运行控制参数最优值返回流化床锅炉的dcs控制系统,根据第二类运行控制参数最优值控制锅炉运行。
[0057]
如图3,锅炉的数字孪生系统包括锅炉物理结构参数库,炉膛、分离器、外置换热器、冷渣器、尾部烟道内的煤颗粒与空气两相流动模型、气体扩散传质模型,受热面管内工质流动模型、煤颗粒燃烧模型、煤颗粒破碎模型、炉膛火焰与壁面换热模型、炉内温度场与气氛场演变模型、烟气与受热面换热模型、受热面沾污积灰模型、受热面氧化与磨损模型、低温腐蚀模型、炉内石灰石脱硫模型、scr系统脱硝模型、电除尘器除尘模型;构建锅炉燃烧、换热、治污仿真系统模型求解器;采用从锅炉dcs控制系统实时获取的第一类运行控制参数作为边界条件运行锅炉仿真系统,获得炉膛、分离器、受热面与尾部烟道内的流动、燃烧、换热、脱硫、脱硝、除尘过程的仿真结果;构建仿真模型优化系统,将仿真结果与从dcs系统获得的与仿真结果对应的dcs参数进行对比,采用误差反向传播算法修正锅炉燃烧和换热仿真系统中的模型,将仿真结果与从dcs系统获得的与仿真结果对应的dcs参数间的误差减小到1%以下。
[0058]
锅炉运行参数寻优系统的优化目标为:
[0059]
min{c
c
c
p
c
pa
c
sa
c
df
c
nox
c
so2
c
dd
c
pl
}
[0060]
其中:
[0061]
c
c
为燃煤成本;
[0062]
c
p
为制粉系统运行成本;
[0063]
c
pa
为一次风机运行成本;
[0064]
c
sa
为二次风机运行成本;
[0065]
c
df
为引风机运行成本;
[0066]
c
nox
为脱硝系统运行成本;
[0067]
c
so2
为脱硫系统运行成本;
[0068]
c
dd
为除尘系统运行成本;
[0069]
c
pl
为管道磨损成本;
[0070]
约束条件为:
[0071][0072]
其中
[0073]
为仿真计算所得的主蒸汽温度;
[0074]
为设定的主蒸汽温度目标值;
[0075]
为仿真所得的再热蒸汽温度;
[0076]
为设定的再热蒸汽温度目标值;
[0077]
q
mdw
为过热蒸汽减温水量;
[0078]
为过热蒸汽减温水最大允许量;
[0079]
q
rdw
为再热蒸汽减温水量;
[0080]
为再热蒸汽减温水最大允许量;
[0081]
t
dpz
为密相区床温;
[0082]
t
d
为入炉煤的灰变形温度;
[0083]
为床层最小允许厚度;
[0084]
l
b
为仿真计算所得的床层厚度;
[0085]
为床层最大允许厚度。
[0086]
数字孪生系统包含锅炉故障预警系统、设备寿命预测系统,故障预警模块包含炉膛结焦预警、管壁超温预警、受热面低温腐蚀预警、空预器堵灰预警模块,寿命预测模块包含受热面管道寿命预测、scr催化剂寿命预测模块,所述故障预警模块、设备寿命预测模块采用设备的故障预测模型、寿命损耗模型结合从dcs系统读取的实时运行参数完成故障预警和寿命预测。
[0087]
该系统与传统依赖人工经验的流化床运行优化相比,优点在于:(1)基于锅炉的精确仿真计算,并全面考虑锅炉制粉、燃烧、换热、脱硫、脱硝、除尘各系统的安全、经济性,实现对各系统整体的最优化,比人工优化更精确,比人工优化中仅考虑某一方面优化而忽略其他方面更能实现锅炉运行的整体优化;(2)系统自动运行,基于数字孪生系统和锅炉运行参数寻优系统获得的的第二类运行控制参数最优值直接返回锅炉dcs控制系统,每5秒对锅炉运行参数进行一次调整,减少人工控制的工作量;(3)具备锅炉故障预警和设备寿命预测功能,保障锅炉运行的安全性,防止人为优化中损坏锅炉安全性操作的发生。
再多了解一些
本文用于企业家、创业者技术爱好者查询,结果仅供参考。